"We choose to go to the Moon in this decade and do the other things, not because they are easy, but because they are hard" - JFK
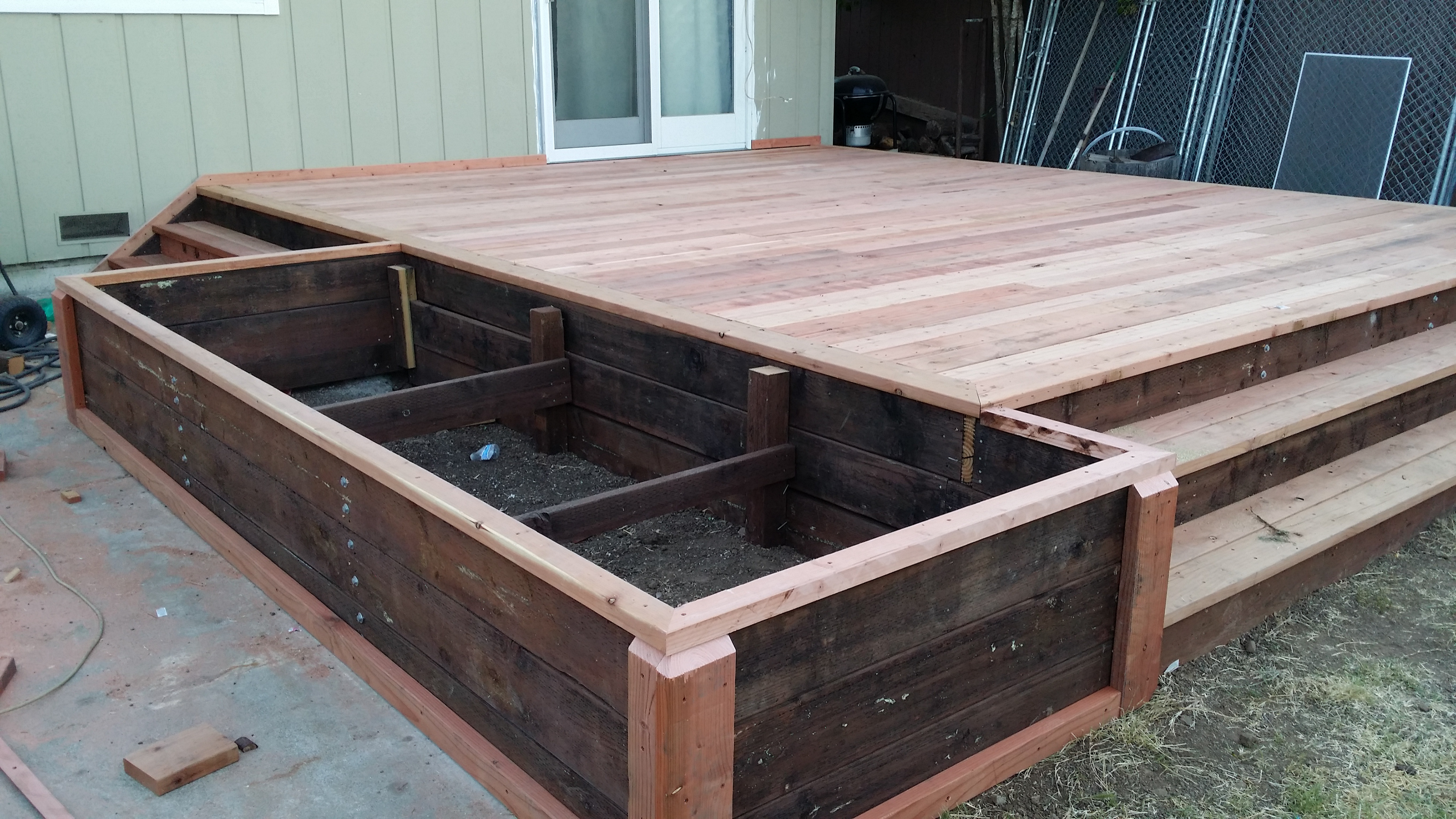
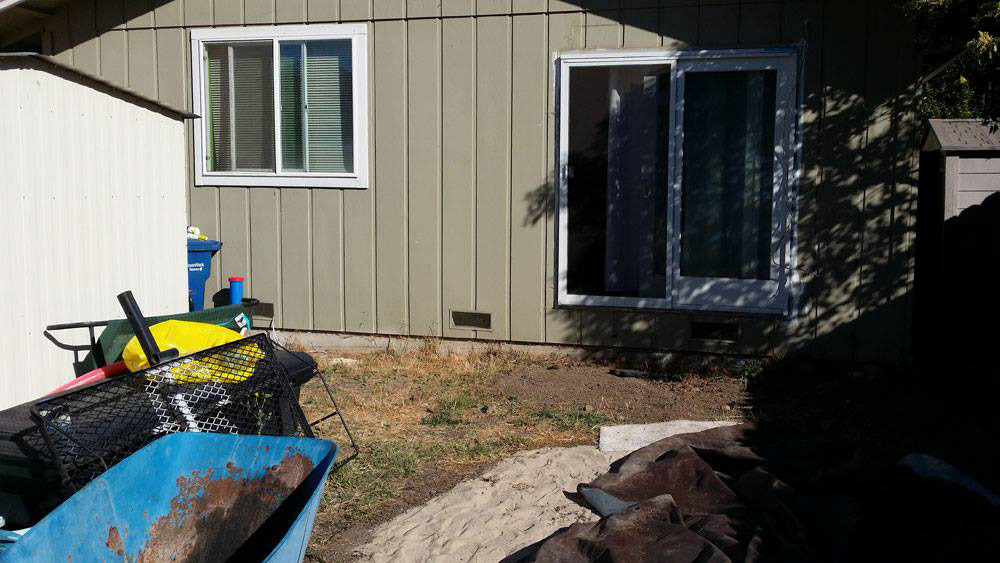
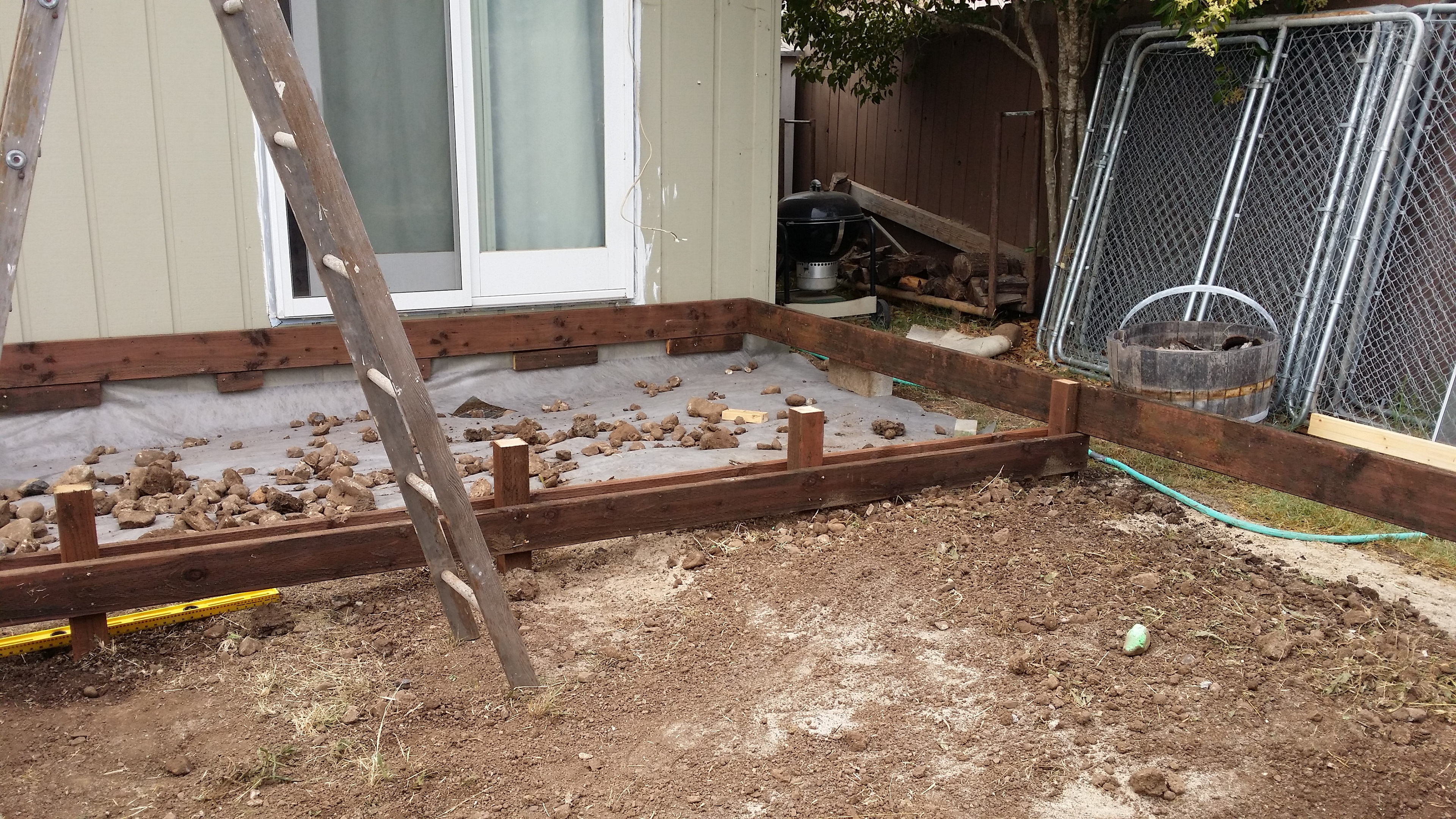
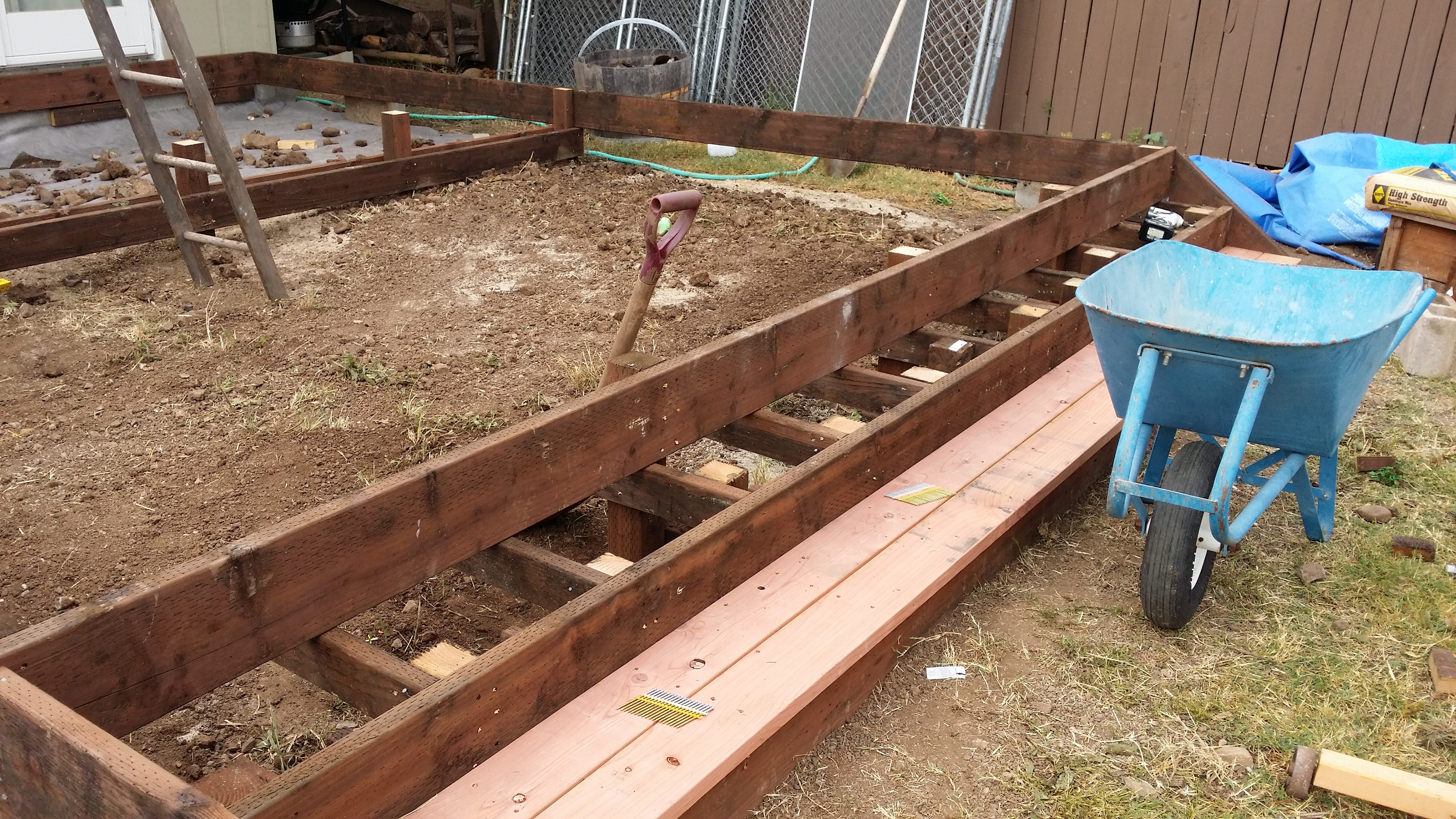
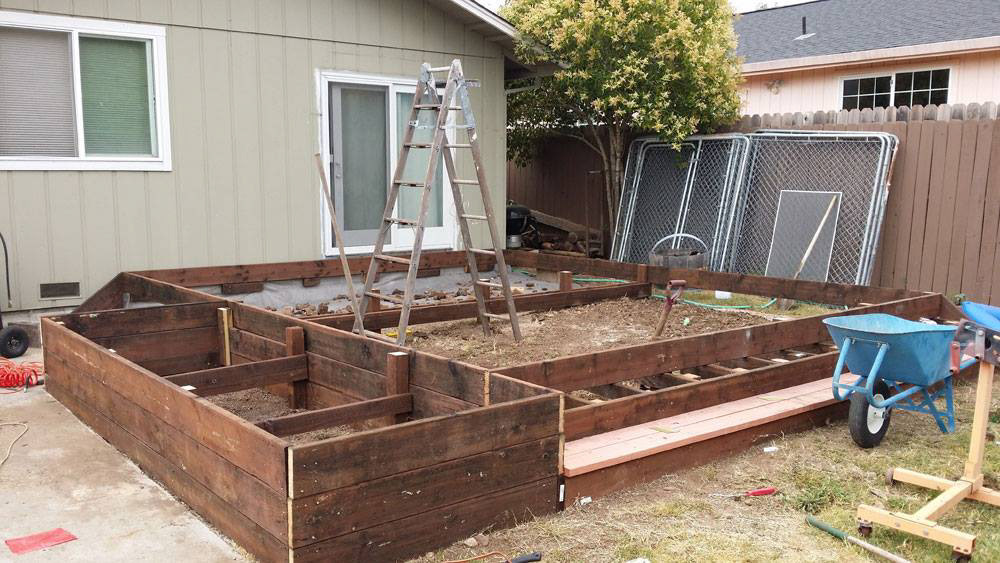
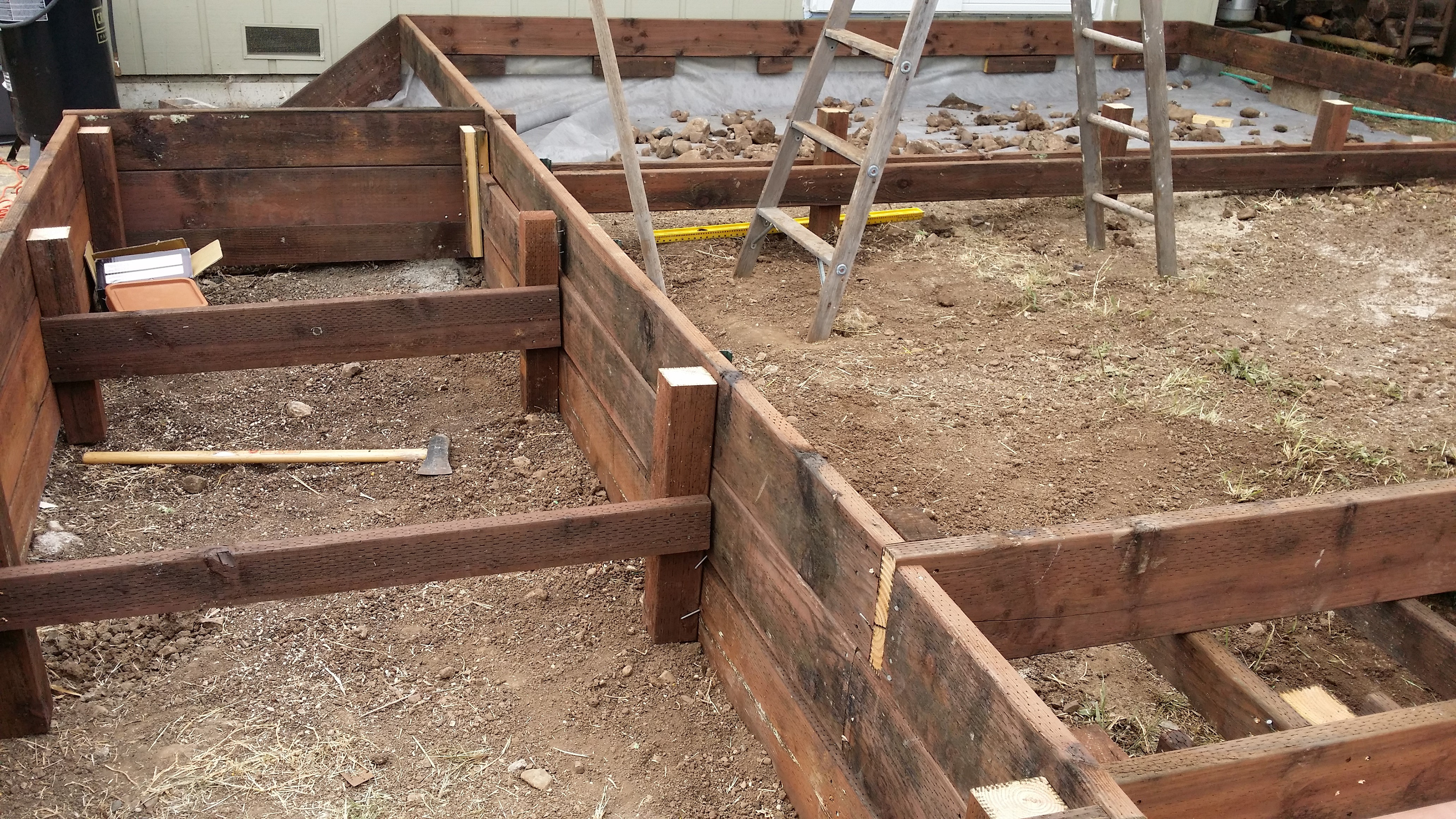
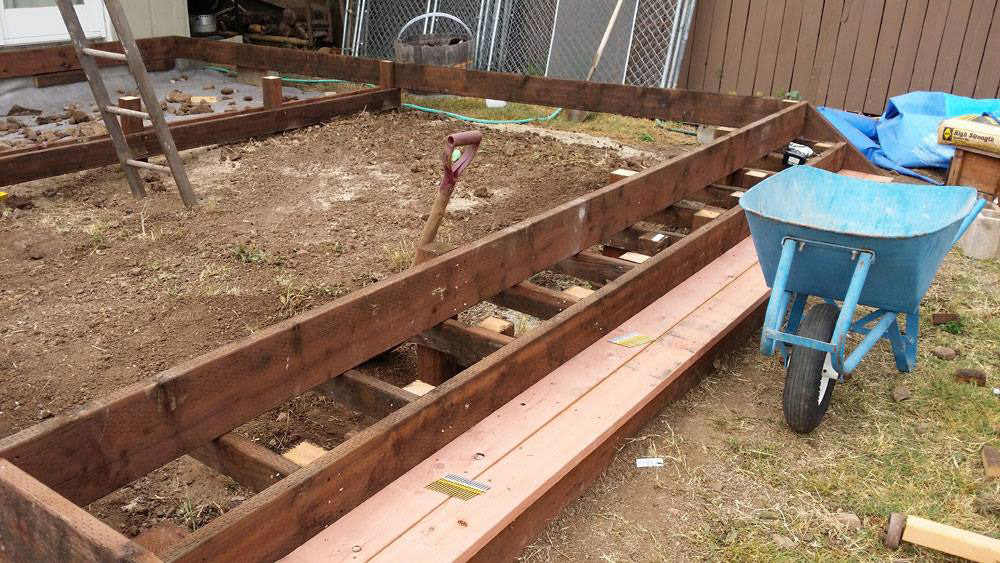
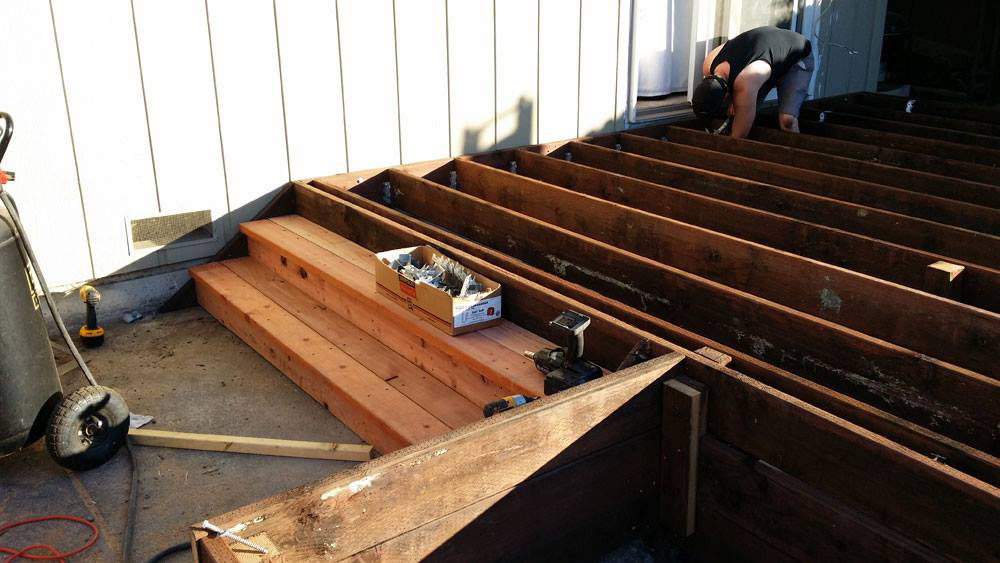
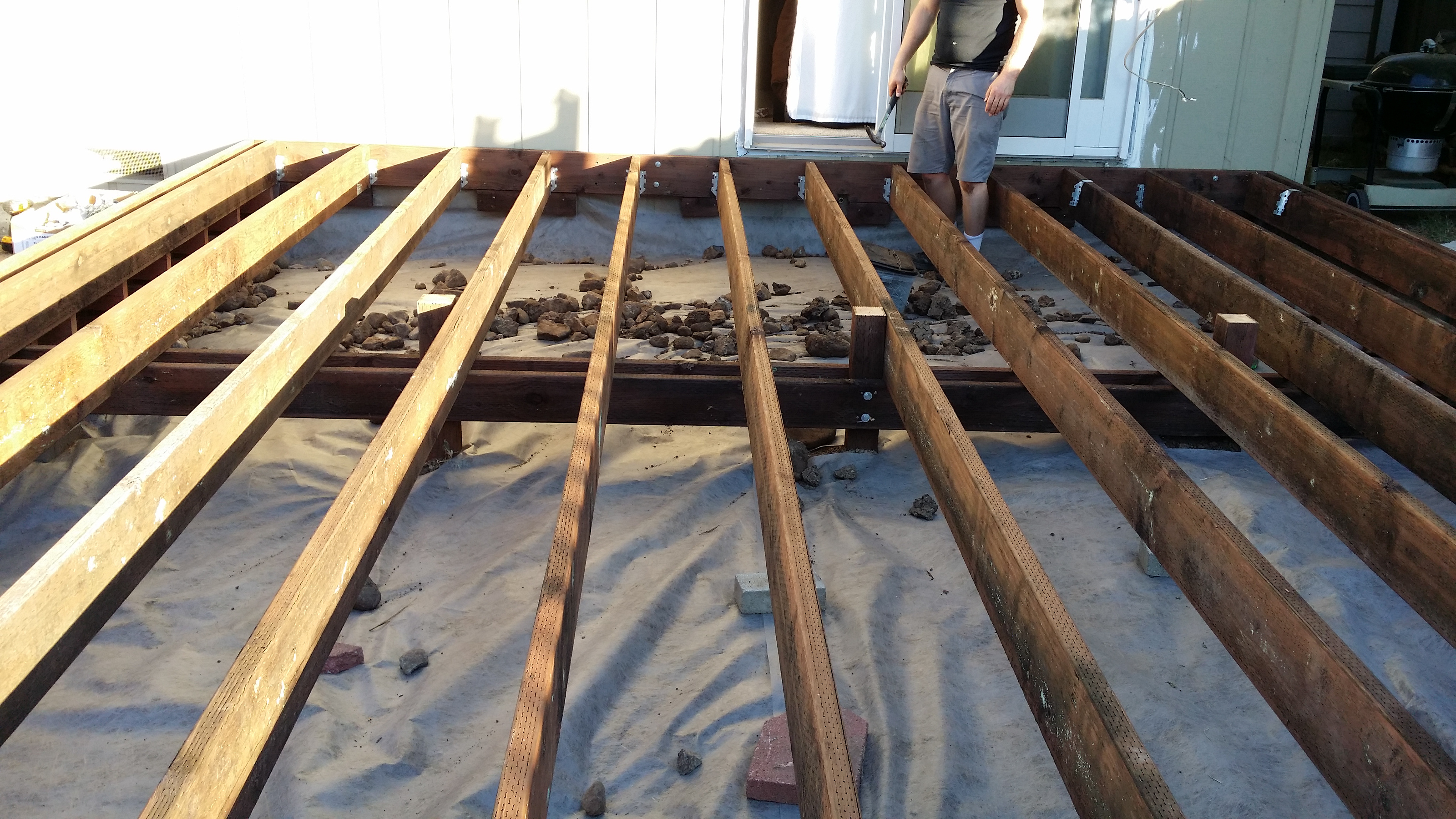
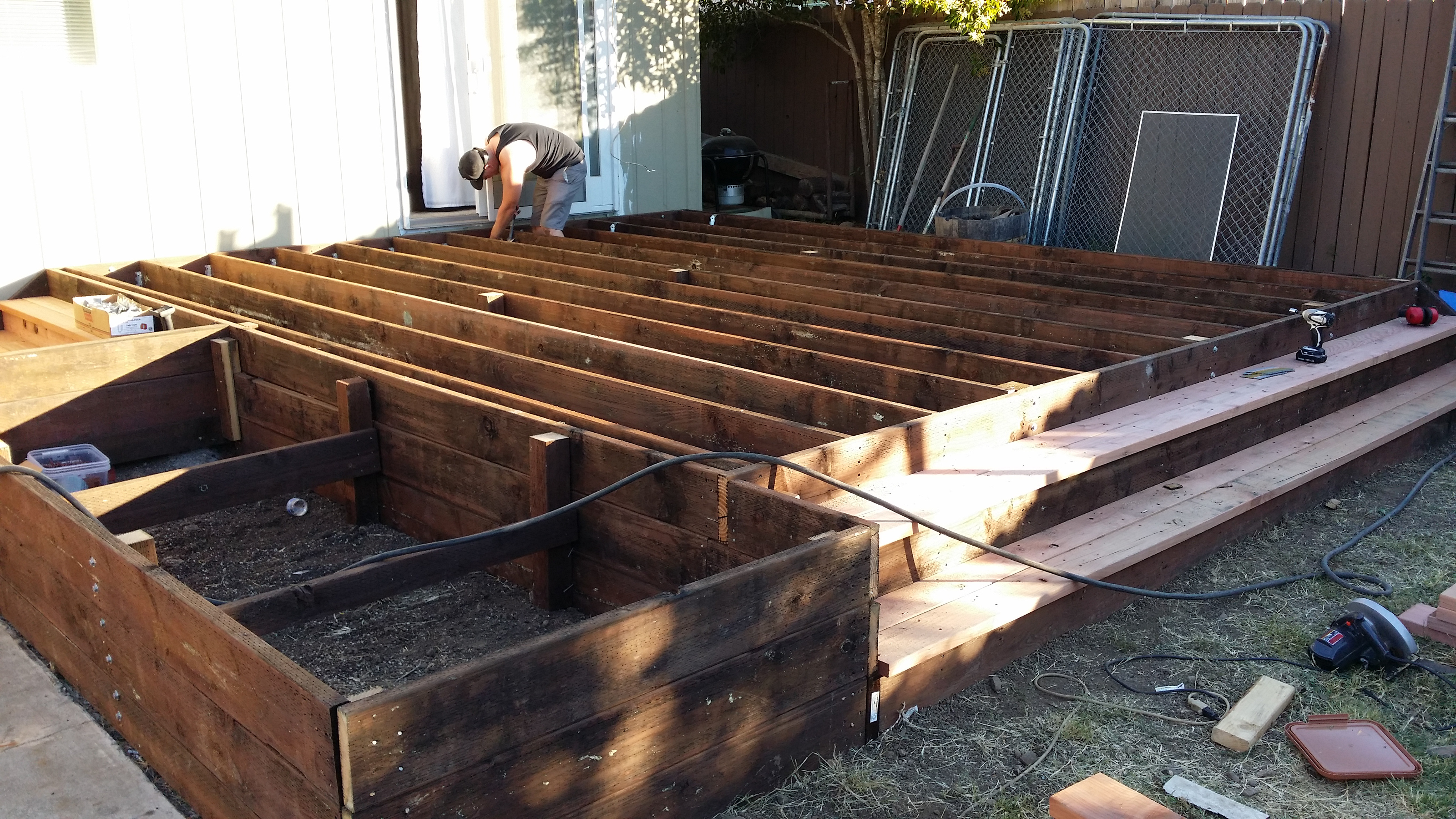
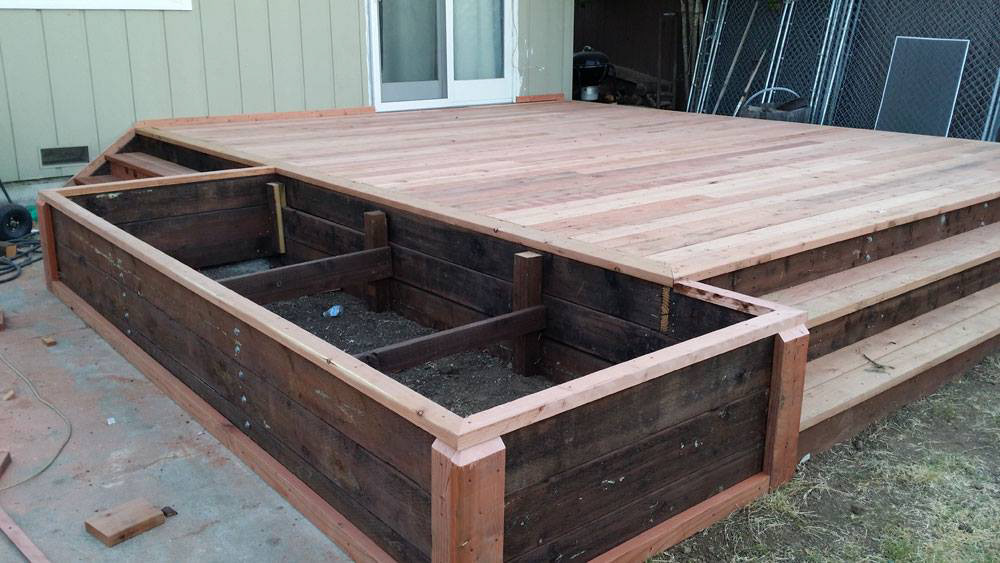
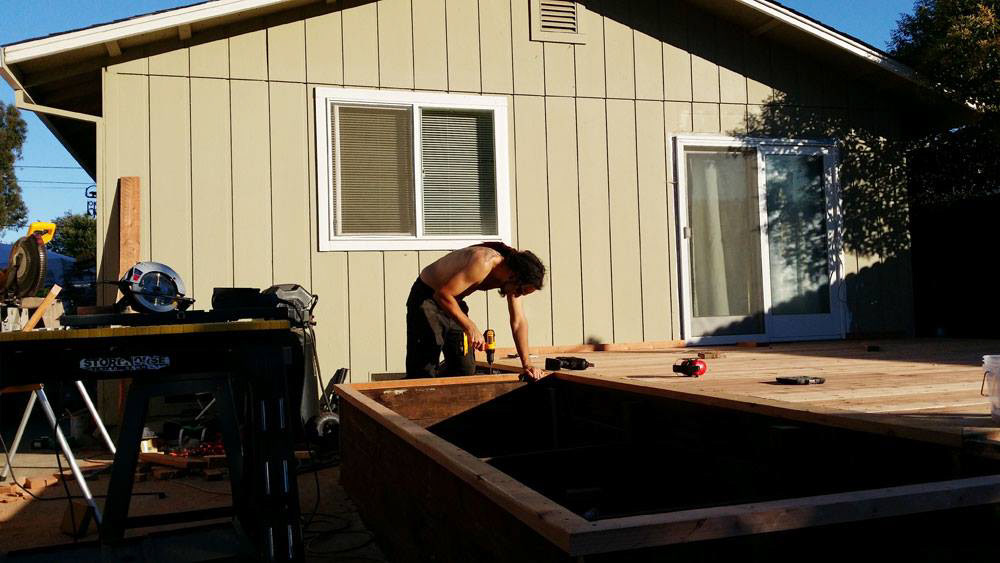
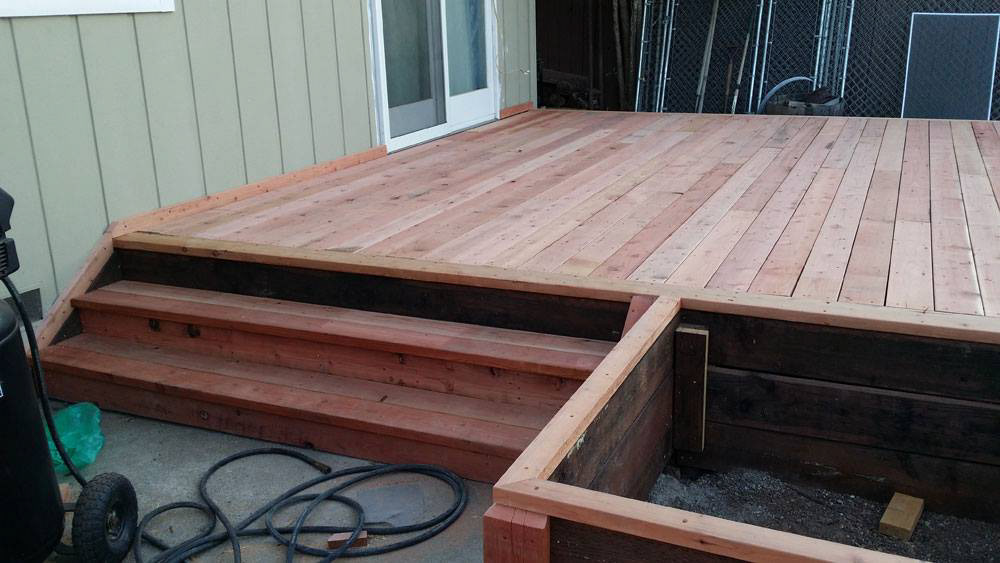
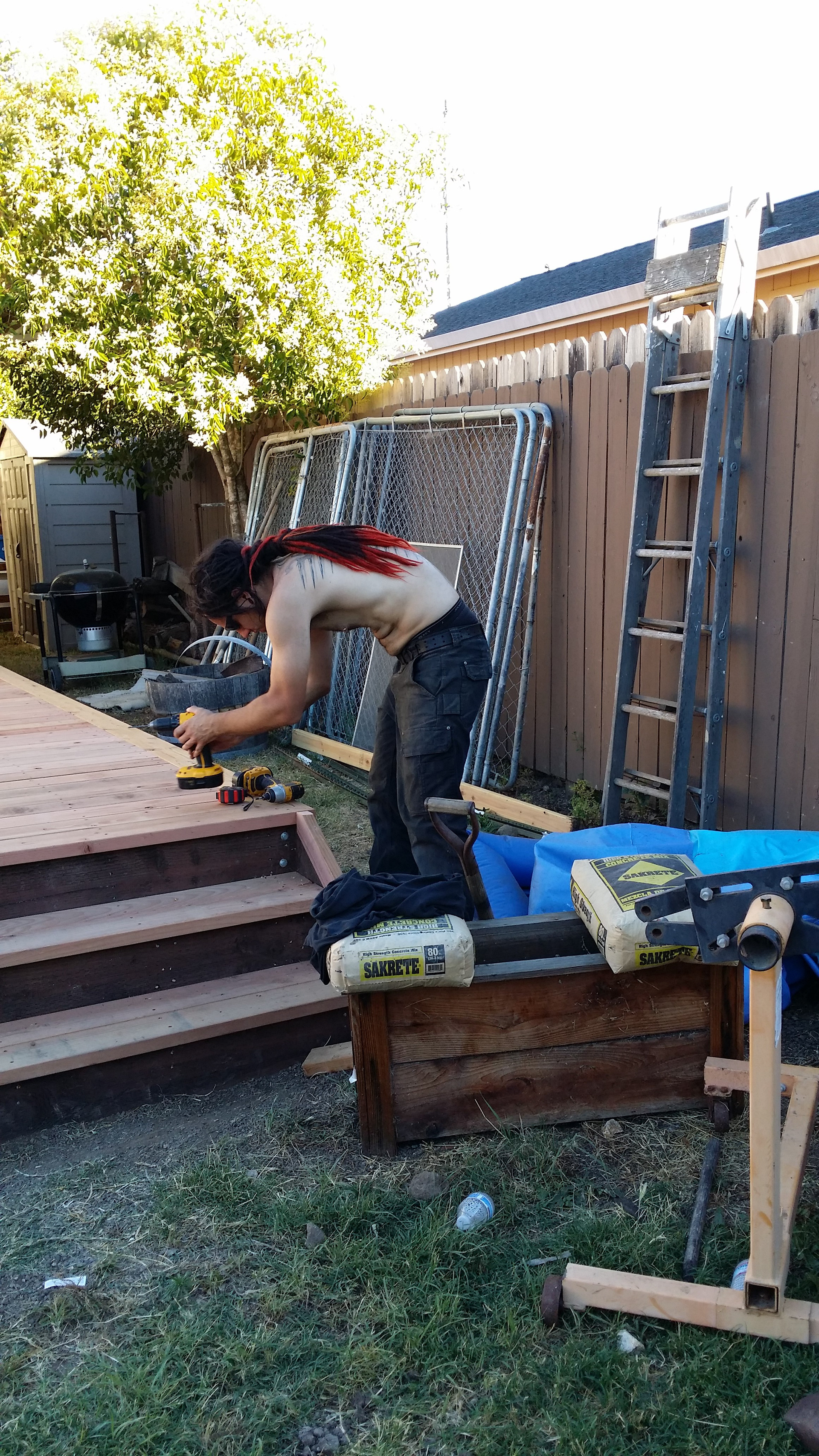
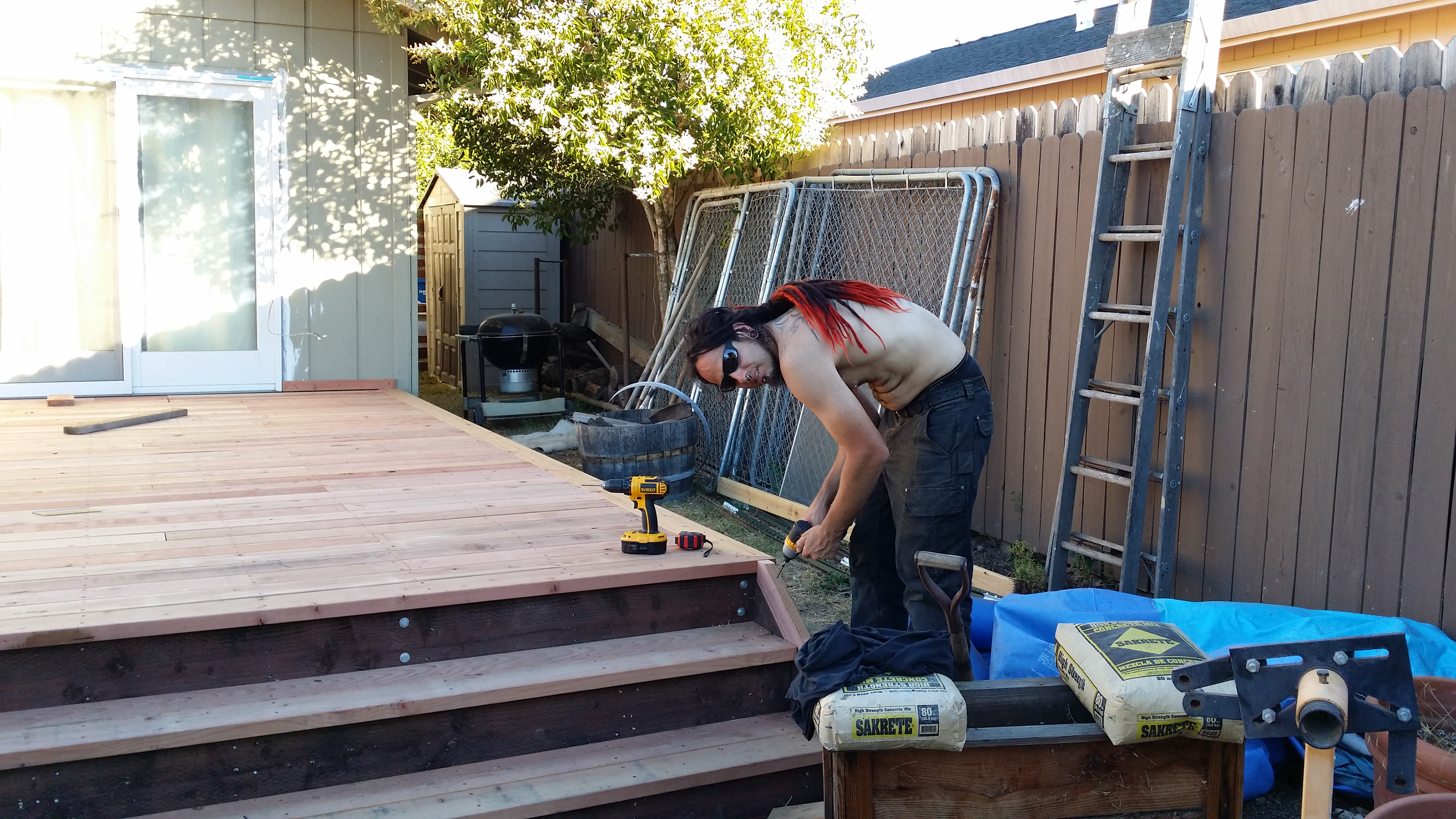
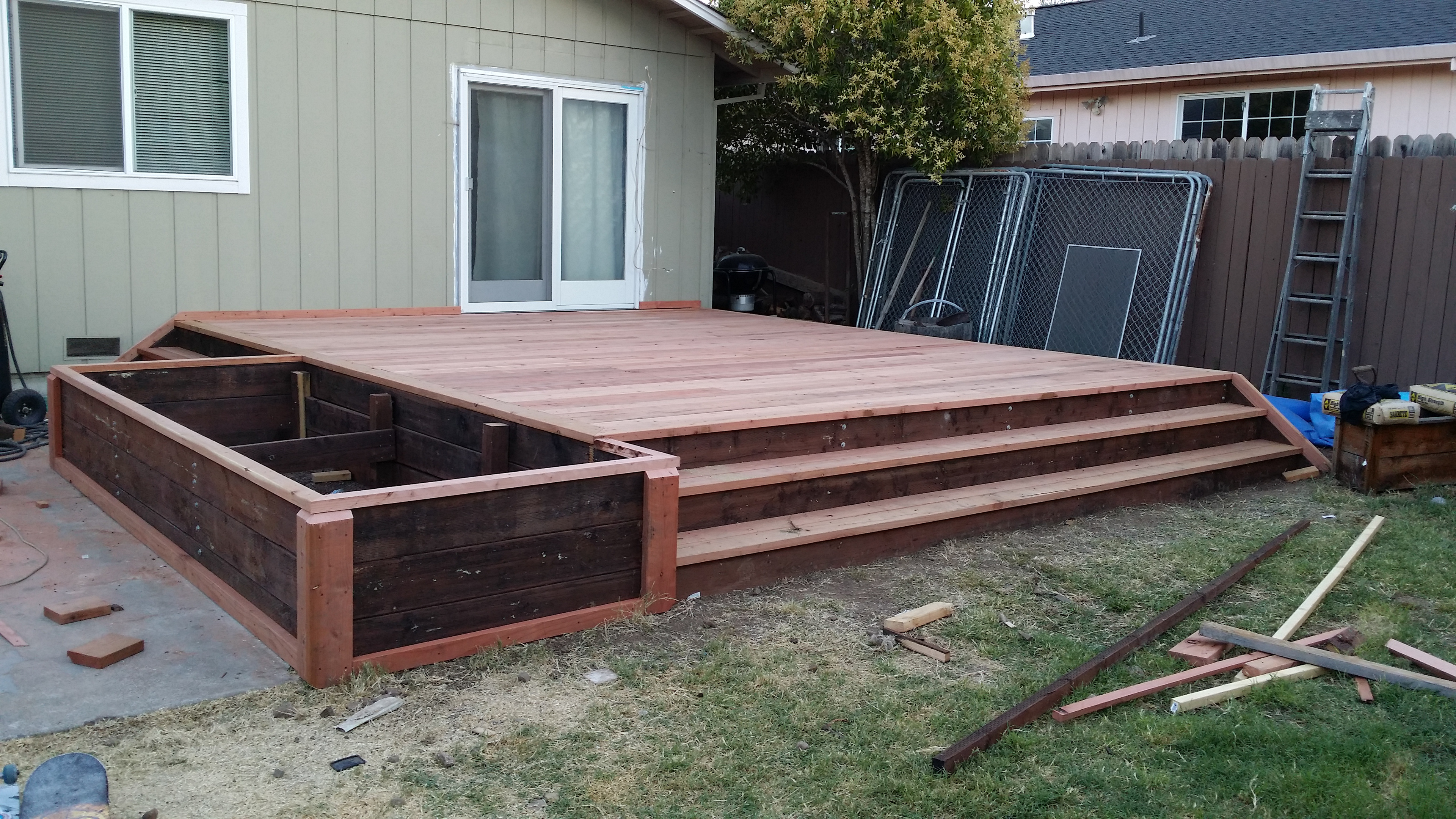
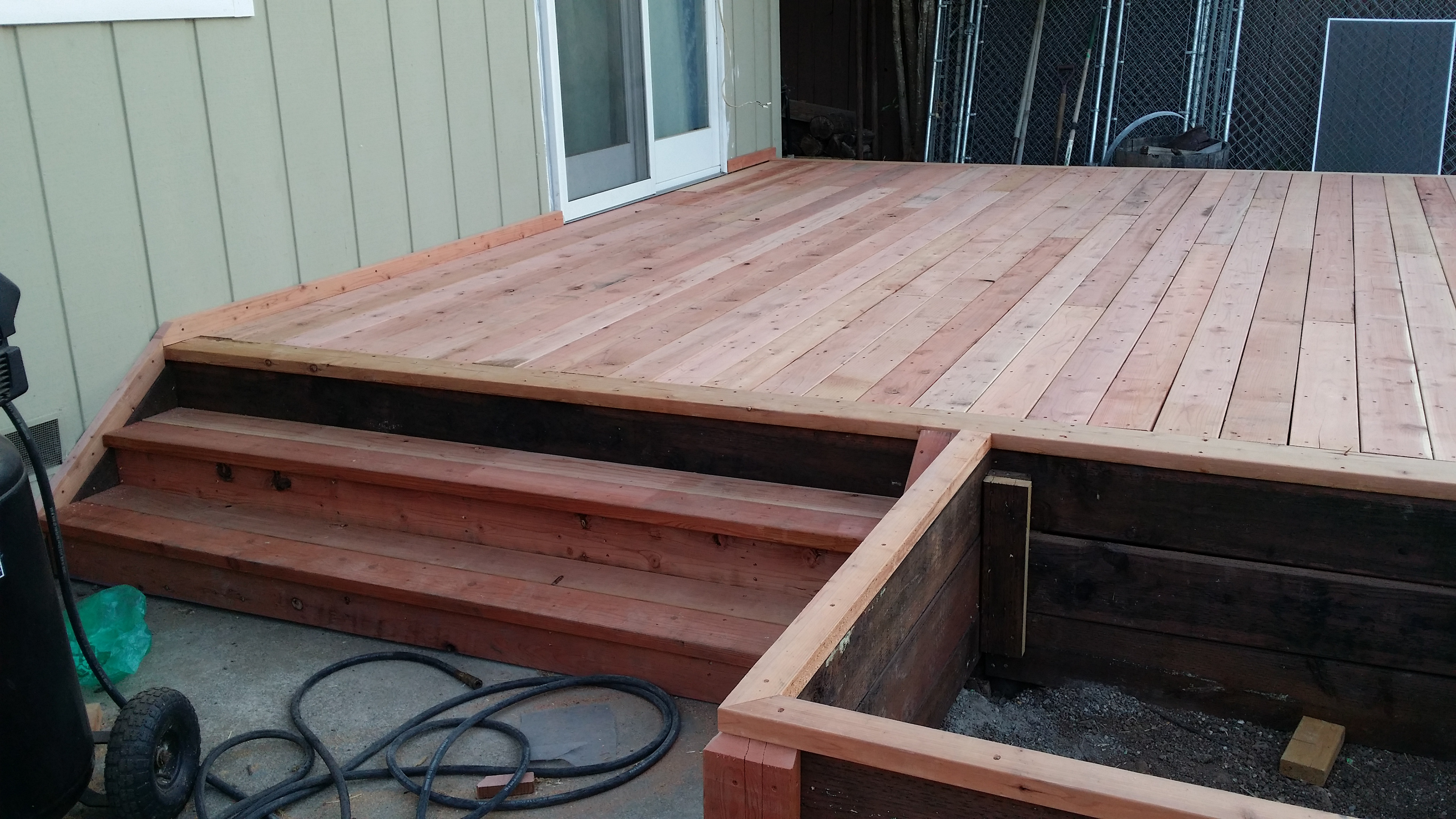
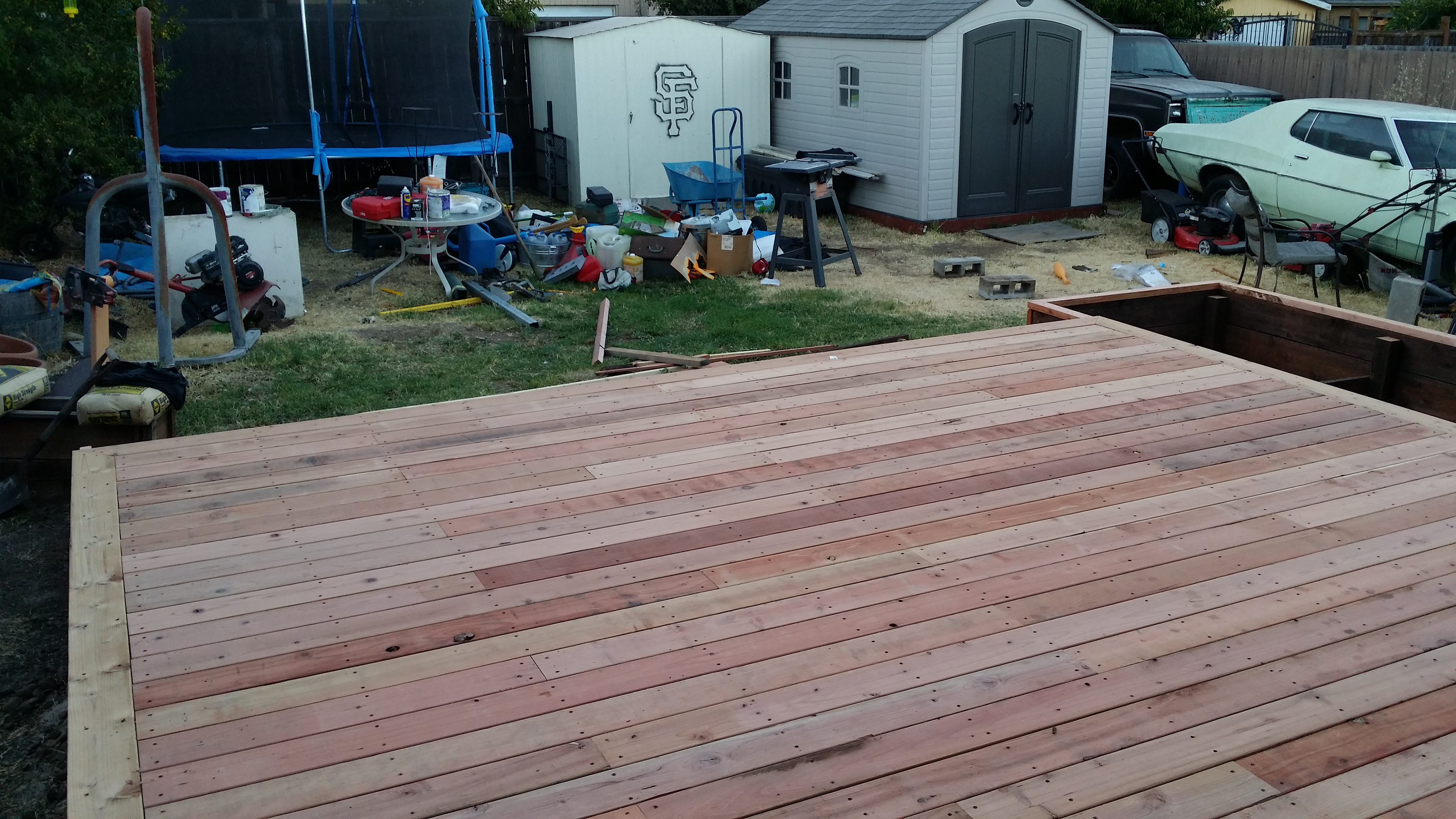
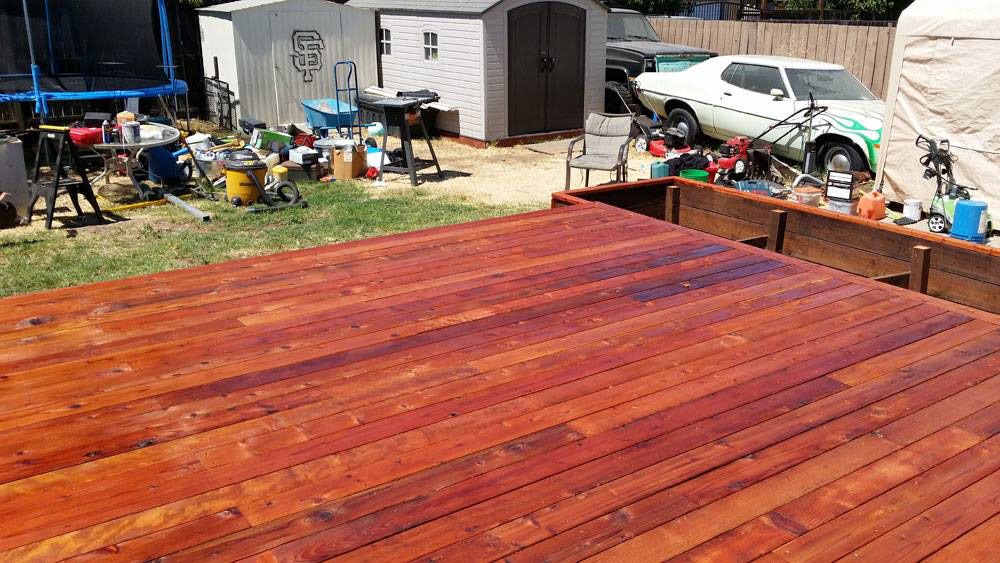
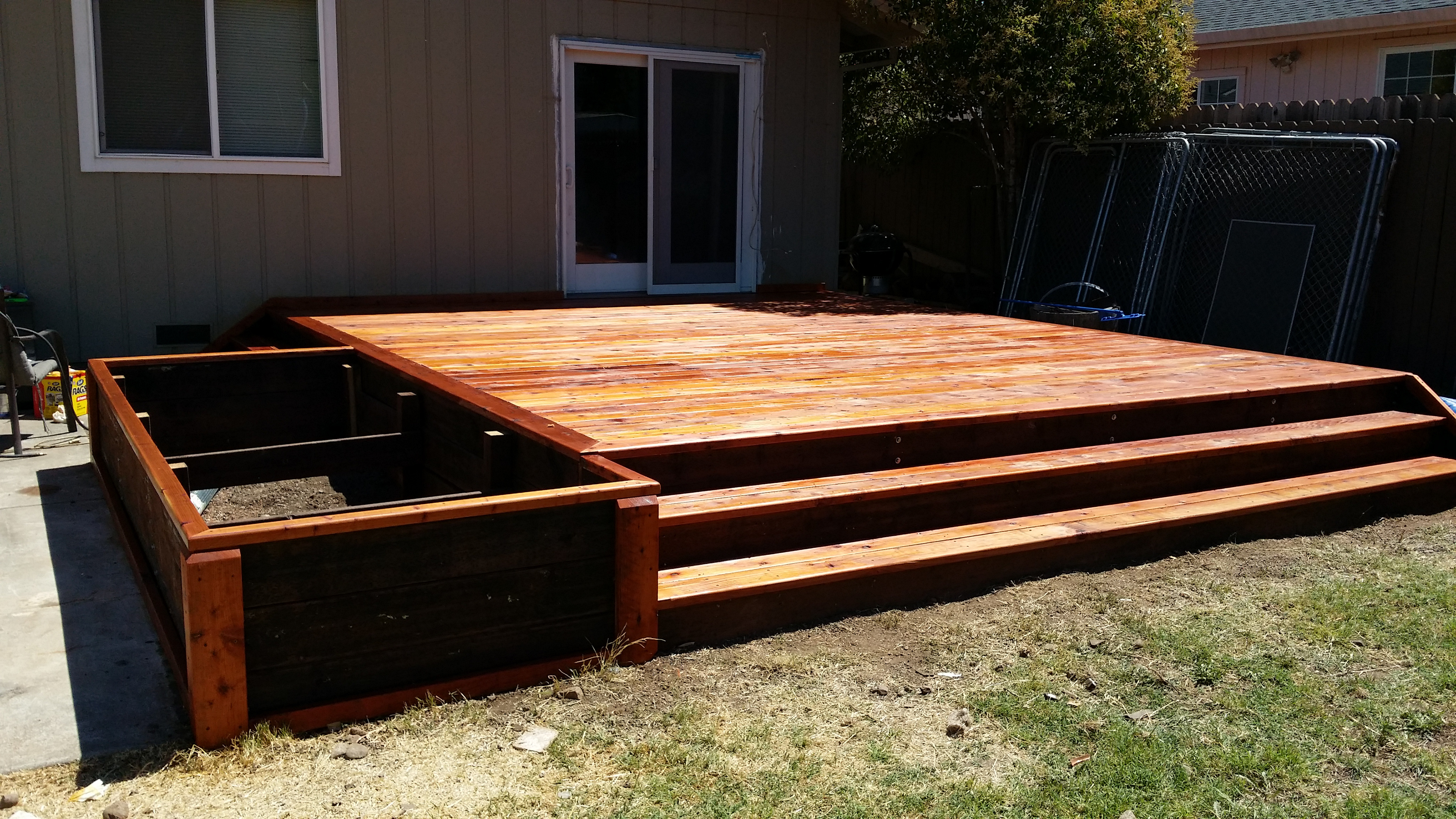
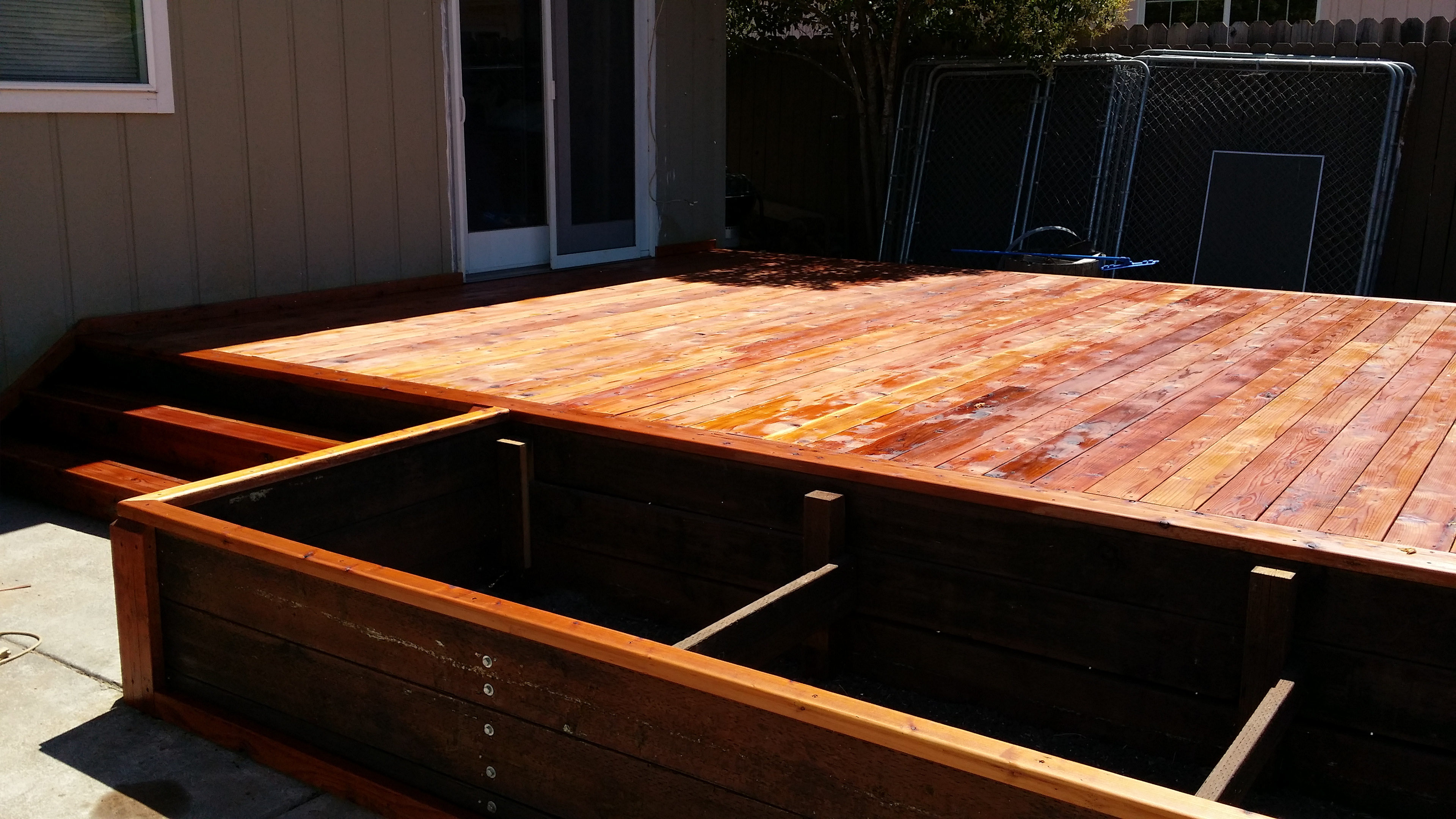
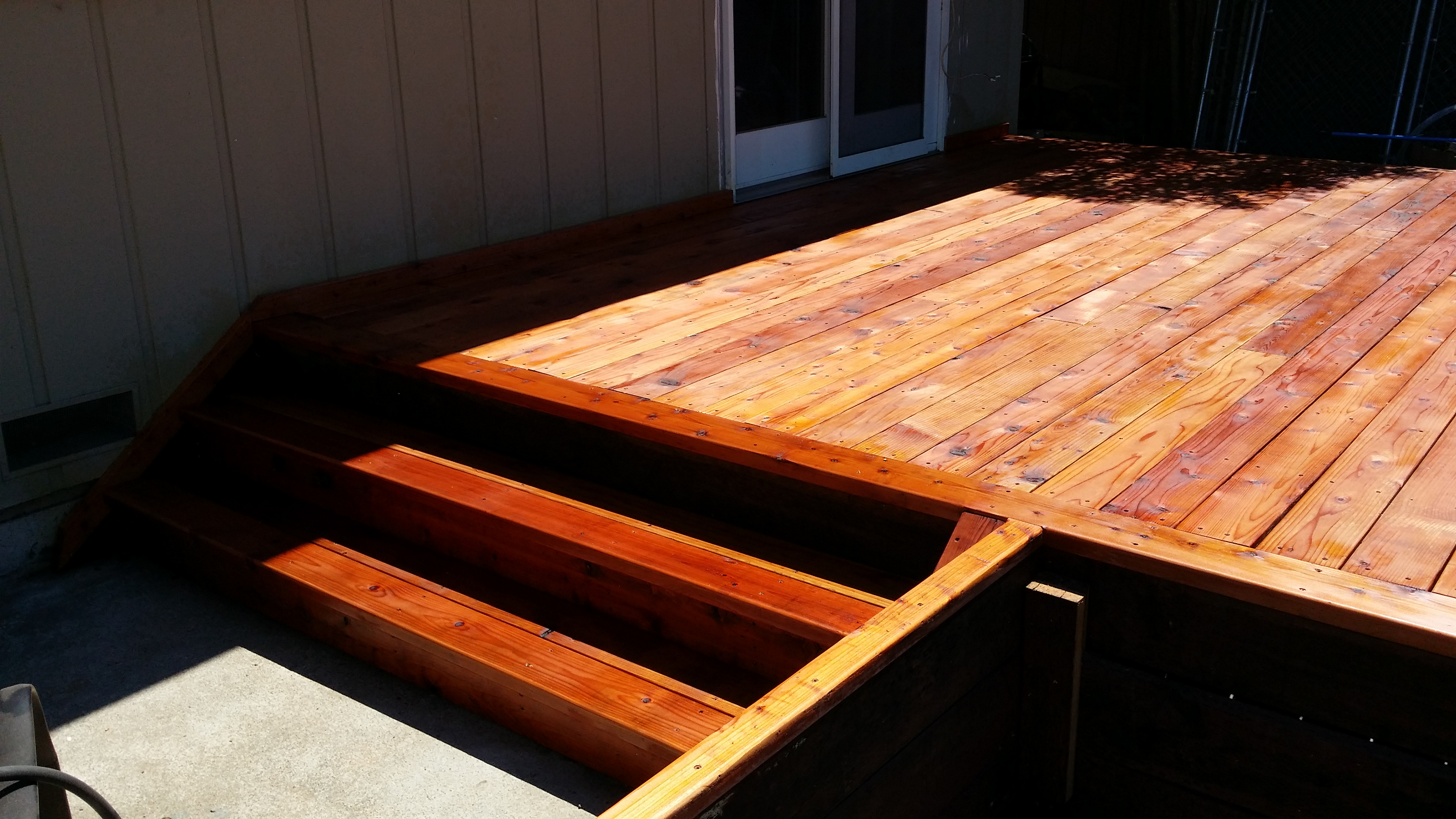
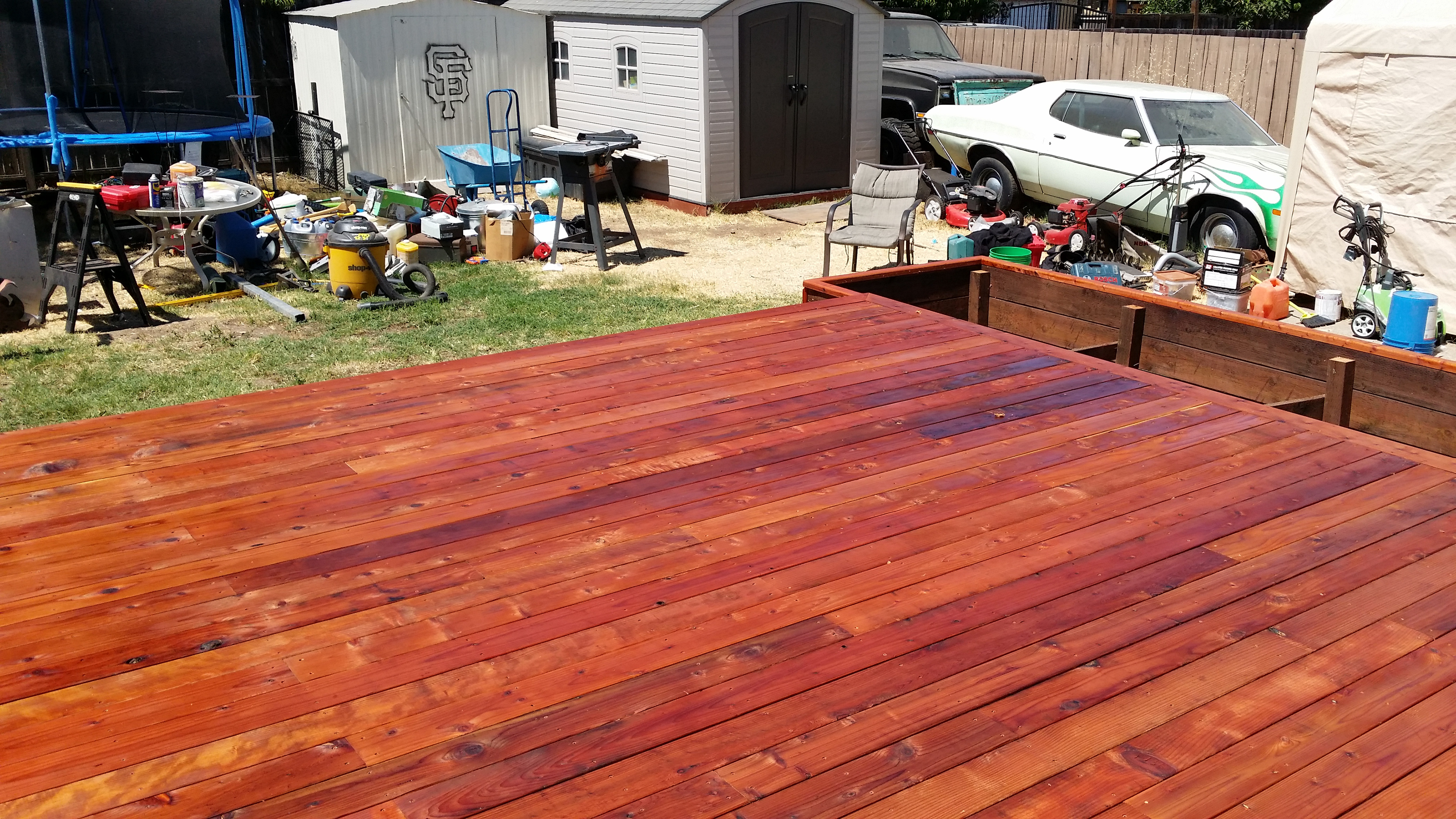
I received a request to make a deck. OK, I though, I have seen This Old House a few times. While this did not immediately elicit confidence, I had a secret weapon... YouTube.
After a hour or so of cramming my head with the best the Internet could offer, I felt confident that I had the skills to make a pile of wood sit 2 feet higher. After all, it was sitting on the ground with almost no effort at all. It seemed like I was already halfway there.
So anyhow, I purchased a bunch of treated wood and a big stack of redwood 2x6s. Thirty pounds of deck screws and a bunch of cuts later, there was a deck. I even had enough redwood left to trim out the planter.
So anyhow, I purchased a bunch of treated wood and a big stack of redwood 2x6s. Thirty pounds of deck screws and a bunch of cuts later, there was a deck. I even had enough redwood left to trim out the planter.
Done and done.
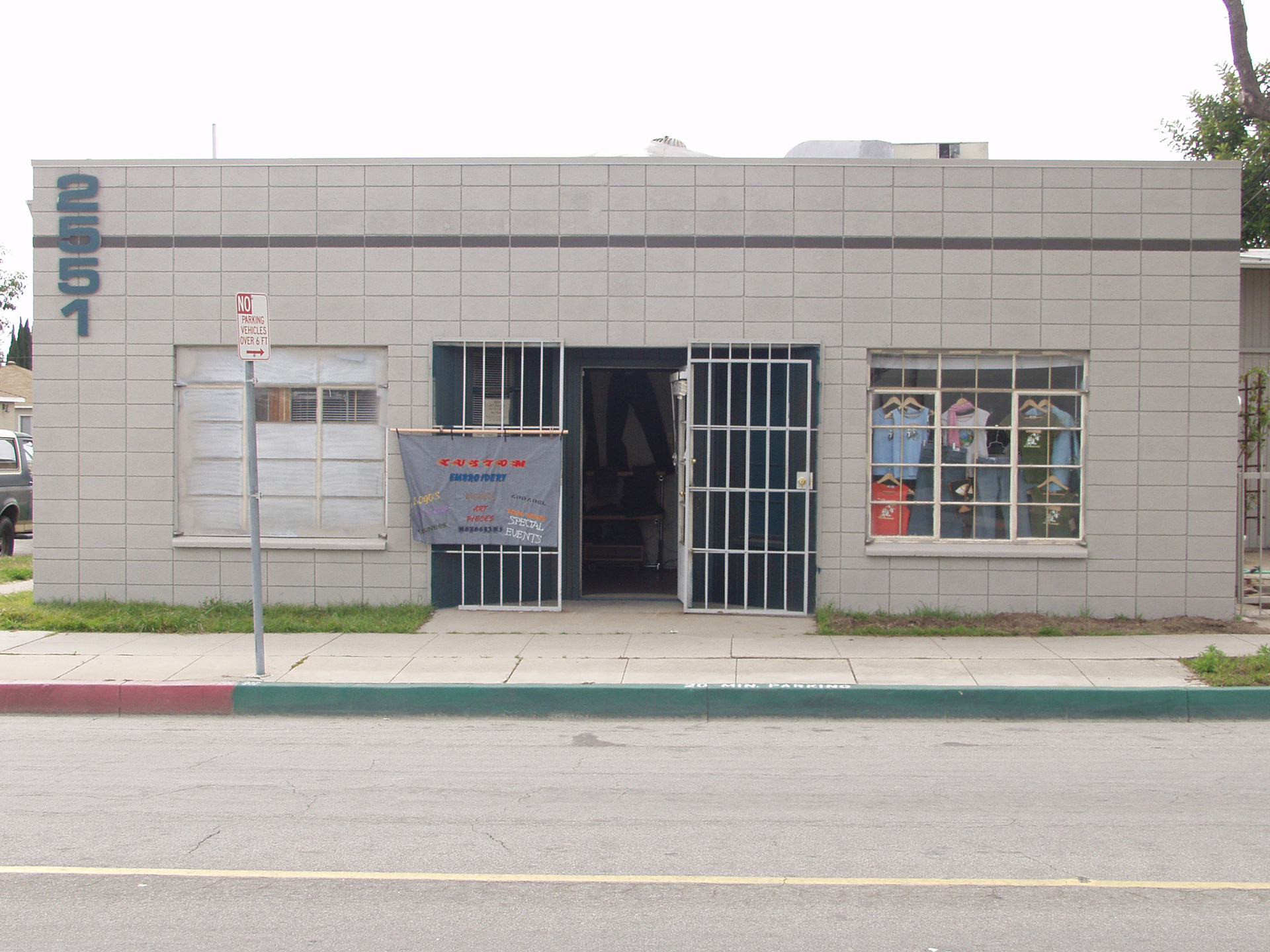
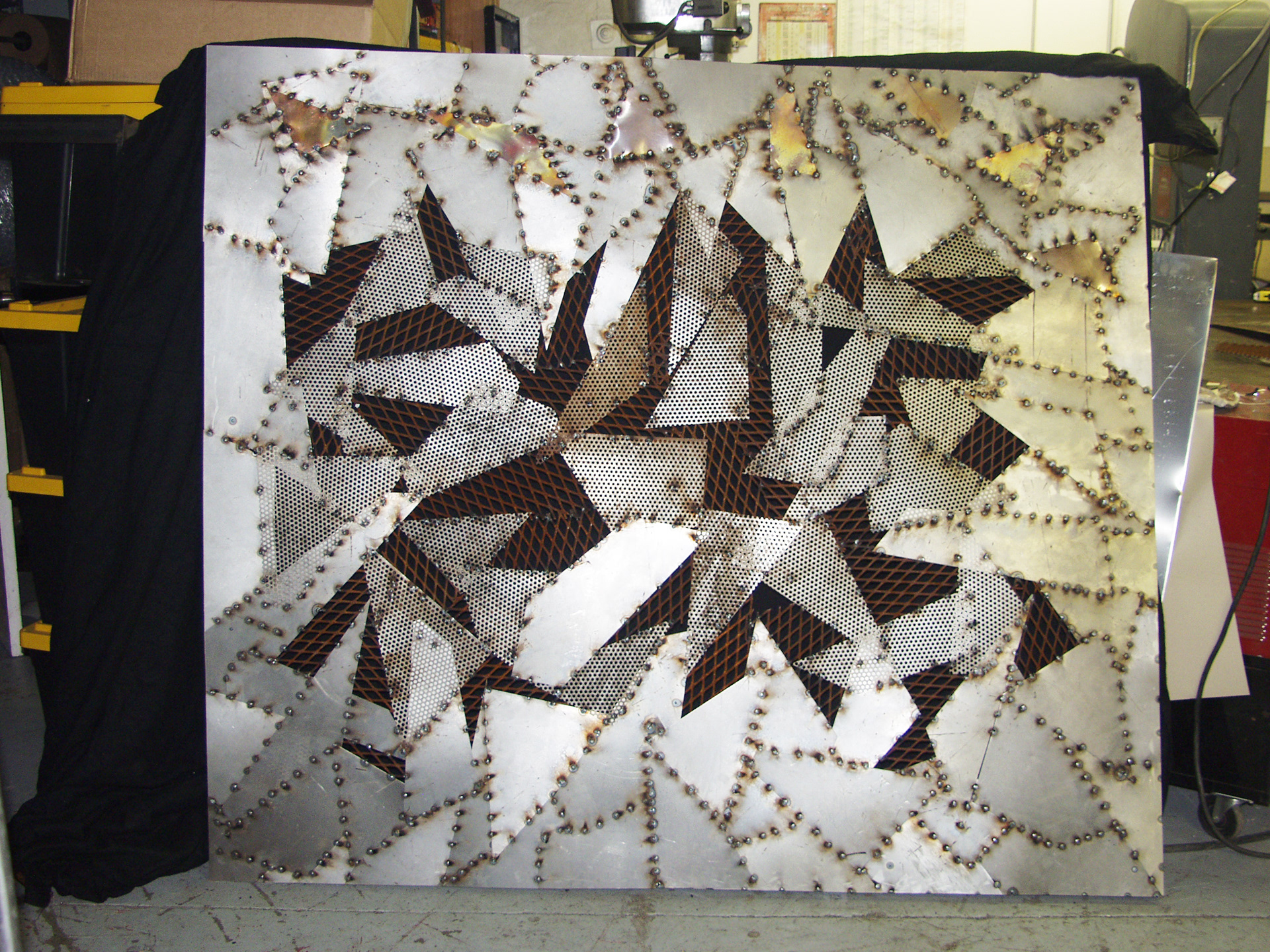
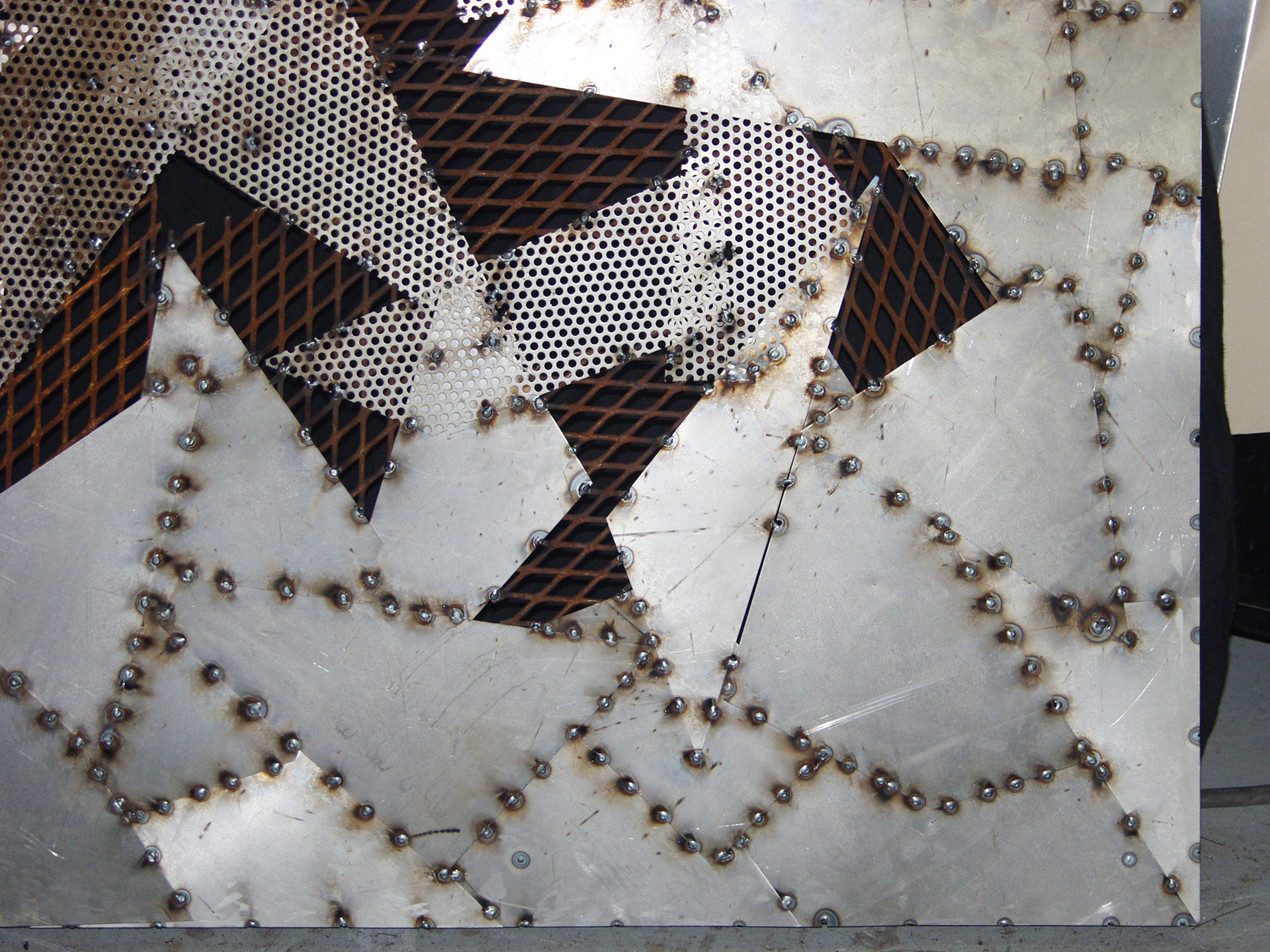
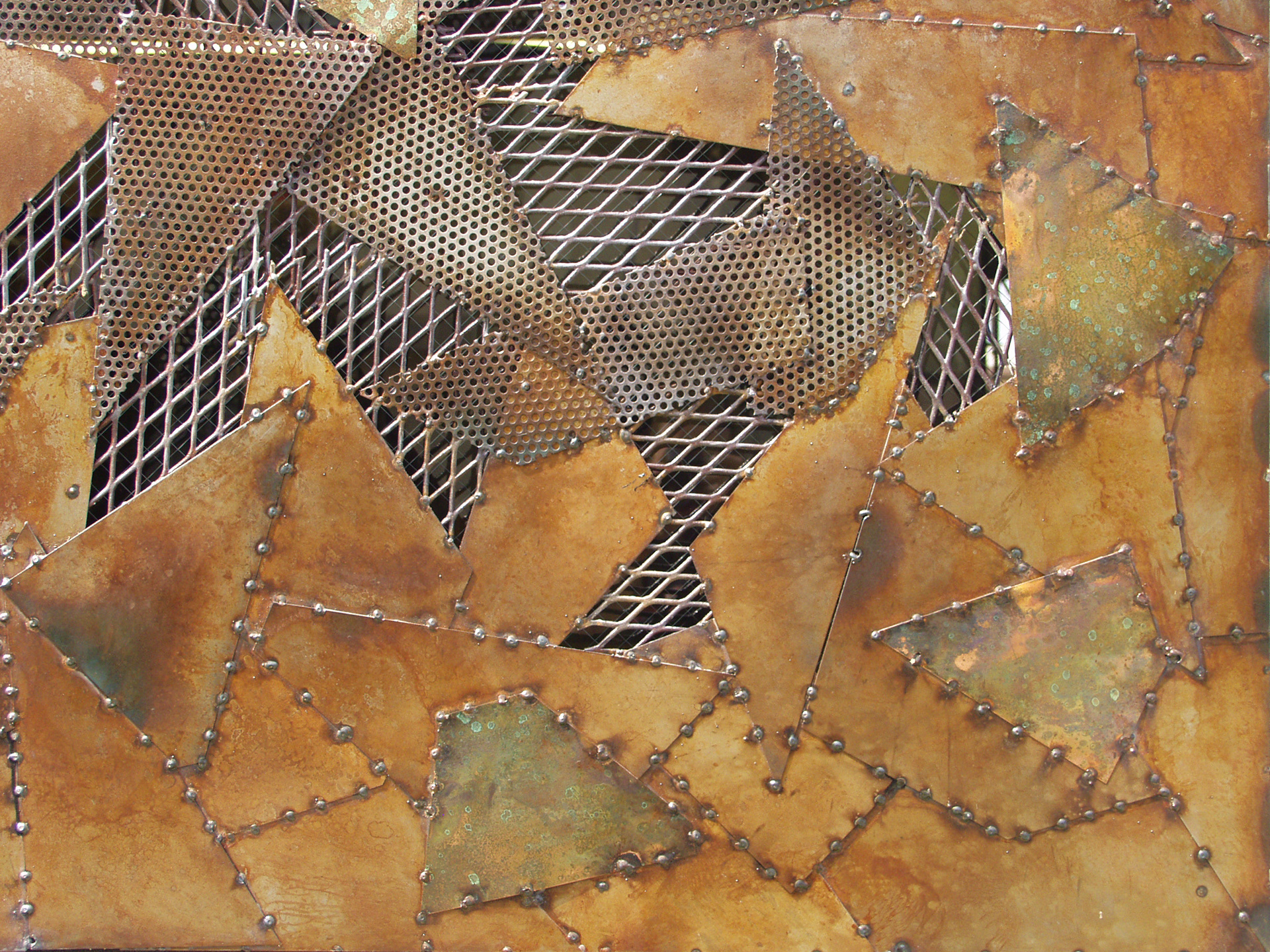
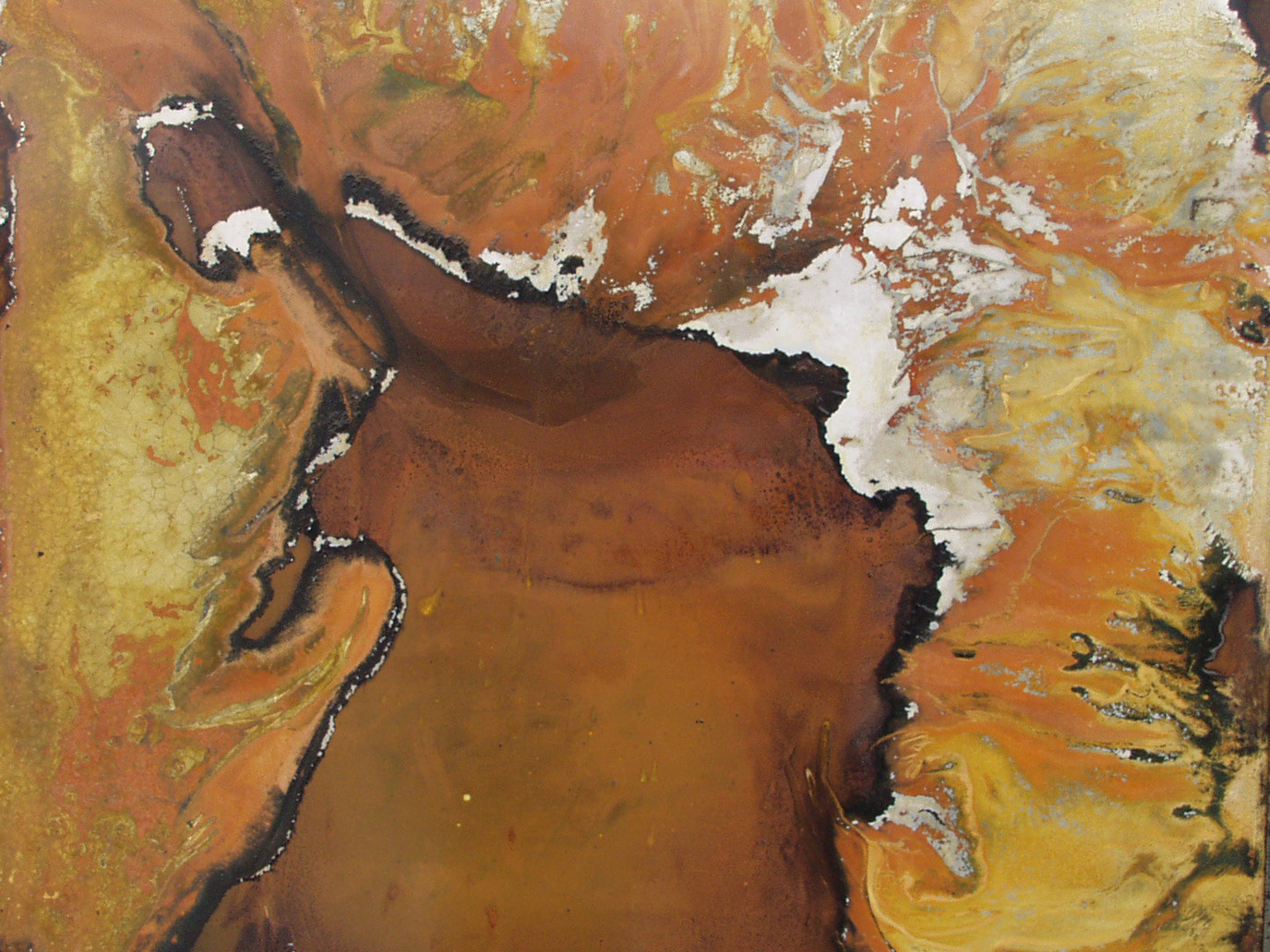
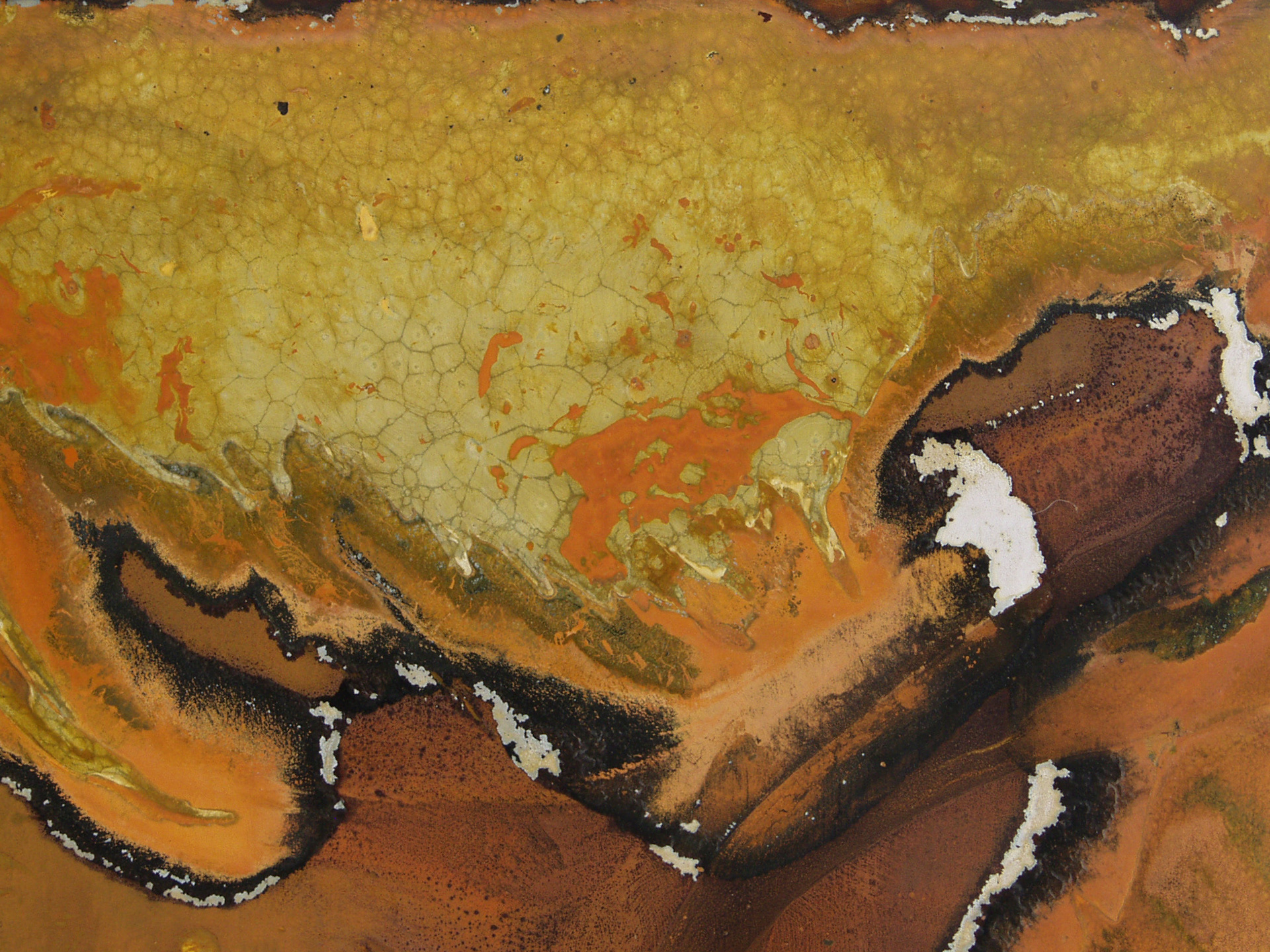
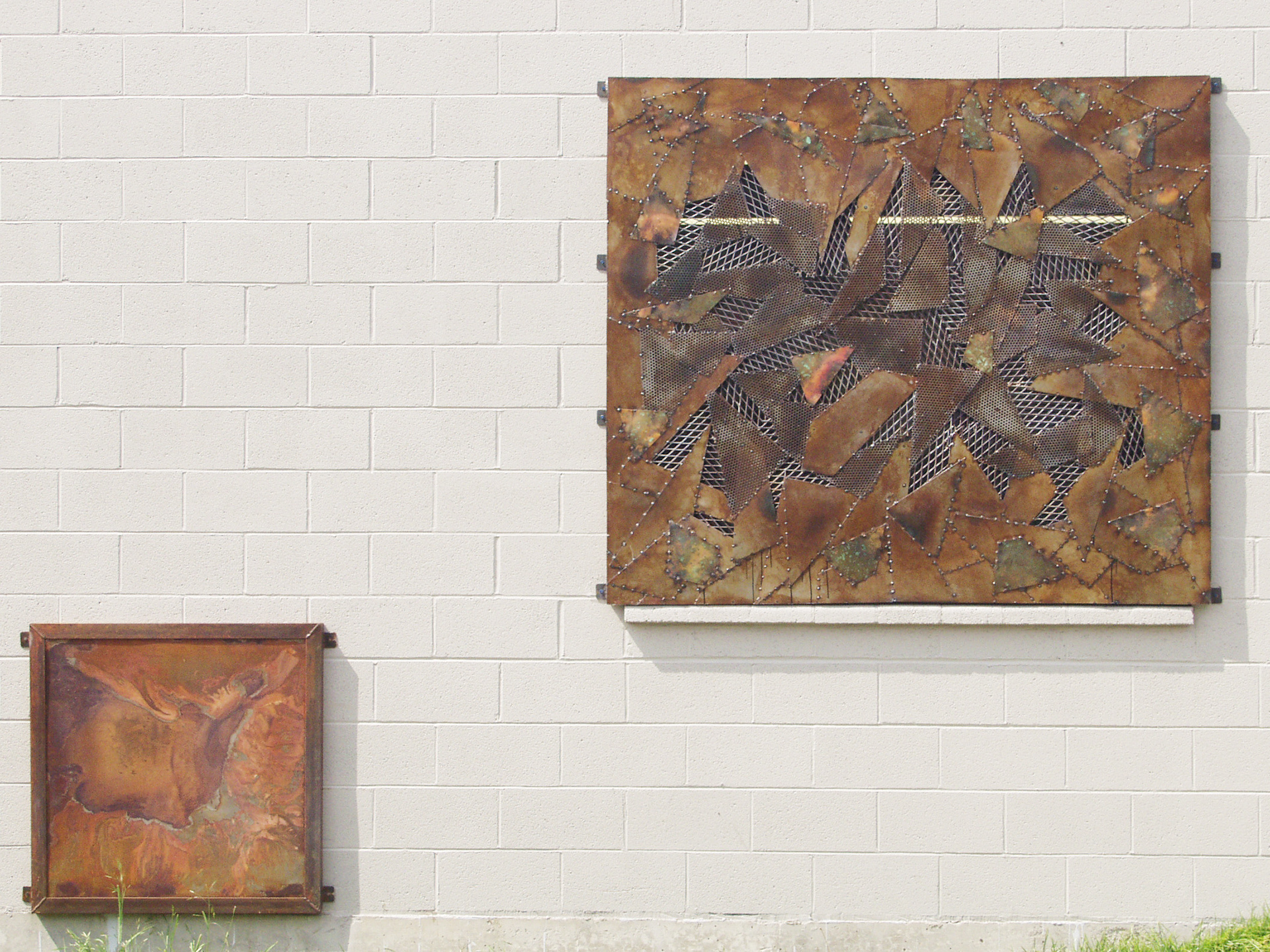
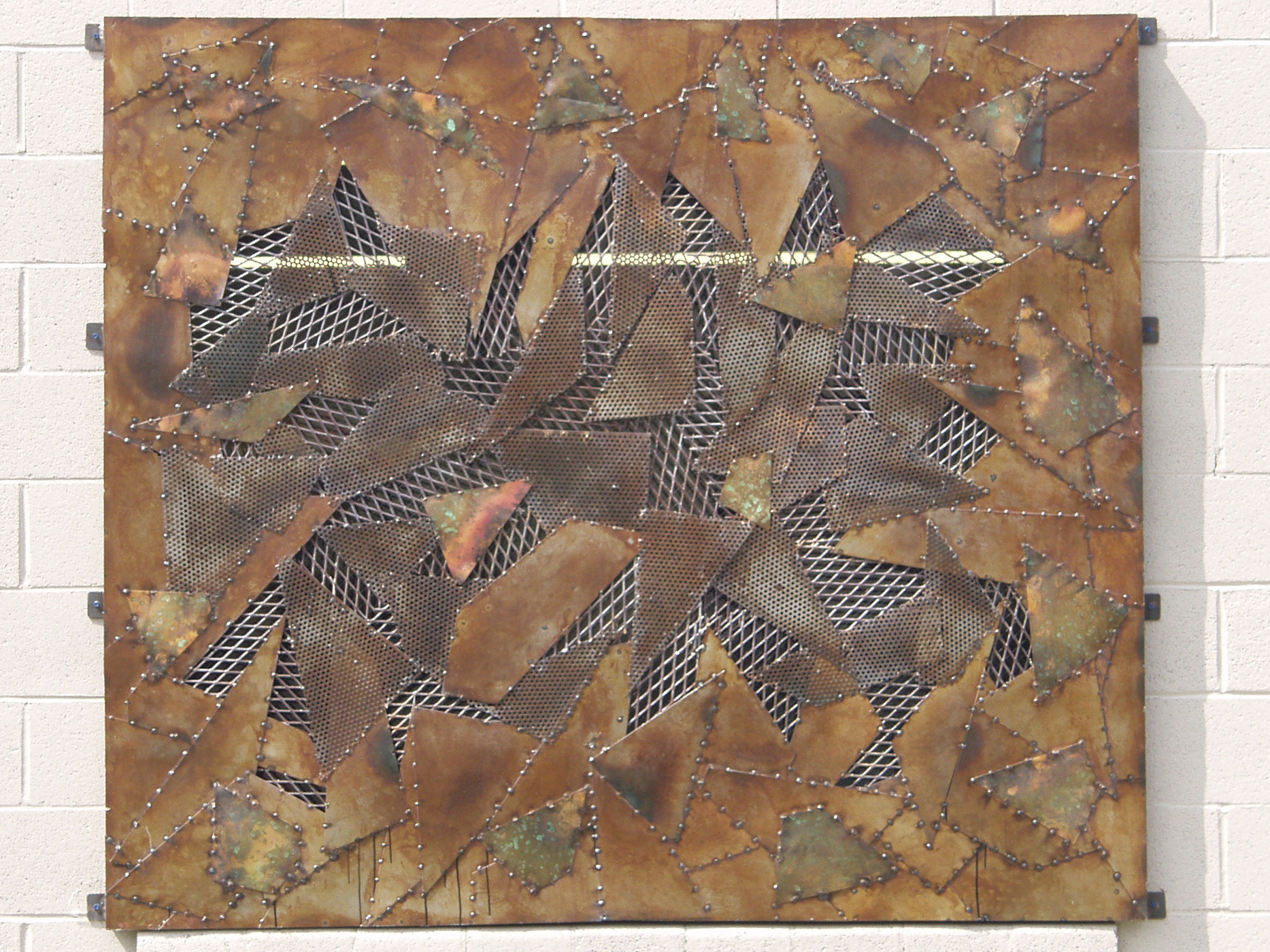
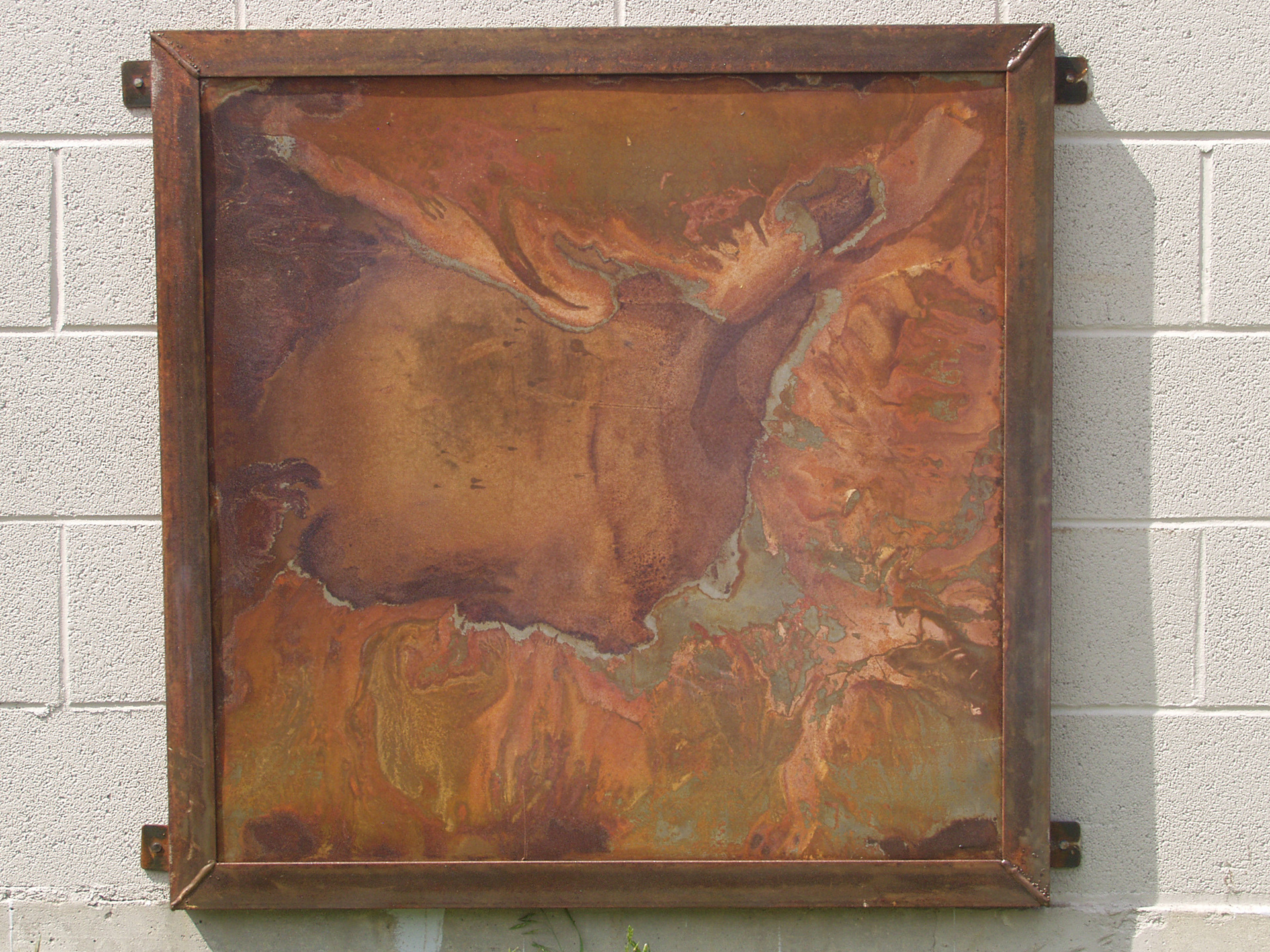
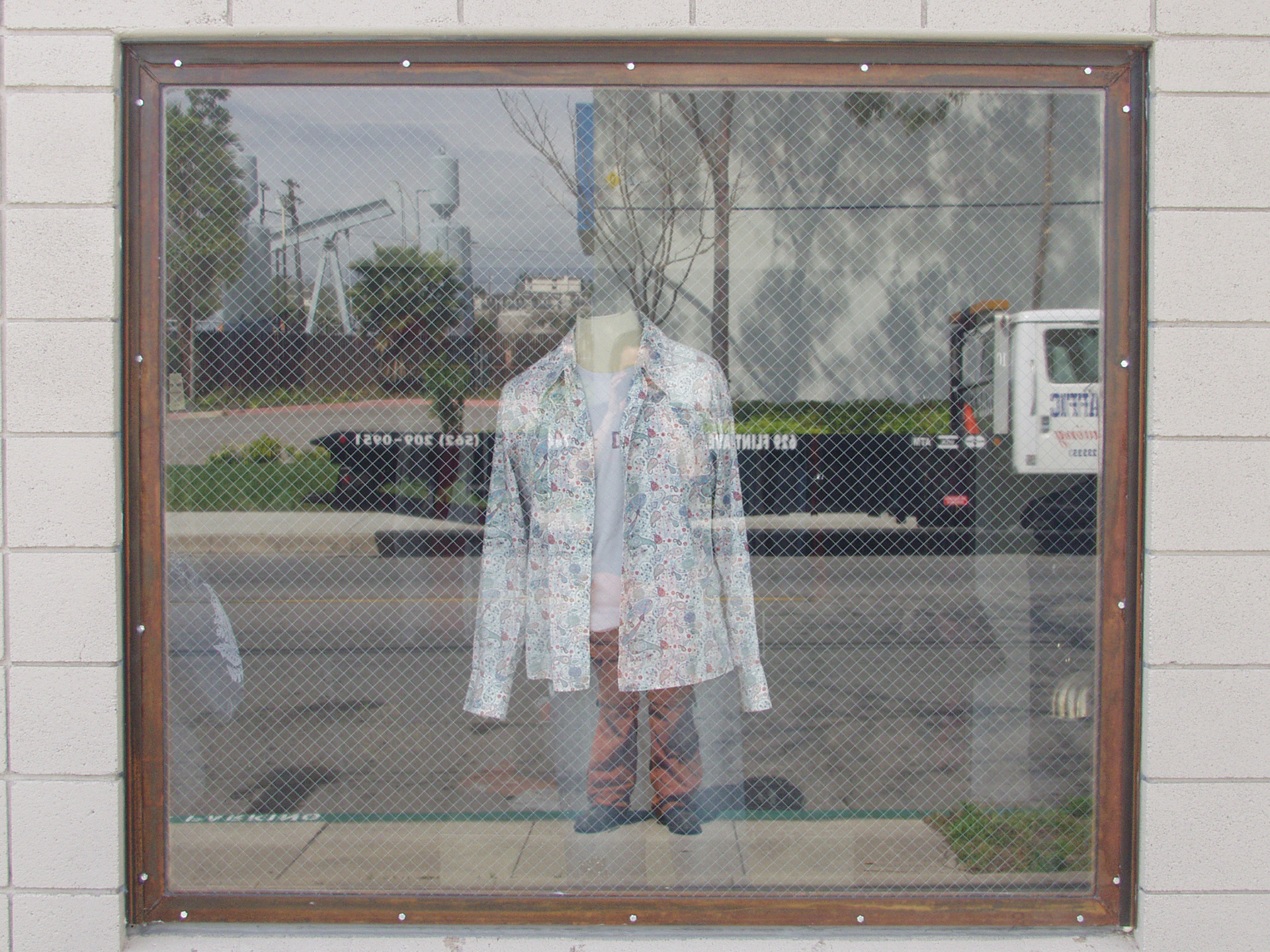
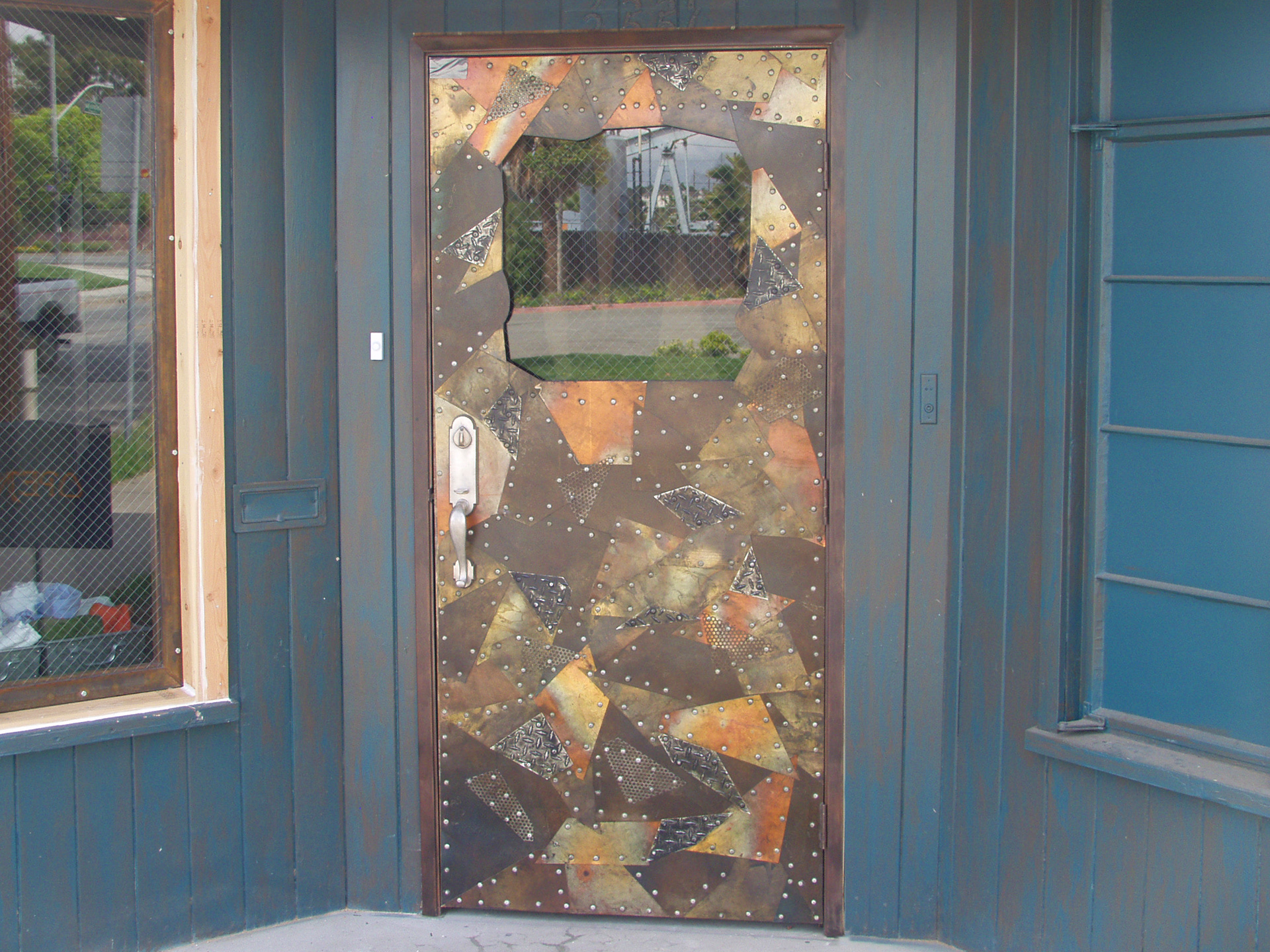
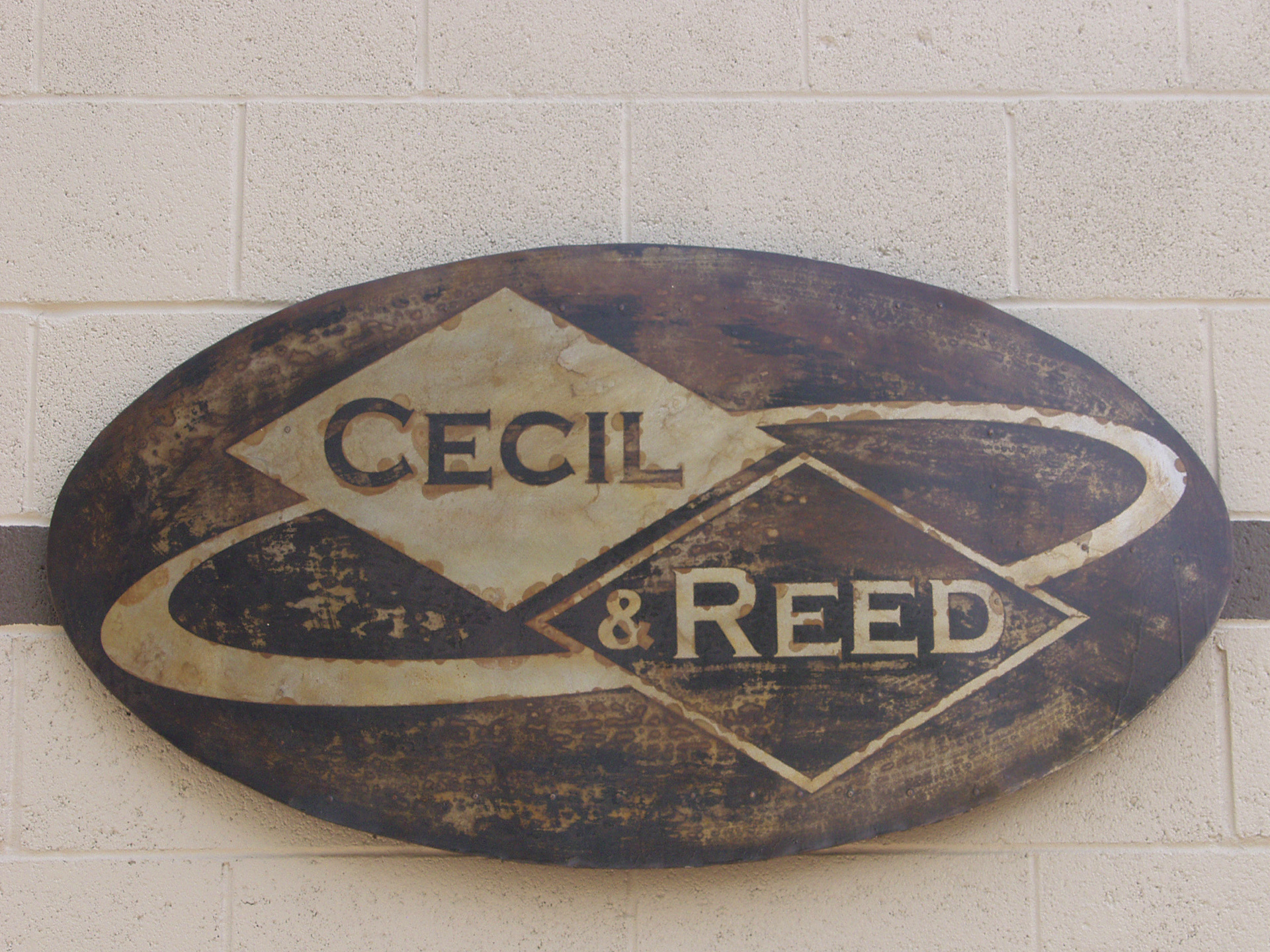
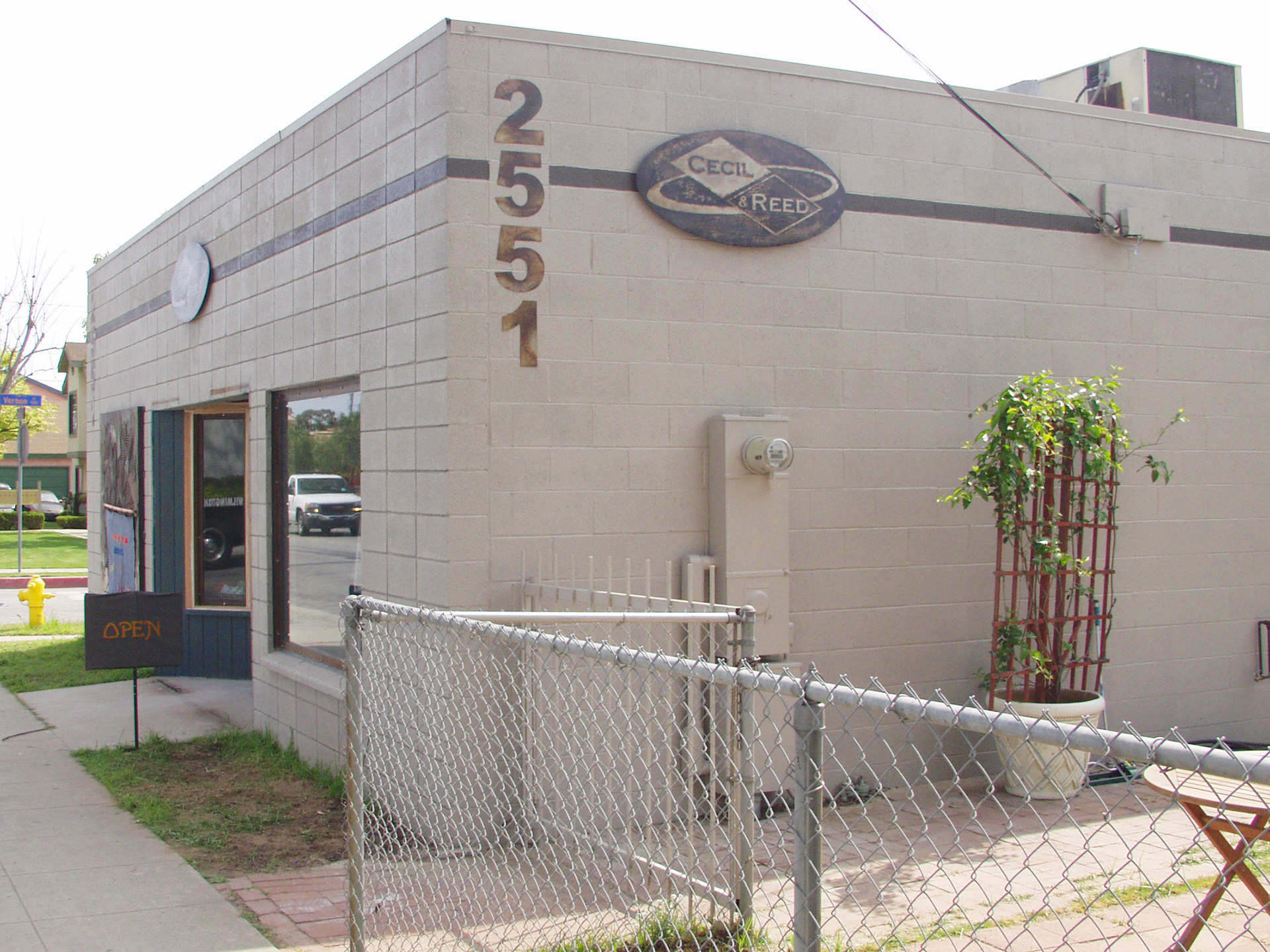
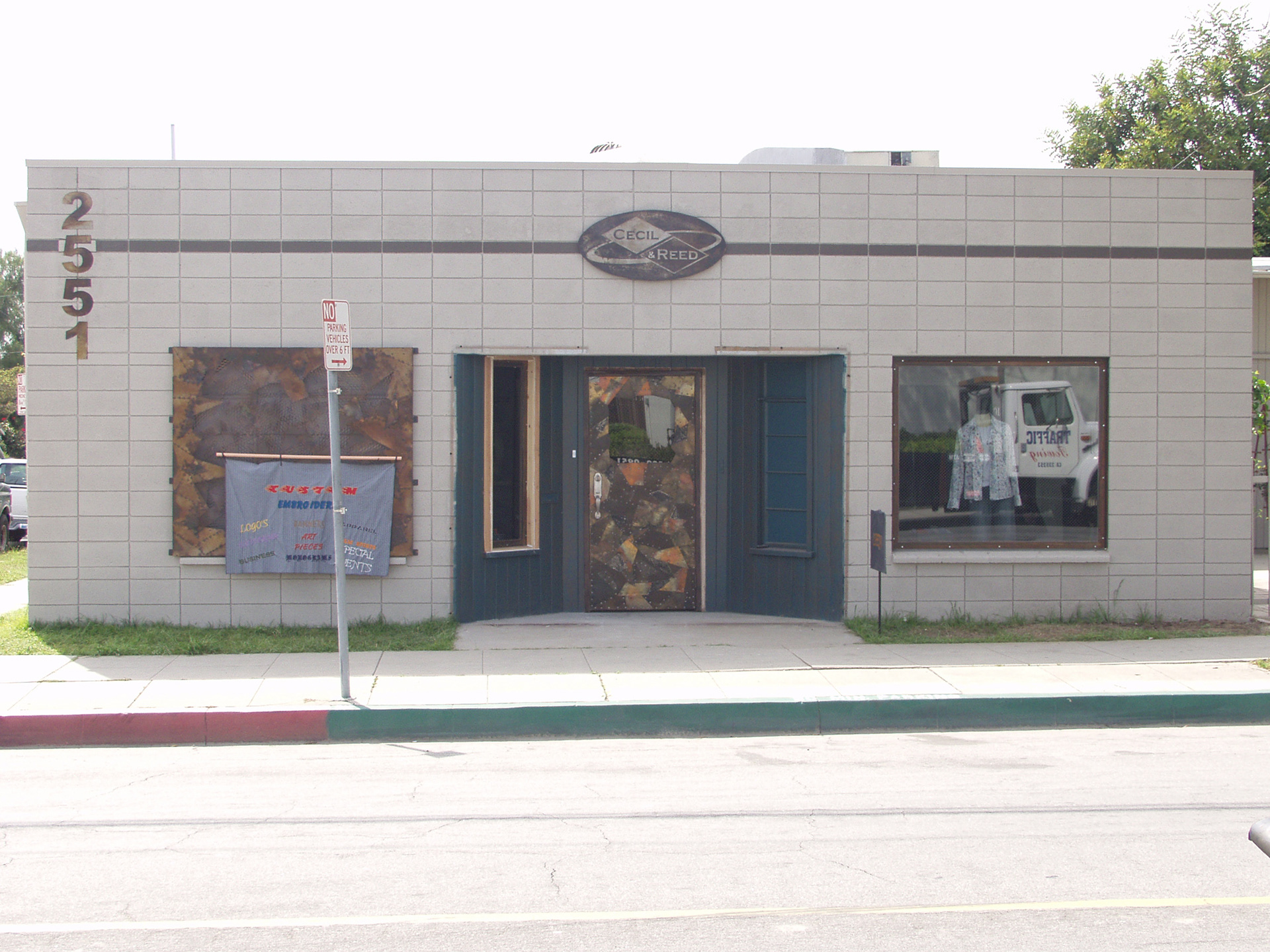
A blast from the past, I was approached by a custom clothing store owner that needed a facelift for his shop. He had approached several window and door installers and they didn’t have anything to offer him that provided the custom feel he was looking for. Knowing that I did some custom metalwork, the told me about the project.
Not being in the best part of town, he wanted me to create something artistic that would also provide a level of security. After showing him some samples of patined steel and copper, we decide to move forward. The main window was replaced with wired glass to give an industrial feel, and provide some additional security. The other windows were covered with a patchwork metal design. I created a front door with a similar patchwork and riveted aesthetic. I then plasma cut out some numbers for the address and two signs on the building. Using some vinyl cut masking, I etched the logo in metal.
Not being in the best part of town, he wanted me to create something artistic that would also provide a level of security. After showing him some samples of patined steel and copper, we decide to move forward. The main window was replaced with wired glass to give an industrial feel, and provide some additional security. The other windows were covered with a patchwork metal design. I created a front door with a similar patchwork and riveted aesthetic. I then plasma cut out some numbers for the address and two signs on the building. Using some vinyl cut masking, I etched the logo in metal.
While this project is a distant memory, it still adds a unique yet functional look to the building.
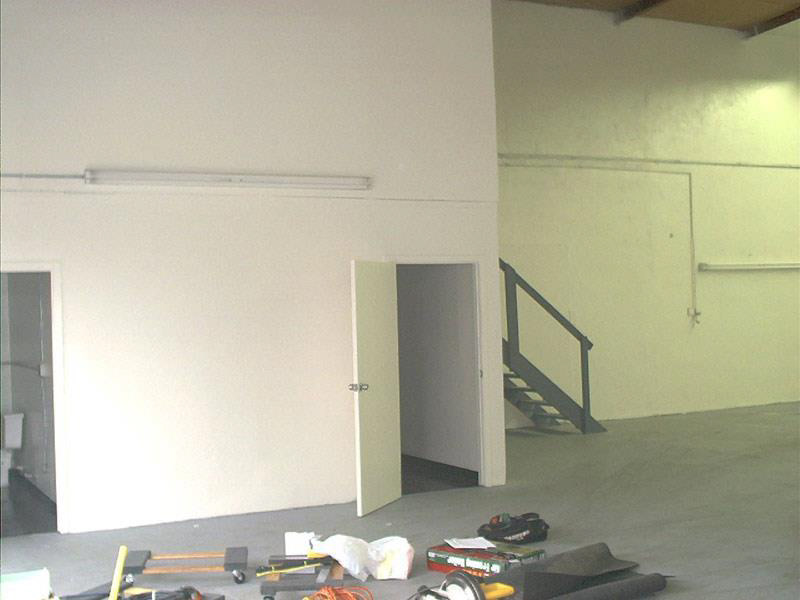
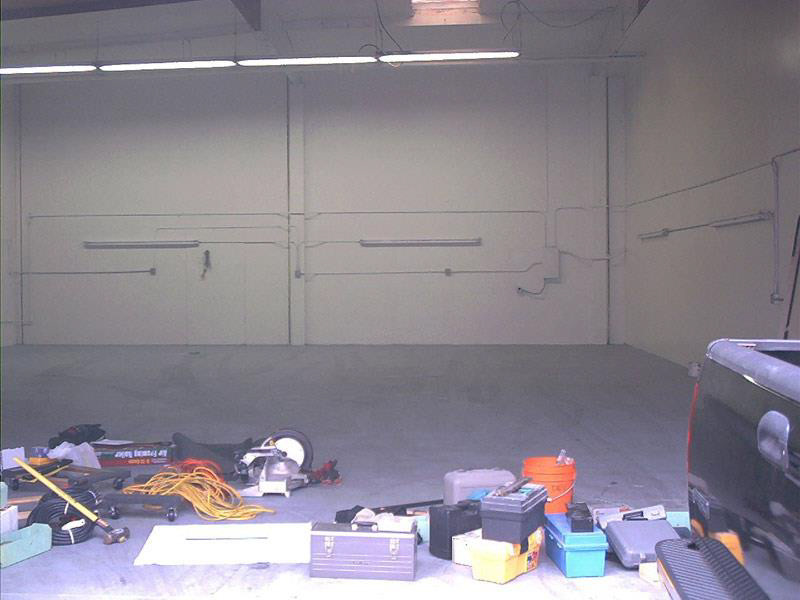
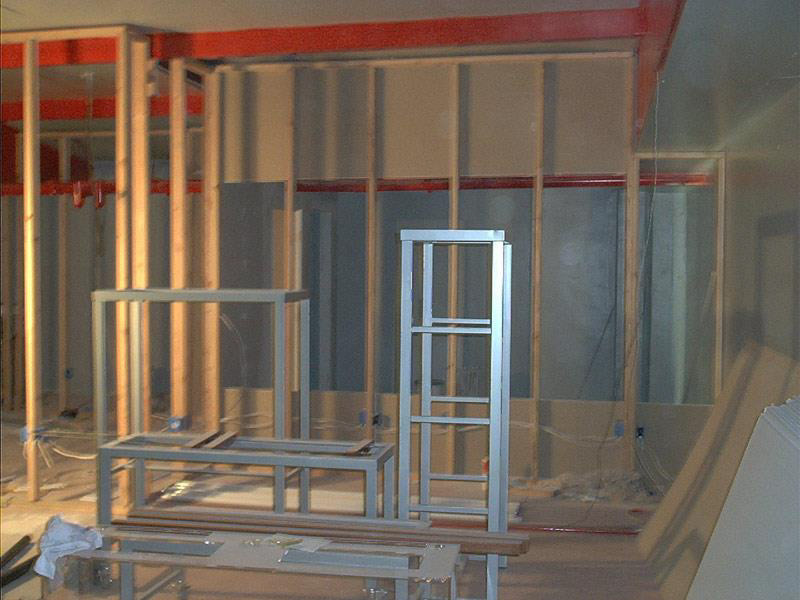
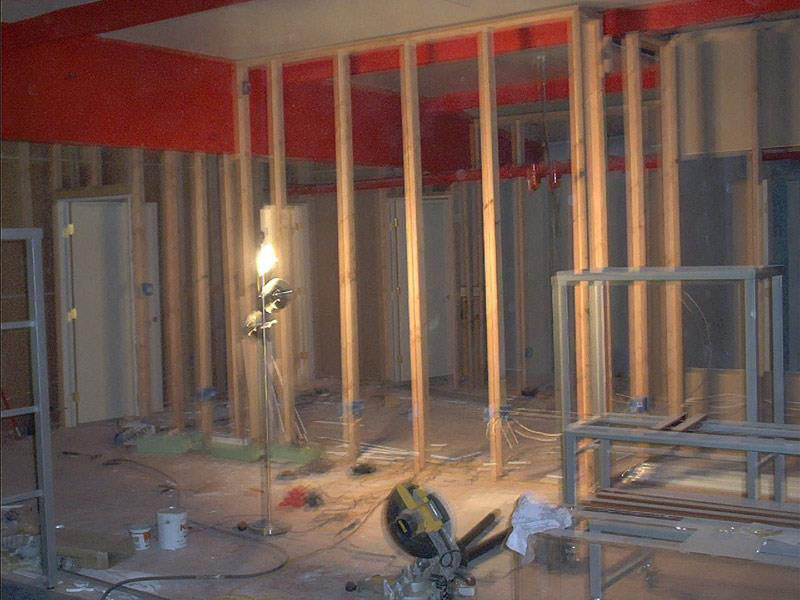

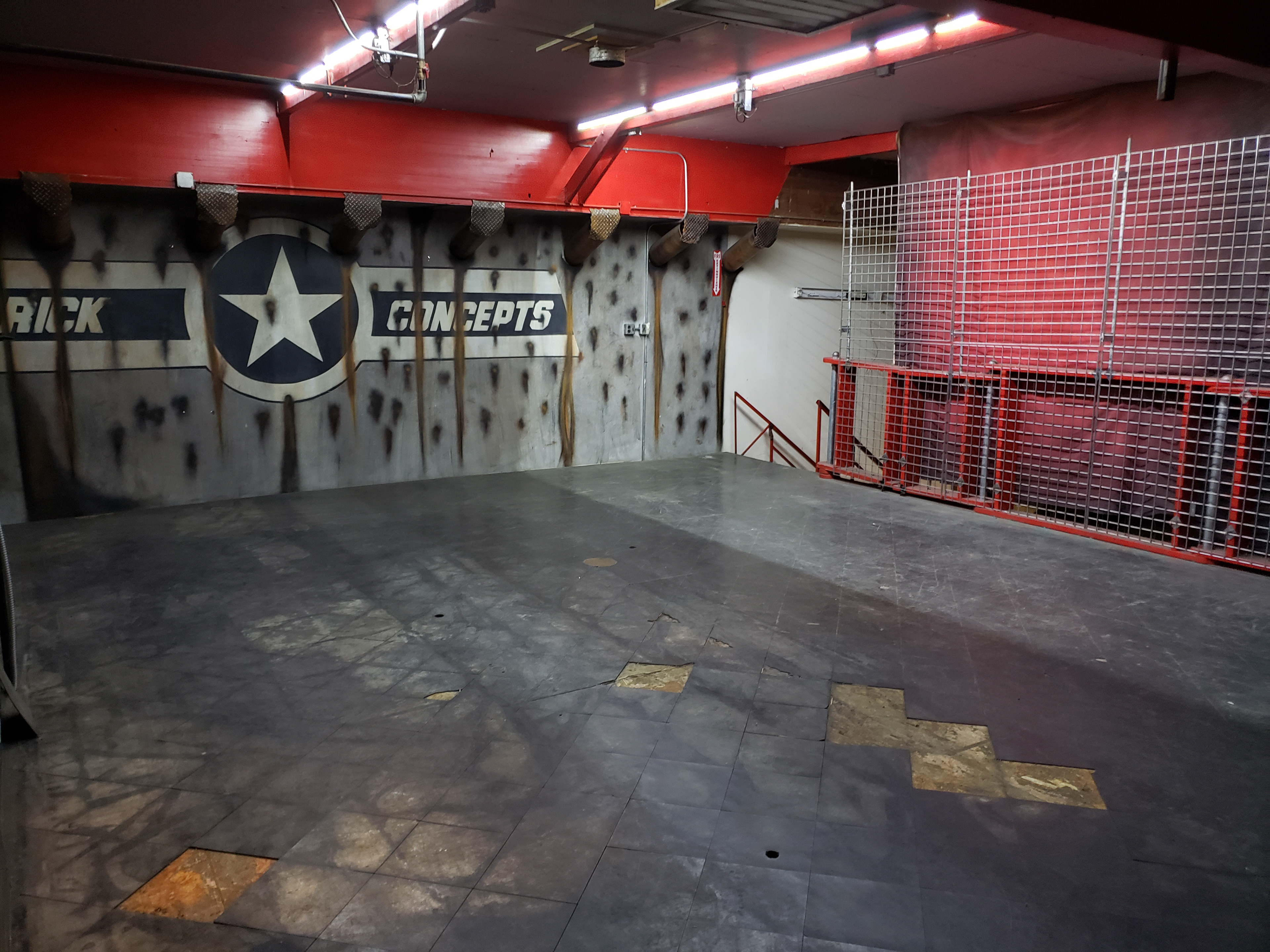
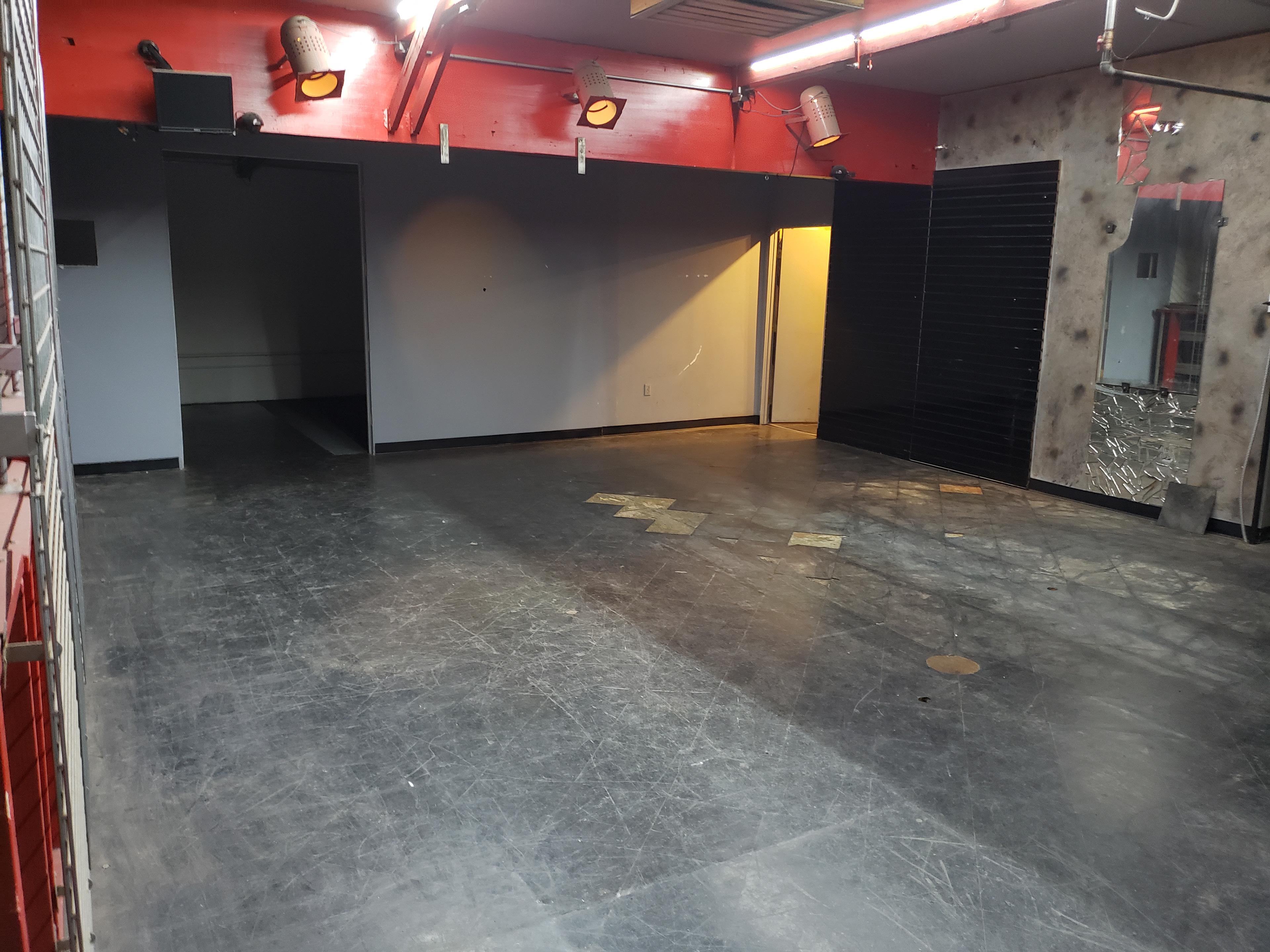



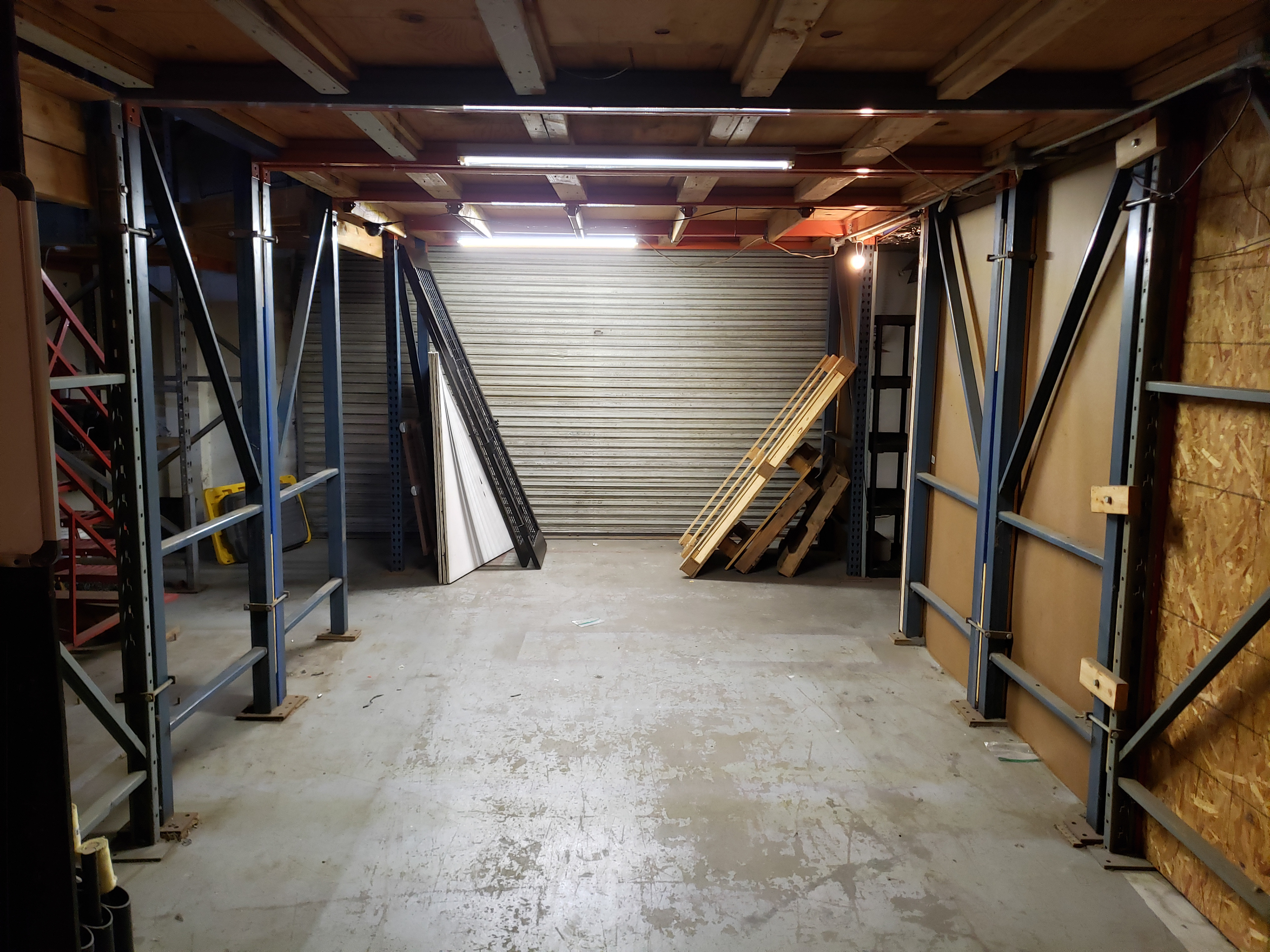
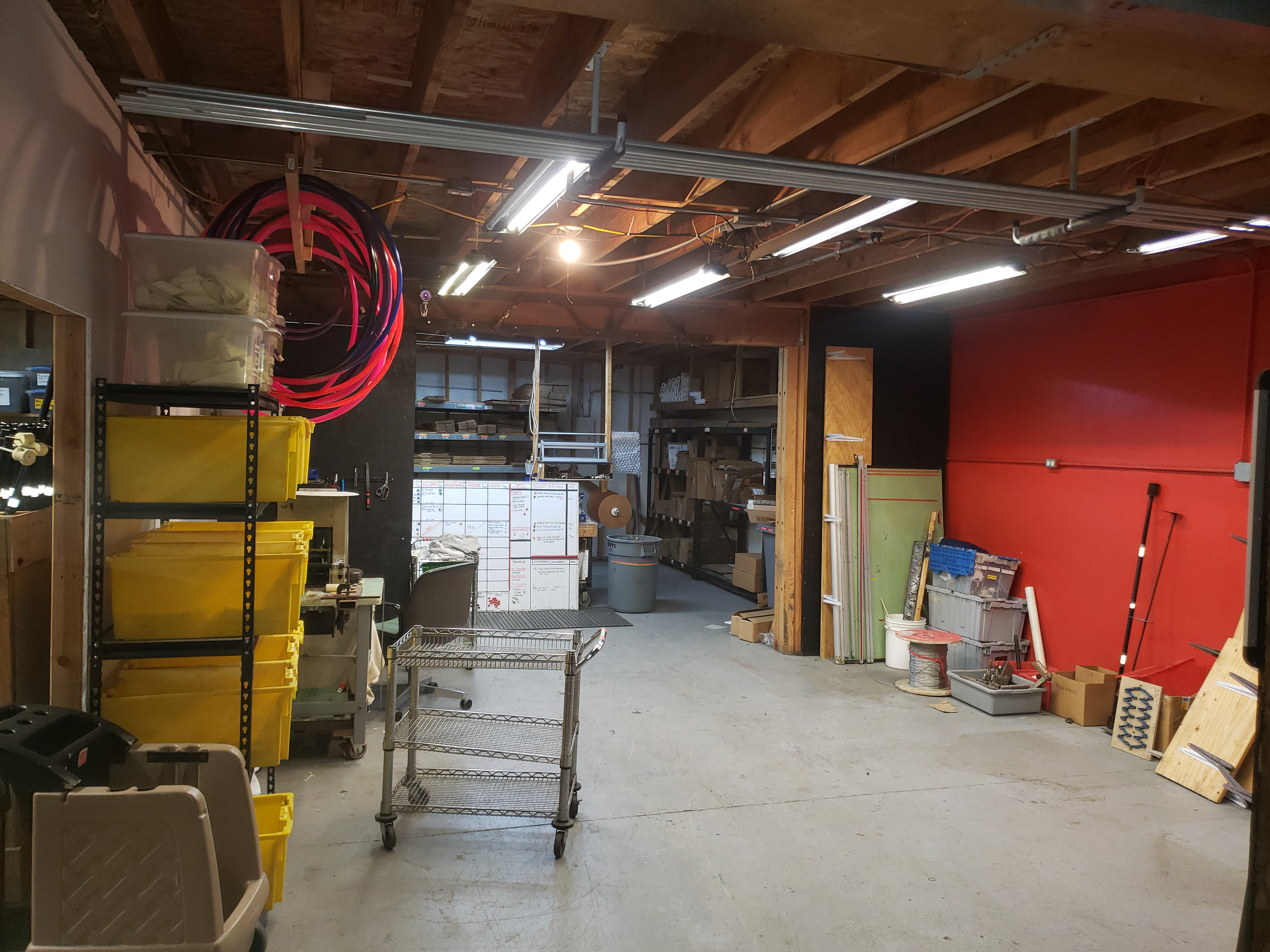
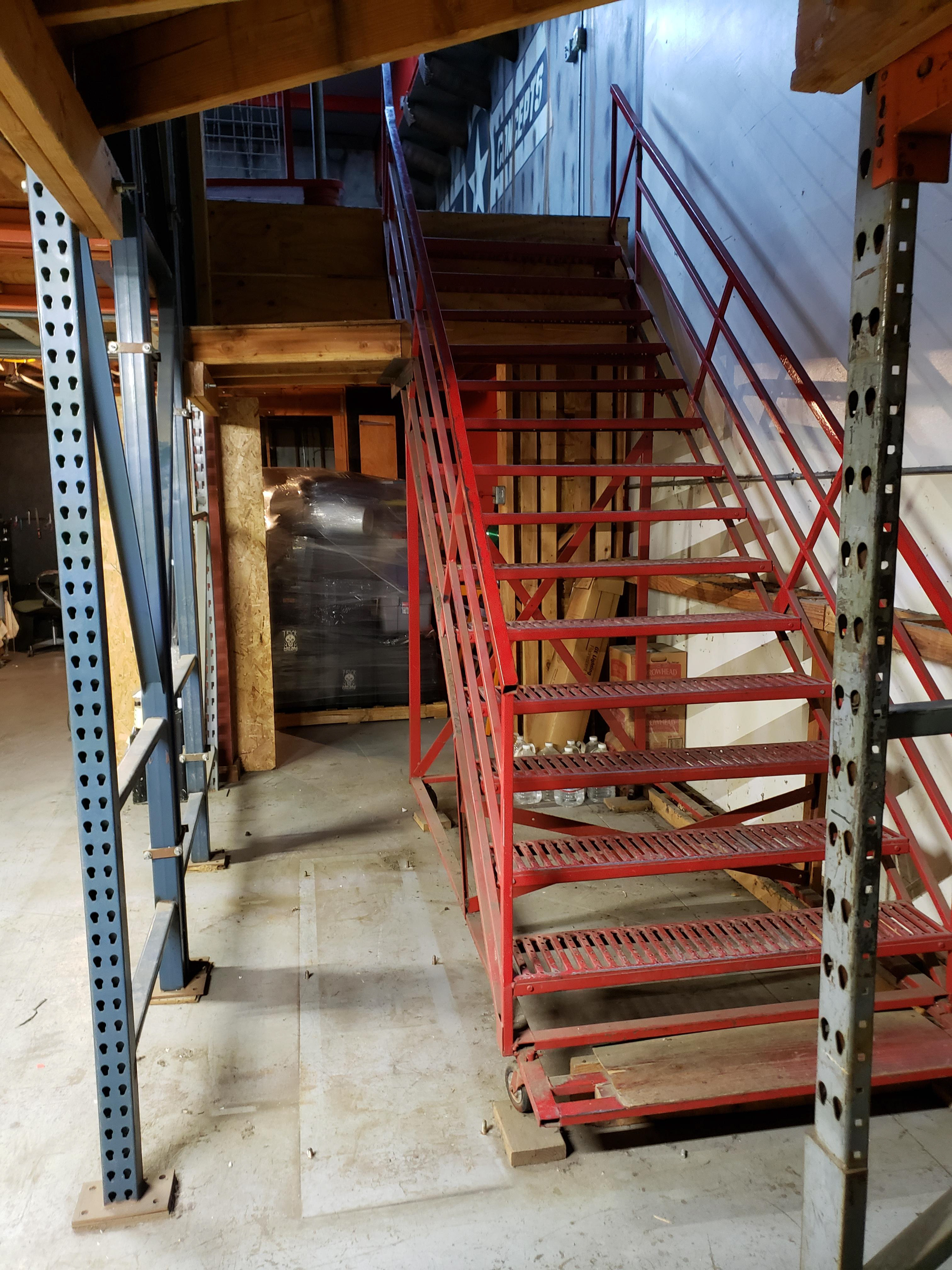
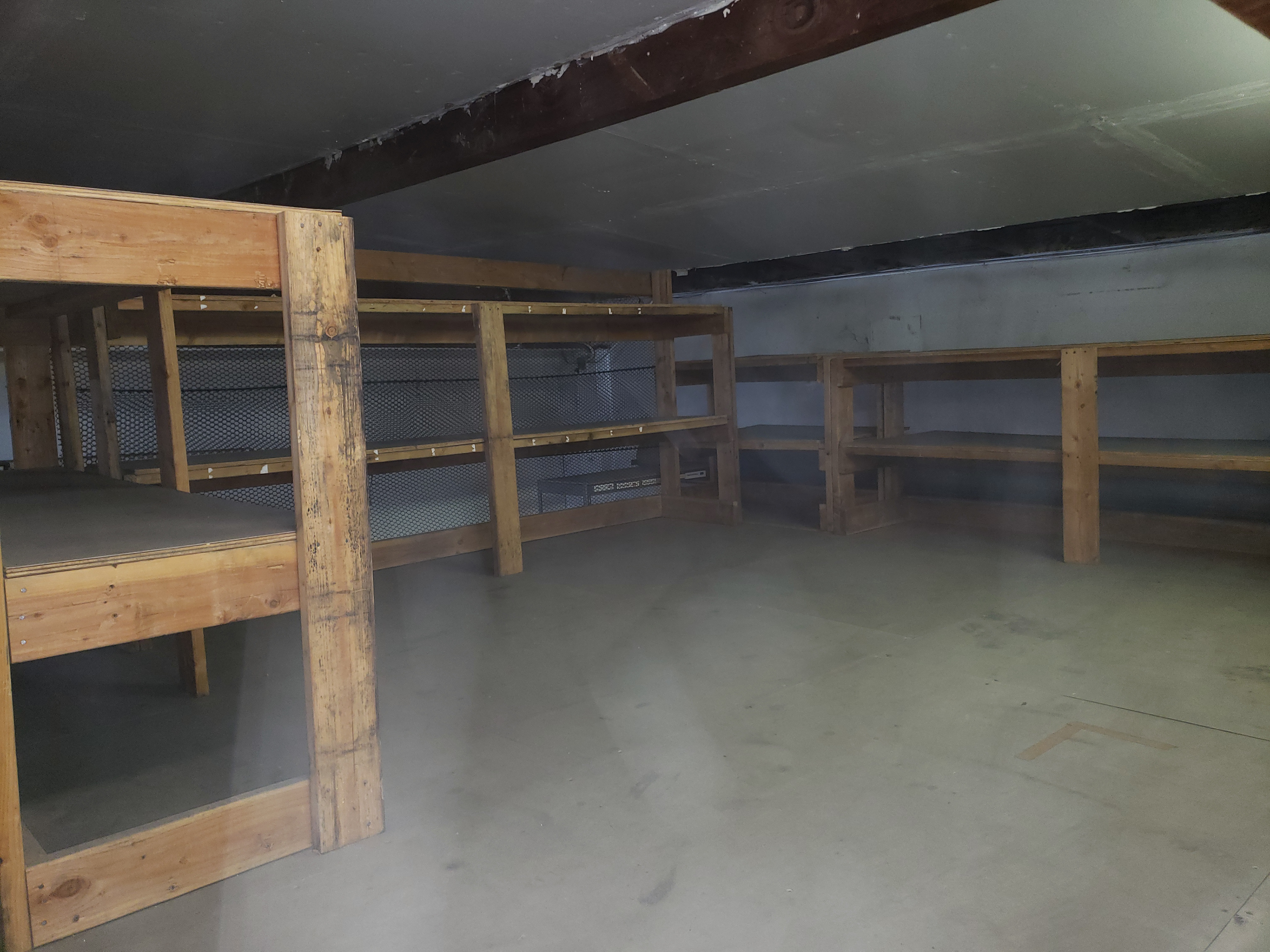
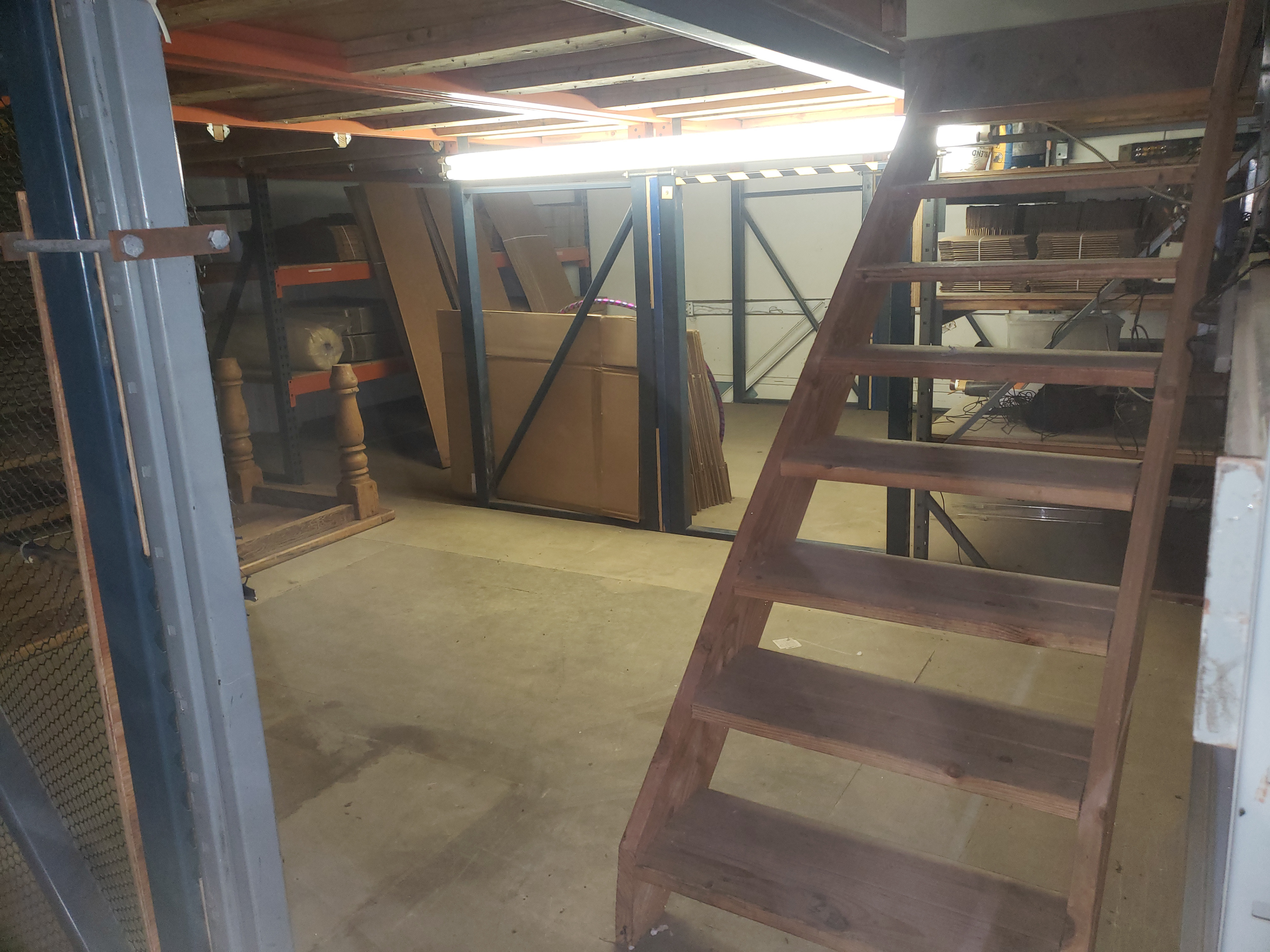
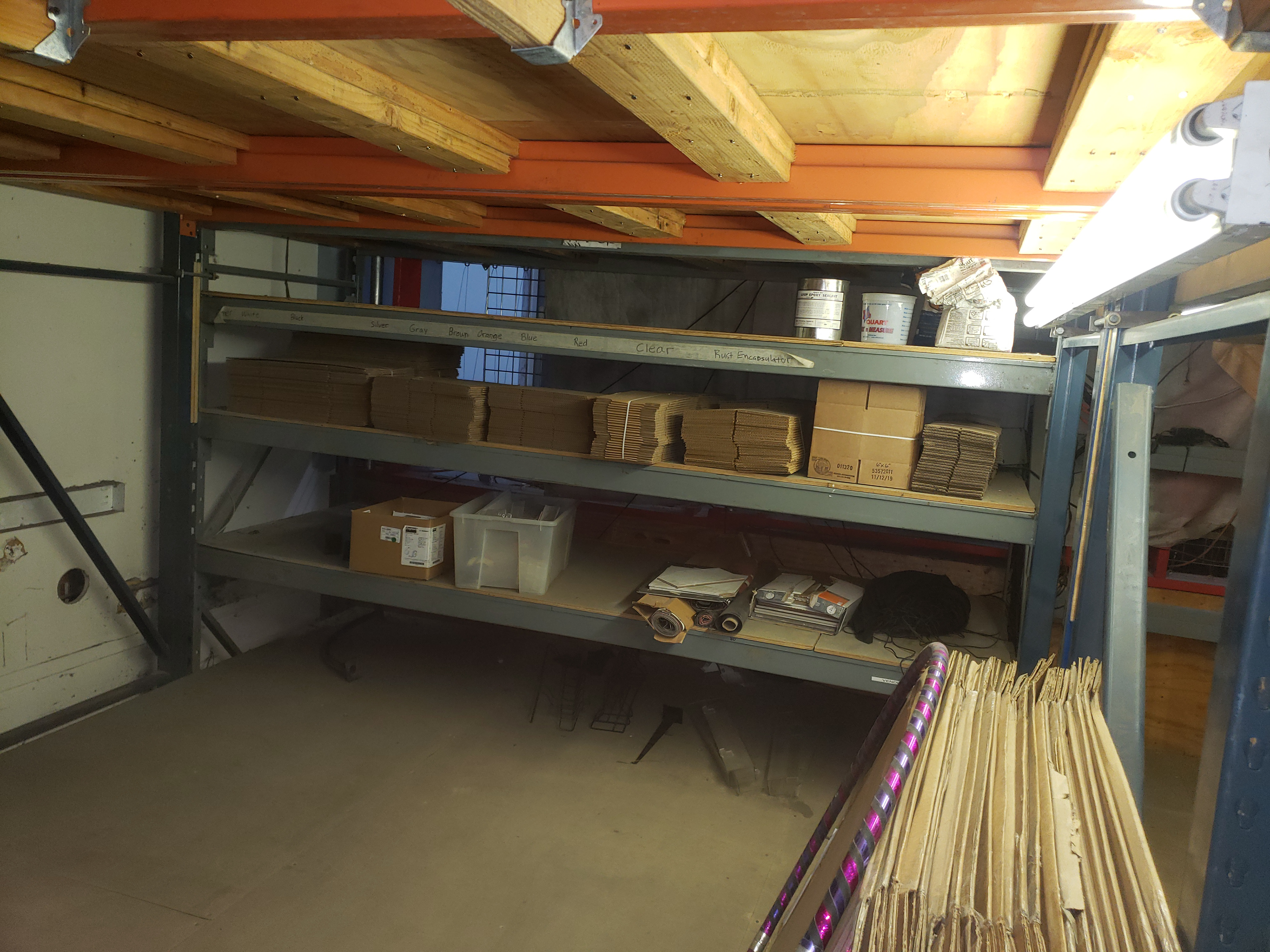
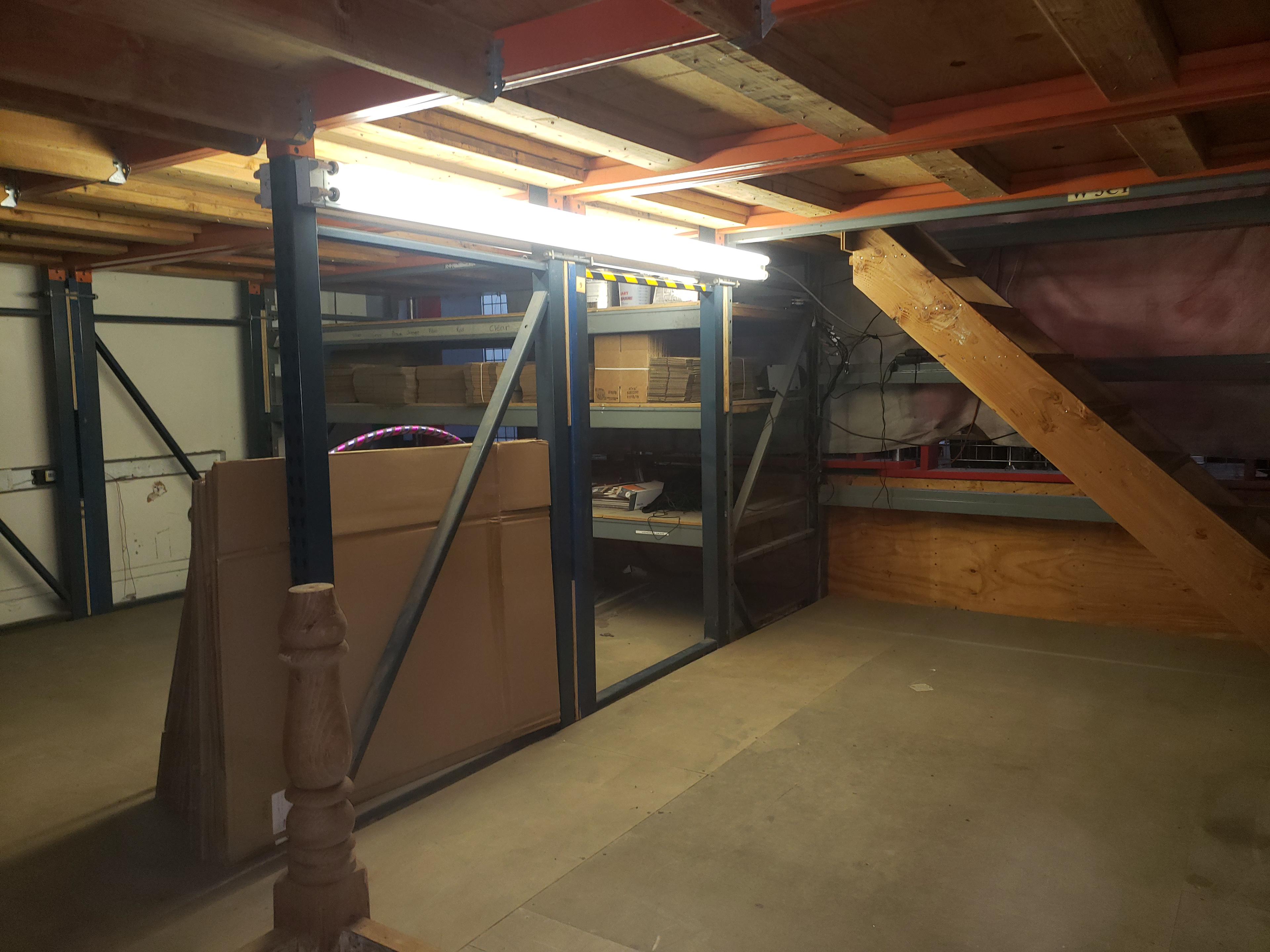
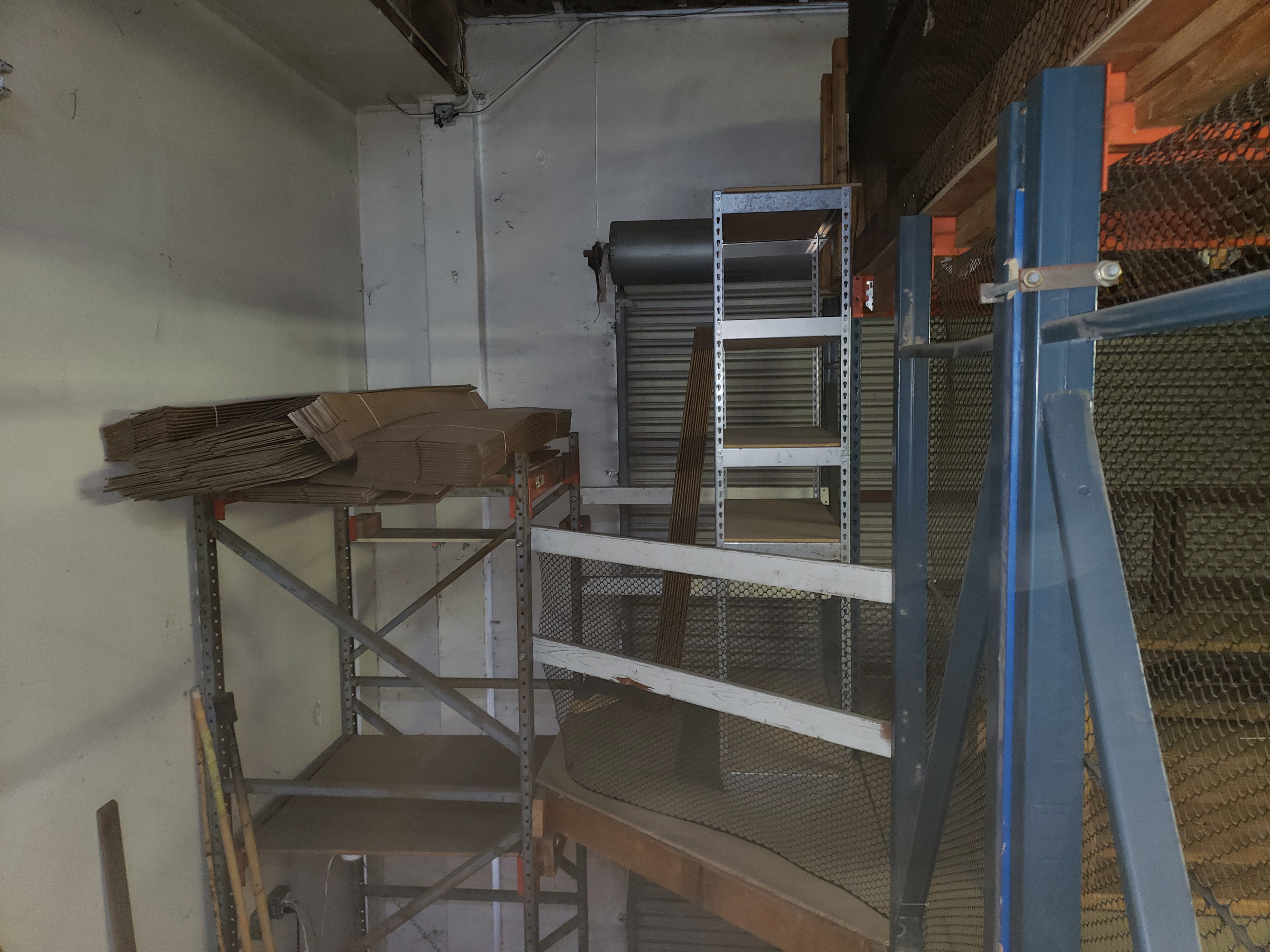
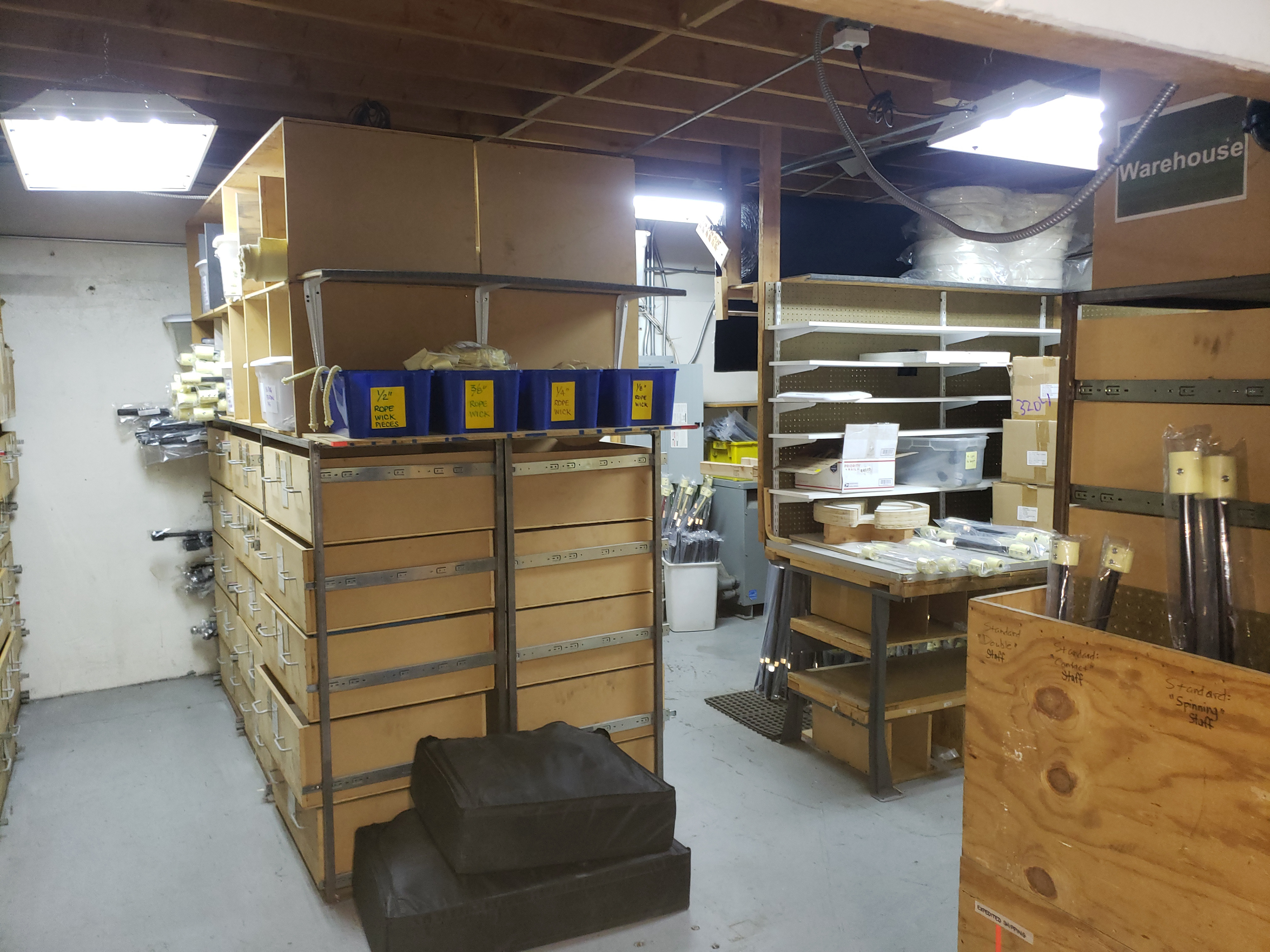
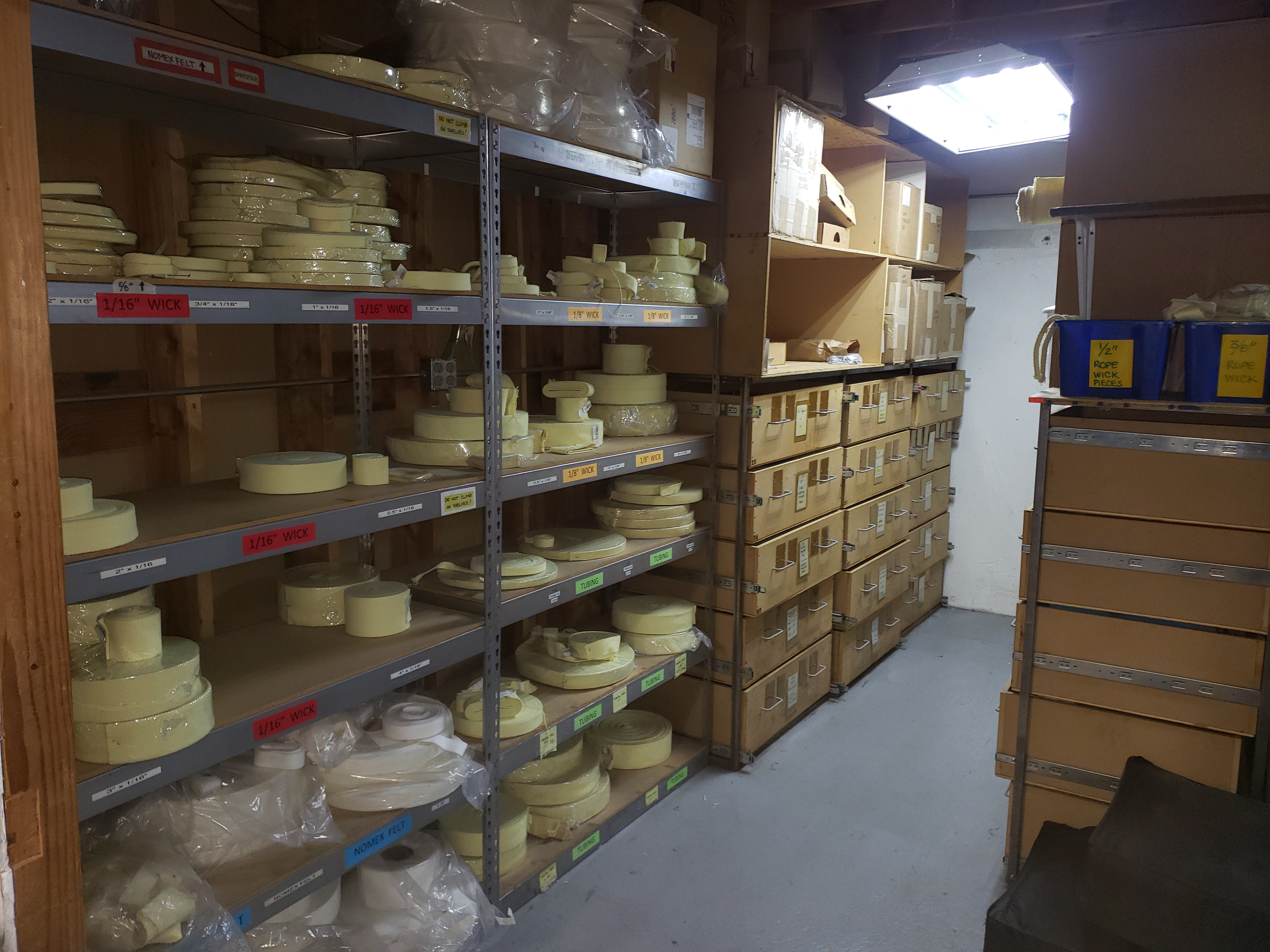
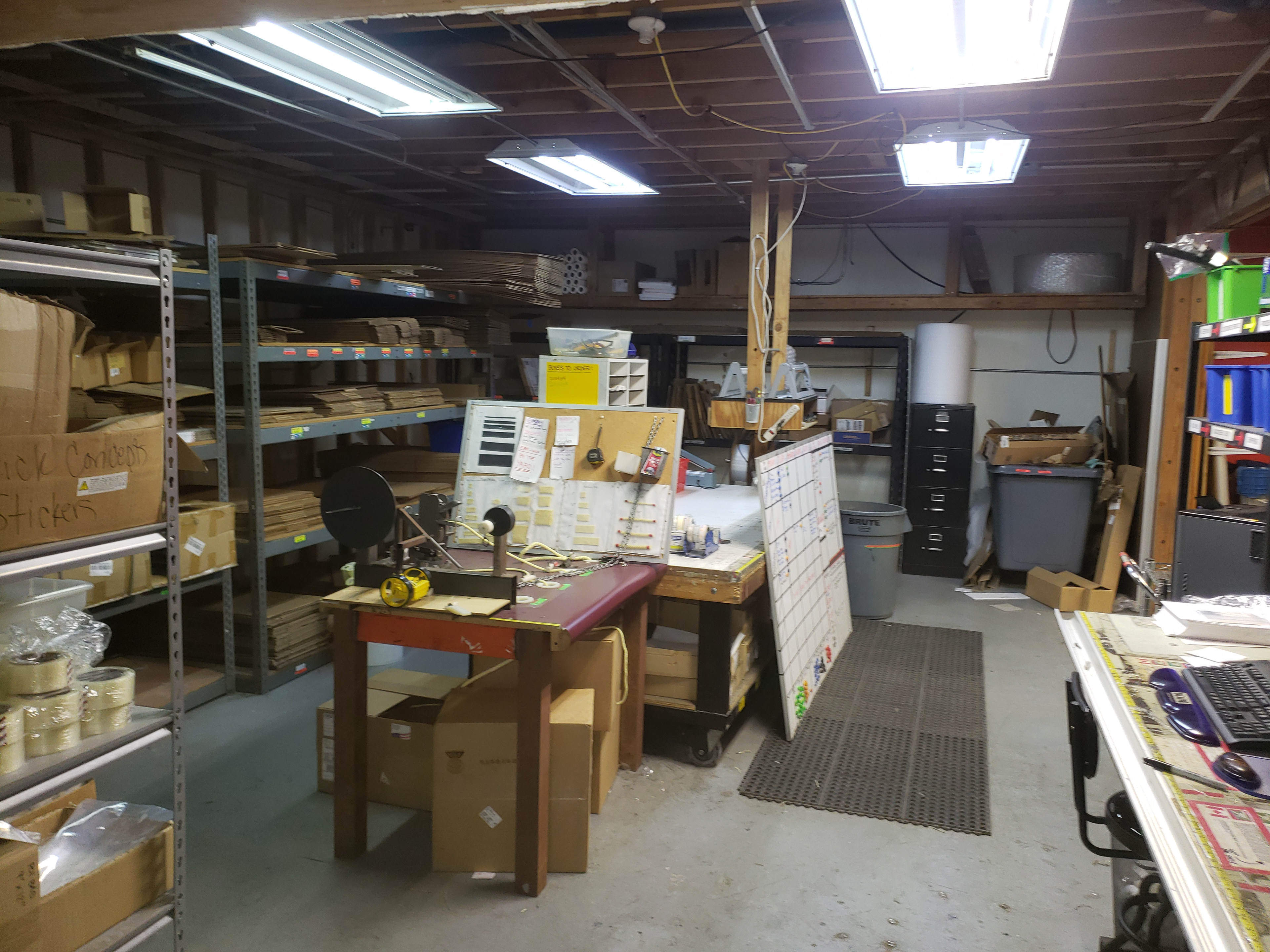
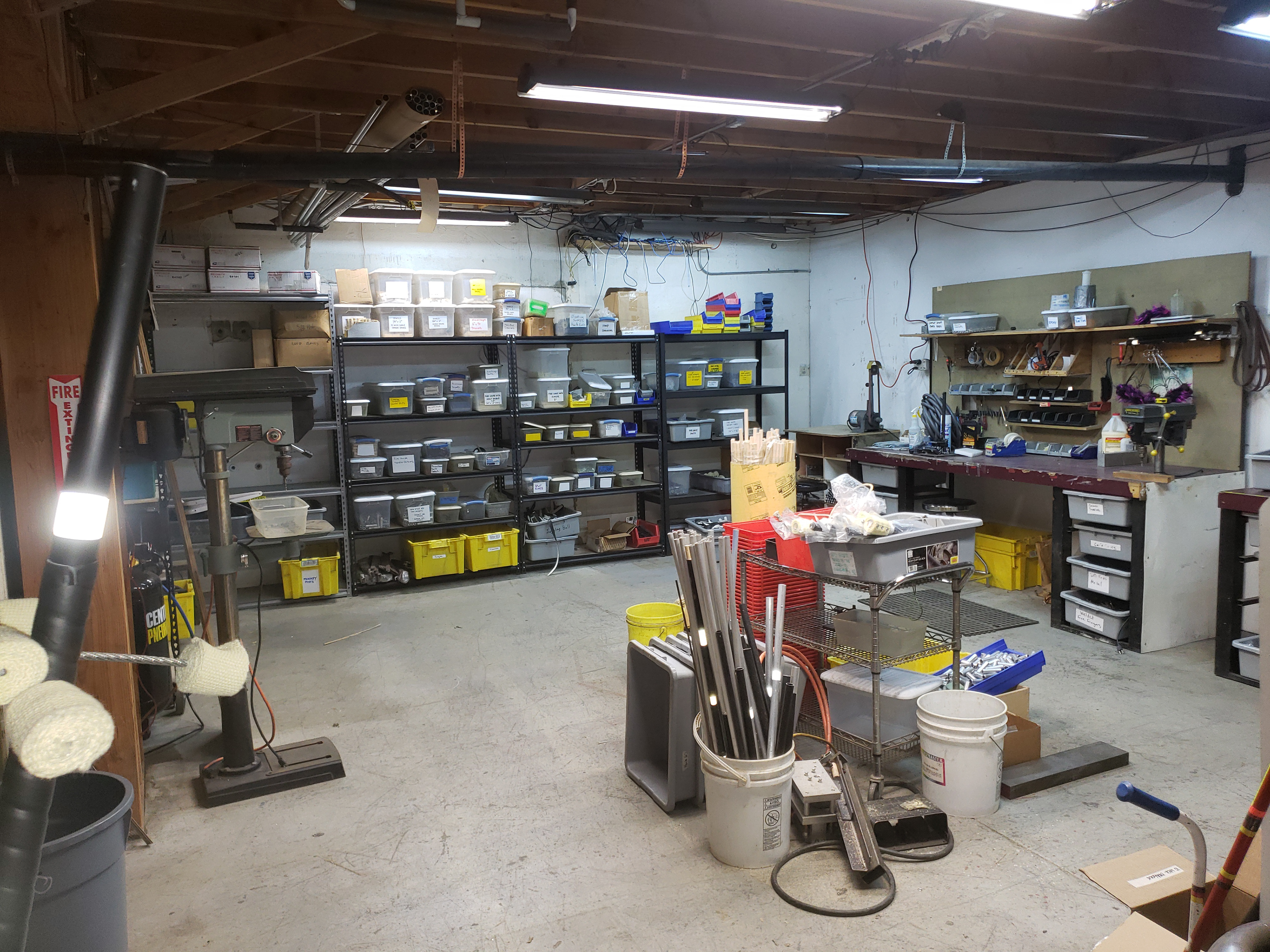
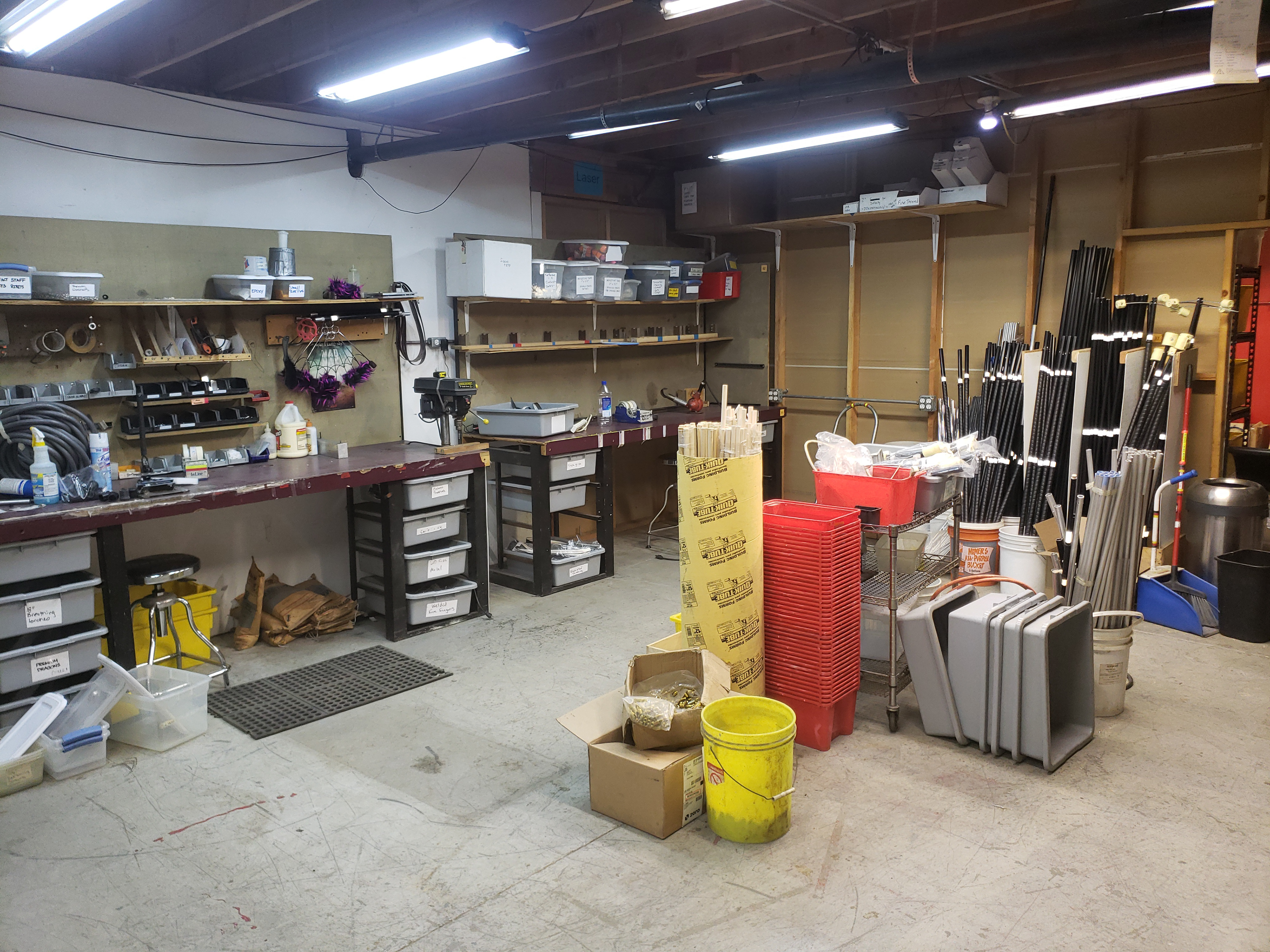
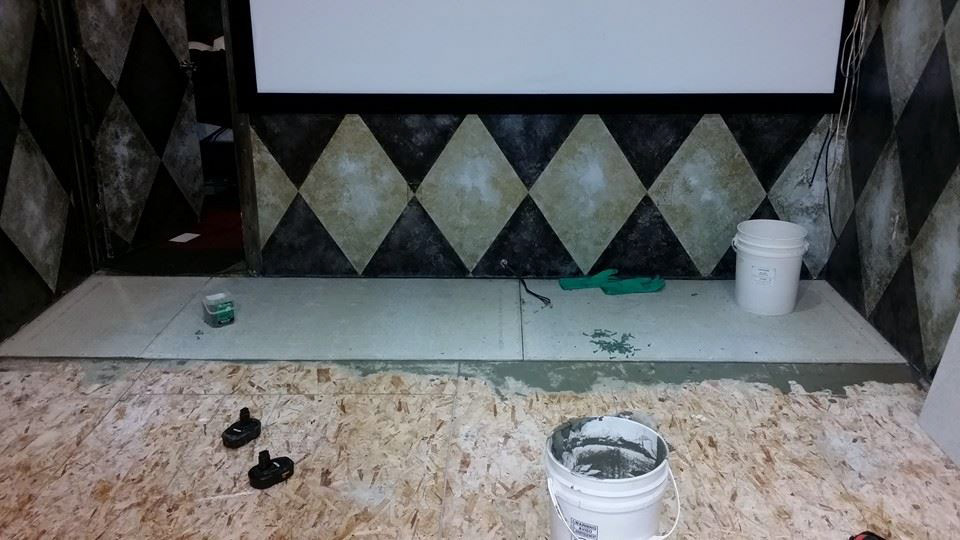
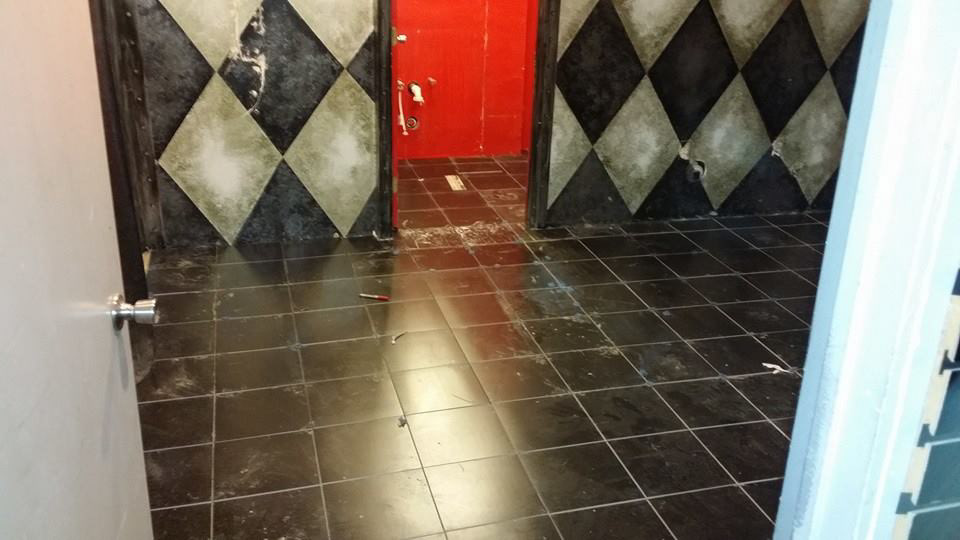

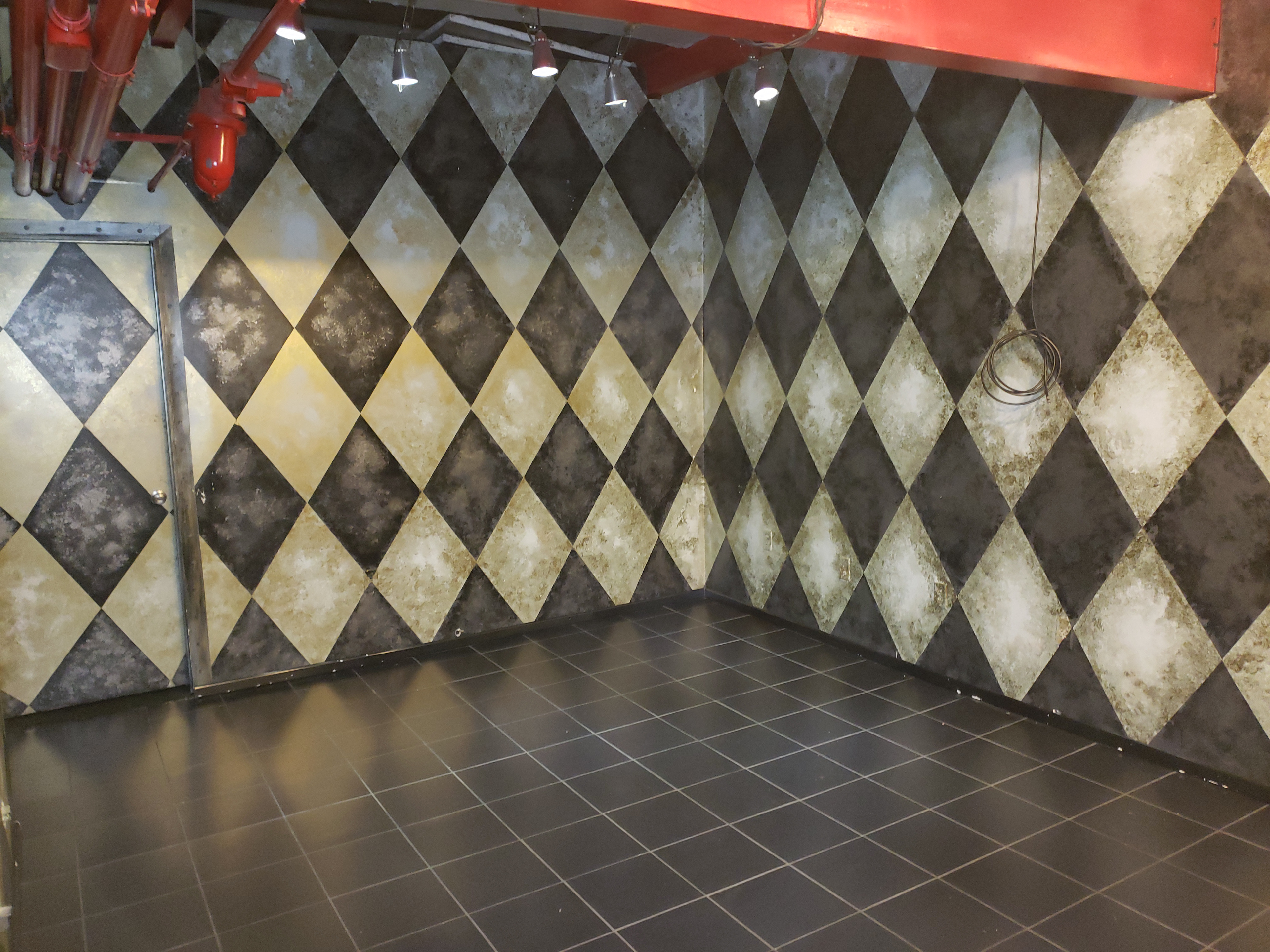
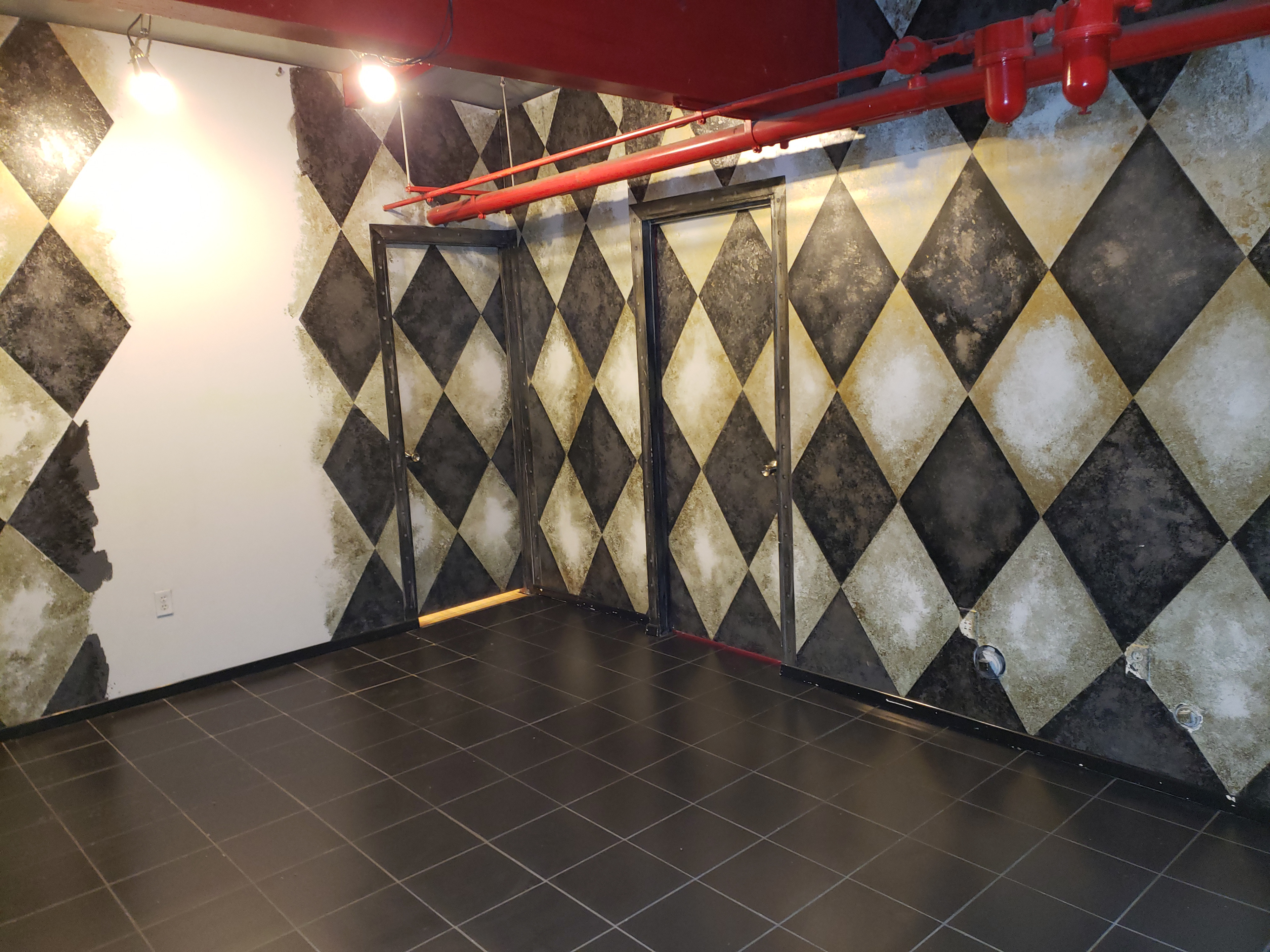
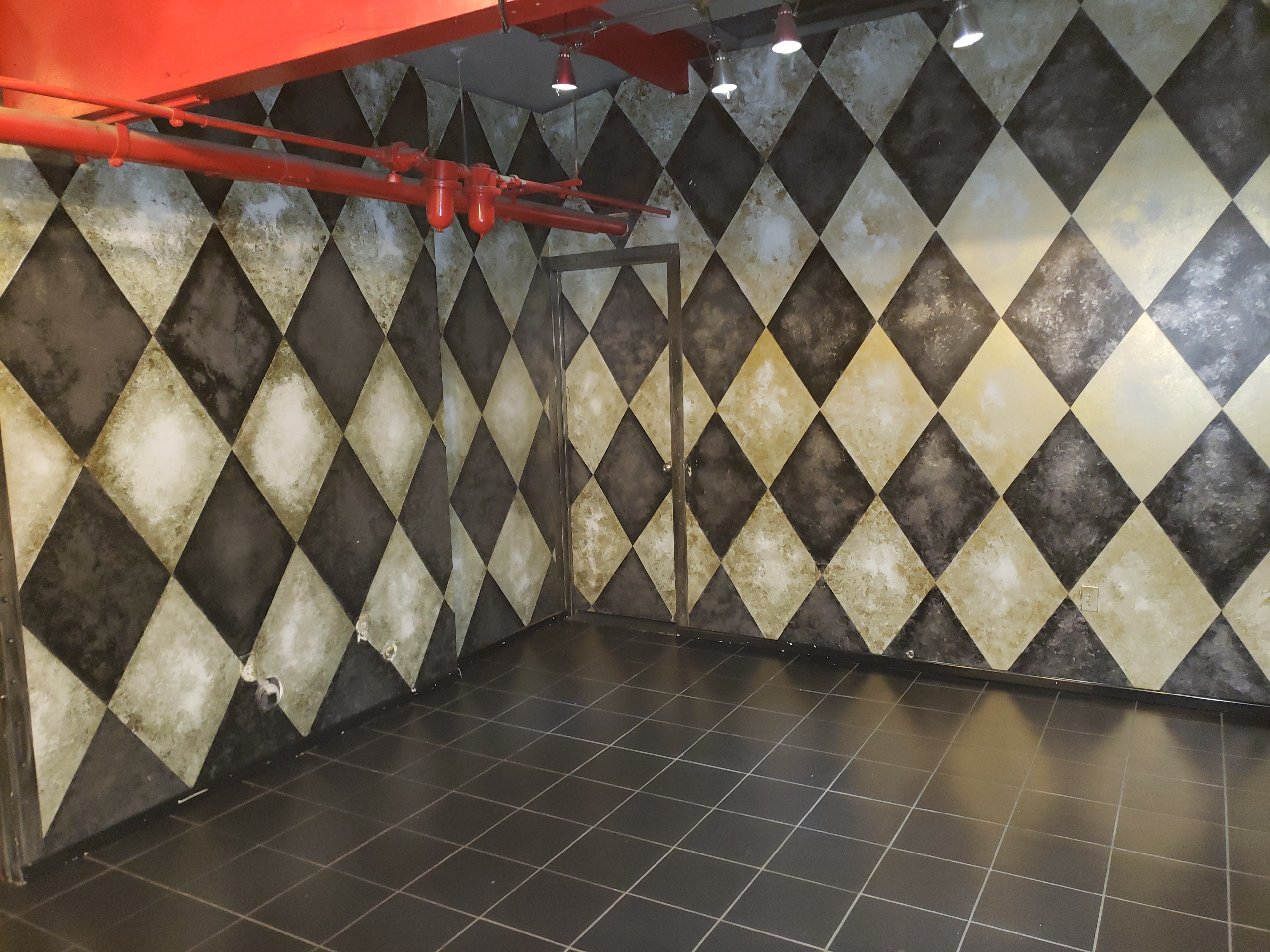
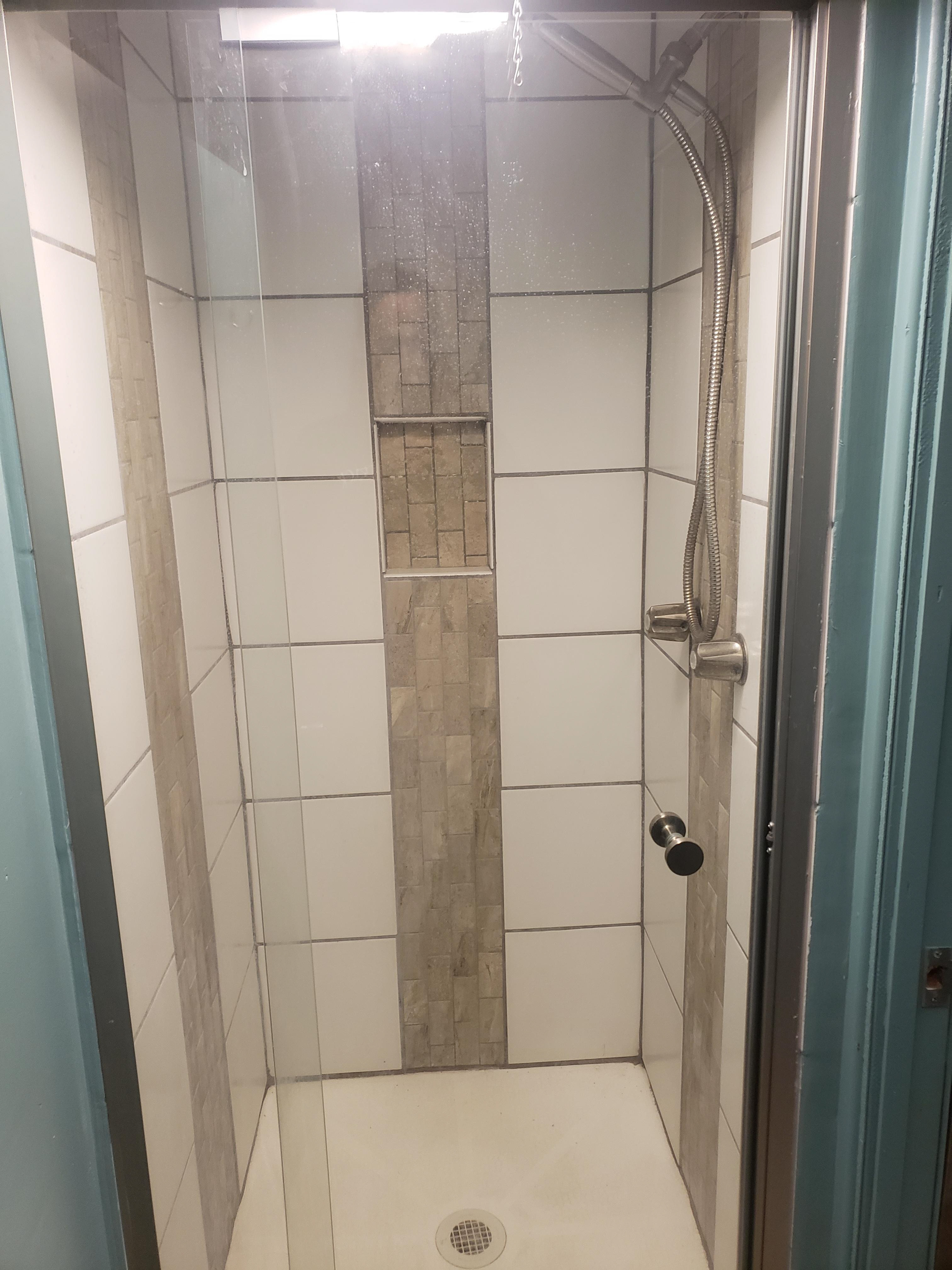

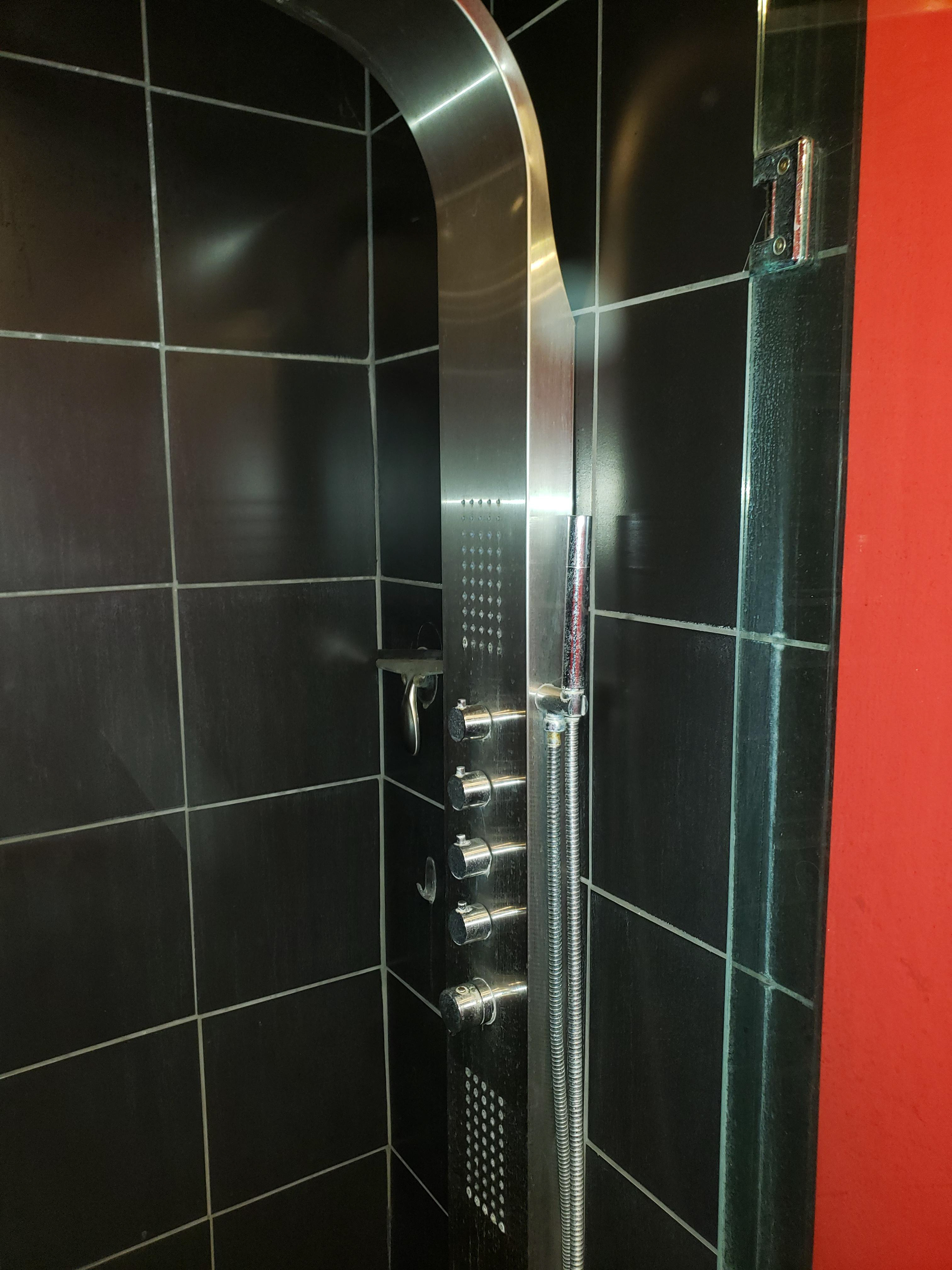
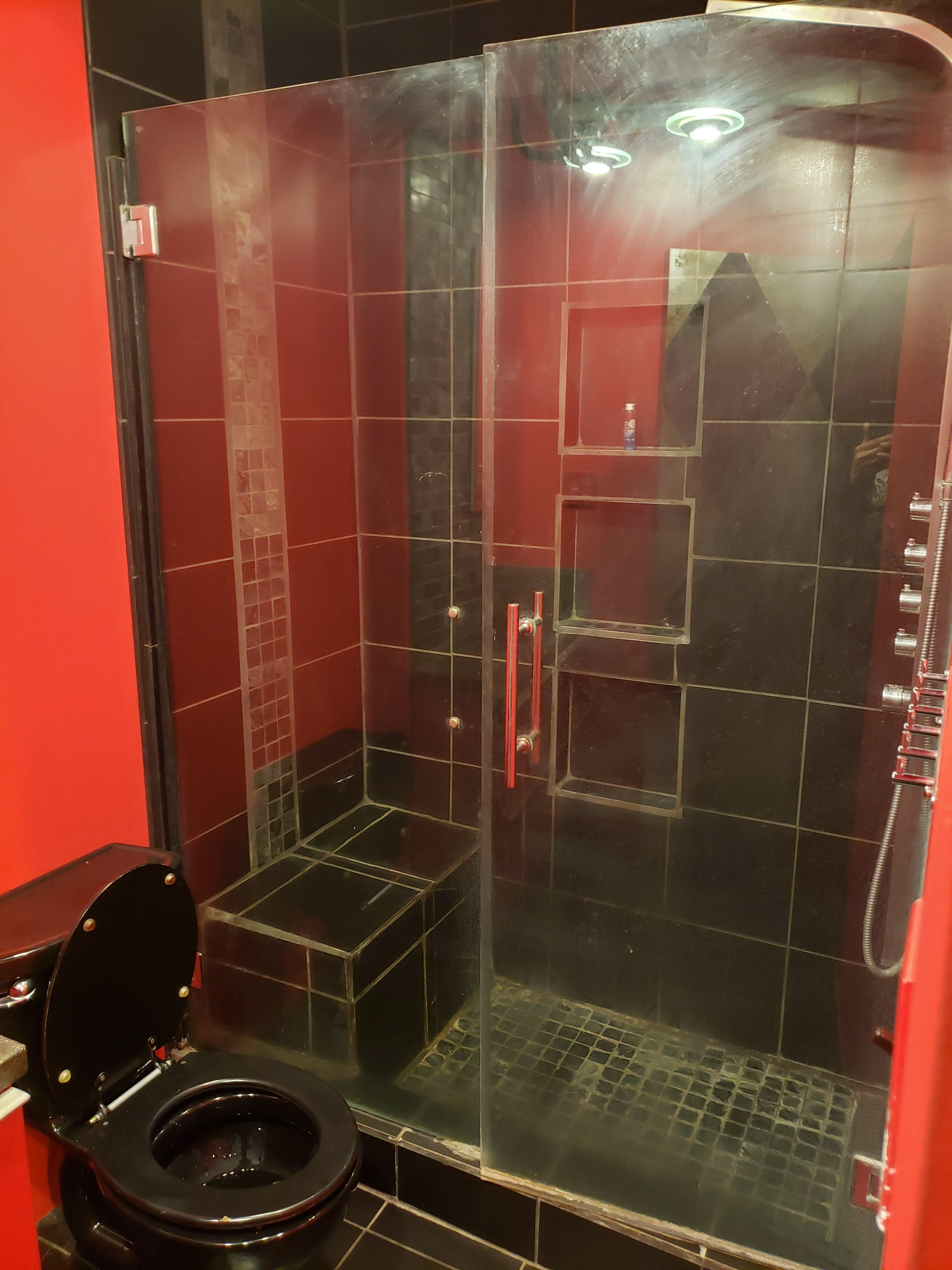

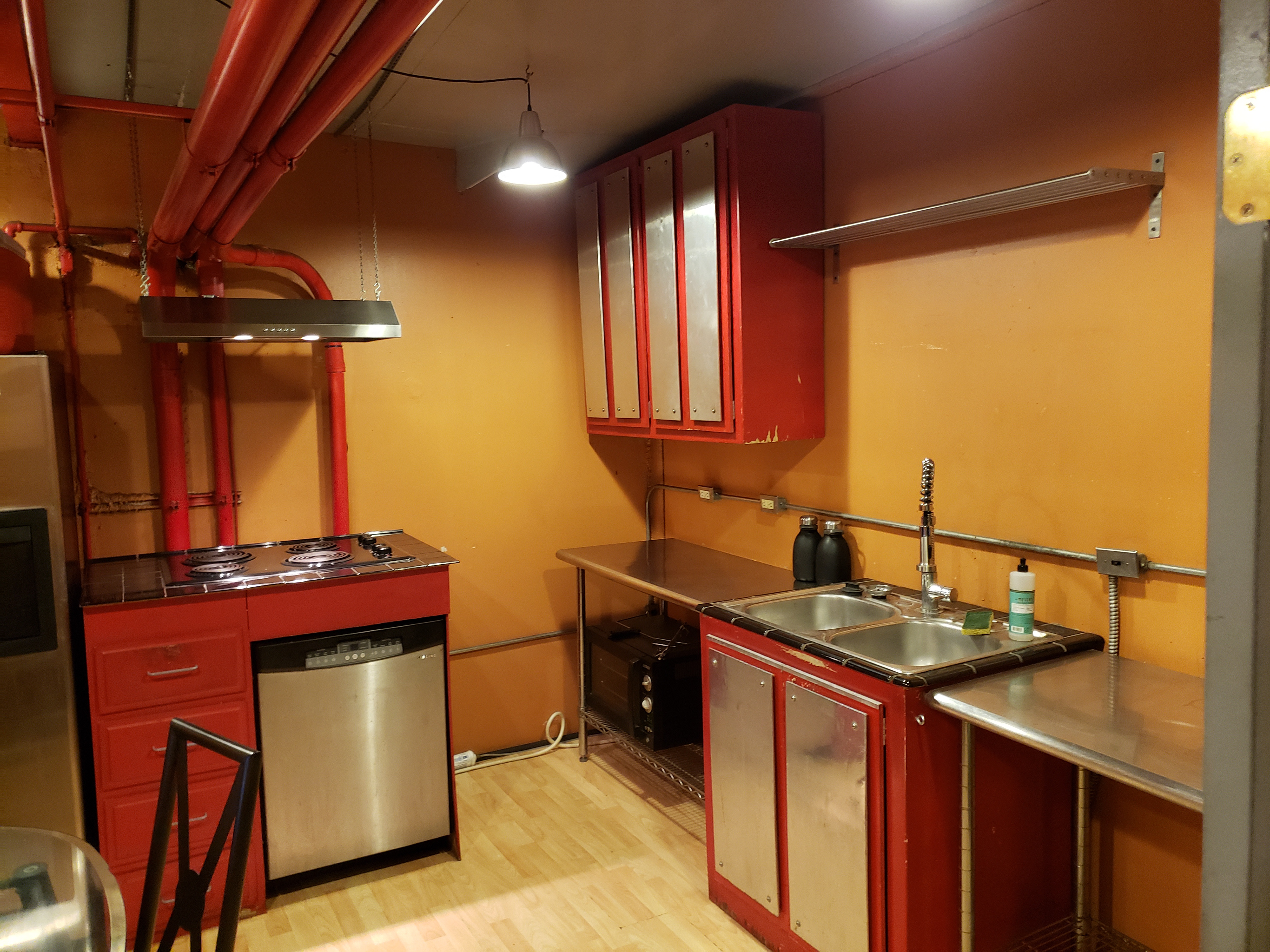
Back in 2003, working as an engineer for General Motors, I was quickly realizing that I was not going to have a career in the world of corporate America. So, I decided to start my own business. Several months prior, I had purchased a bankrupt screenprinting company. With more ambition than direction, I found a warehouse in Los Angeles and spent the next six months constructing a place to work and live.
With a big open space and a half-baked vision, I pulled out a nail gun and went for it. Still working full-time for General Motors, I work nights and weekends building a loft so I could have a shop downstairs and a showroom and living area upstairs.
After about a year of running the screen-printing business, and another year of making tools for building hot rods, I started the fire prop business Trick Concepts with my now wife. Quickly, we ran out of space and I framed out the rest of the front of the shop with some pallet racks to make a two-level mezzanine for back stock and shipping supplies.
Down the road, we decided to give the living area a facelift. We spent three weekends painting the living the room in a New Orleans style harlequin pattern. With a very limited budget, I made a new bathroom and shower, plus tiled the living room, all for around $1200. We also added a second shower to the downstairs bathroom.
We stayed here until 2020 when we moved to Arizona with our new business Intelligent Harvest Systems.
We stayed here until 2020 when we moved to Arizona with our new business Intelligent Harvest Systems.
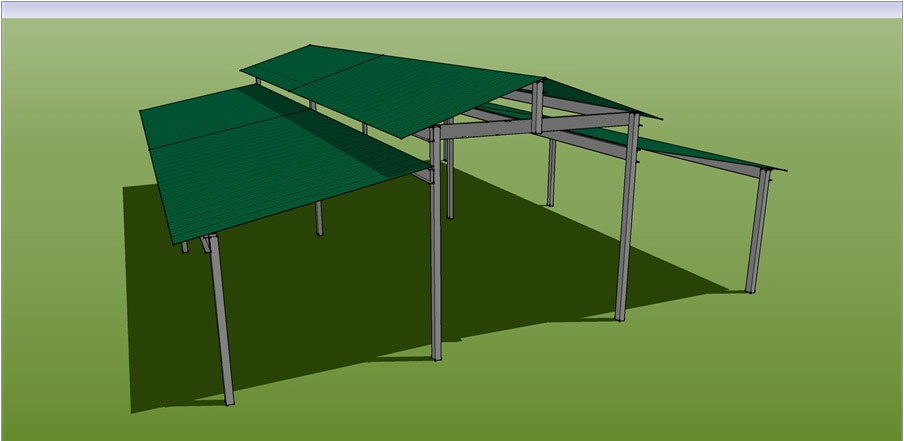
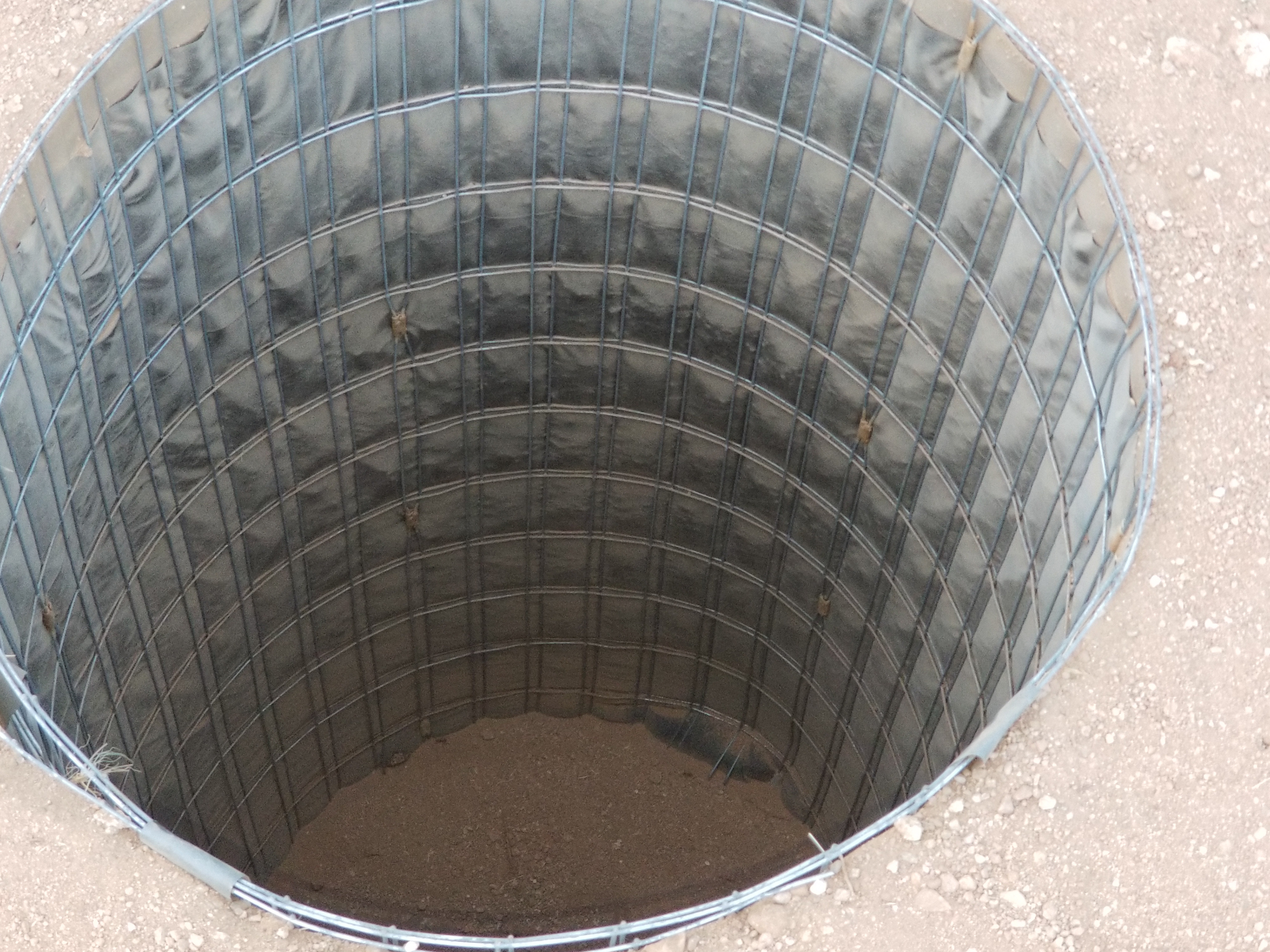
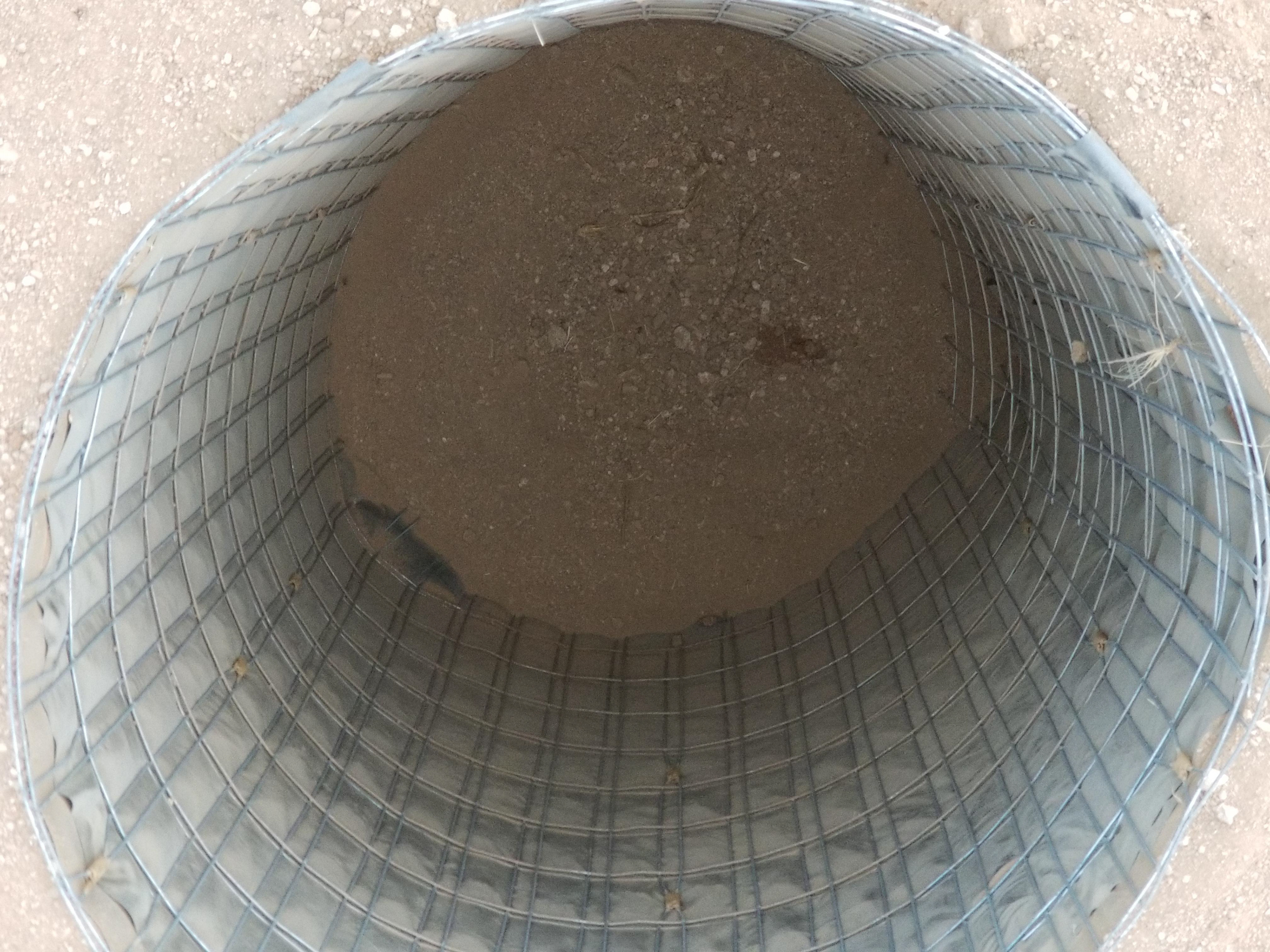
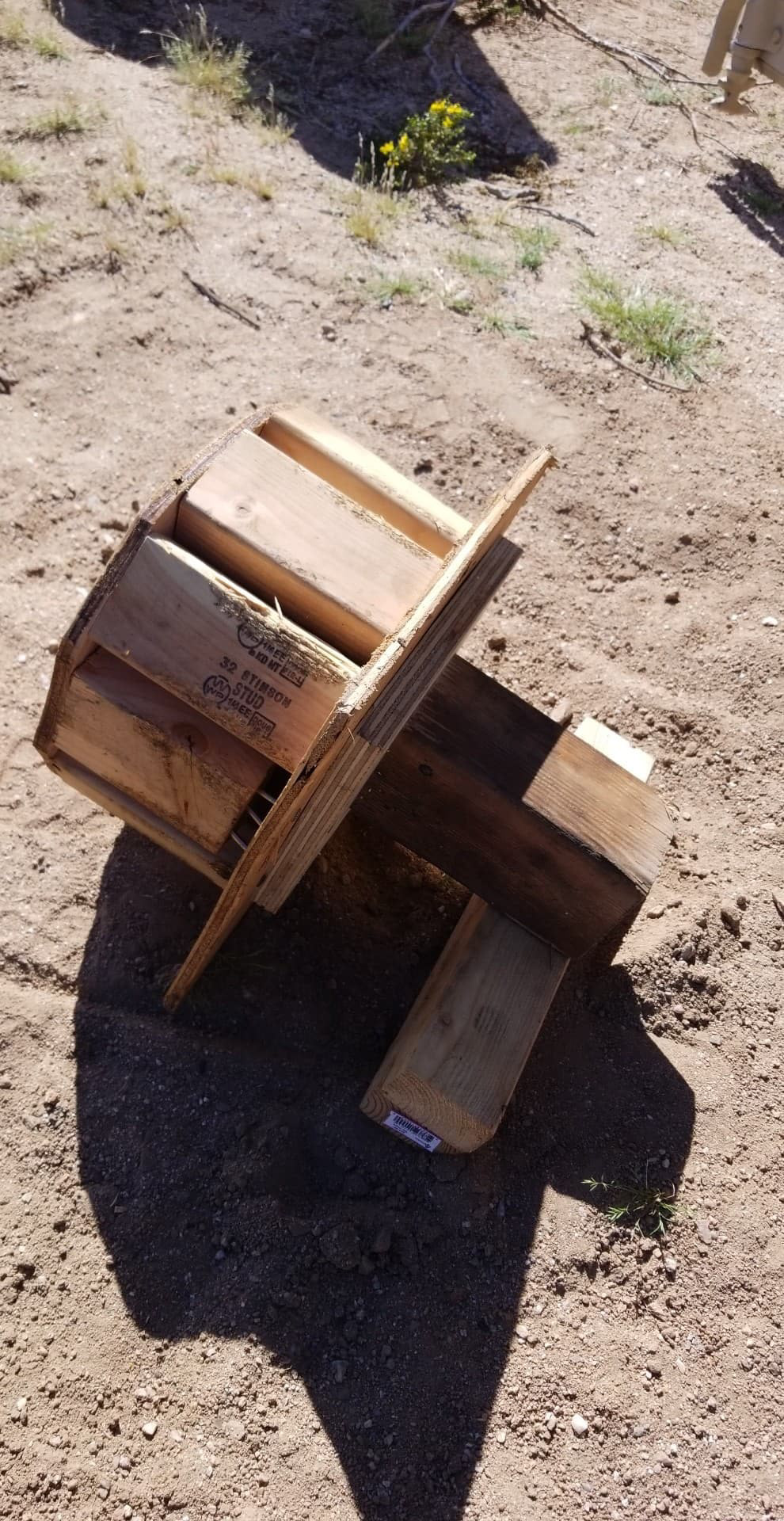
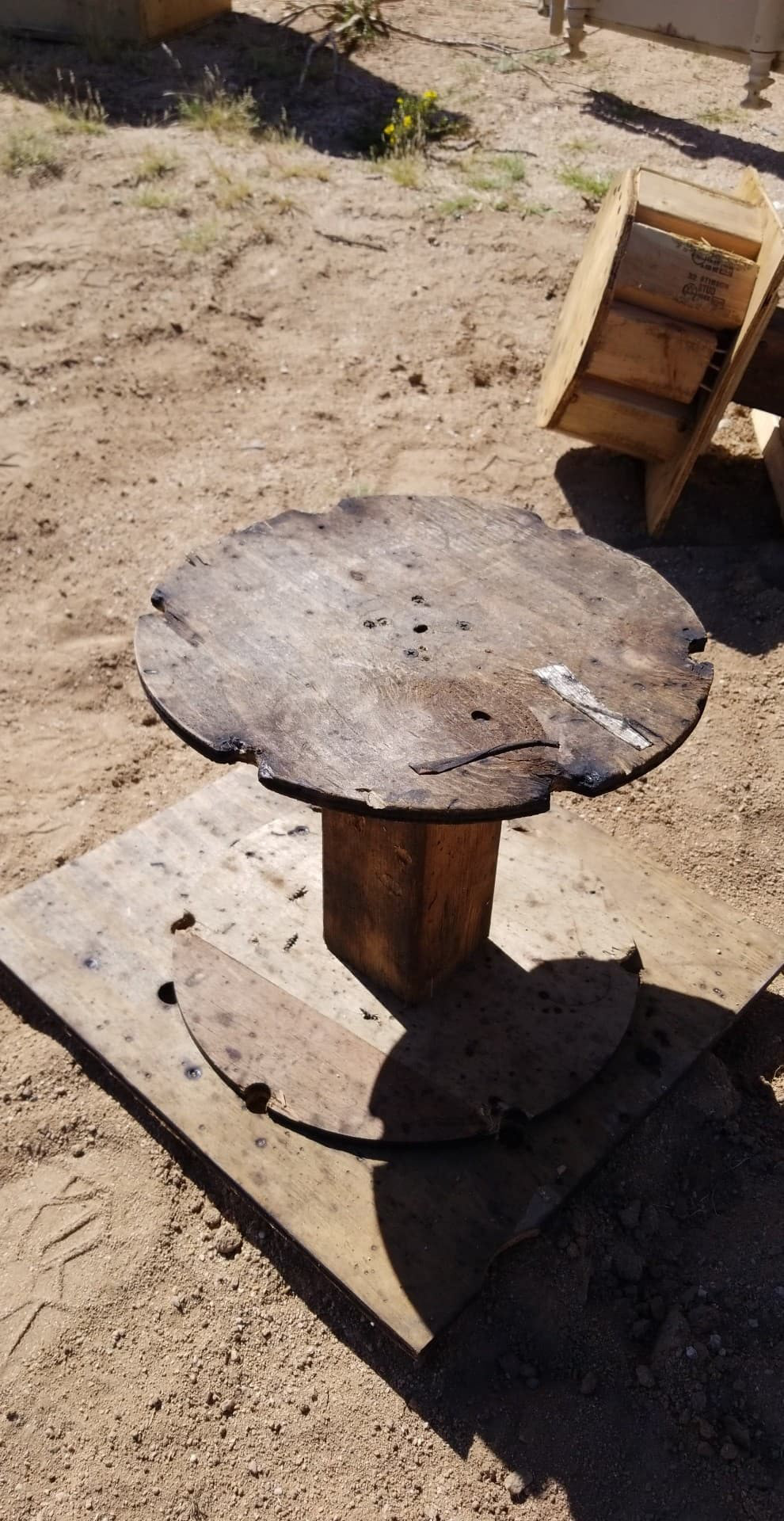
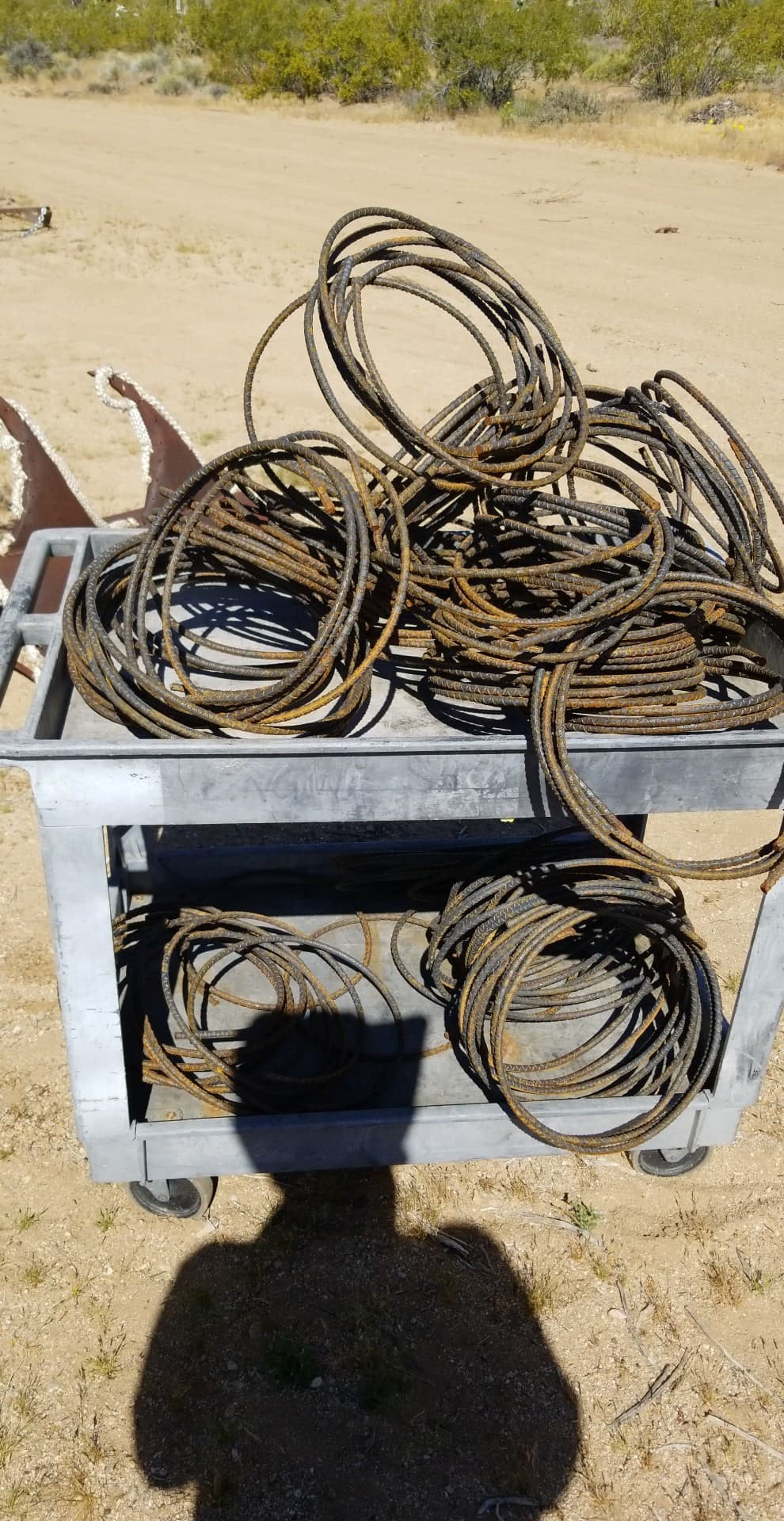
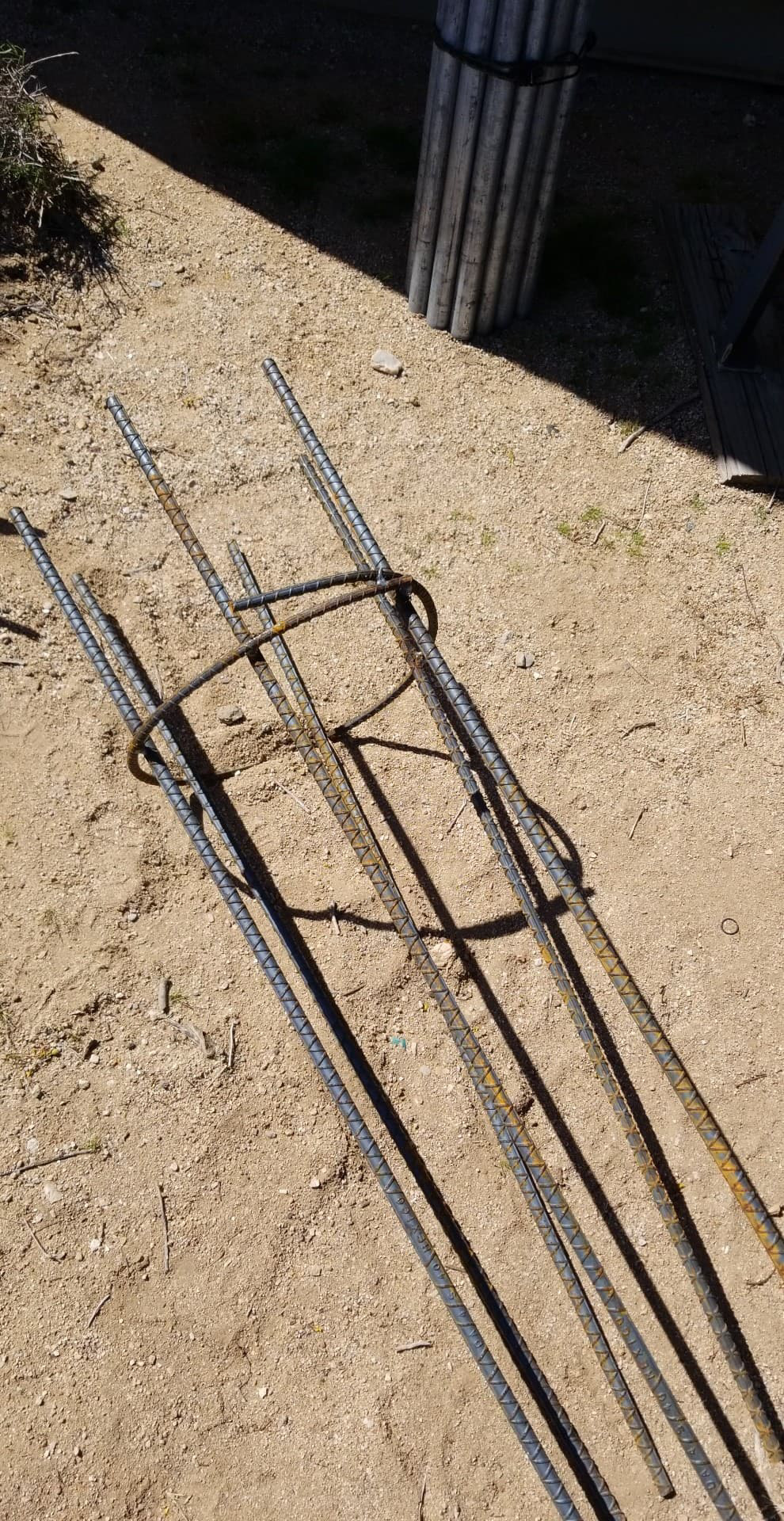
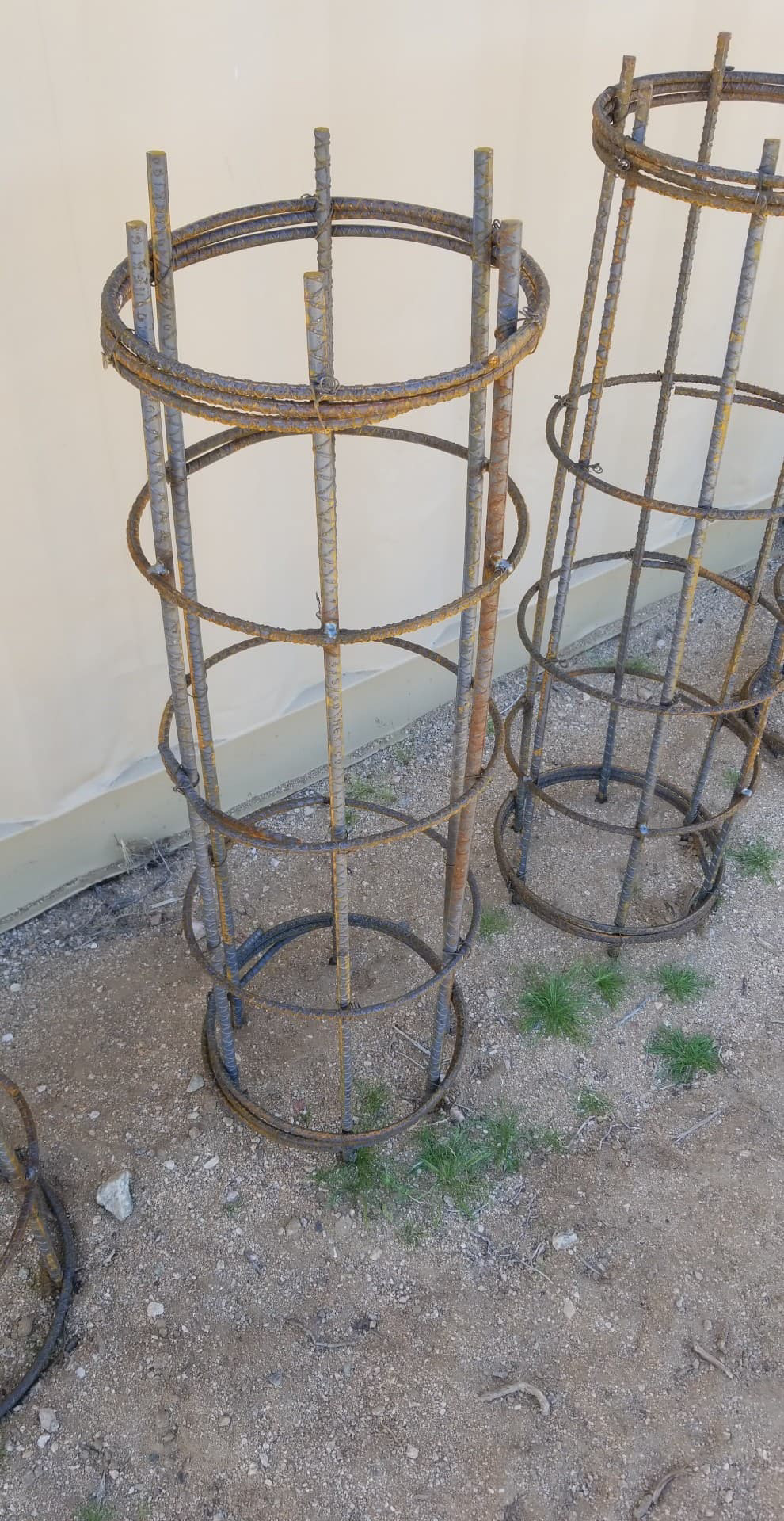
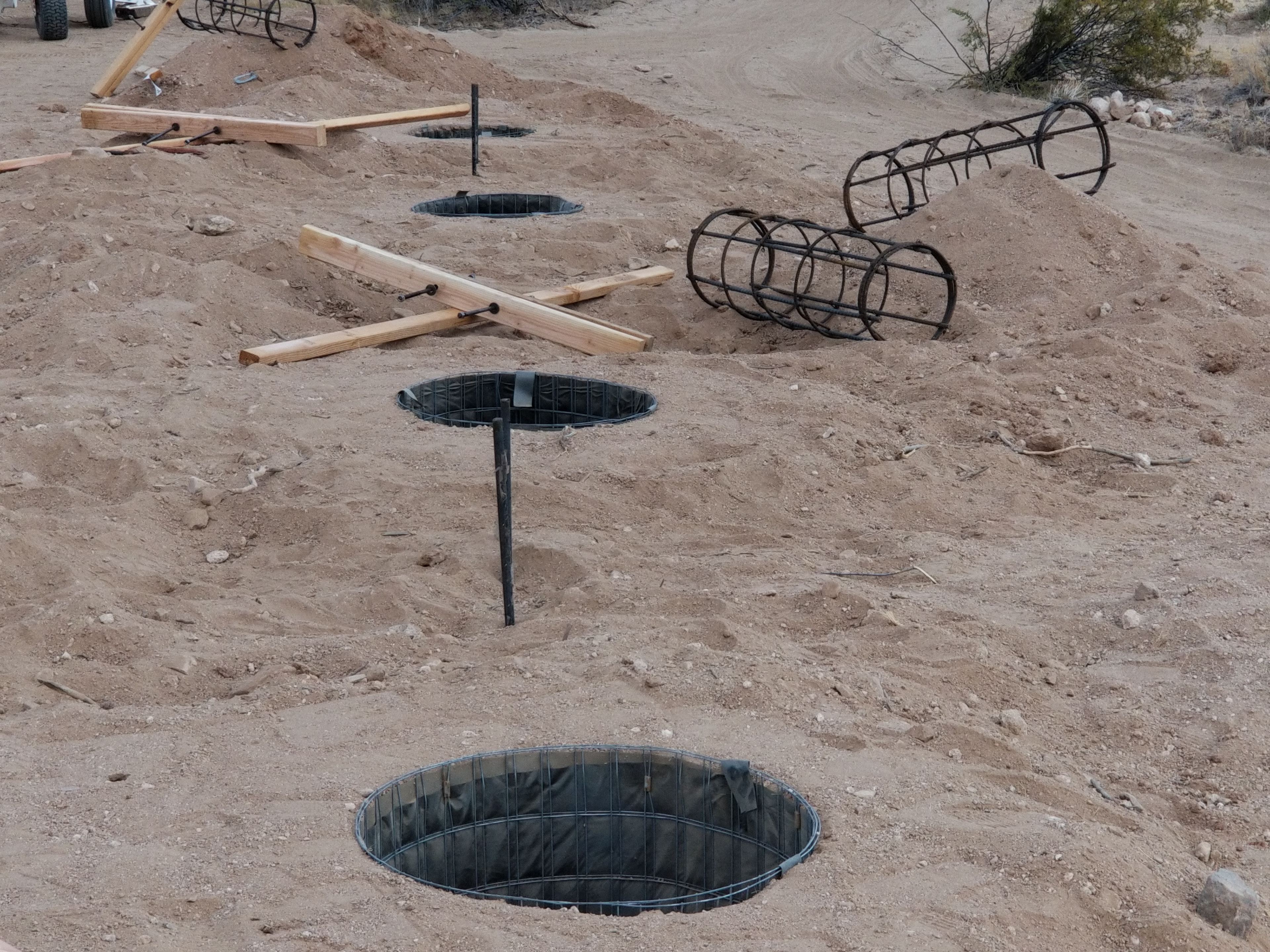
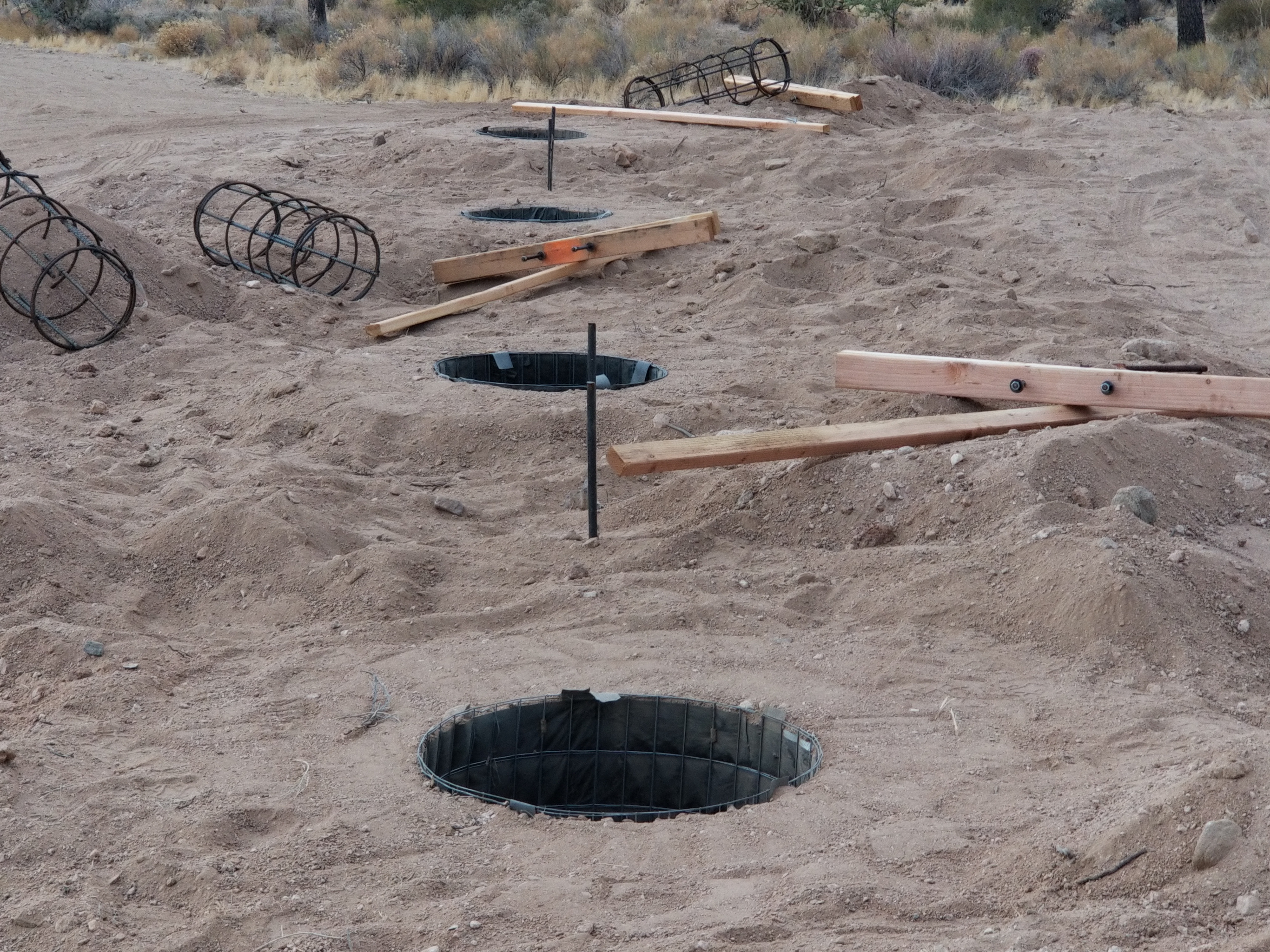
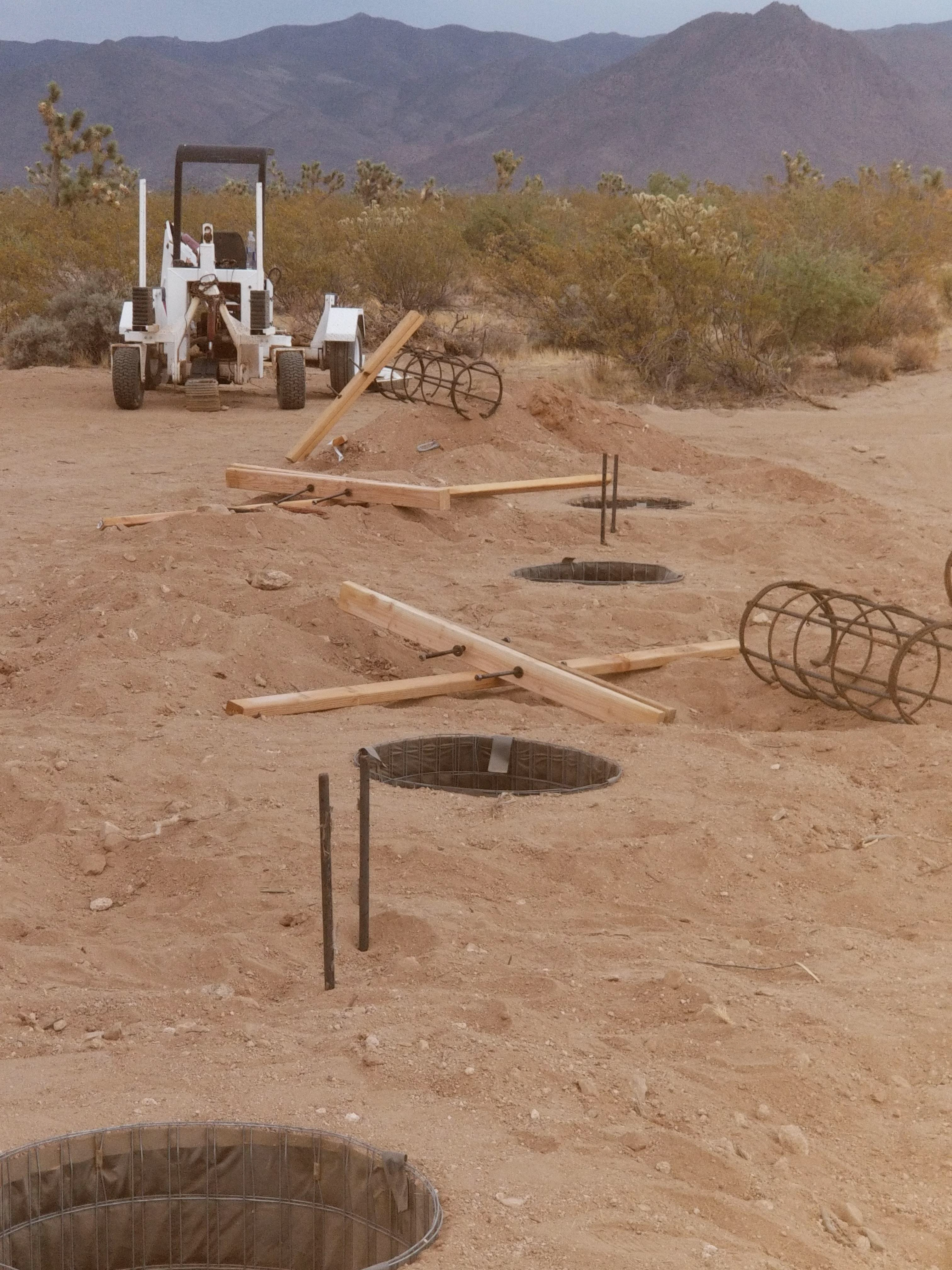
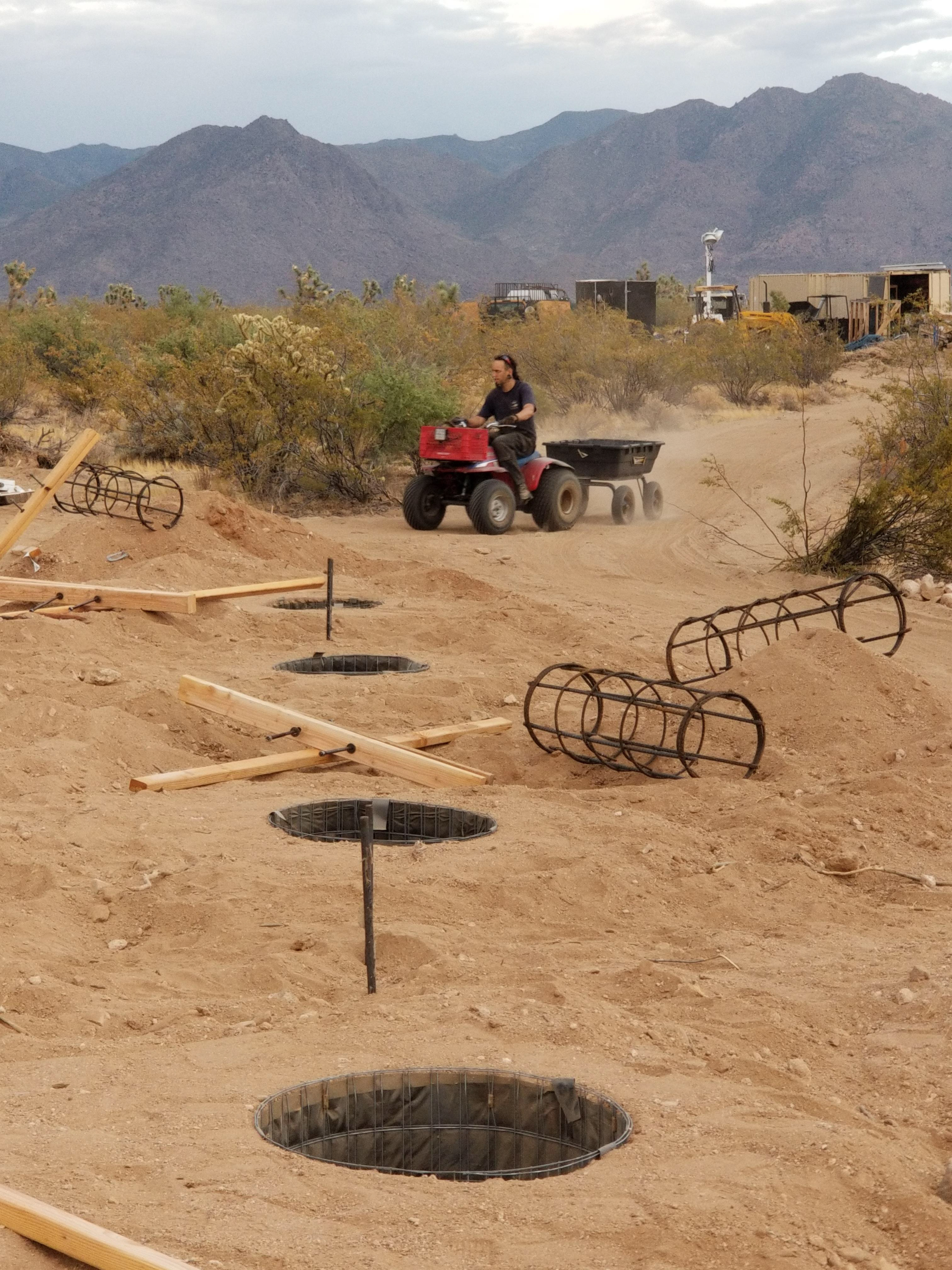
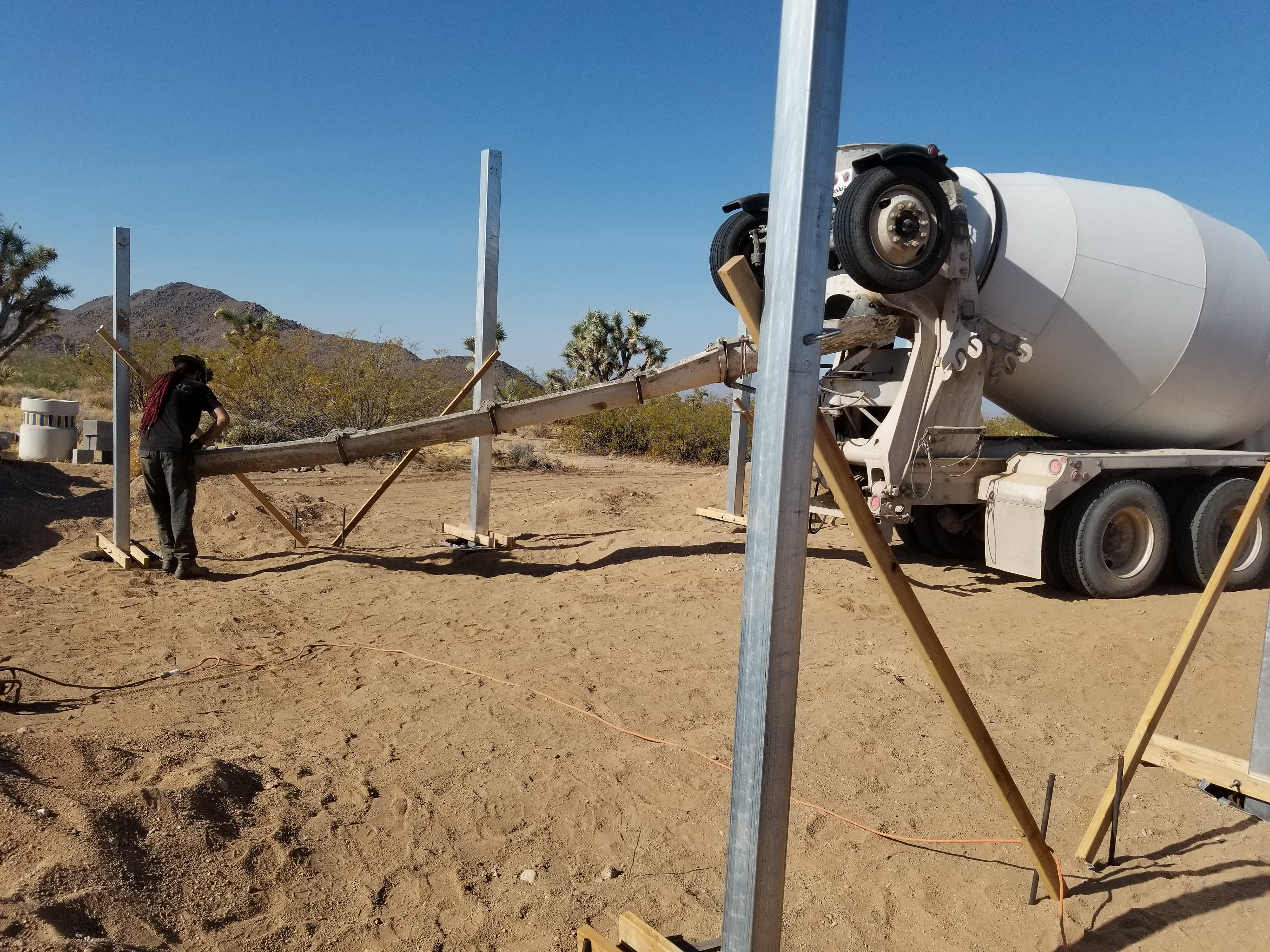
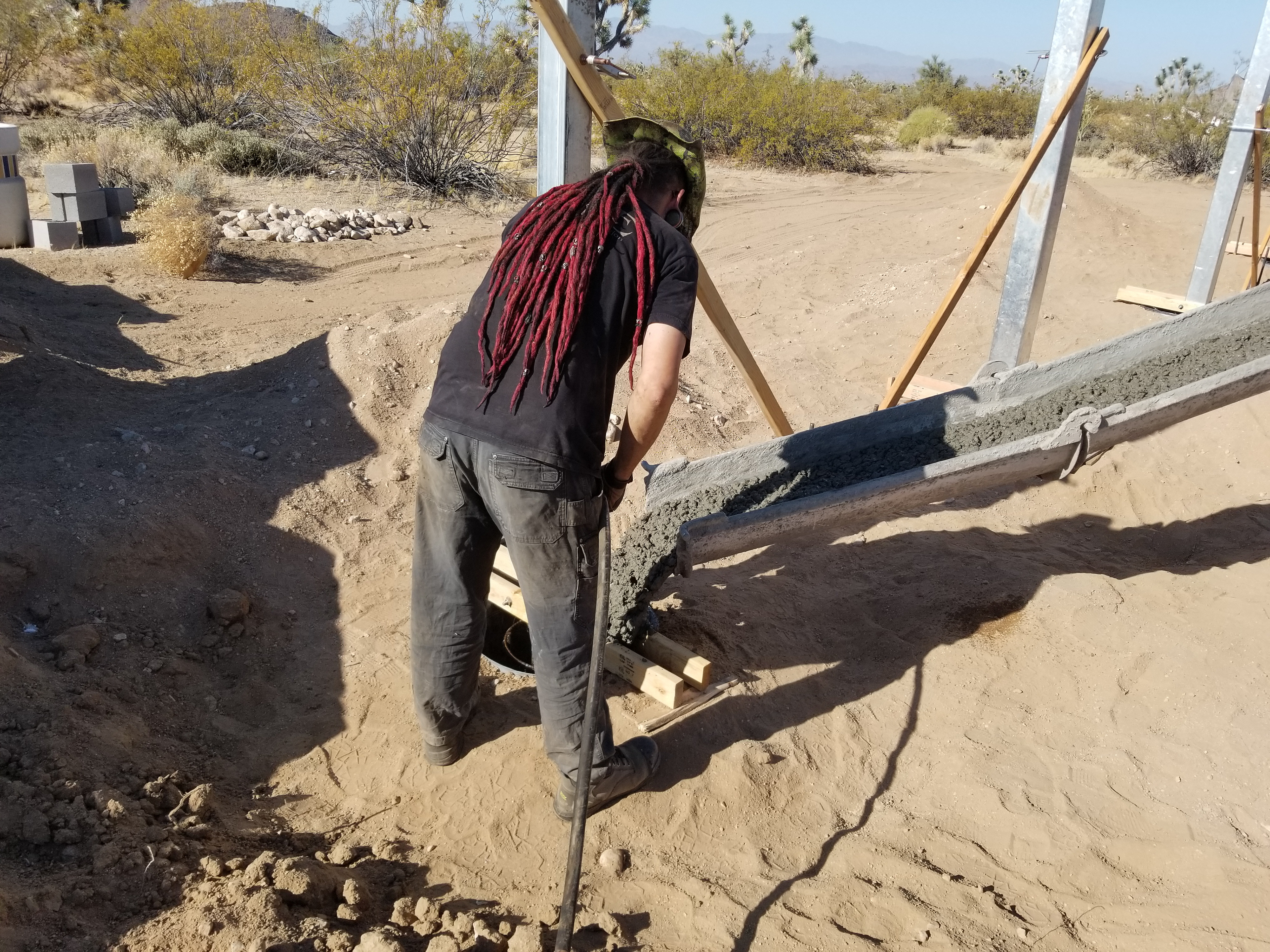
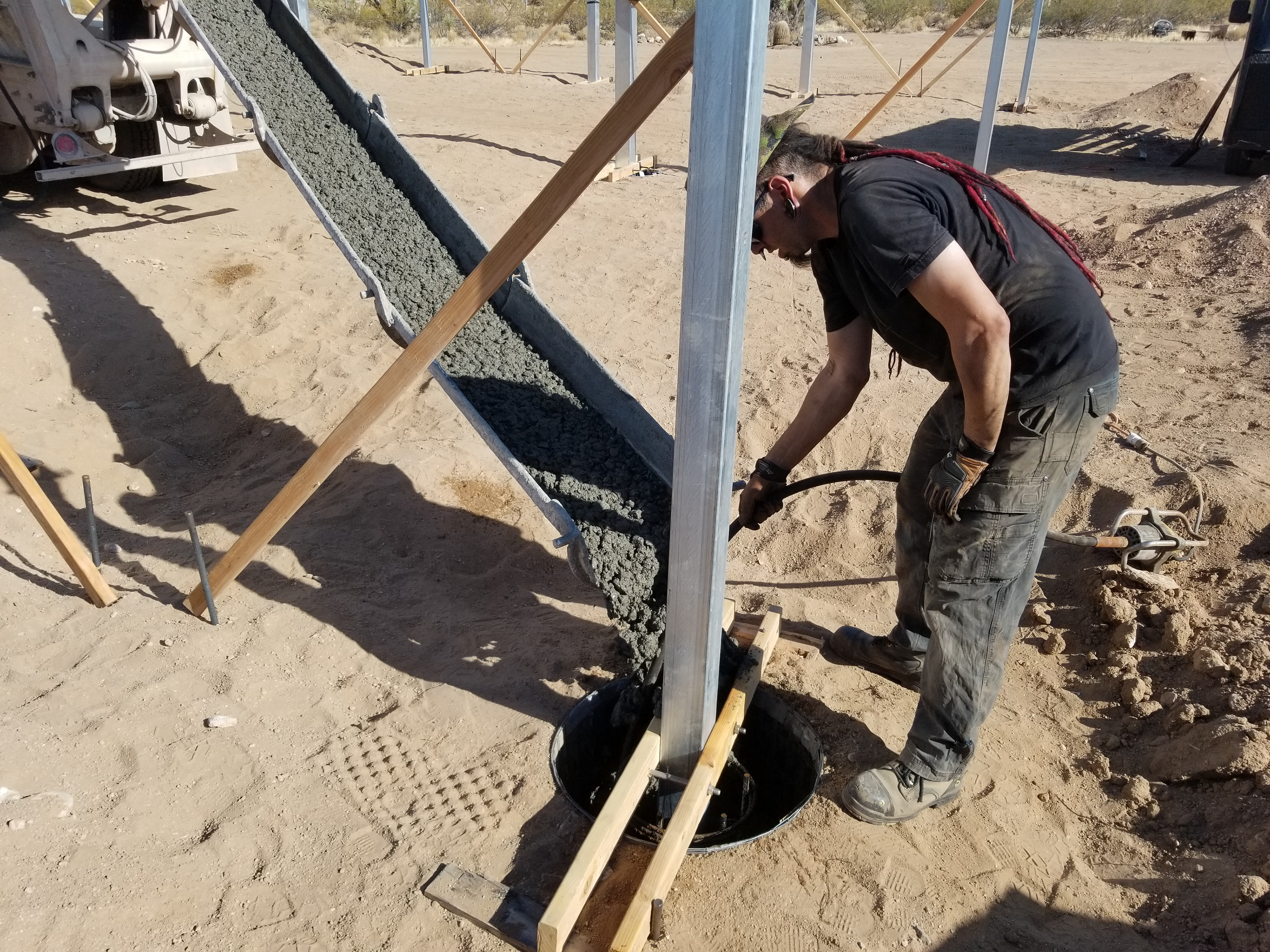
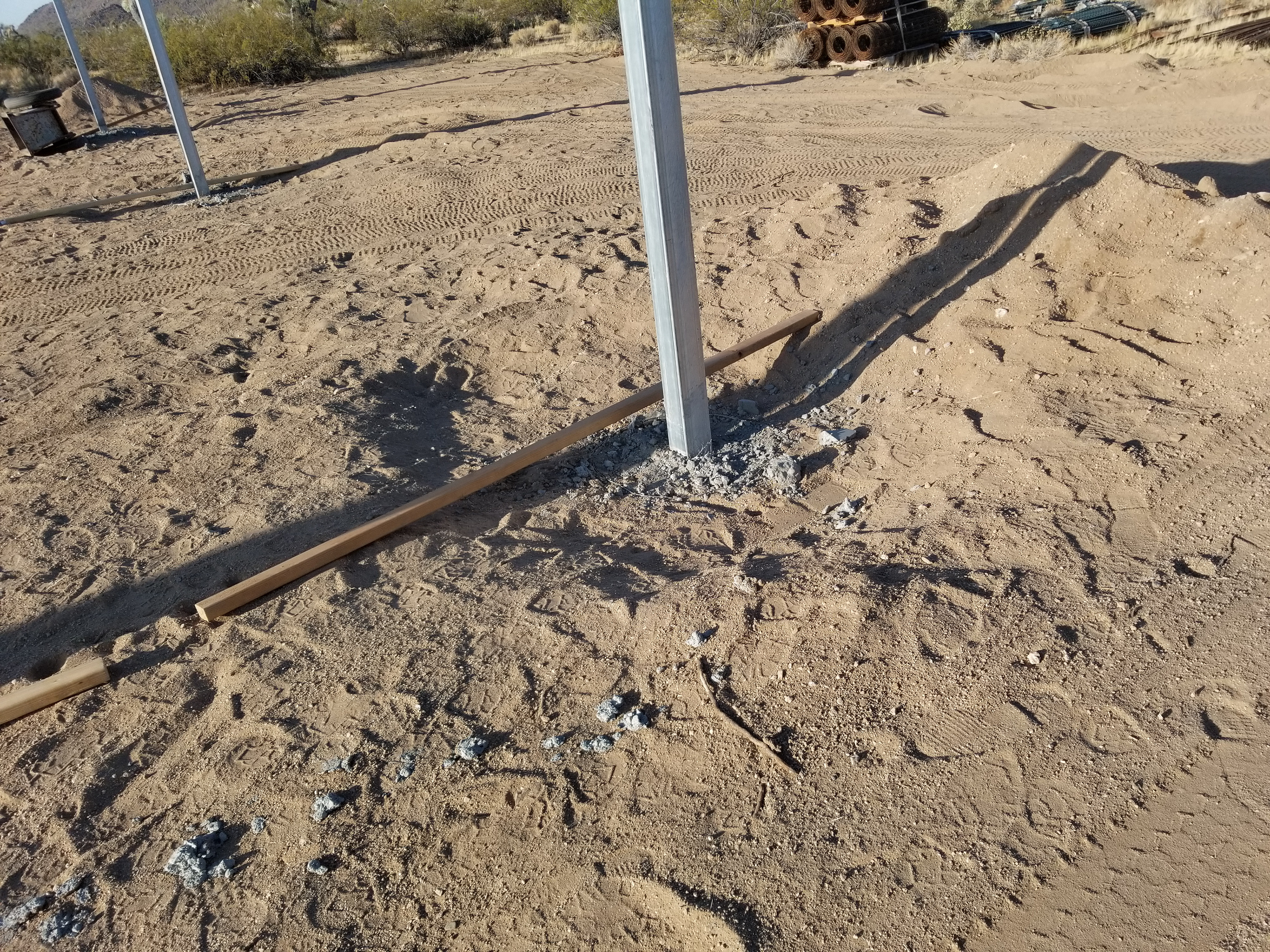
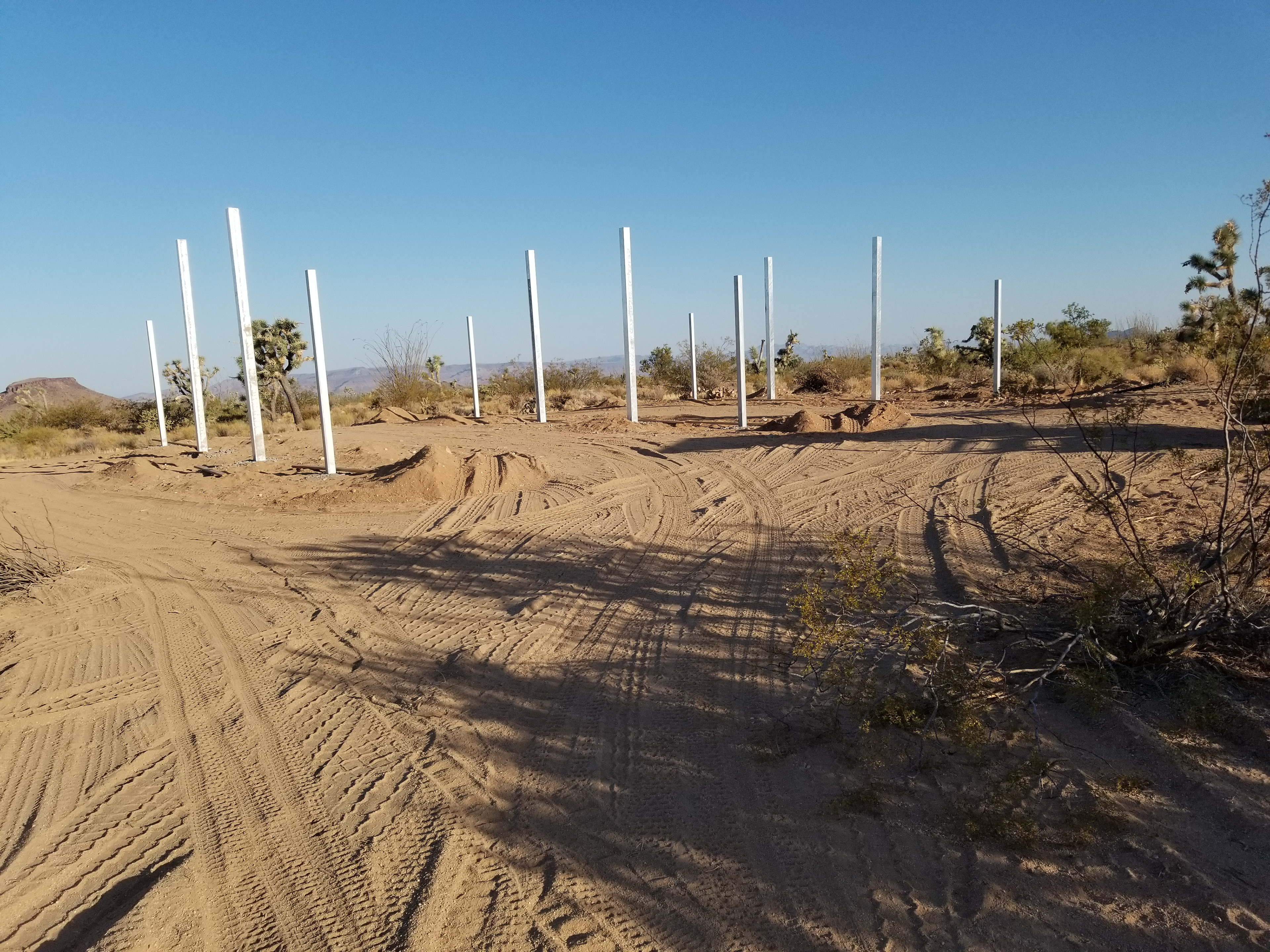
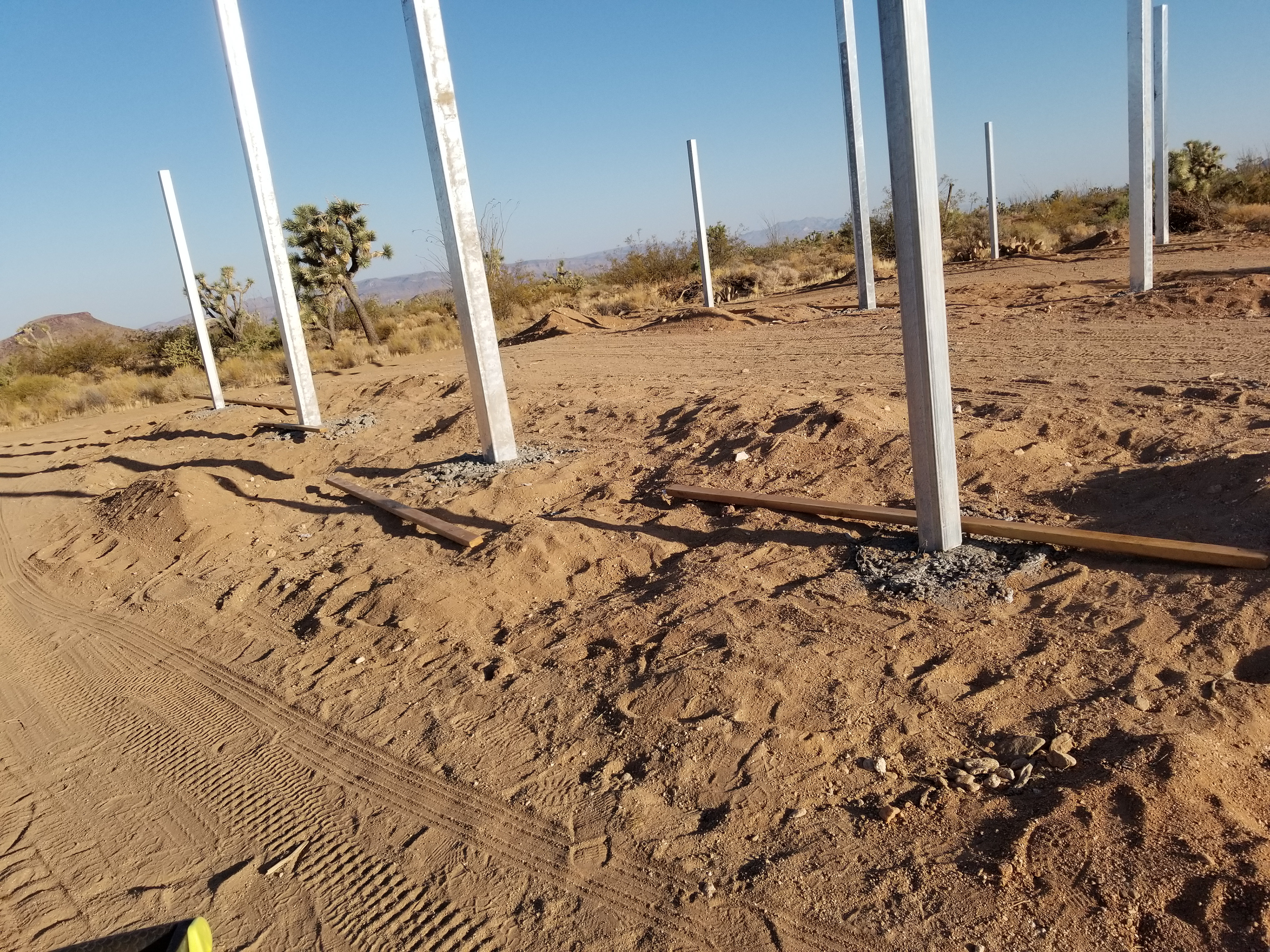
On our 40 acre property, we decided that it was time to start moving forward on developing the land. We decided to start with two 36’ x 48’ shelters. One would be converted into a shop, and other would be used as an outdoor living area with a barbecue, hot tub, fireplace and social area.
The plans called out for 2 foot diameter and 4 foot deep concrete piers for all 24 post. While this was probably complete overkill, that’s with the engineer requested. With the price of 24” carboard sonotubes being out of my budget and difficult to get, I made some cages out of hardware cloth and plastic film.
I also had to build 24 rebar cages so I made some simple wood fixtures to roll the rings. I welded the top ring in place with the 6 straight pieces for each cage. My wife had the fun job of wiring on the rest of the rings on. Digging the 24 holes and positioning all the cages in the correct location became a quite time-consuming endeavor. I ended up wiring all the cages to the vertical post and then set the whole assembly in the hole with my tractor. After everything was secured in place, I ordered 10 yards of concrete, which just barely finish the job.
I also had to build 24 rebar cages so I made some simple wood fixtures to roll the rings. I welded the top ring in place with the 6 straight pieces for each cage. My wife had the fun job of wiring on the rest of the rings on. Digging the 24 holes and positioning all the cages in the correct location became a quite time-consuming endeavor. I ended up wiring all the cages to the vertical post and then set the whole assembly in the hole with my tractor. After everything was secured in place, I ordered 10 yards of concrete, which just barely finish the job.
After the post were installed, we ended up purchasing another property nearby with a house and shop on it. This project is on hold until the house is remodeled and the business is completely up and running in the new location.