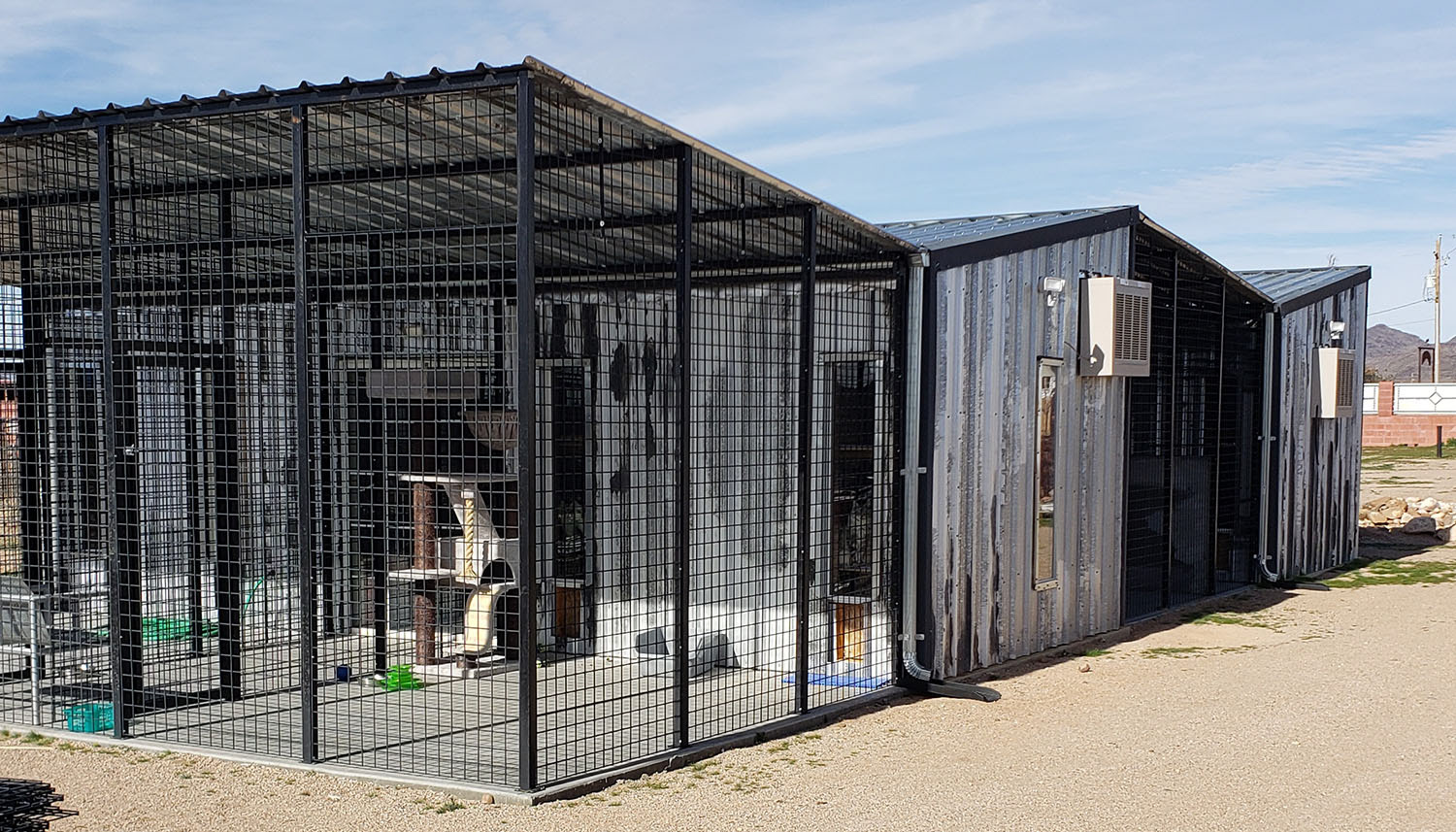
Outside of running a business, this is probably the biggest project I’ve taken on. My wife, requested that I make her a cattery. Honestly, I think I can say that I had never heard of the term “cattery” before this moment. I figured it must have something to do with those adorable little furballs that she seemed so fond of. I soon found out that her vision of a cattery was pretty specific.
Given our new location in the hot Arizona desert, I knew there was quite a bit I was going to have to figure out to make this project a success. This wasn’t one of those, shoot from the hip type of things, and work out the details after the fact.
This was one of those engineering projects the required water, power, and HVAC. Not to mention that the fury things needed in indoor and outdoor living area.
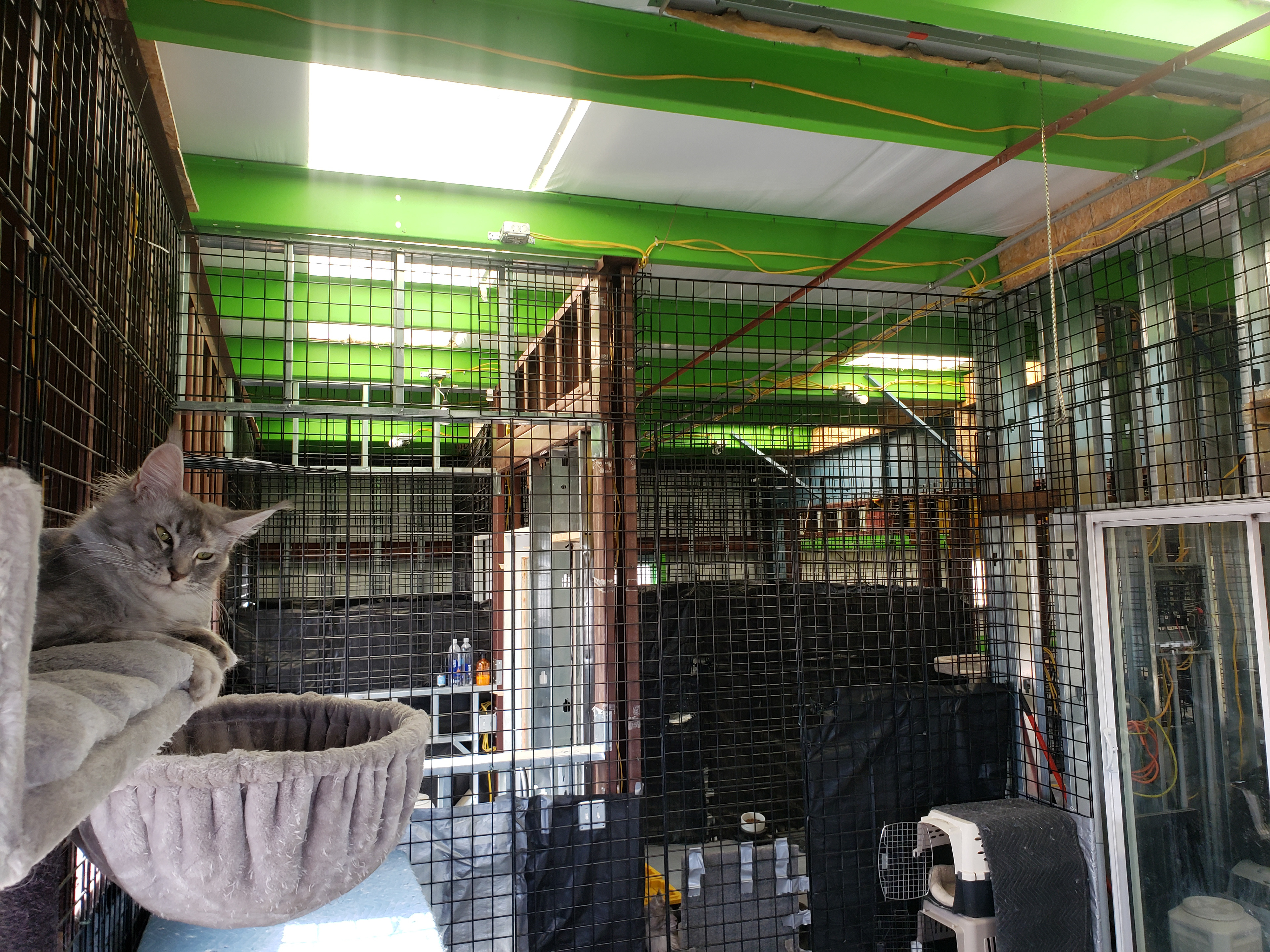
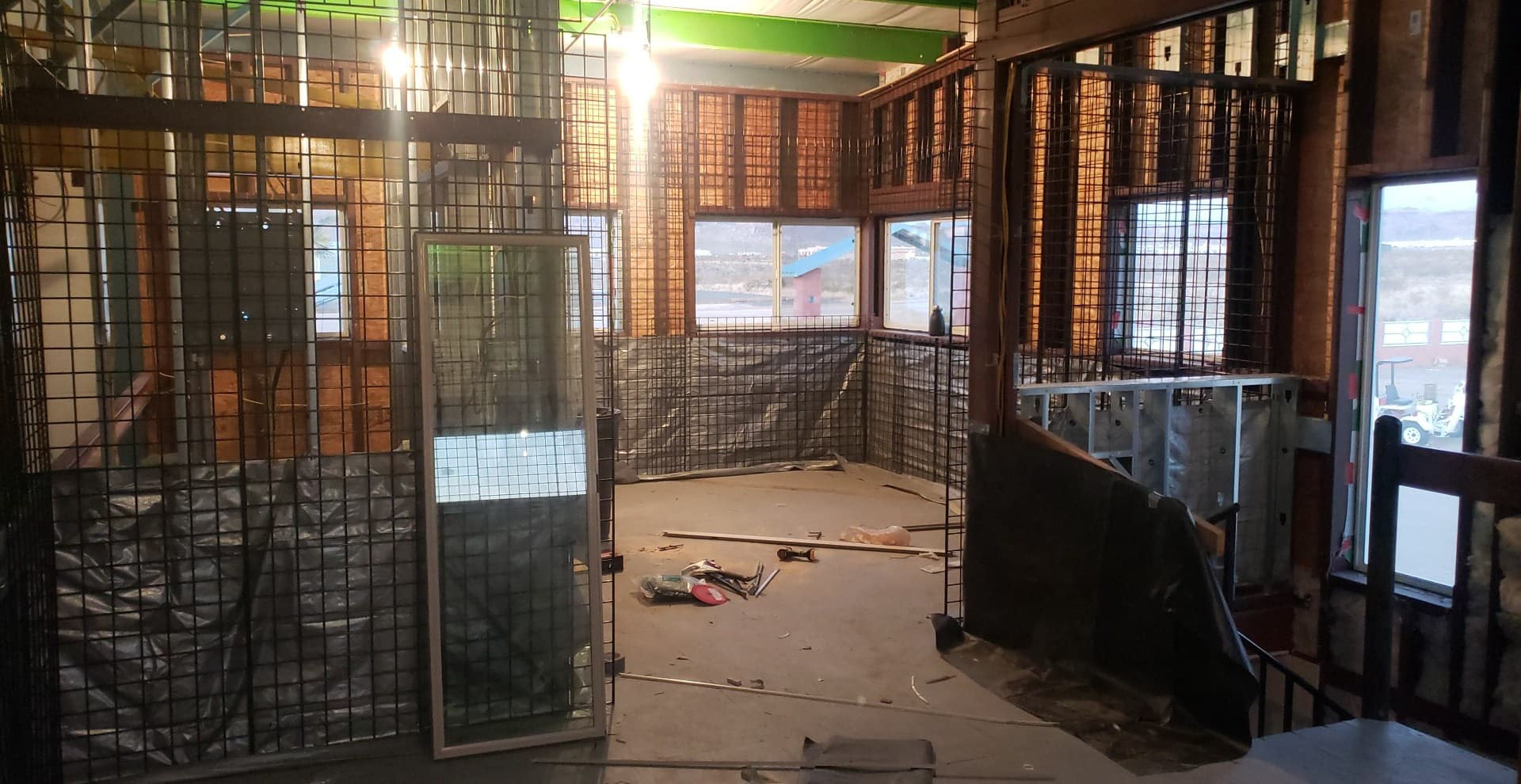
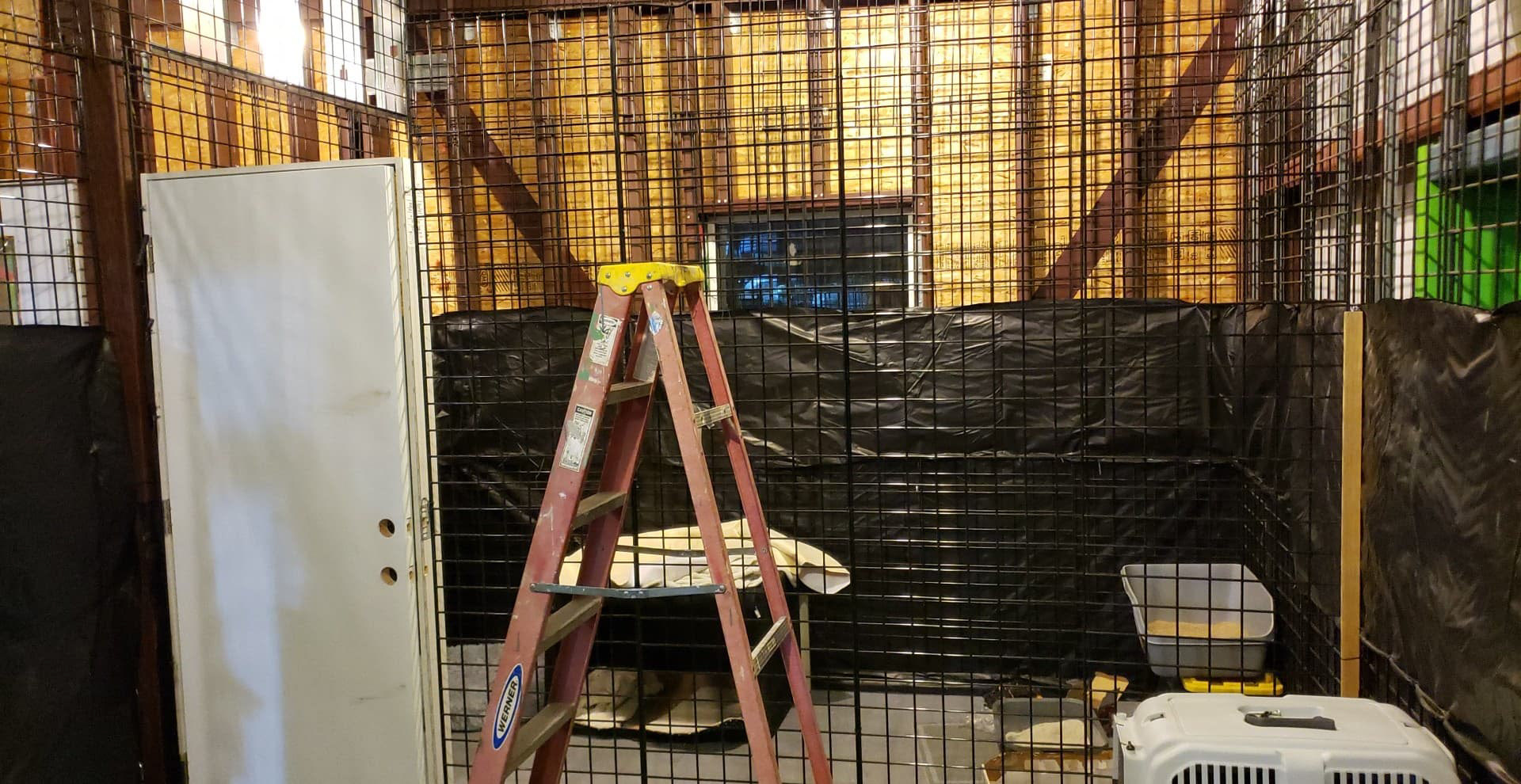
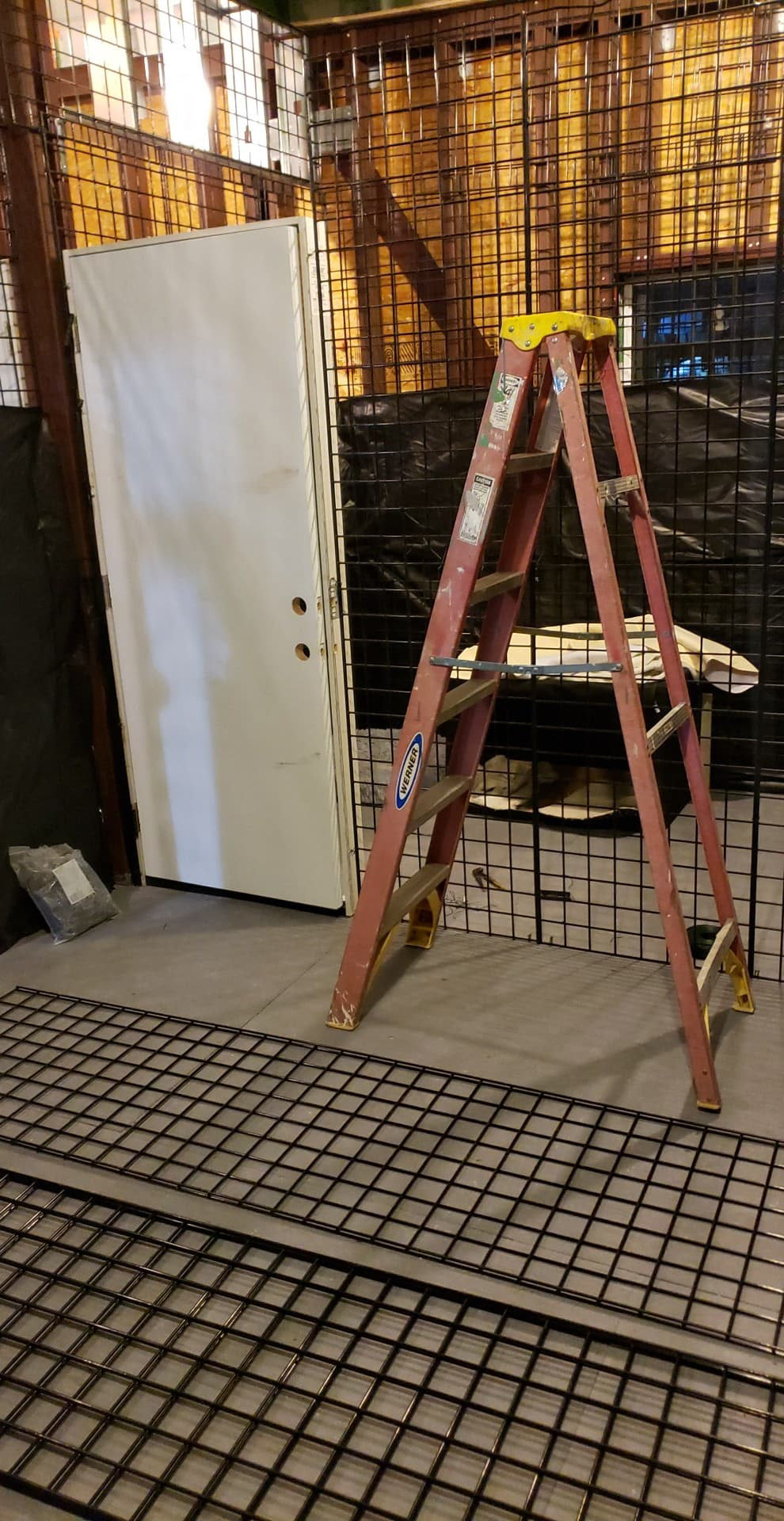
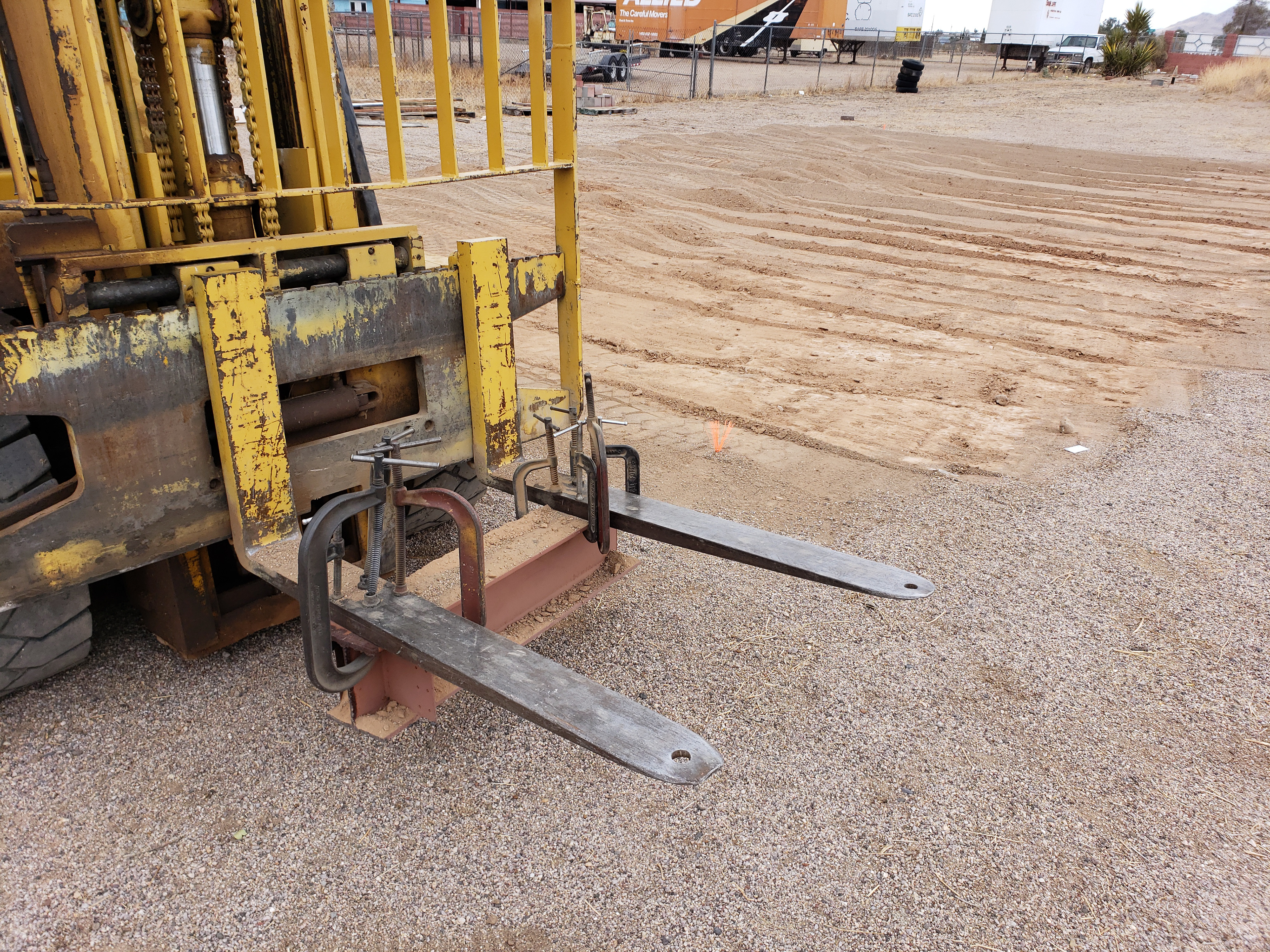
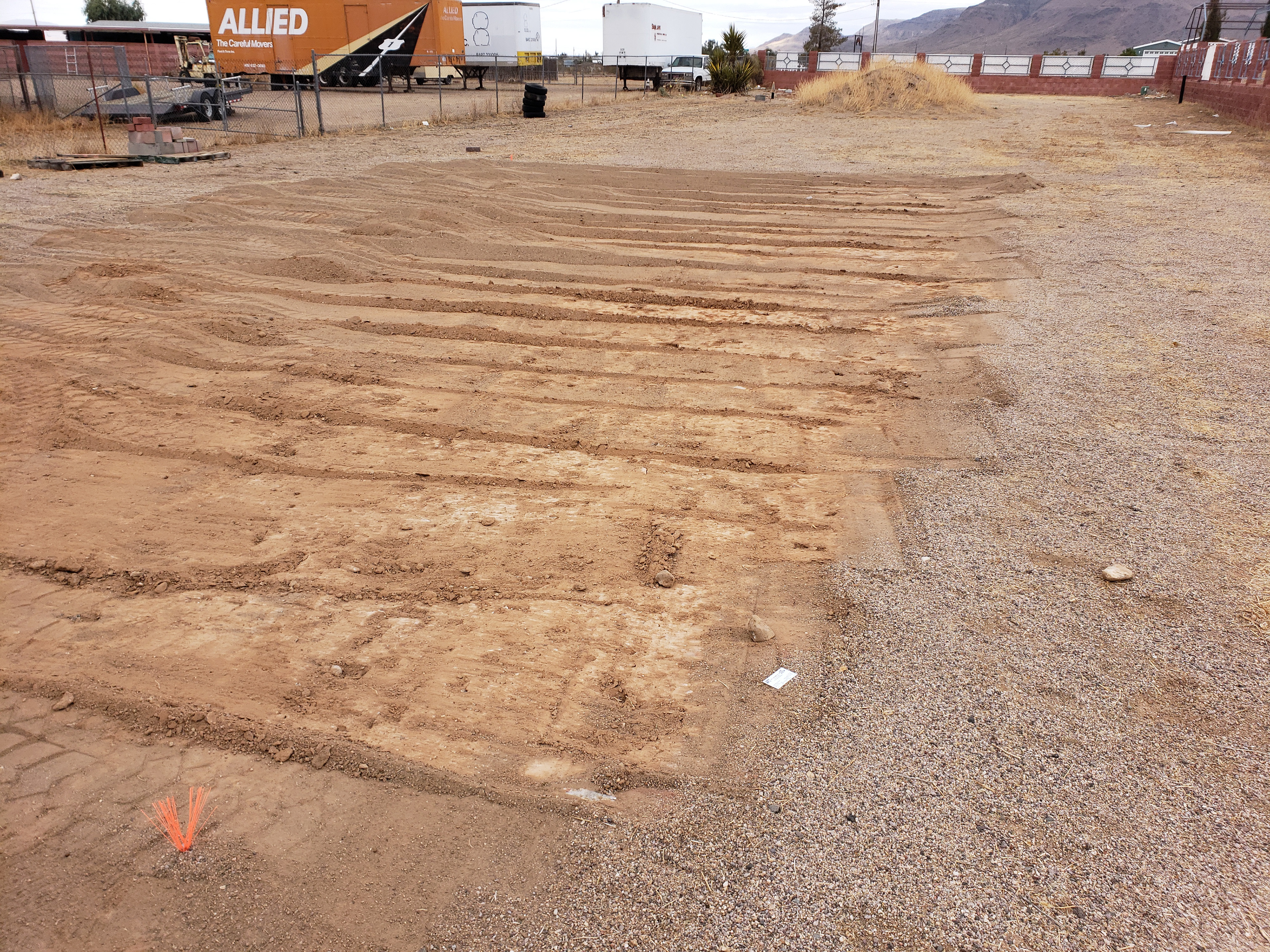
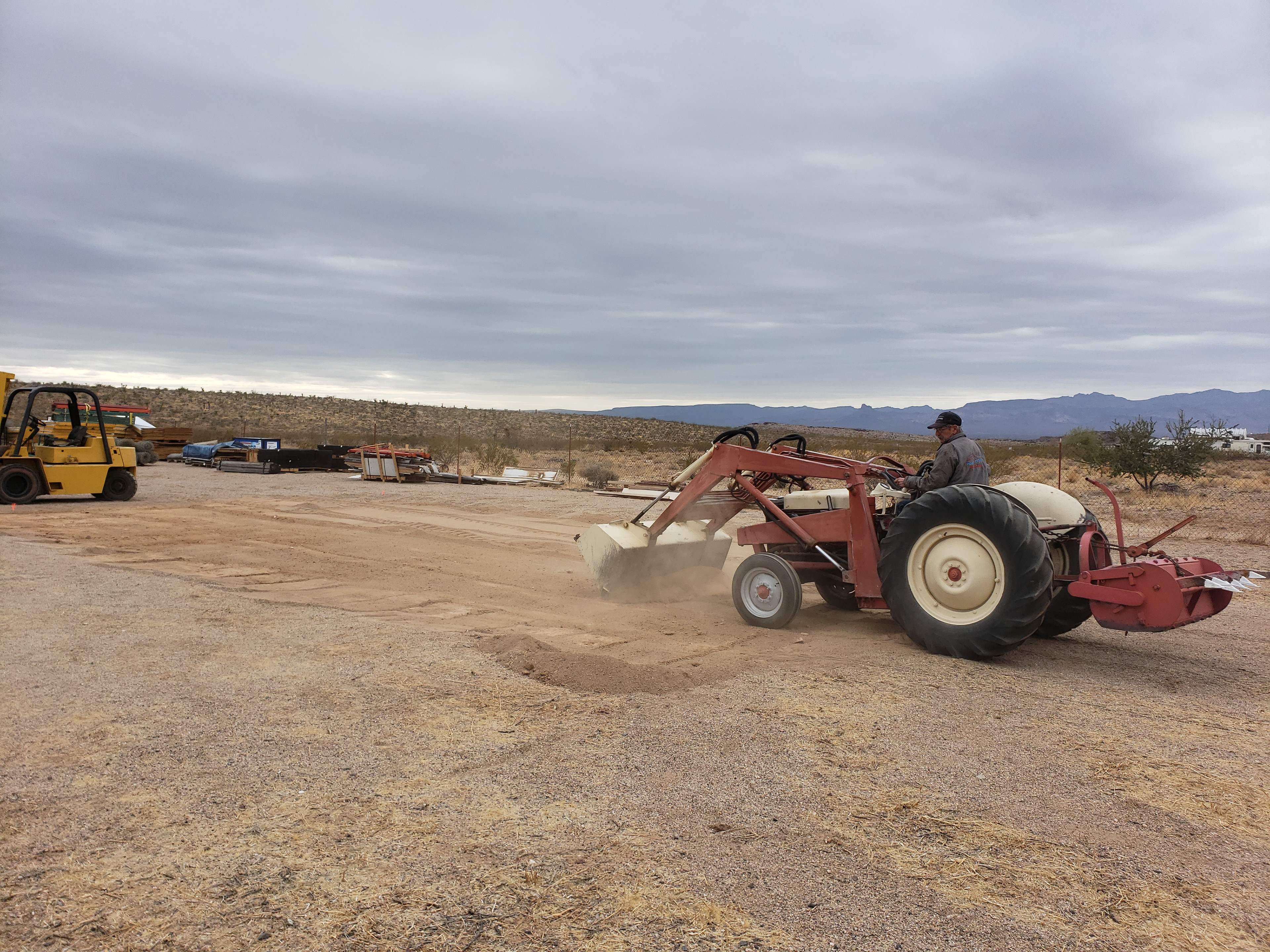
If you are wondering, the box on the back of his tractor worked on the concrete inspired dirt about as well as the hand rake.
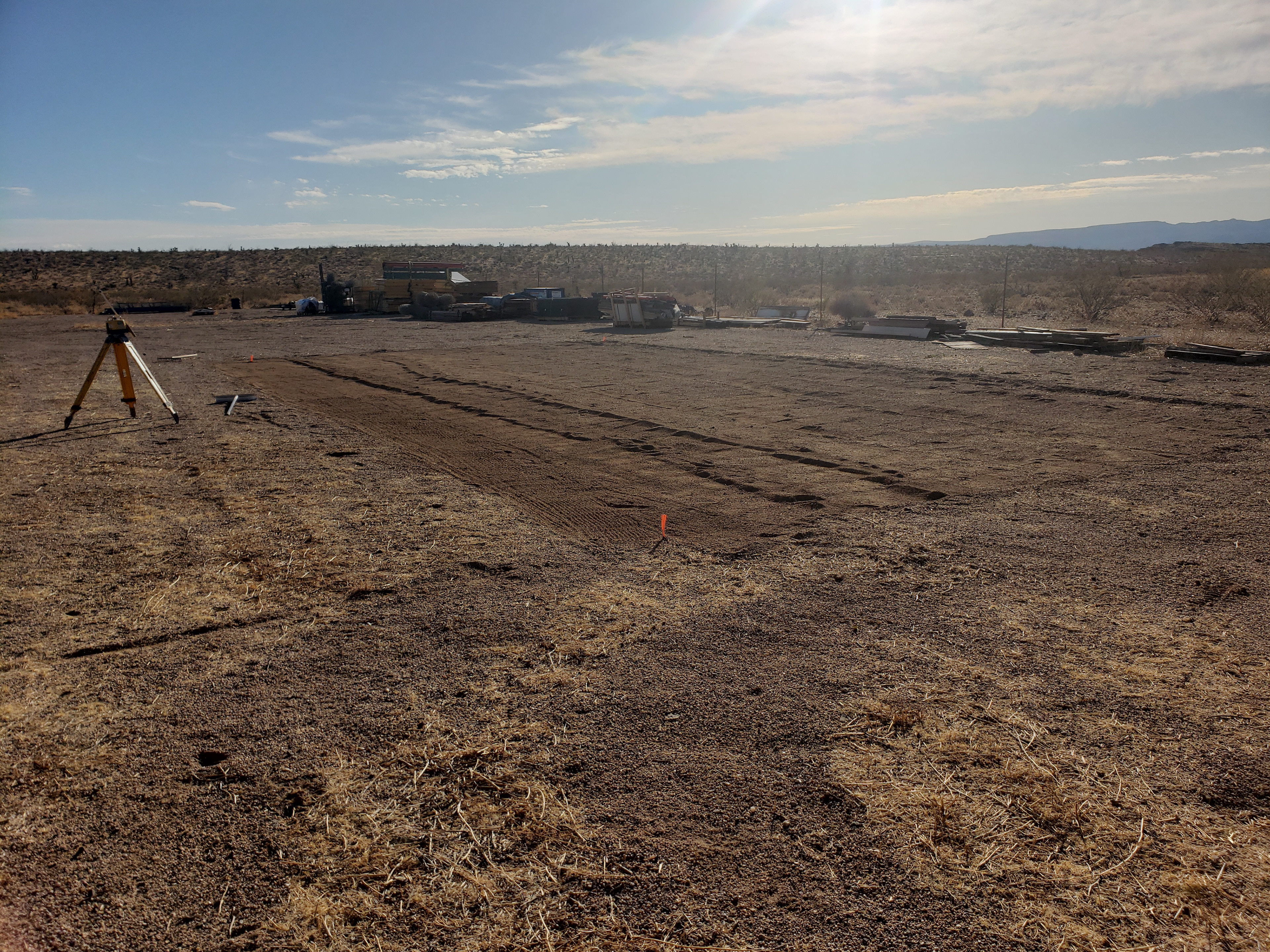
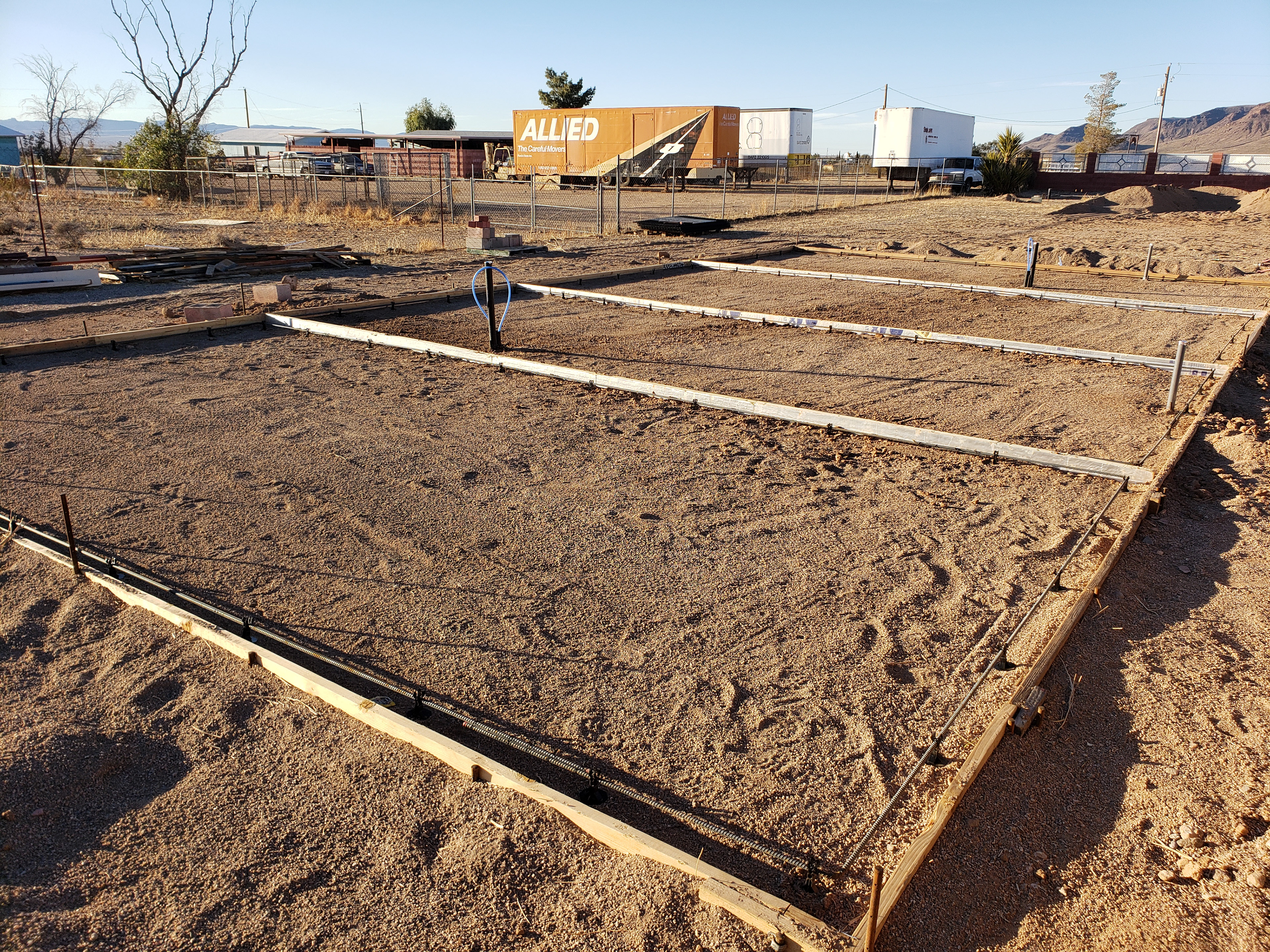
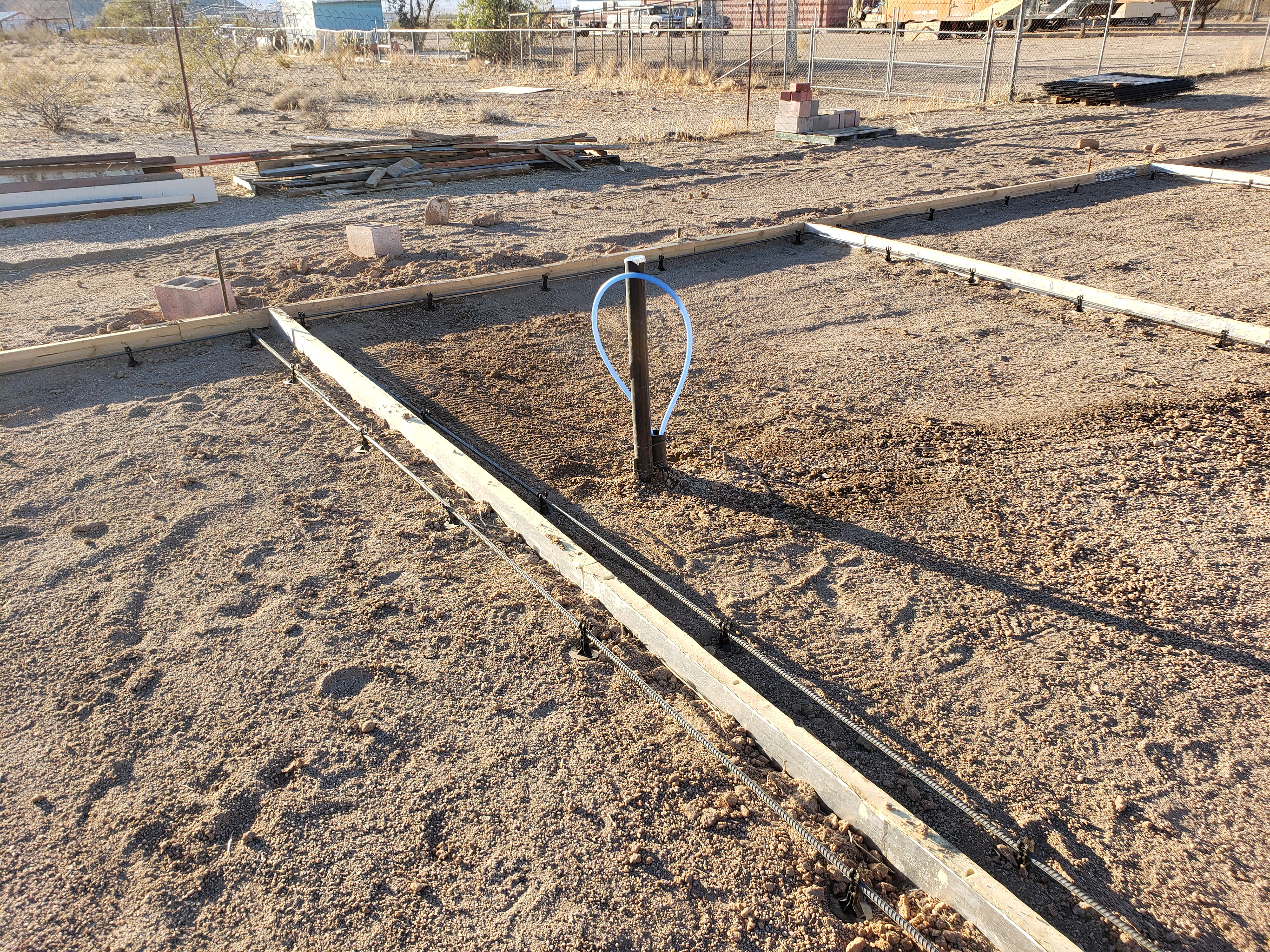

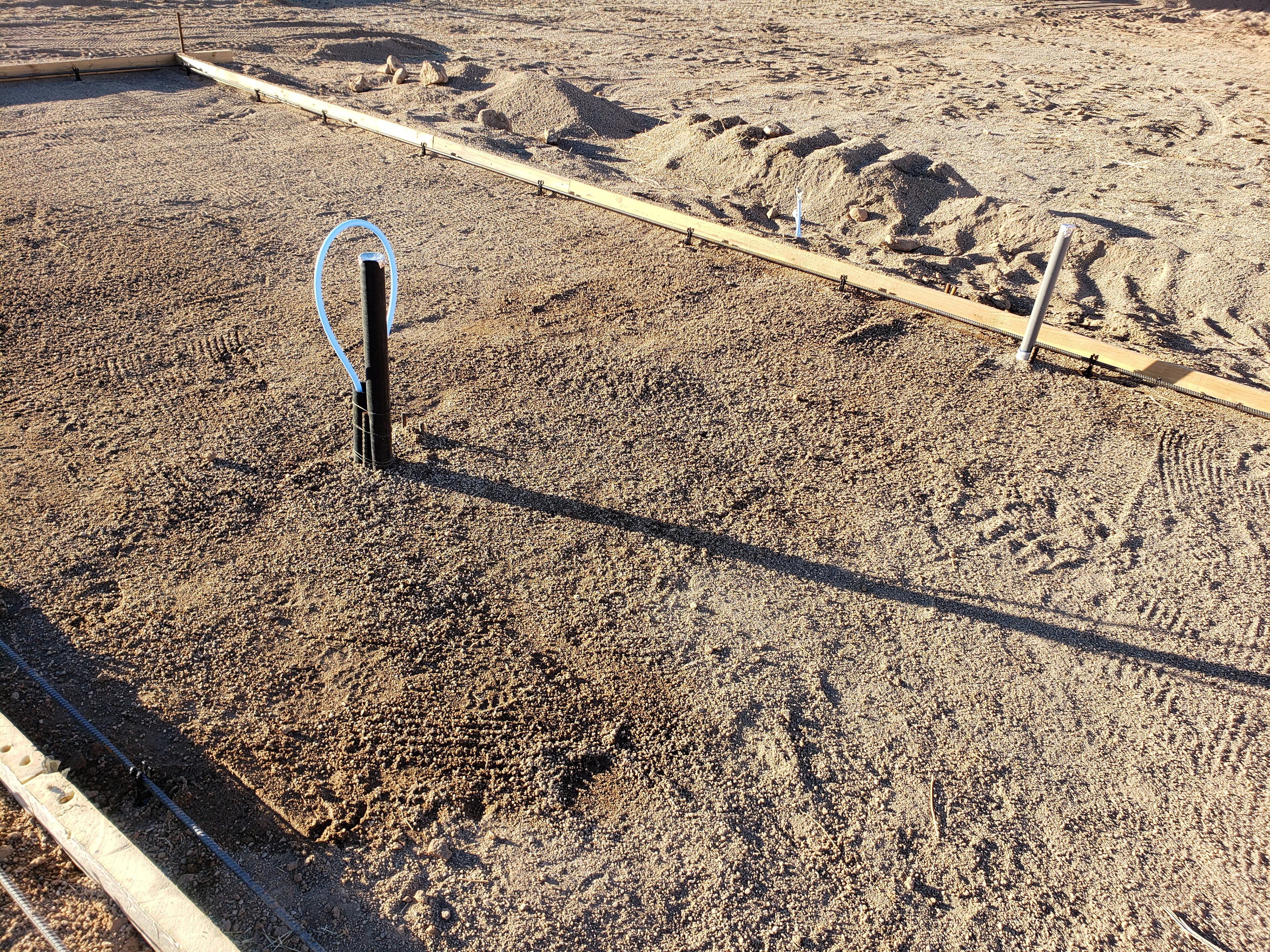
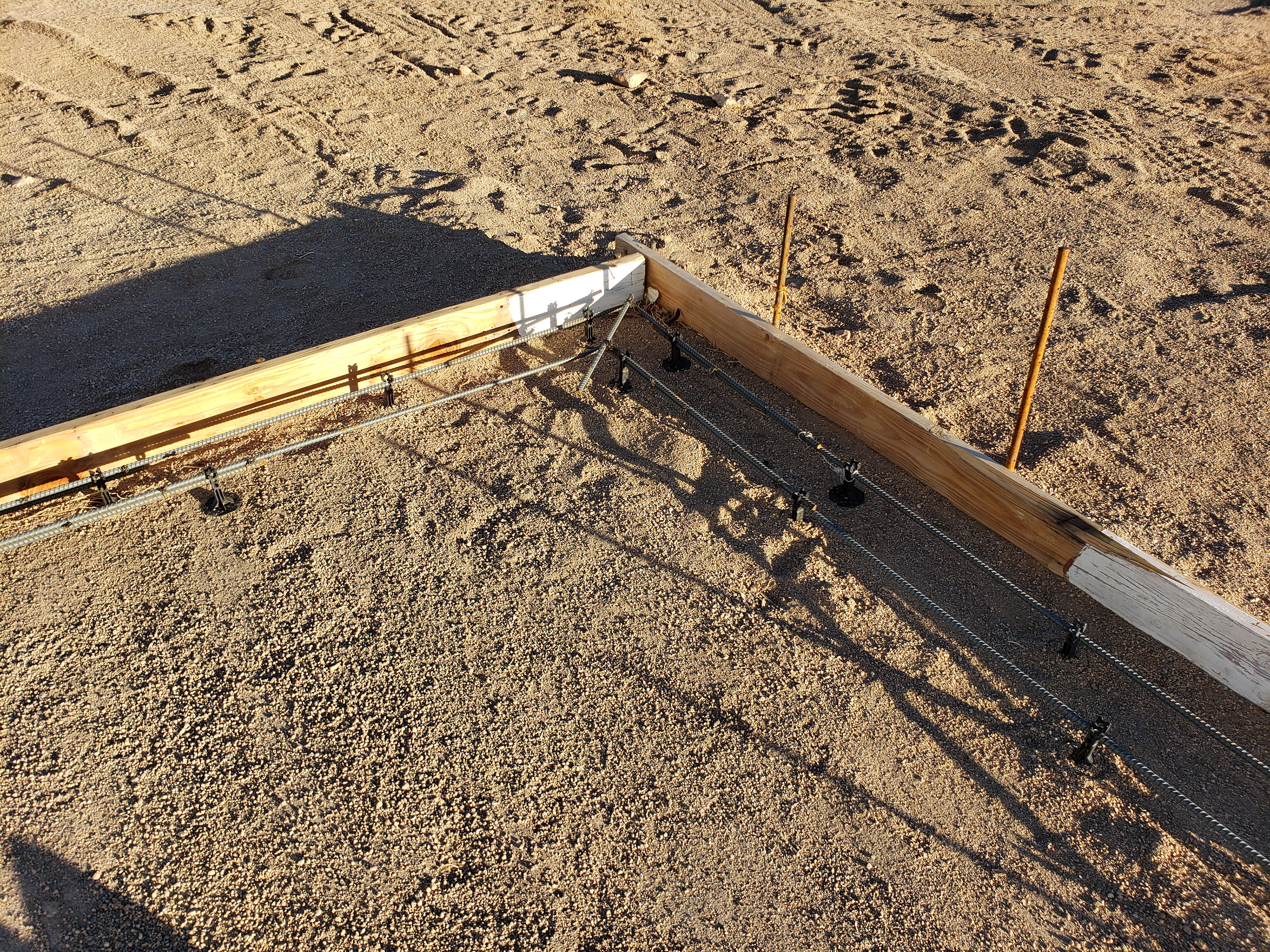
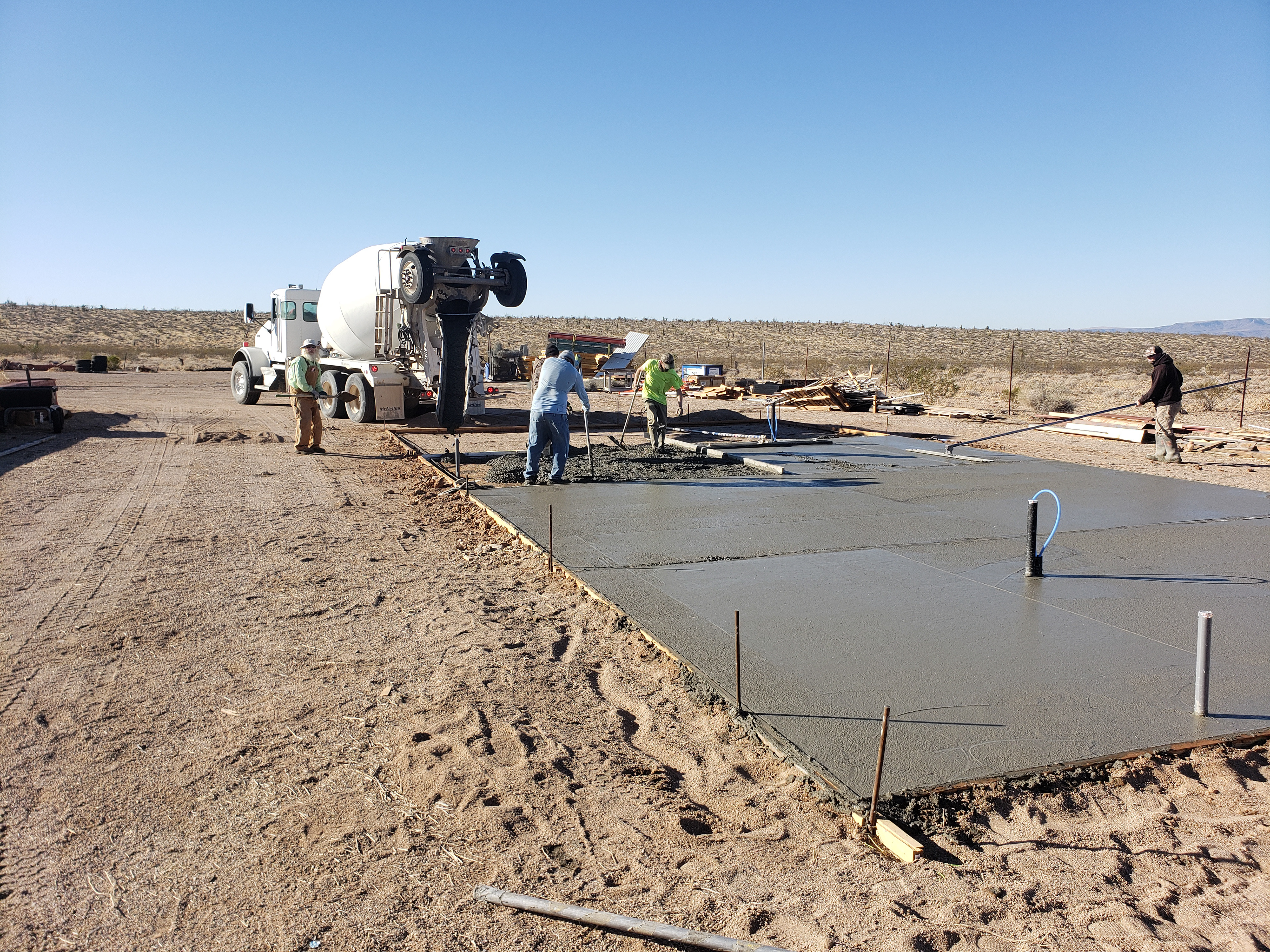


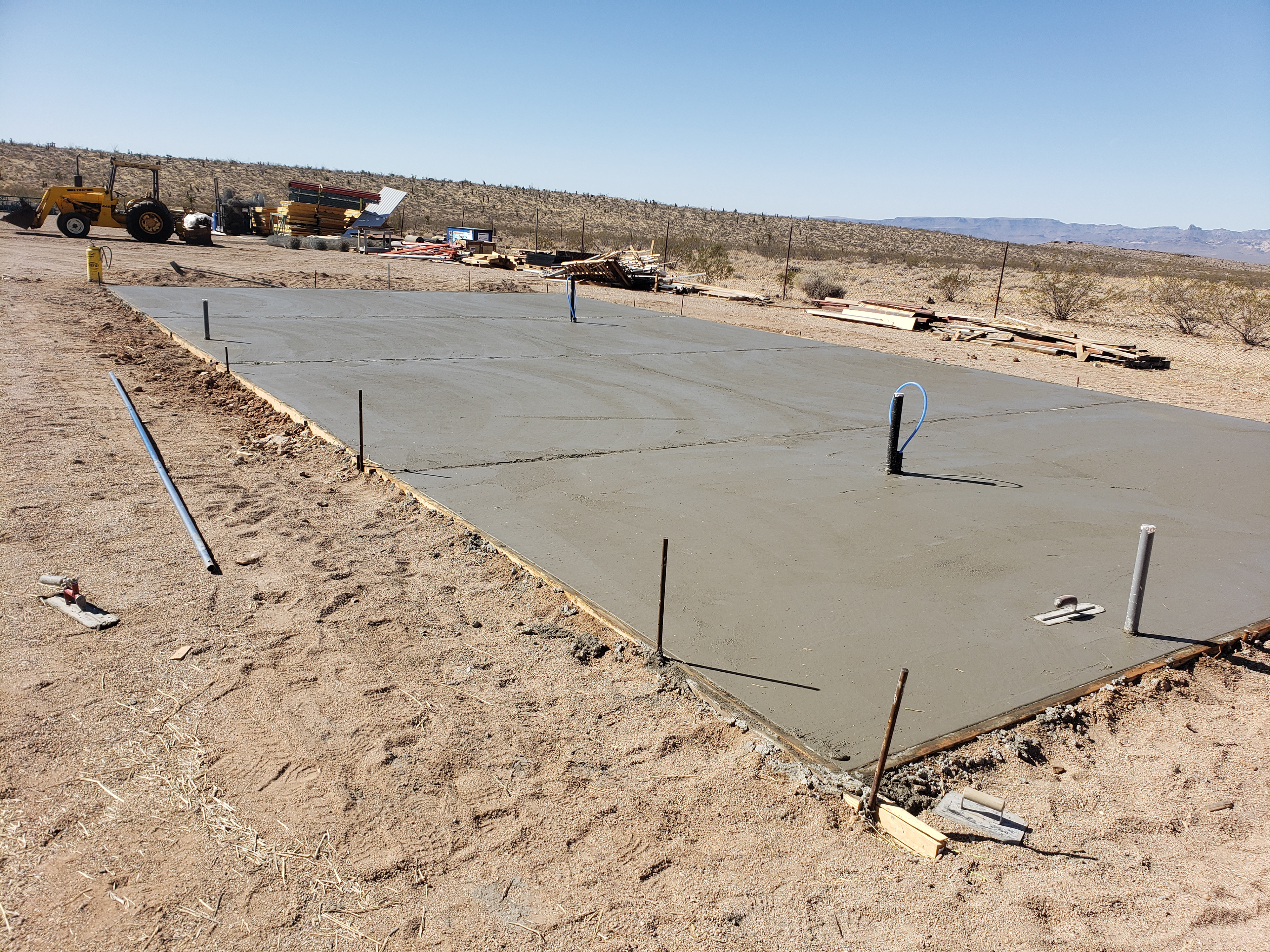

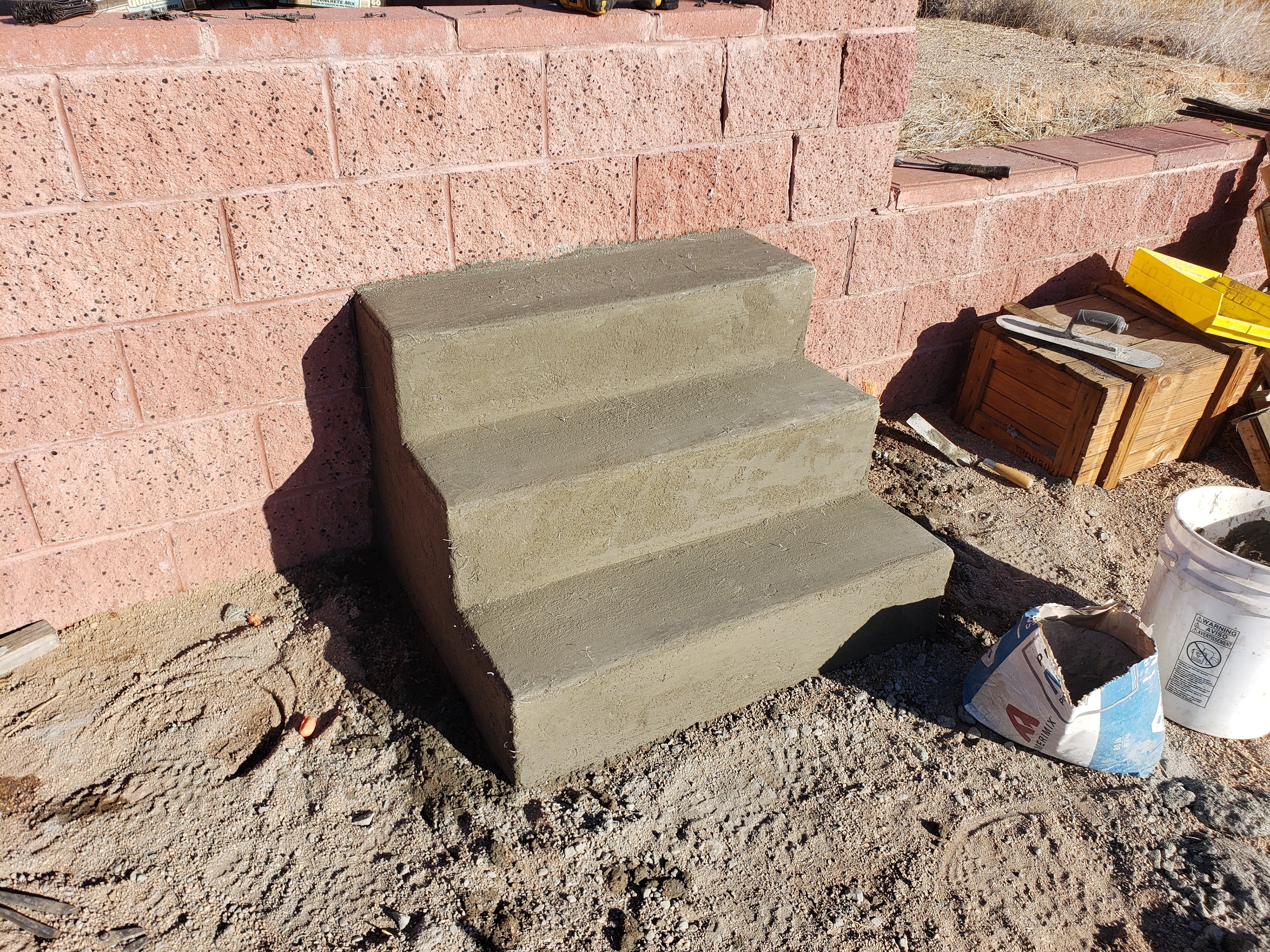
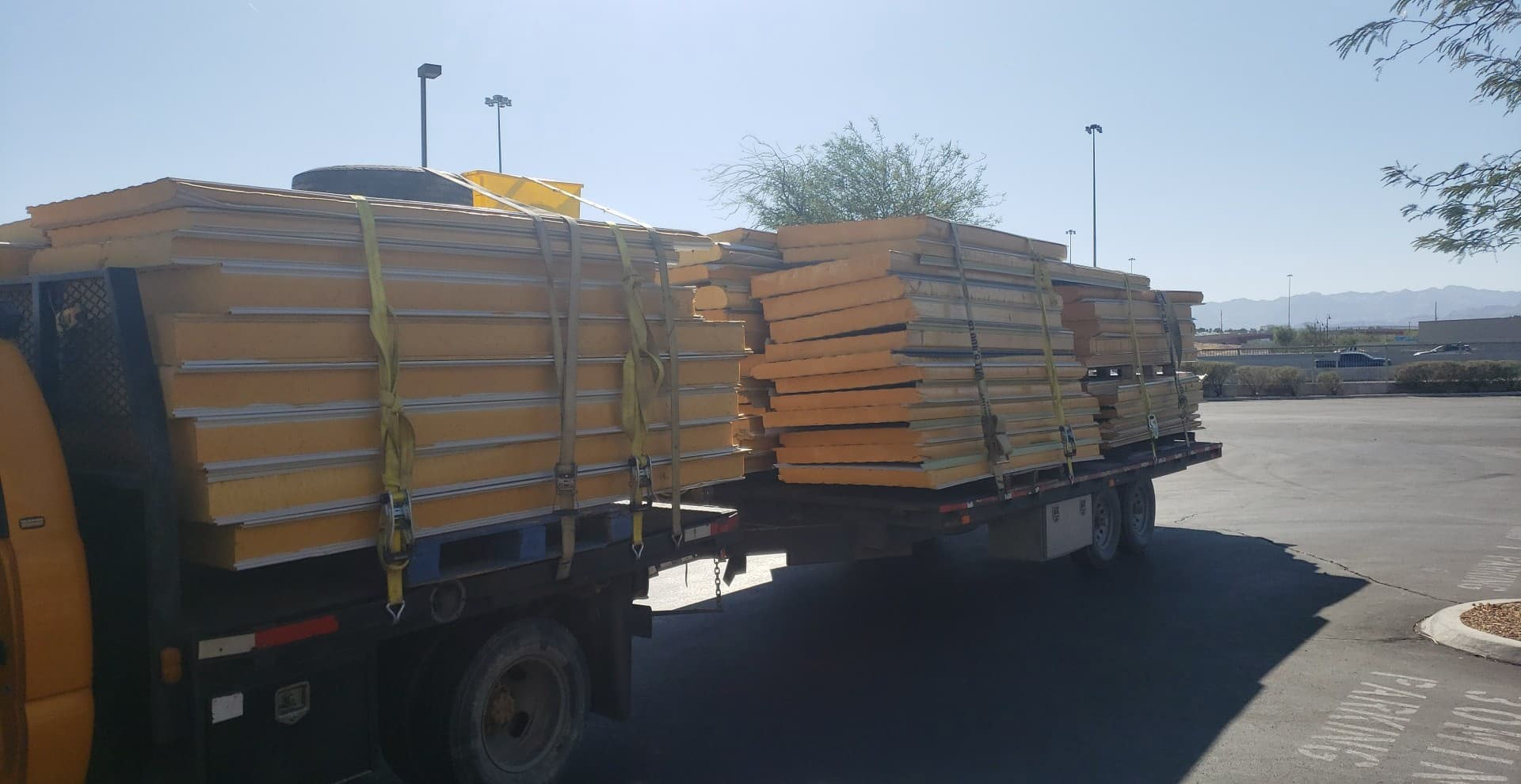
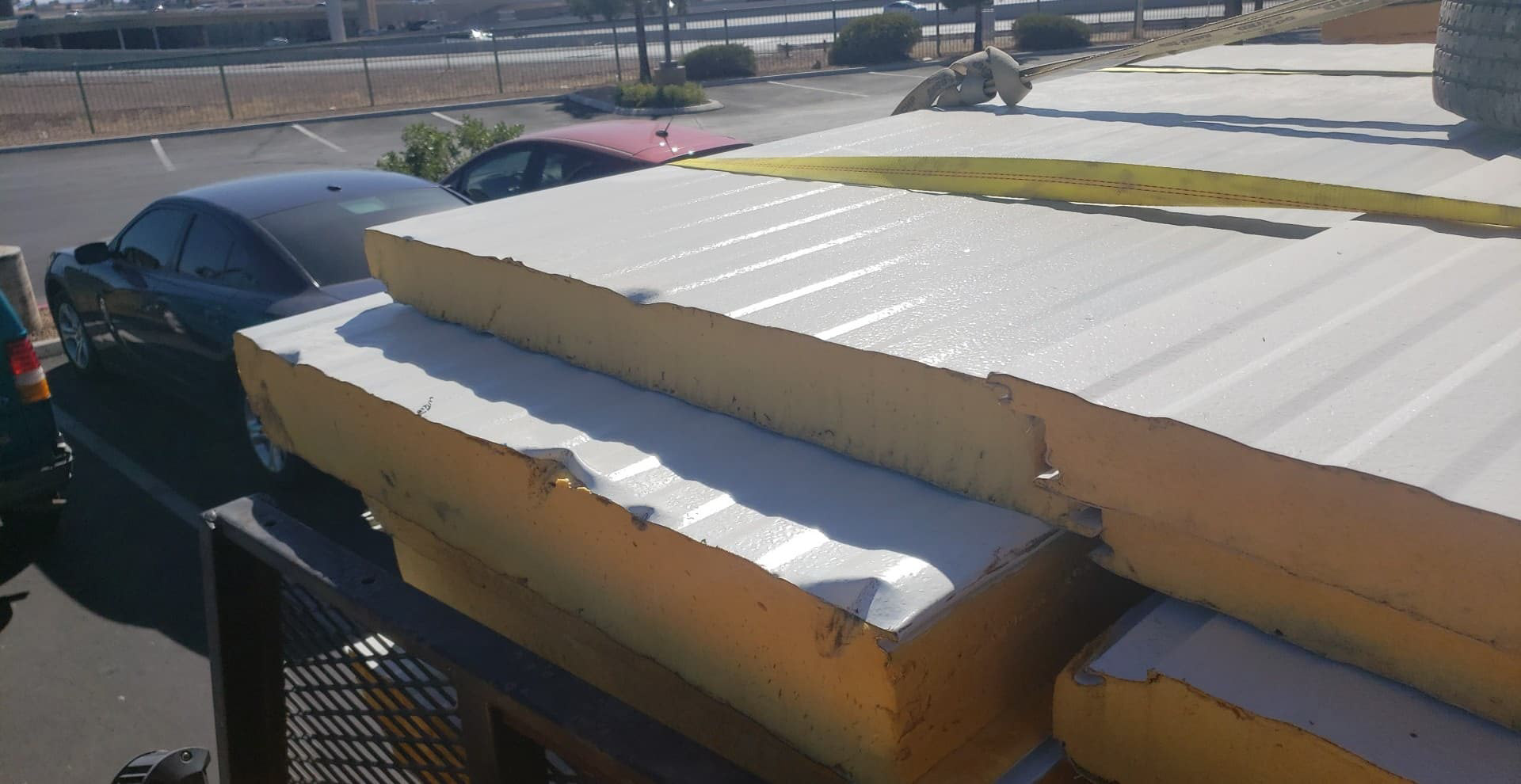
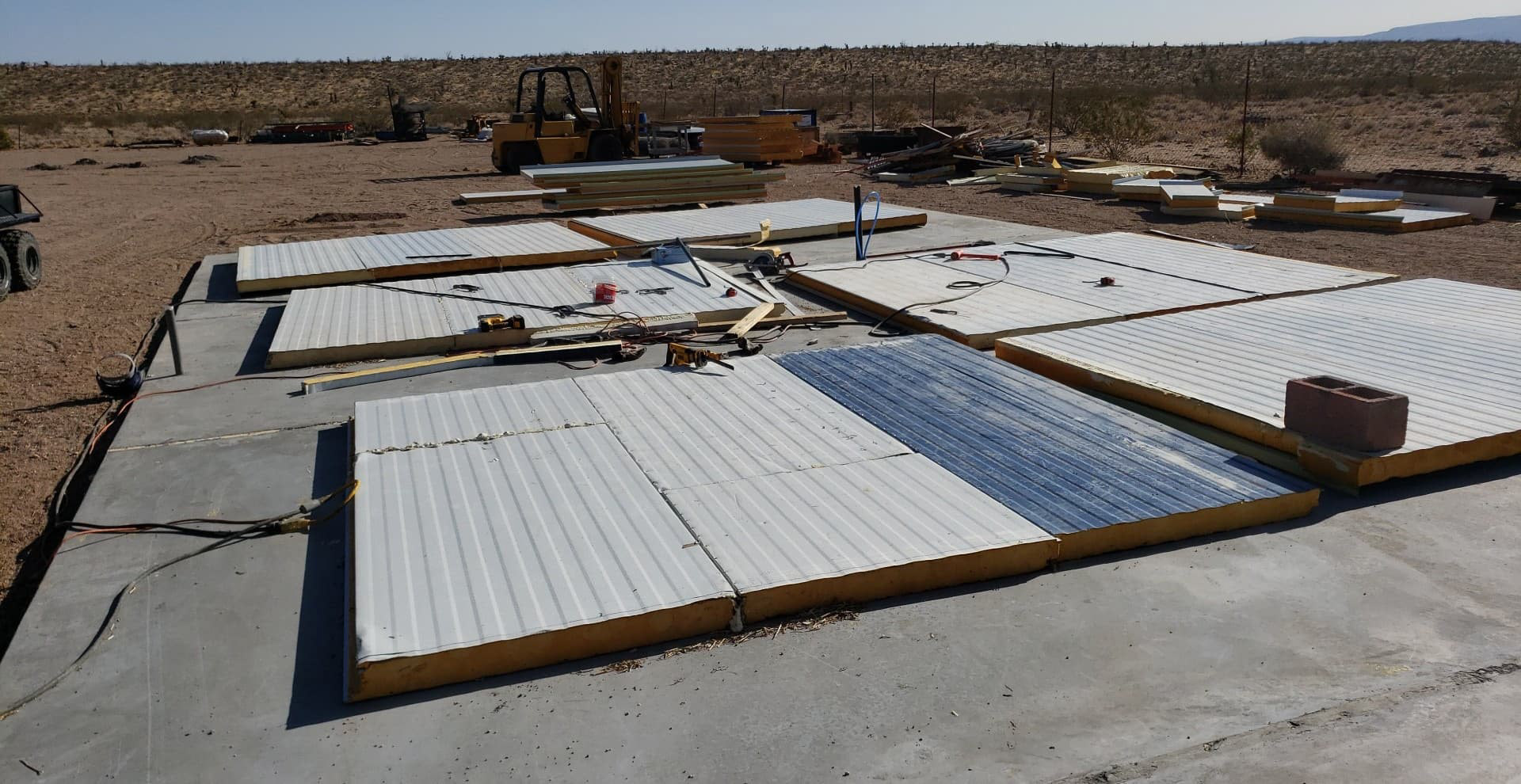
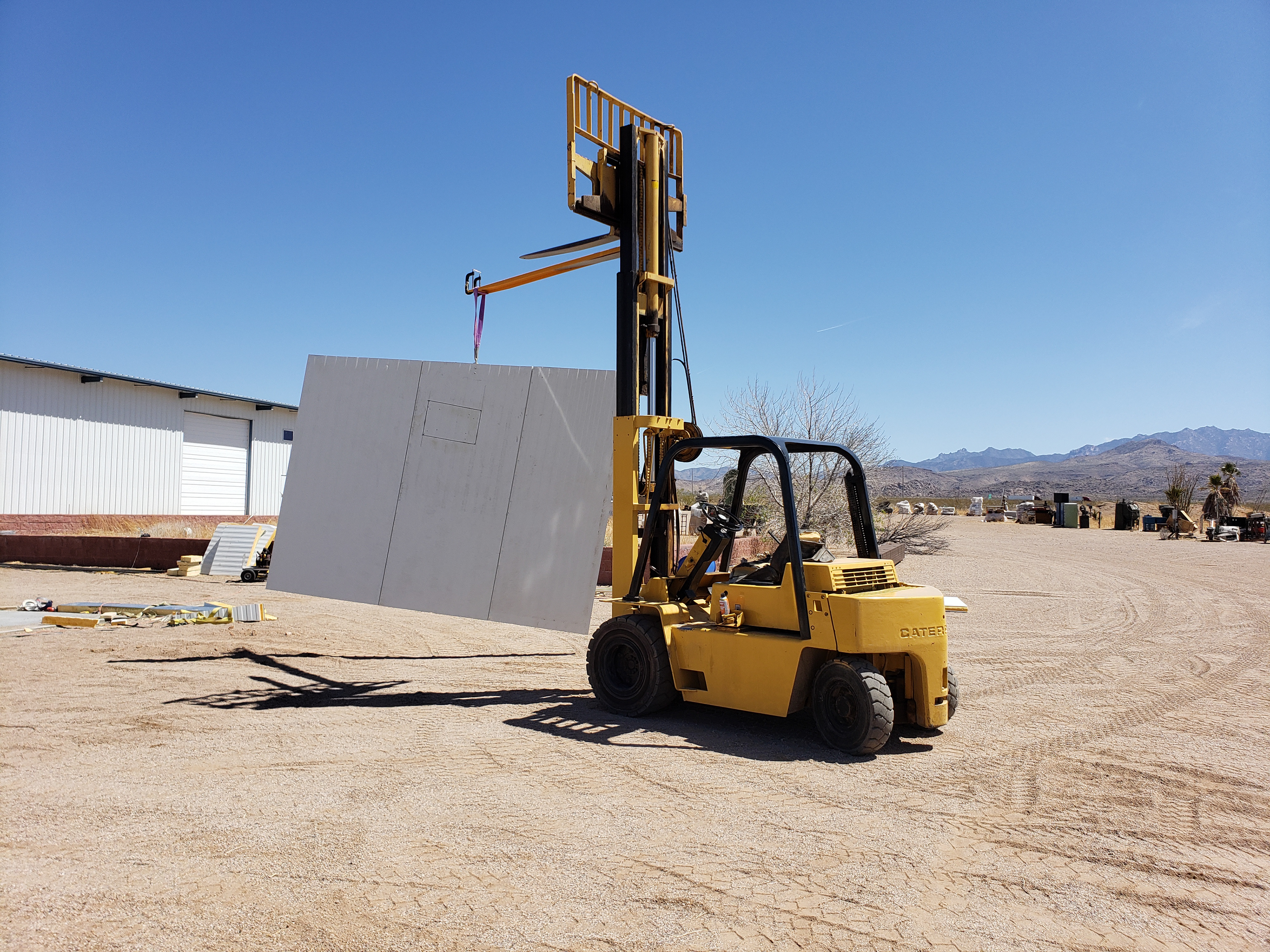
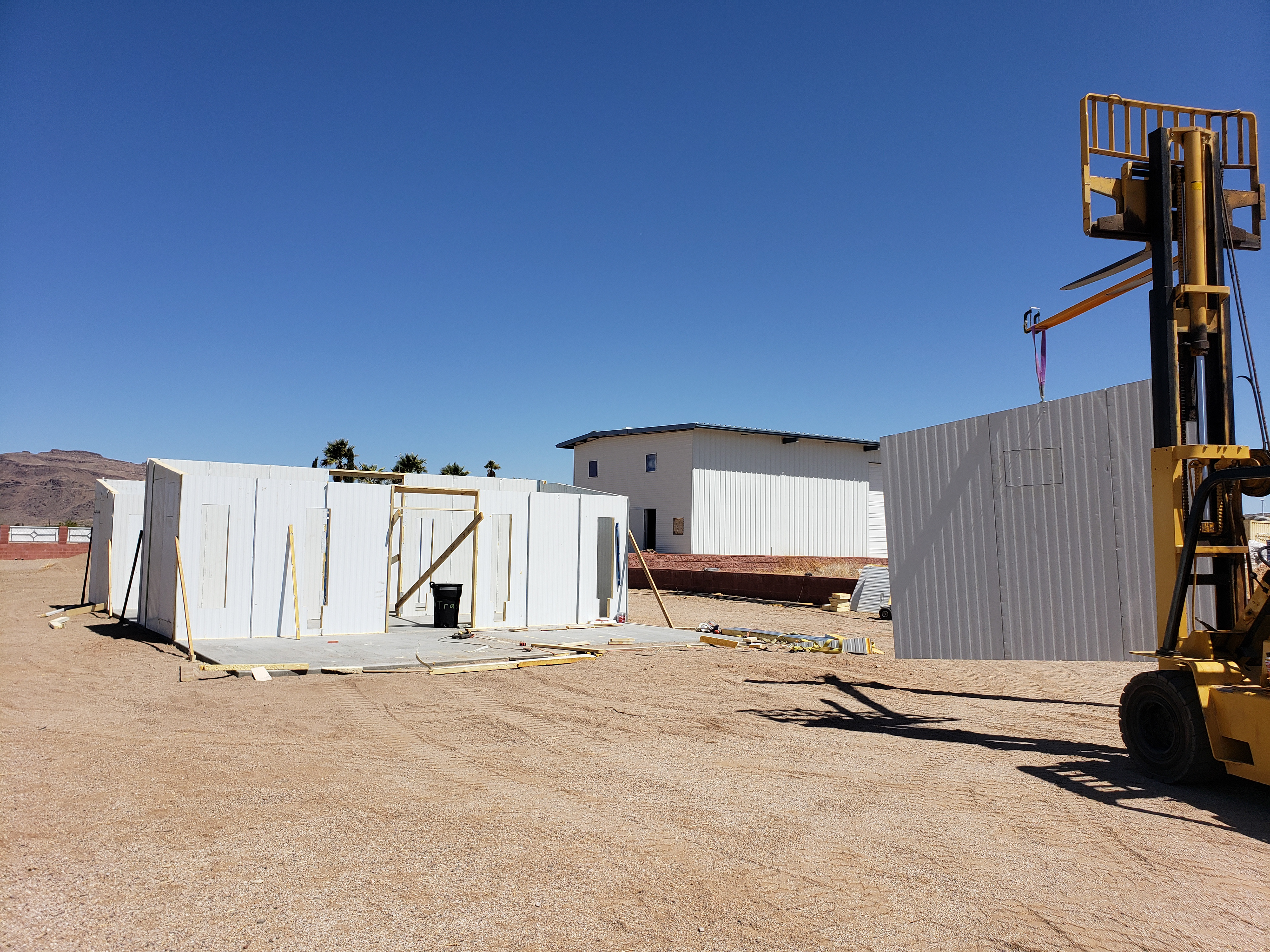
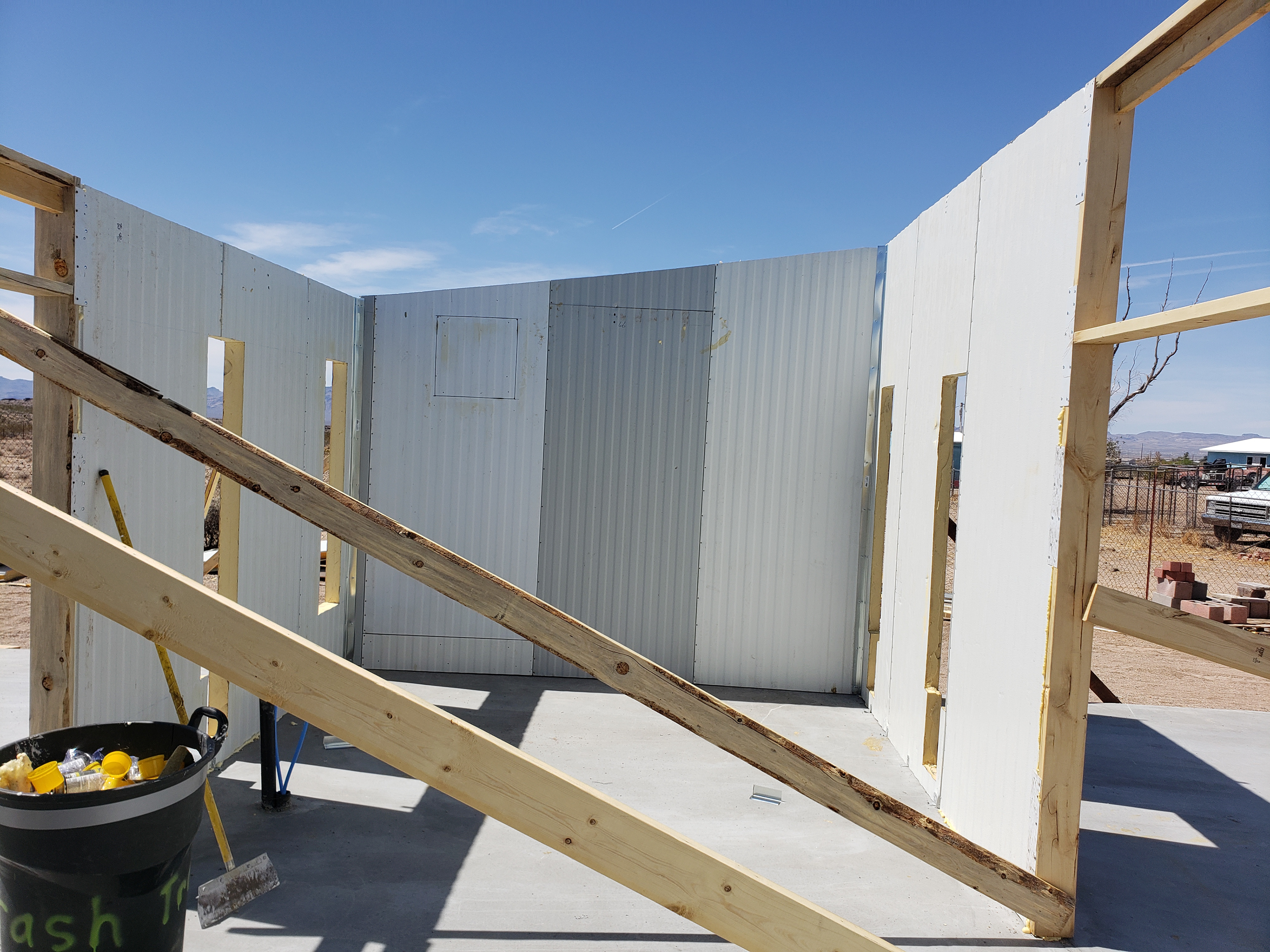
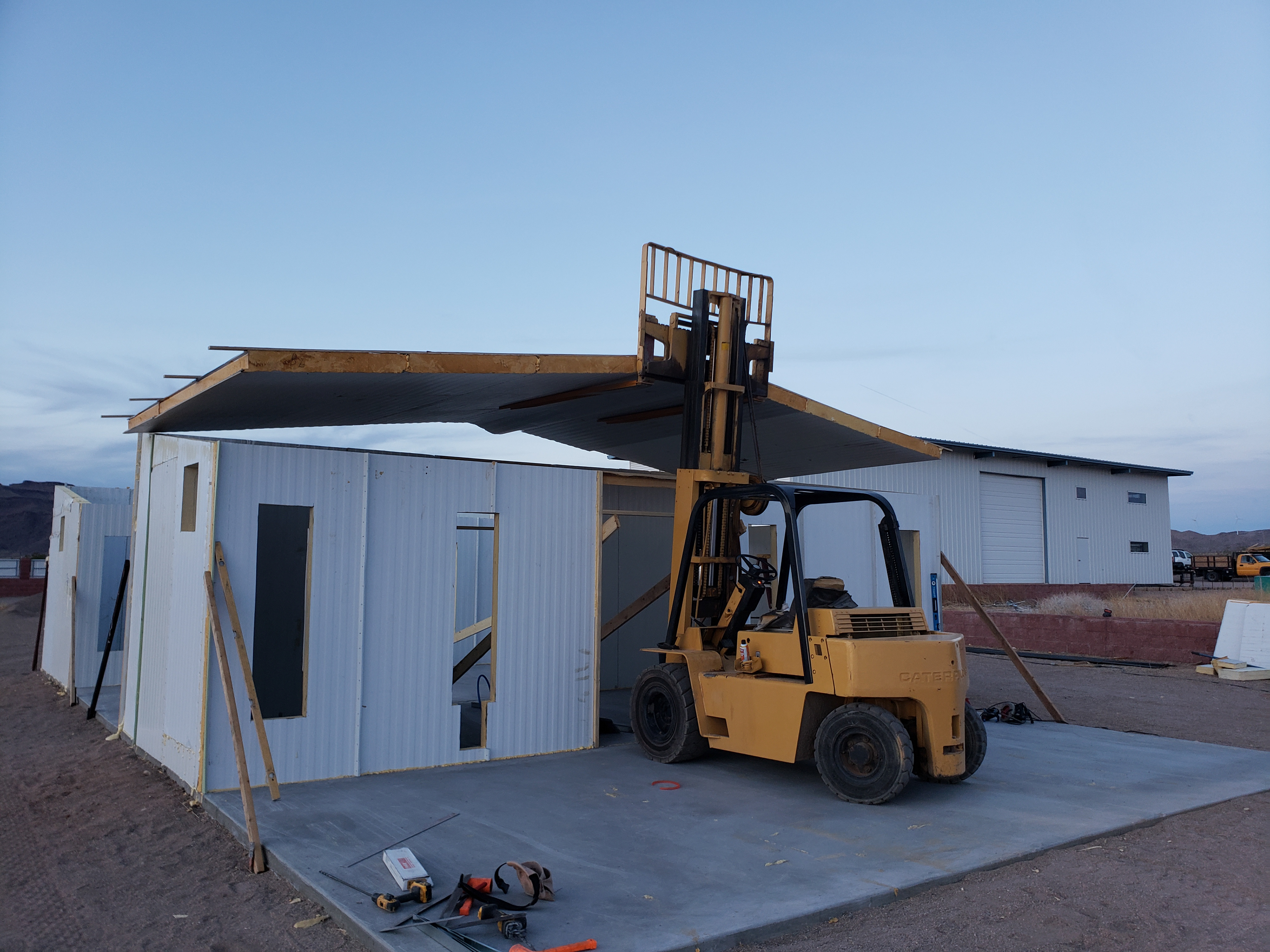
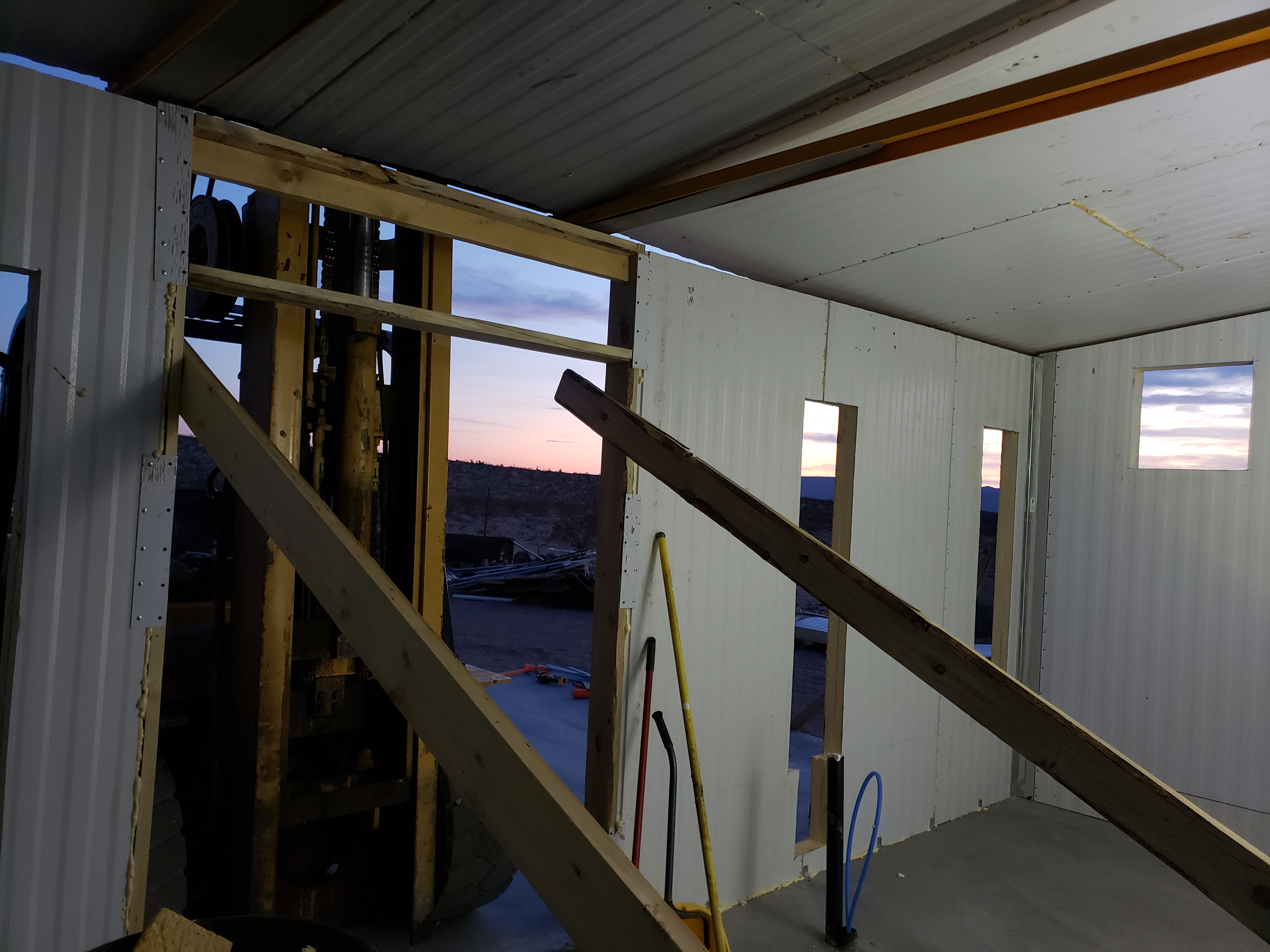
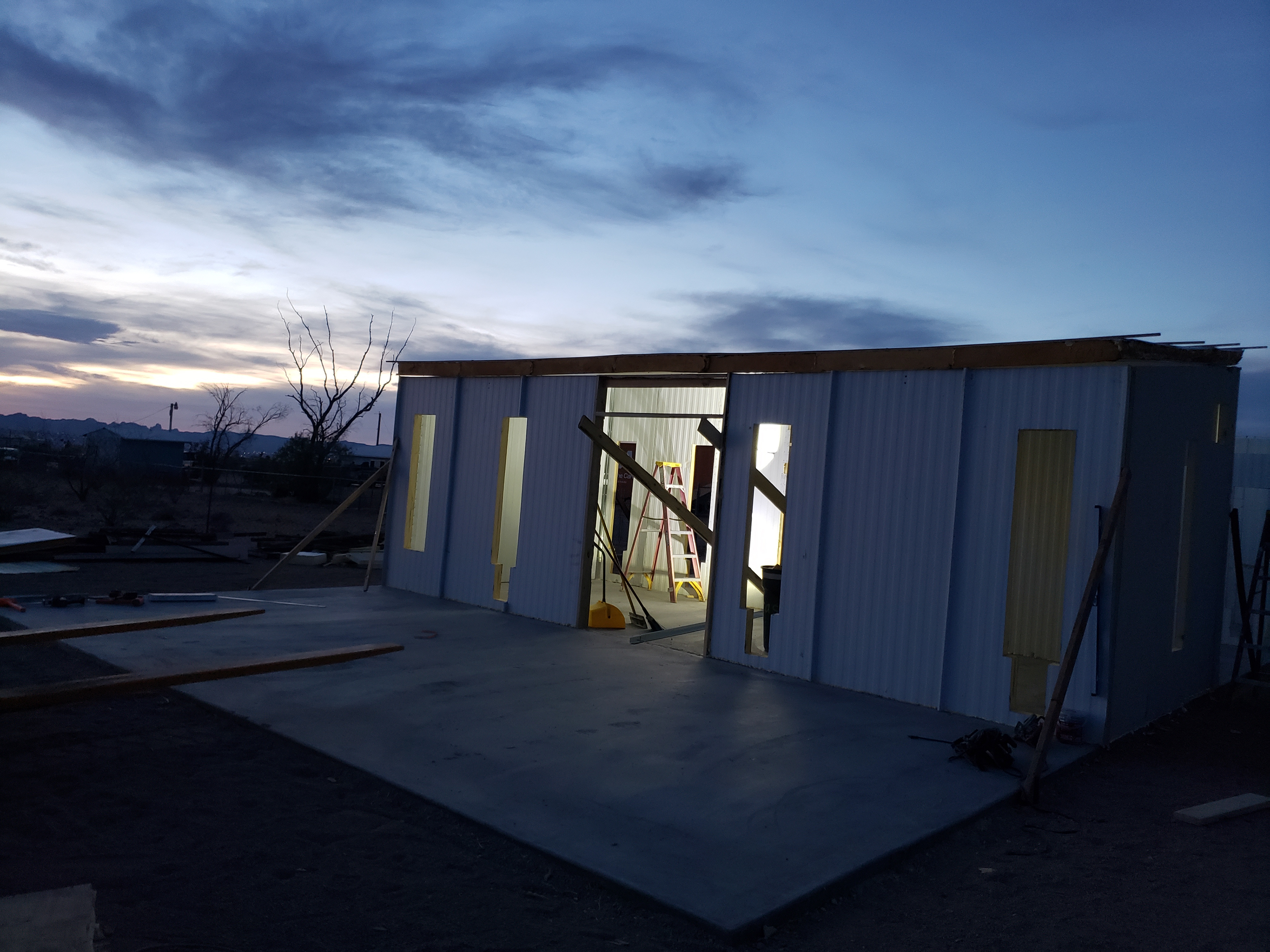
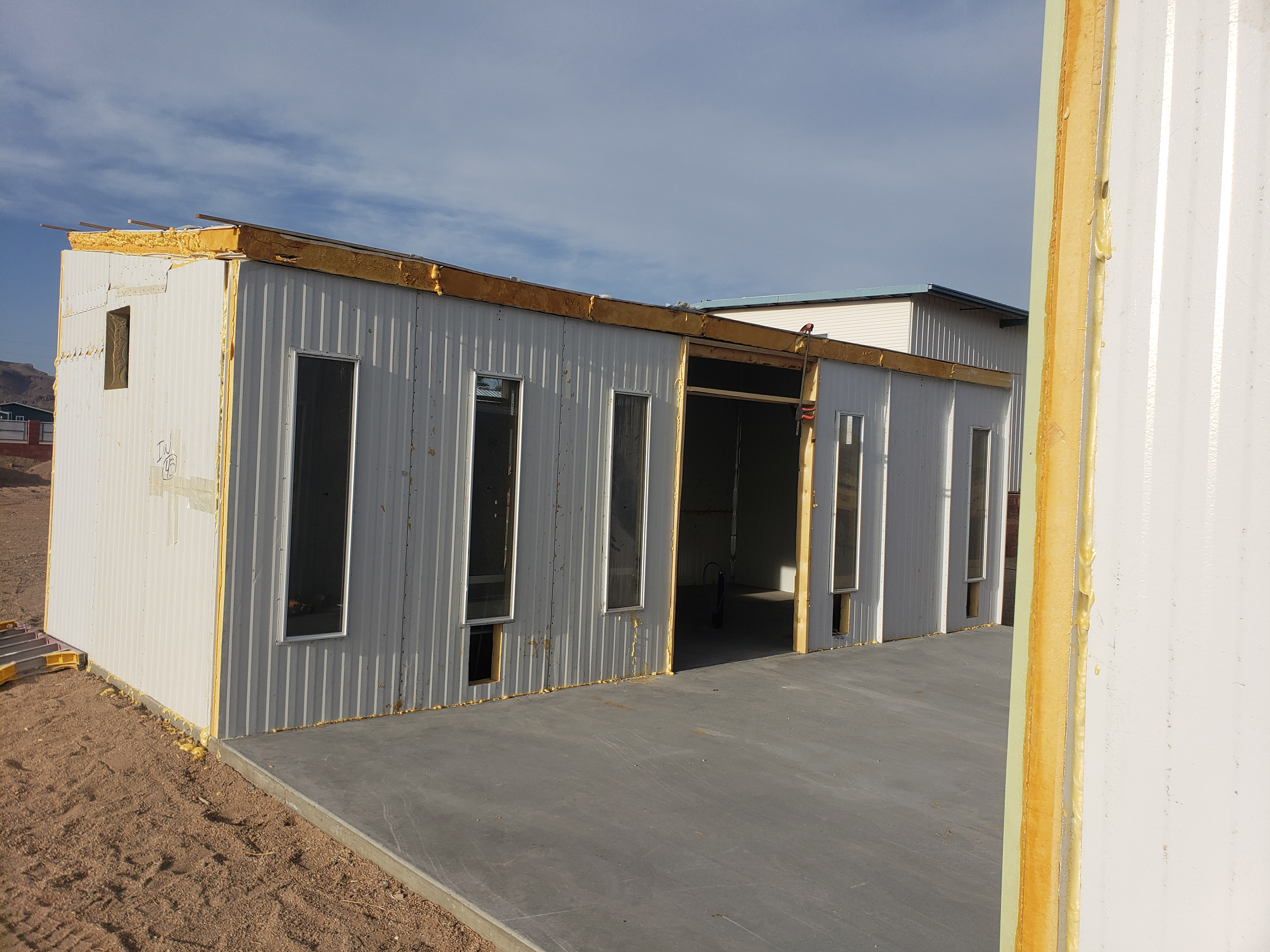
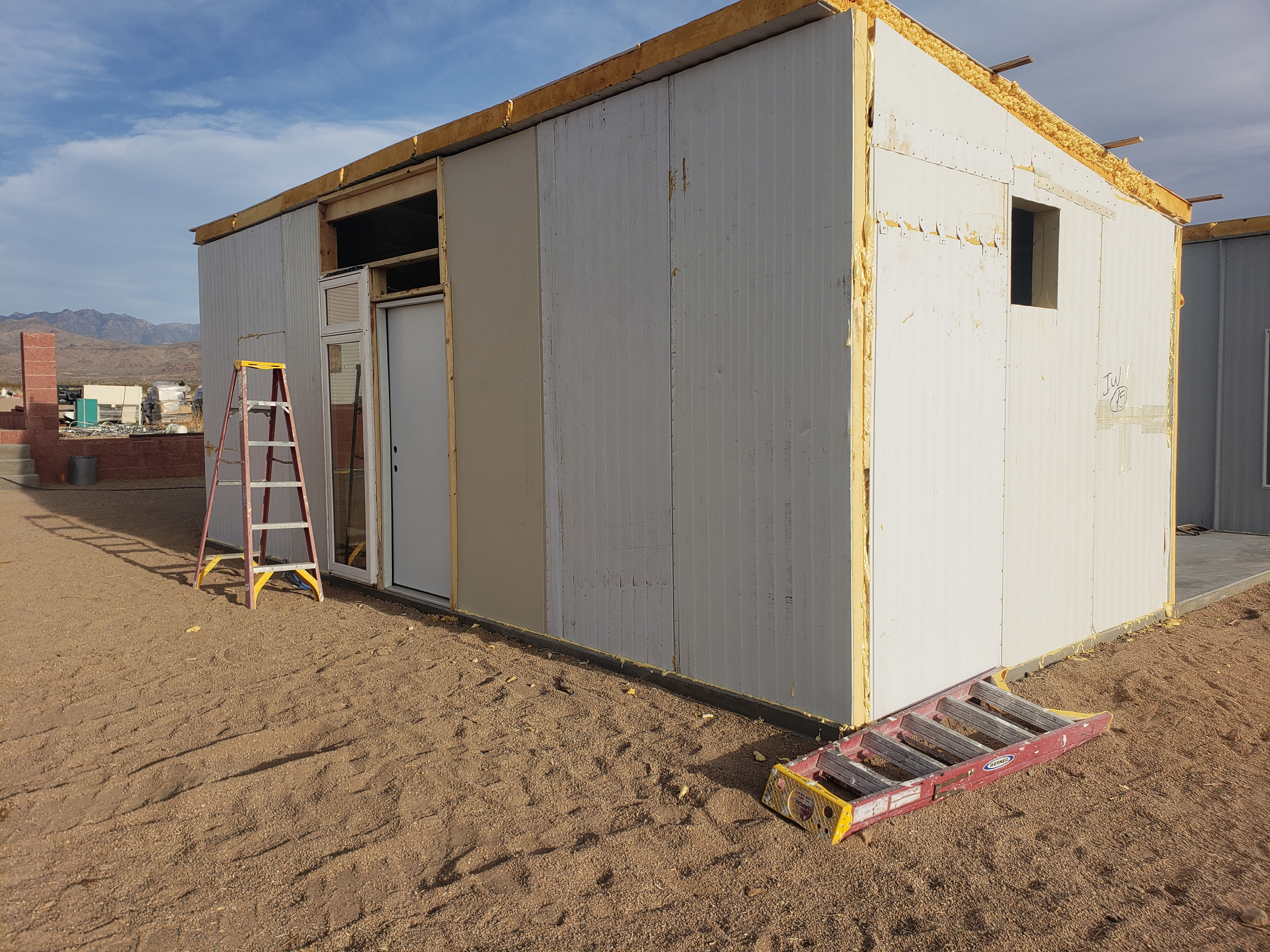

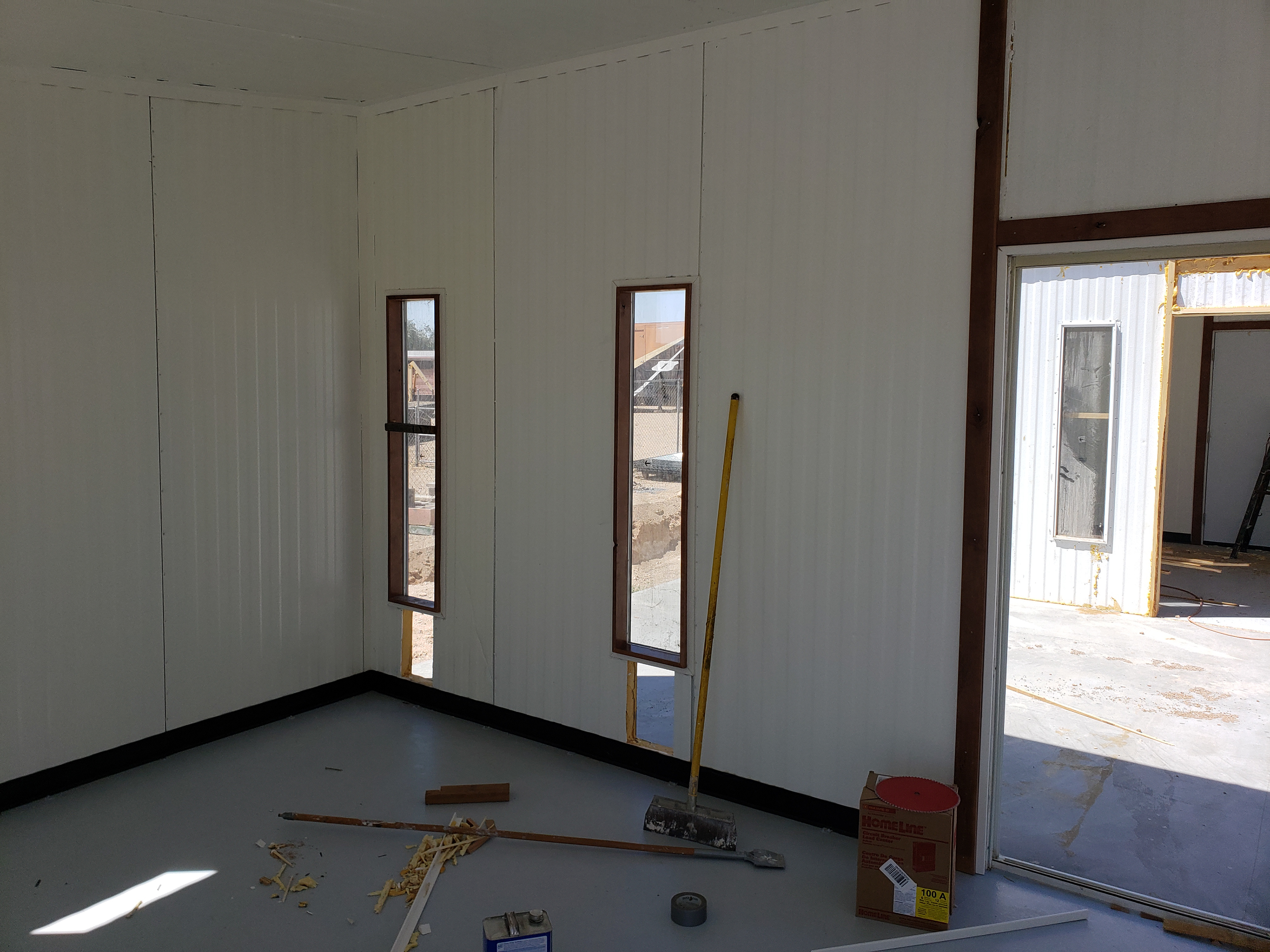
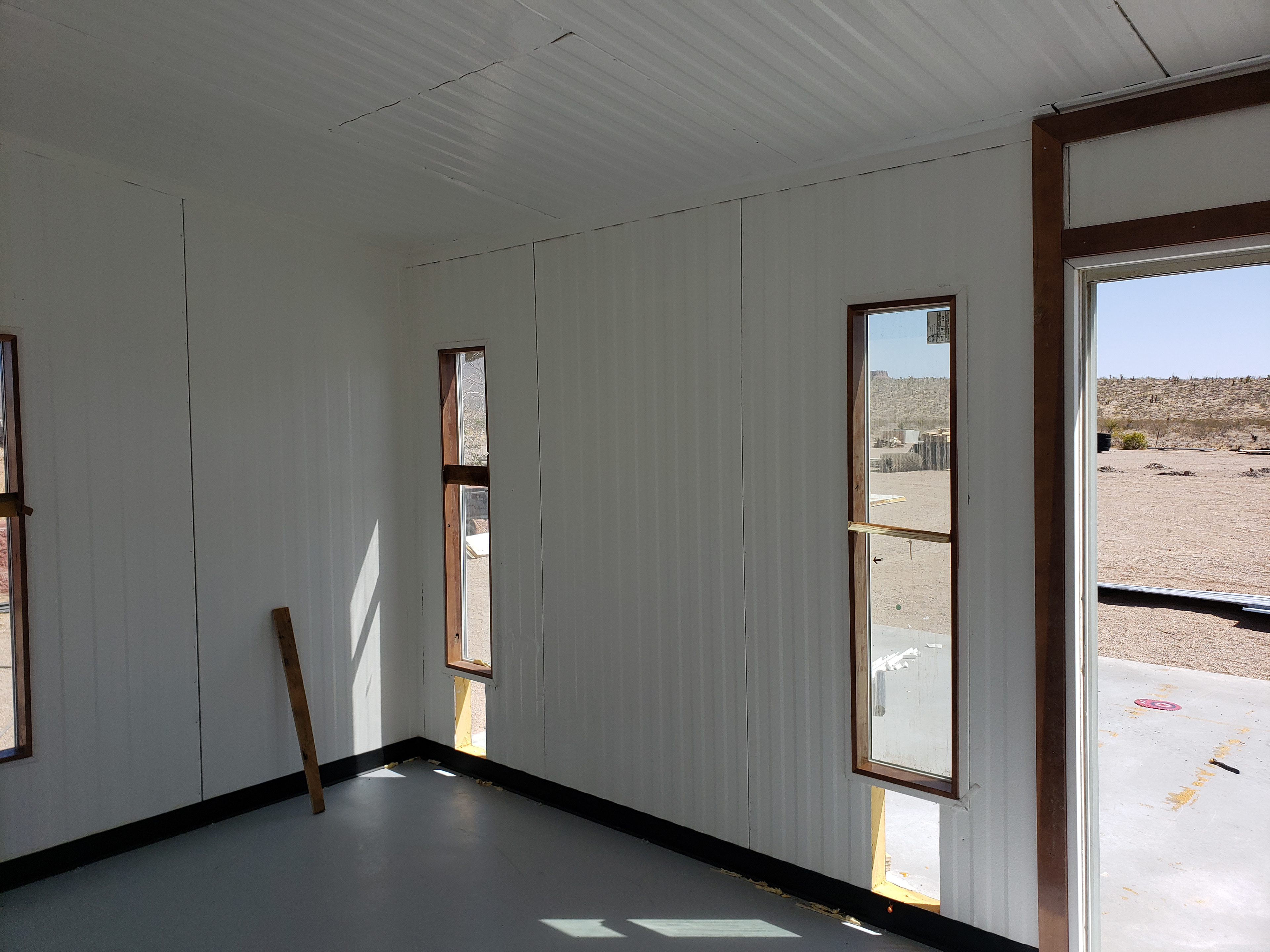
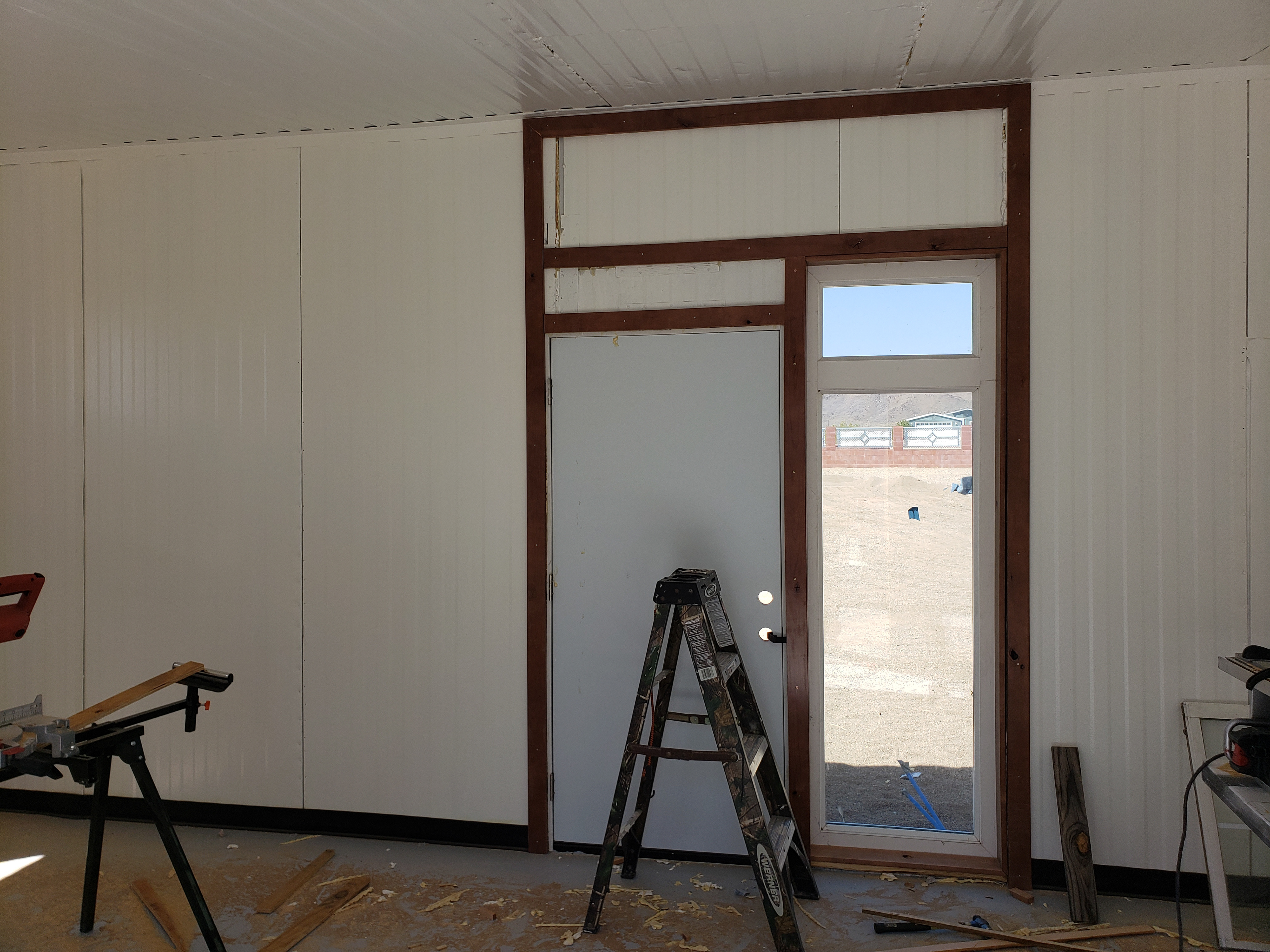
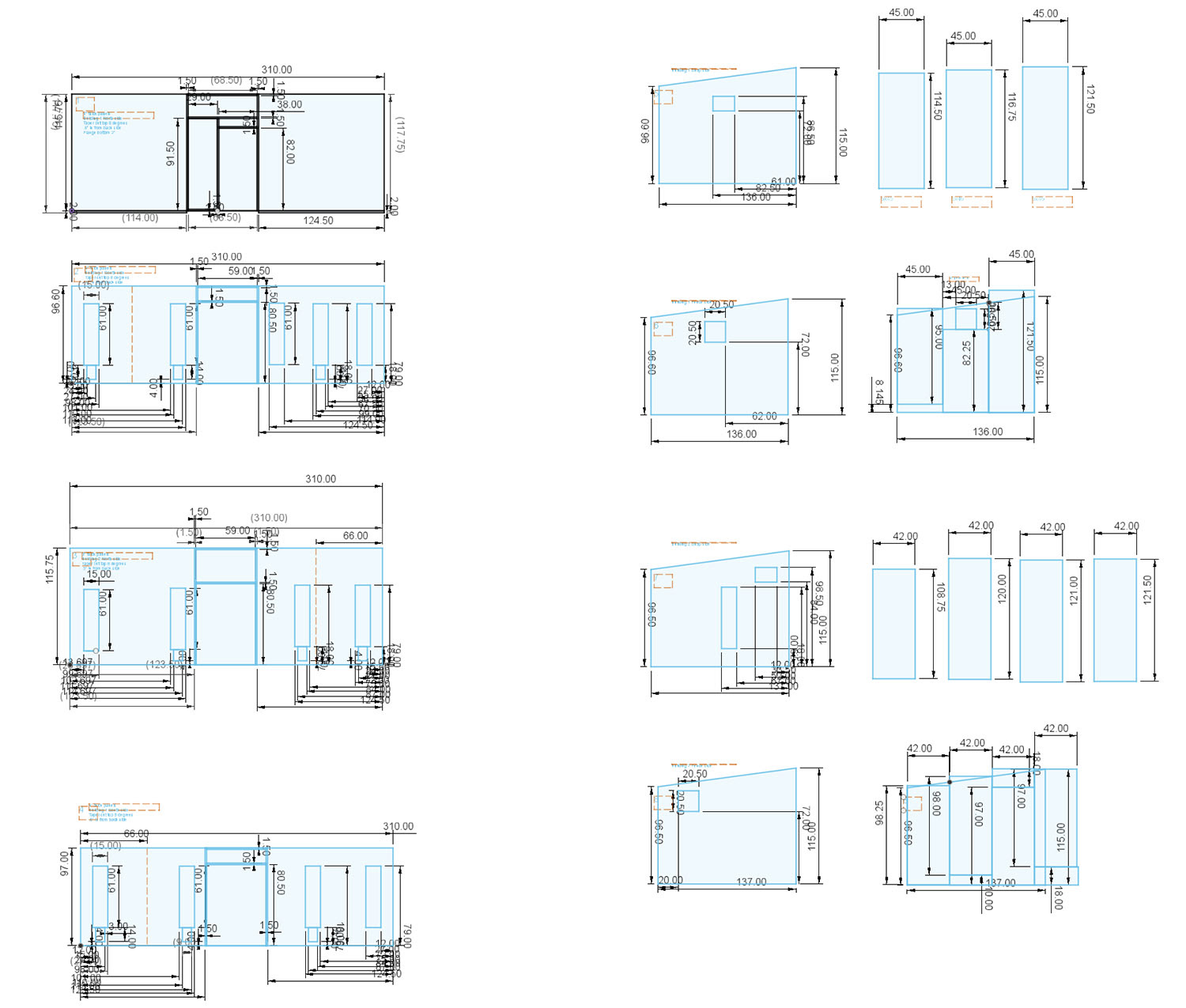
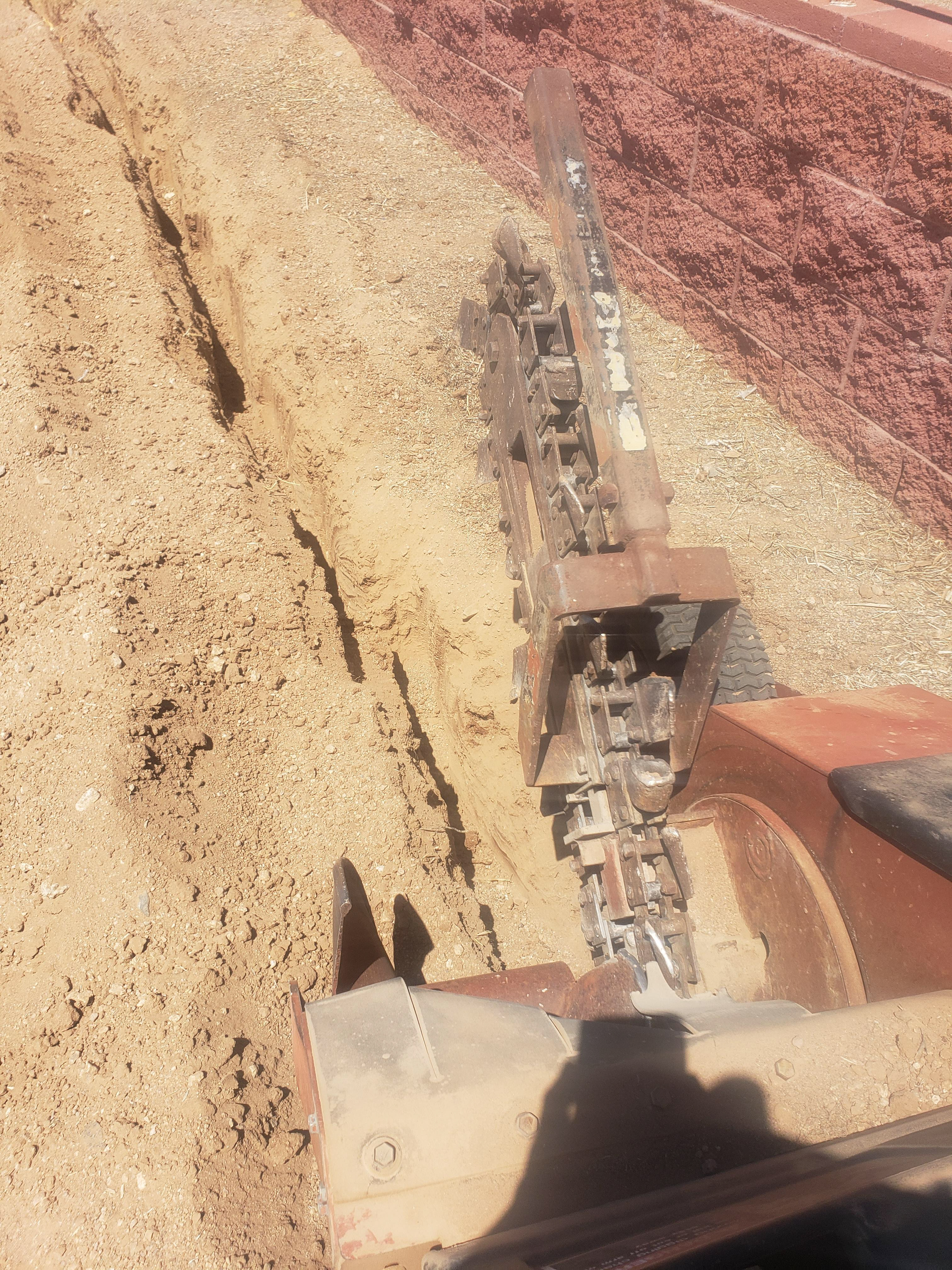
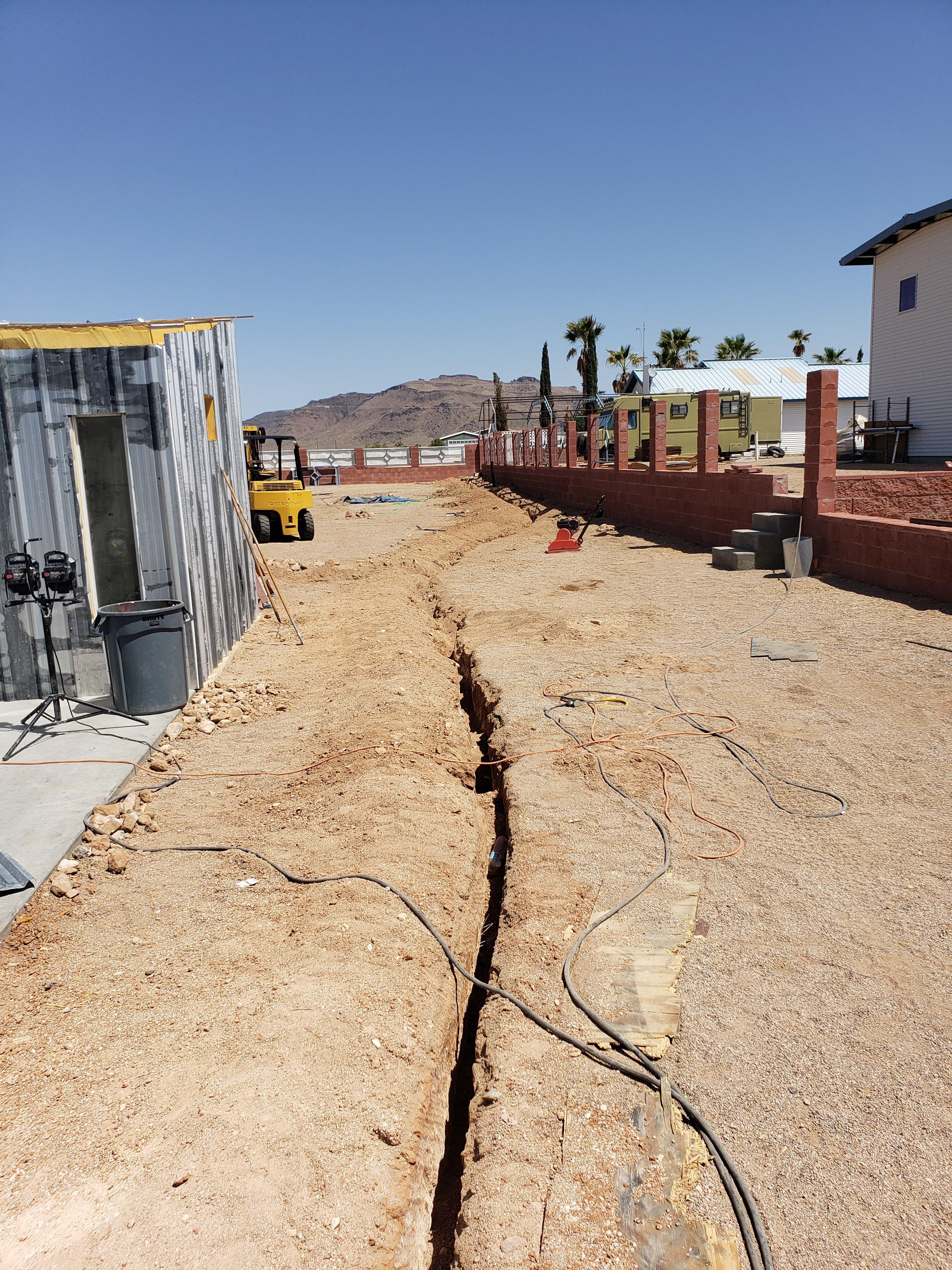
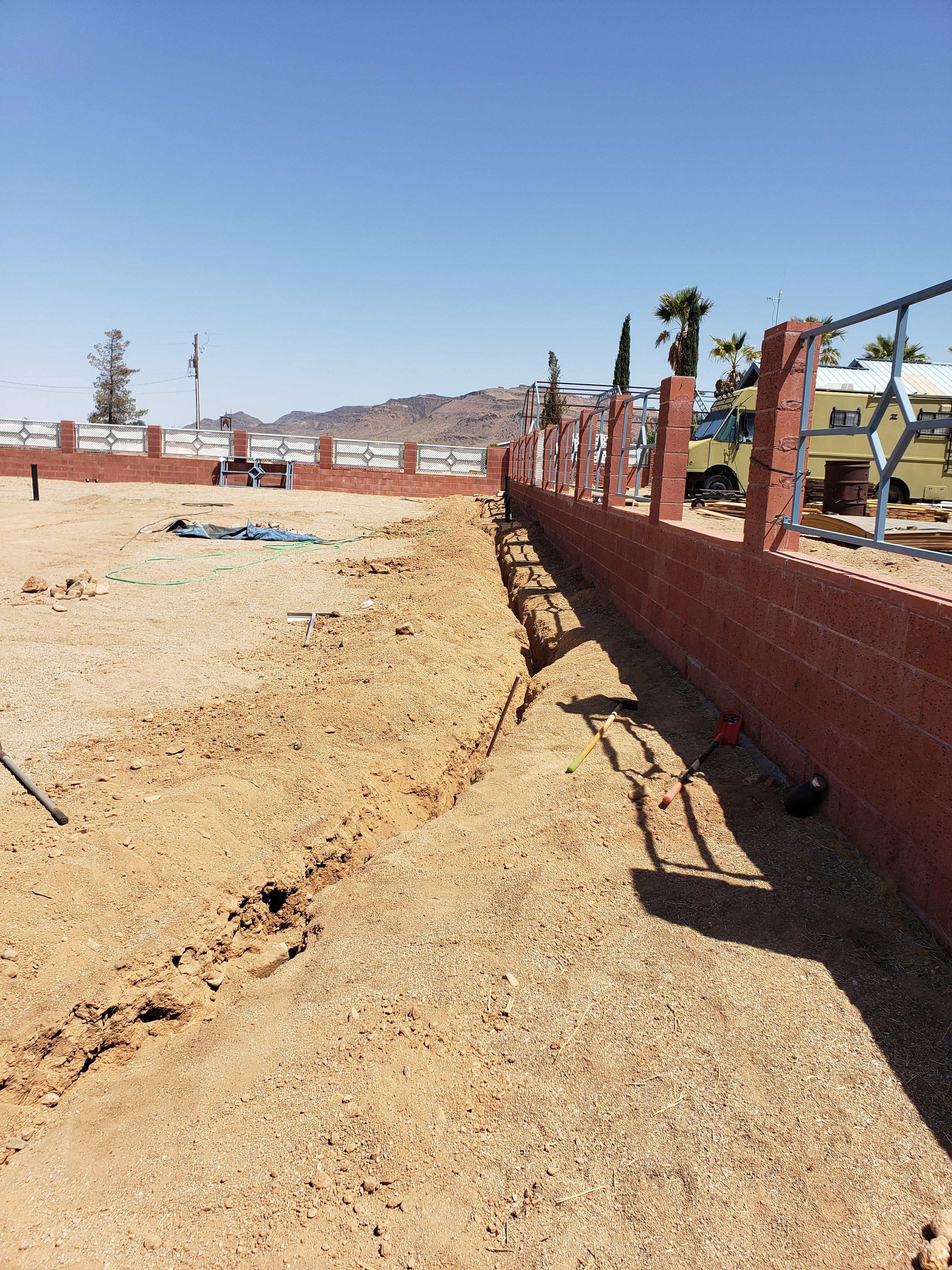
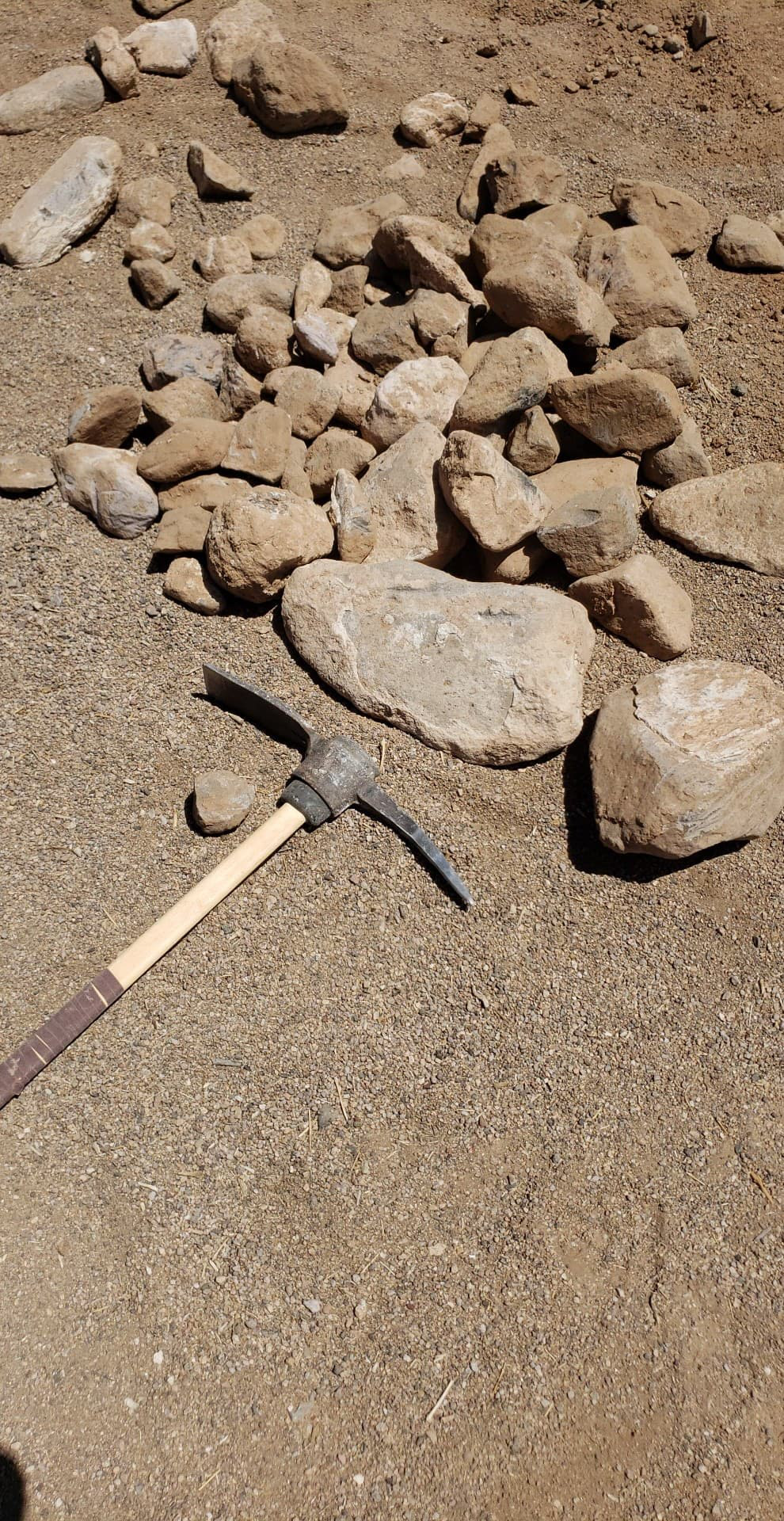
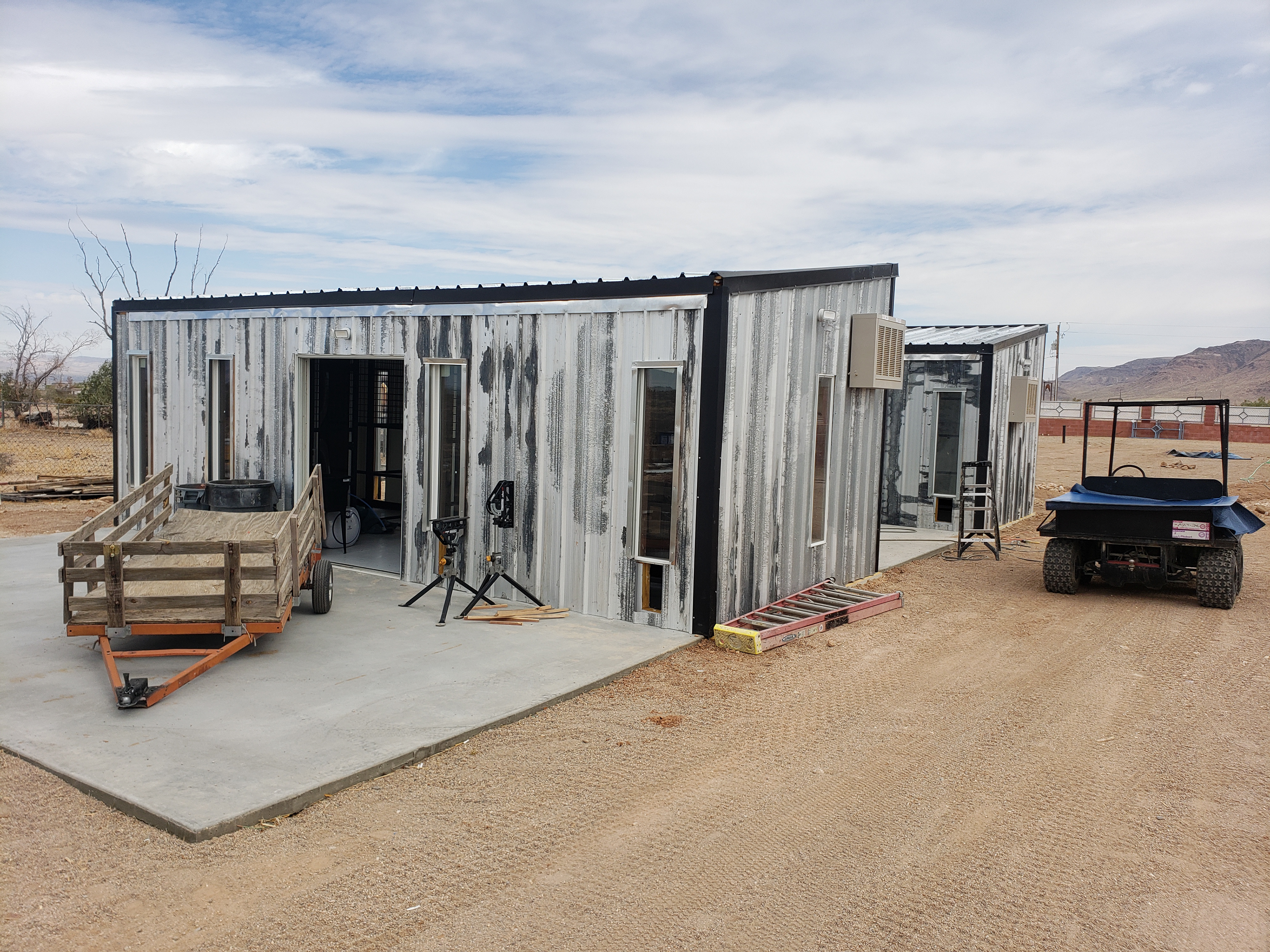
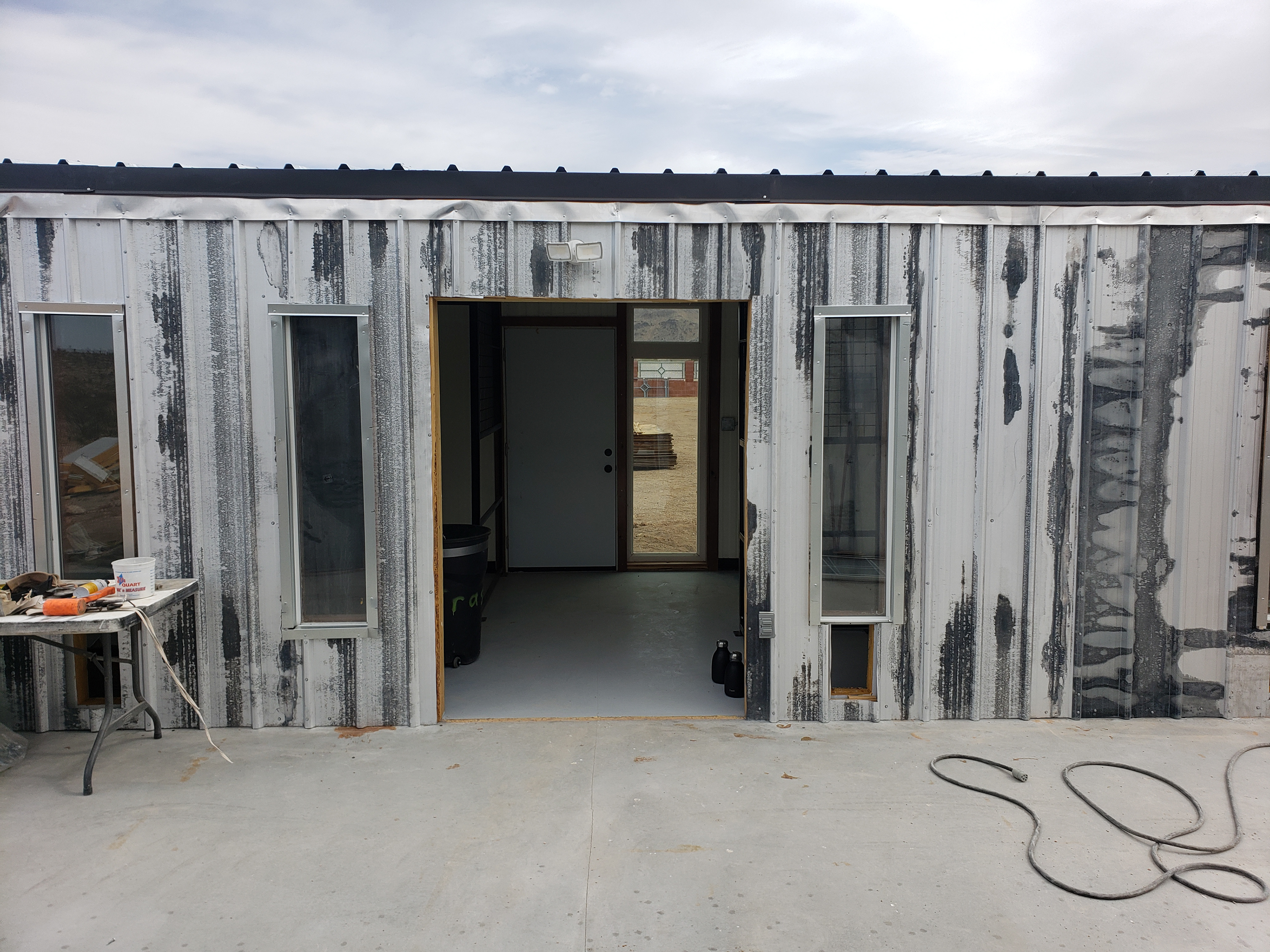
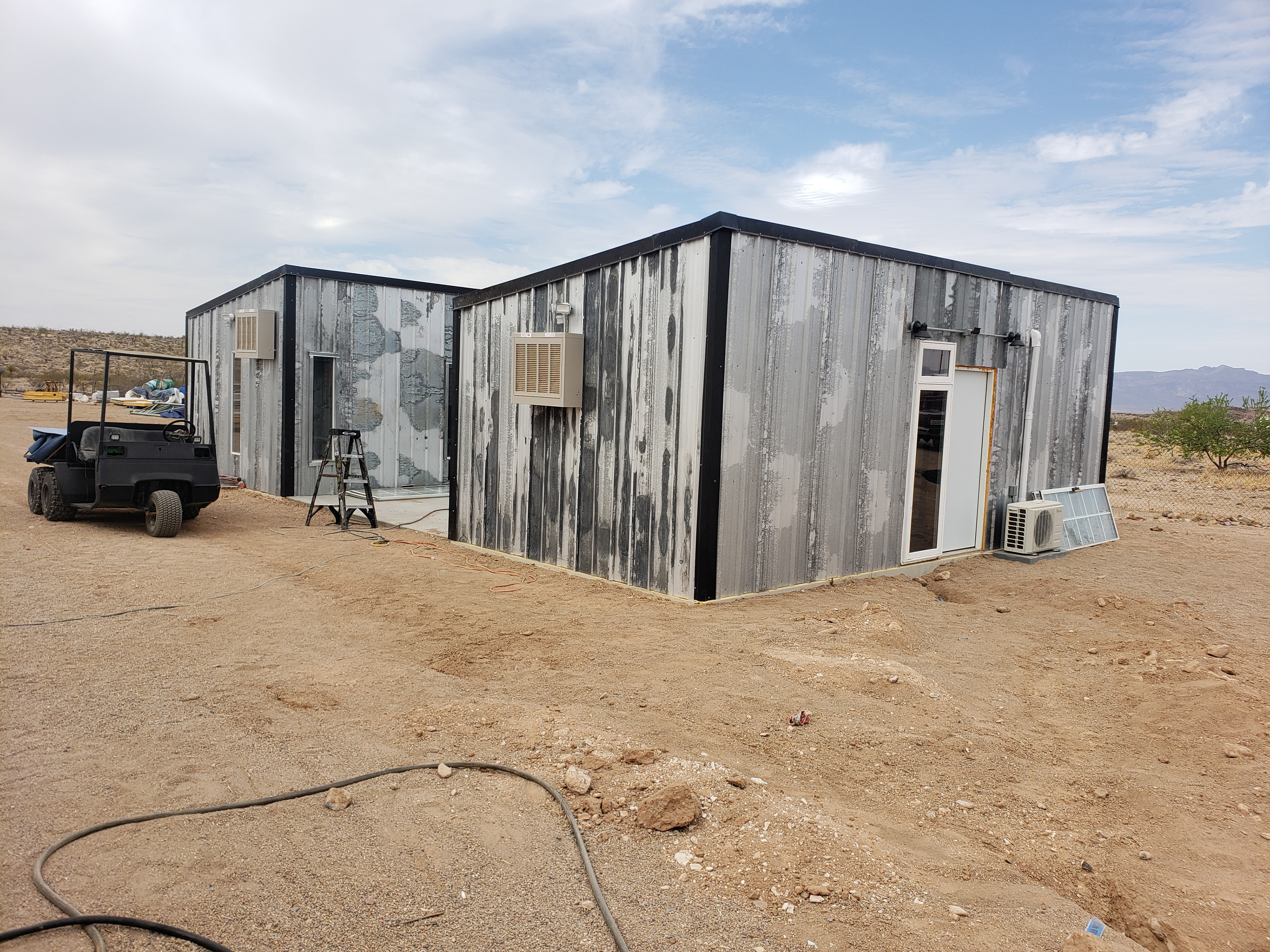
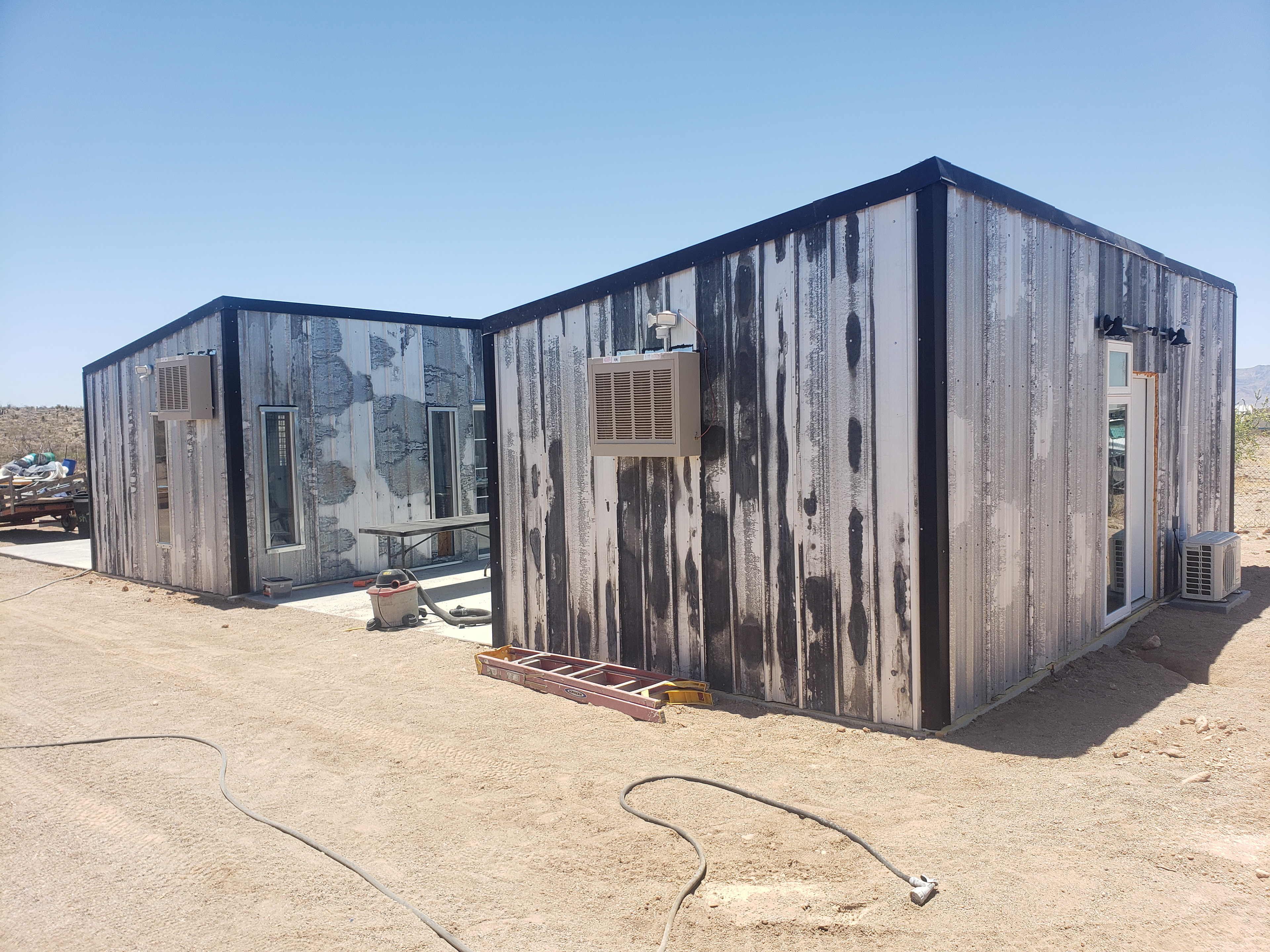
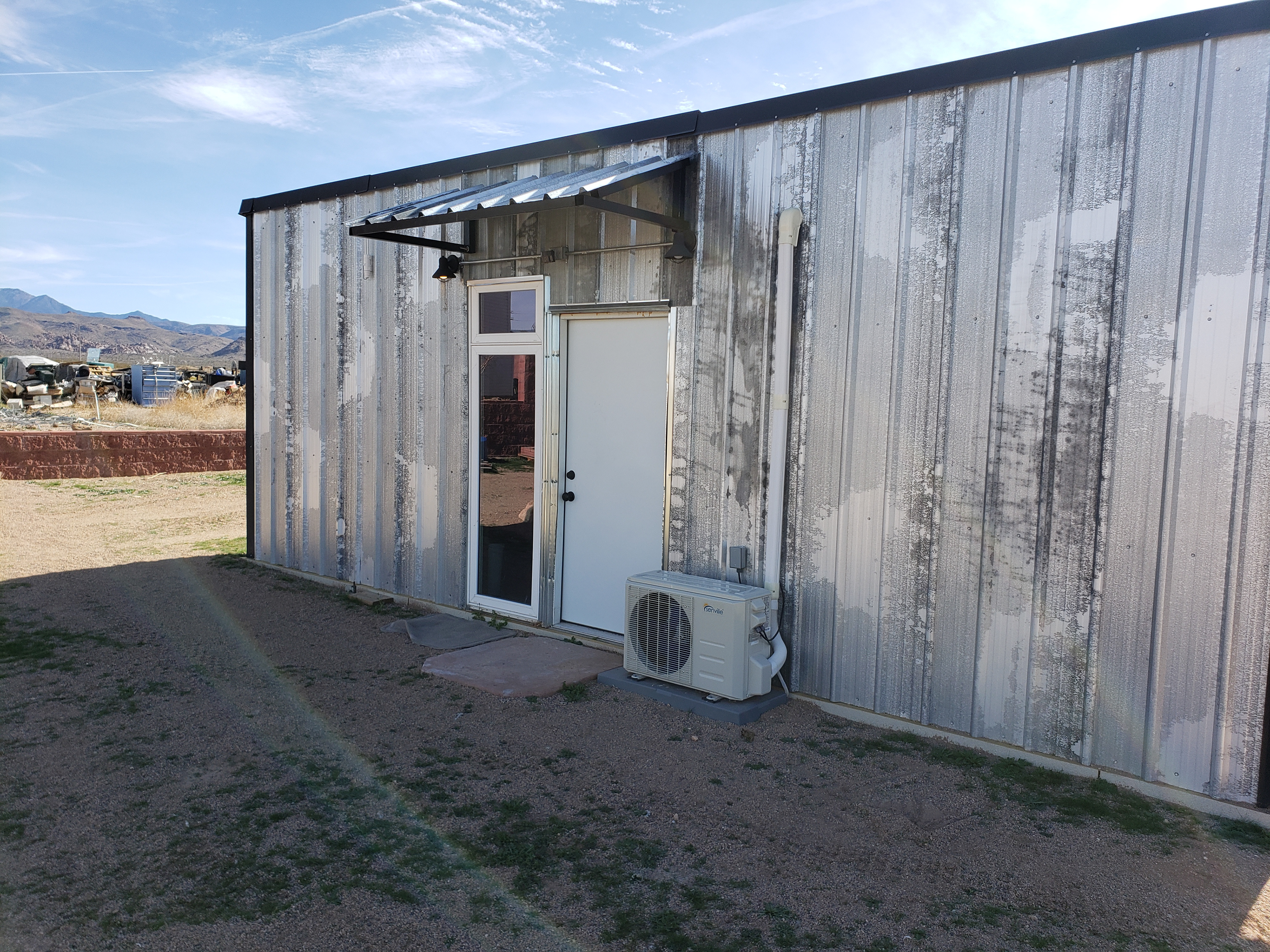
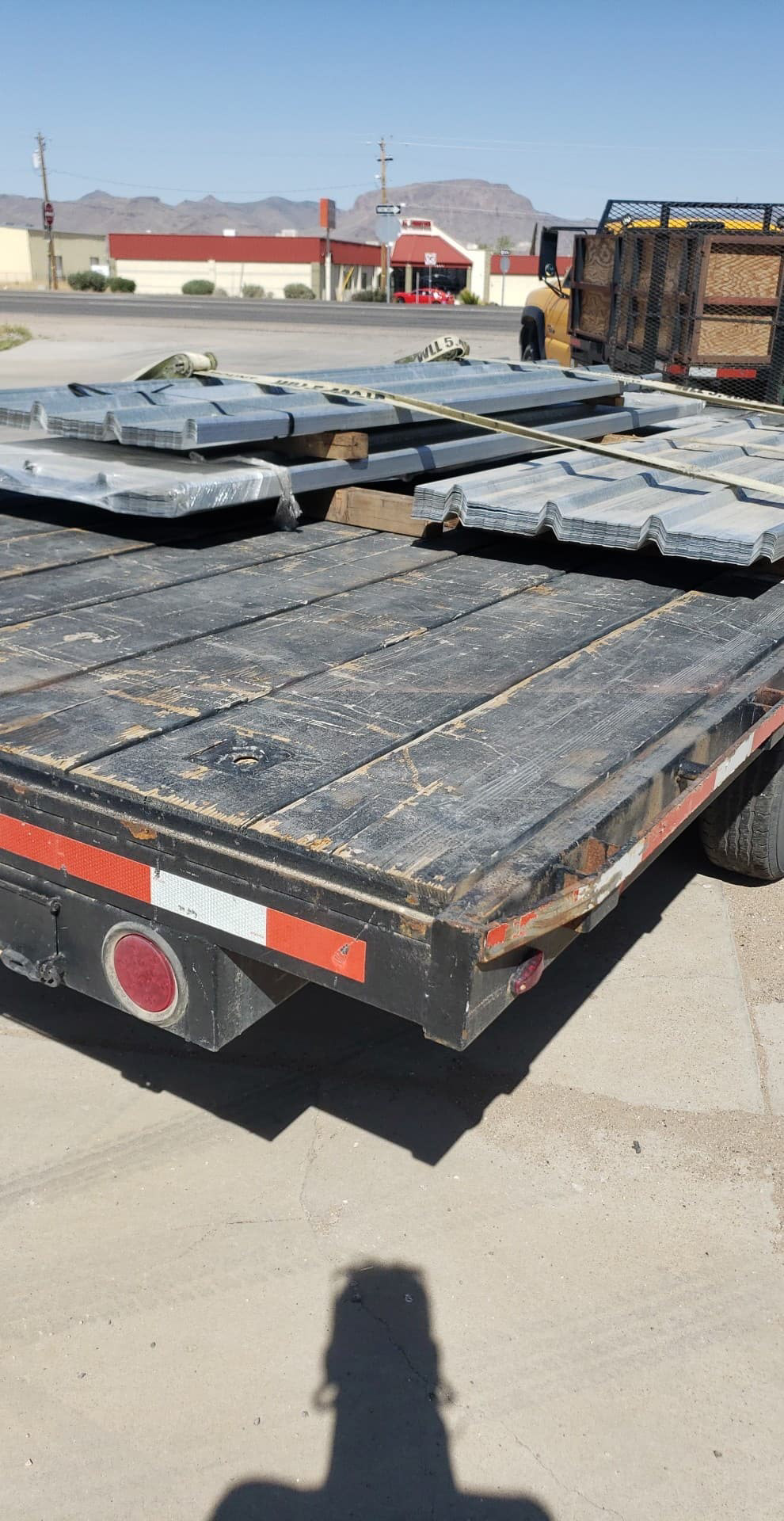
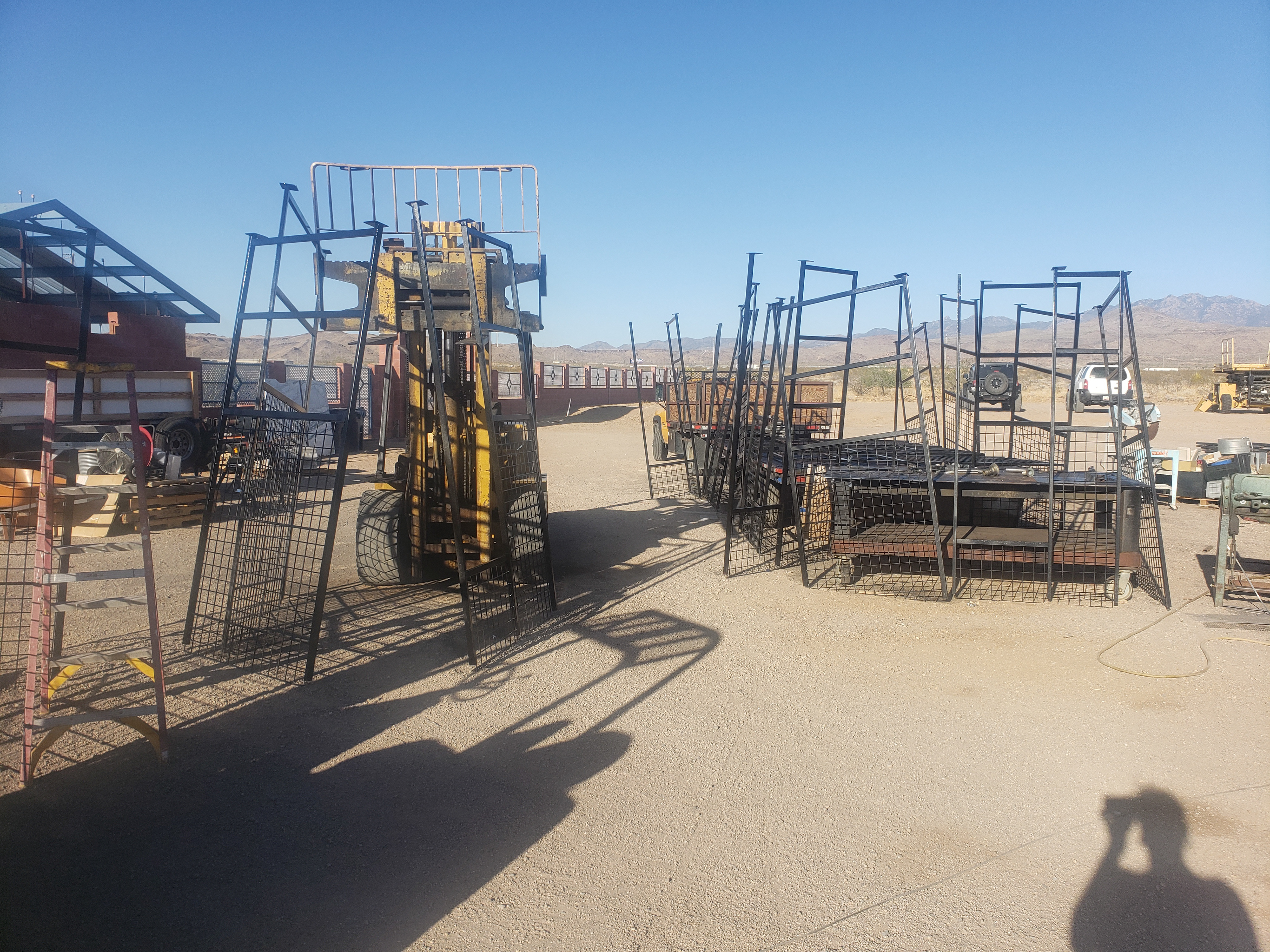
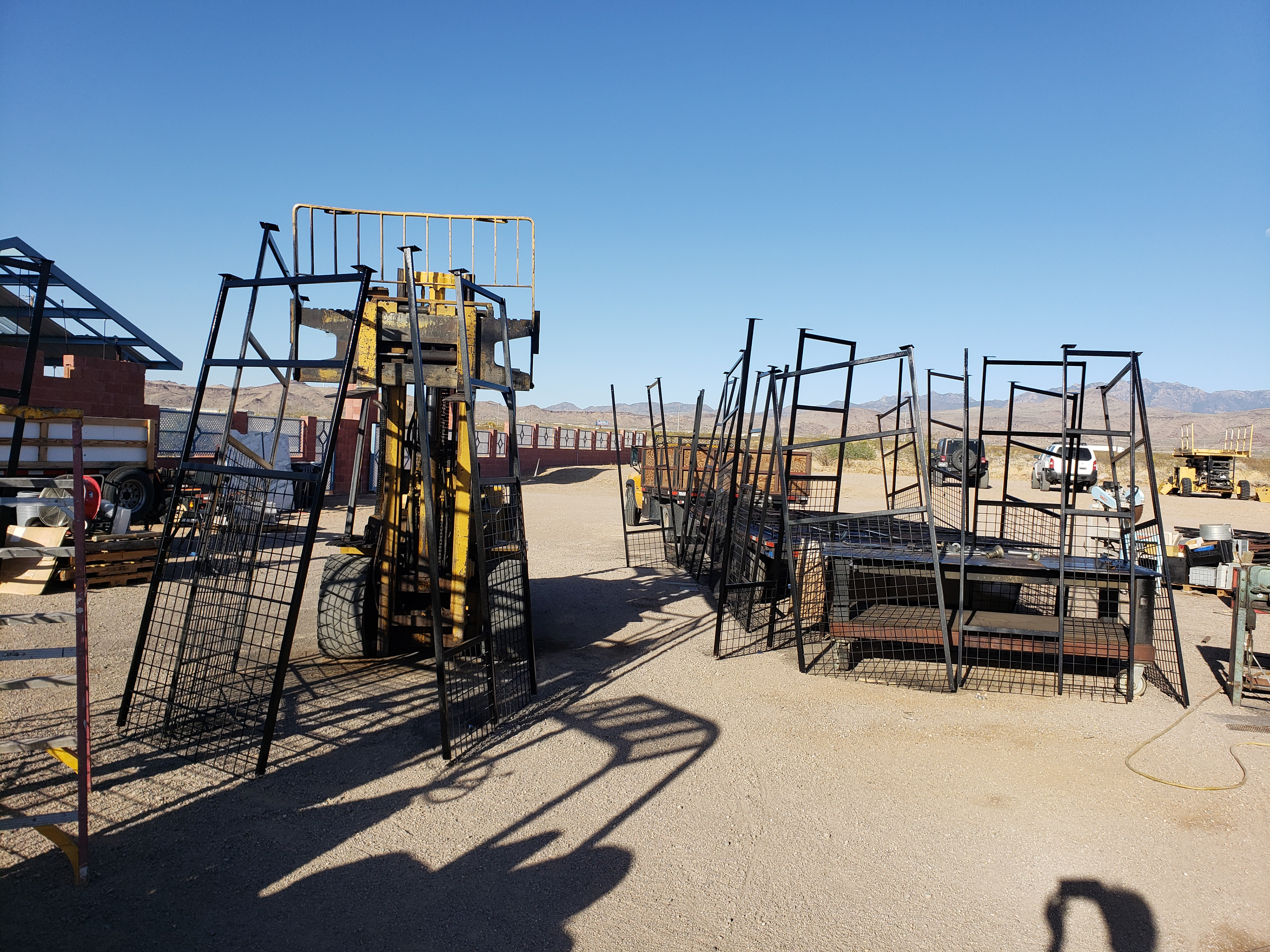
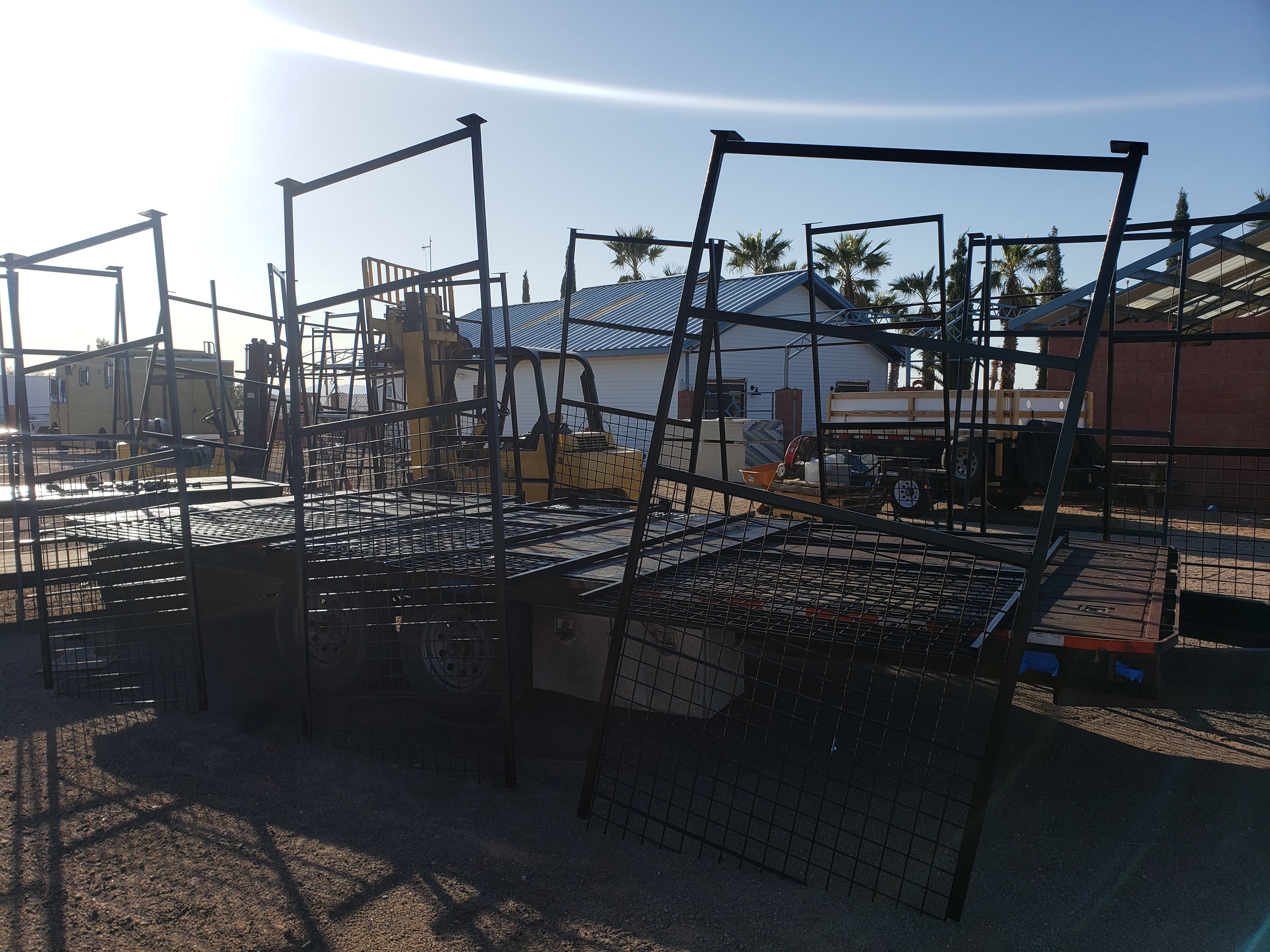
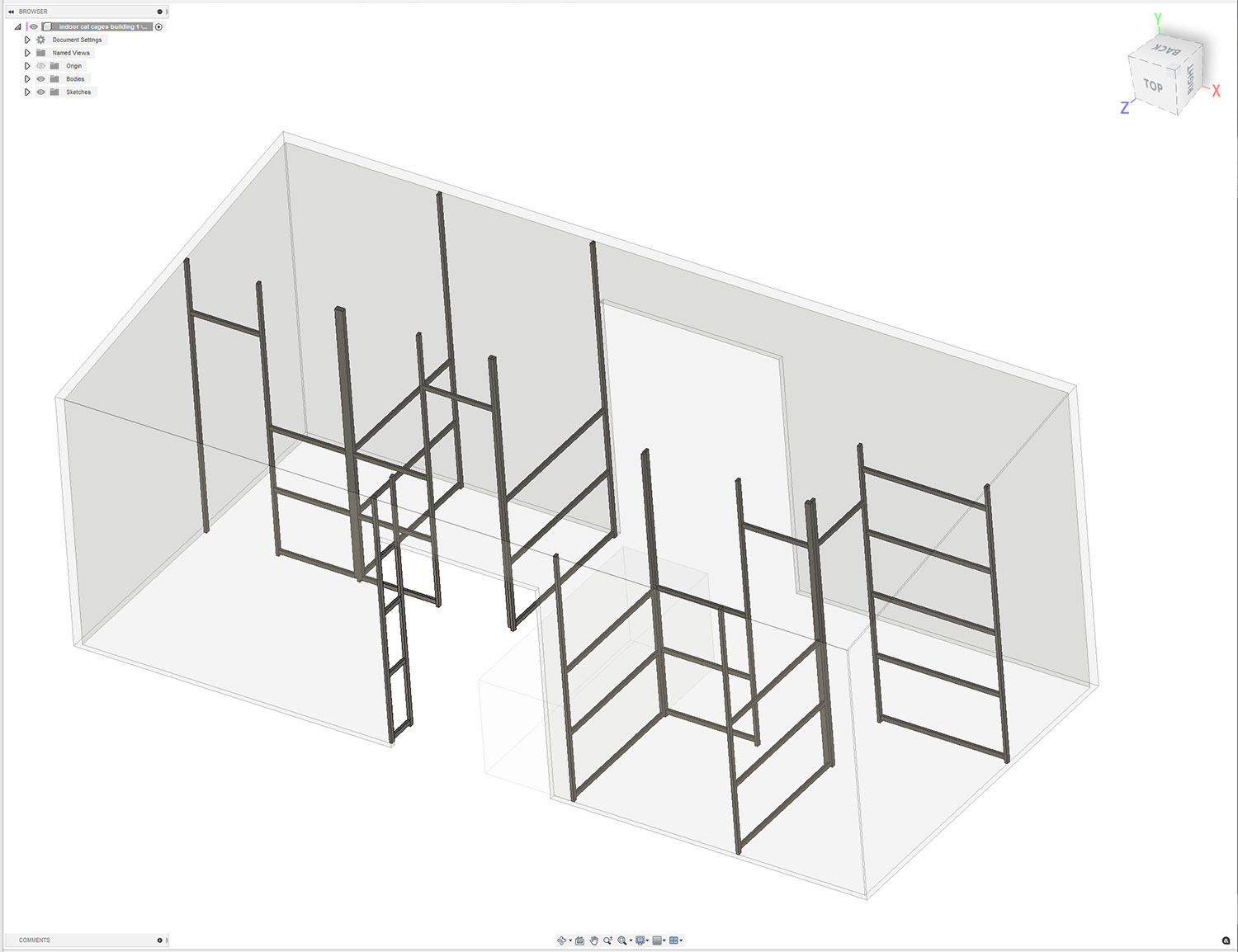
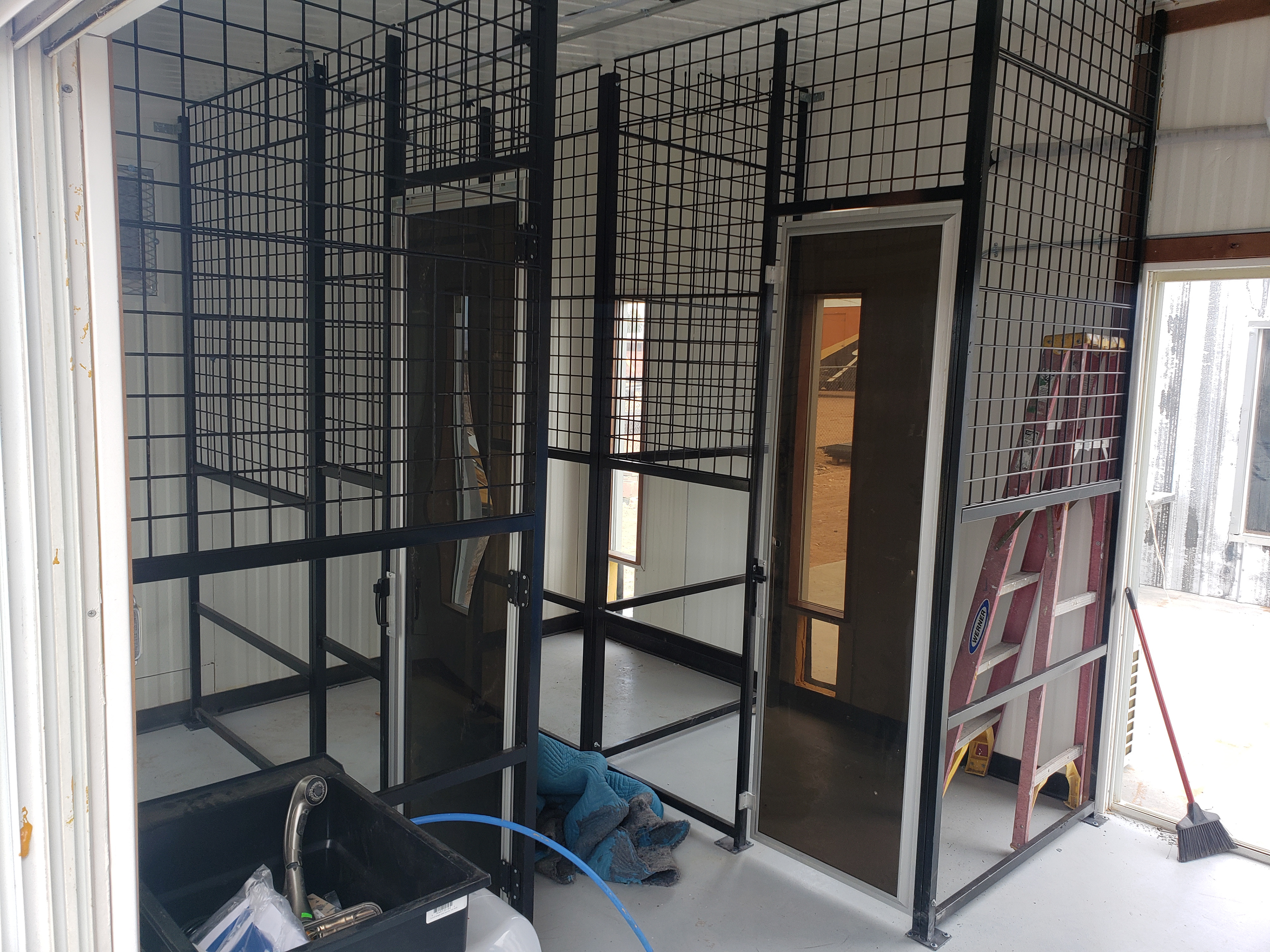
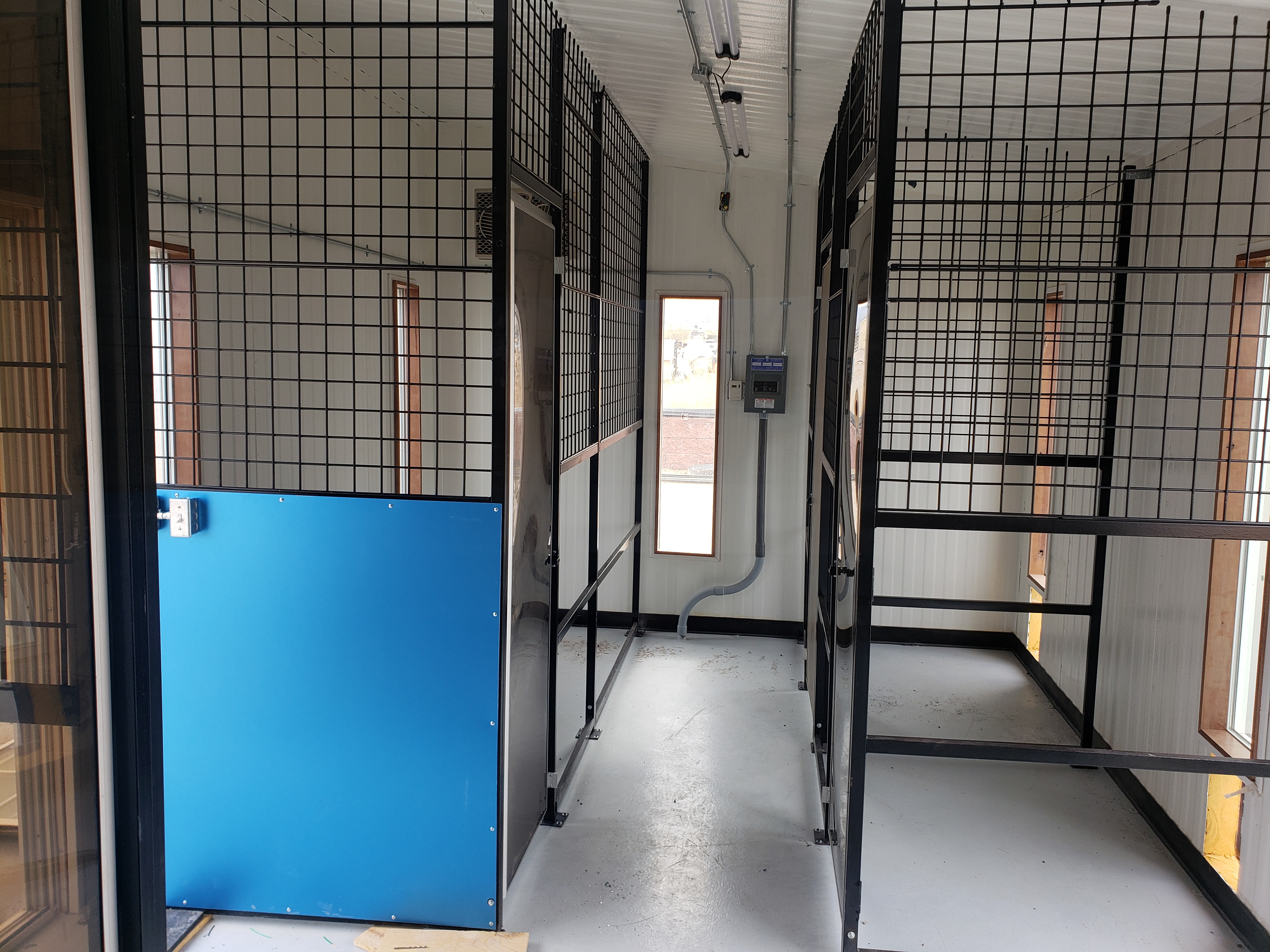
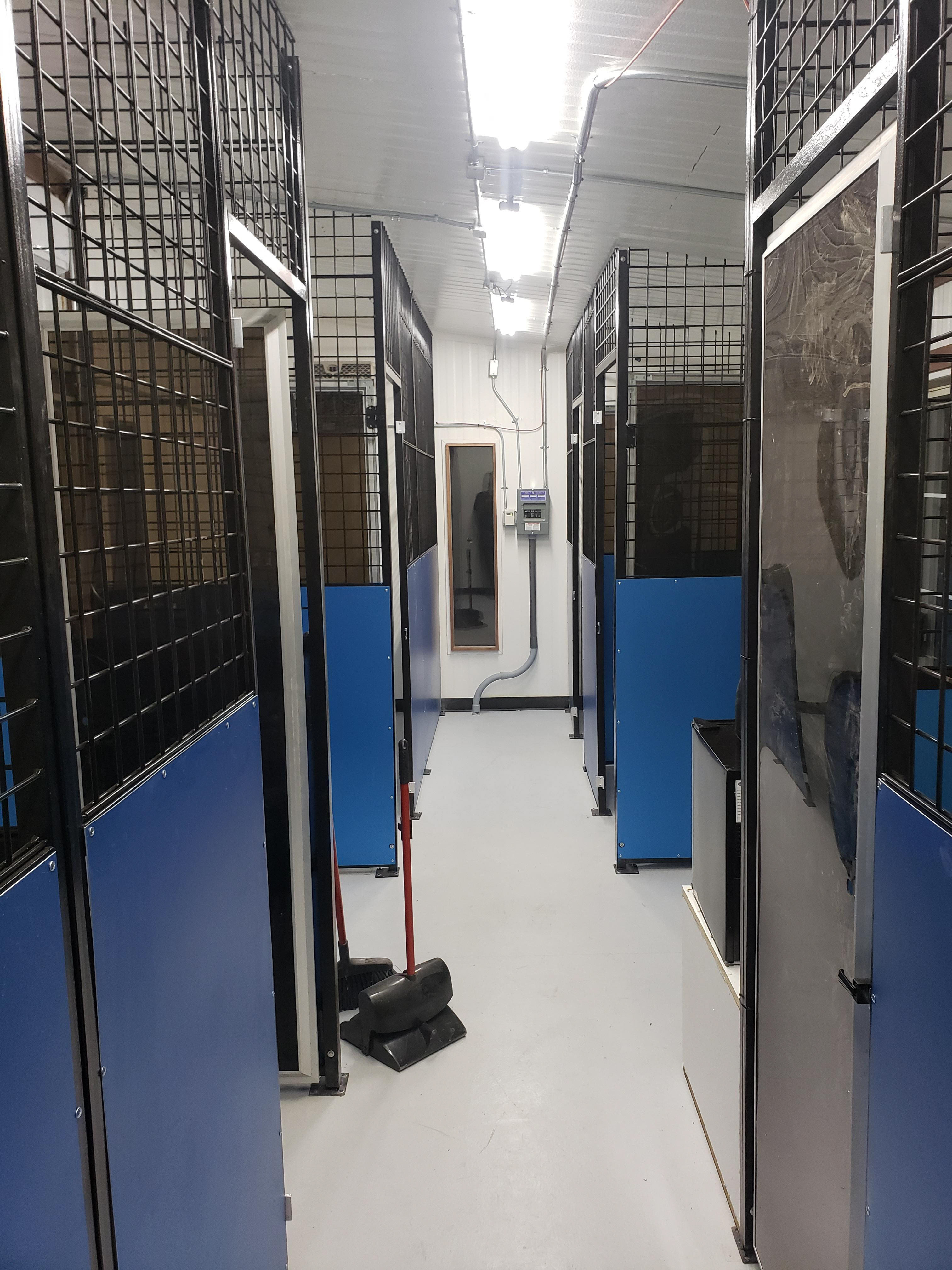
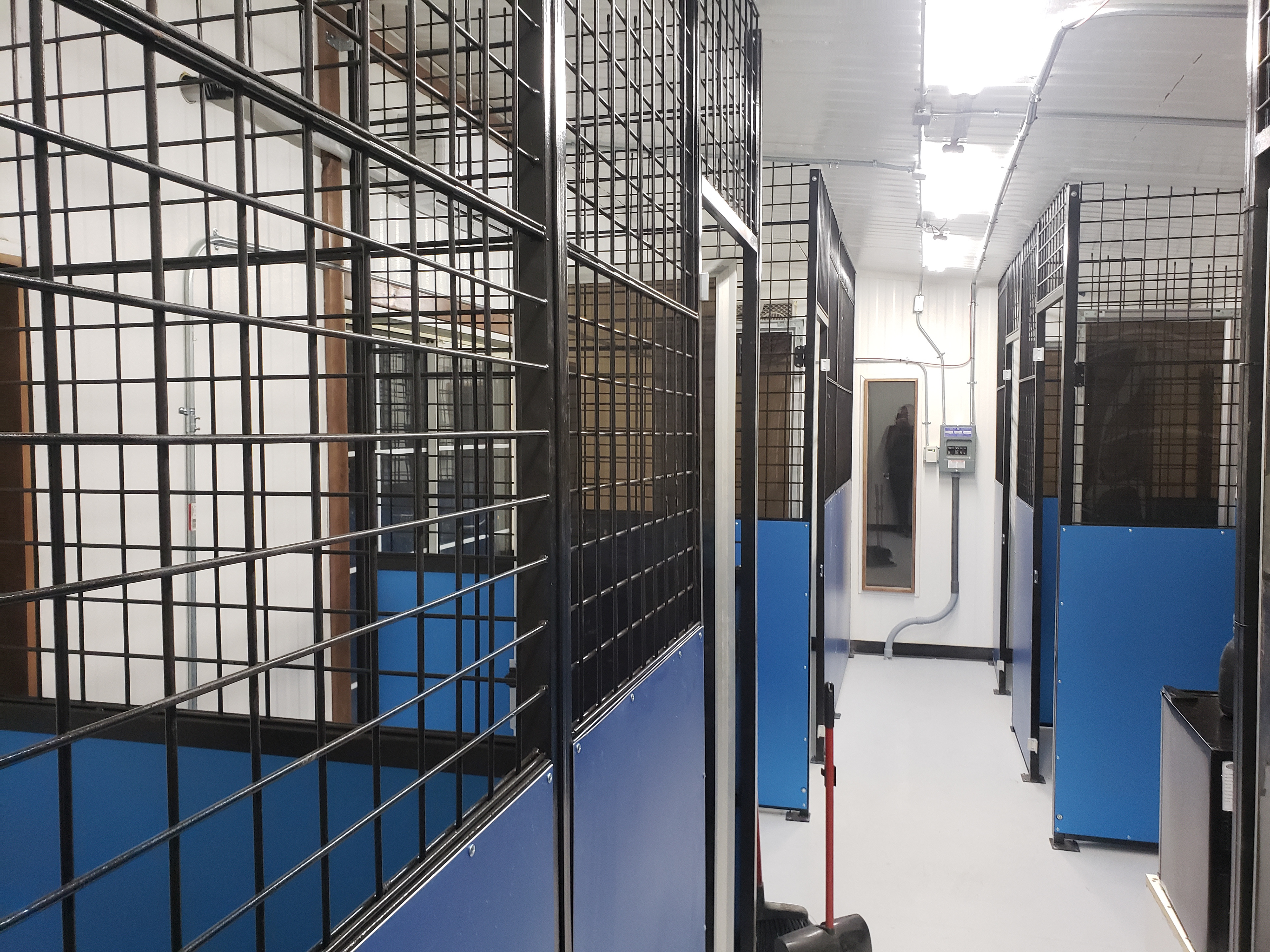
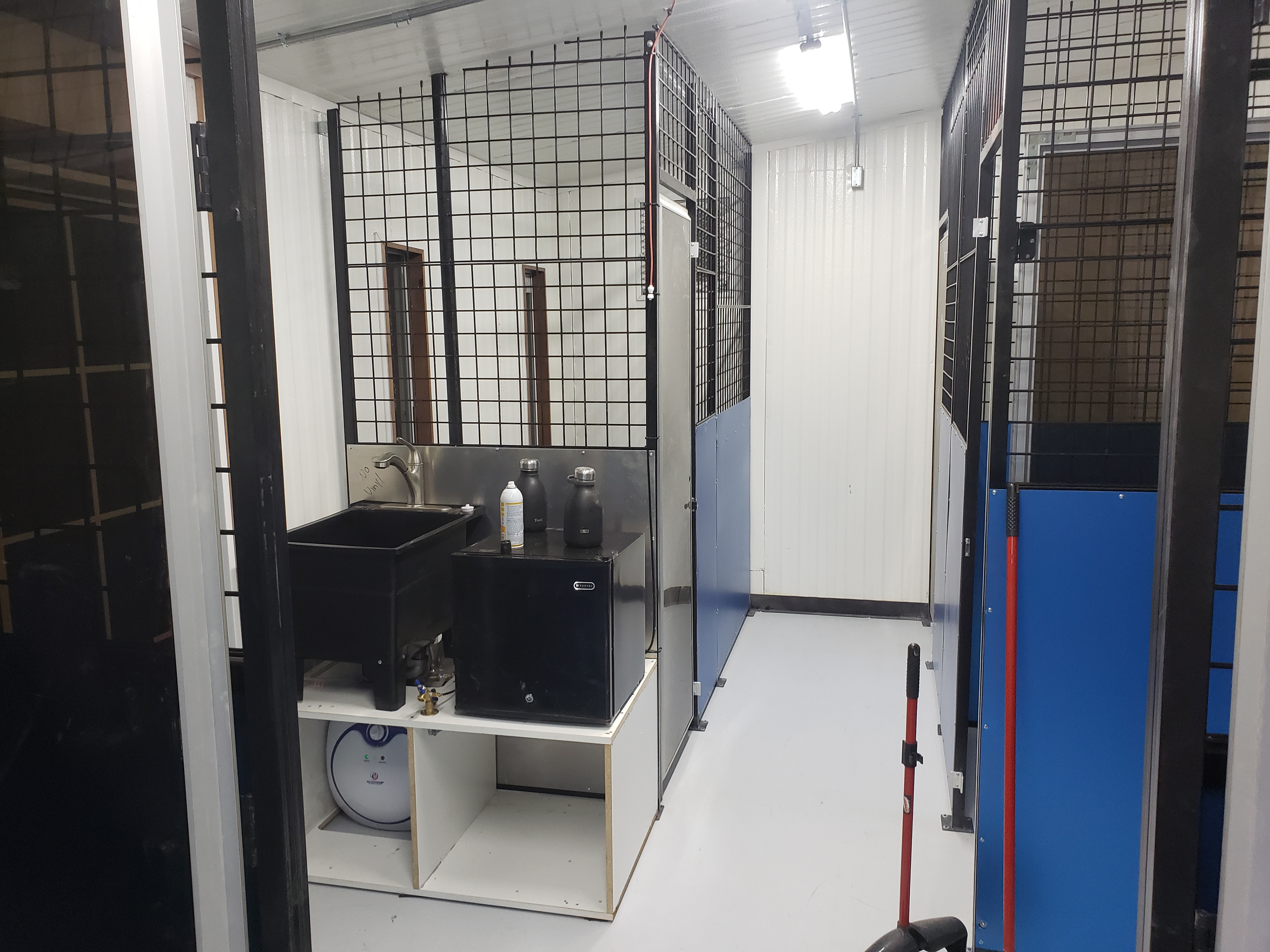
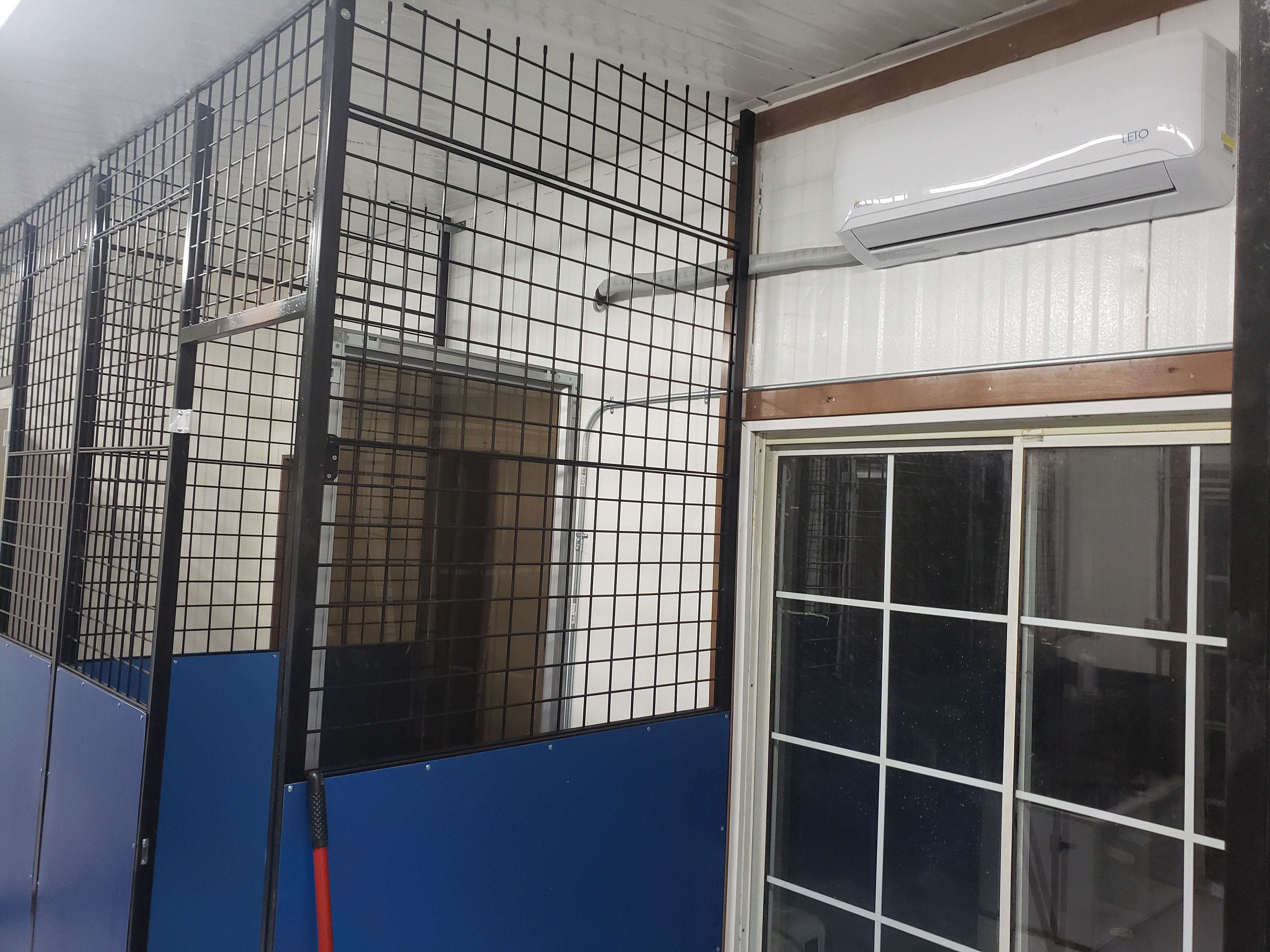
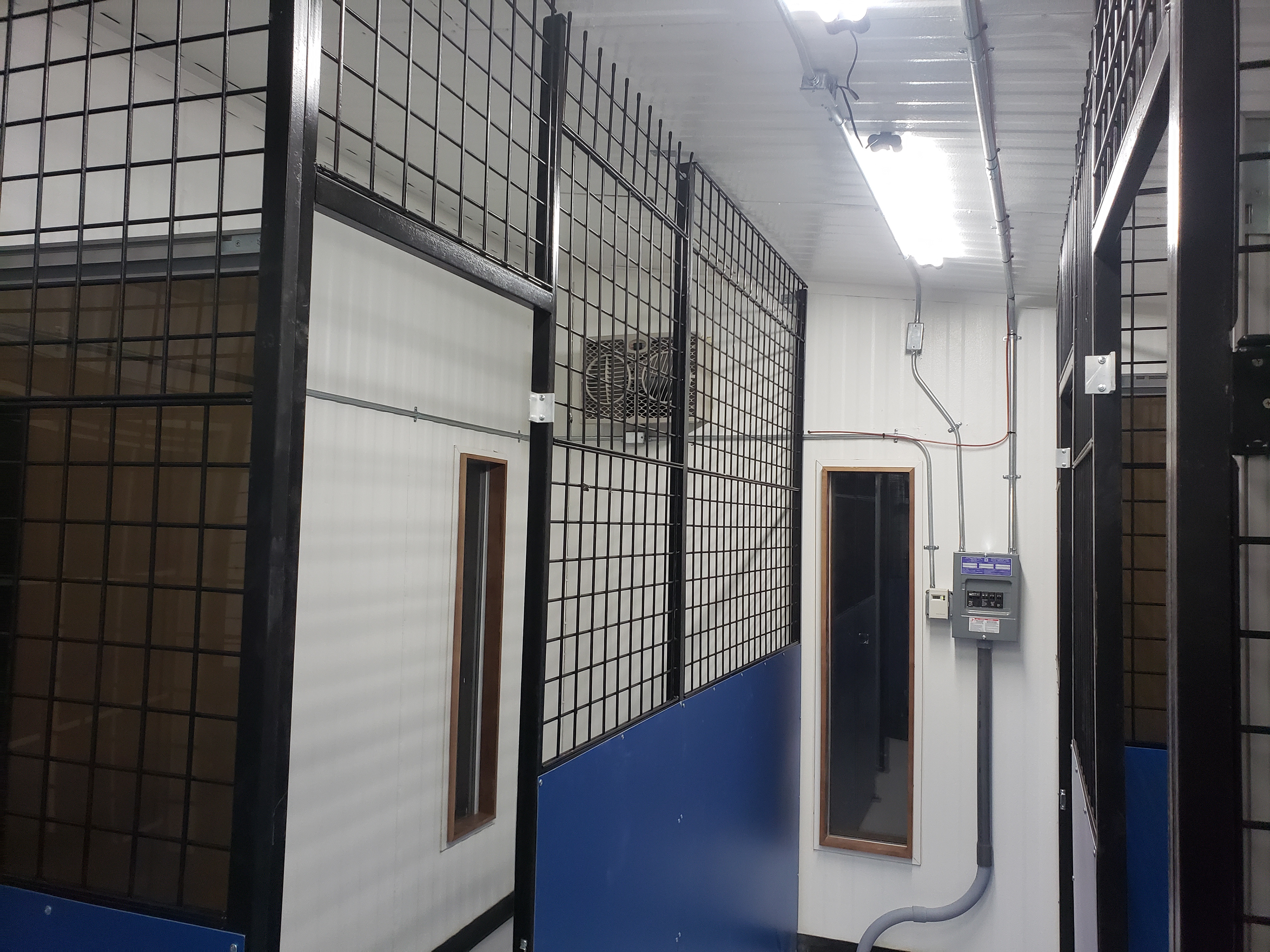
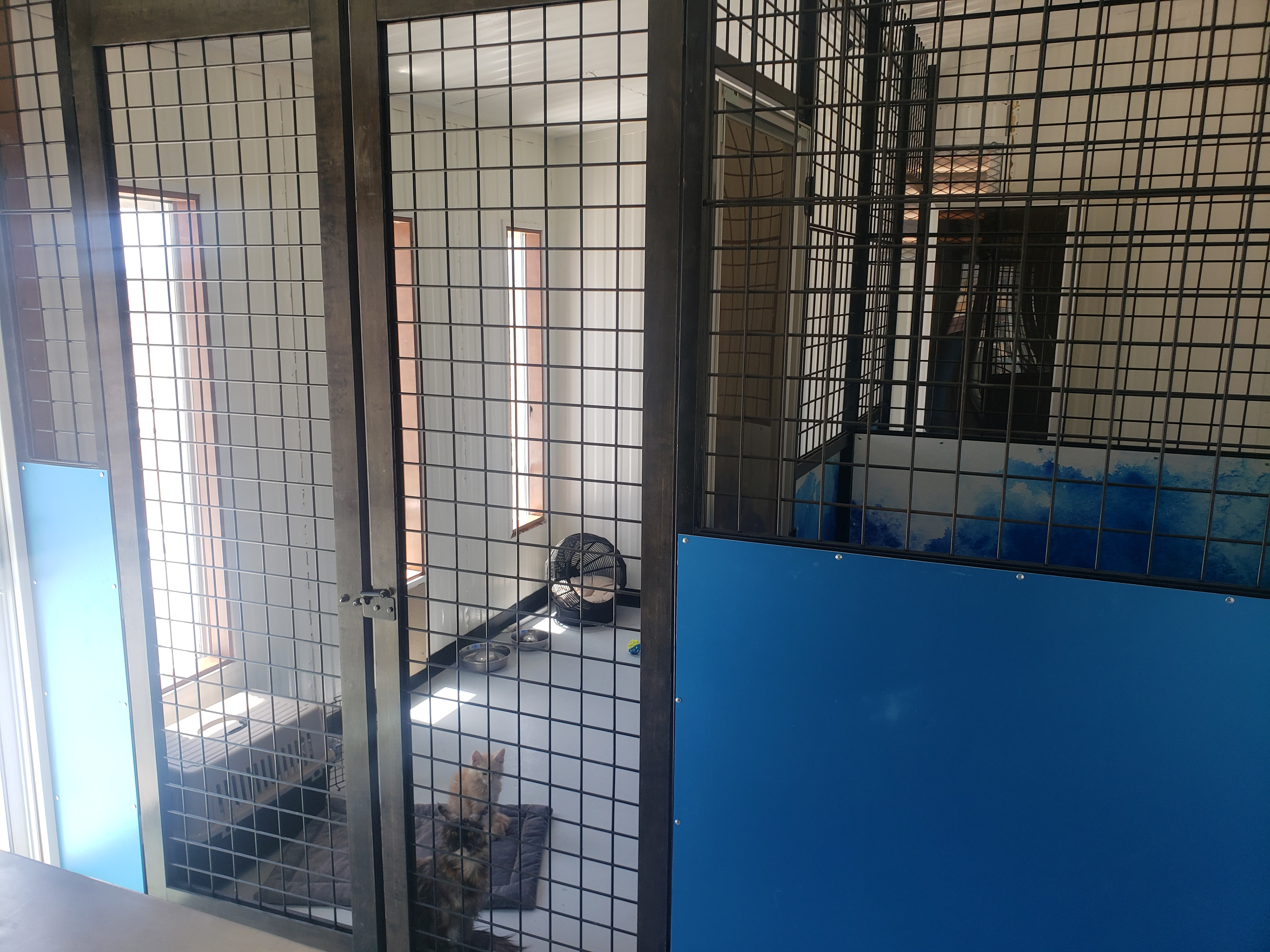
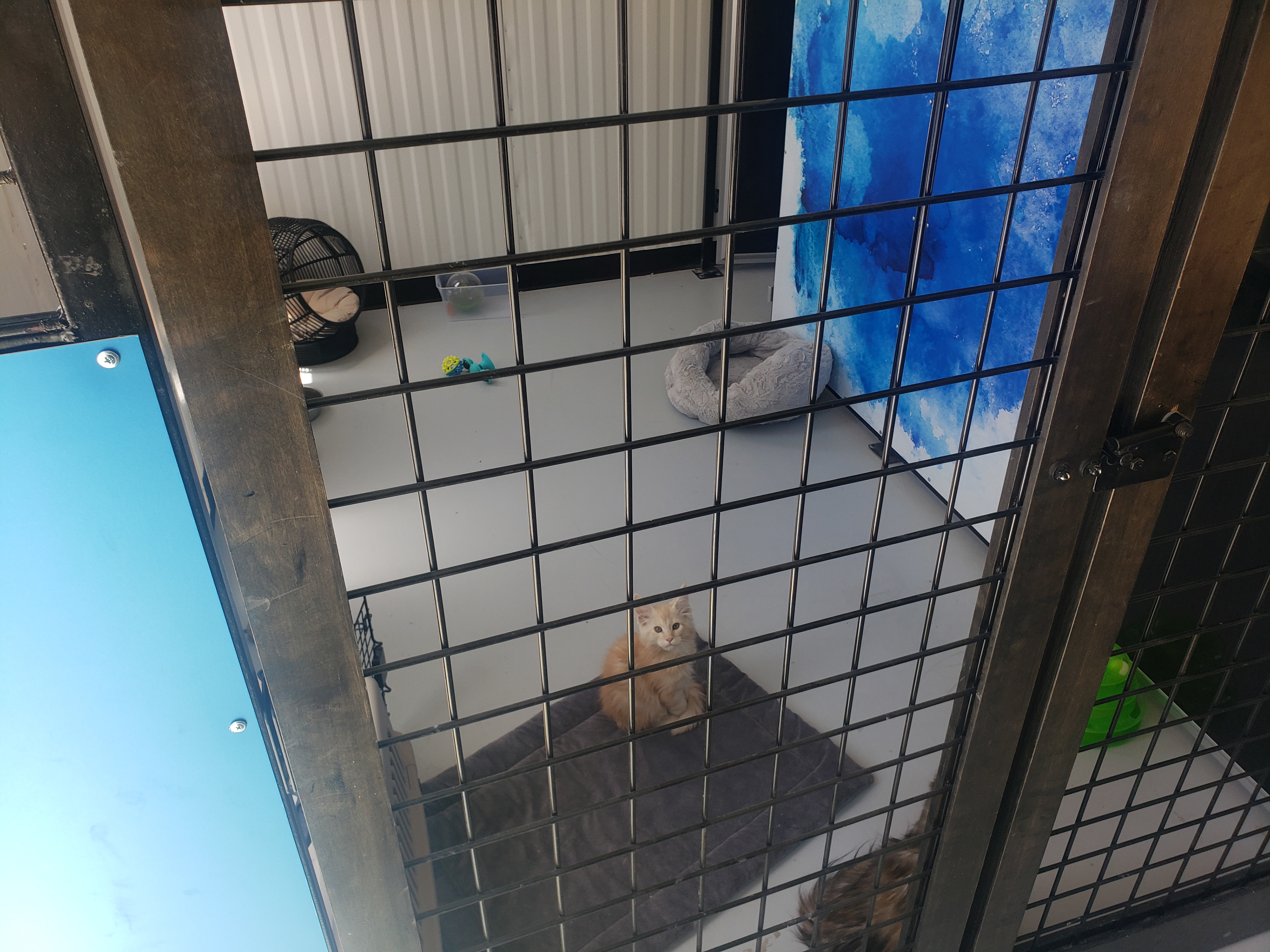
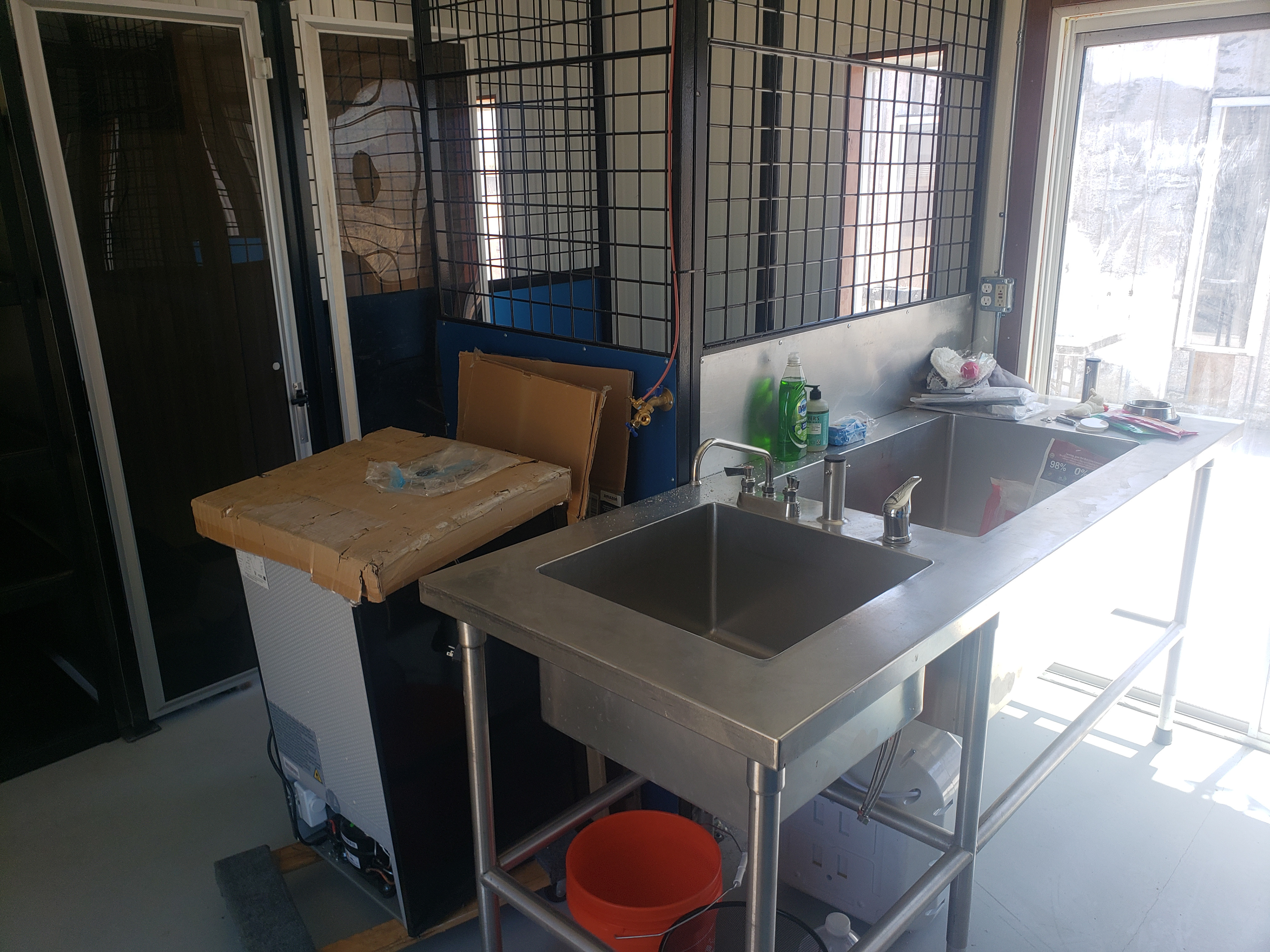
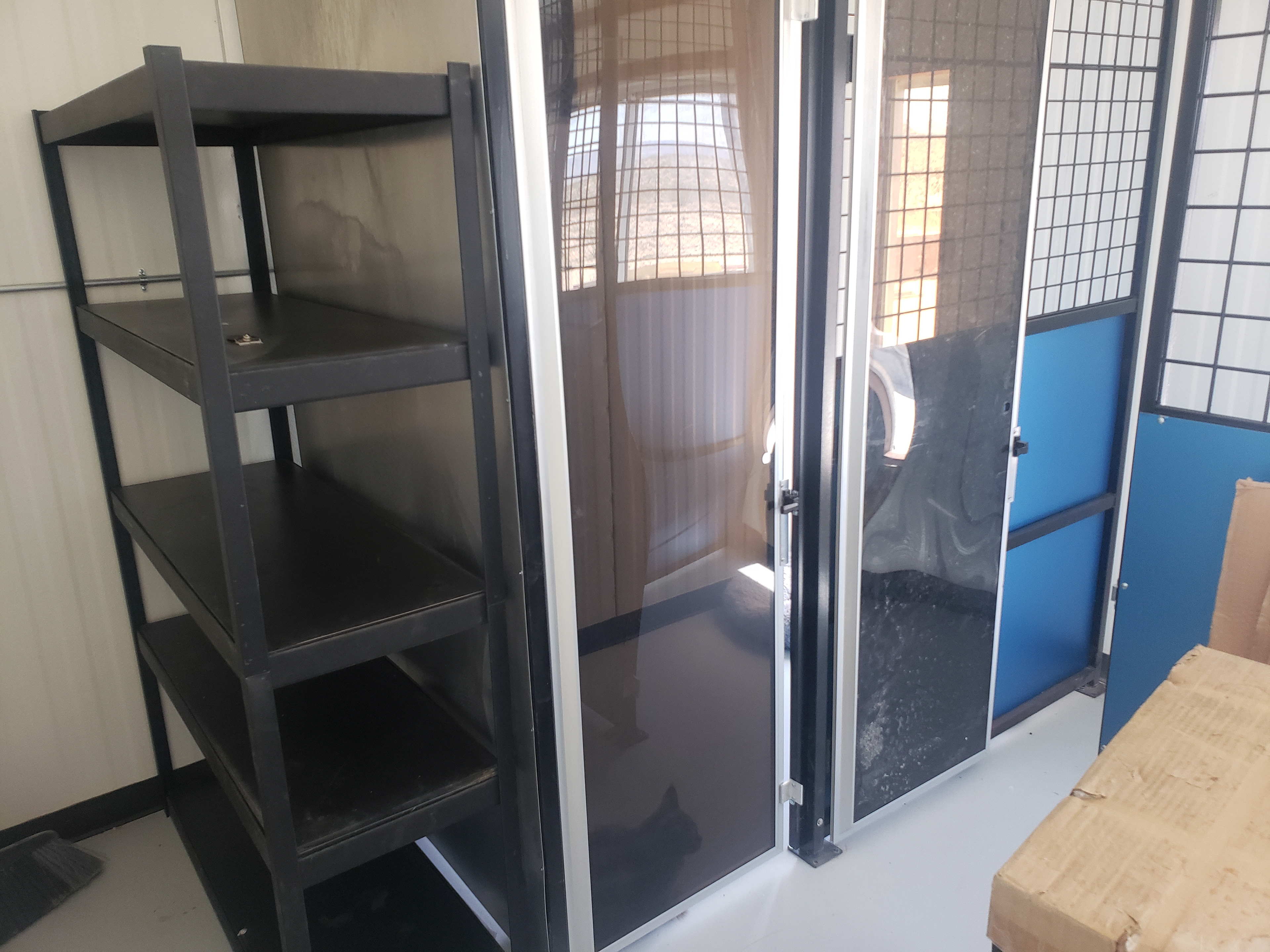
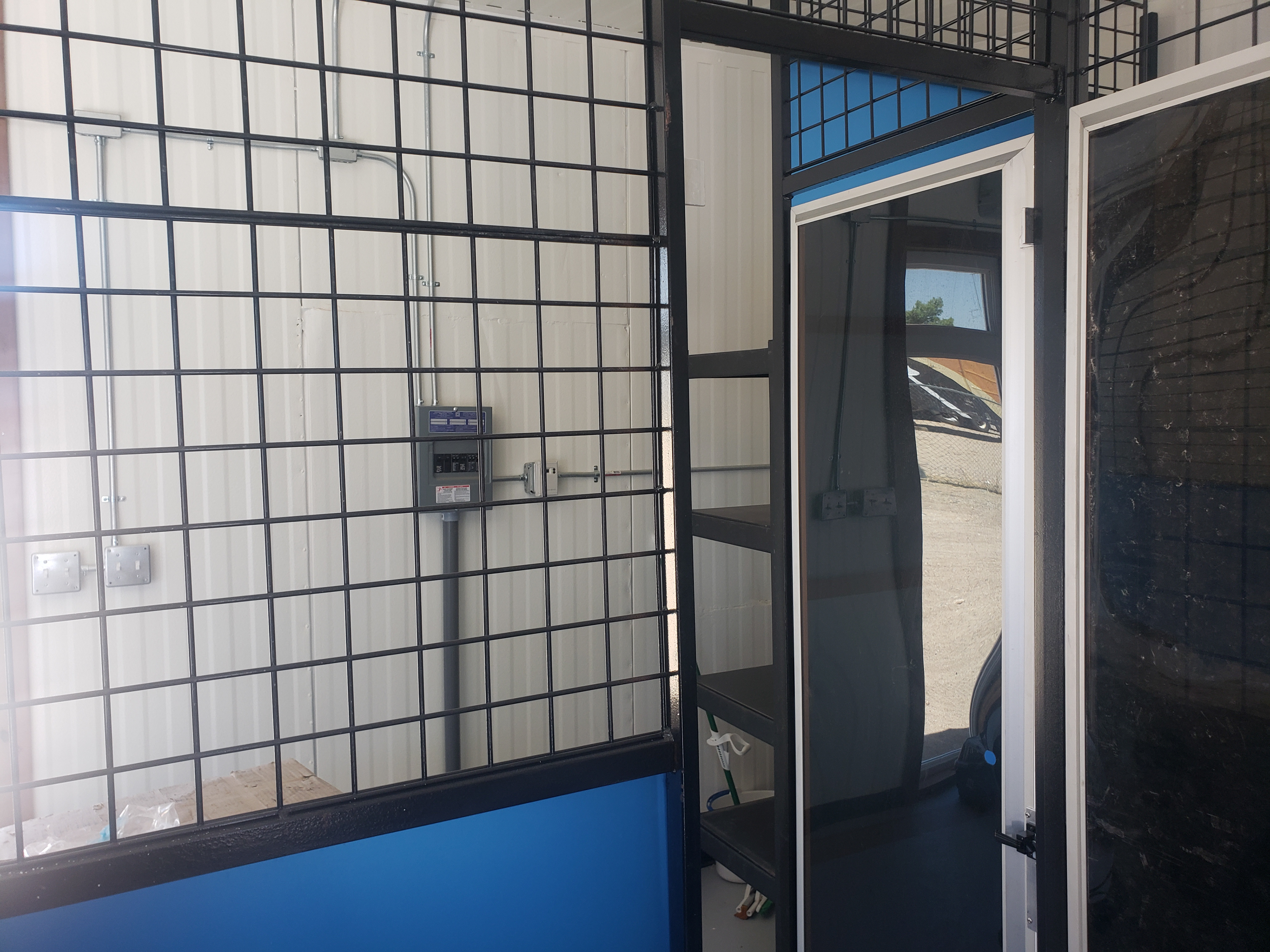
The lower blue aluminum panels received a layer of vinyl car wrap, and were screwed in place. Refrigerators and freezers were added to store the food. It was getting together just in time, as summer was creeping in.
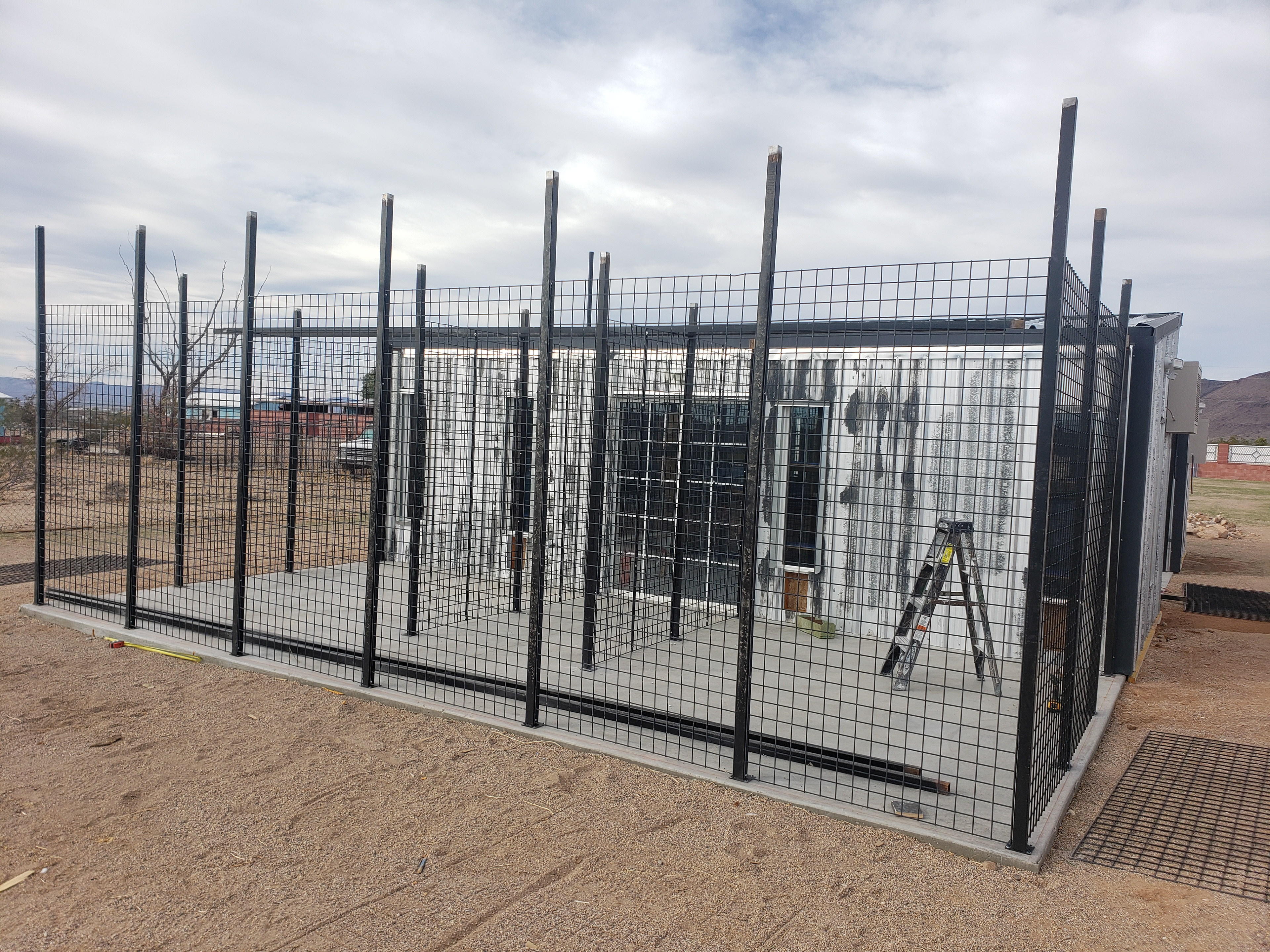

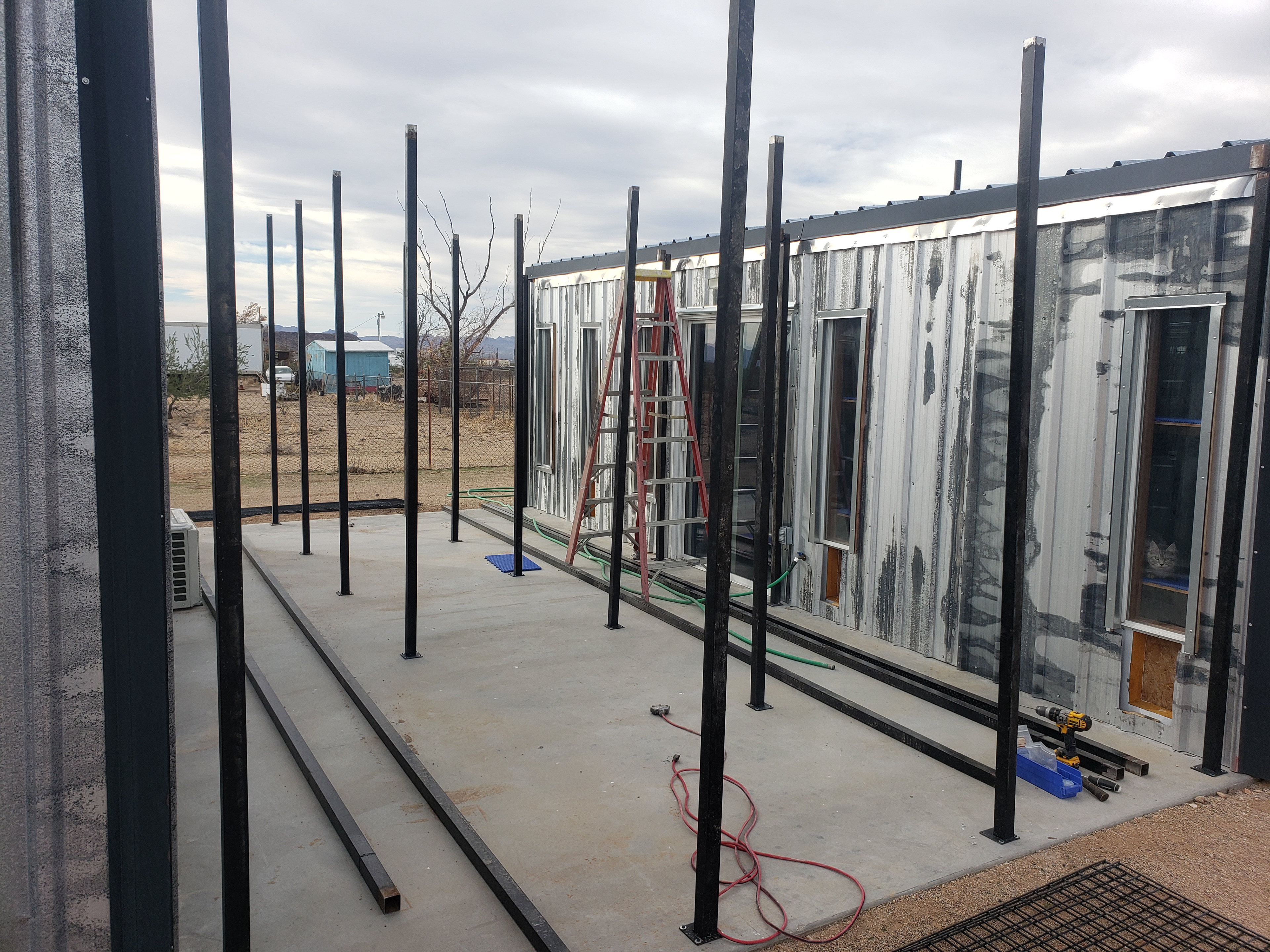
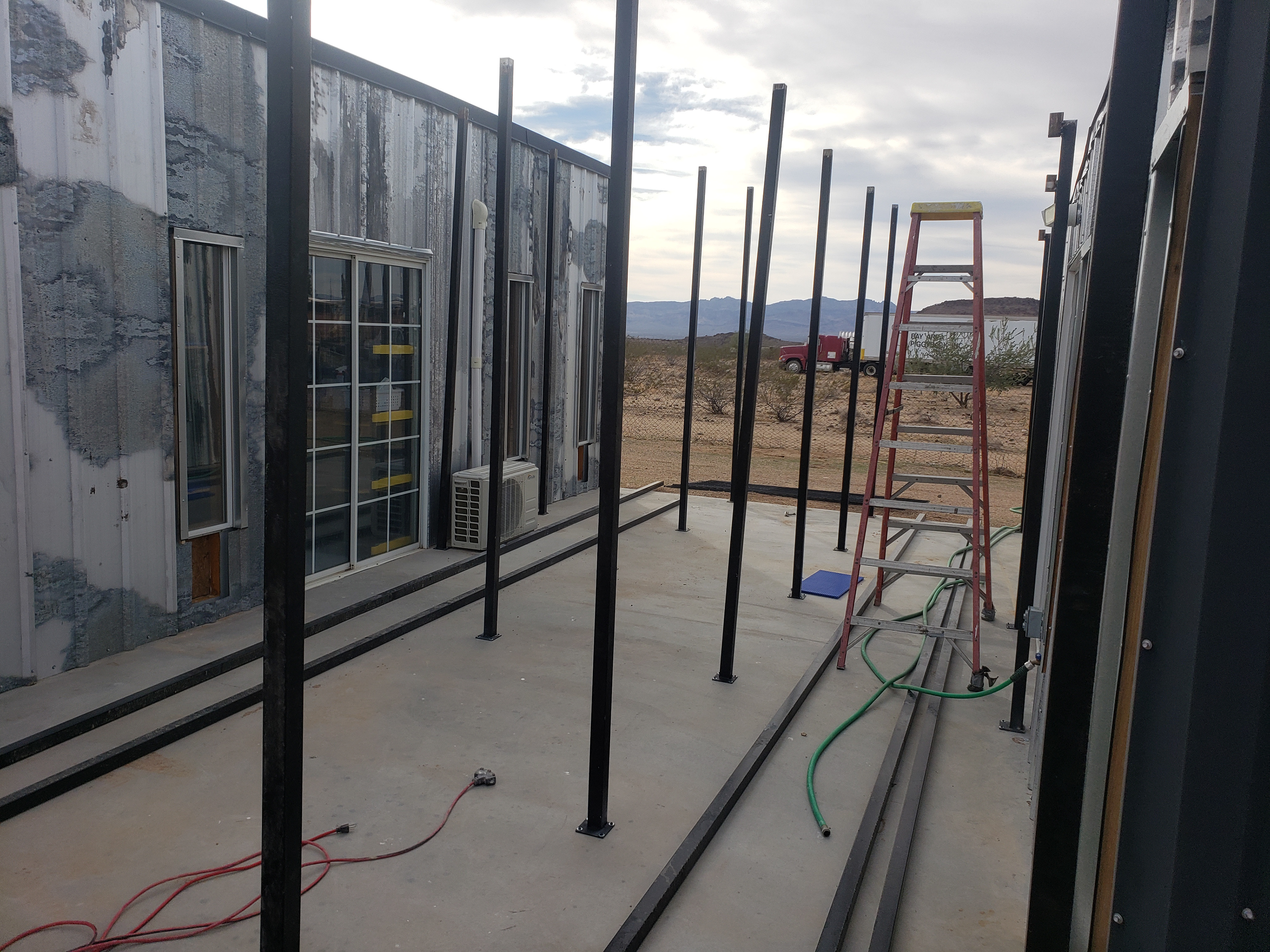
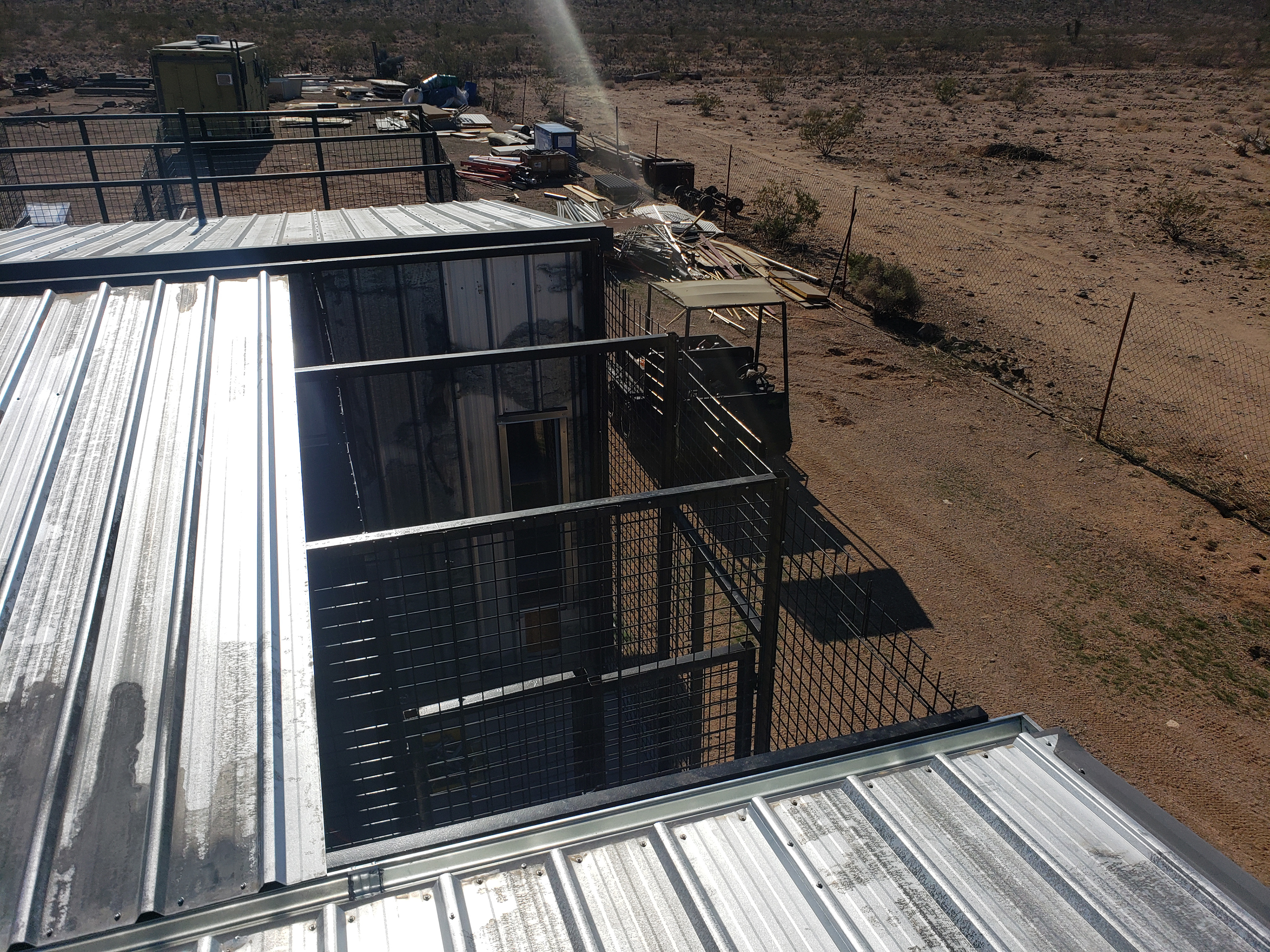

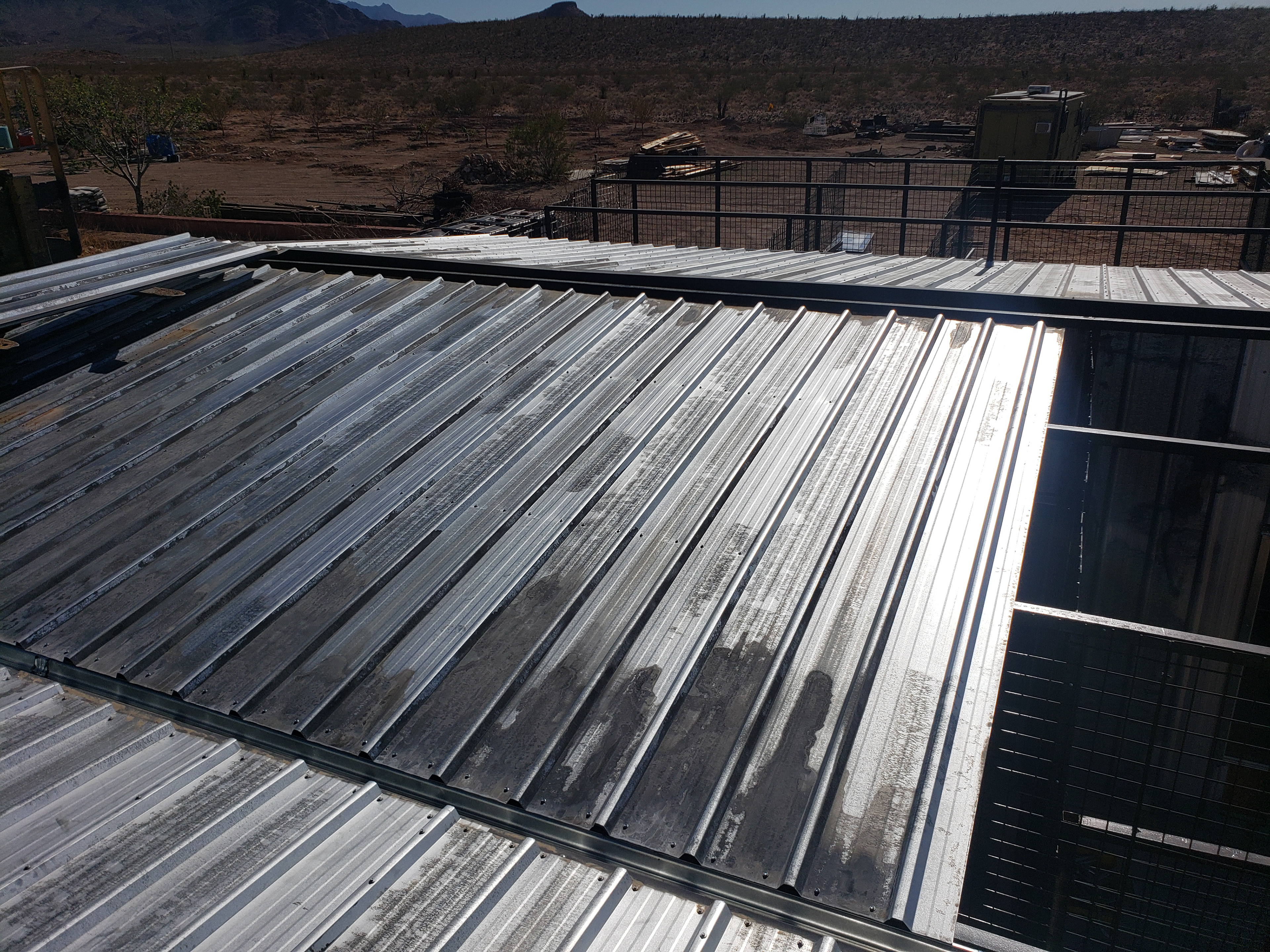
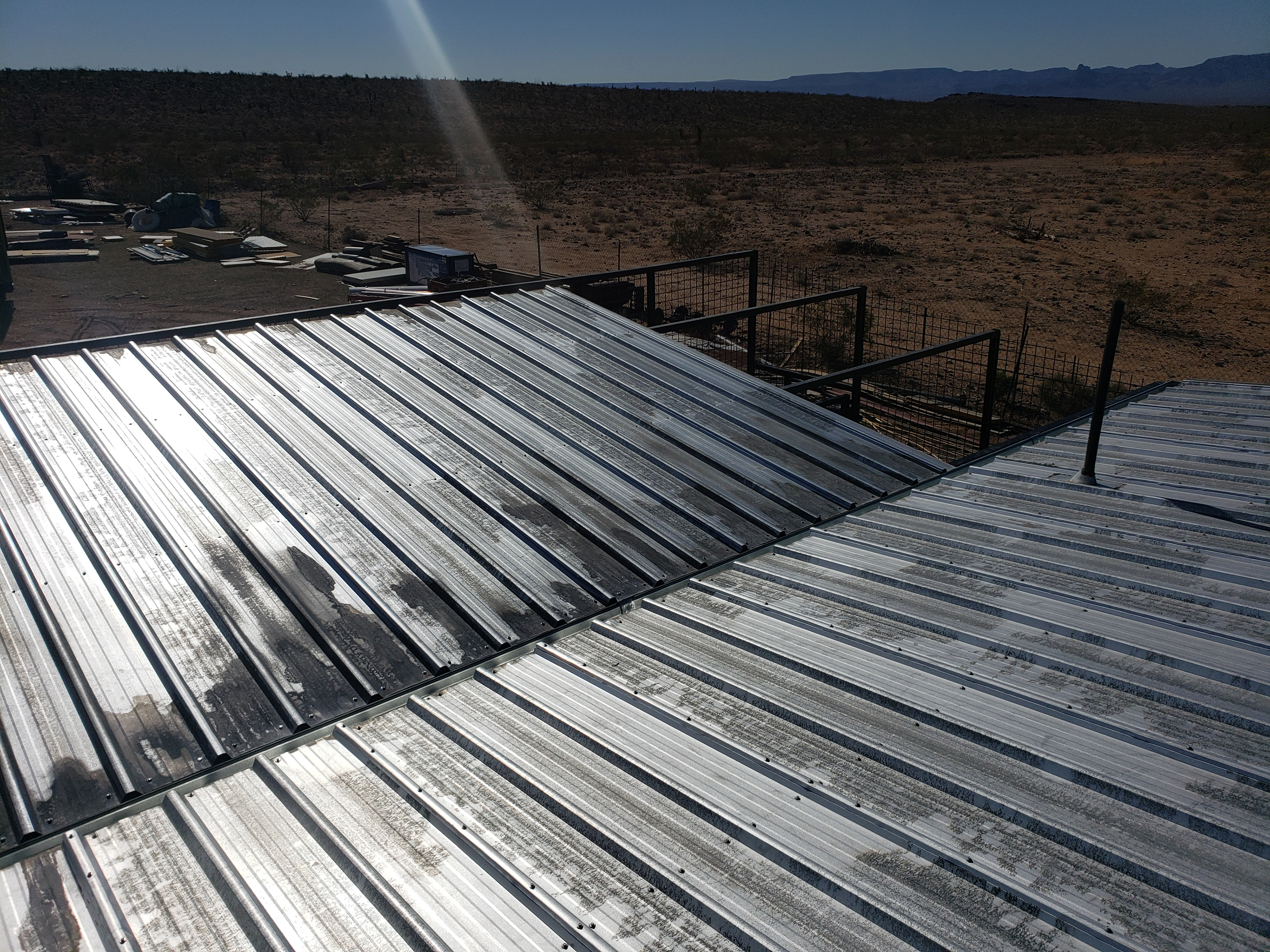
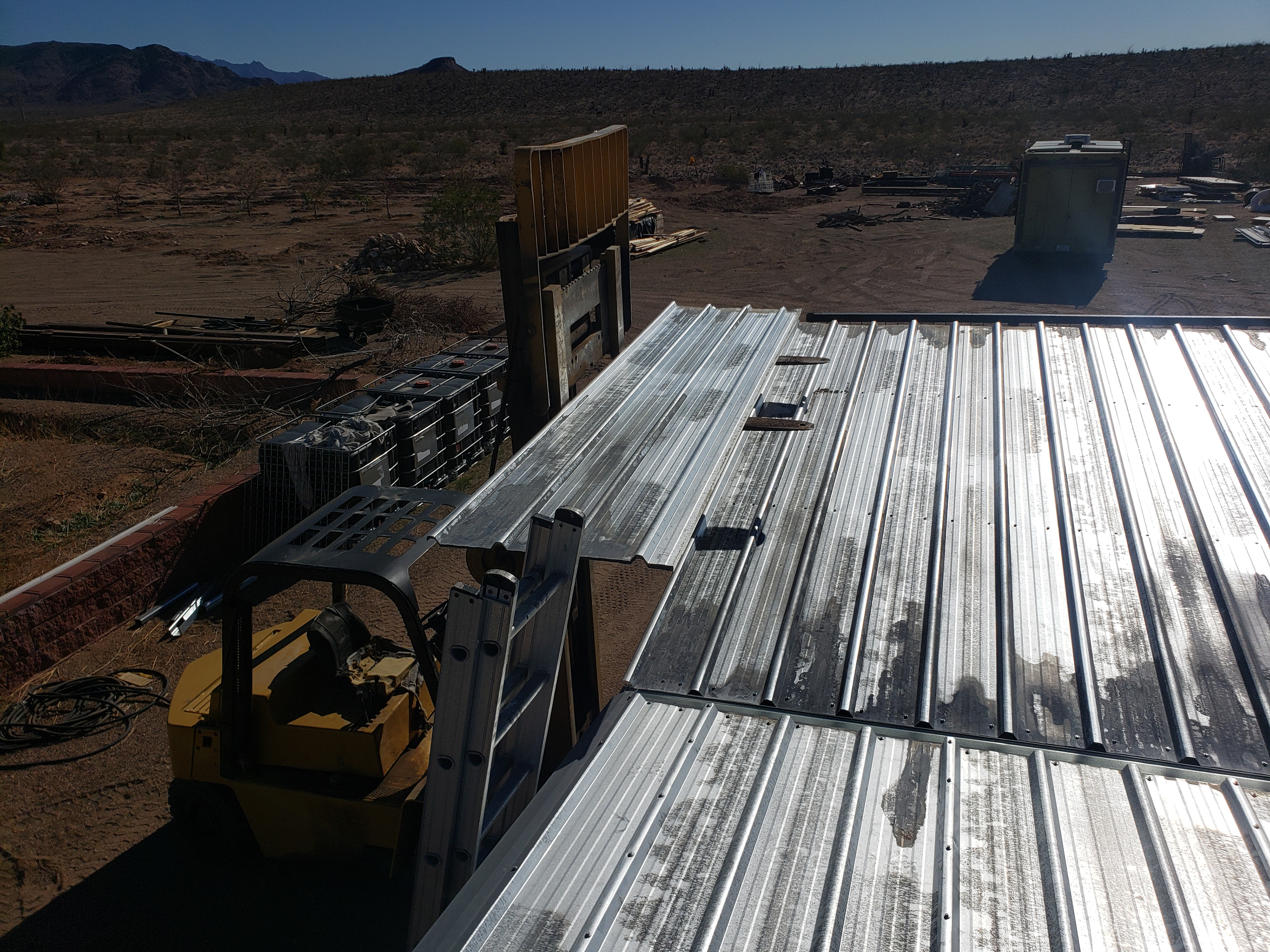
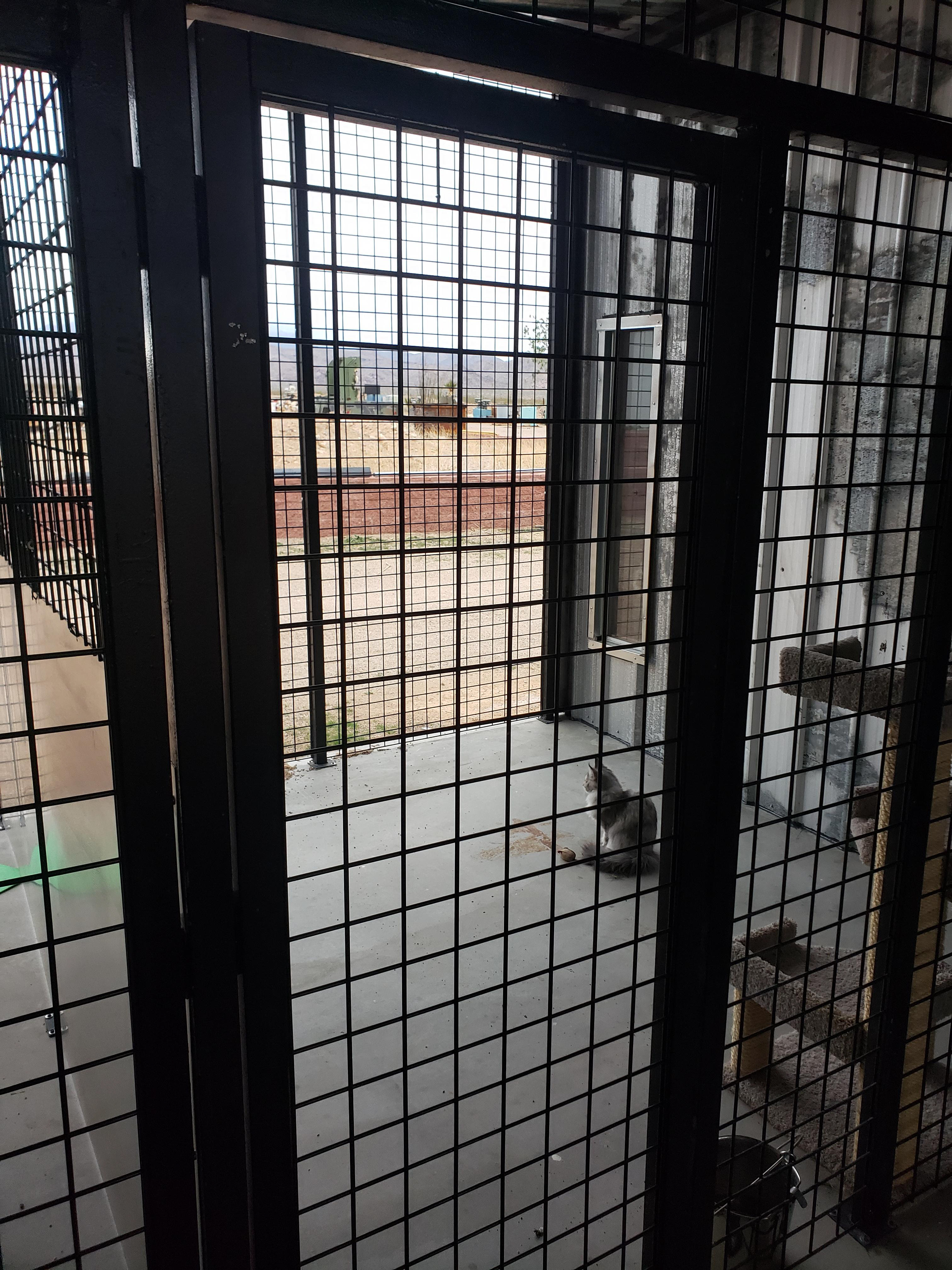
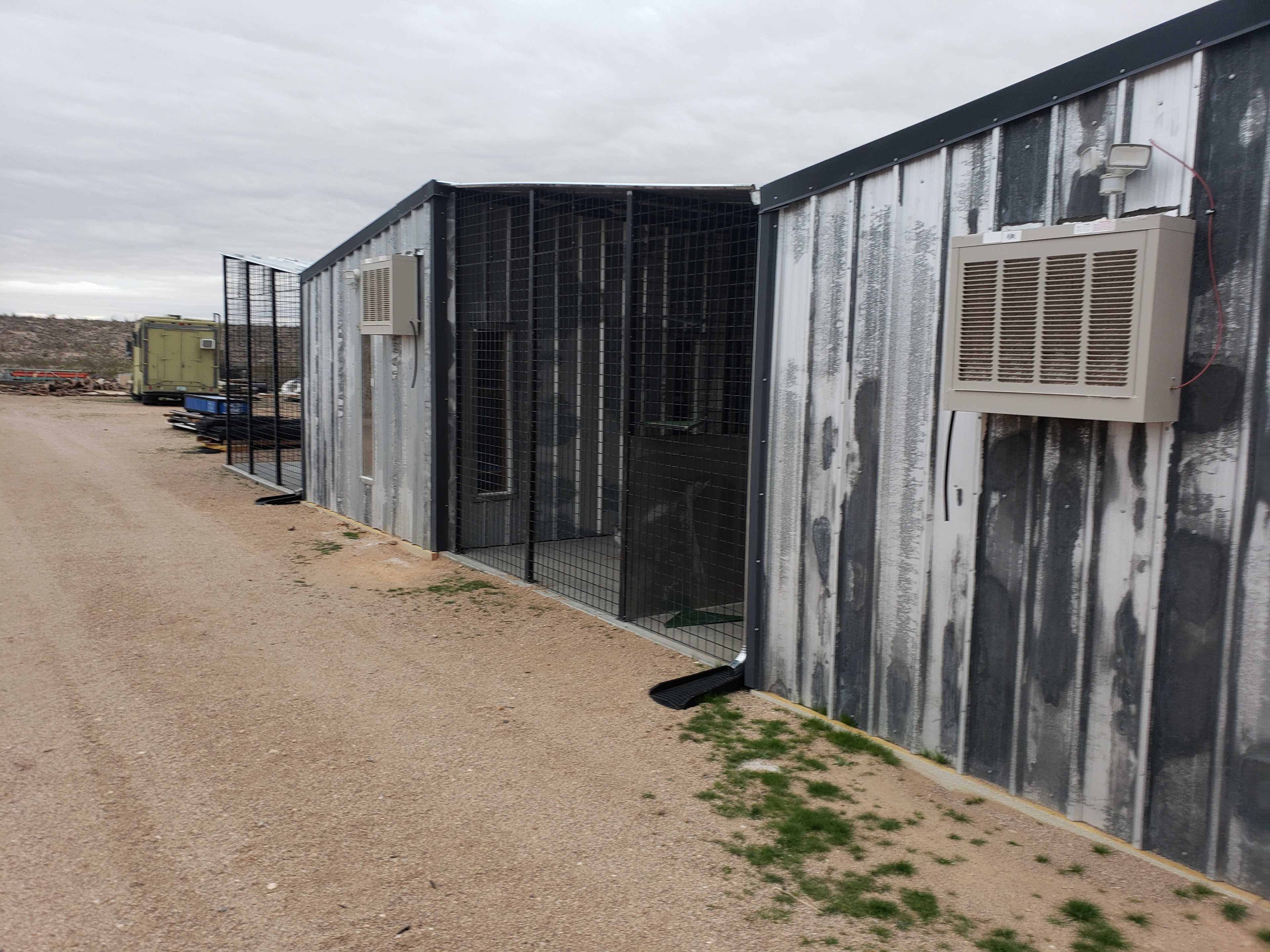
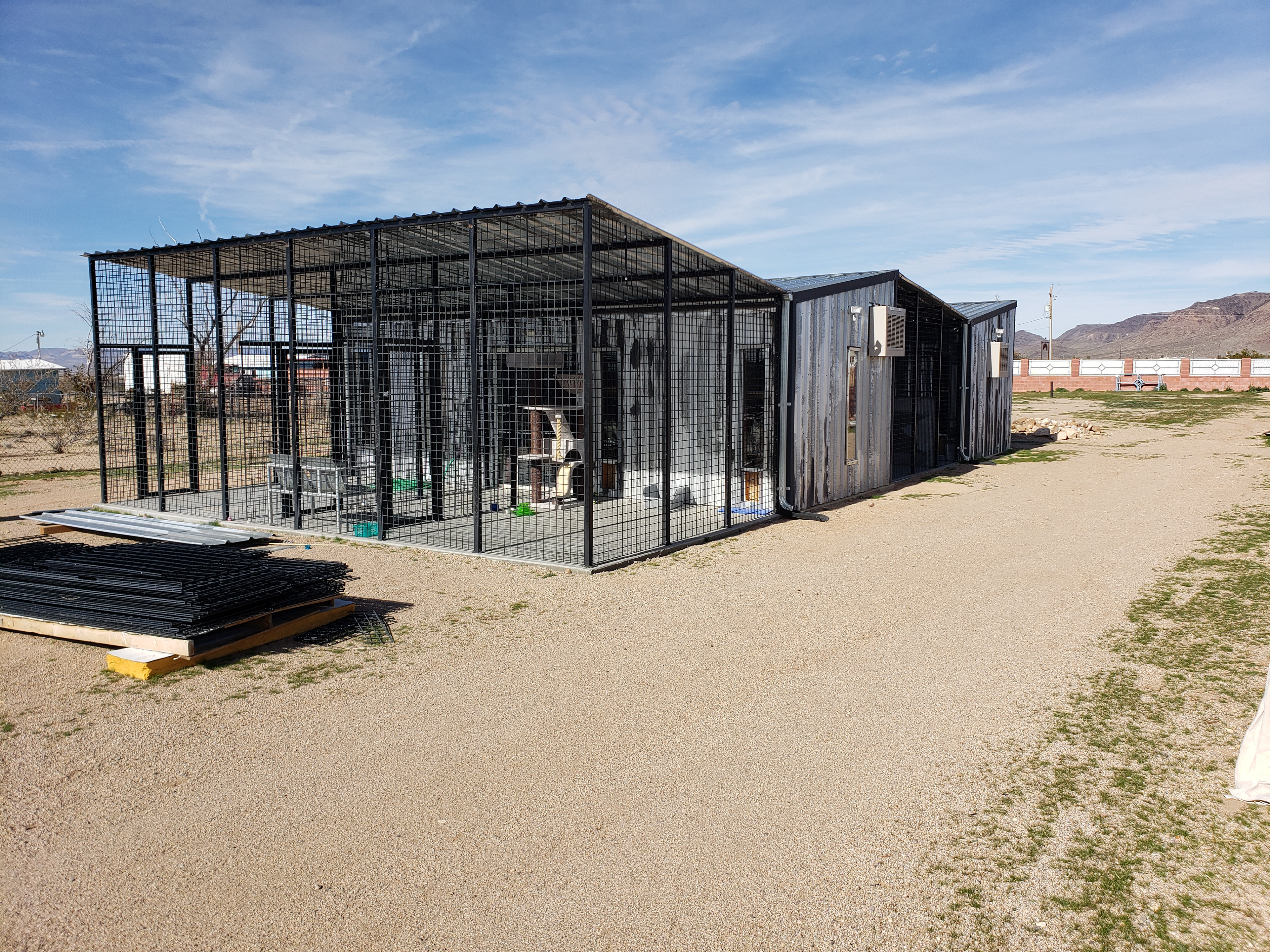
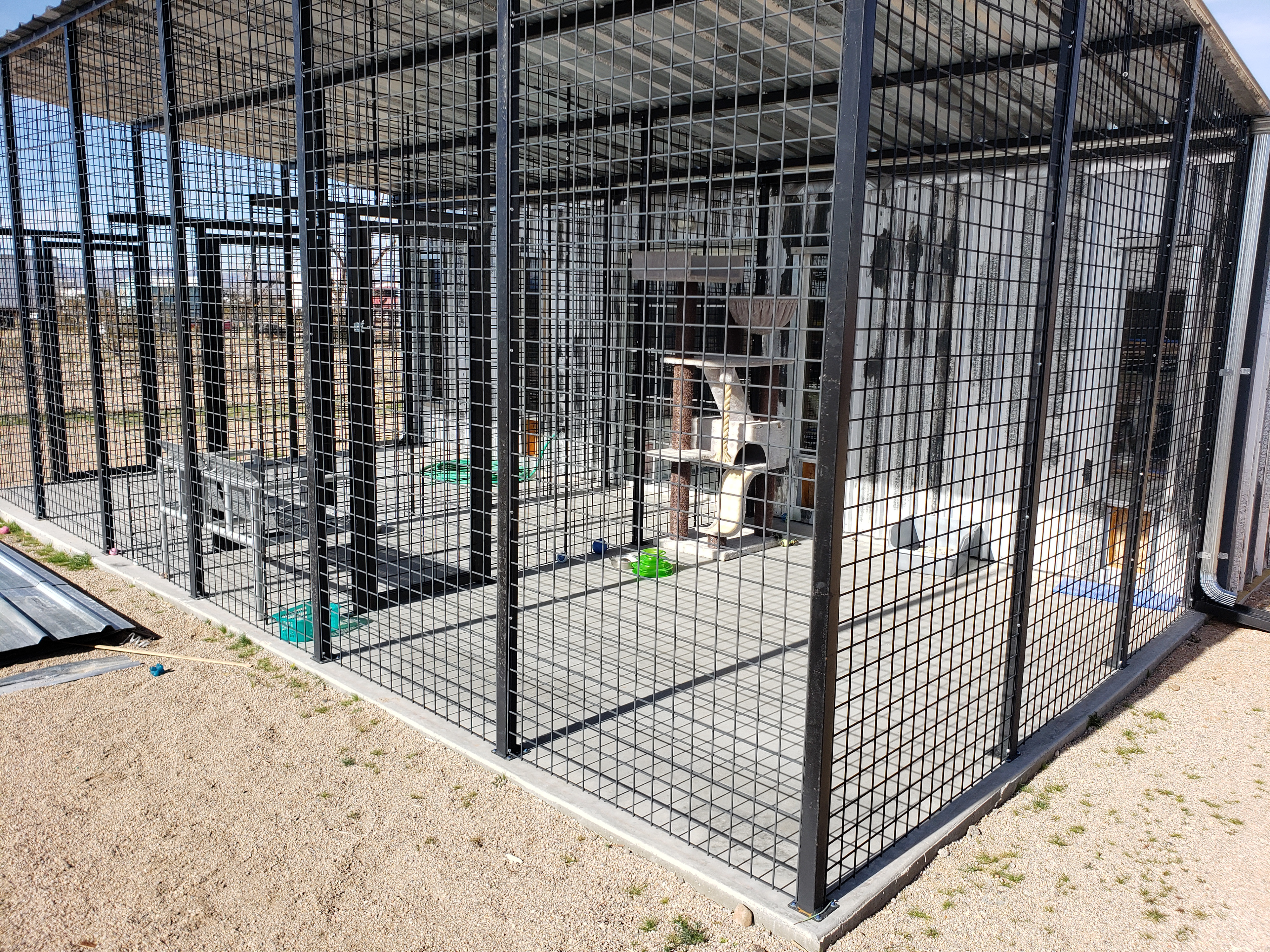
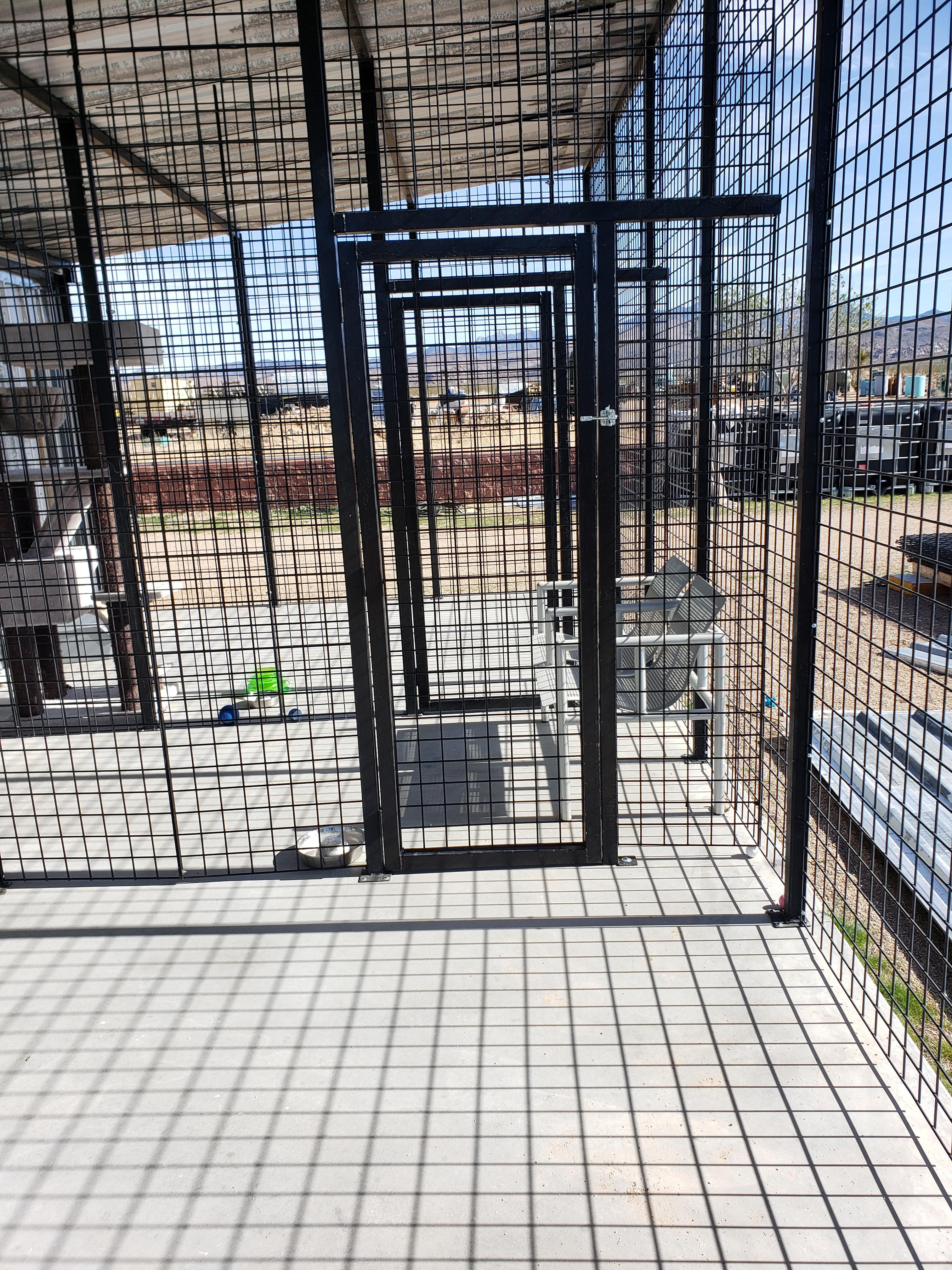
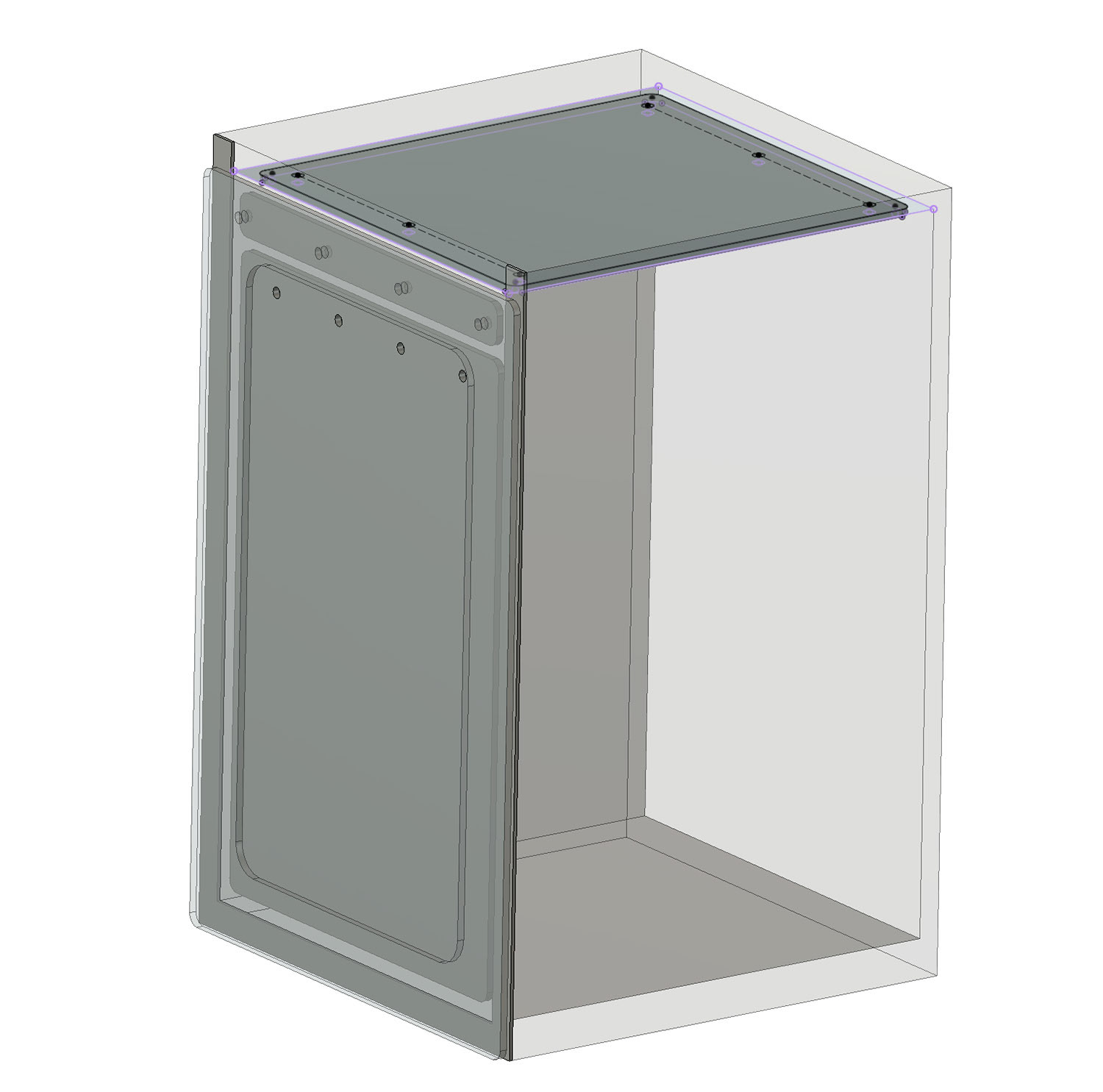
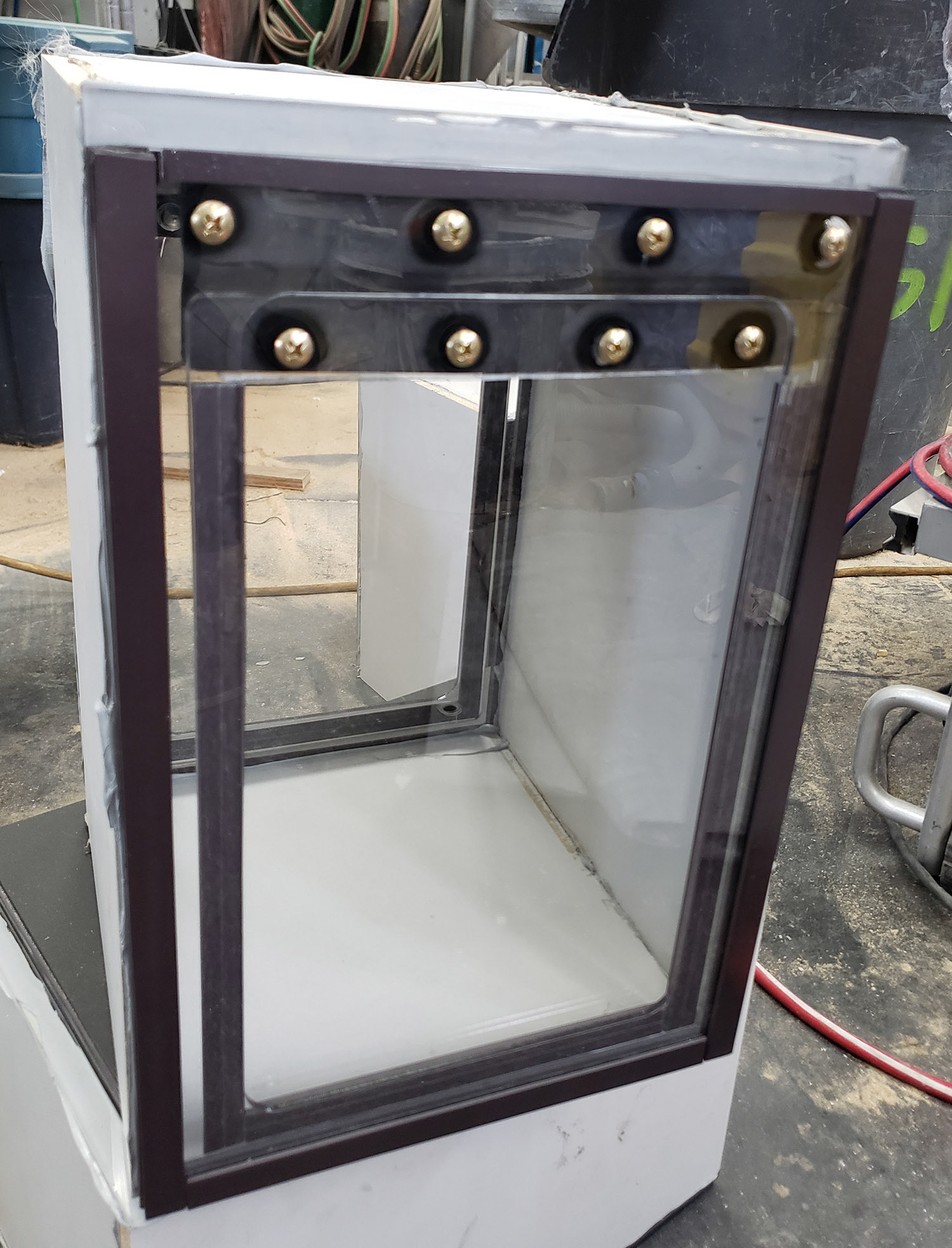
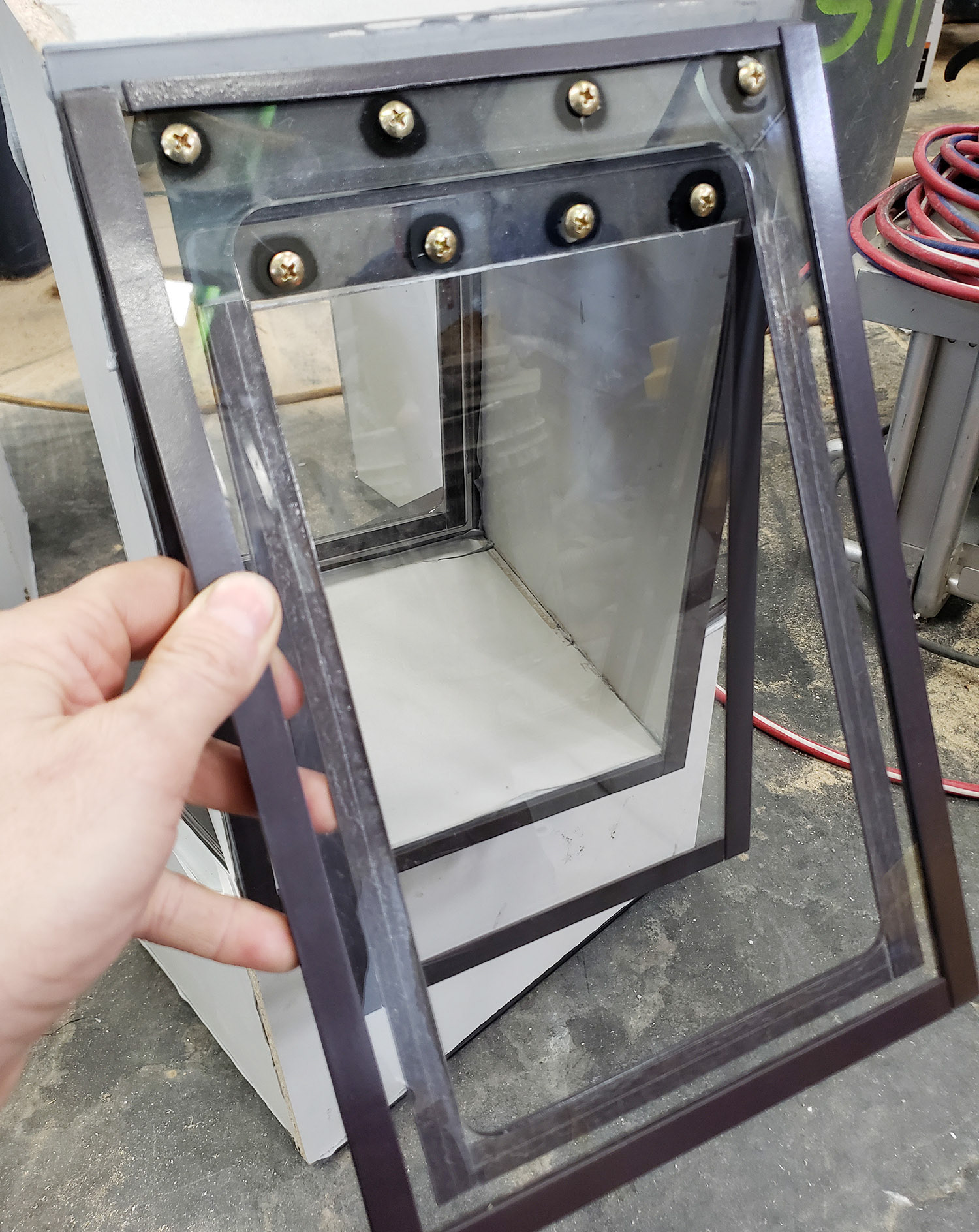