Every machine is a smoke machine under the right conditions.
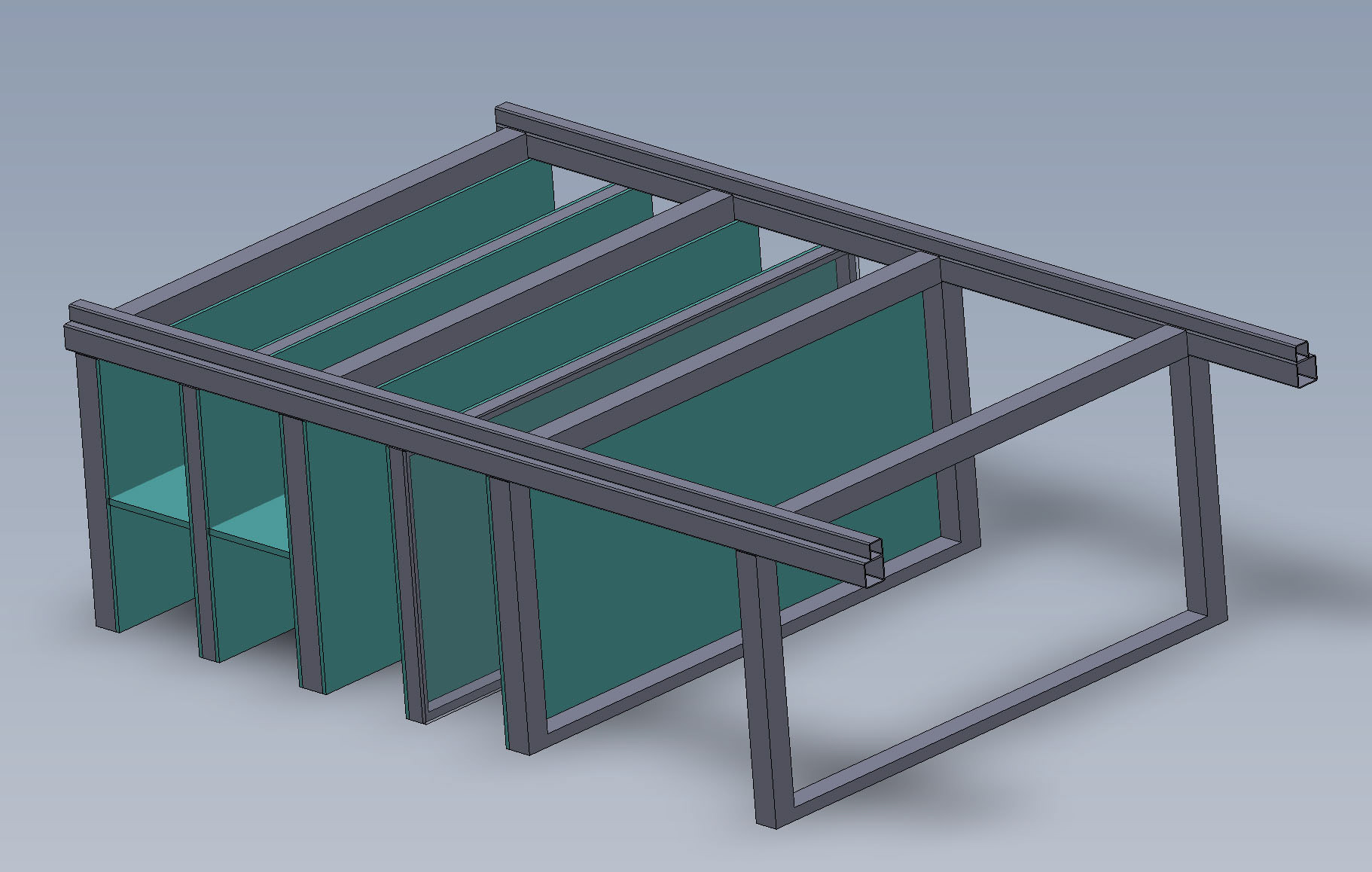
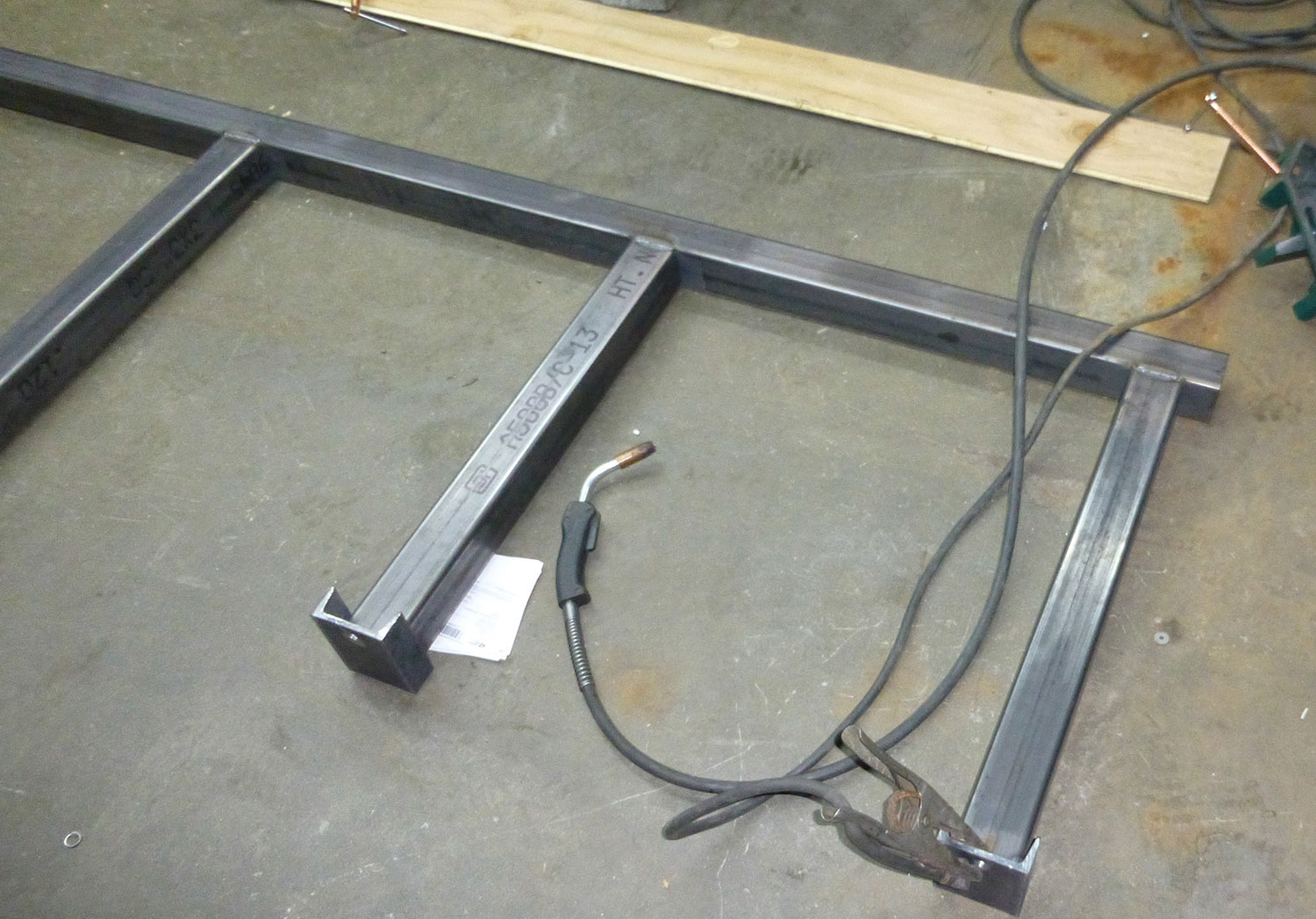
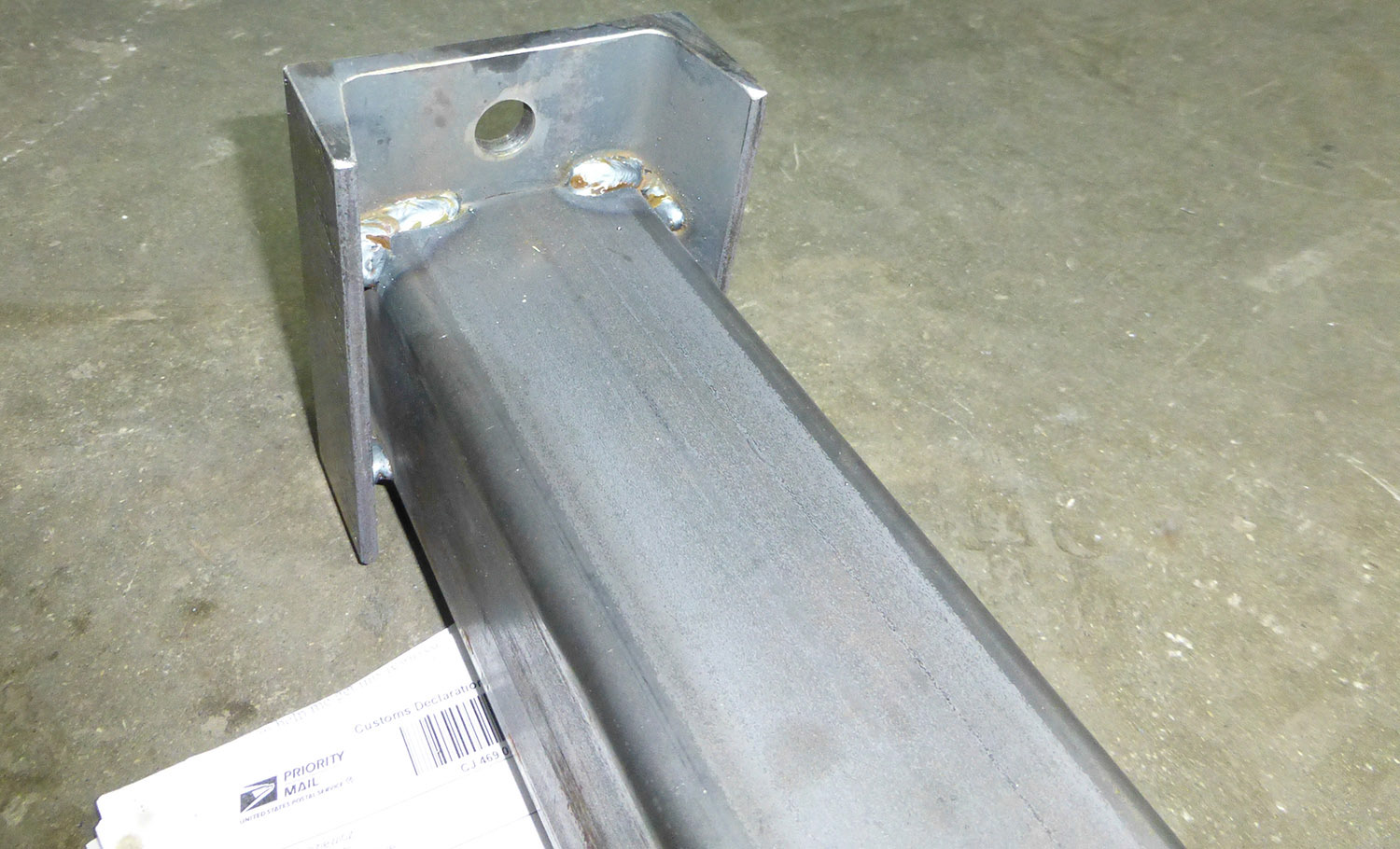
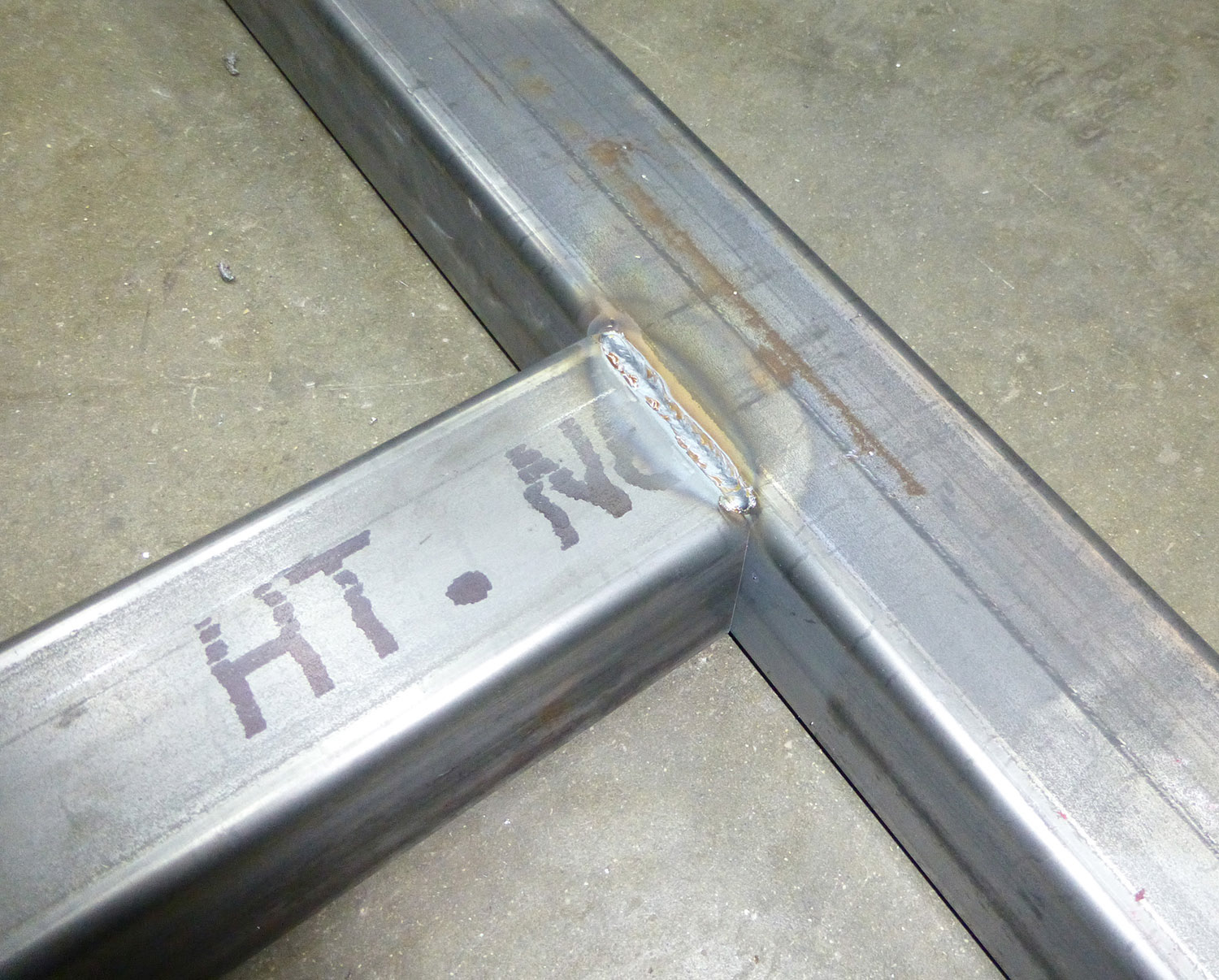
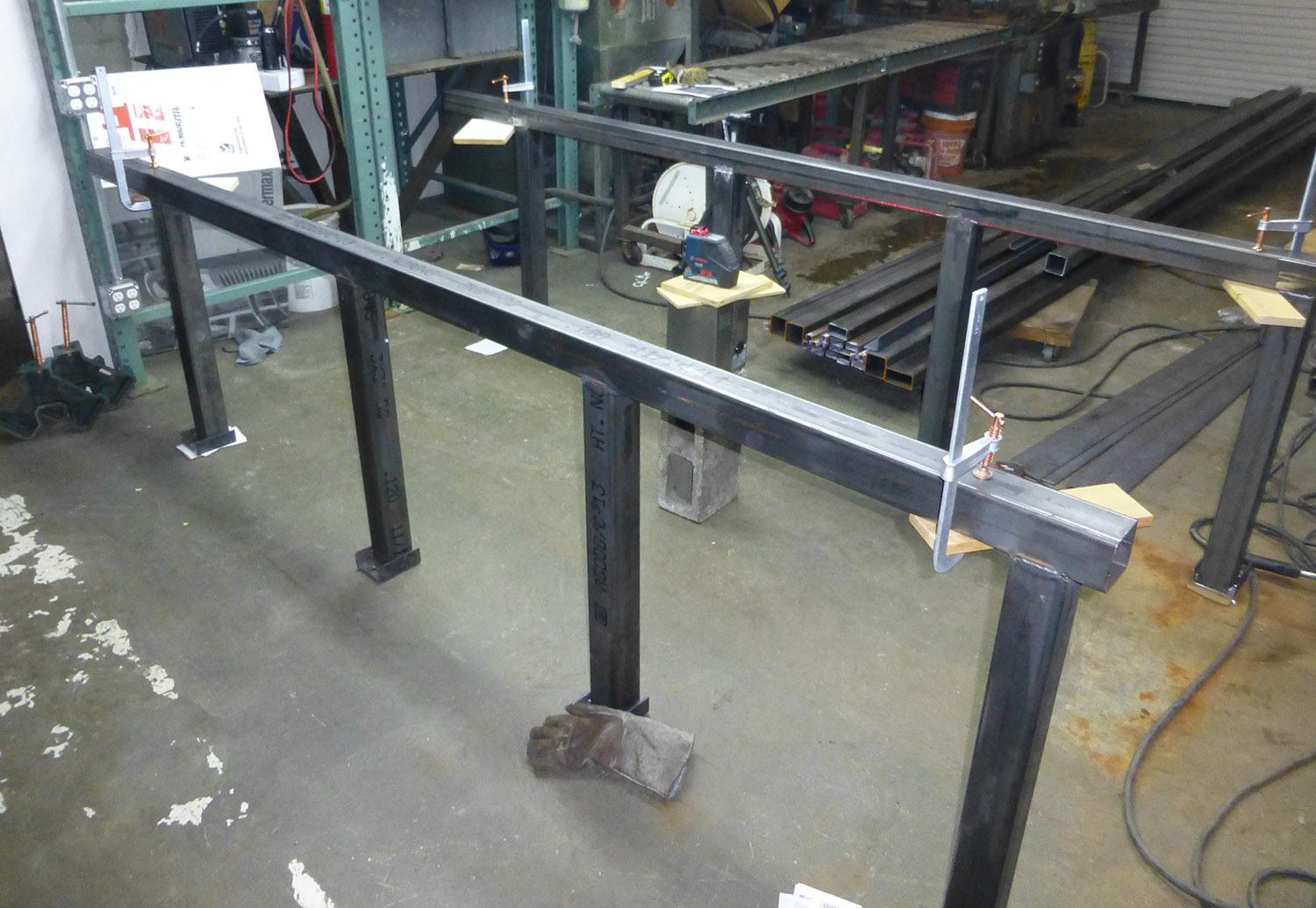
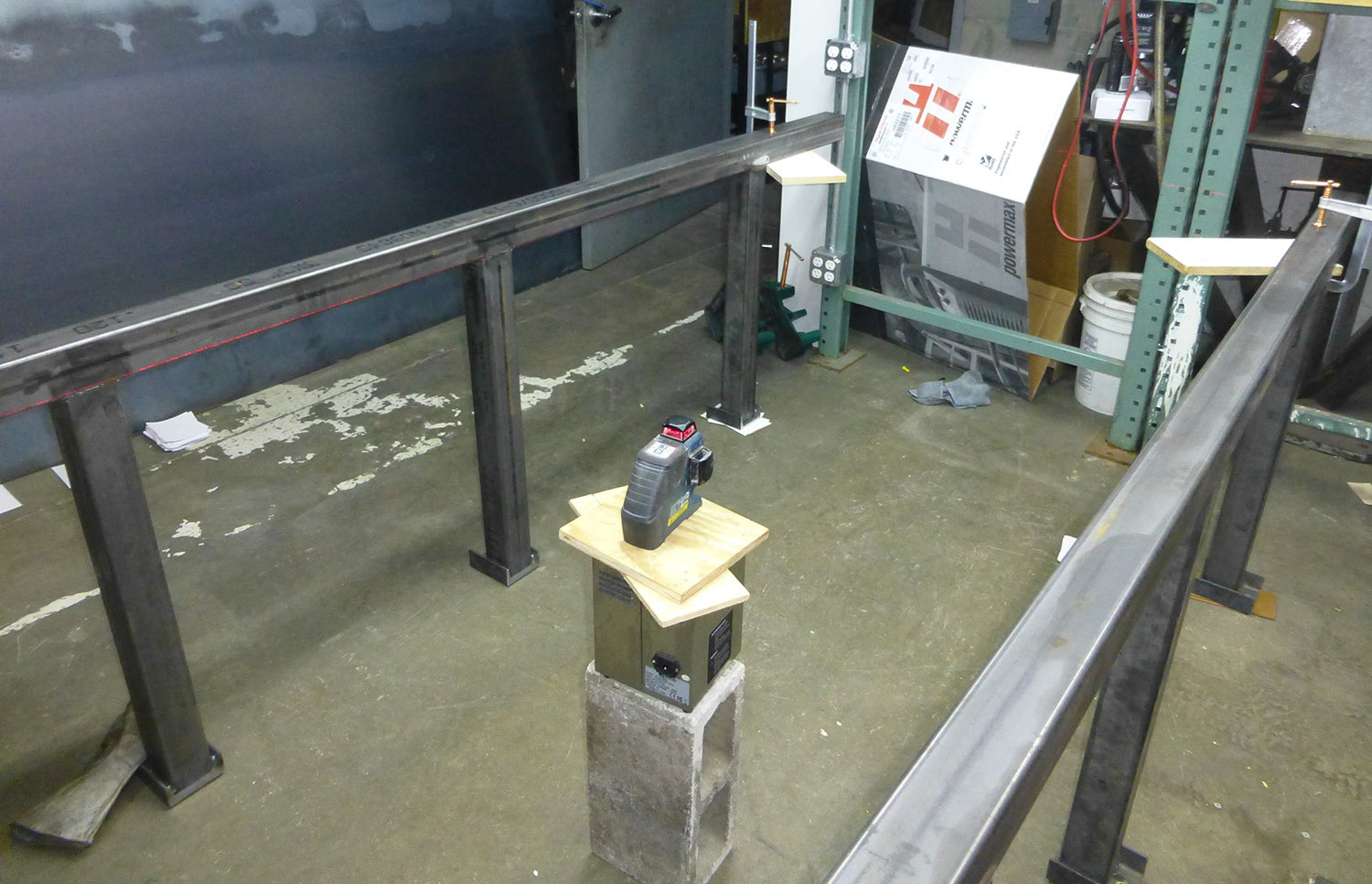
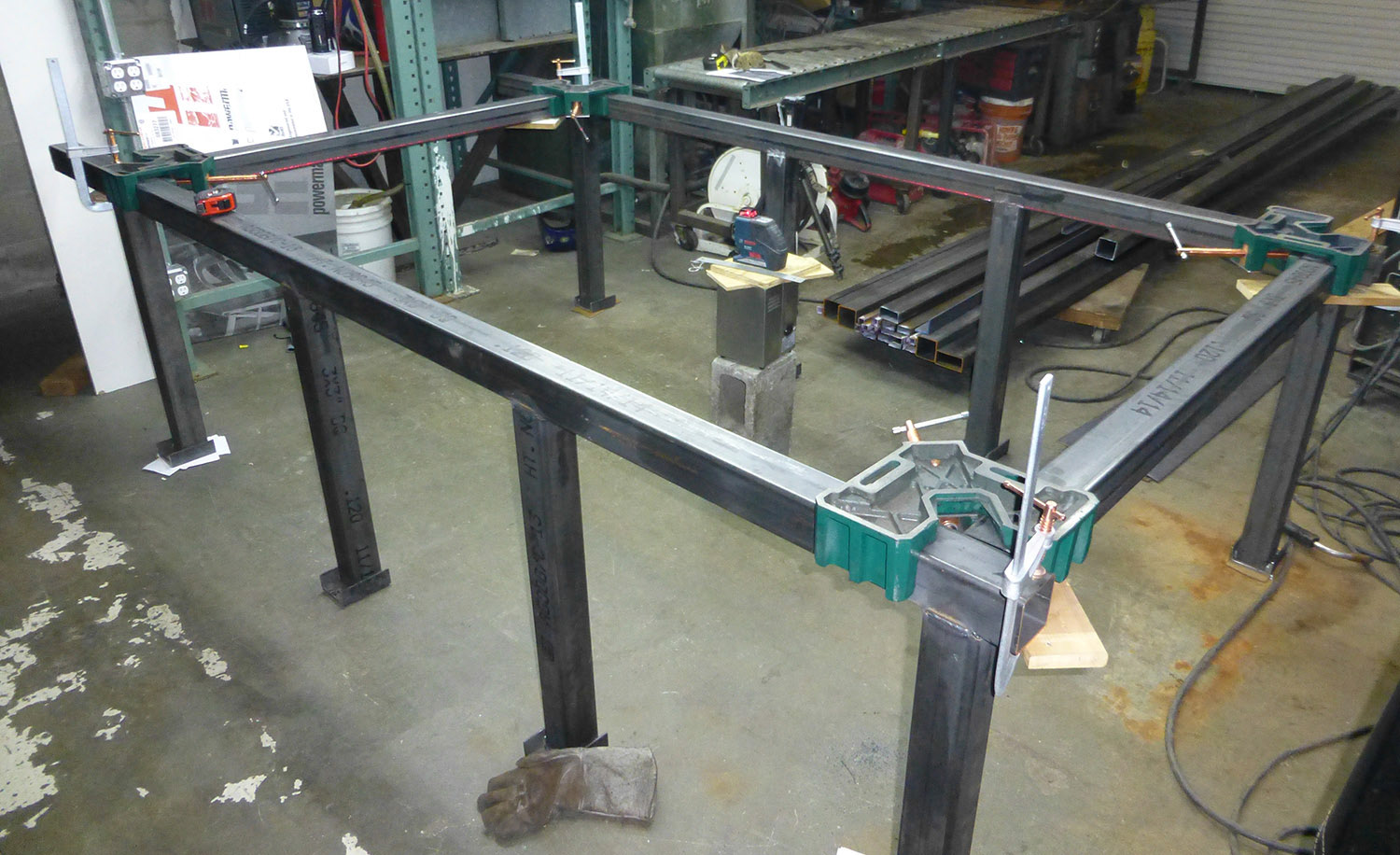
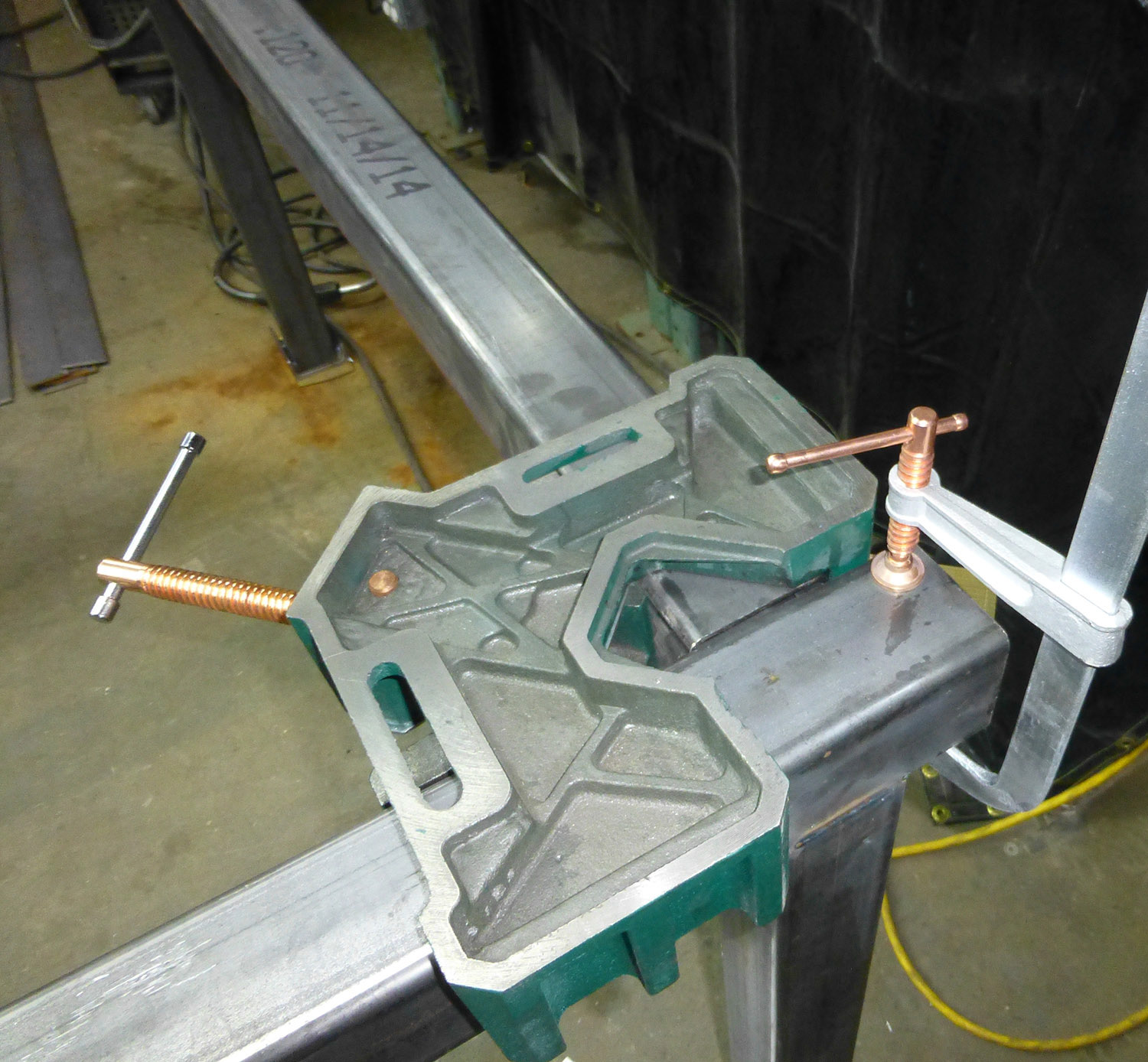
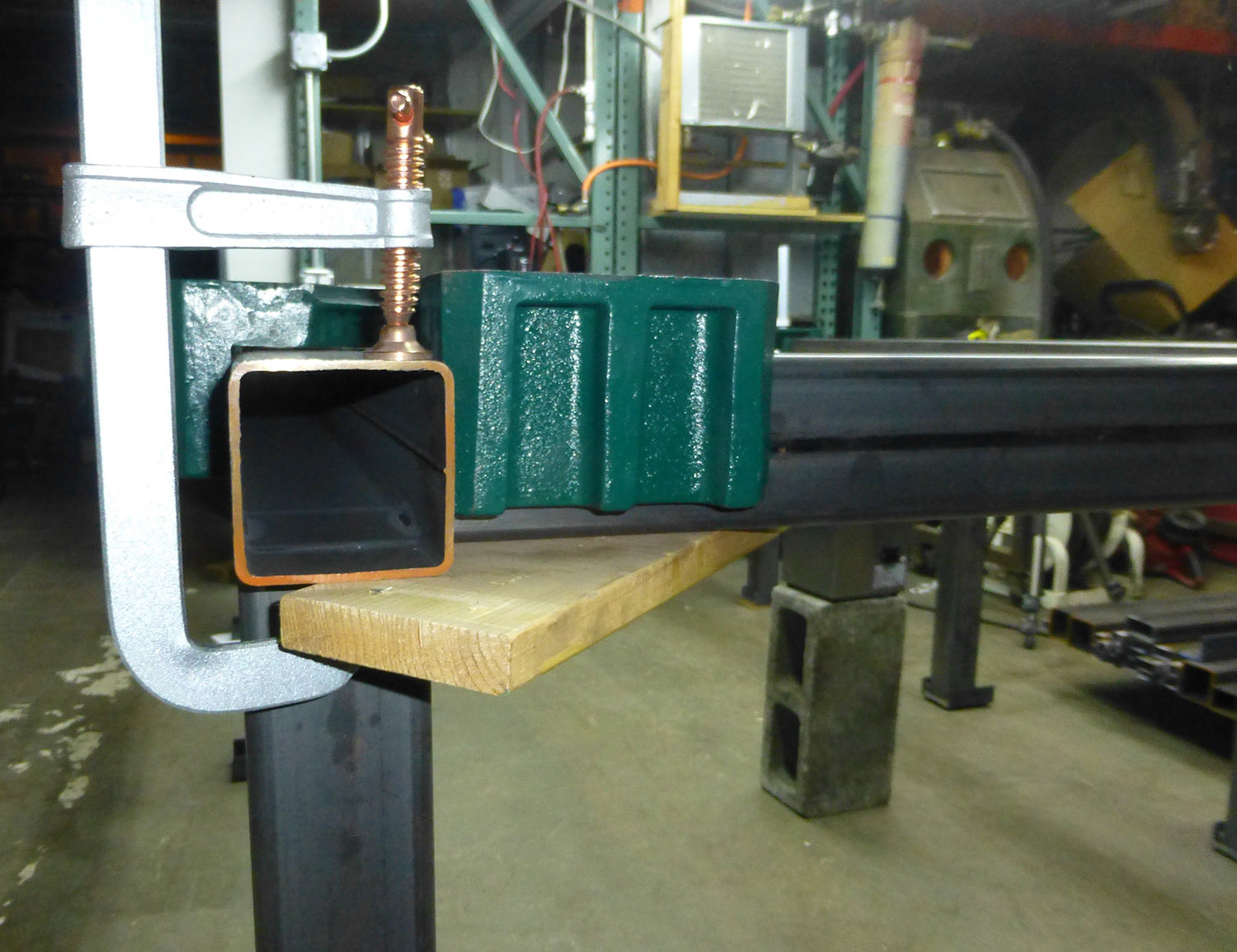
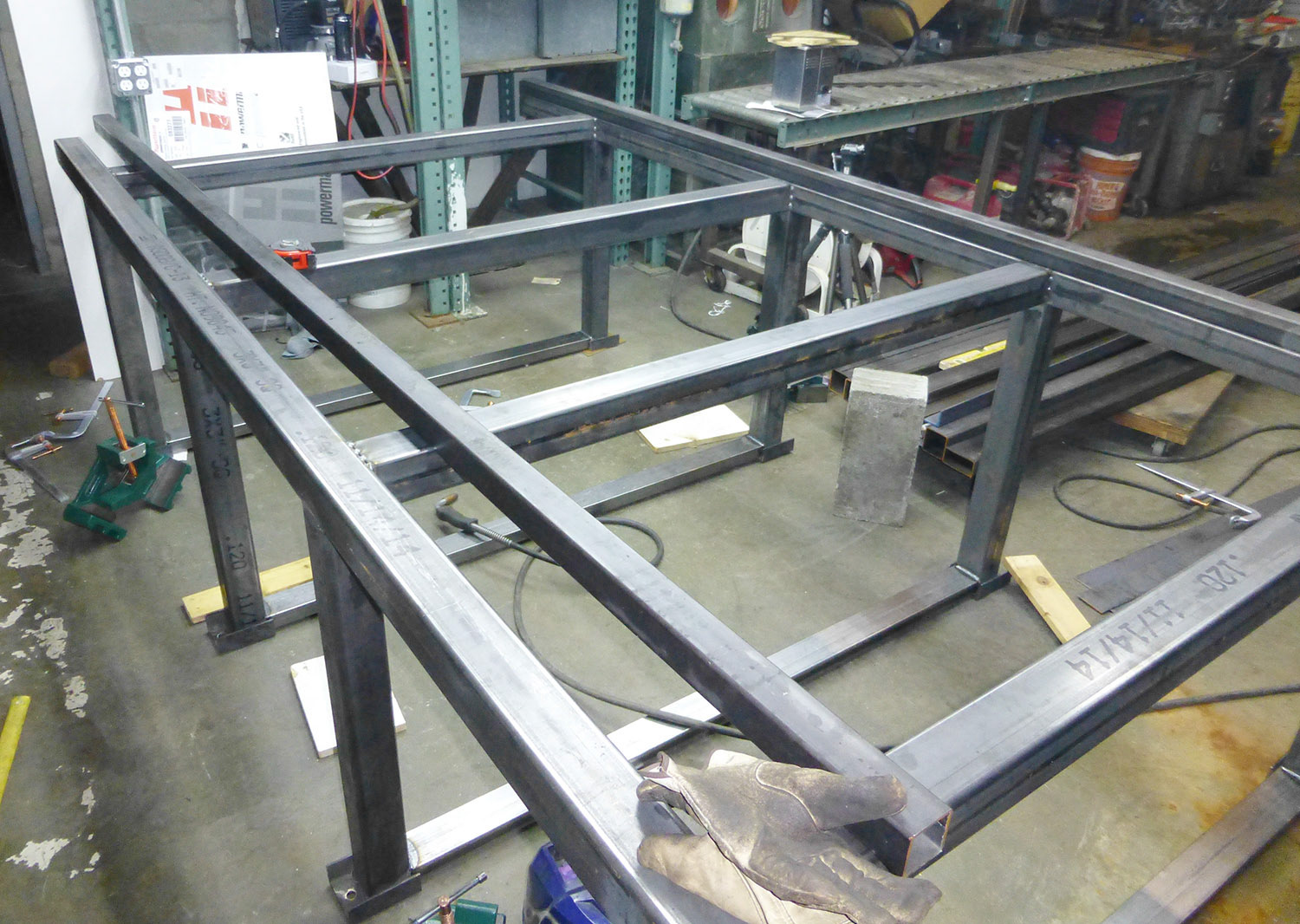
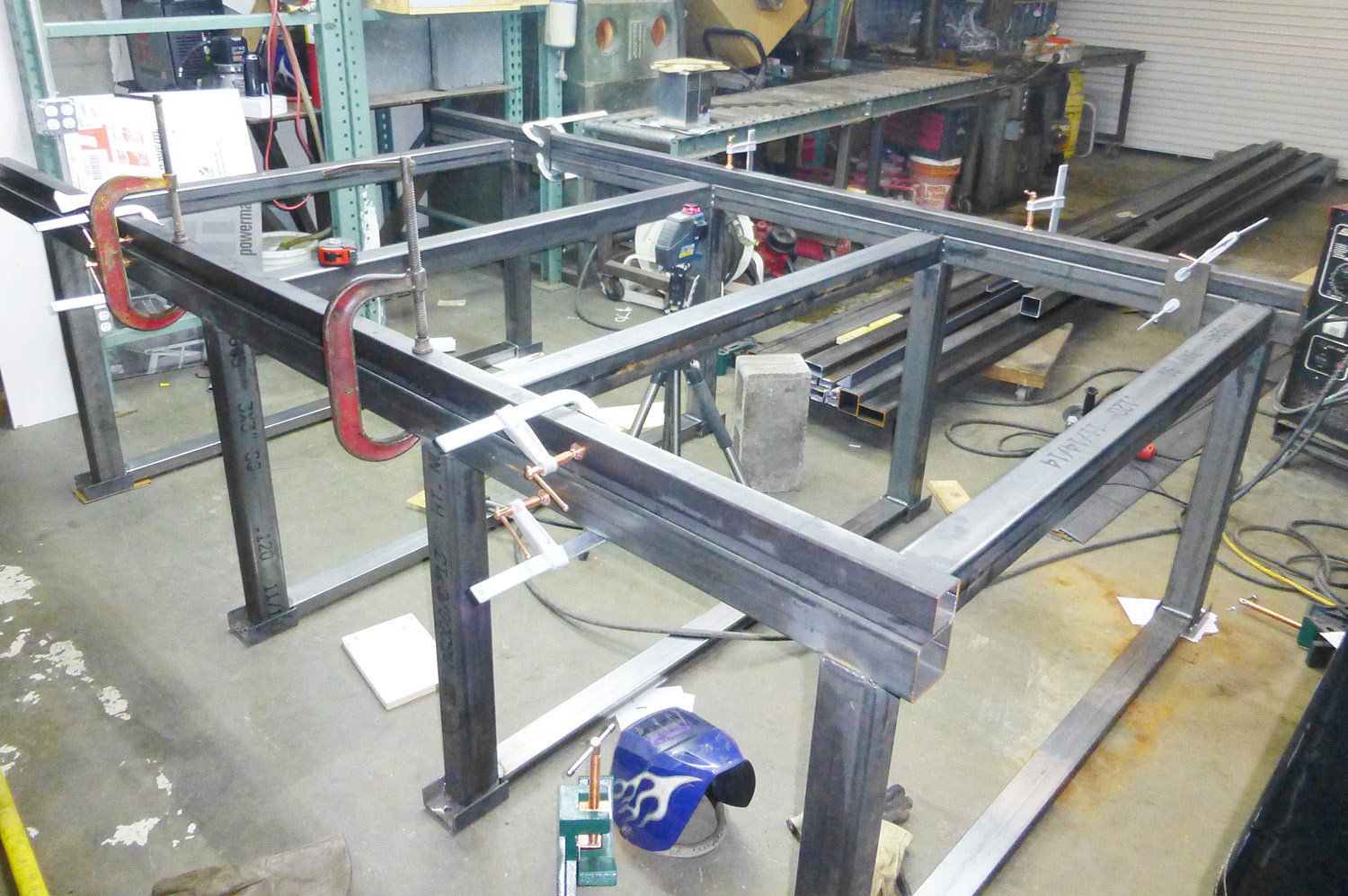
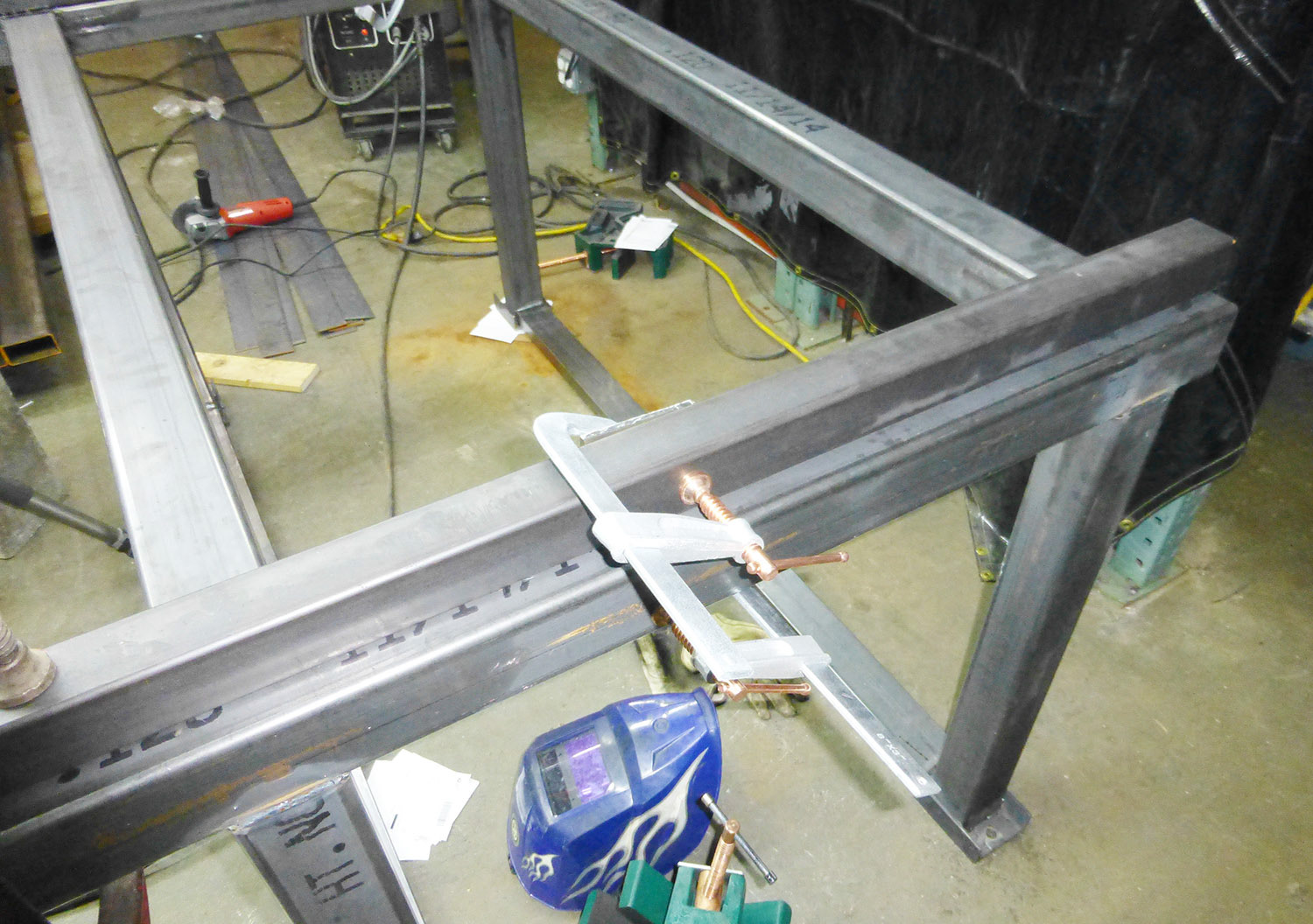
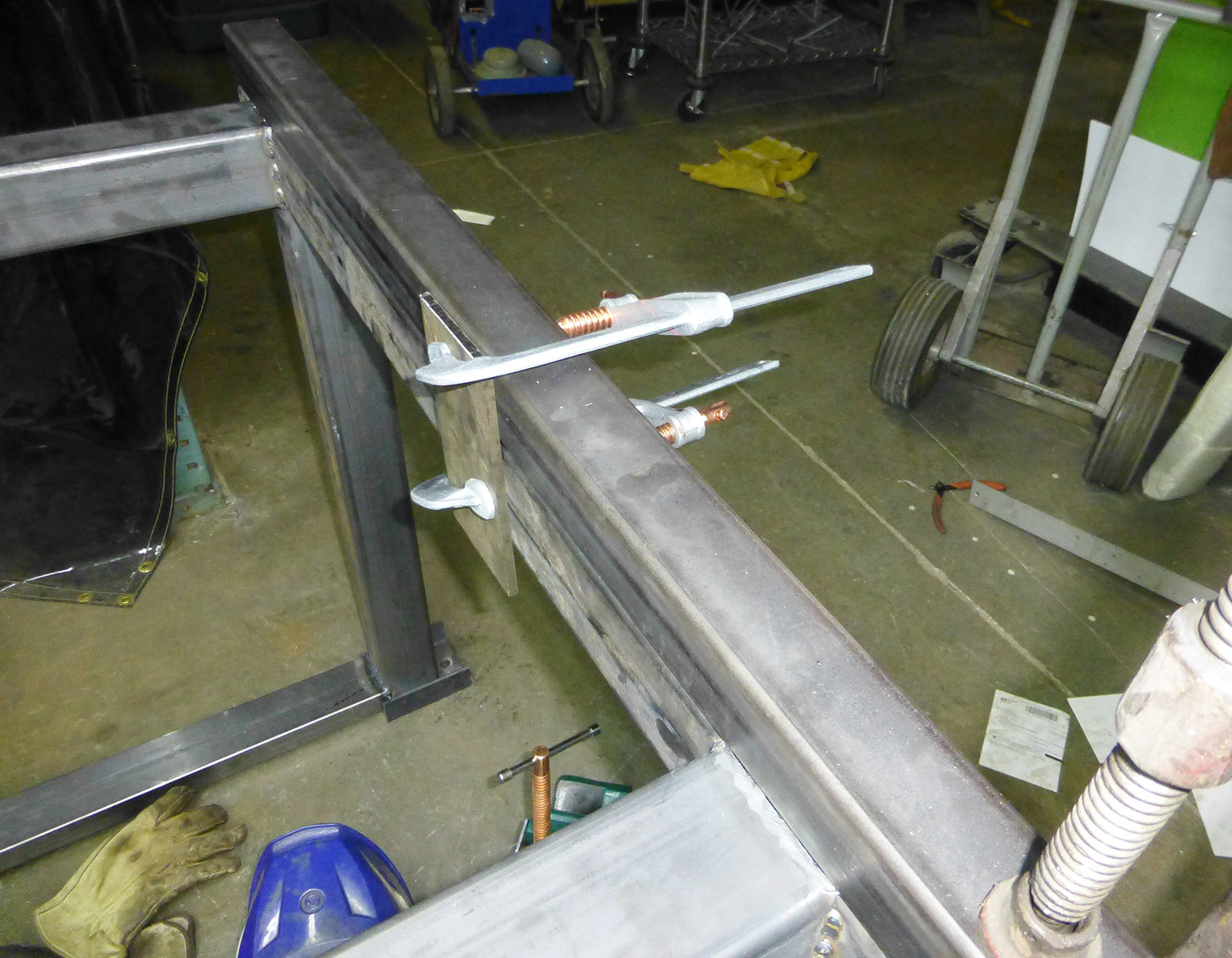
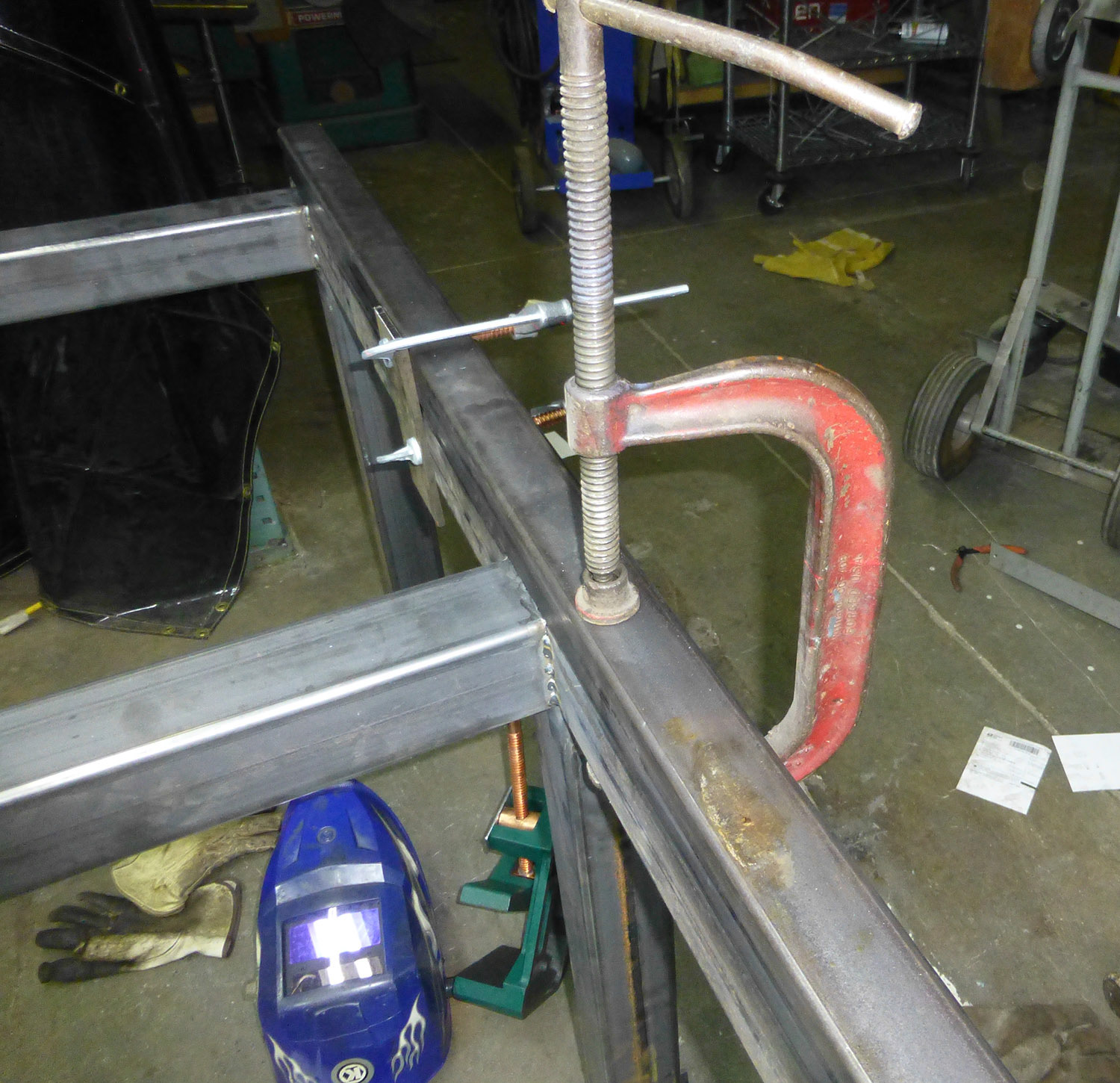
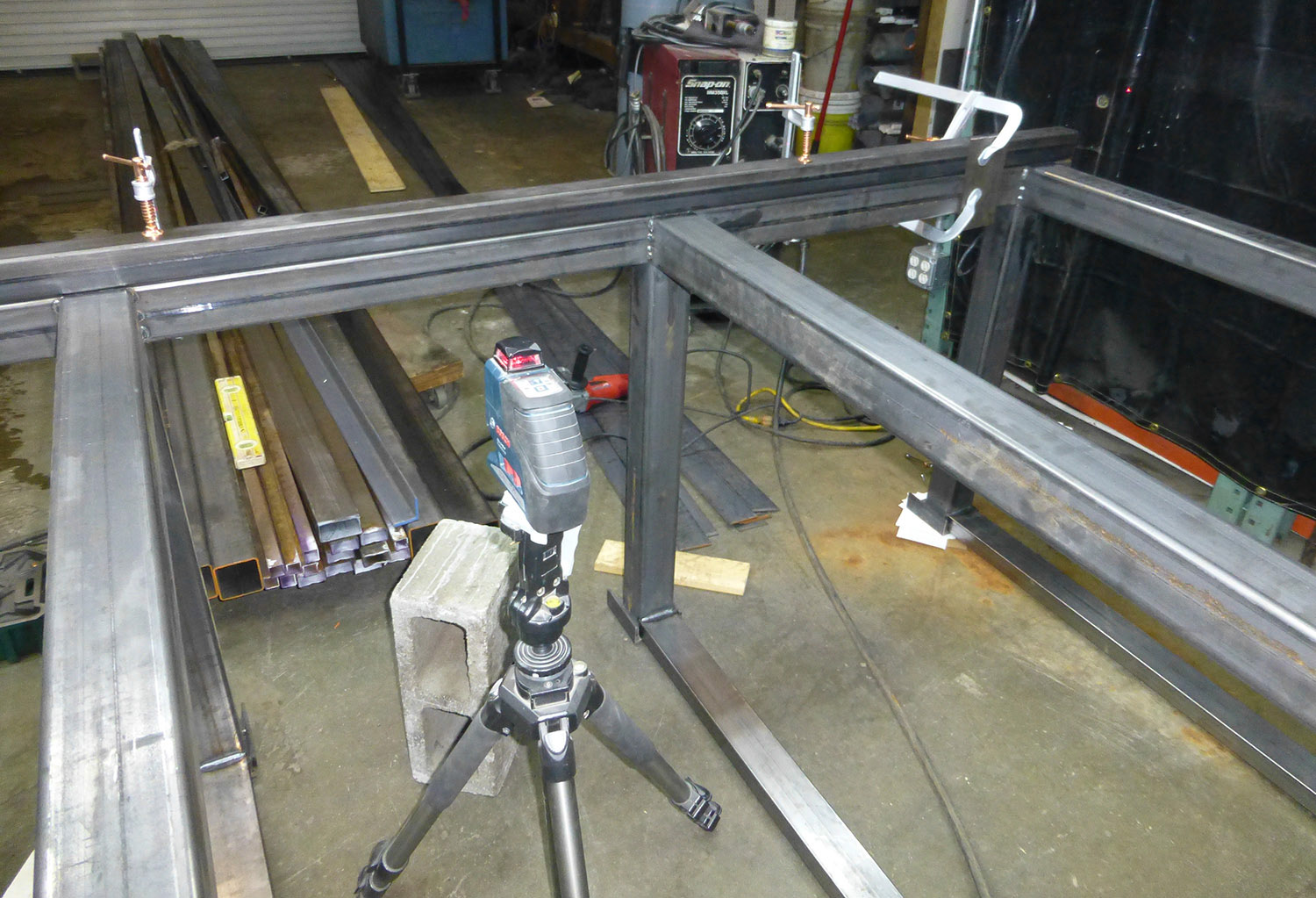
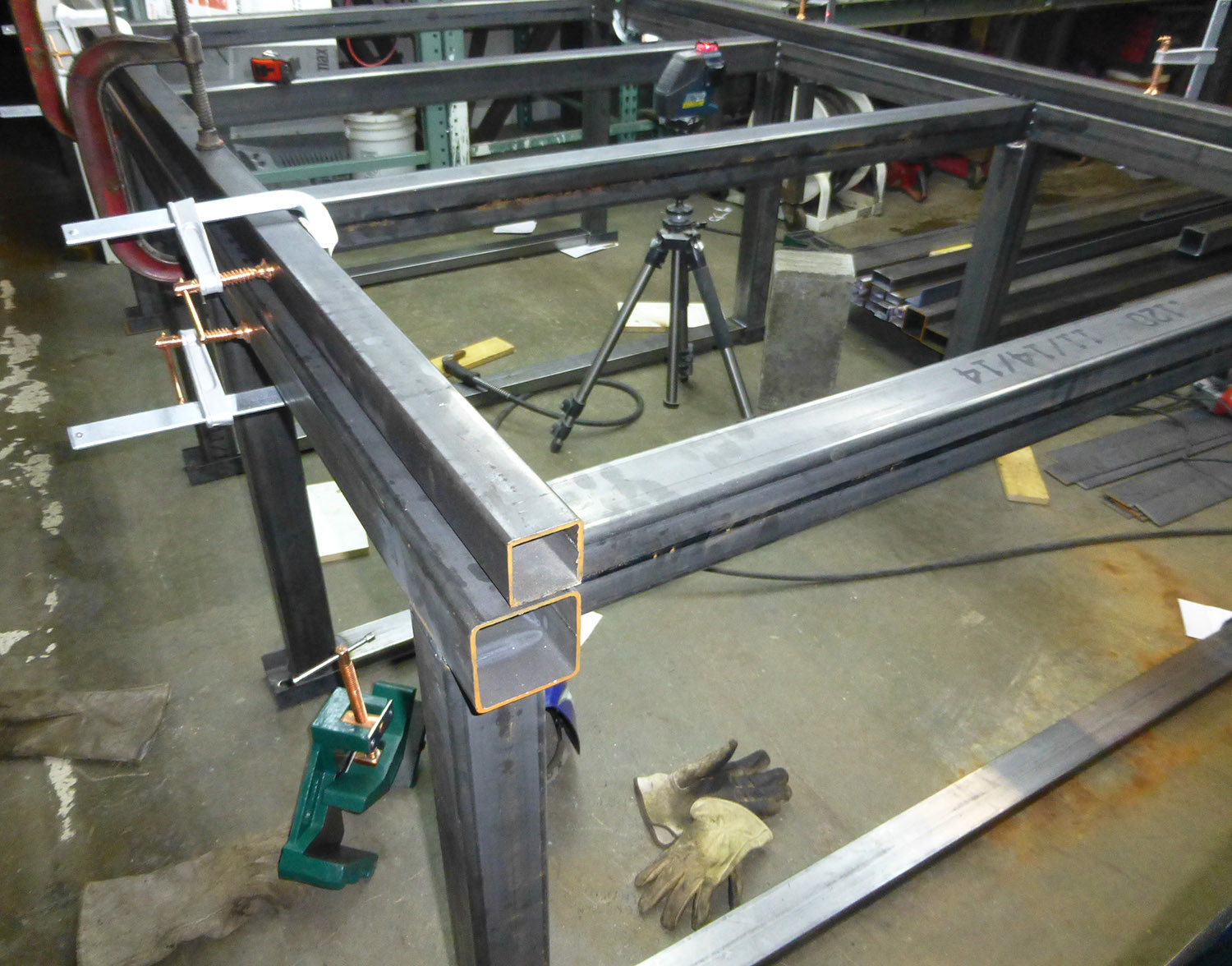
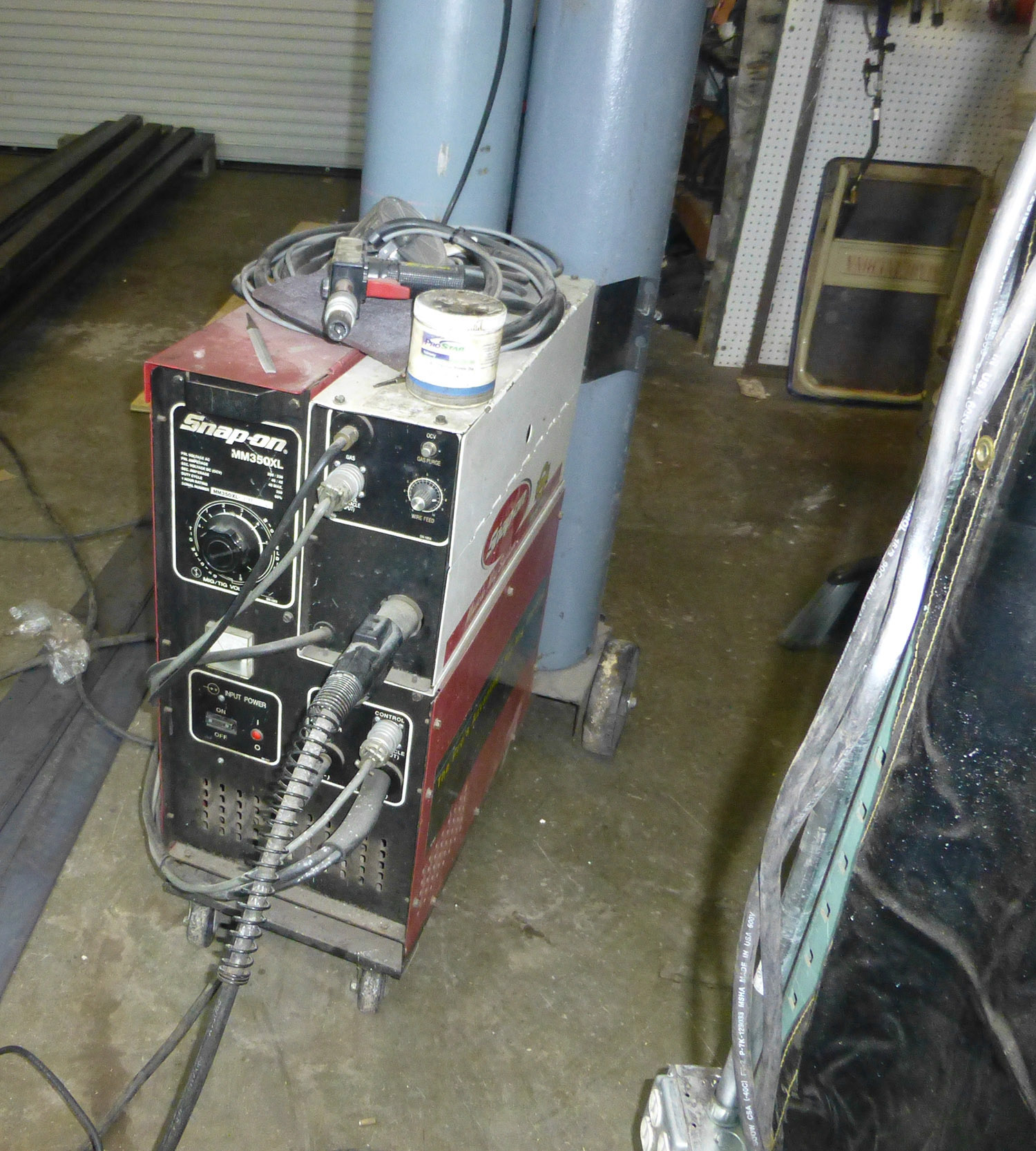
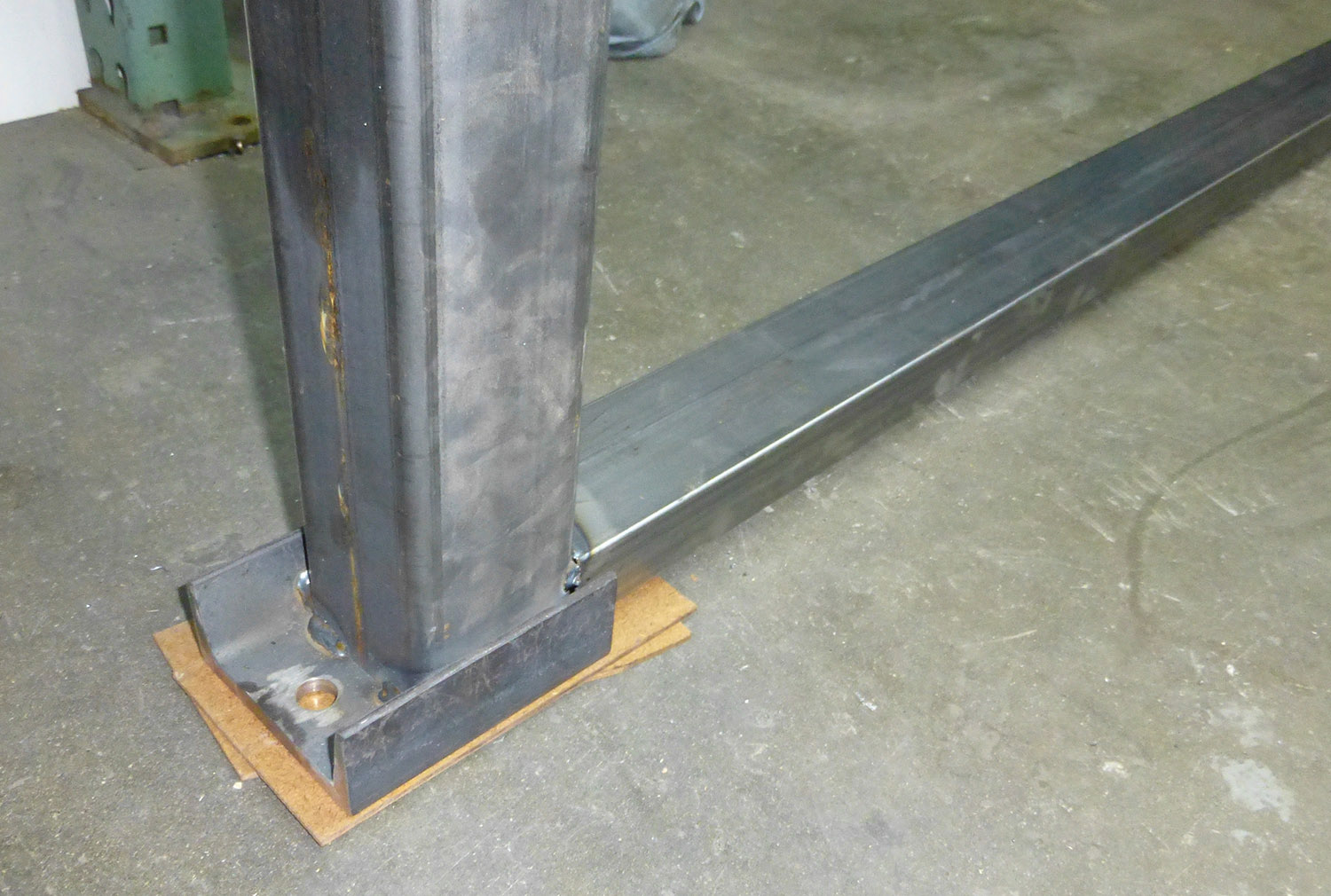
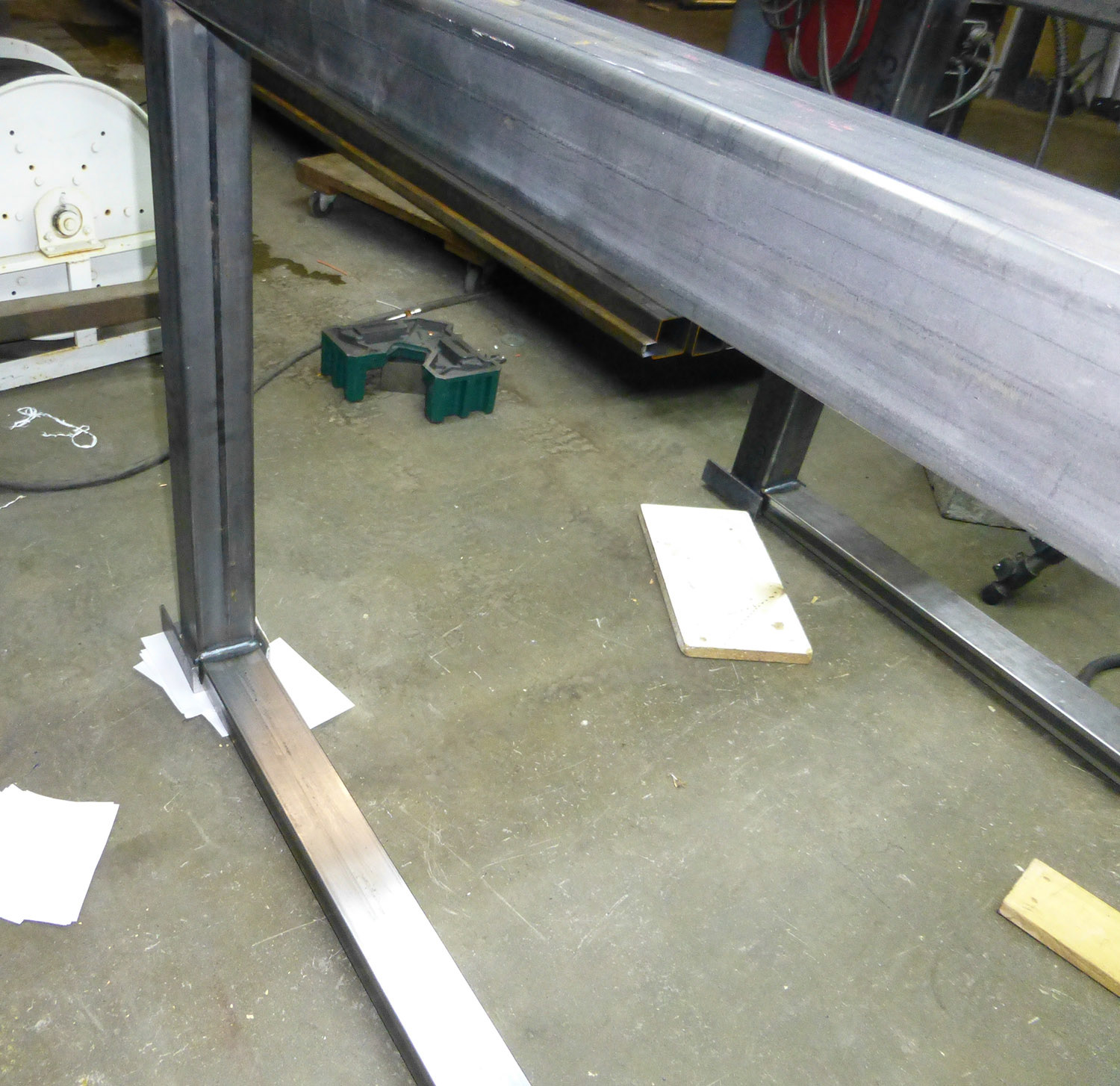
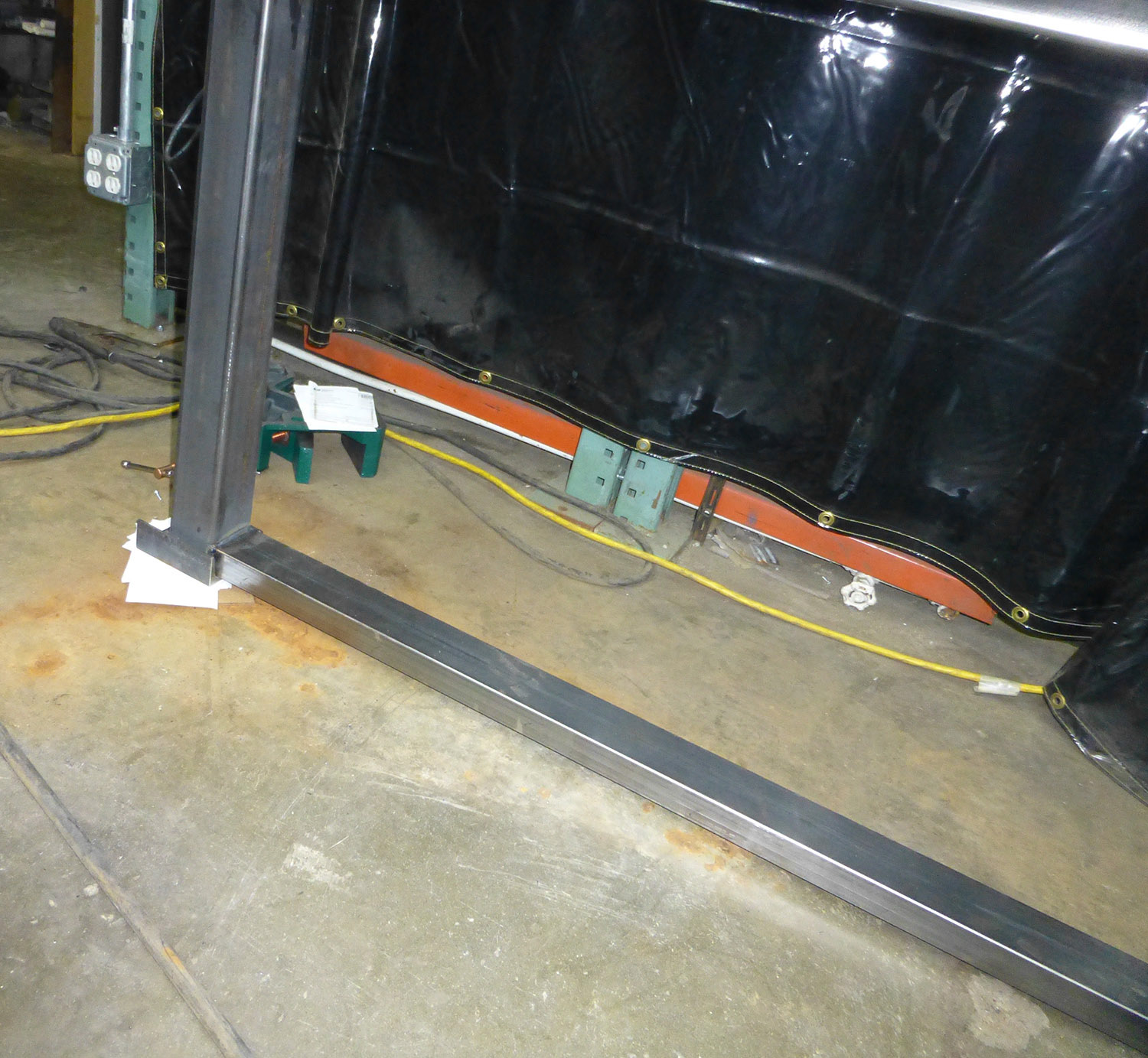
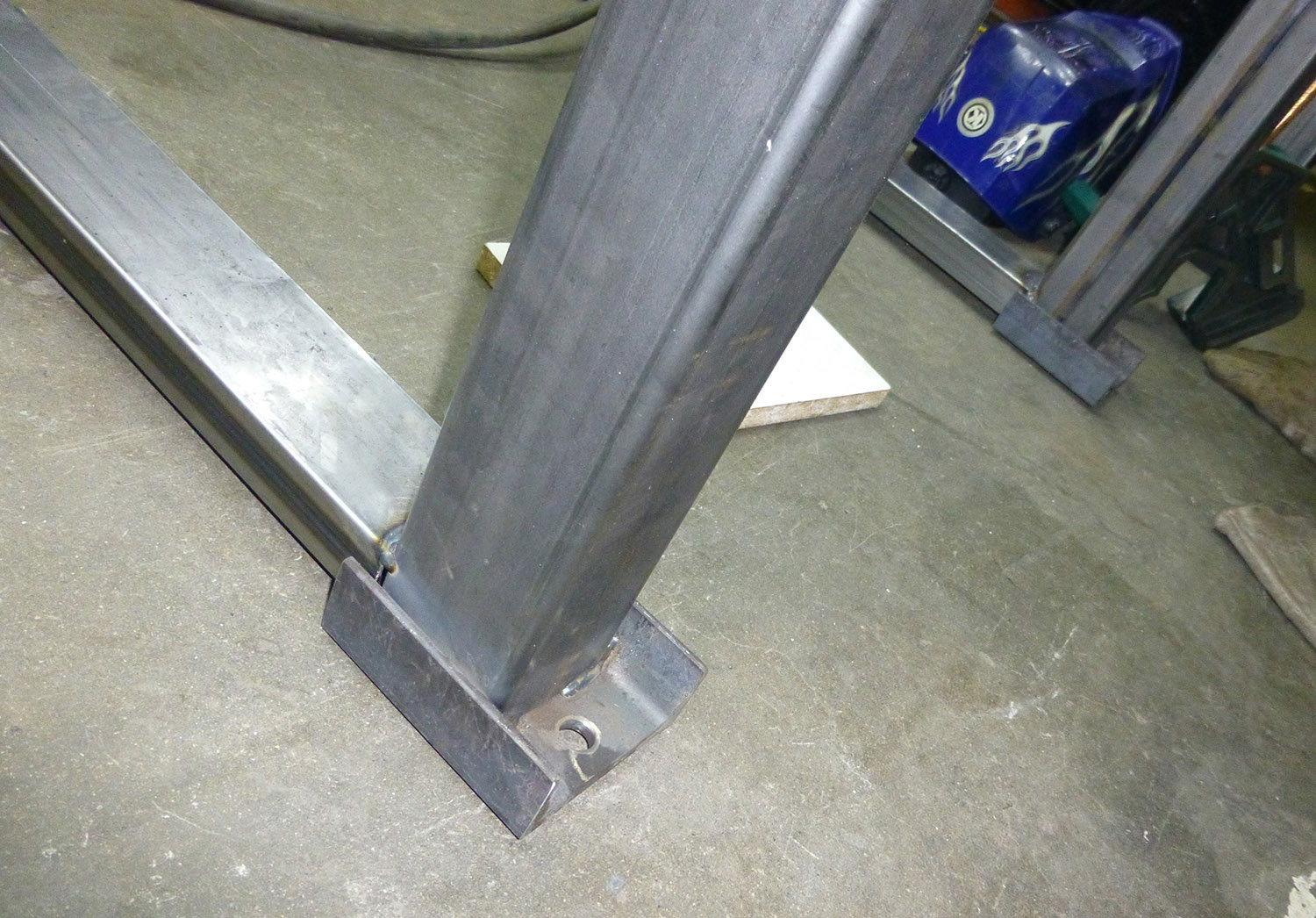
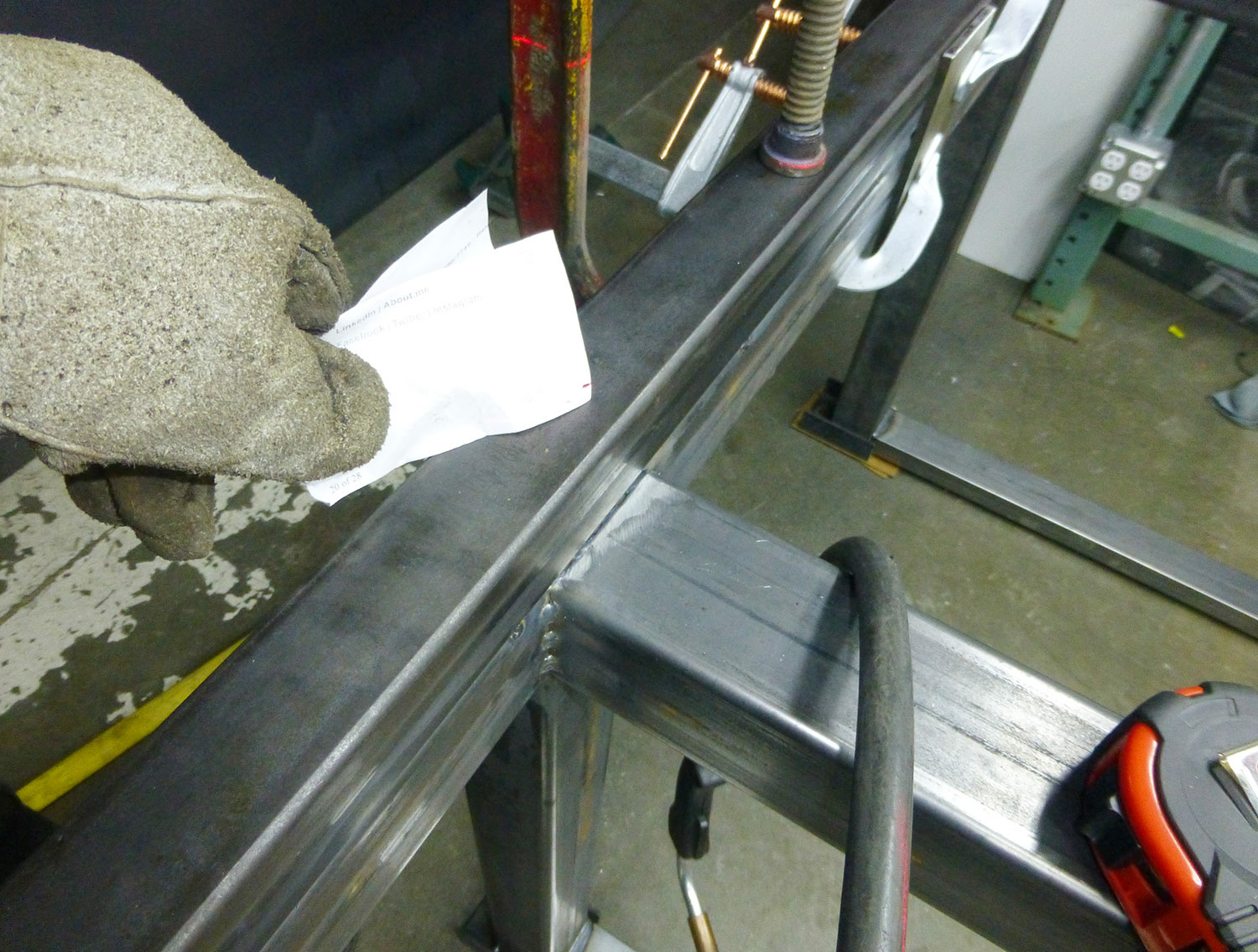
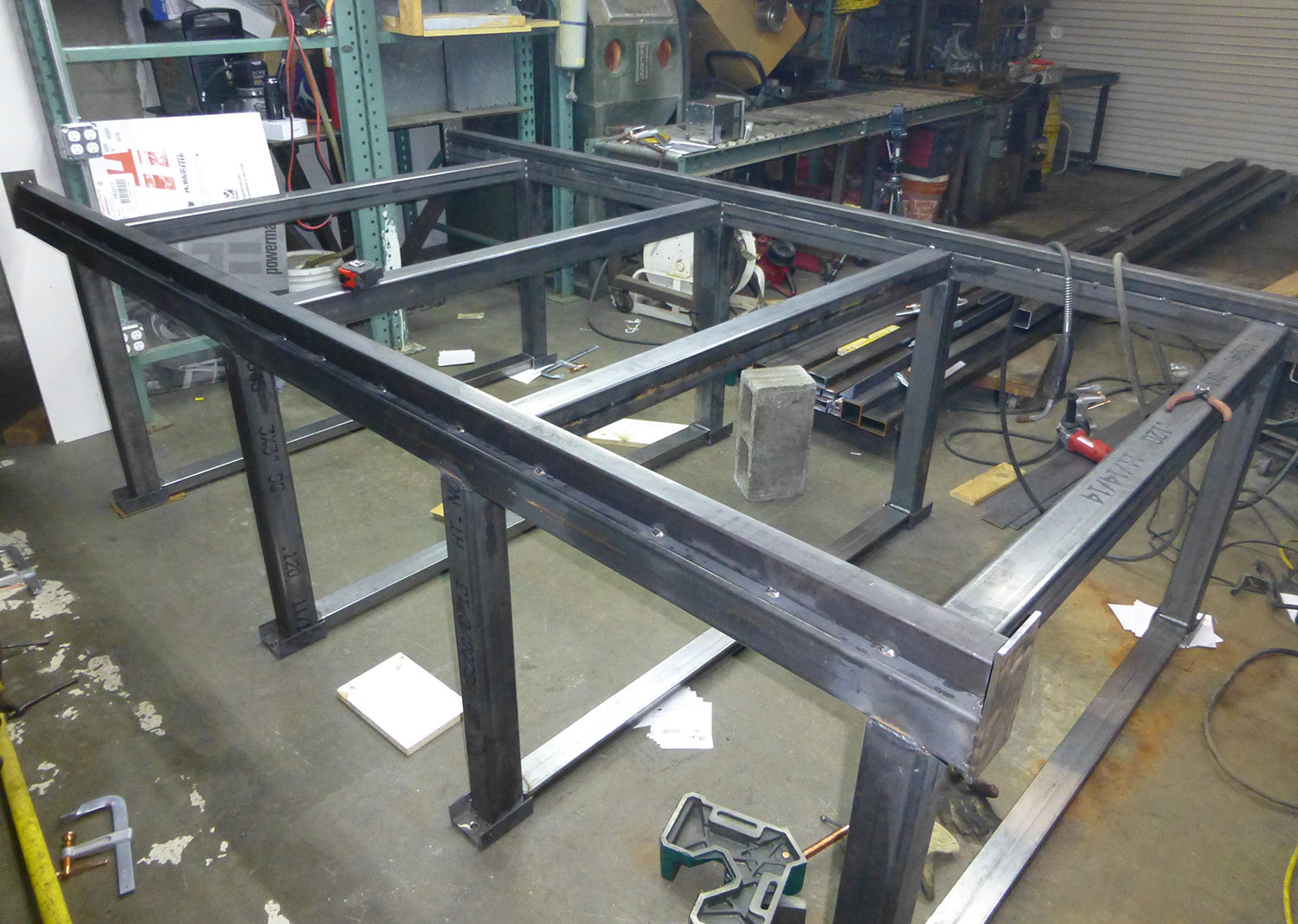
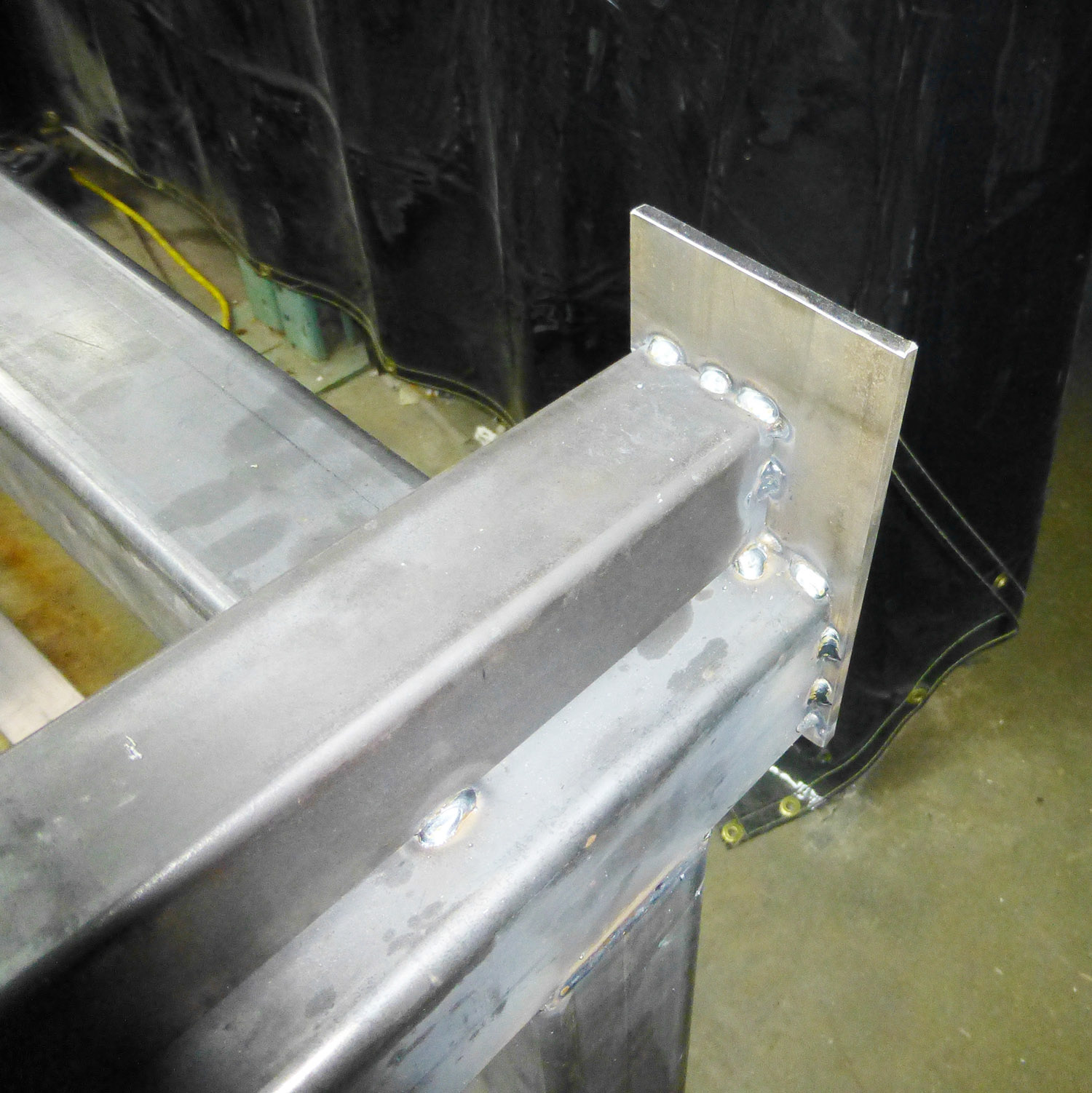

After too many years of cutting things out with a grinder and a handheld plasma cutter, it was time to bite the bullet and build of 4’ x 8’ plasma table.
I ordered a gantry kit, and designed the table in SolidWorks. I ordered an extra wide gantry so that the cutting head could extend beyond the table so I could add a rotary axis for cutting tubing. With the gantry on order, I started on the table. I shimmed the floor to get everything level, and used a laser to dial all the dimensions in.
I ordered a gantry kit, and designed the table in SolidWorks. I ordered an extra wide gantry so that the cutting head could extend beyond the table so I could add a rotary axis for cutting tubing. With the gantry on order, I started on the table. I shimmed the floor to get everything level, and used a laser to dial all the dimensions in.
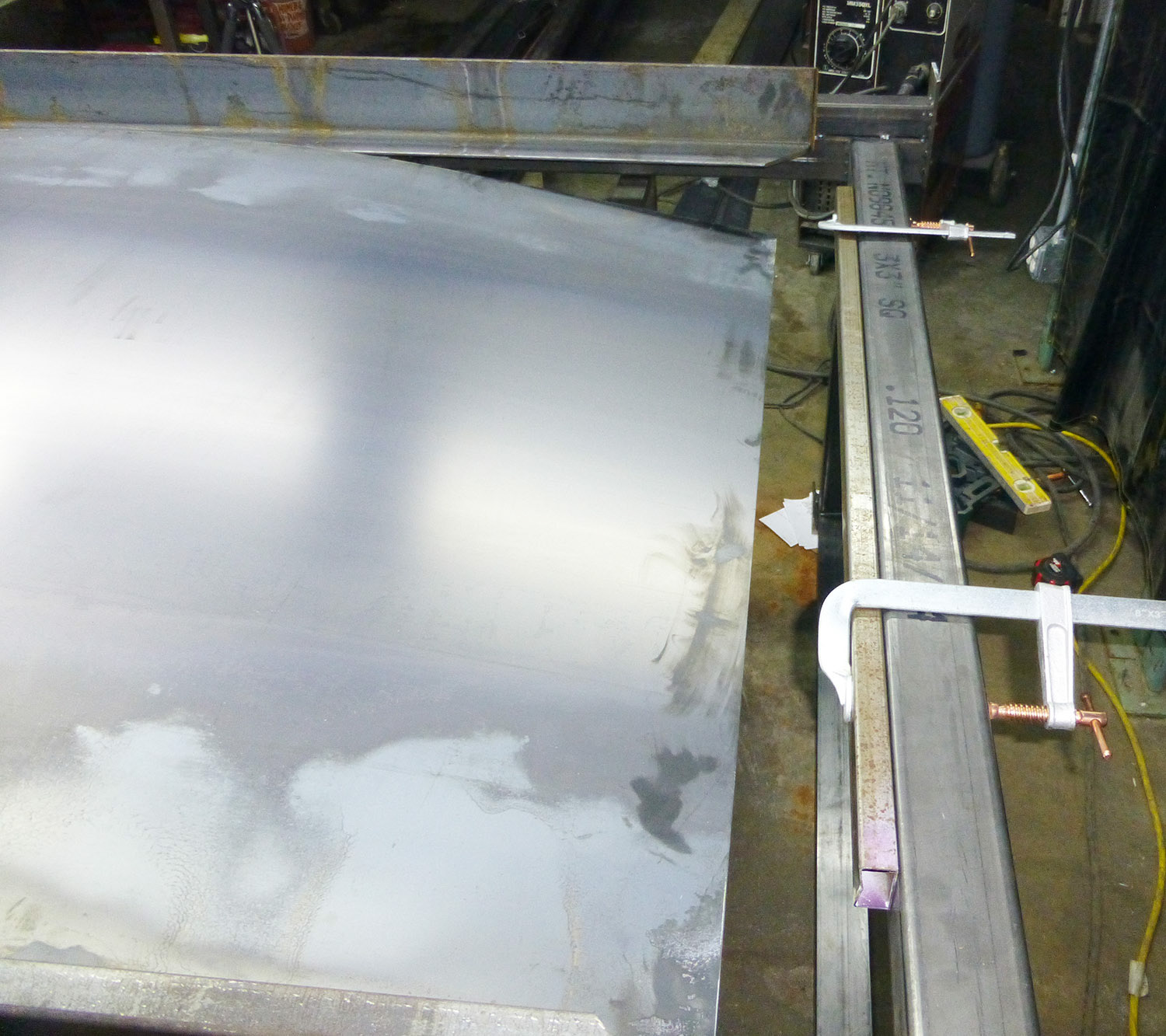
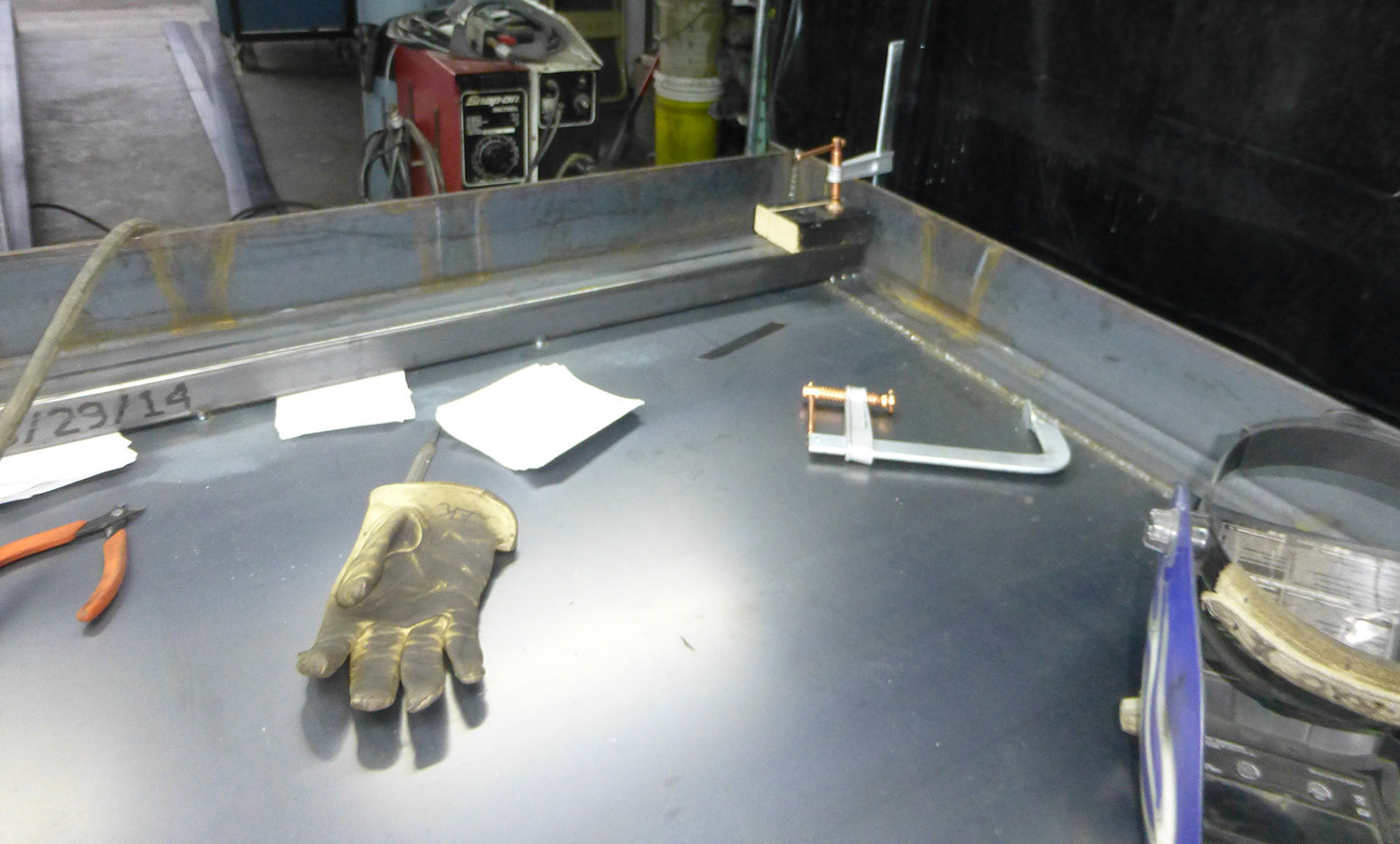
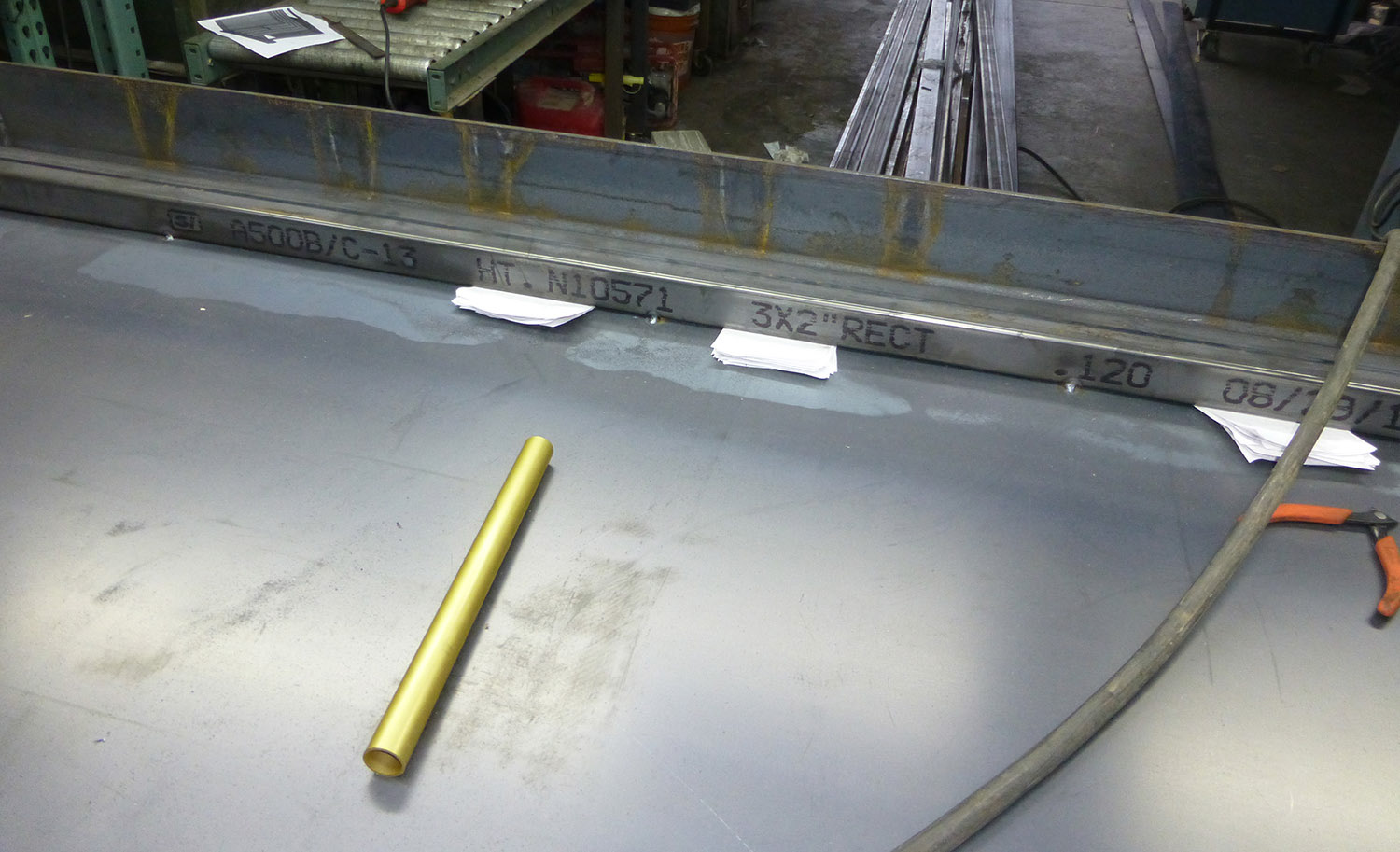
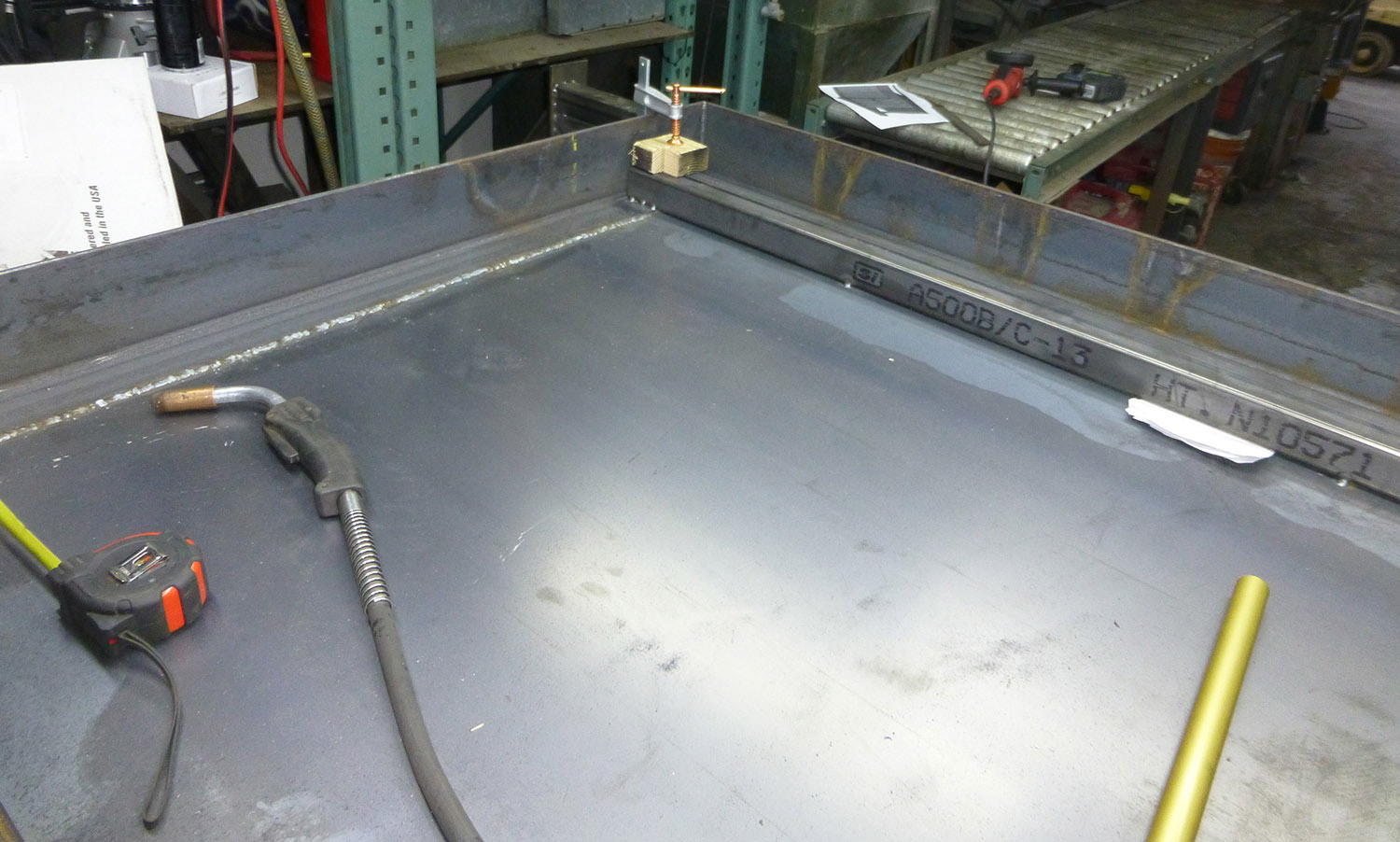
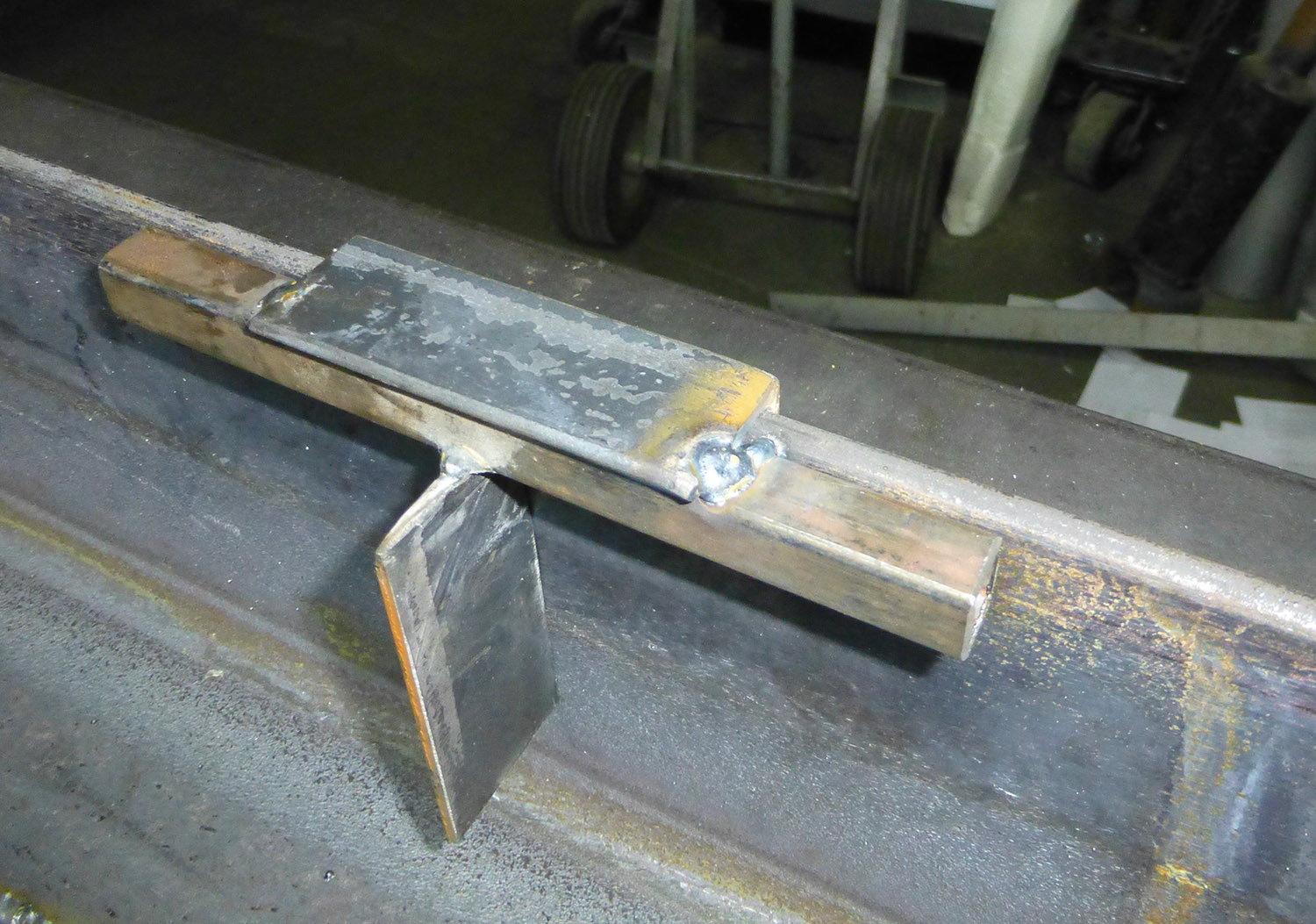
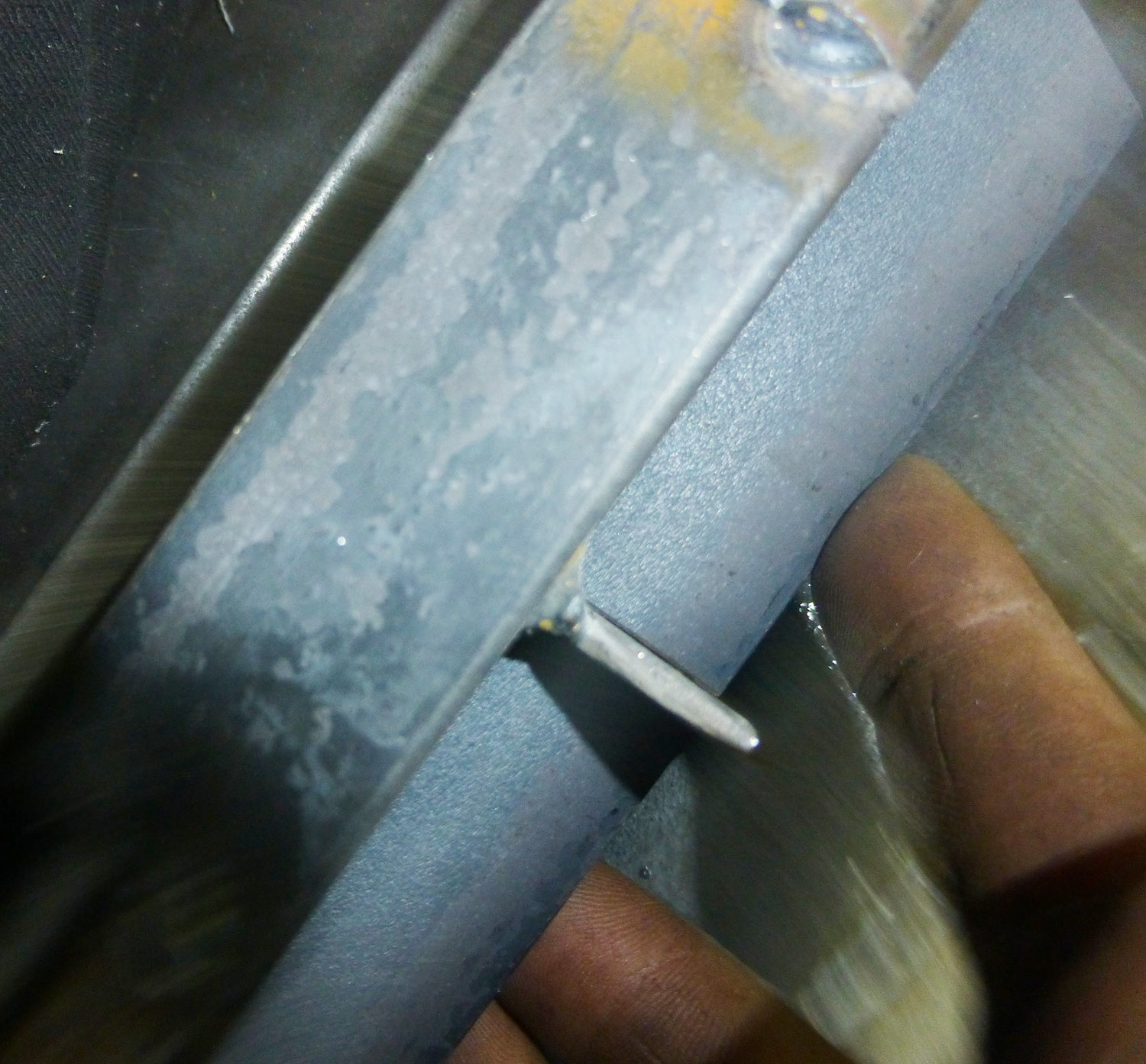
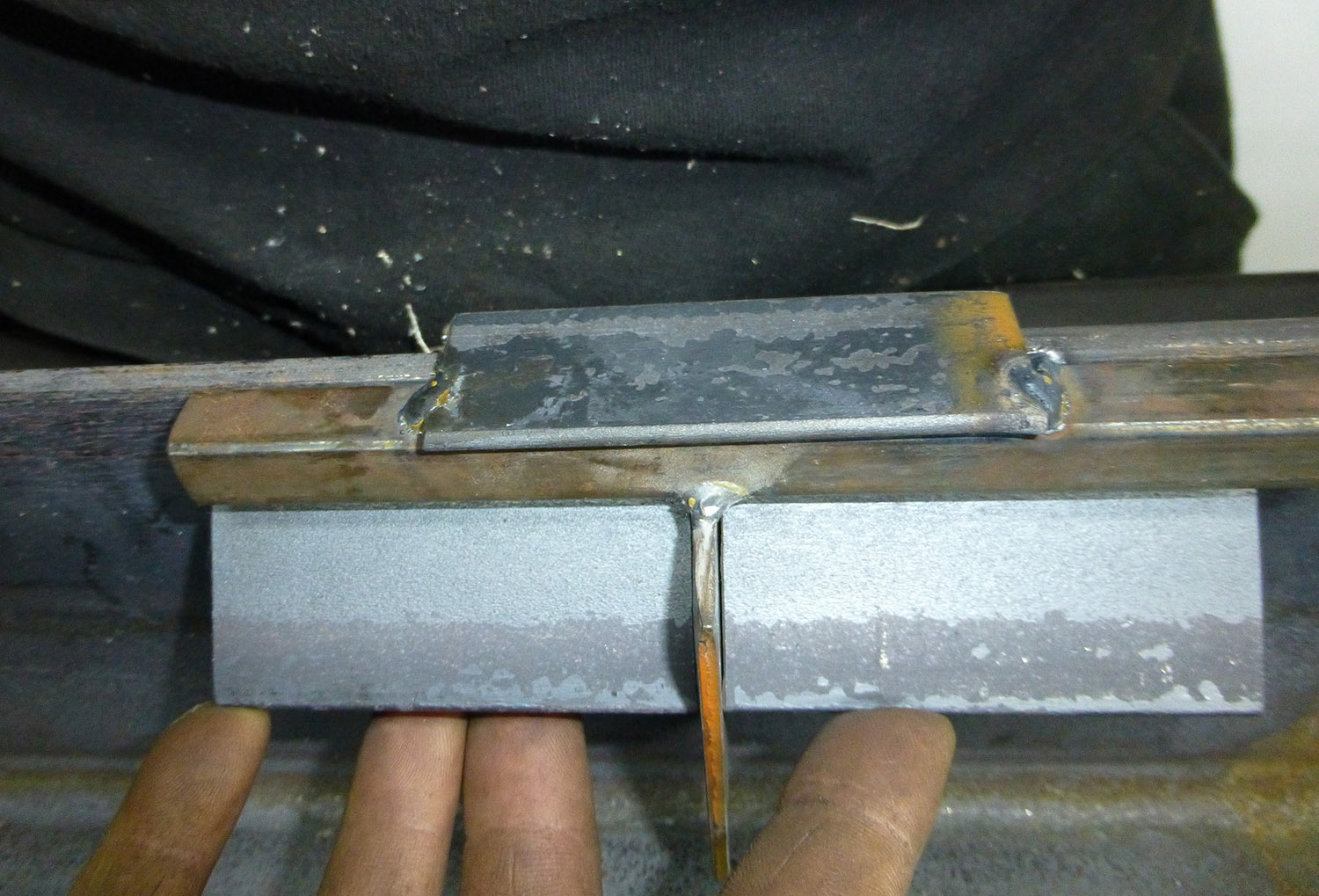
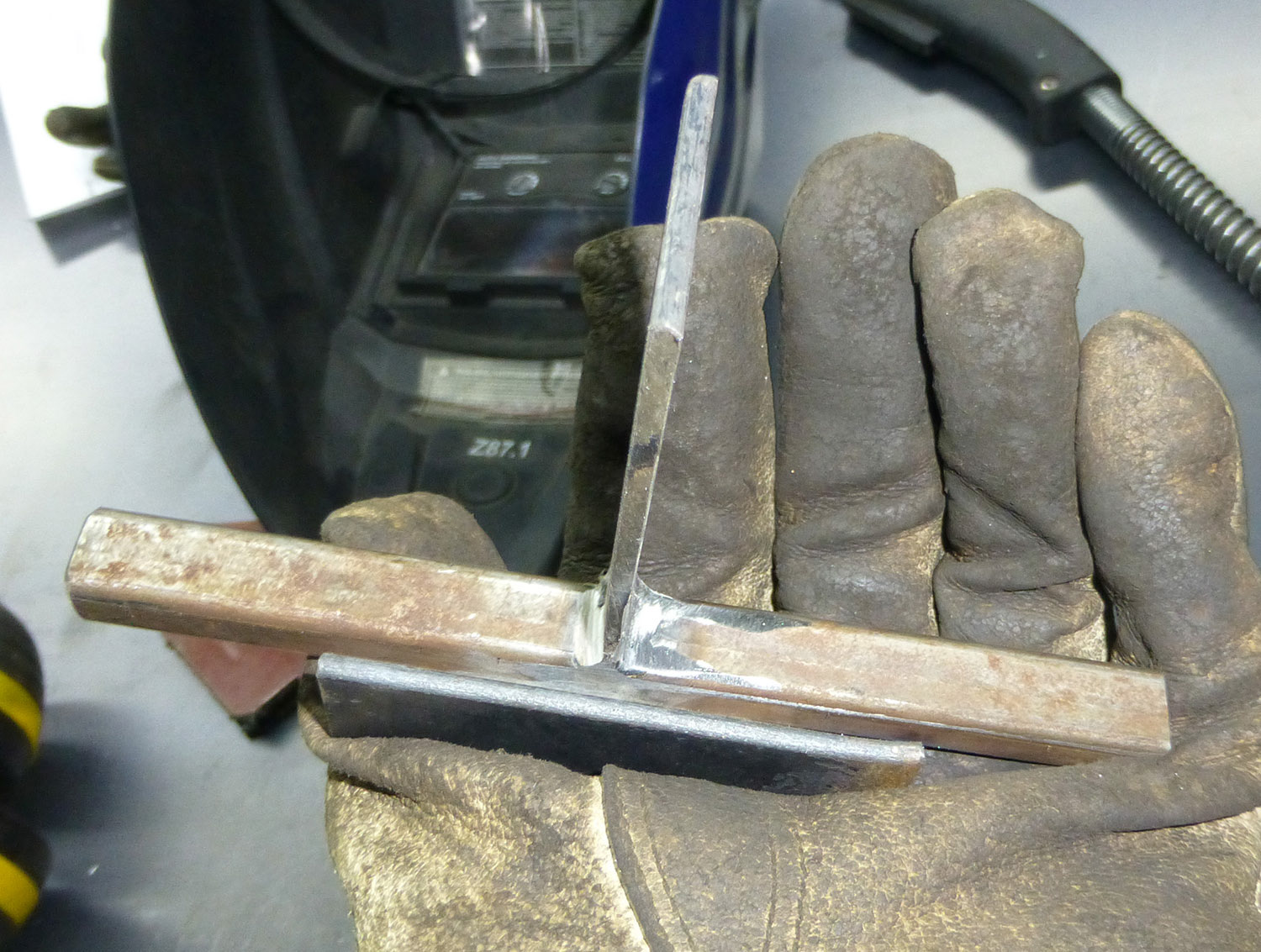
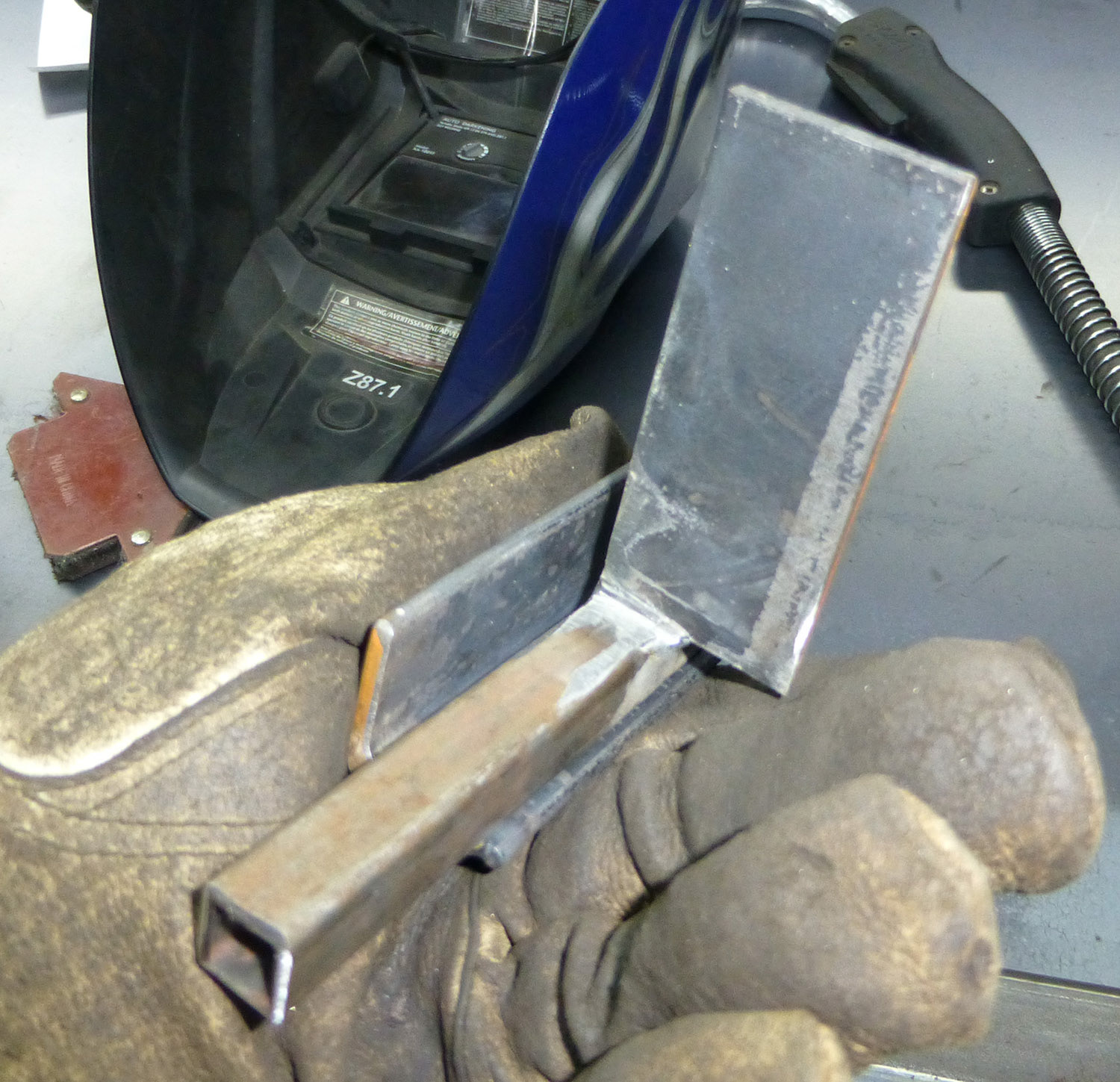
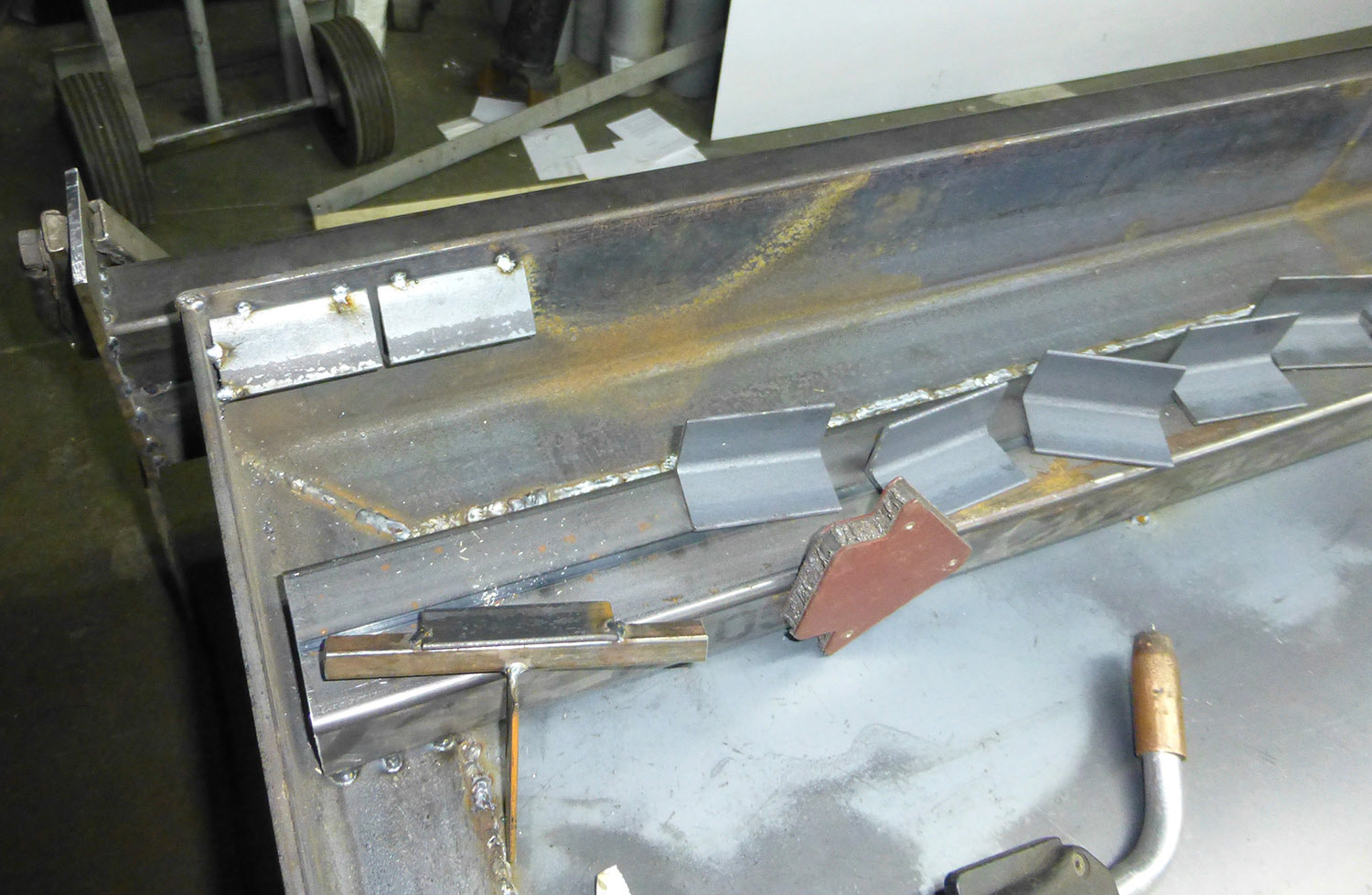
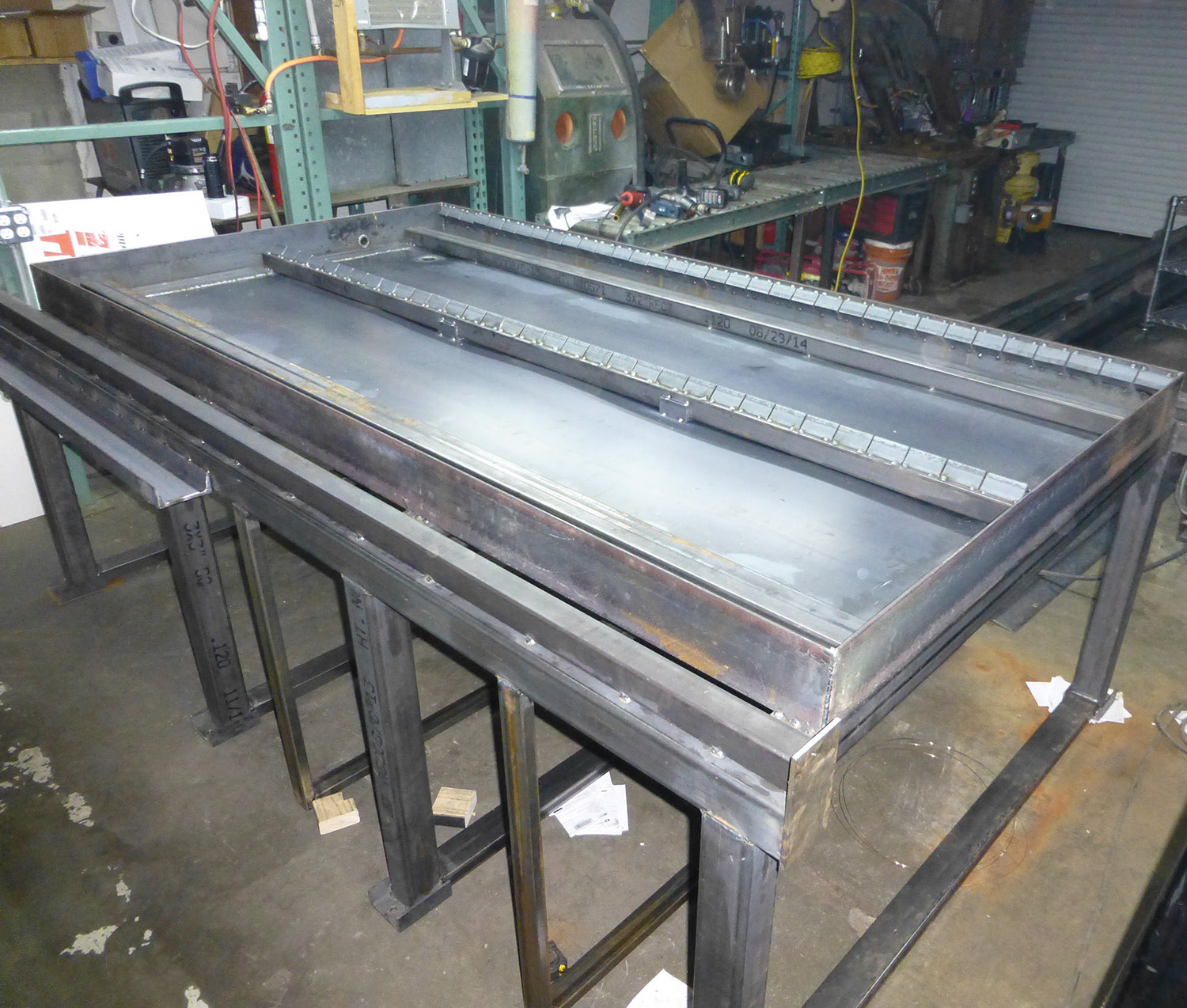
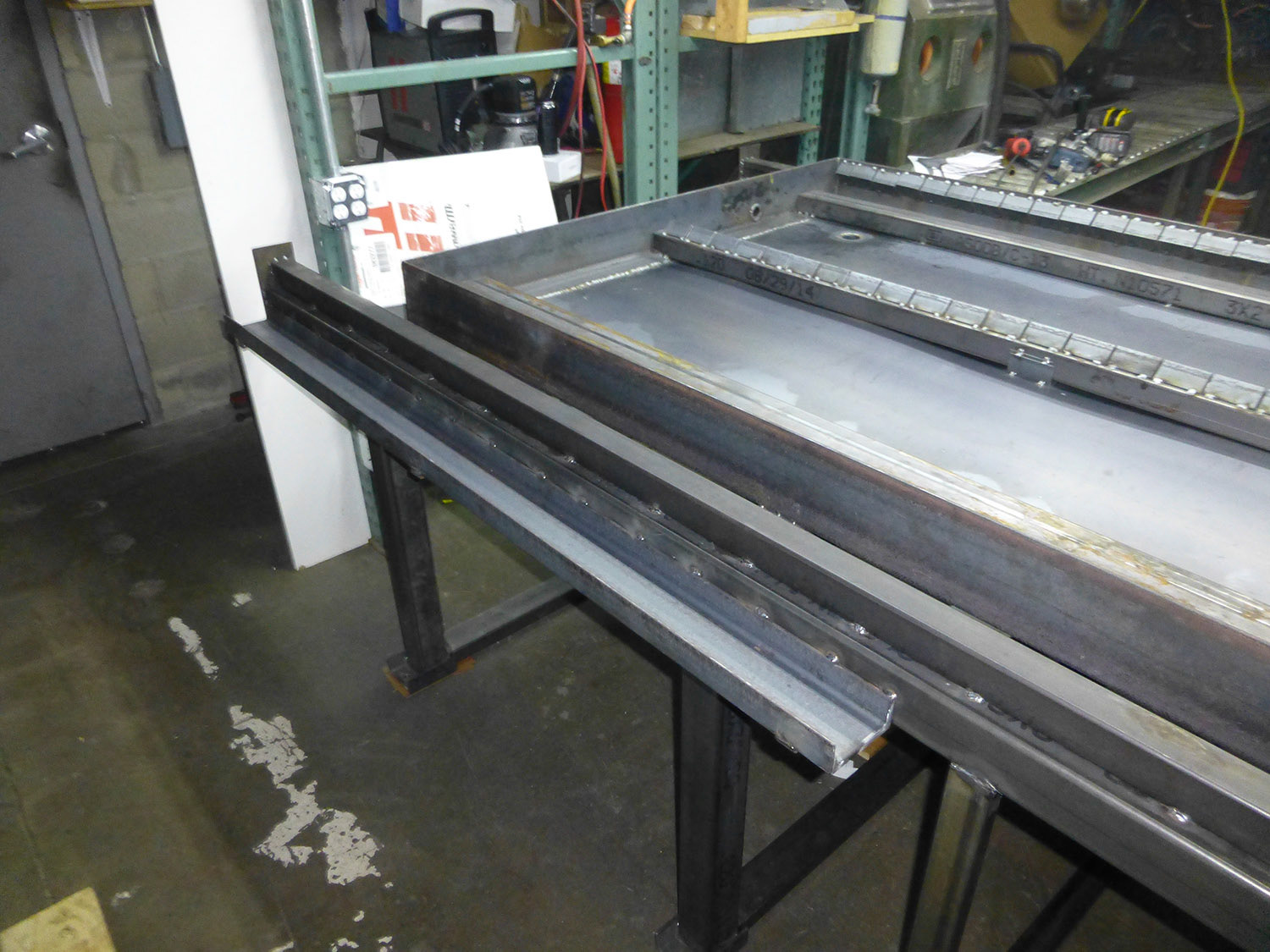
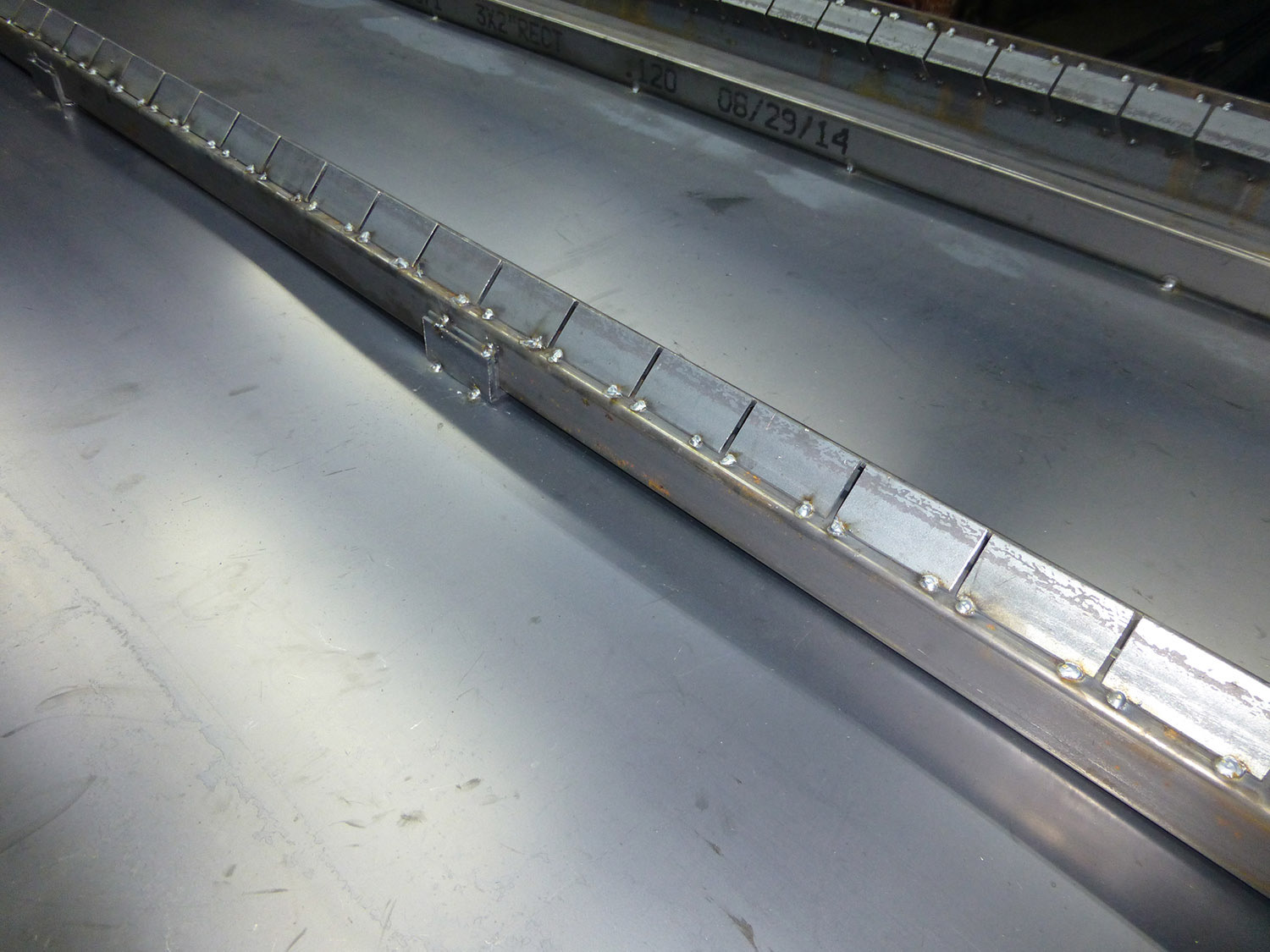
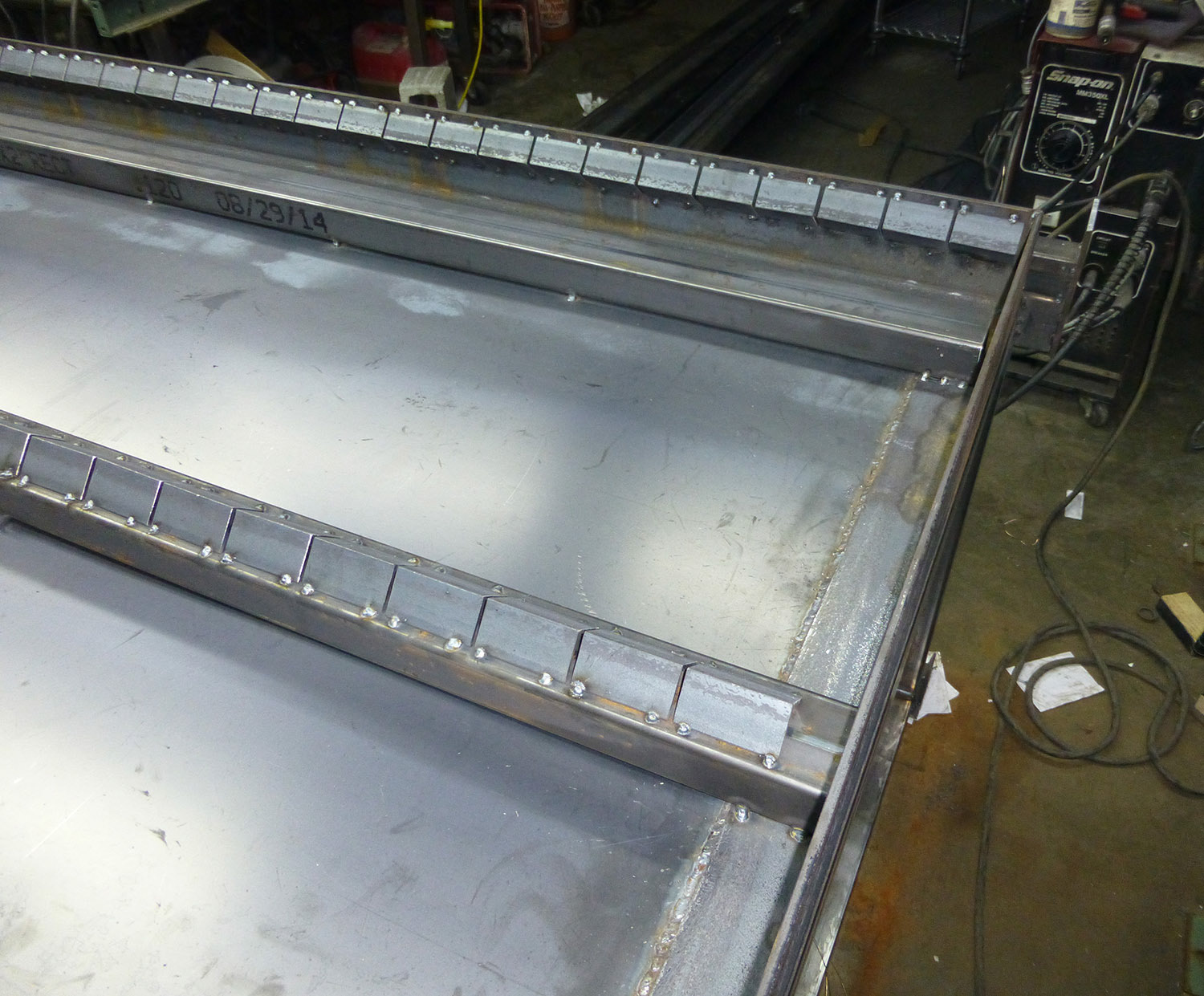
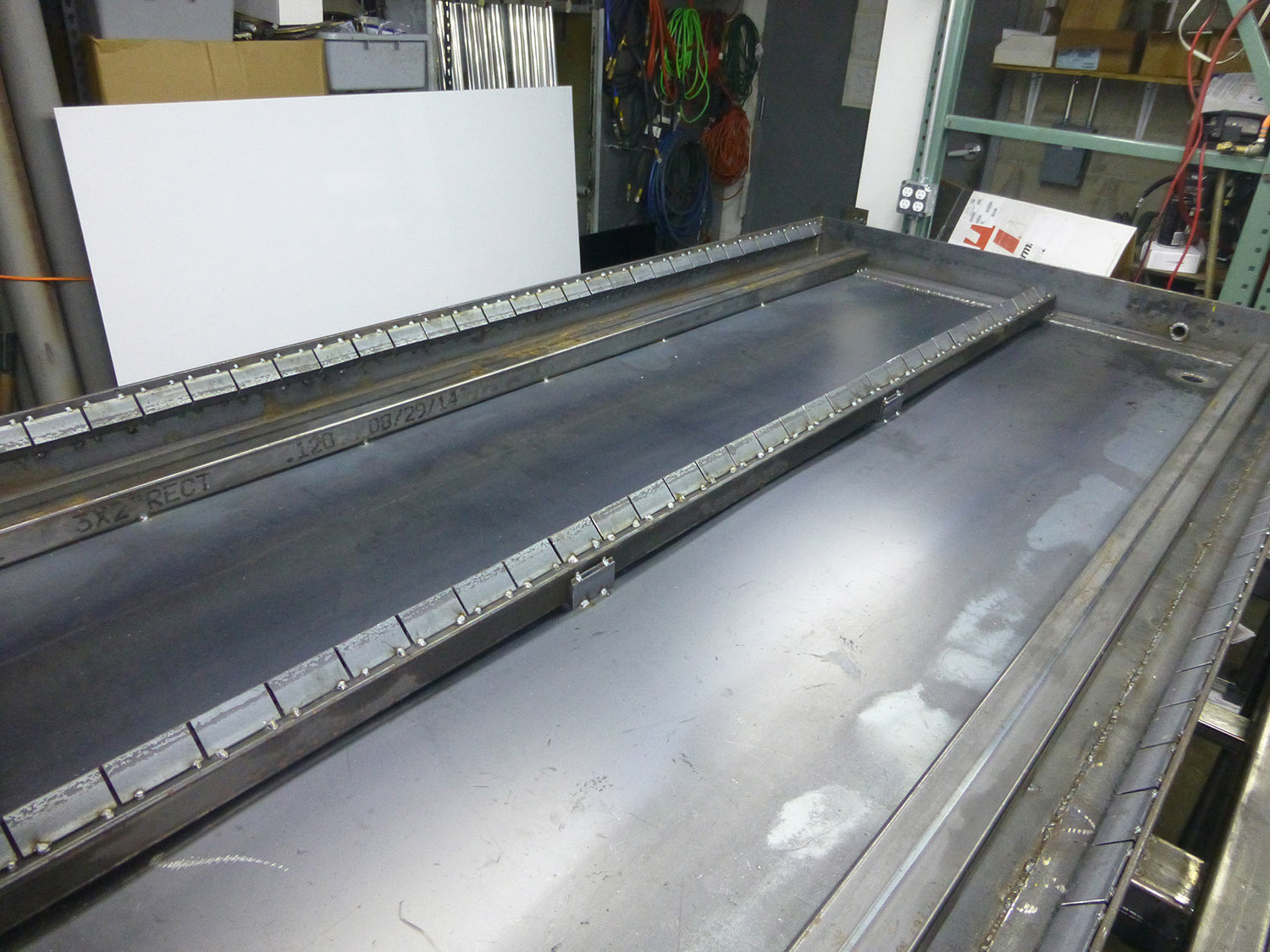
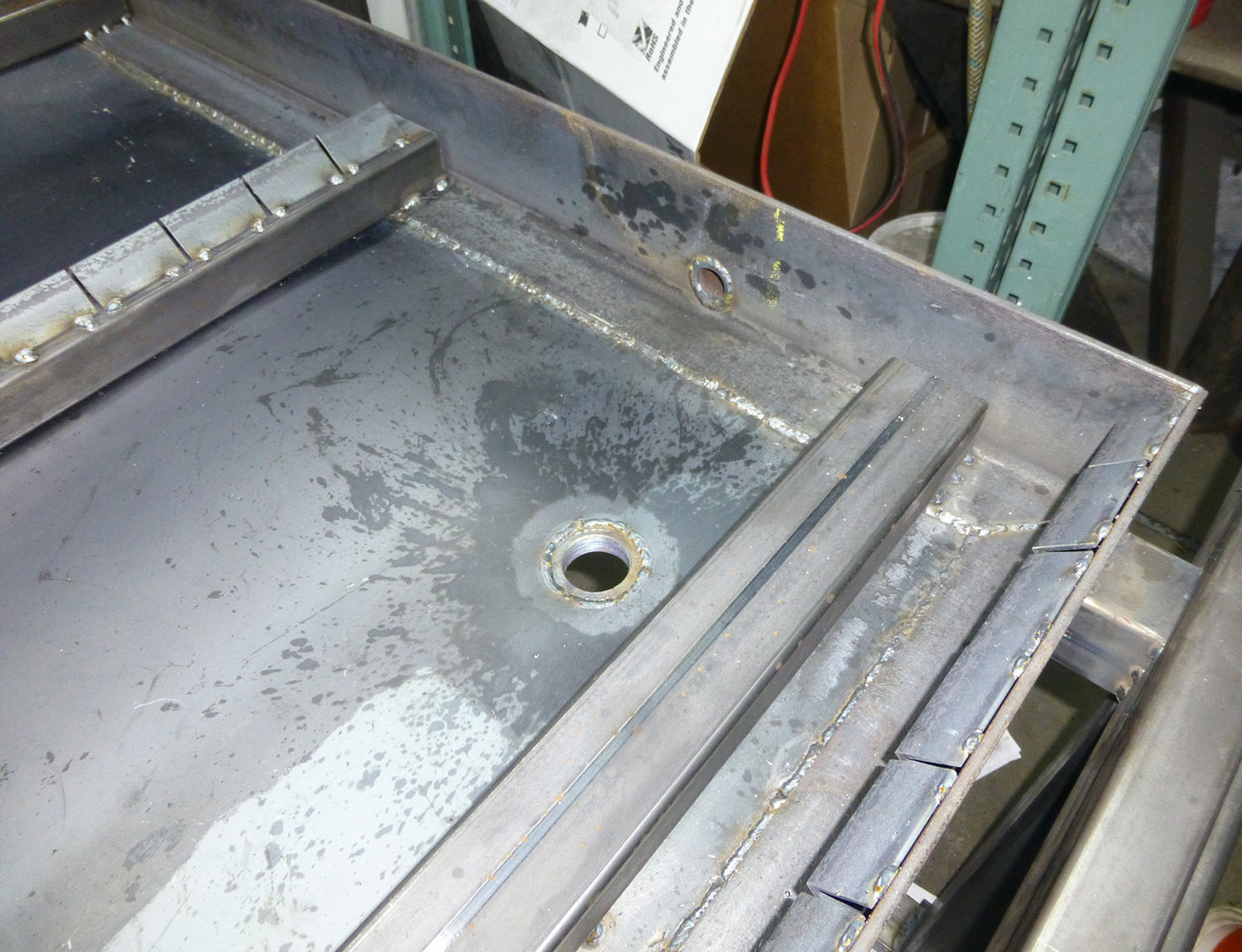
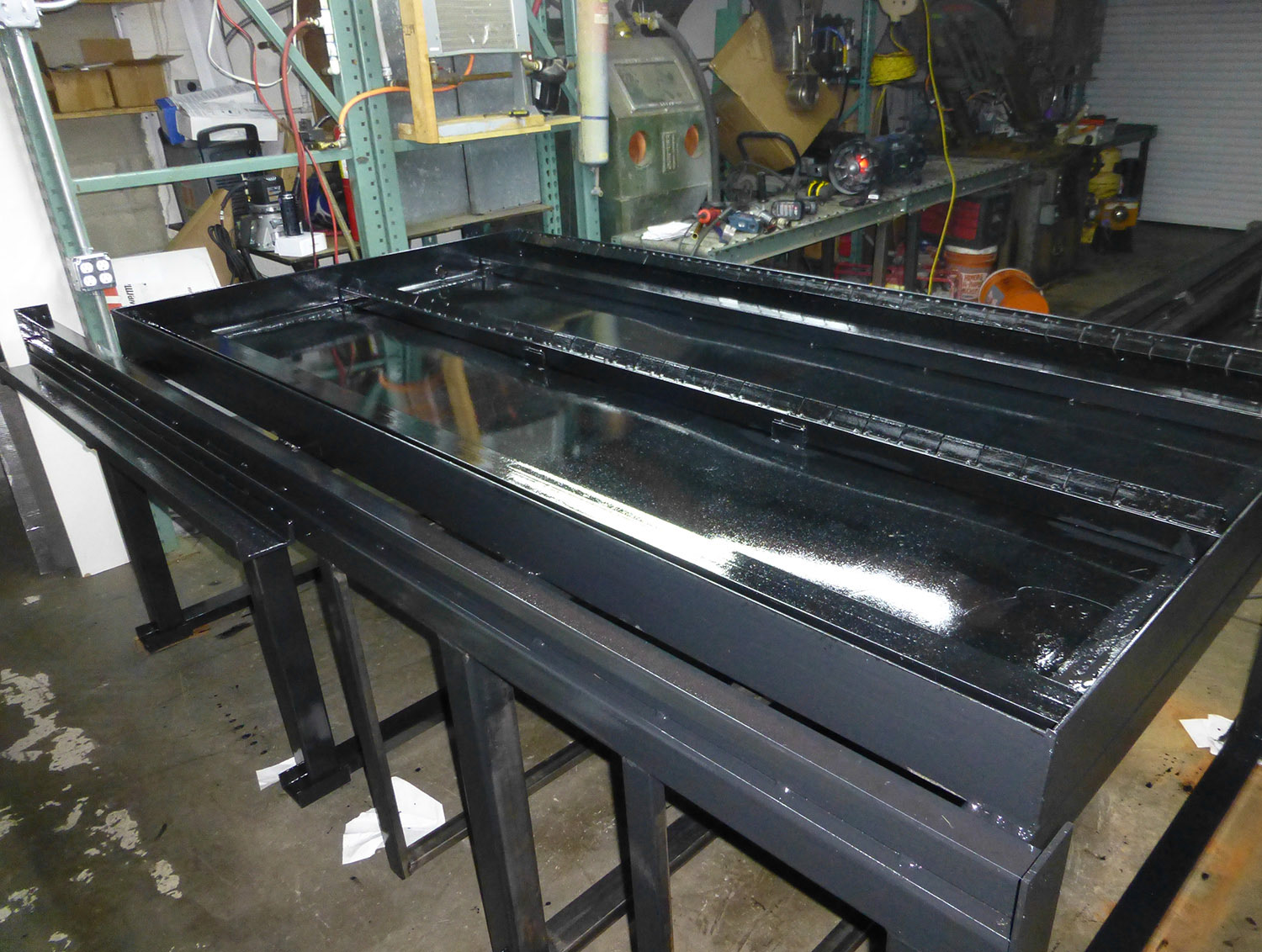
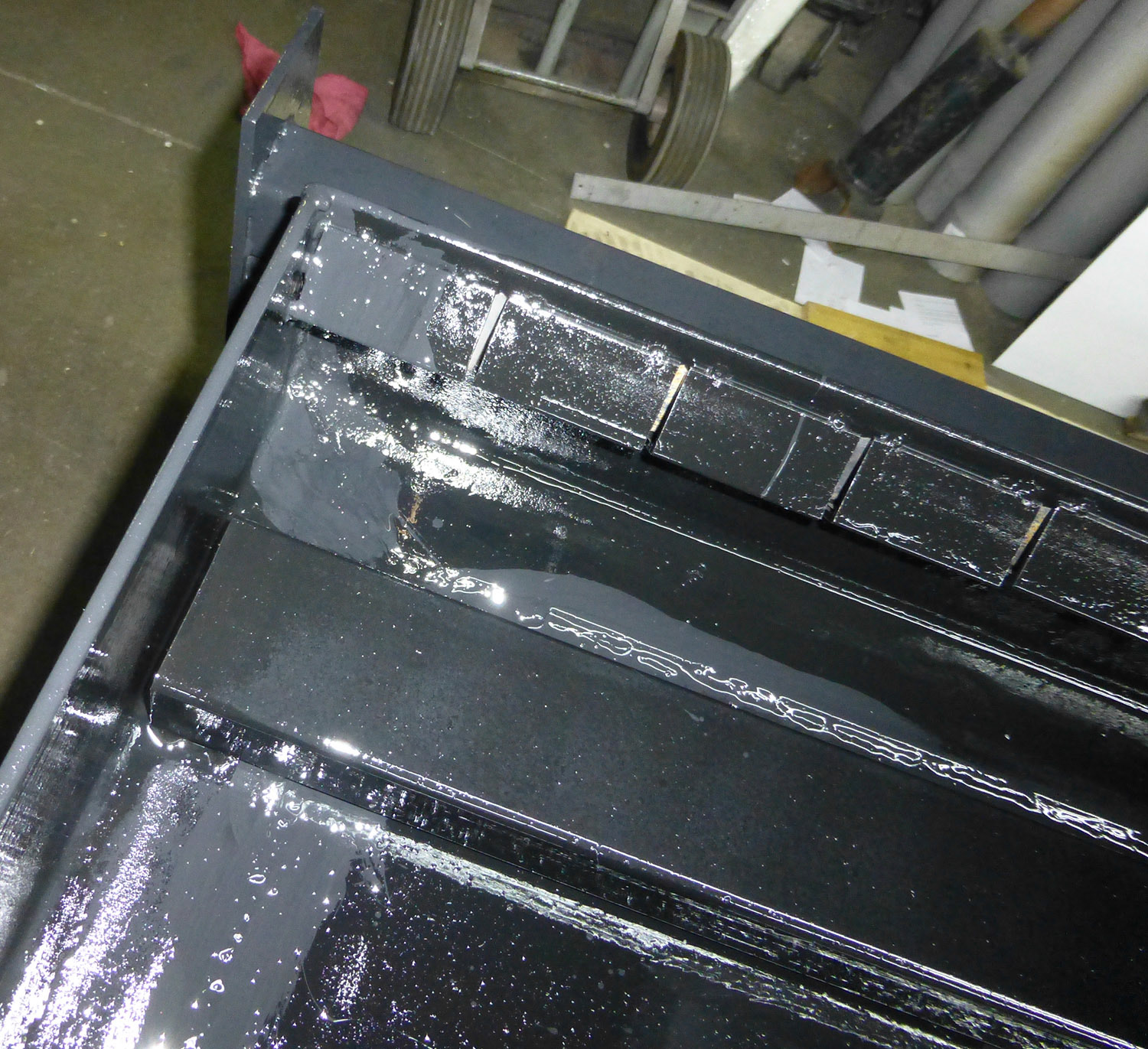
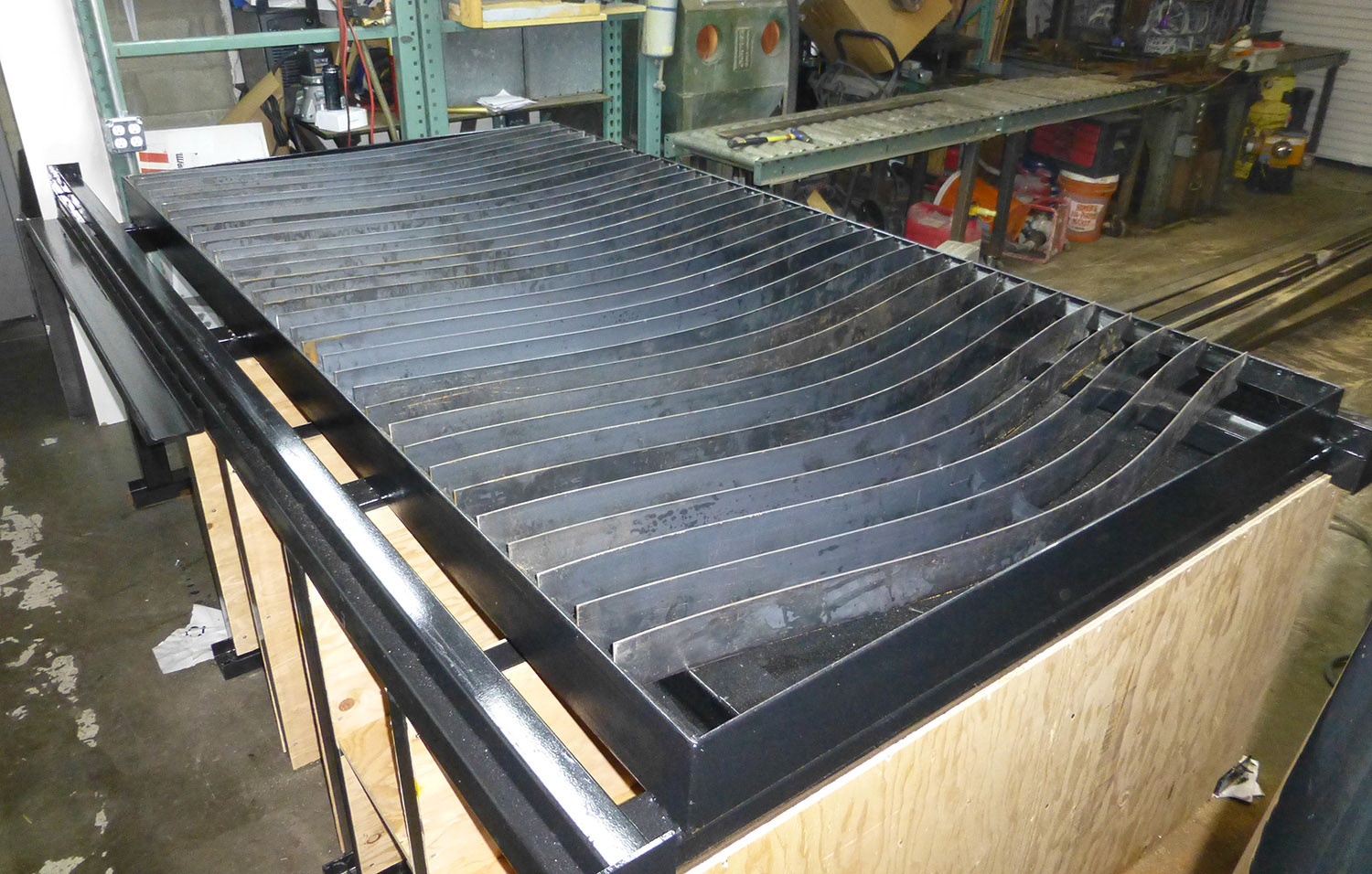
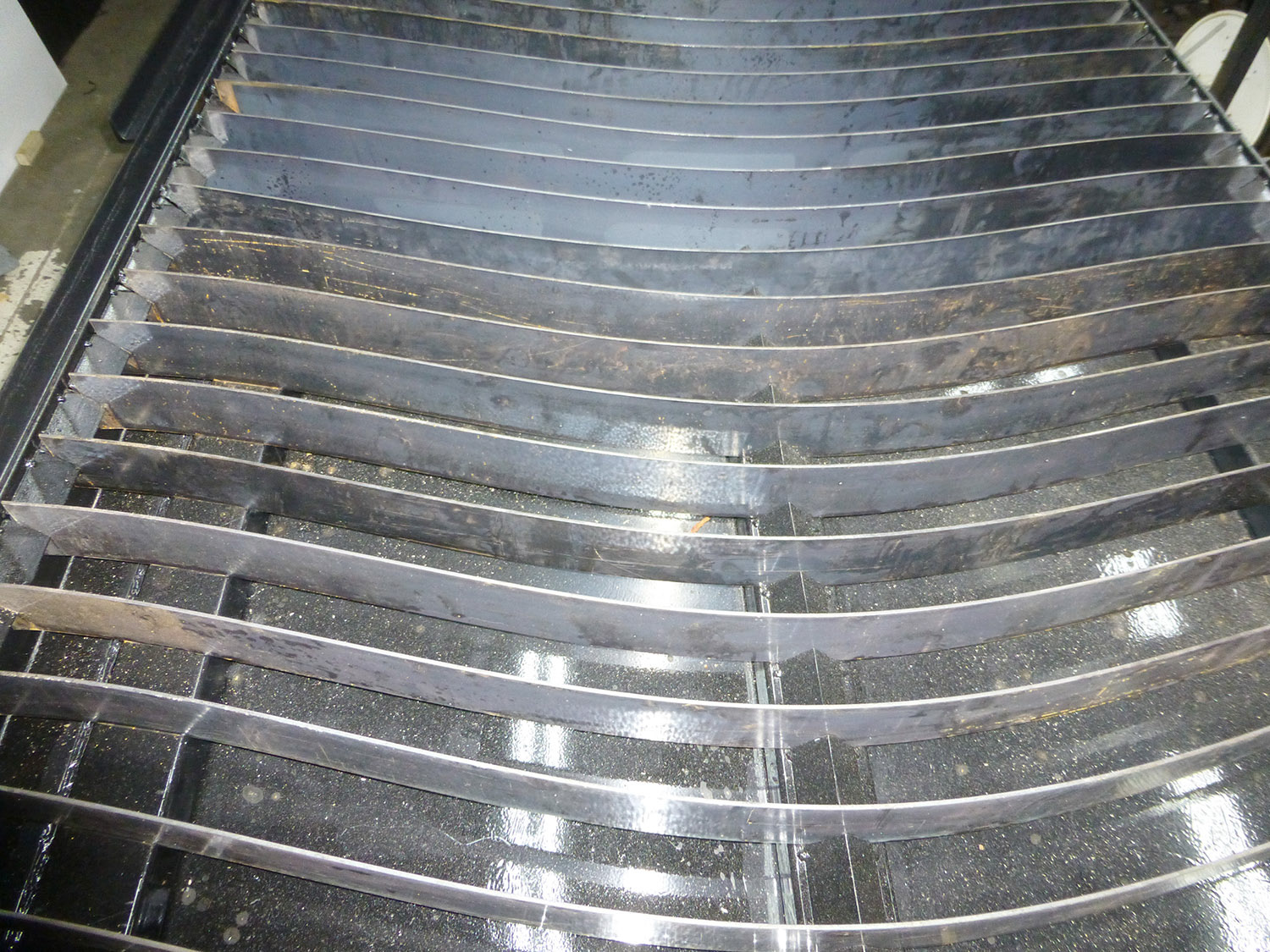
With the frame completed, it was time to work on the table. I added a piece of eighth inch steel for the tray. I then added some box steel to provide support for the cross slats. I made a fixture to position all the pieces of angle iron that will be holding the slats in position. I added a drain and inlet for the water. I painted everything with a heavy coat or Rust-Oleum paint to seal it up and reduce the rust. I then added the slats.
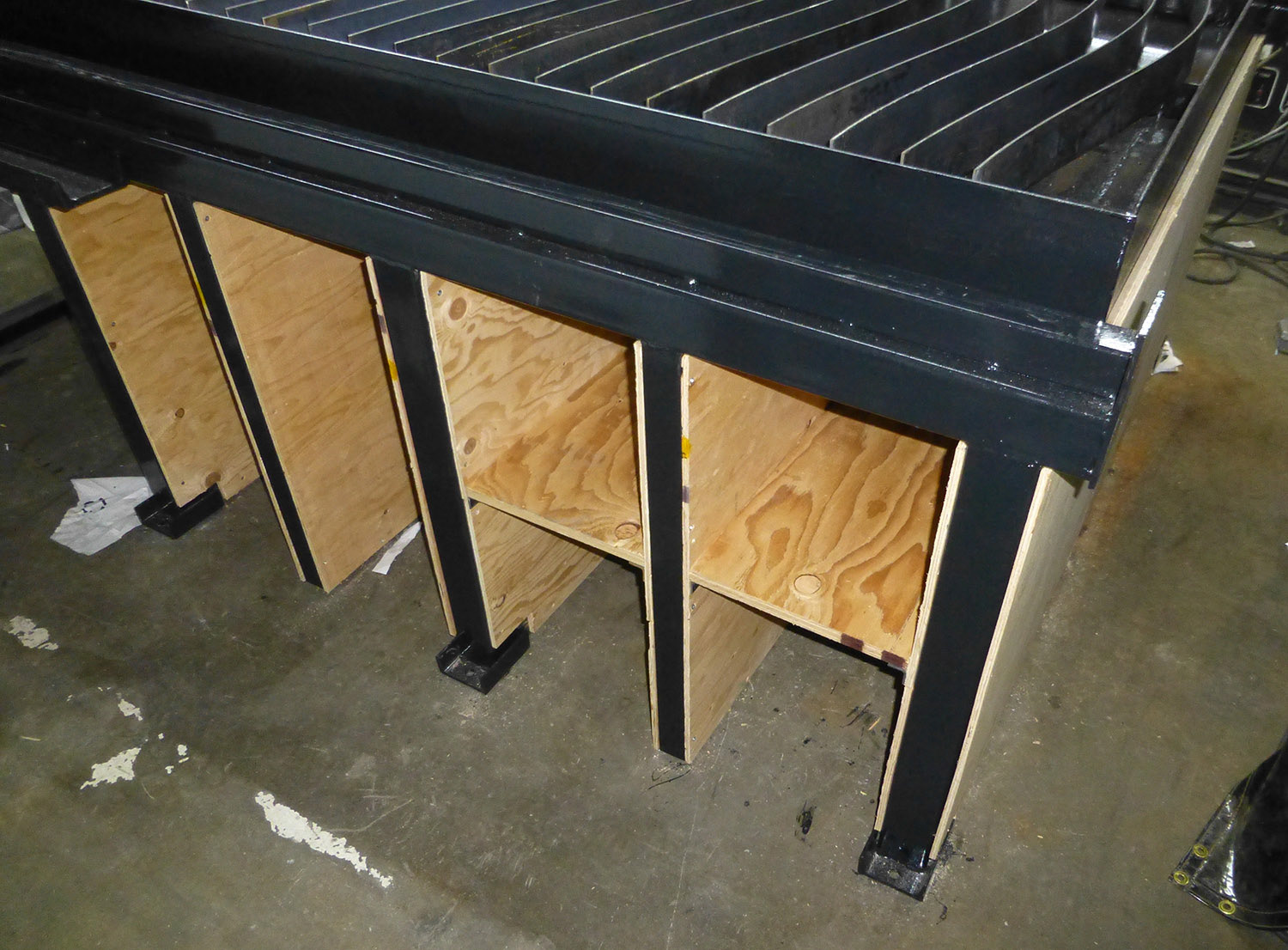
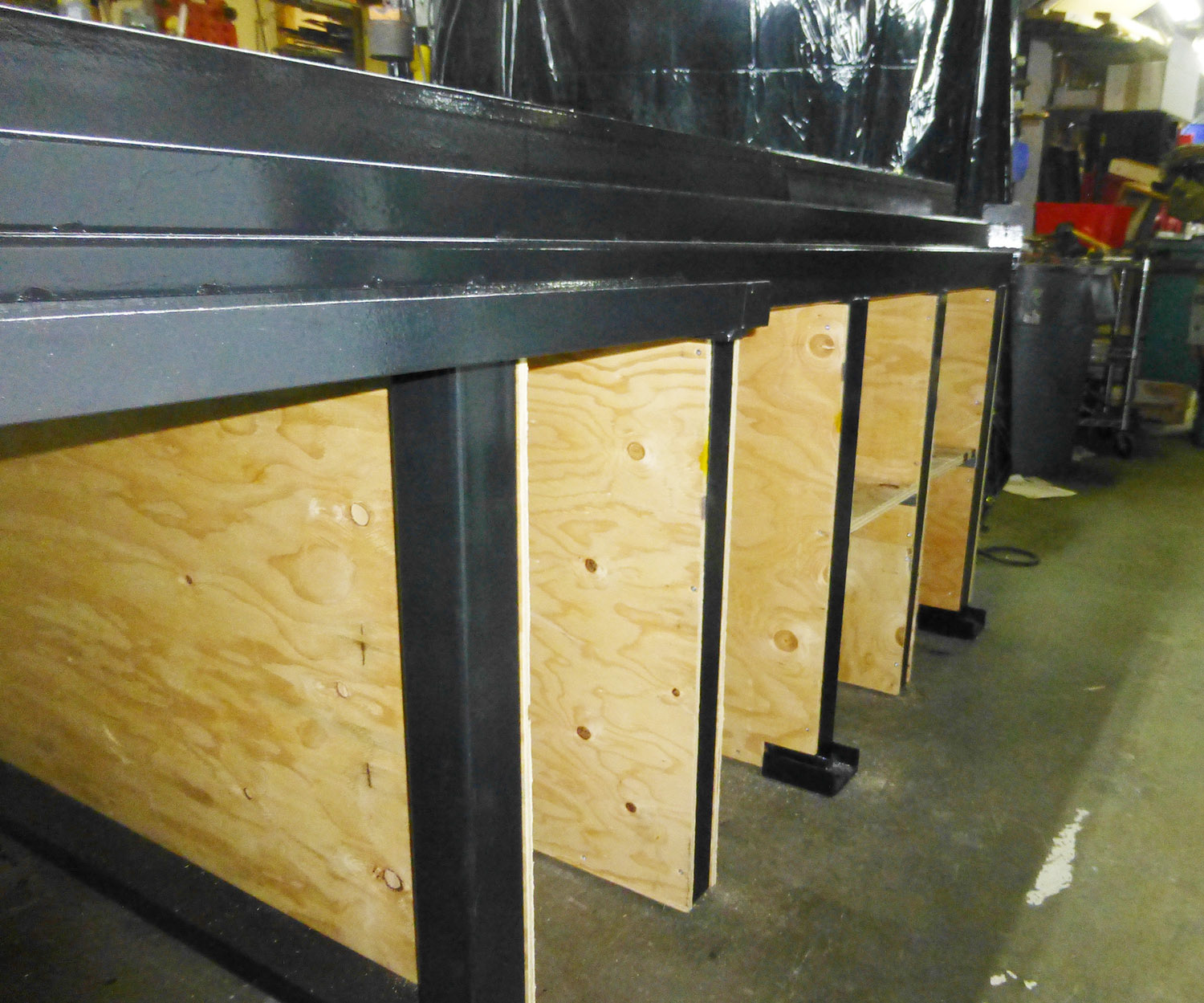
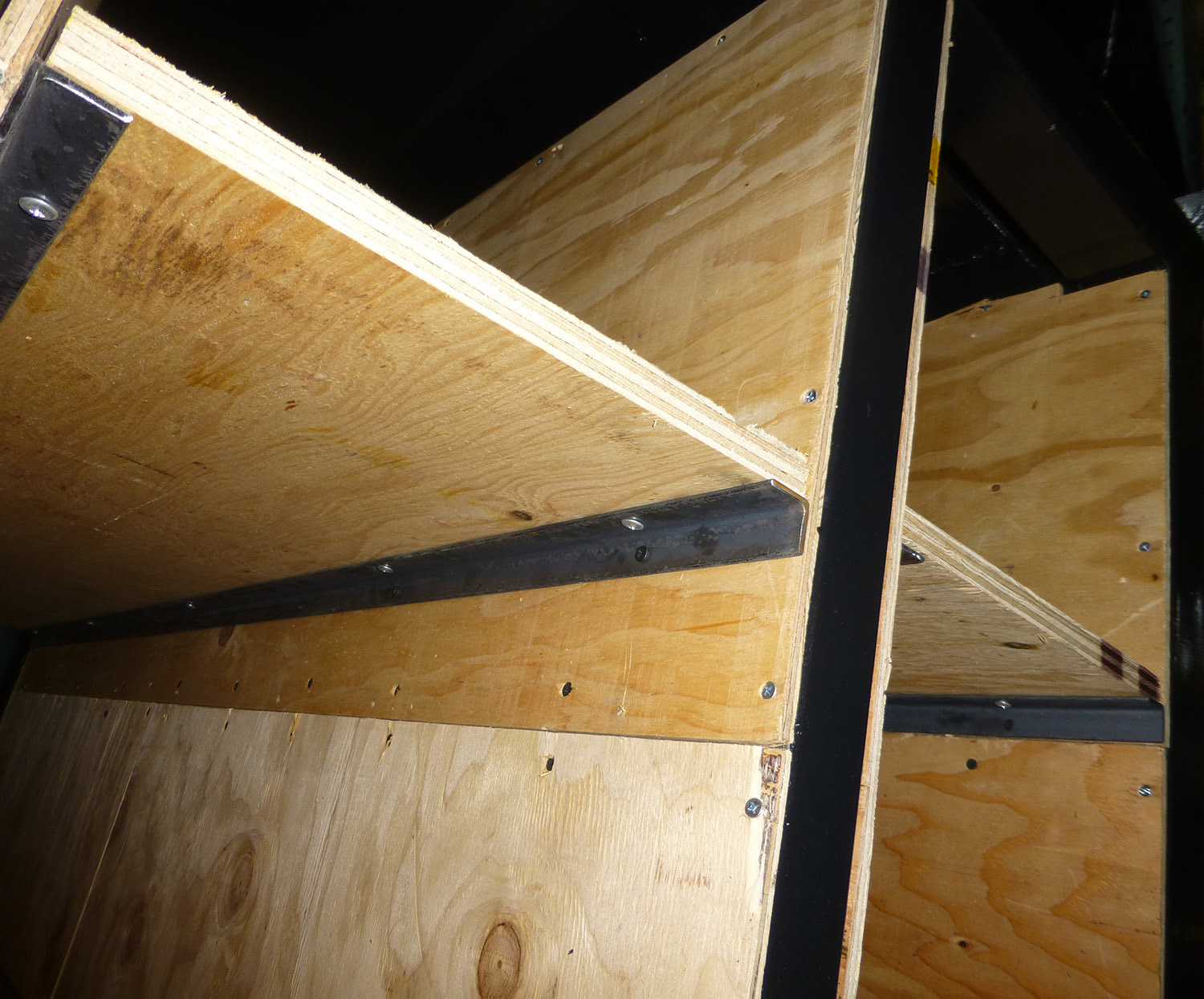
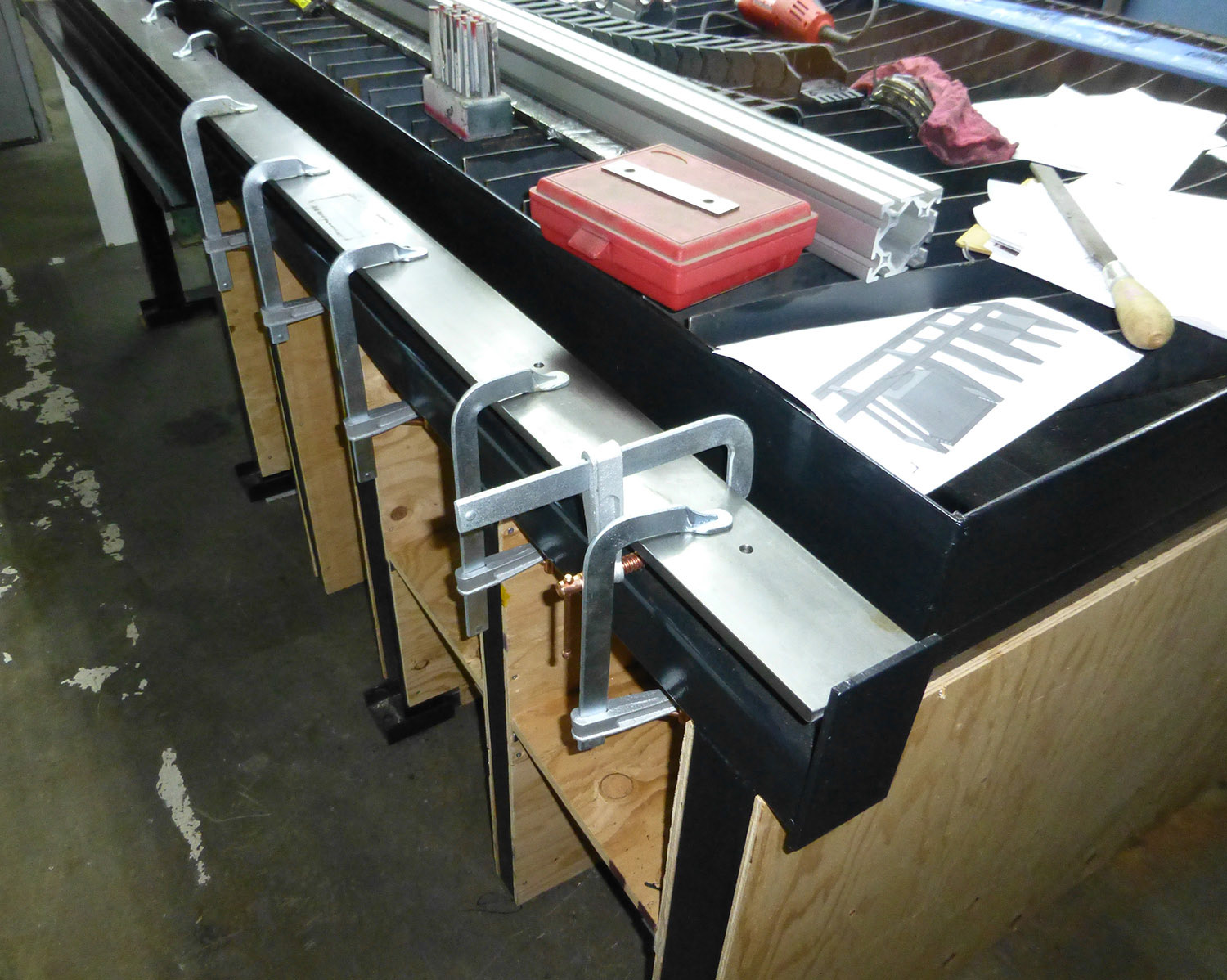
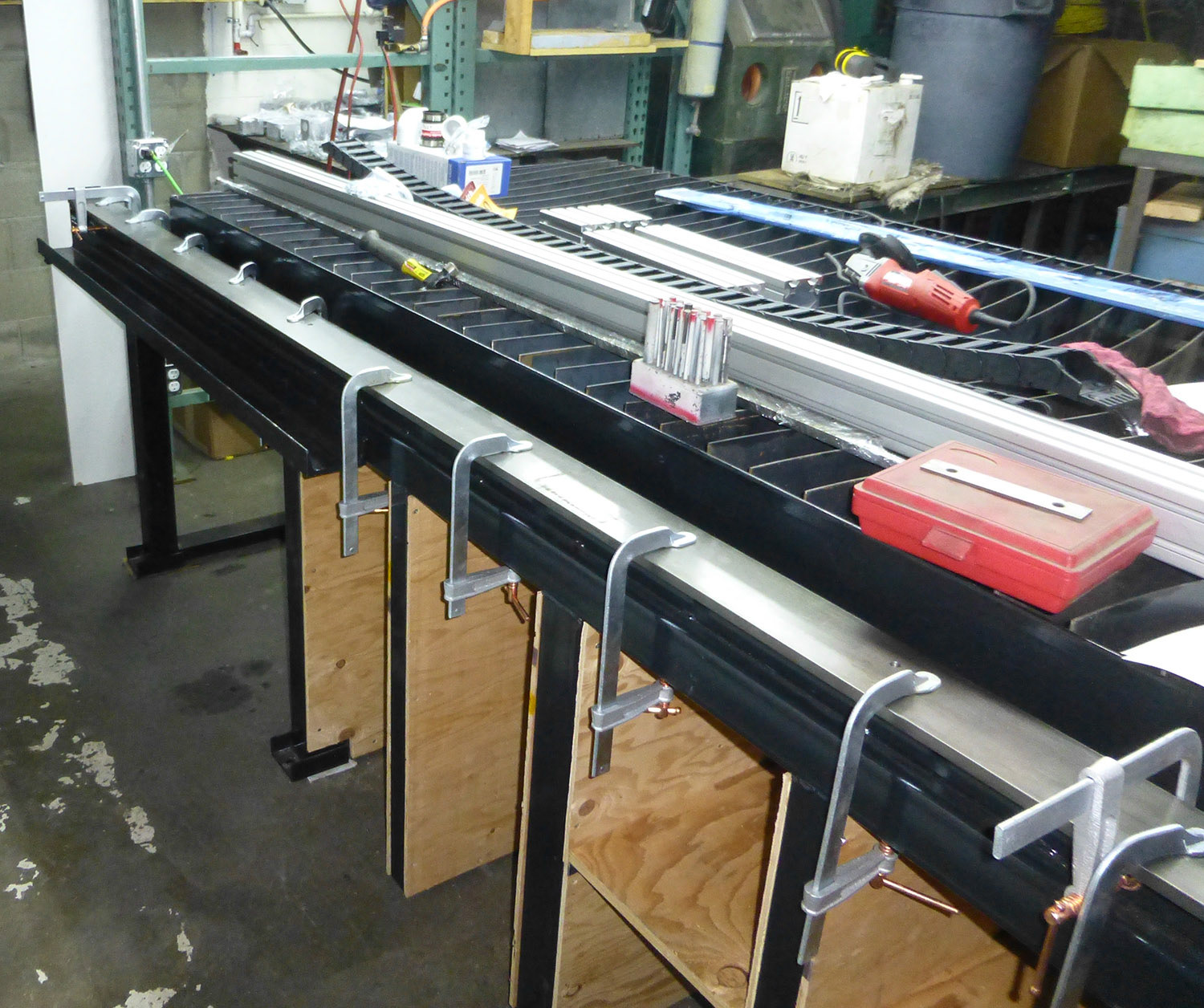
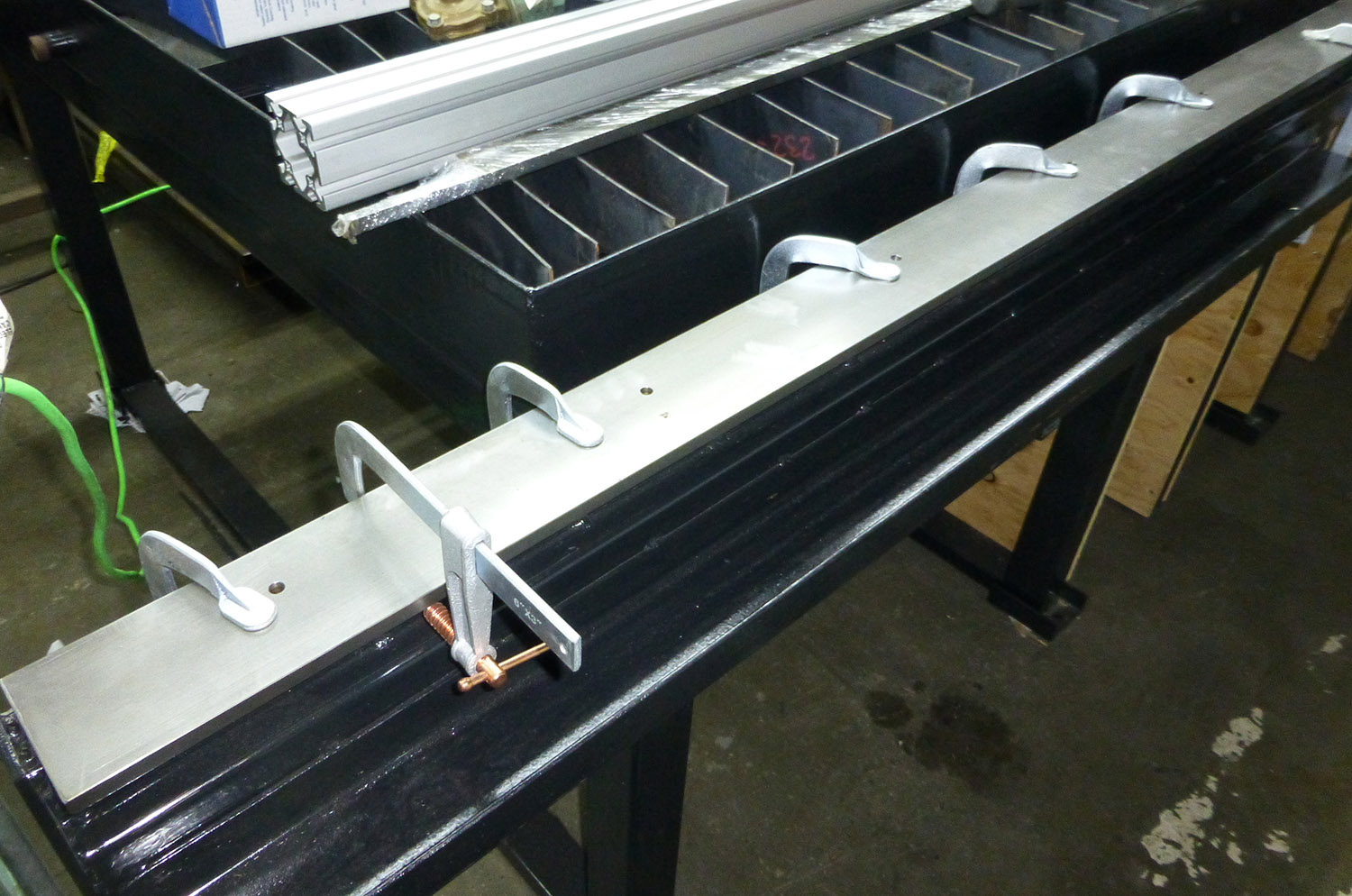
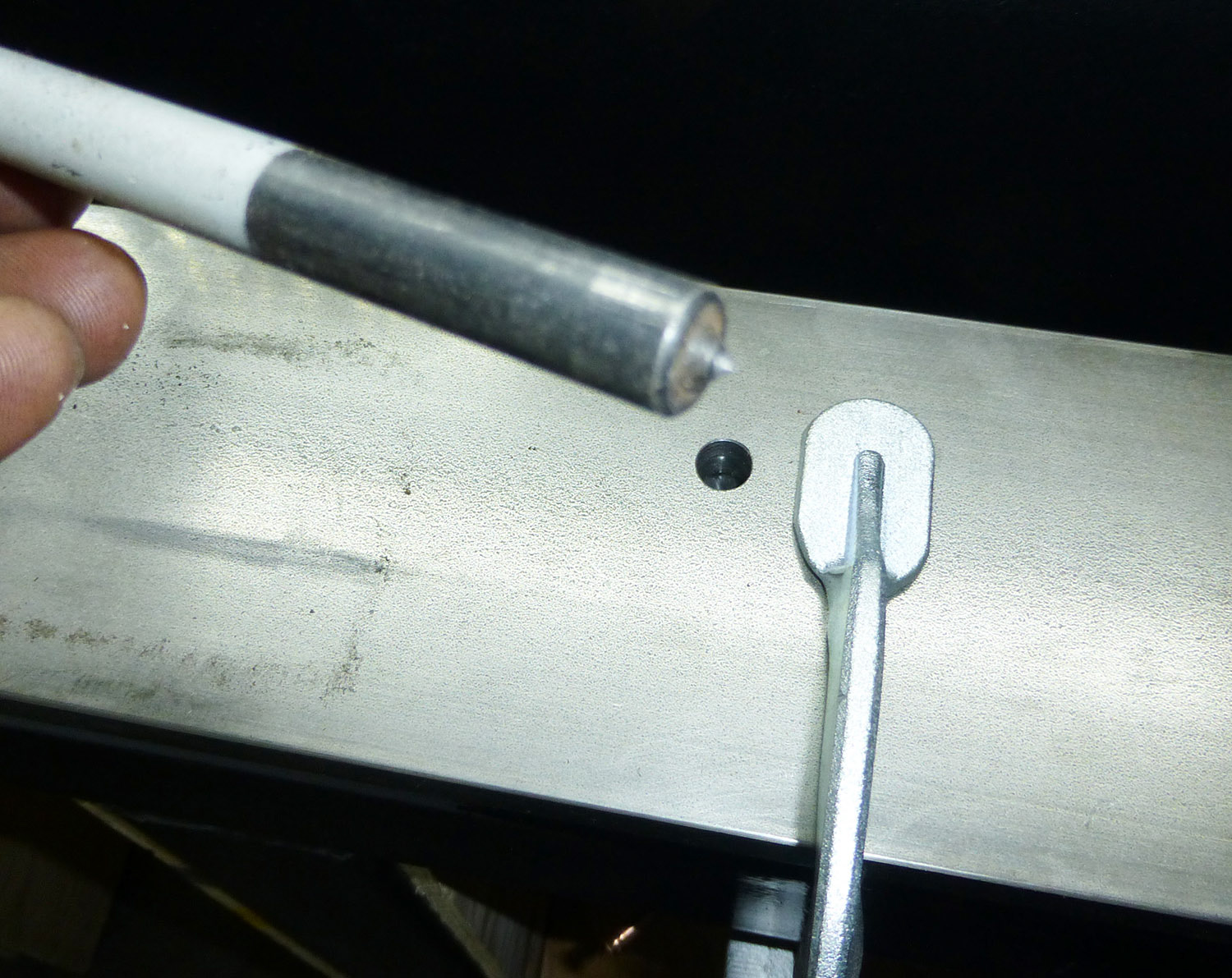
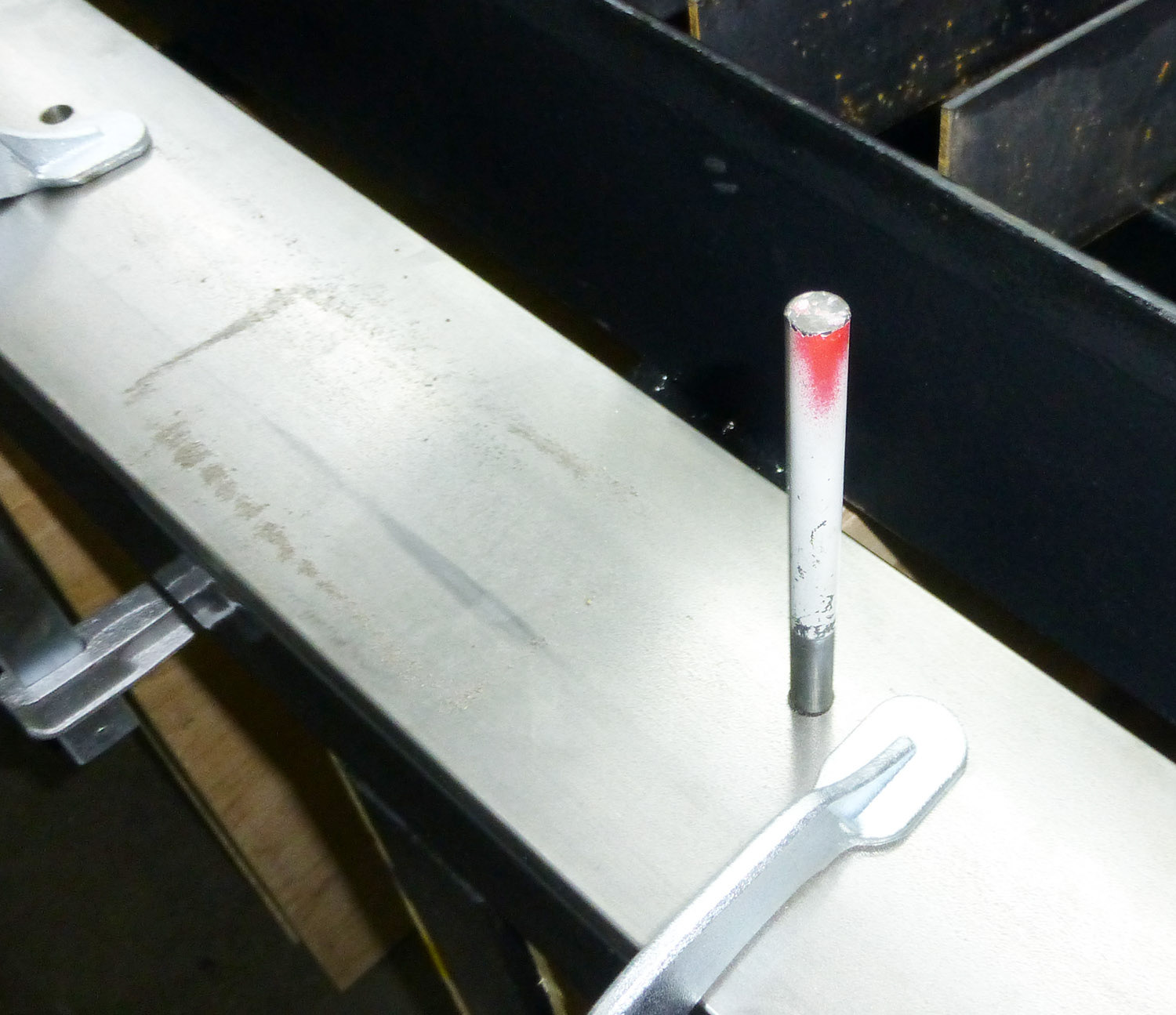
With everything painted, and plywood installed to store scrap metal, it was a time to add the 3-inch-wide steel bar that the gantry would ride on.
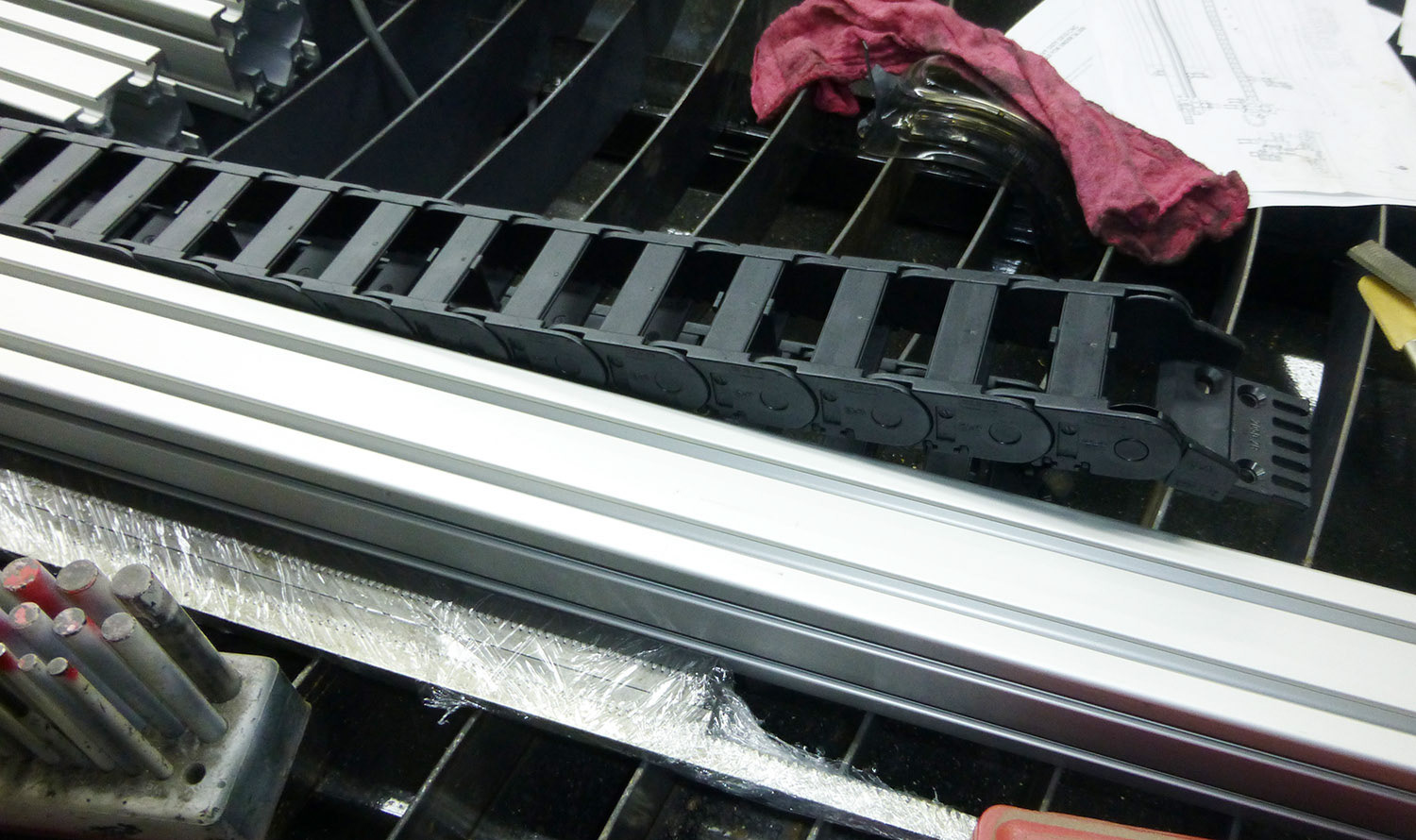
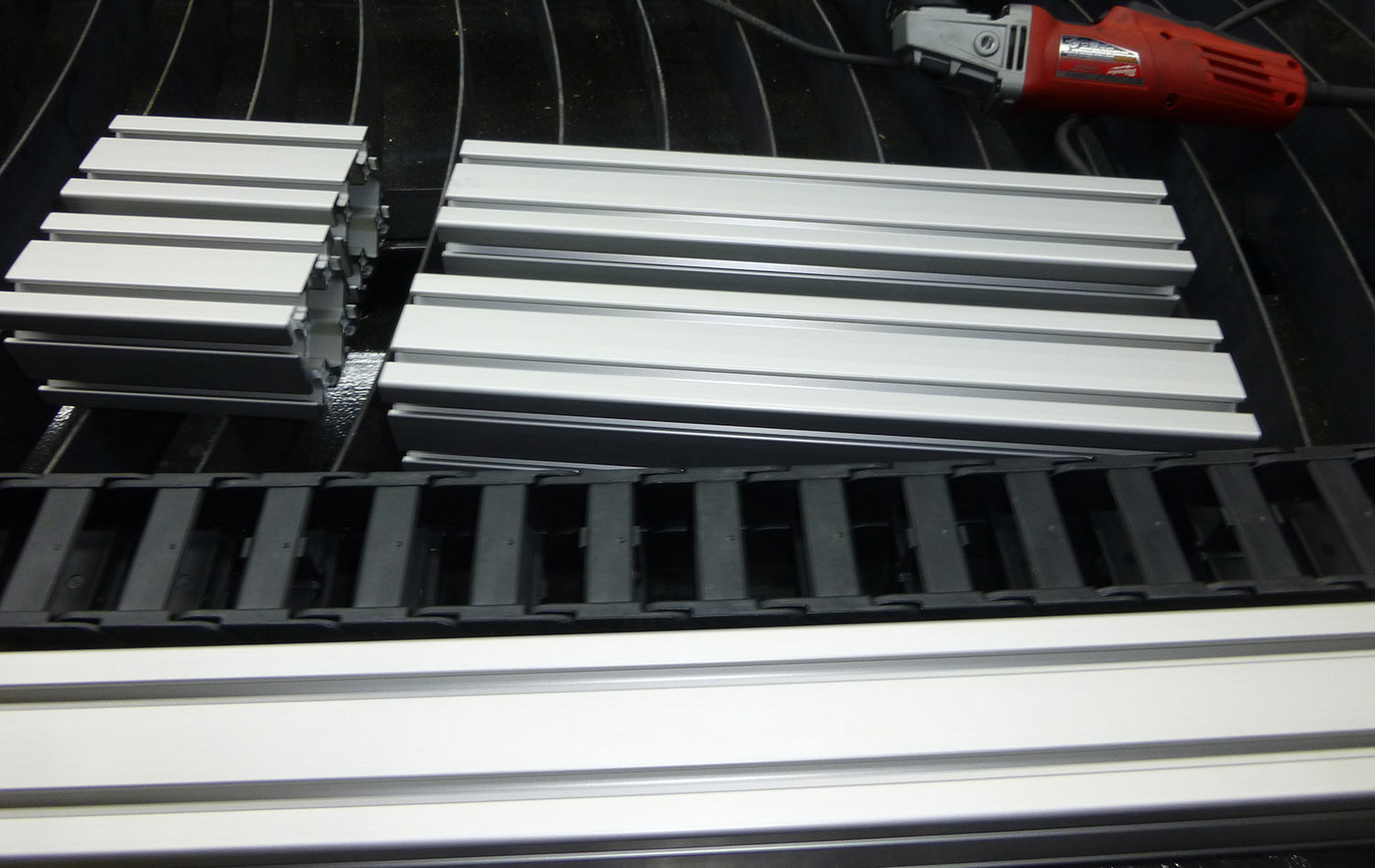
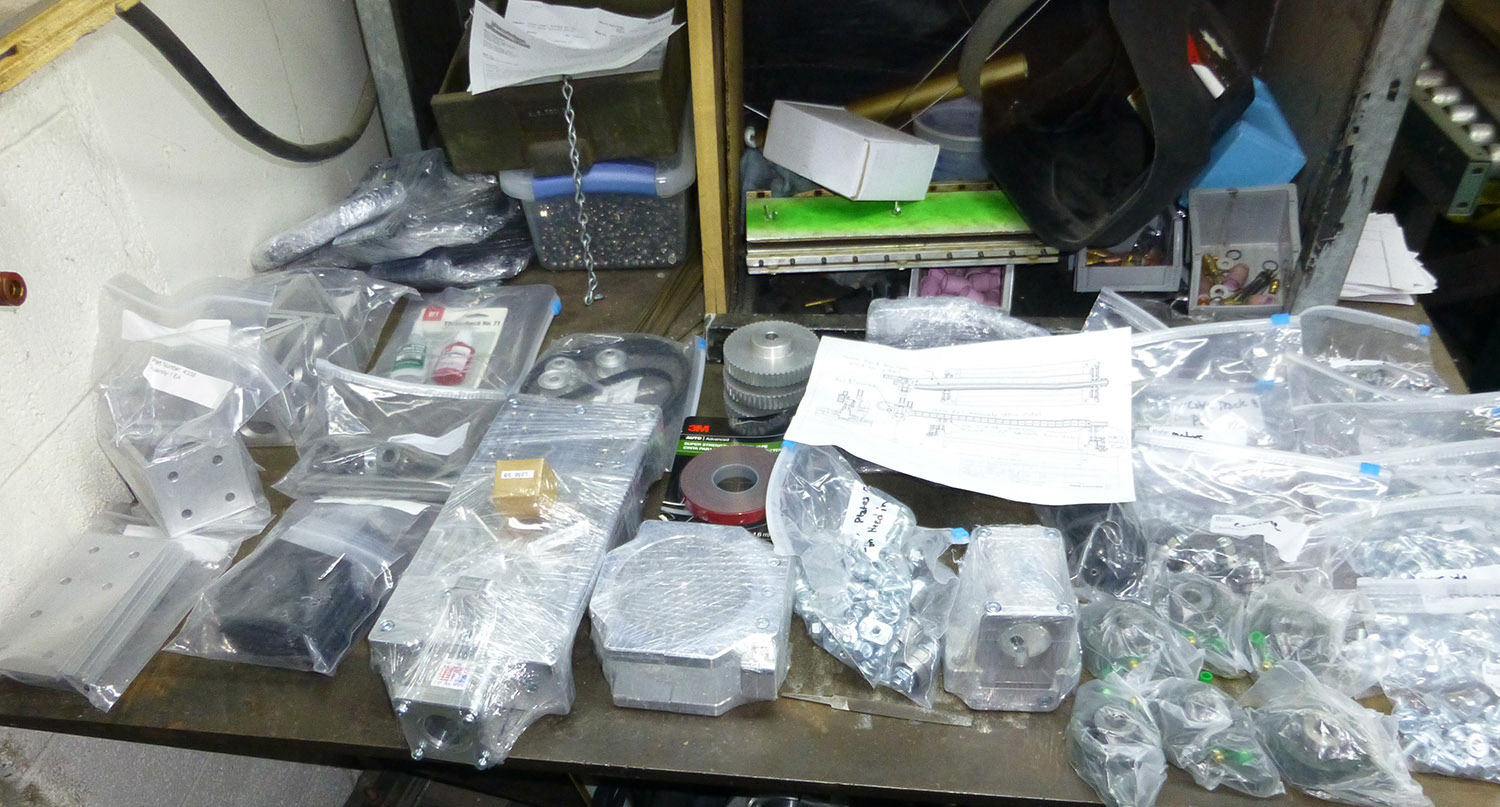

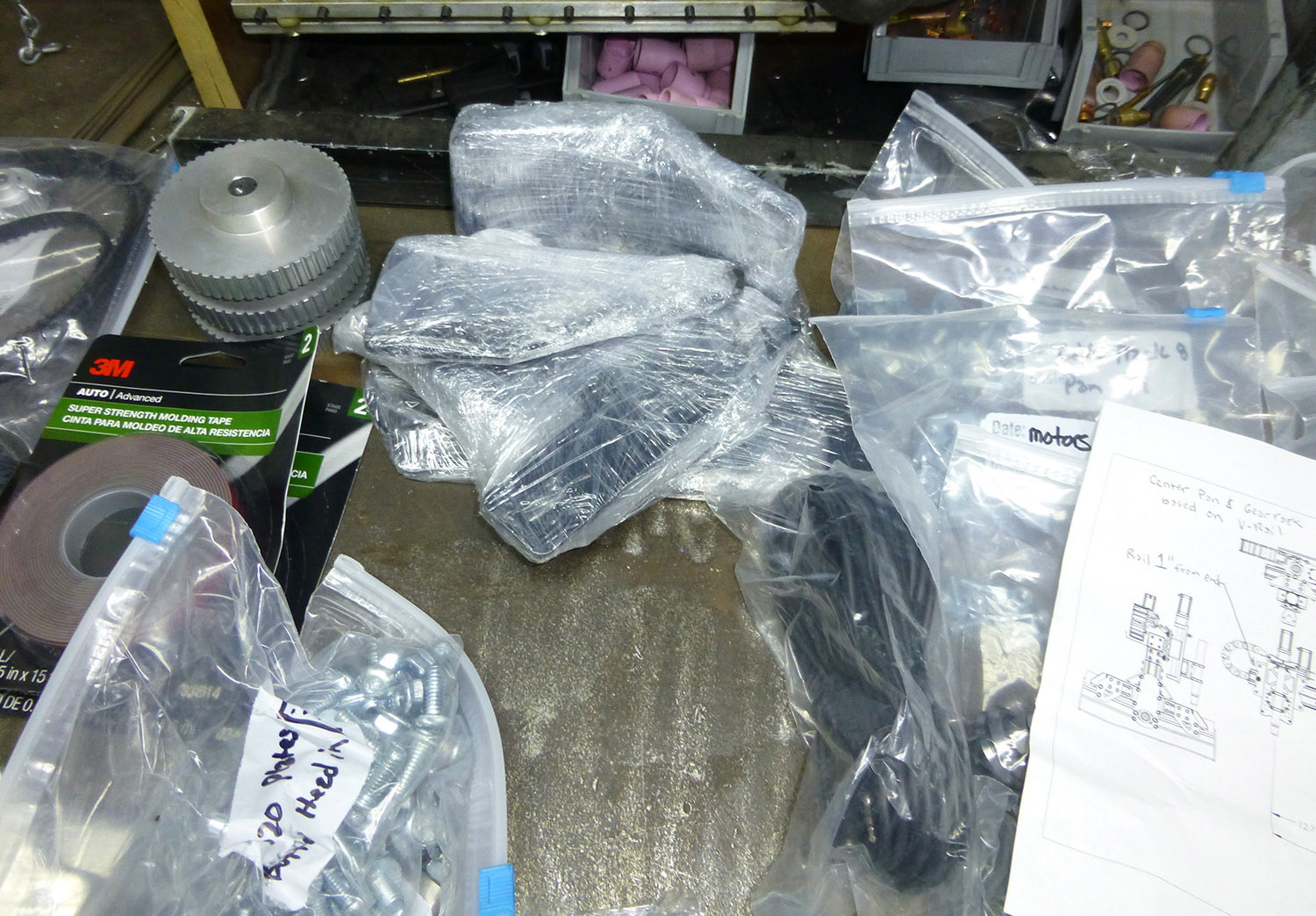
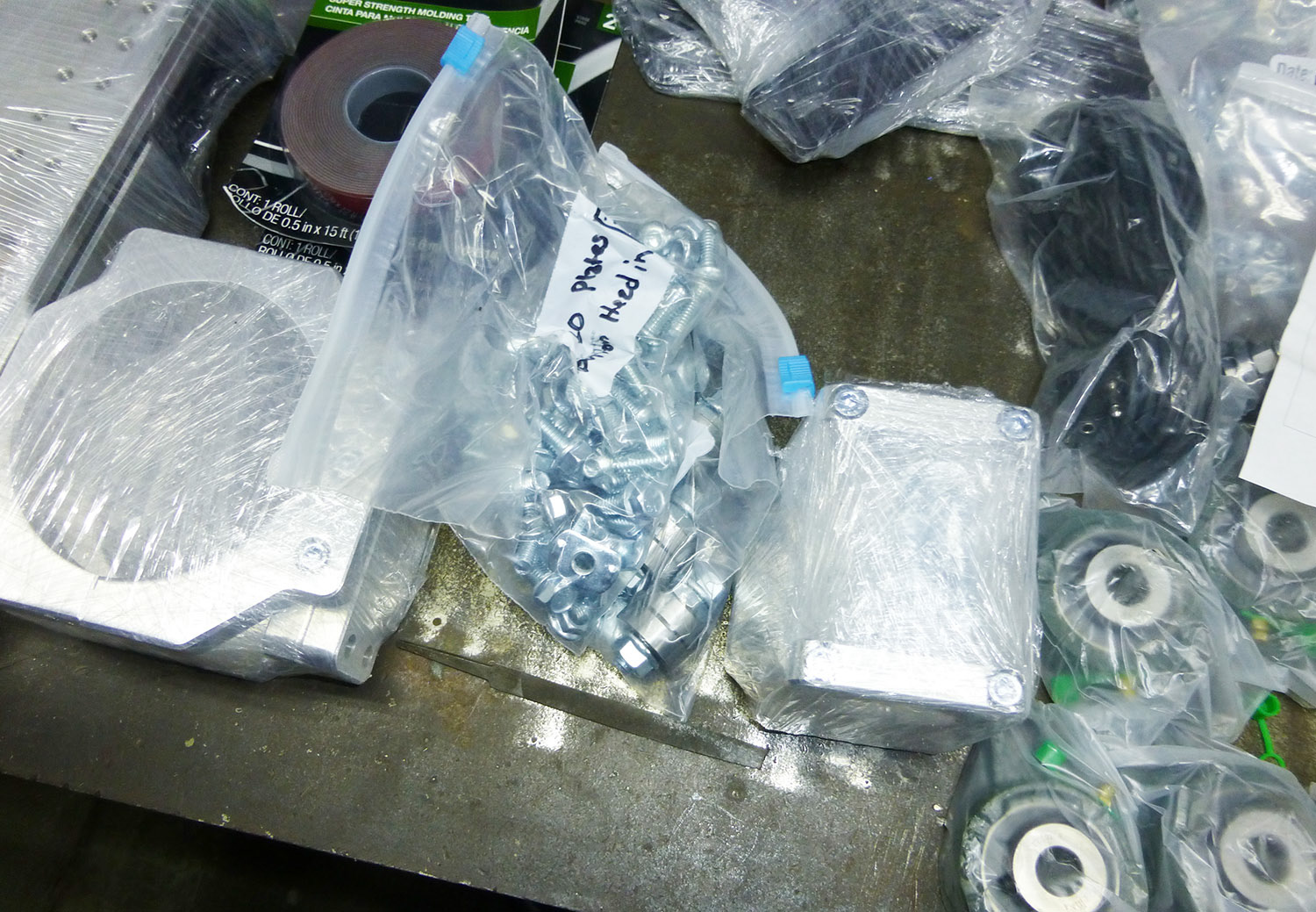
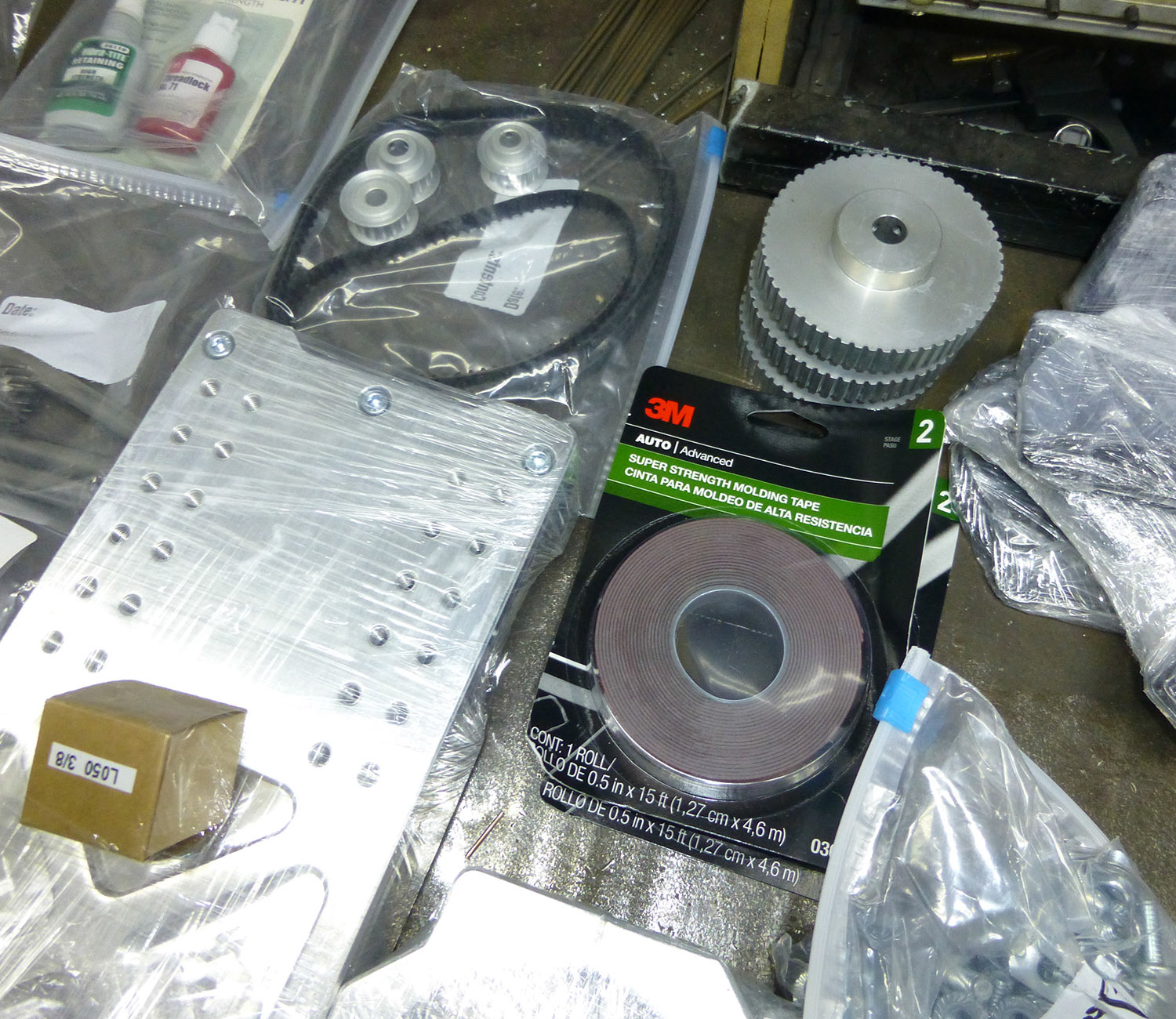
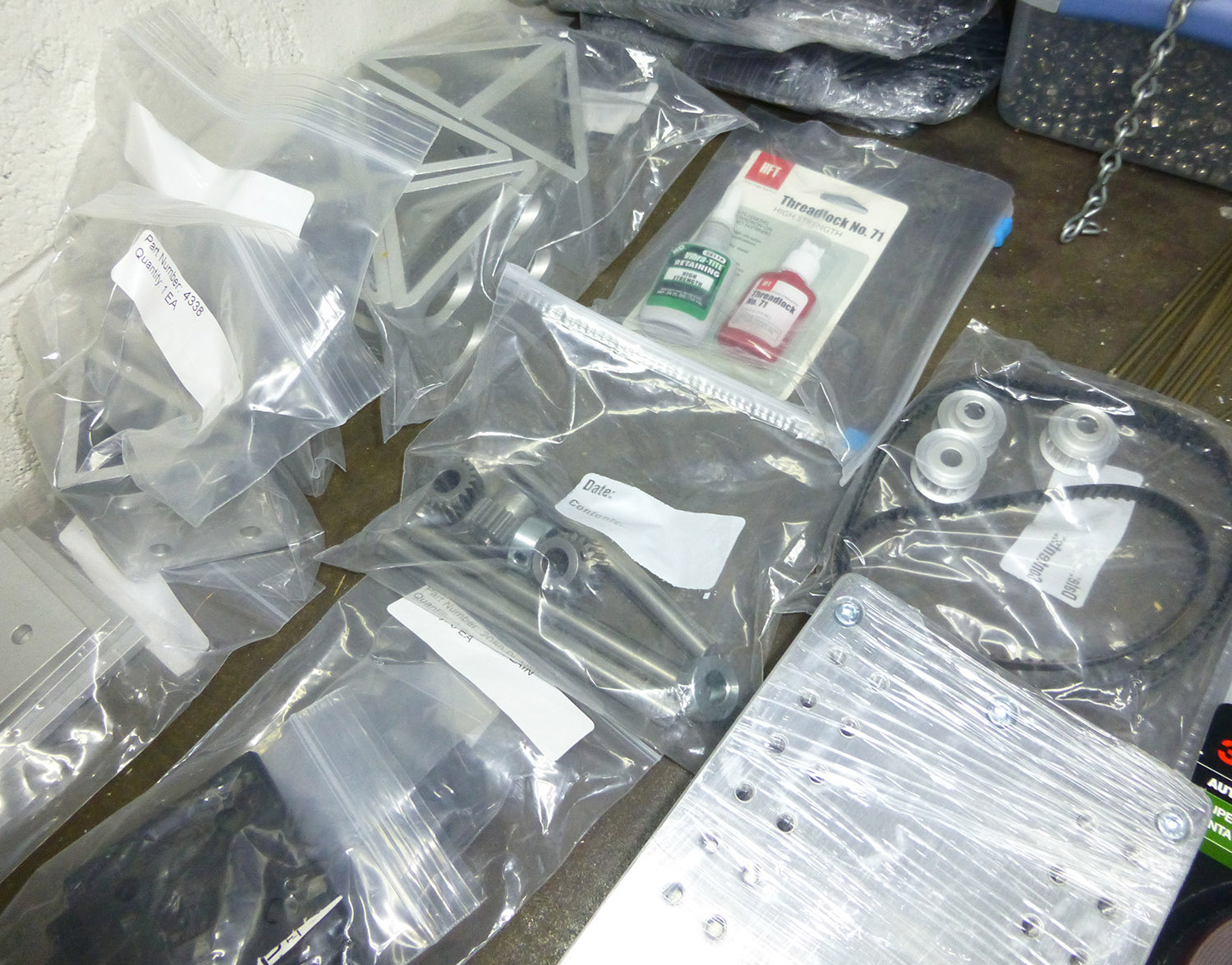

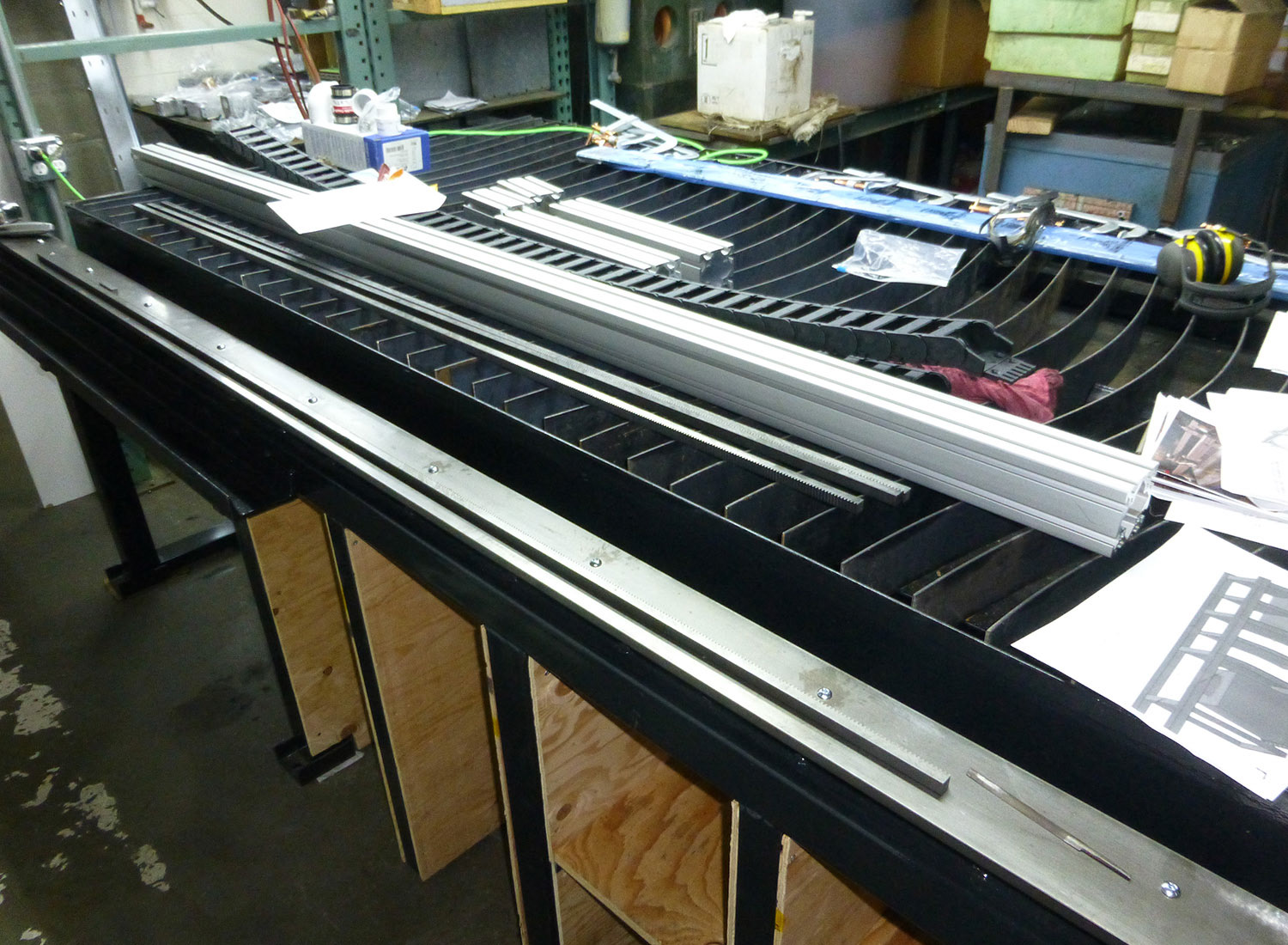
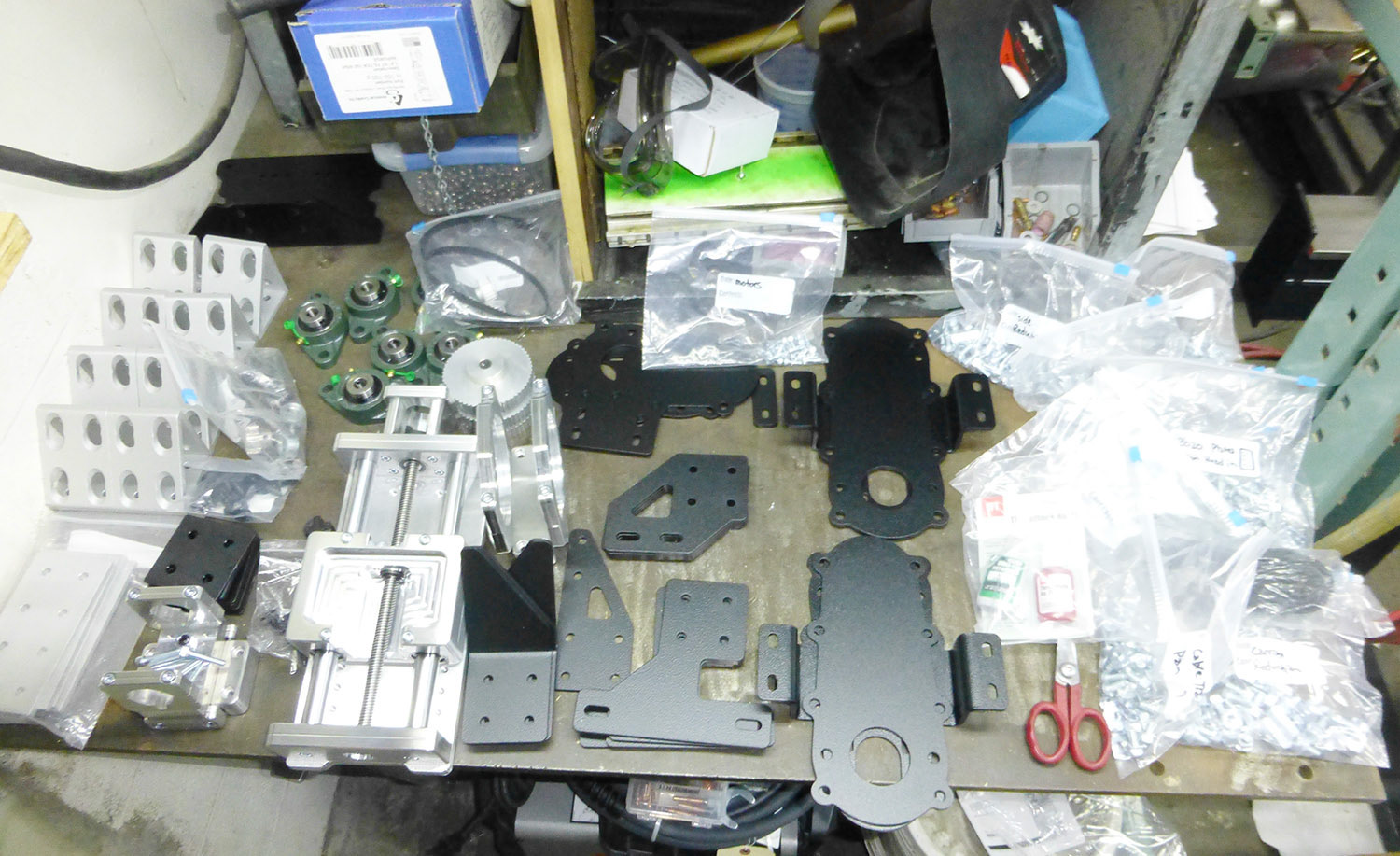
I then took inventory of the gantry kit and got it organized for the next steps.

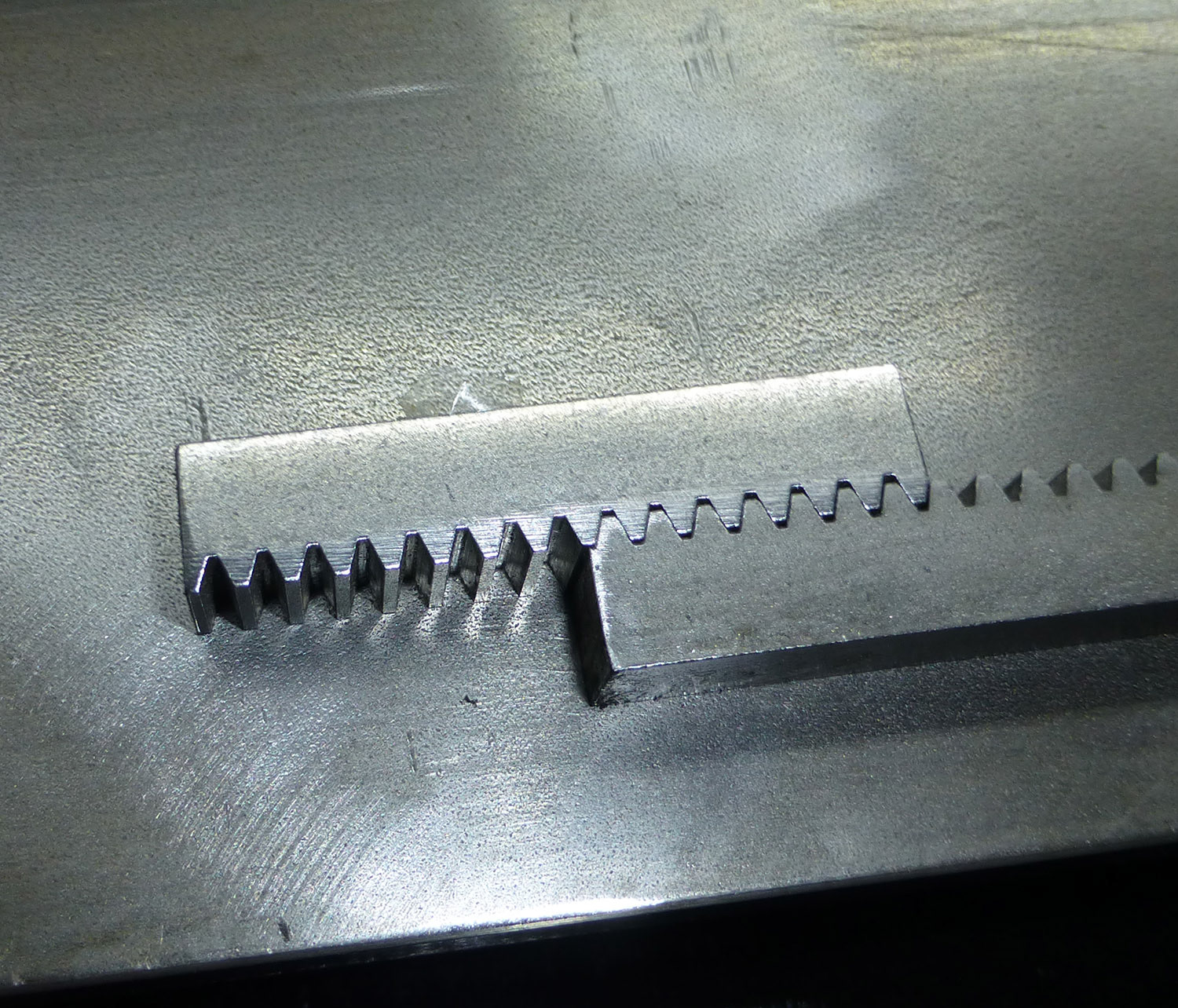
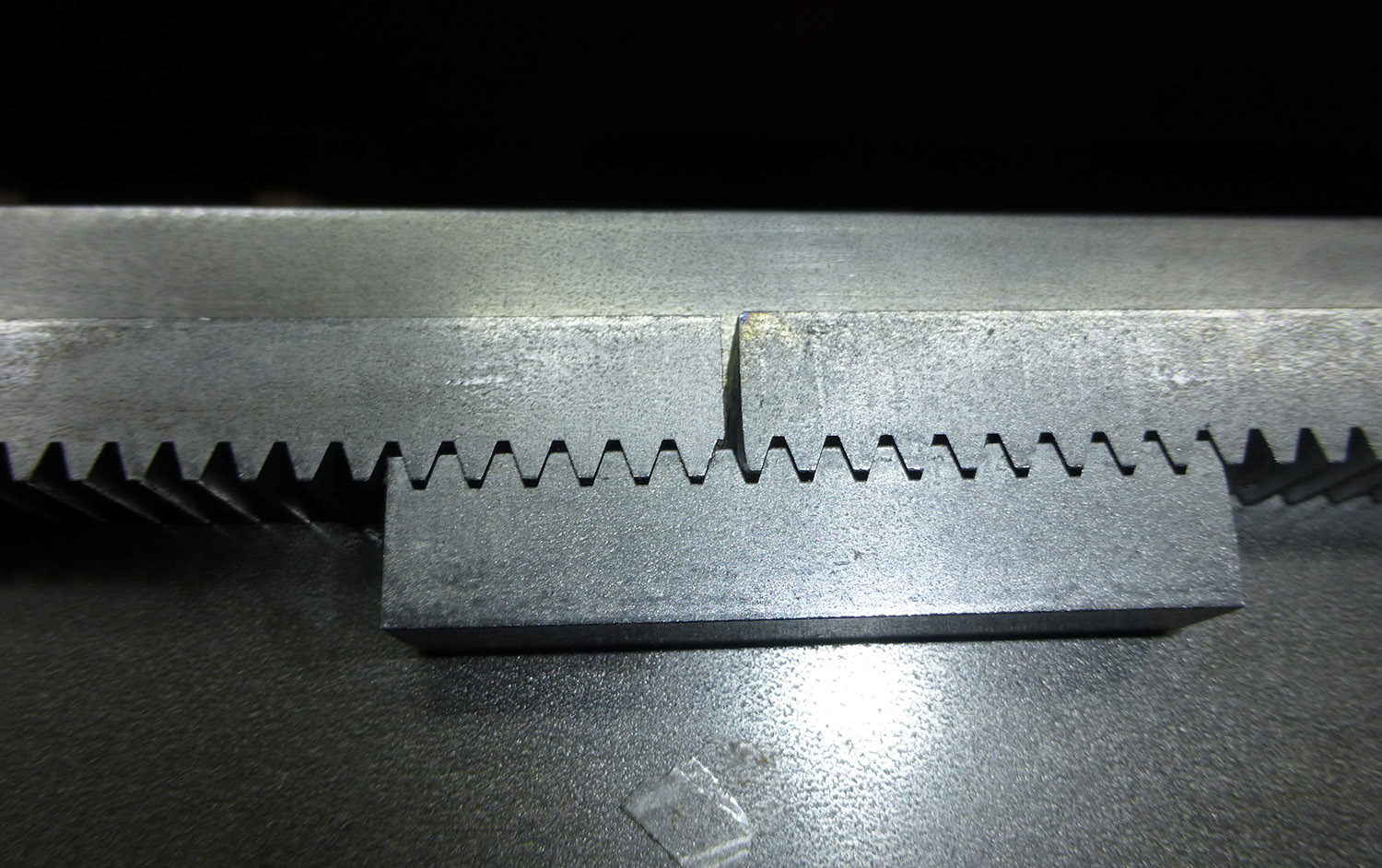
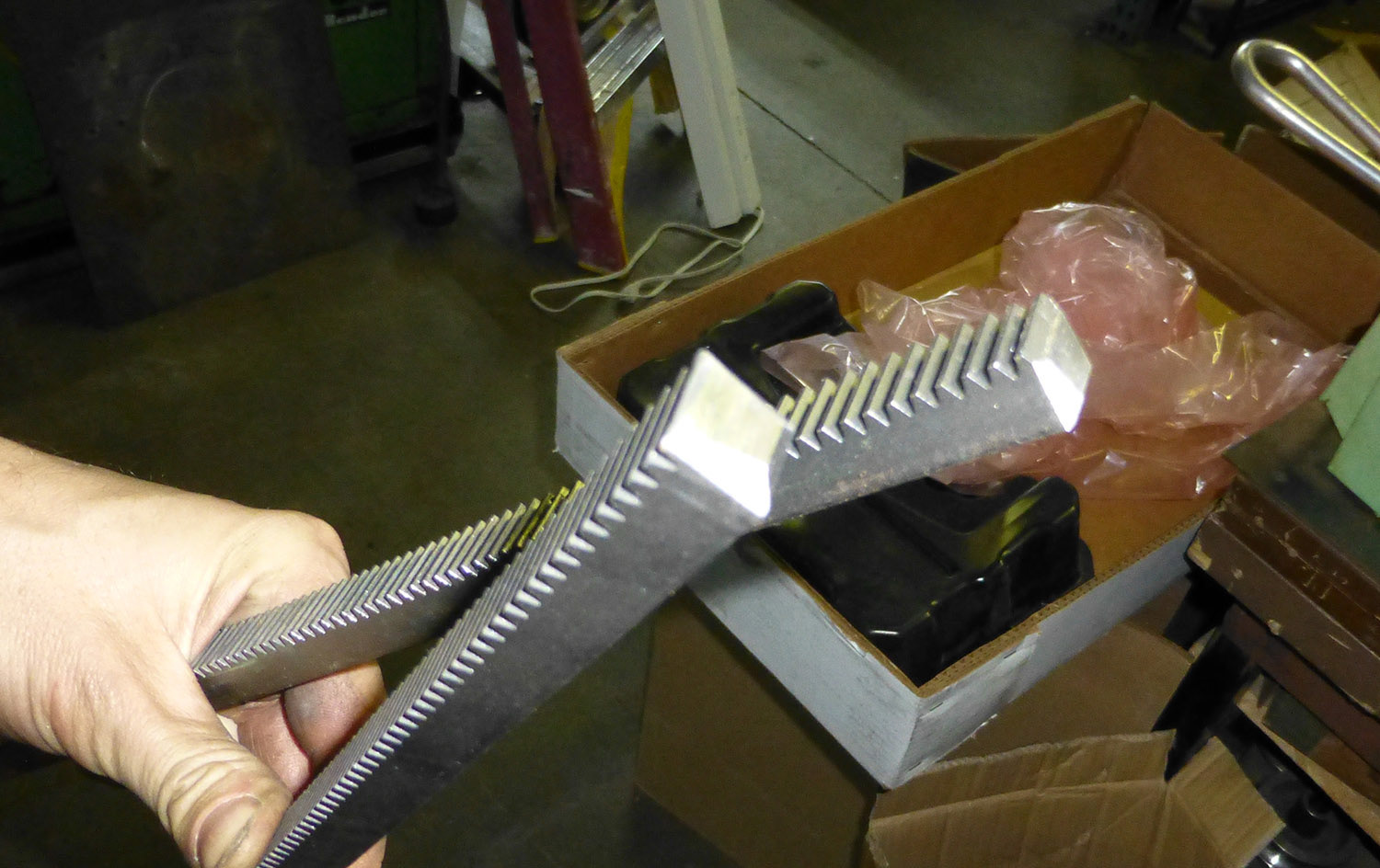
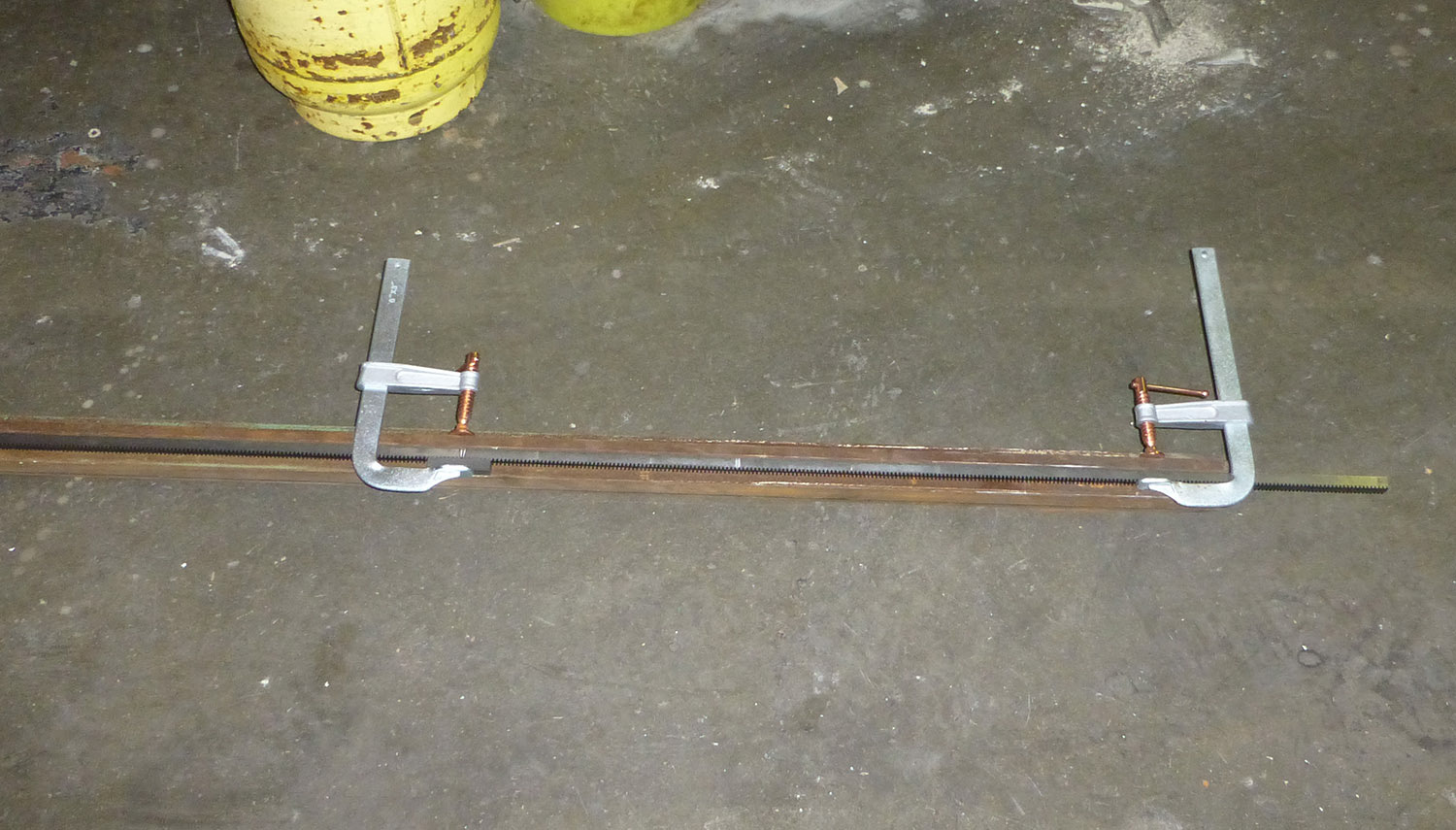
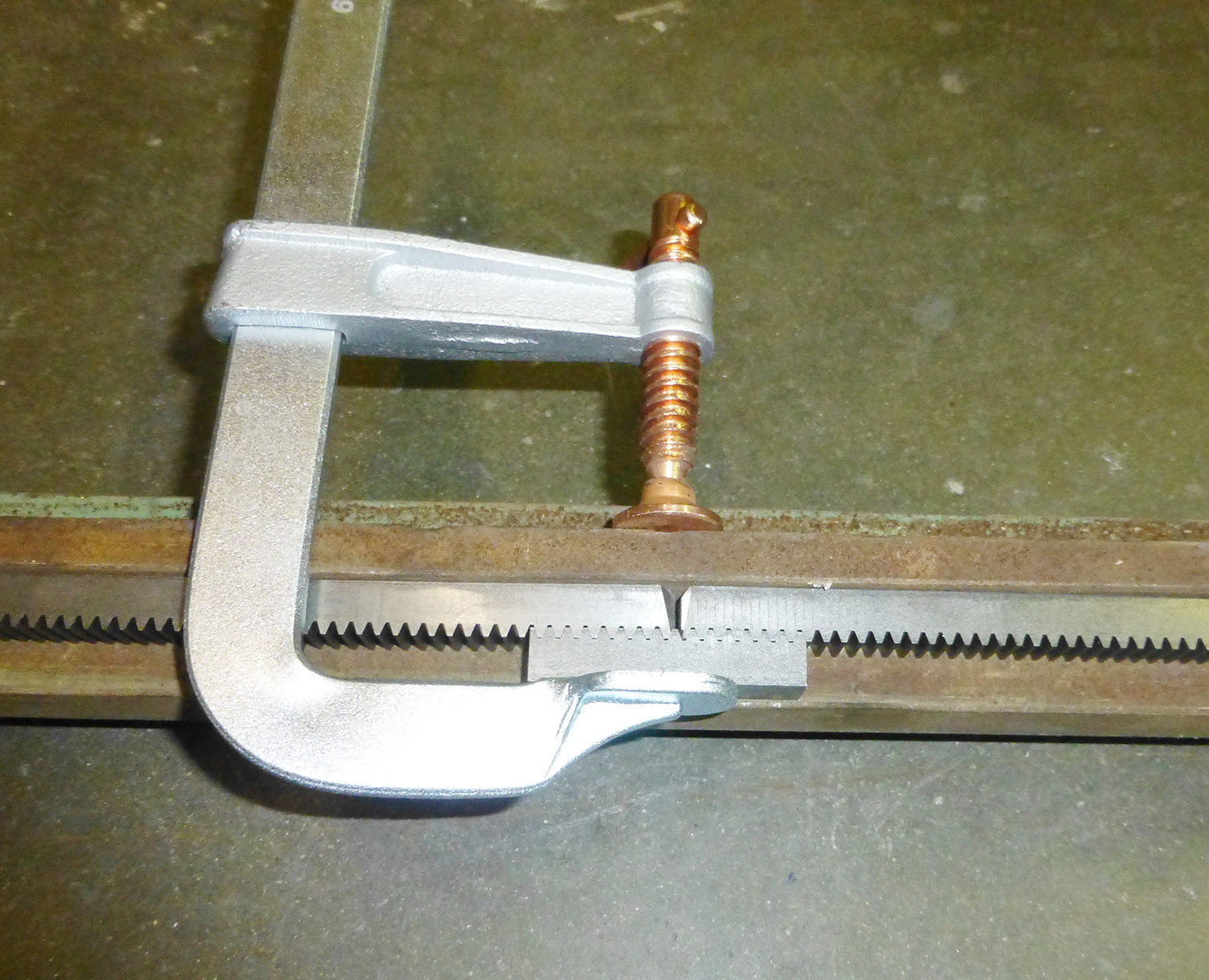
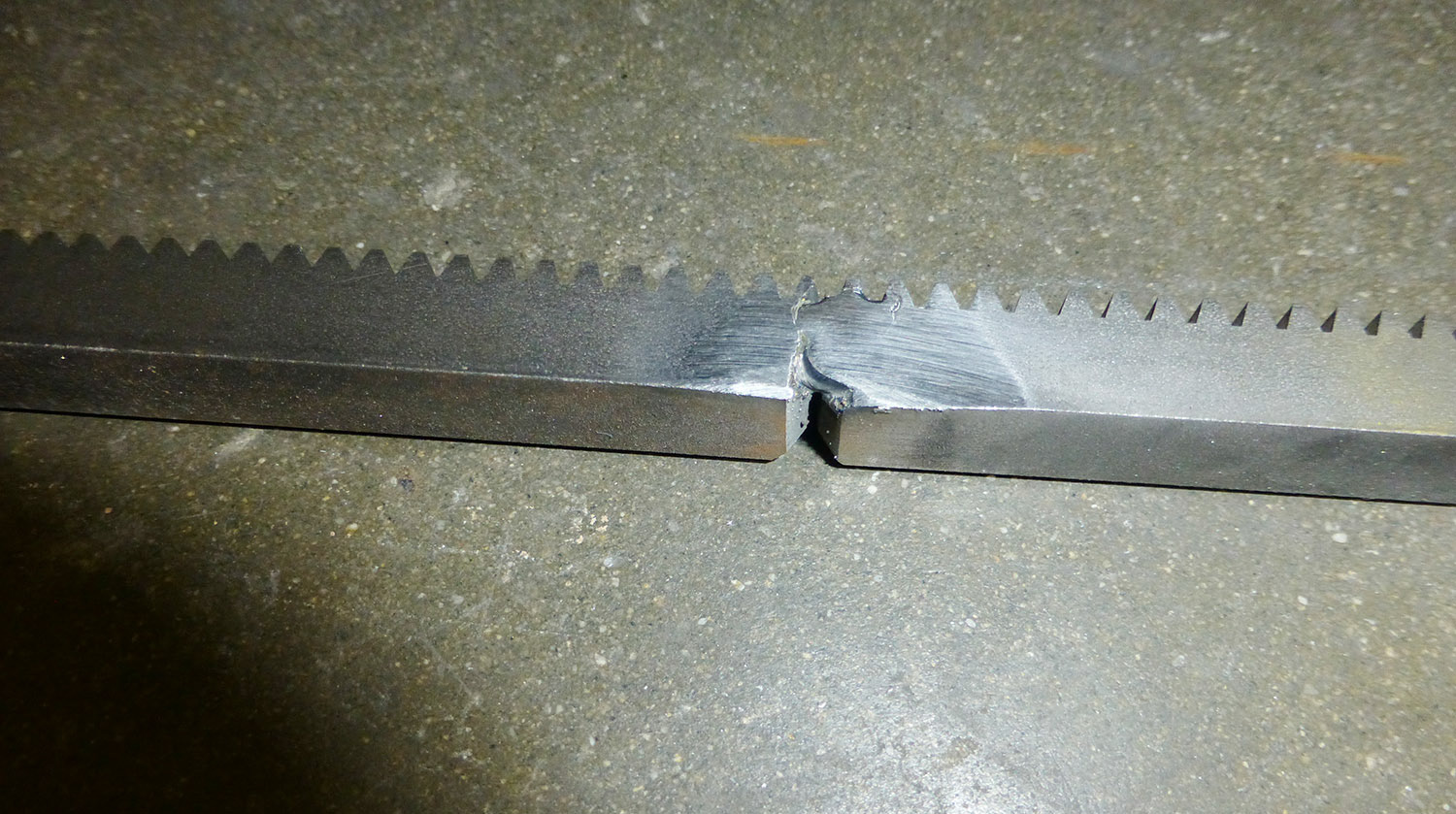
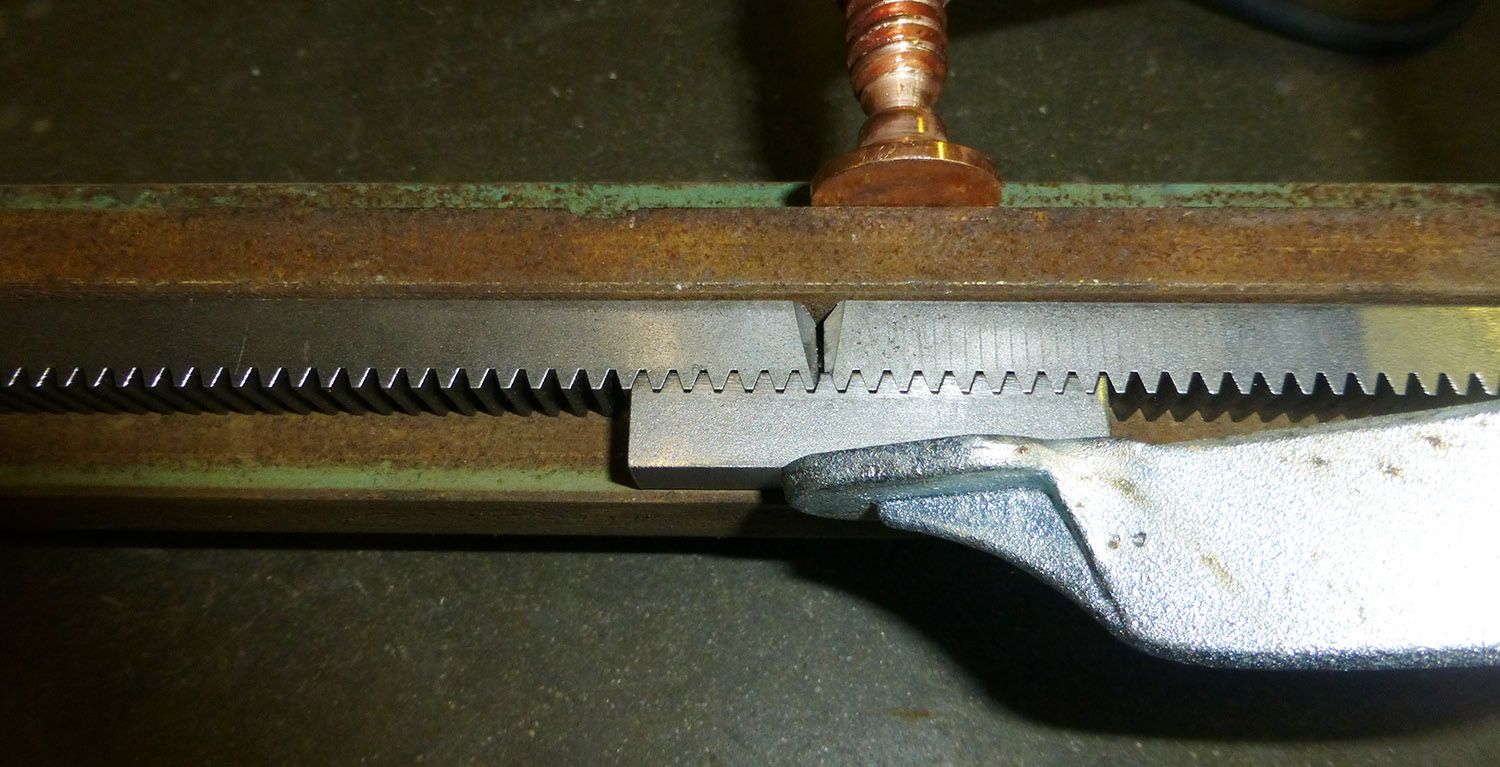

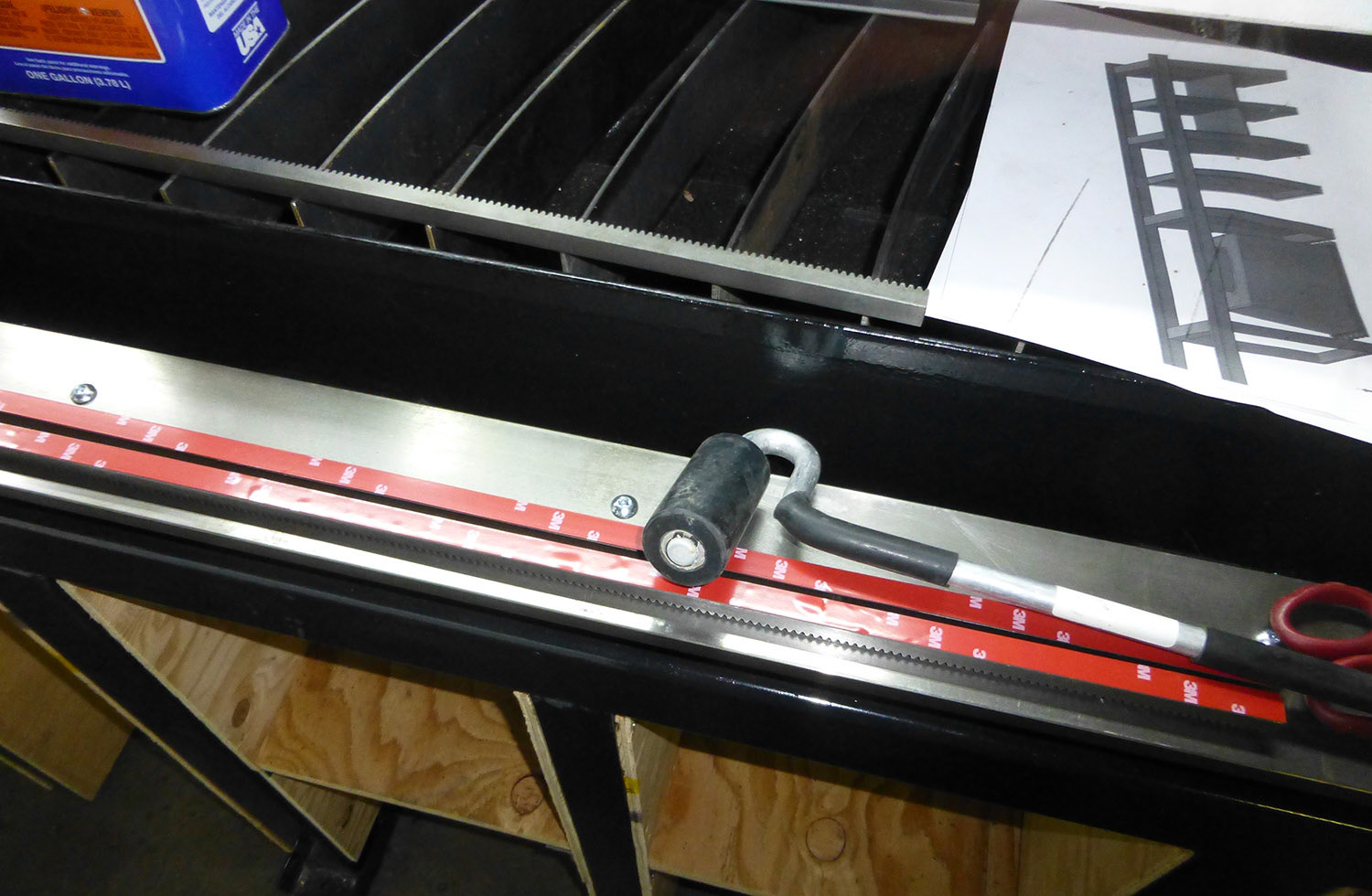
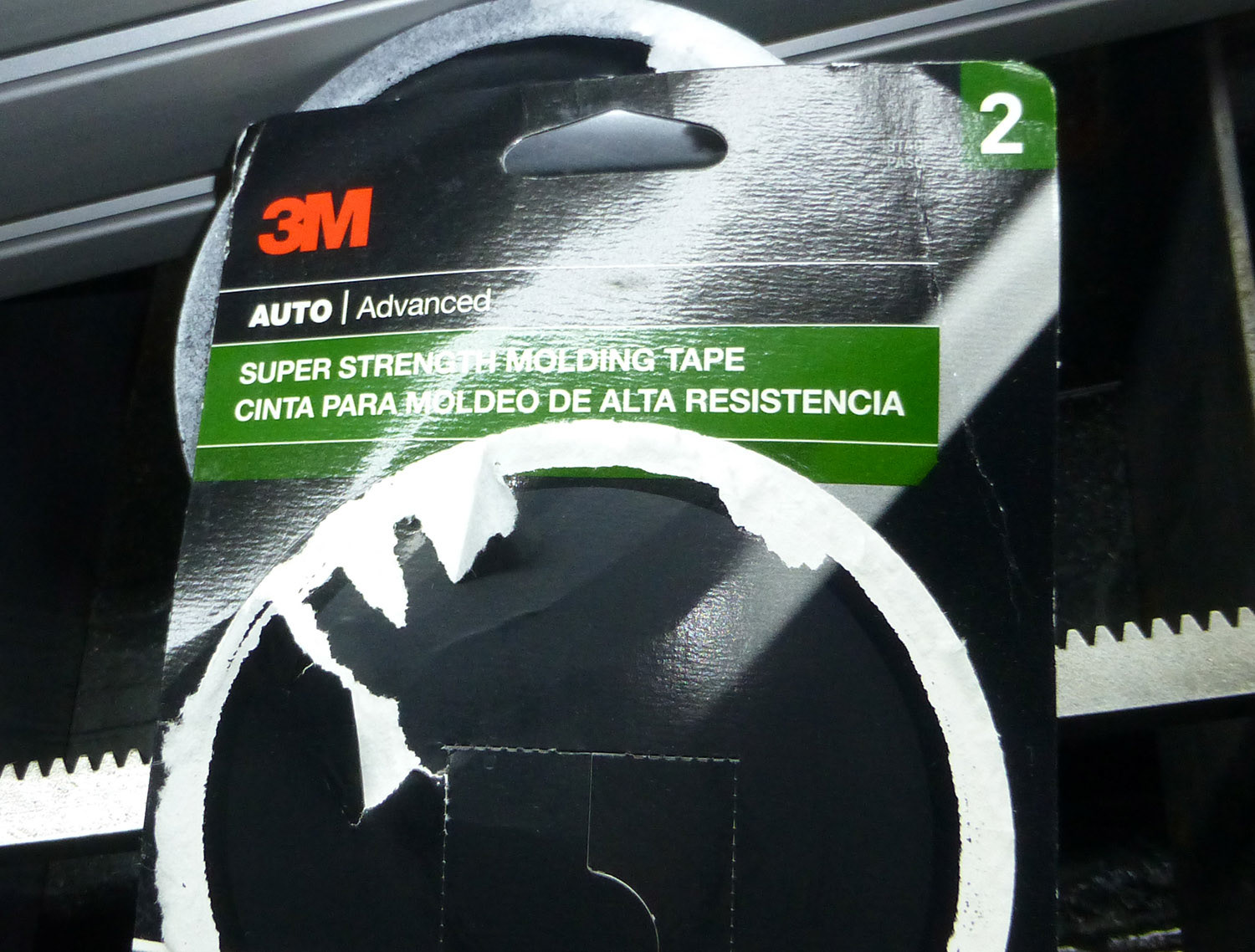
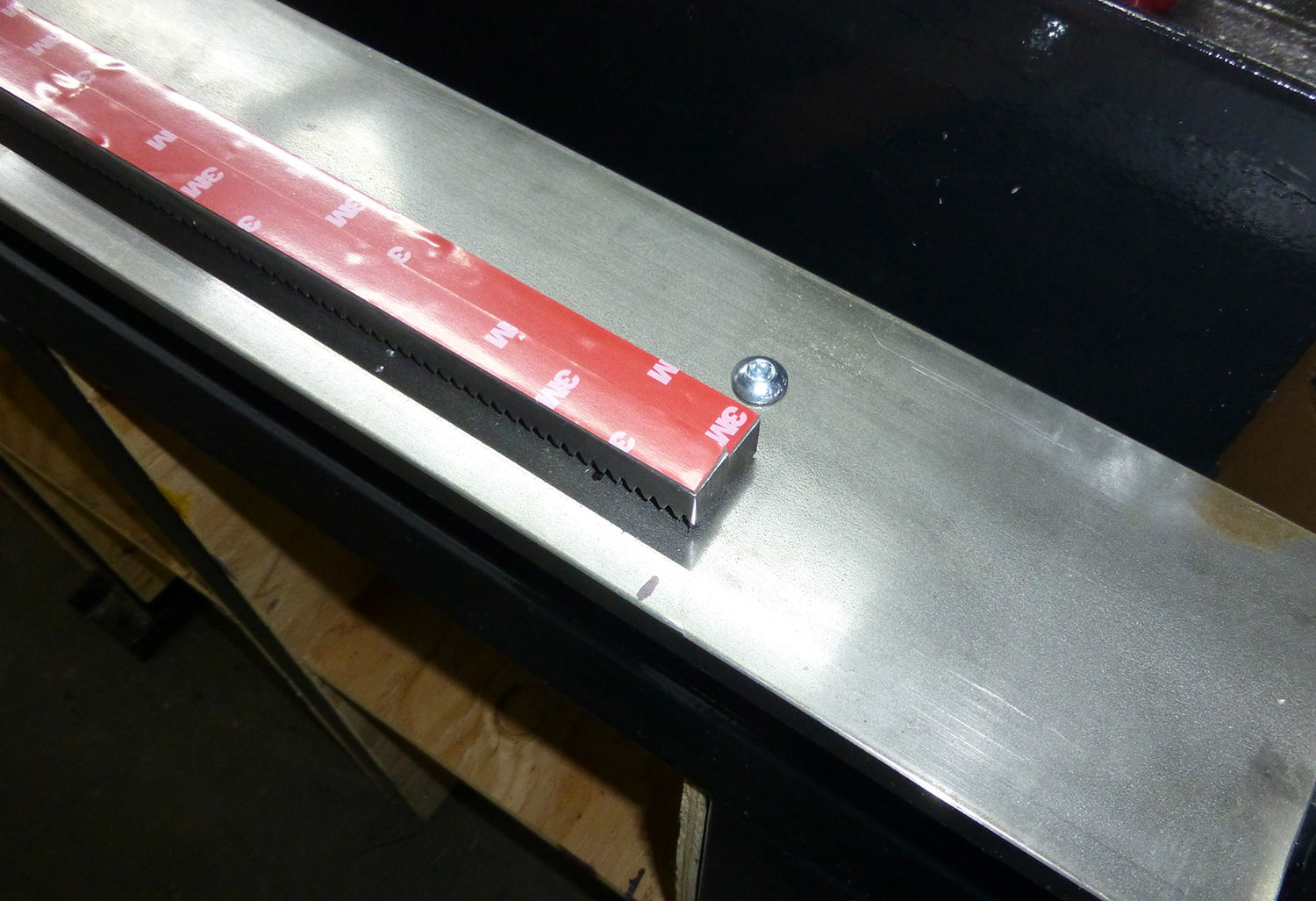
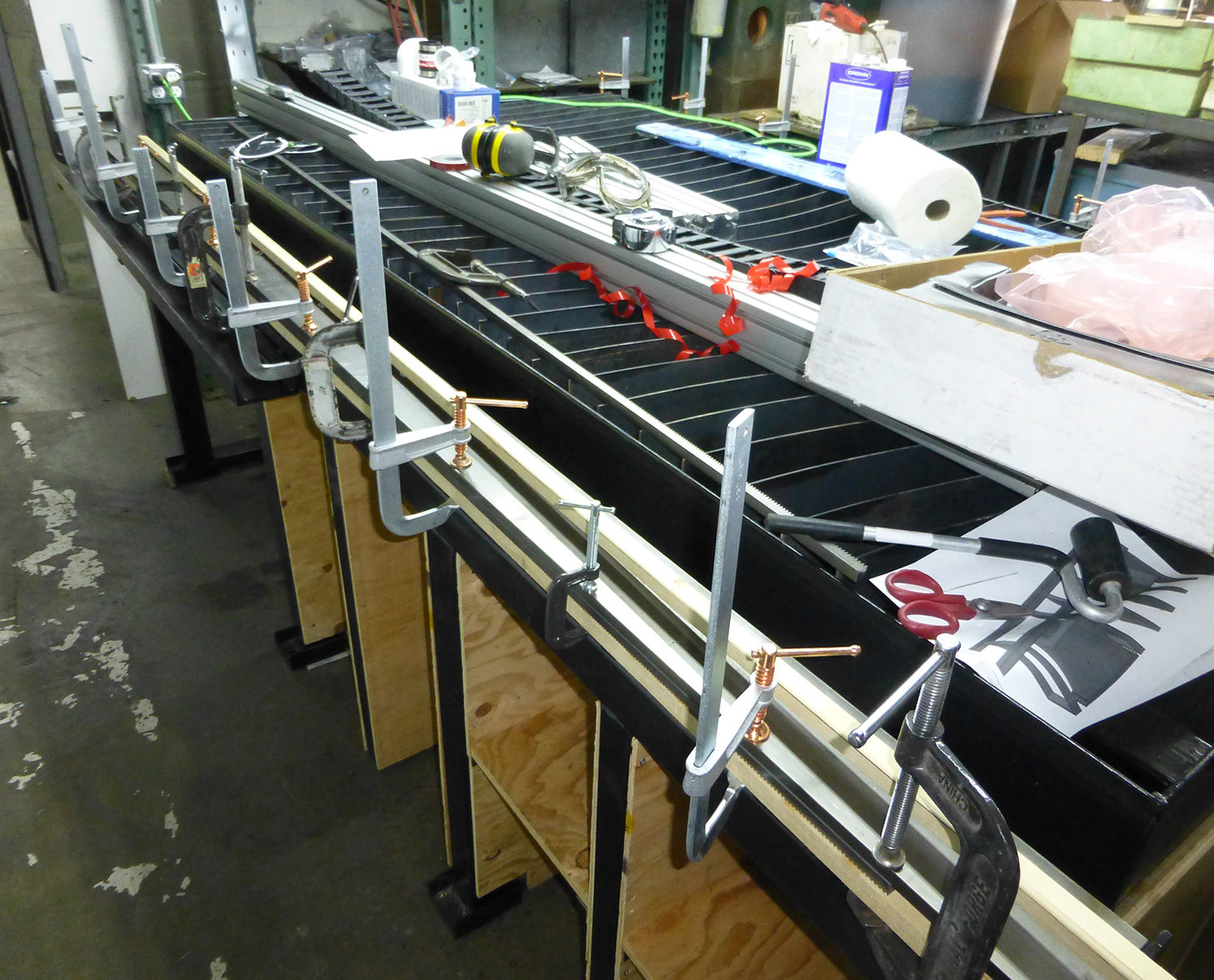
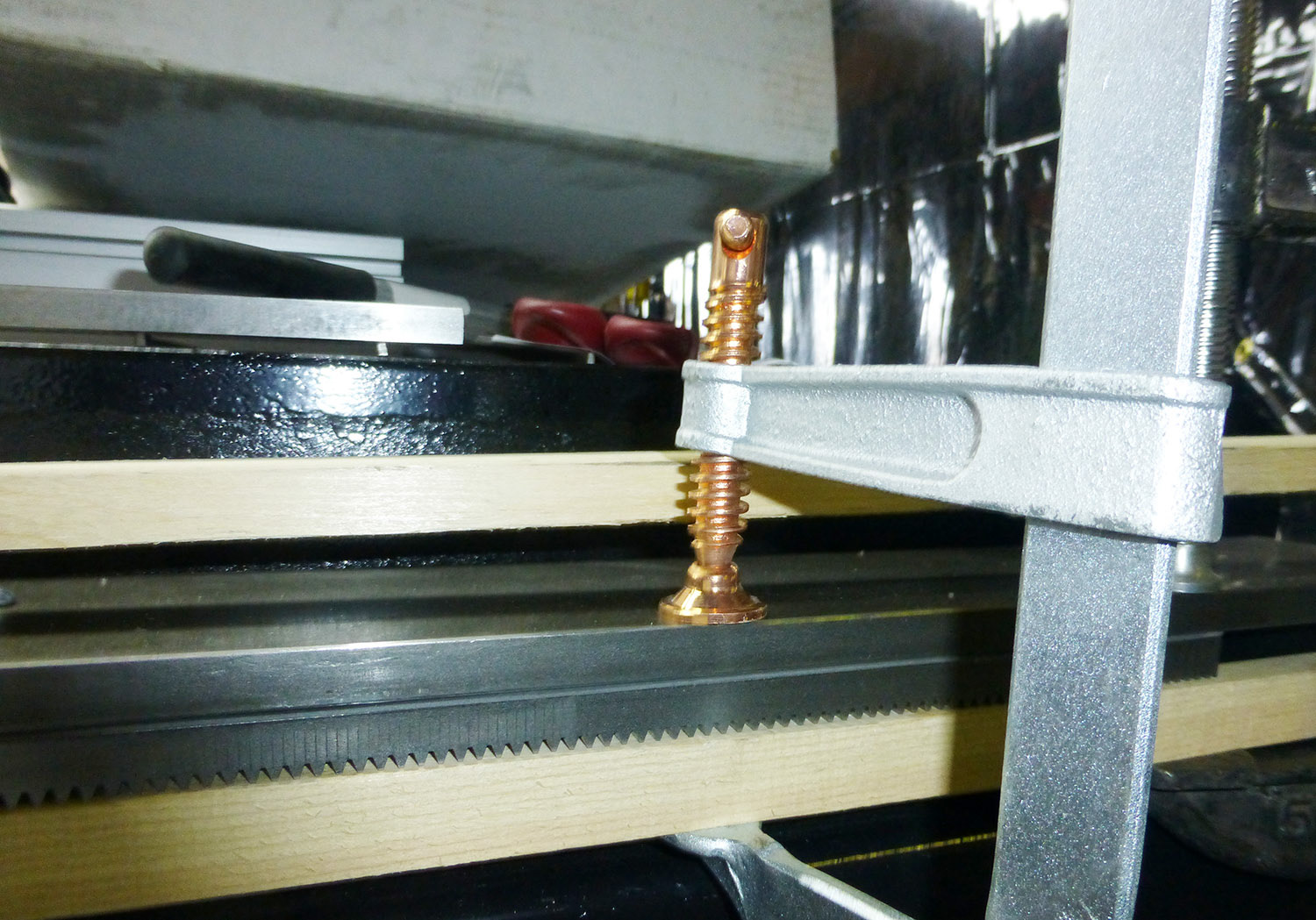
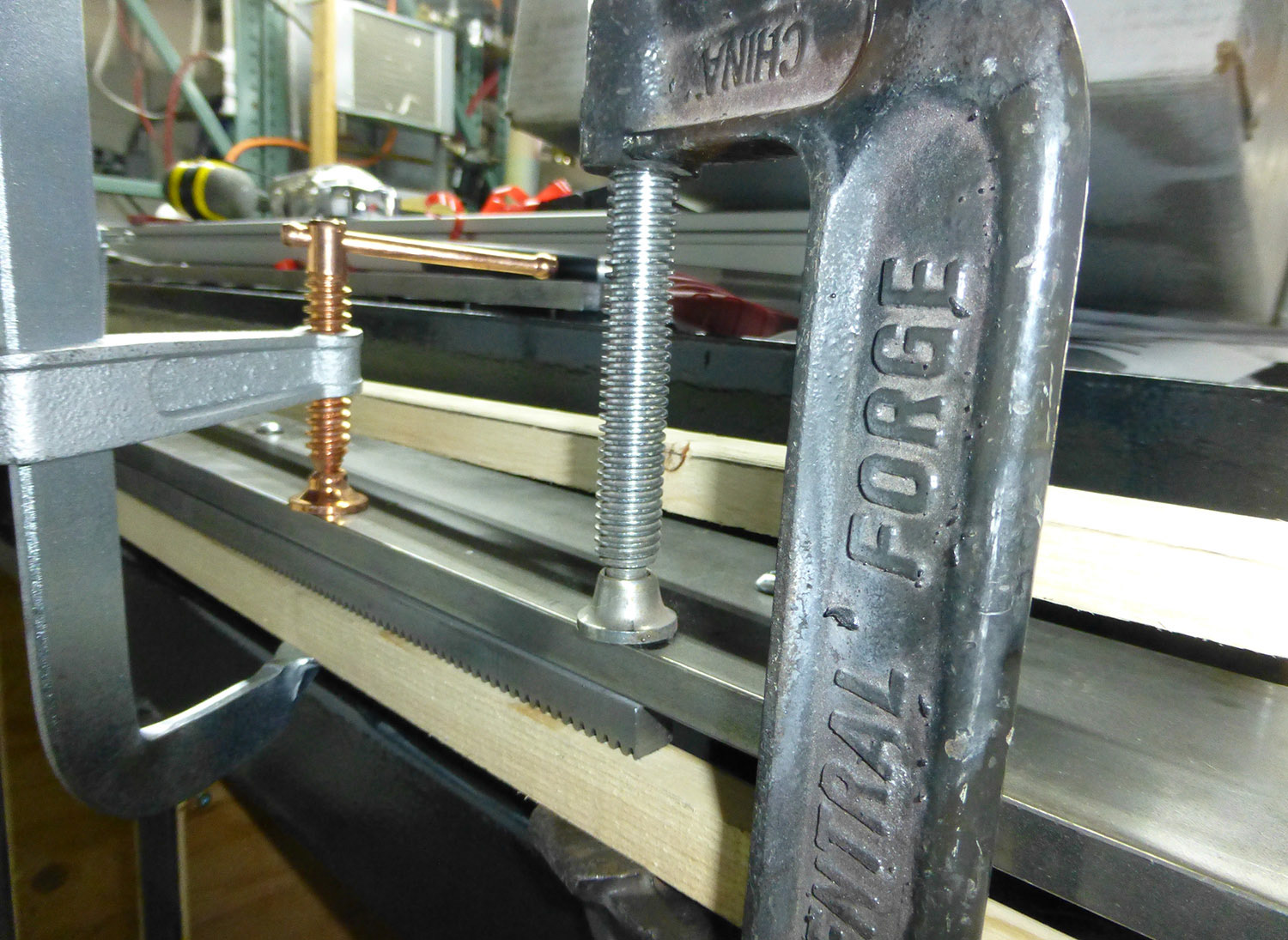
For shipping reasons, the rack that the gantry will drive on shipped in 2 pieces. Here, I weld the rack together and attach it to the plasma table with double-sided 3M tape.
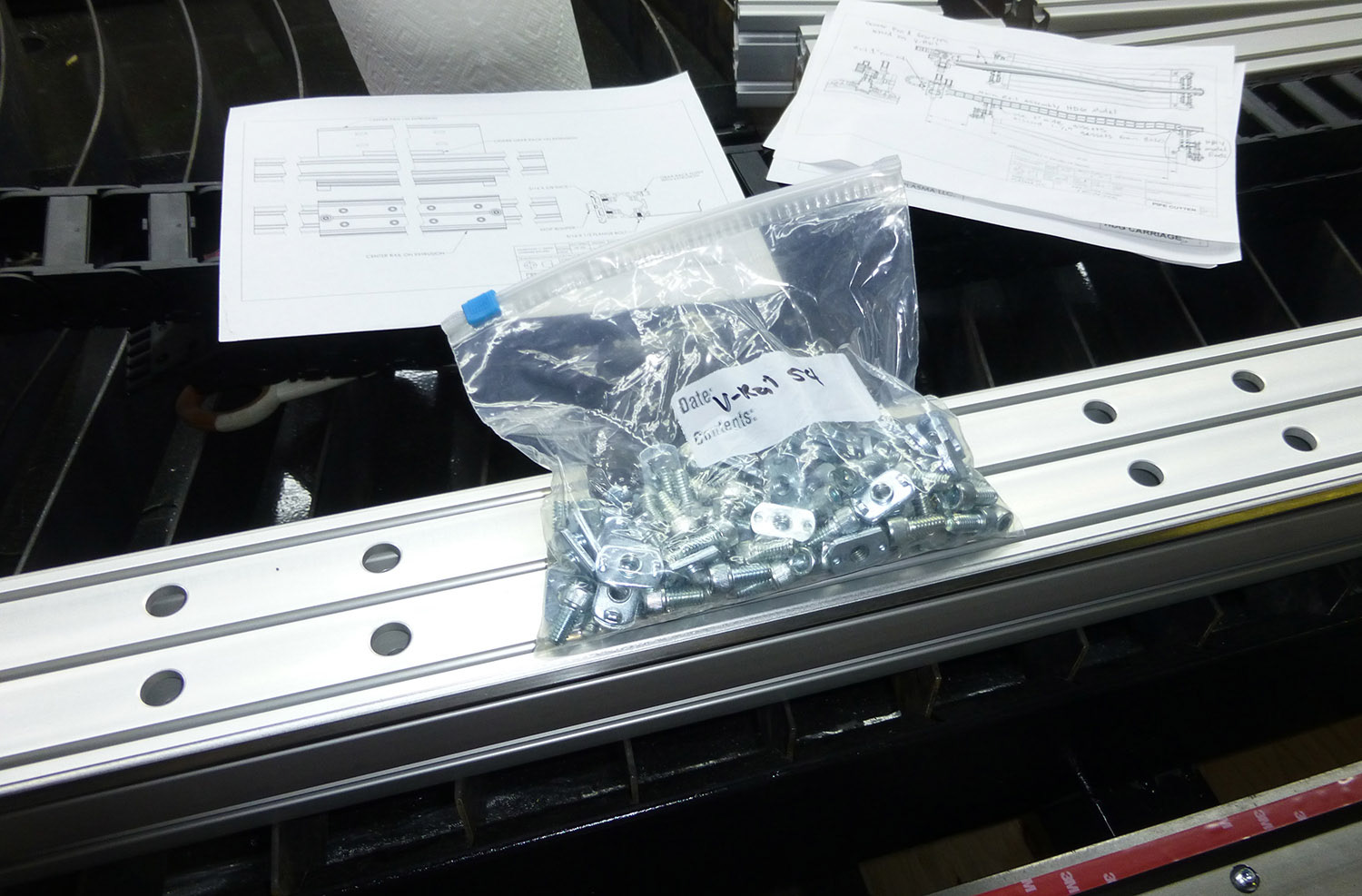
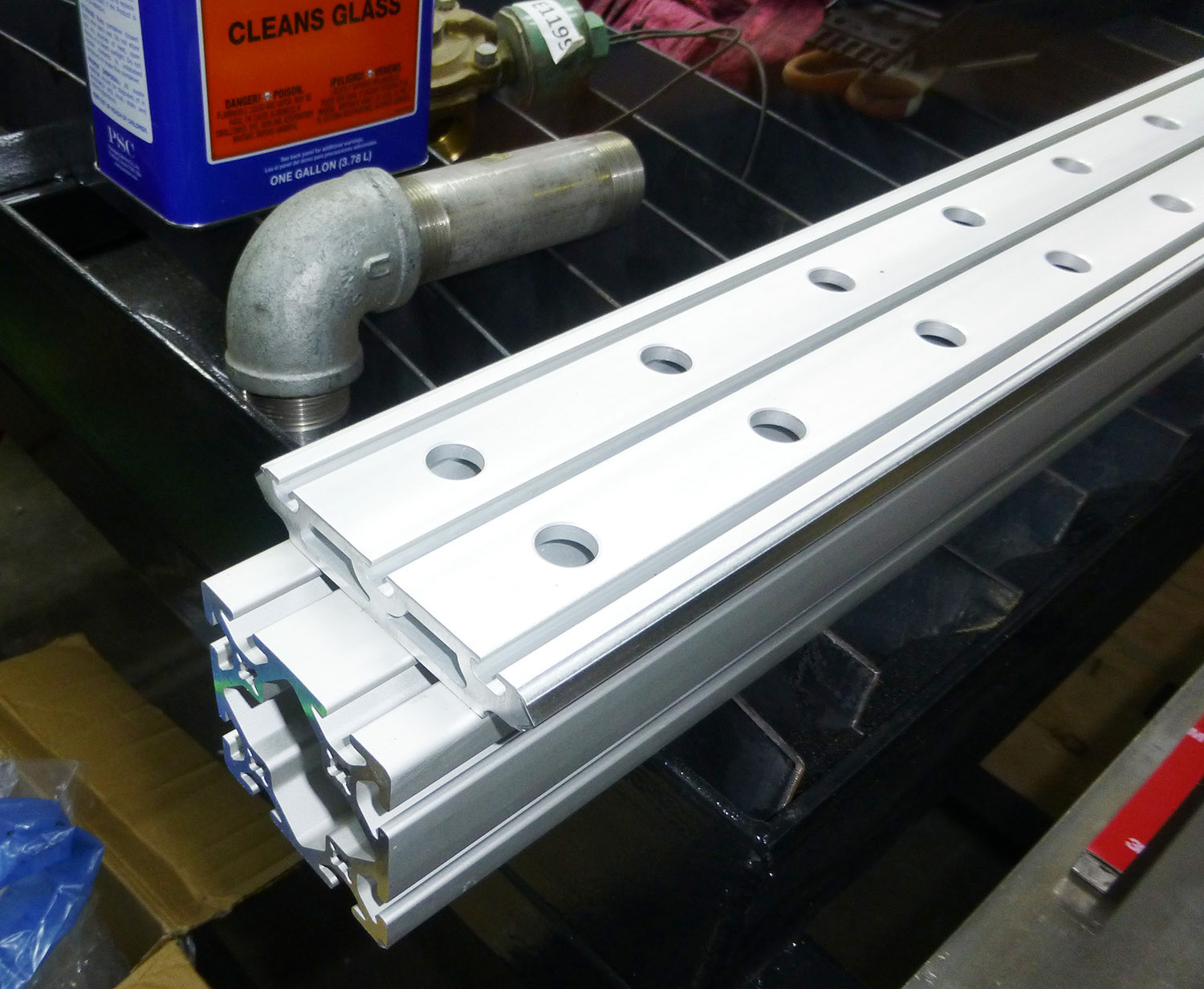
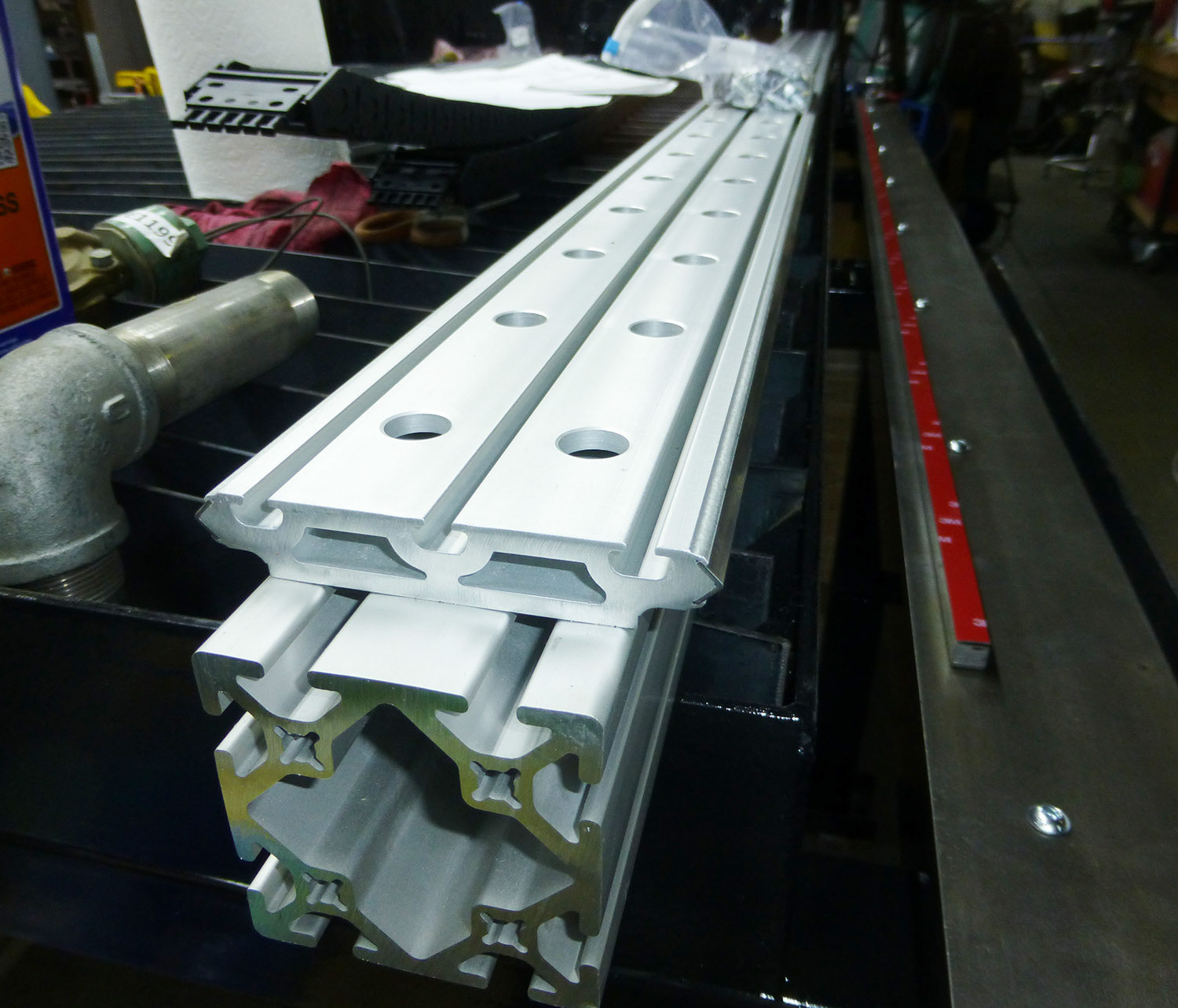
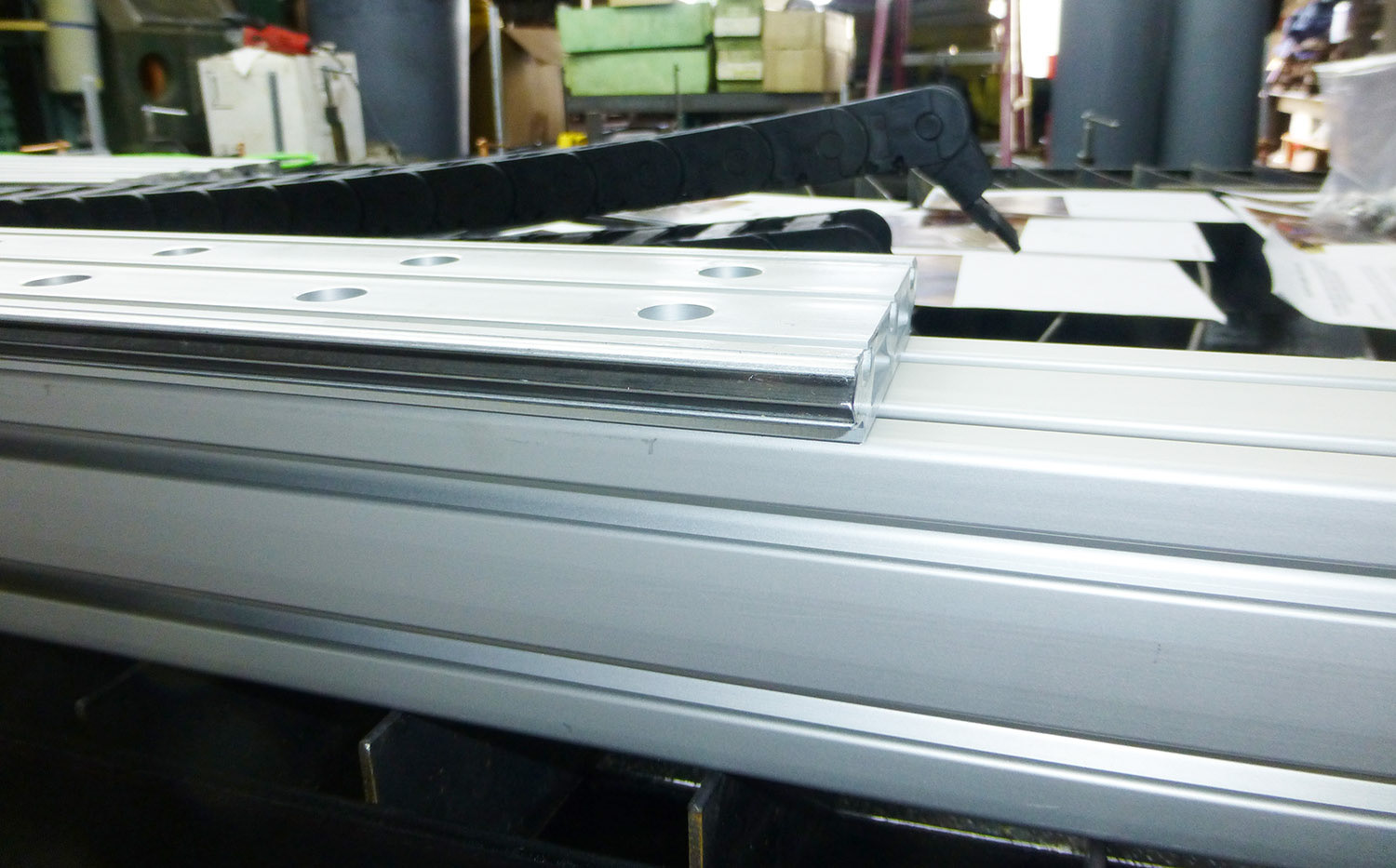
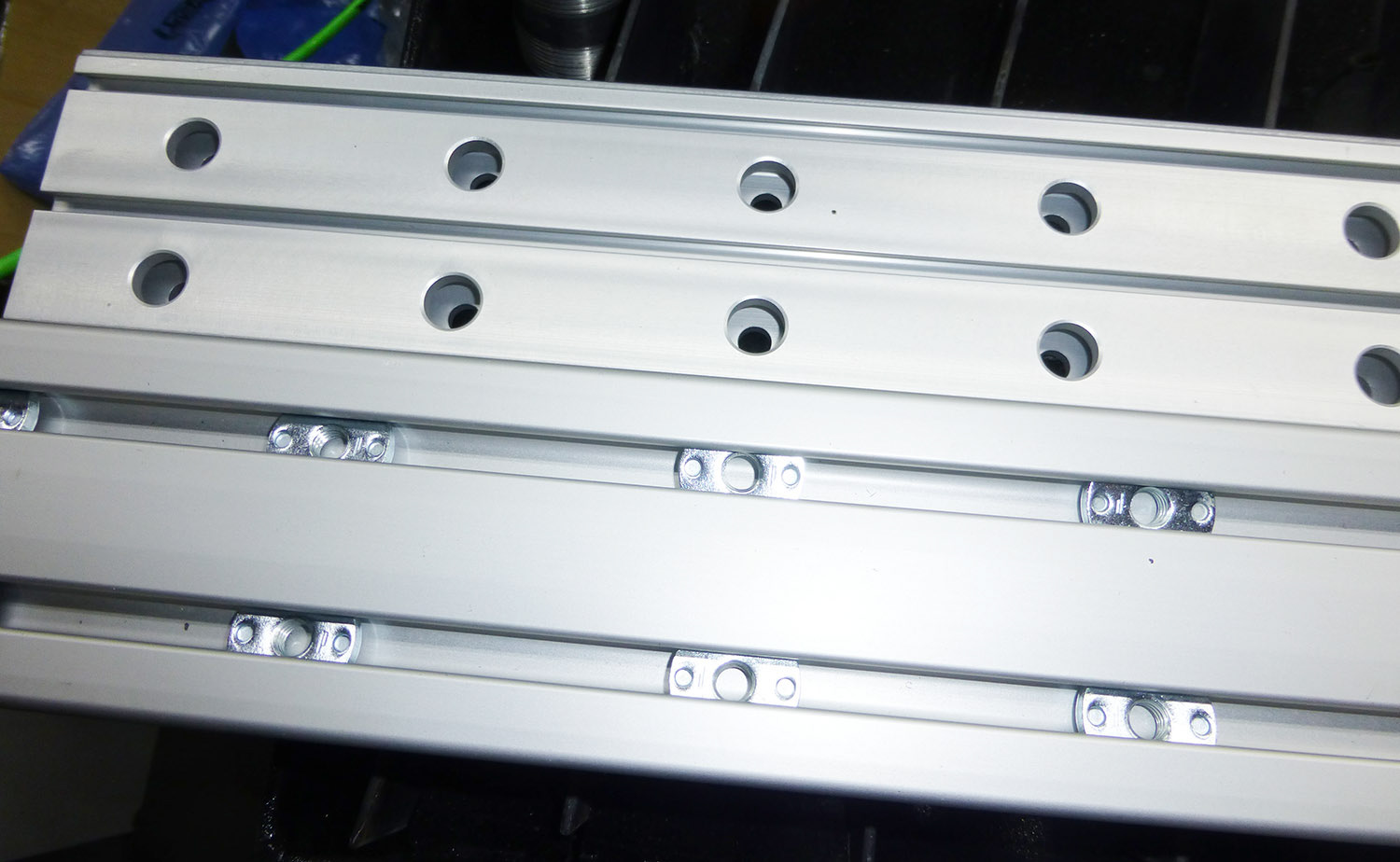
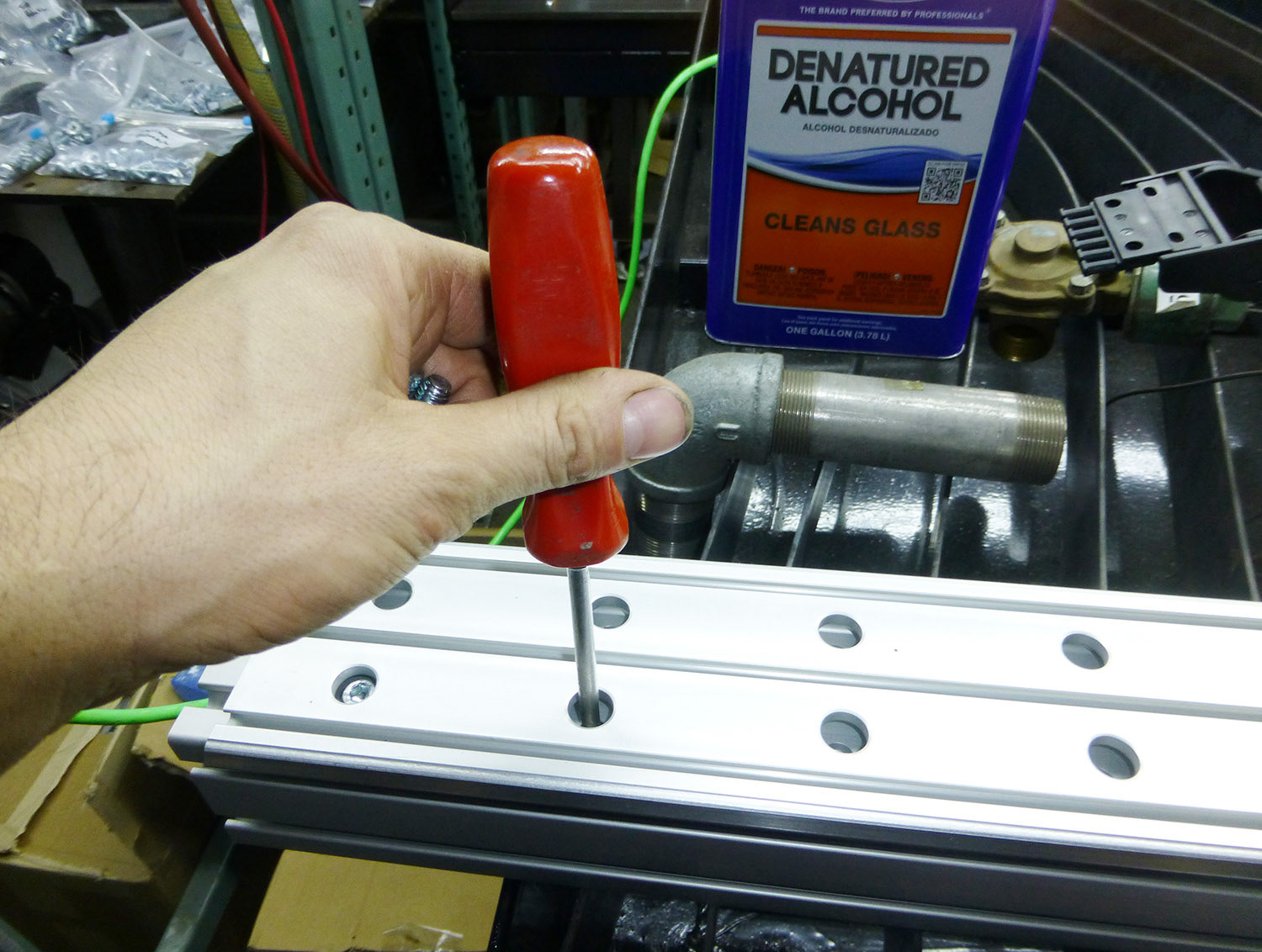
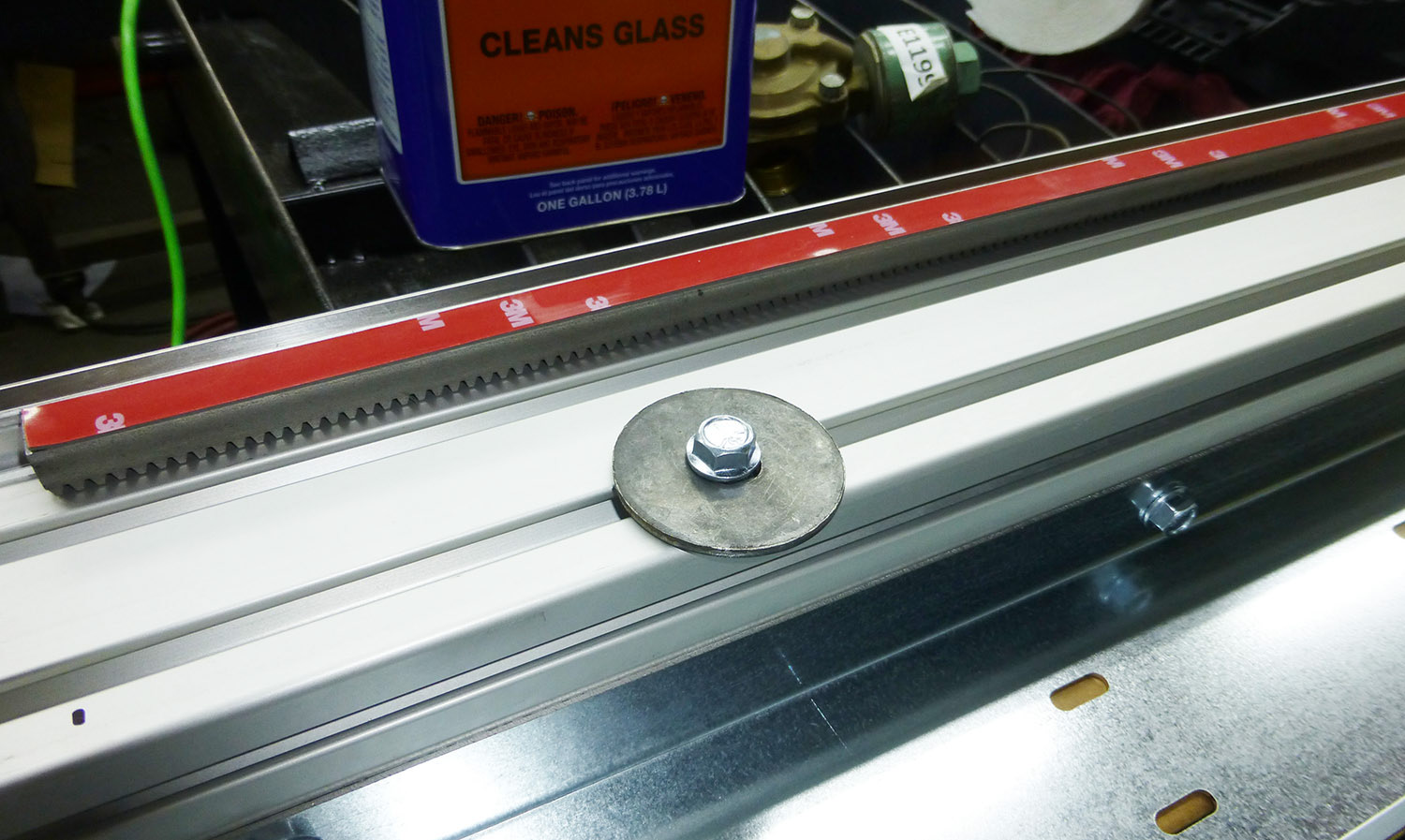
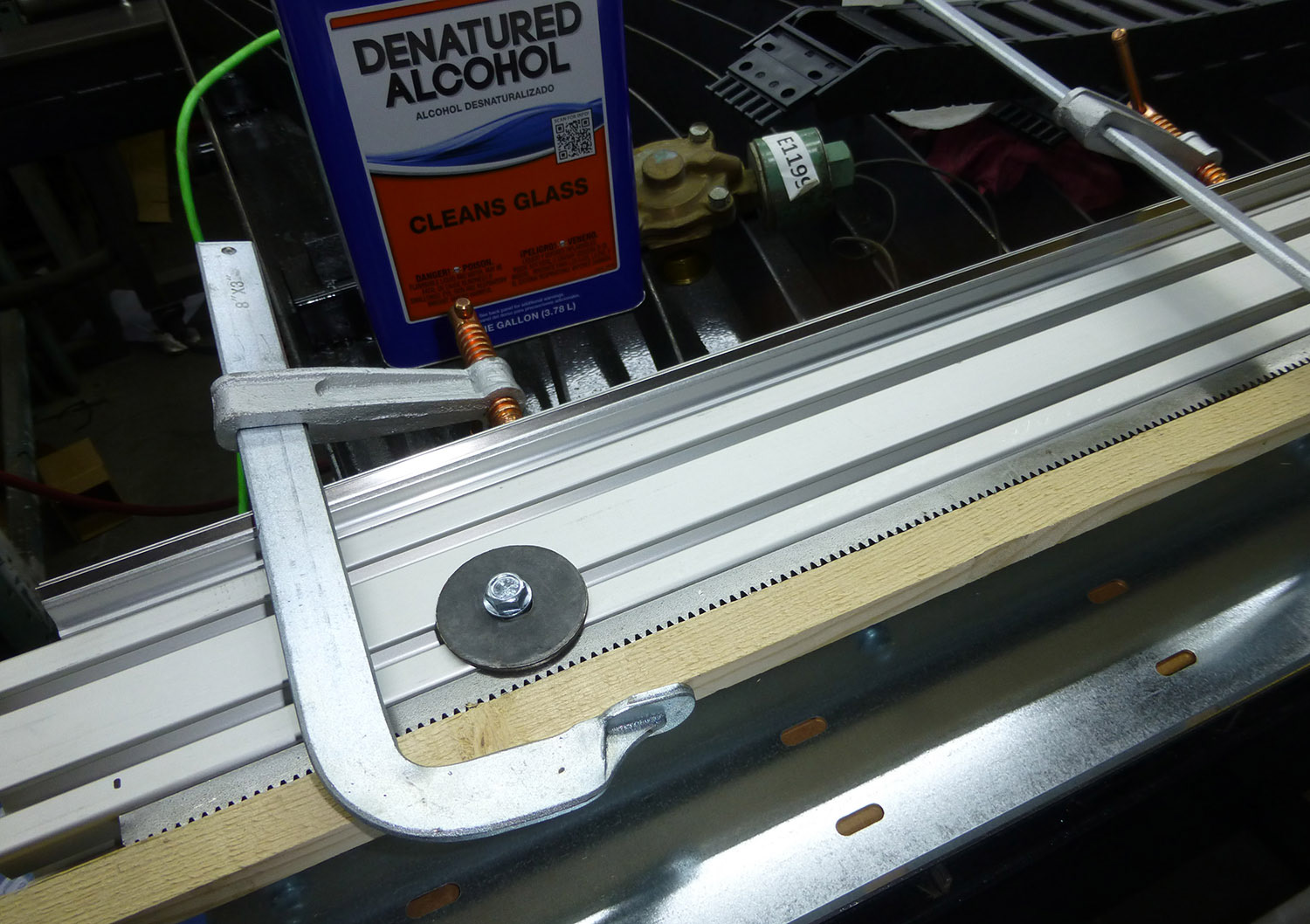
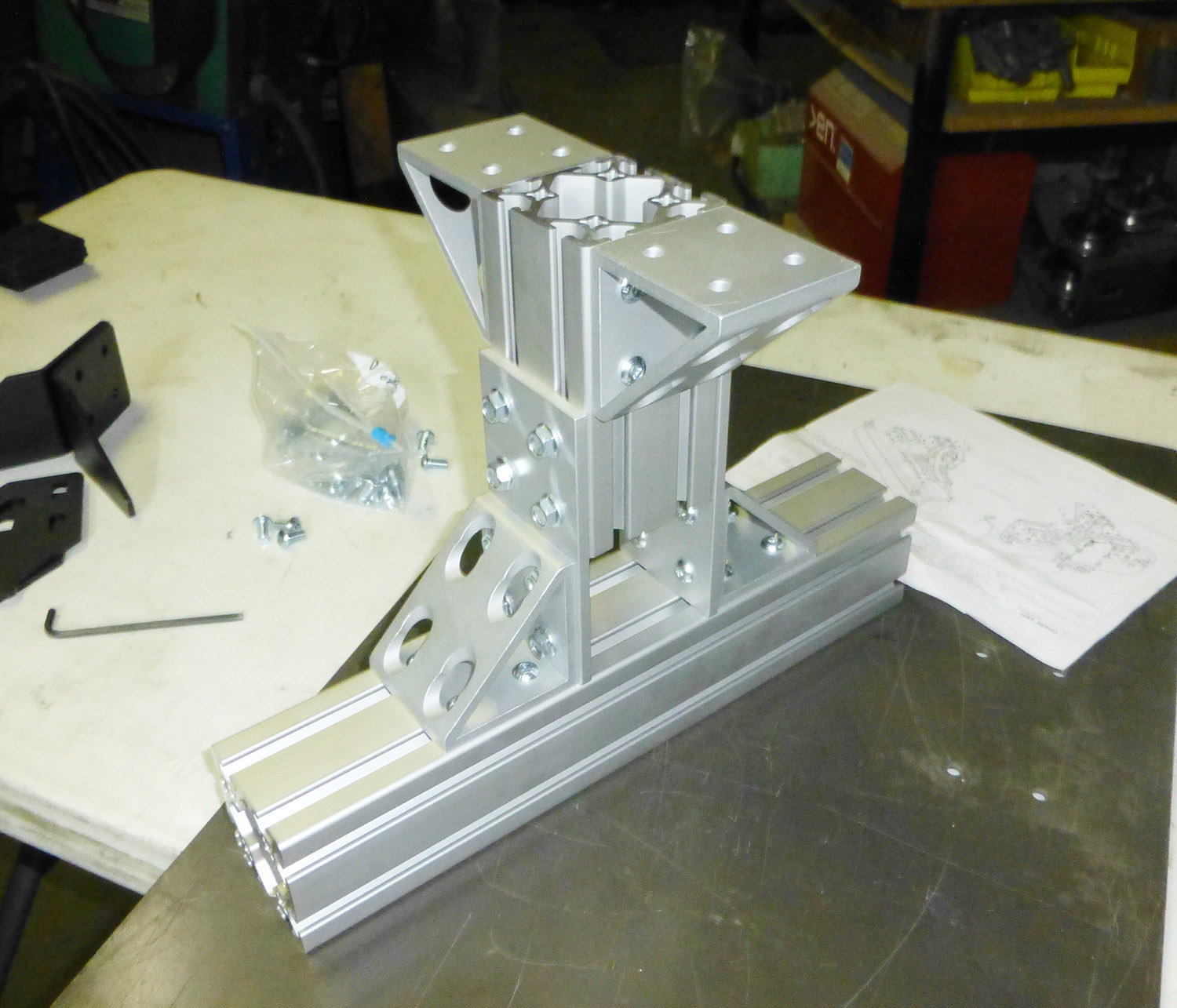
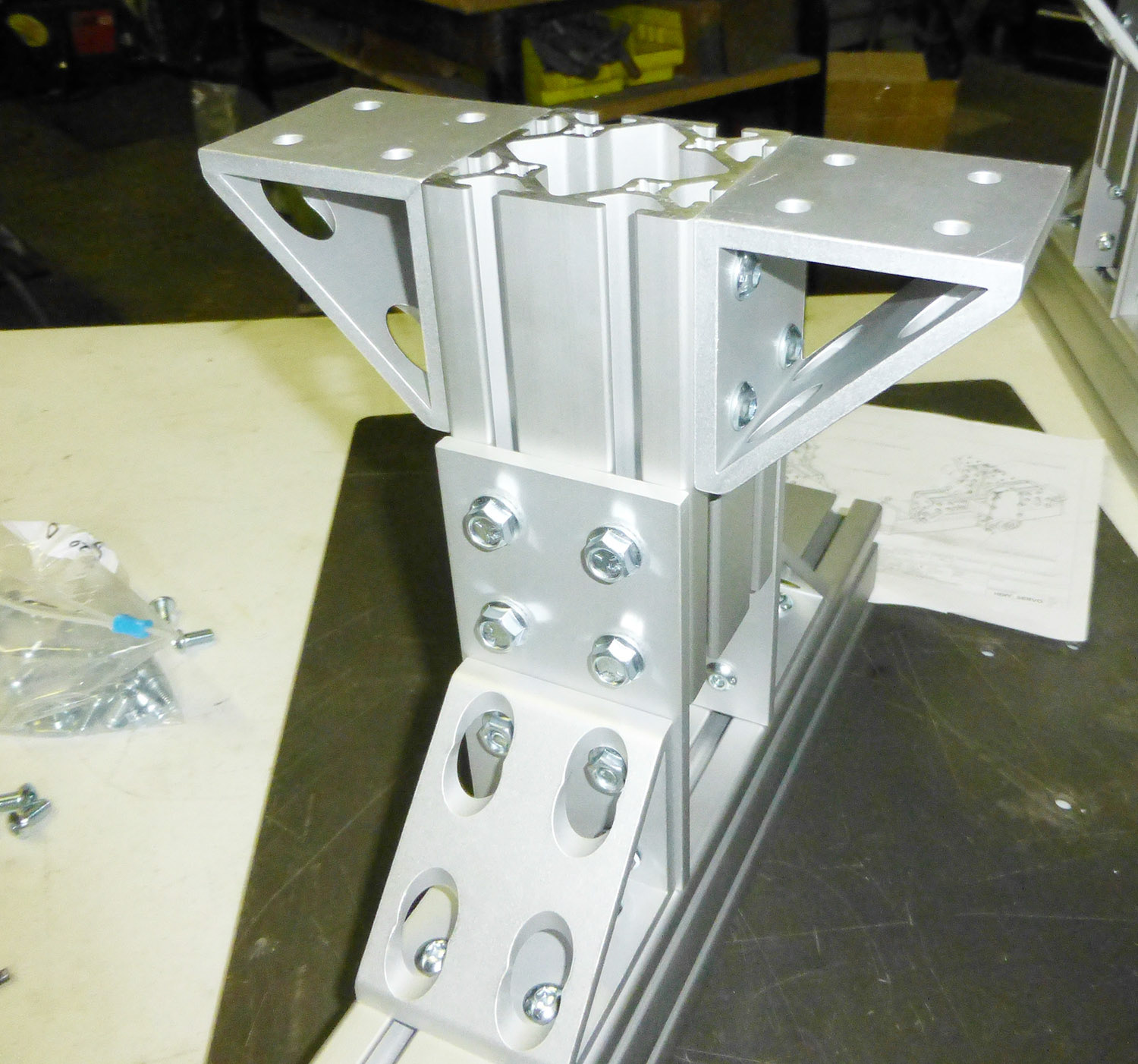
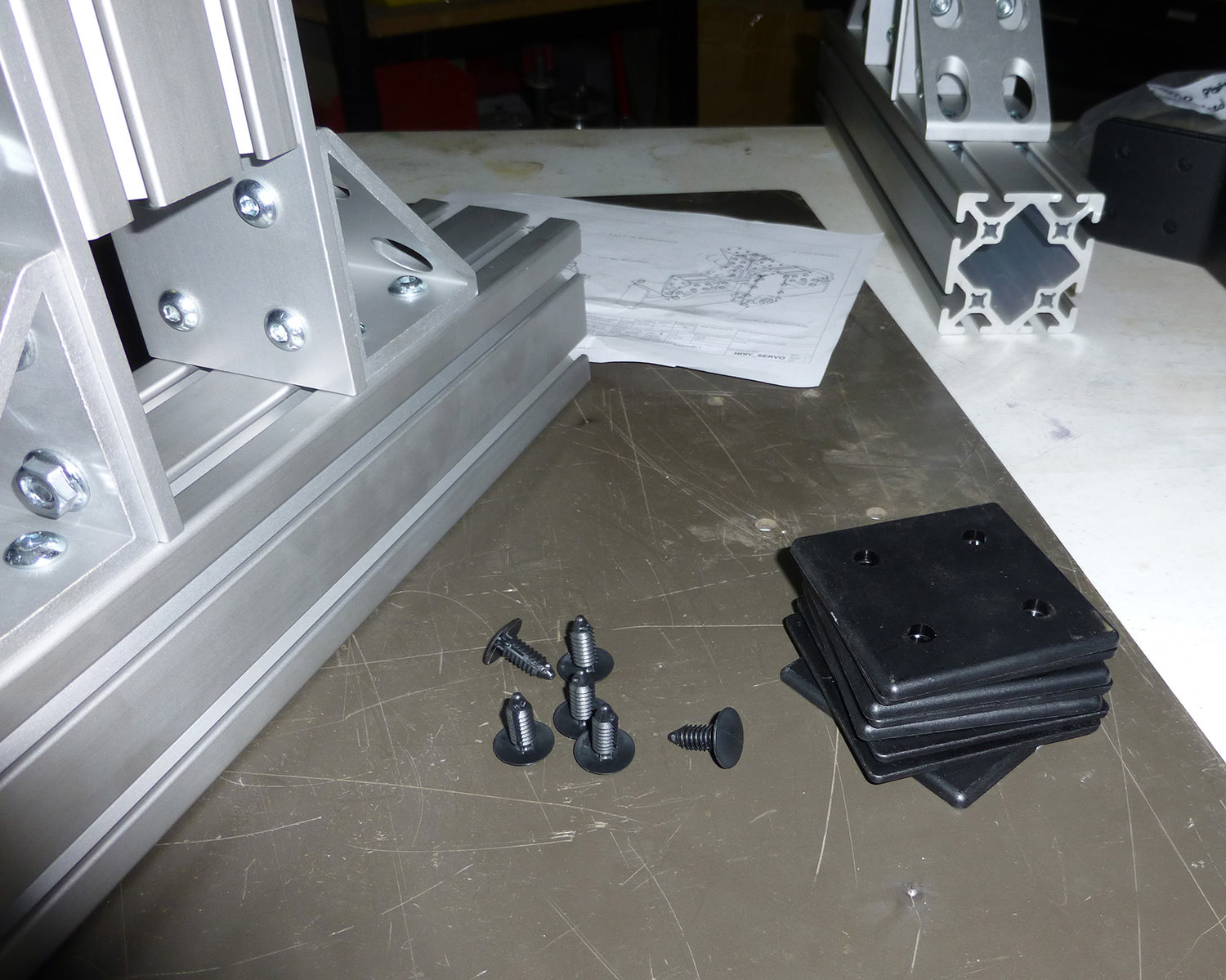
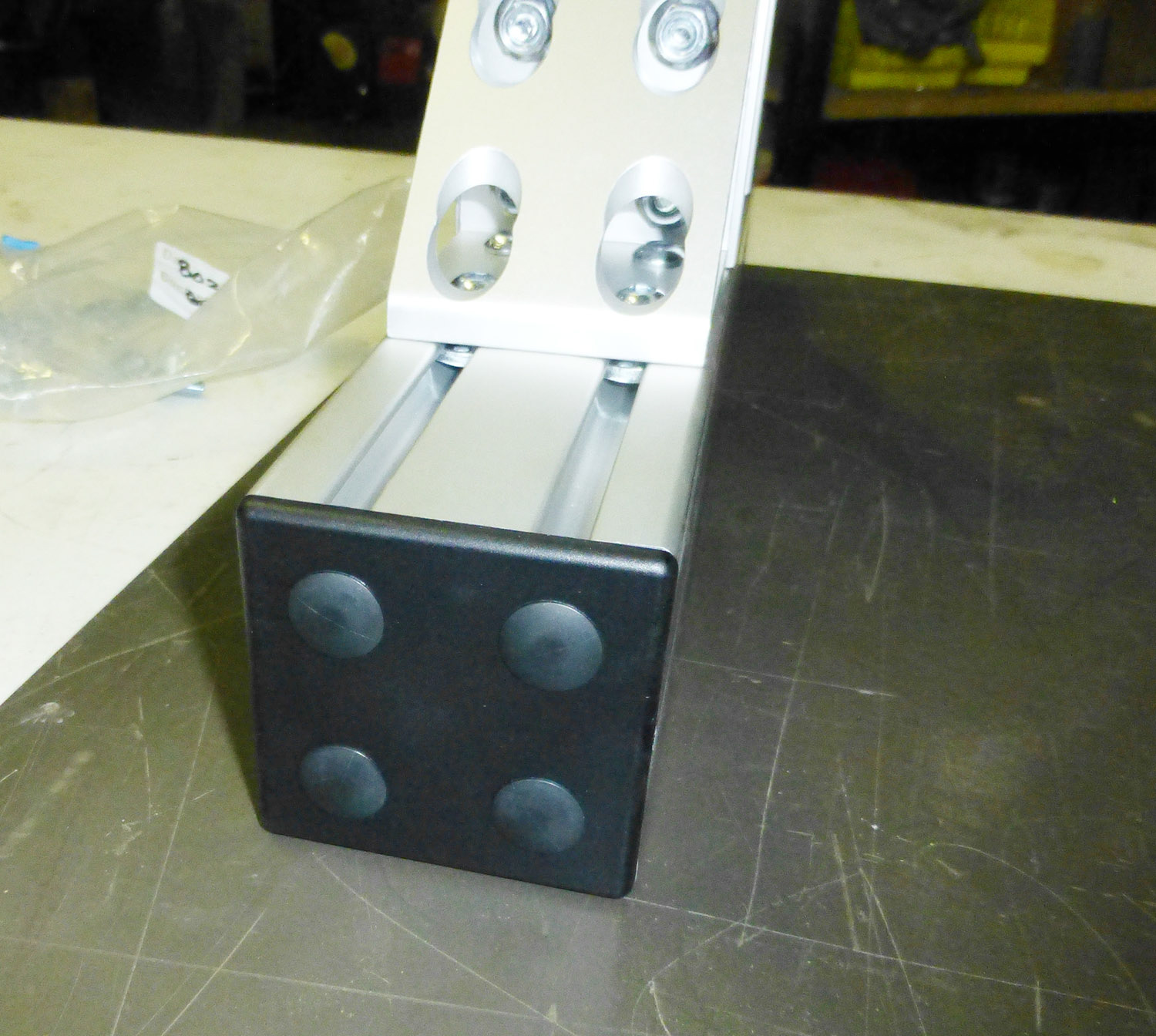
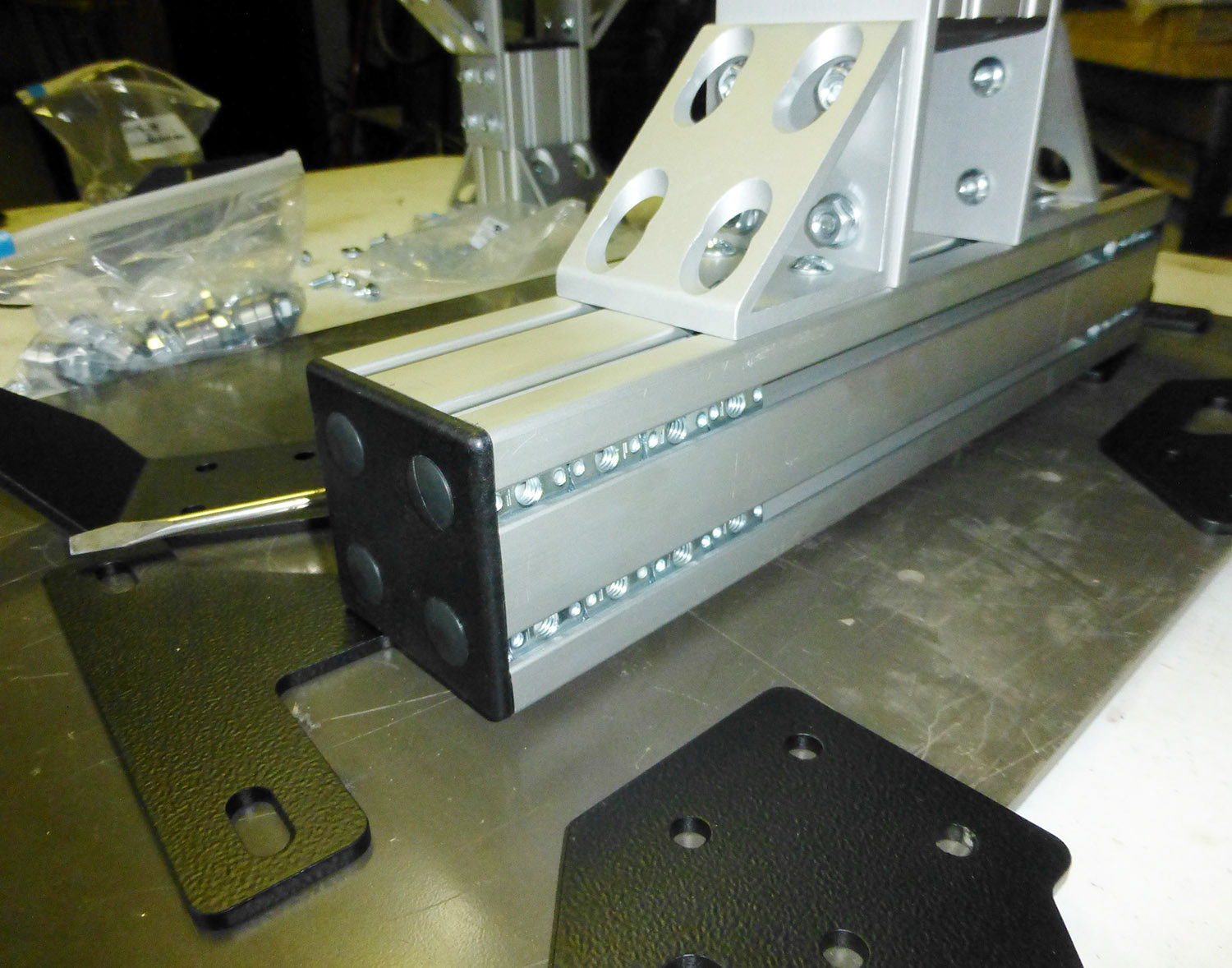
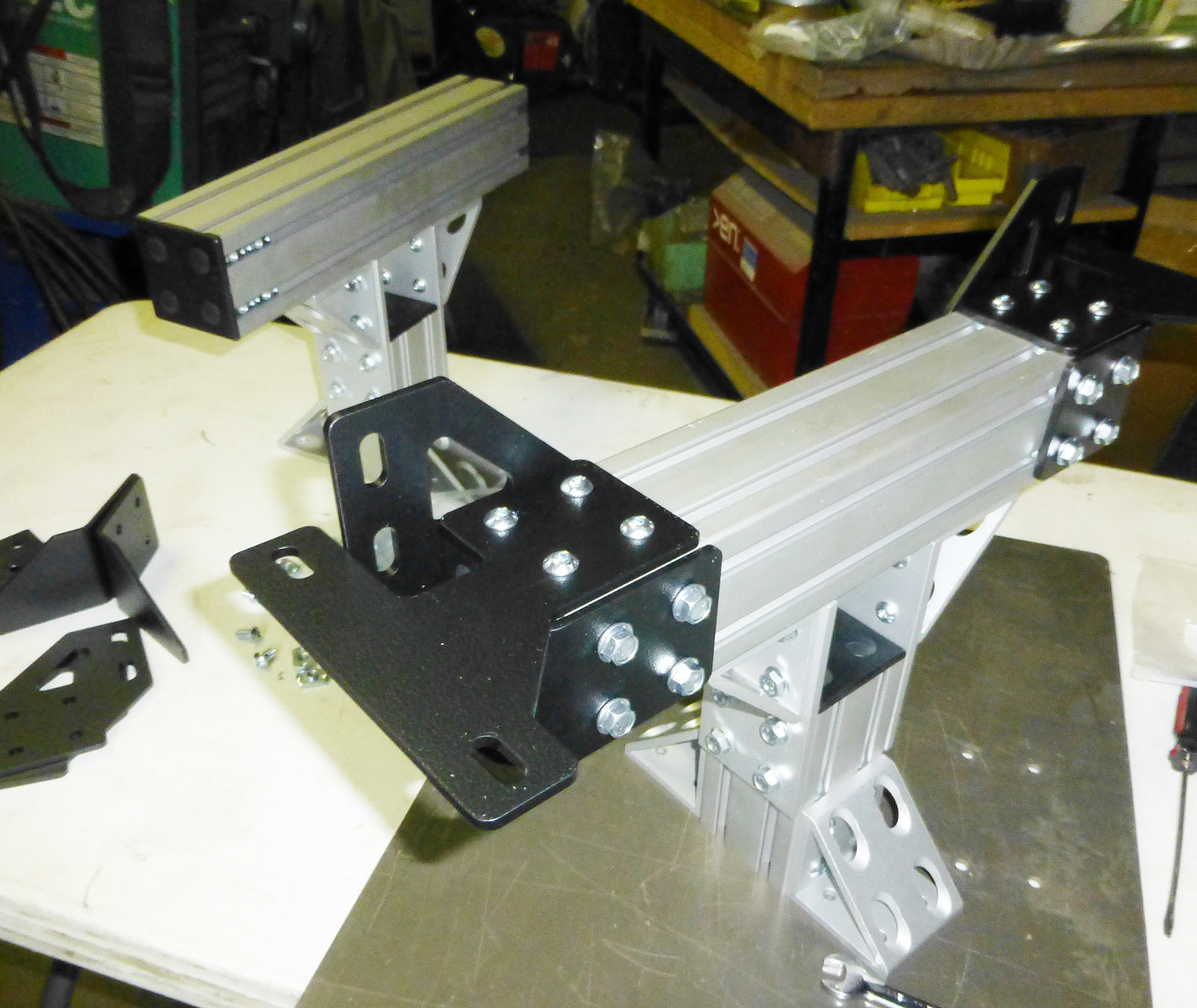
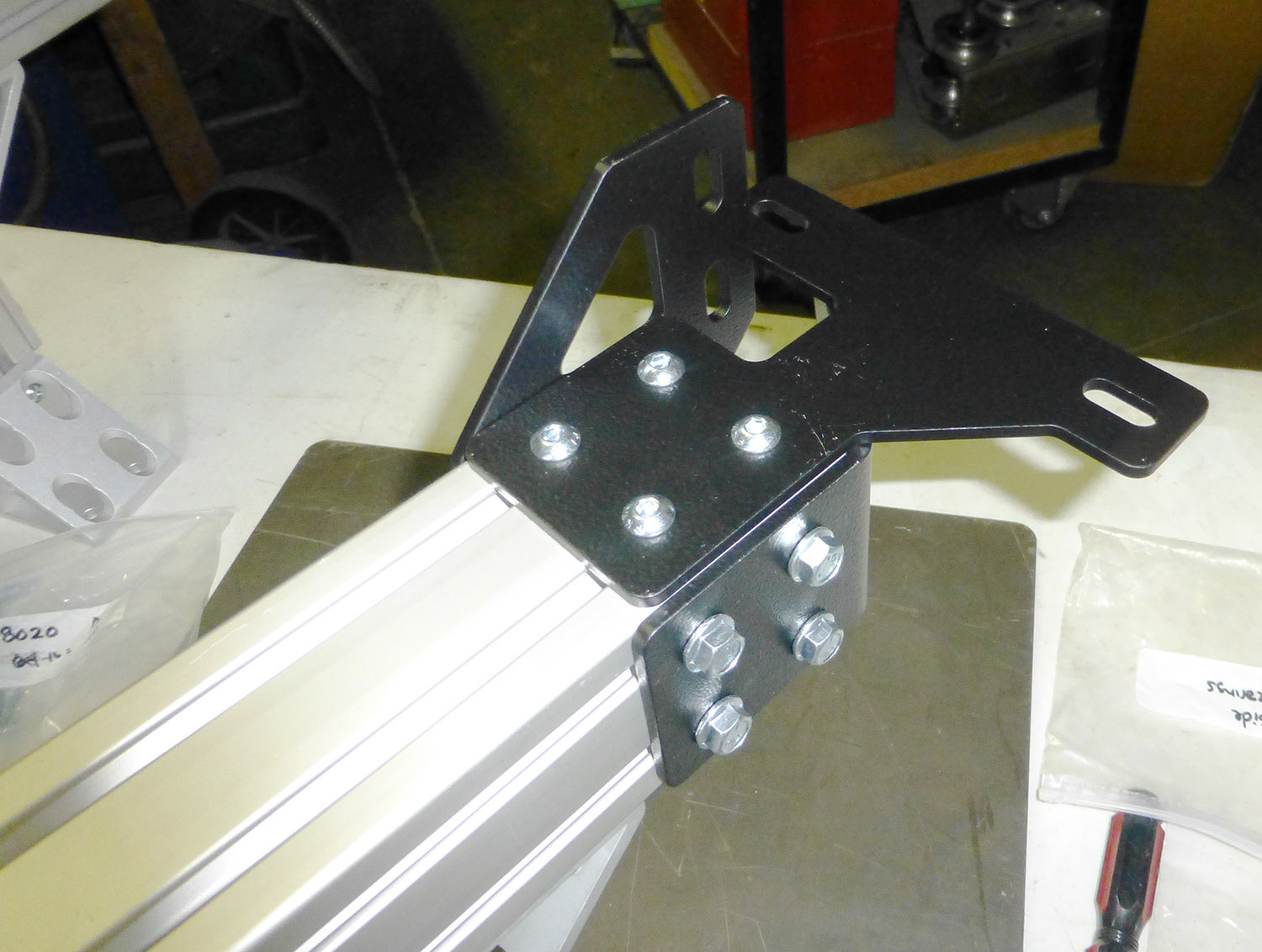
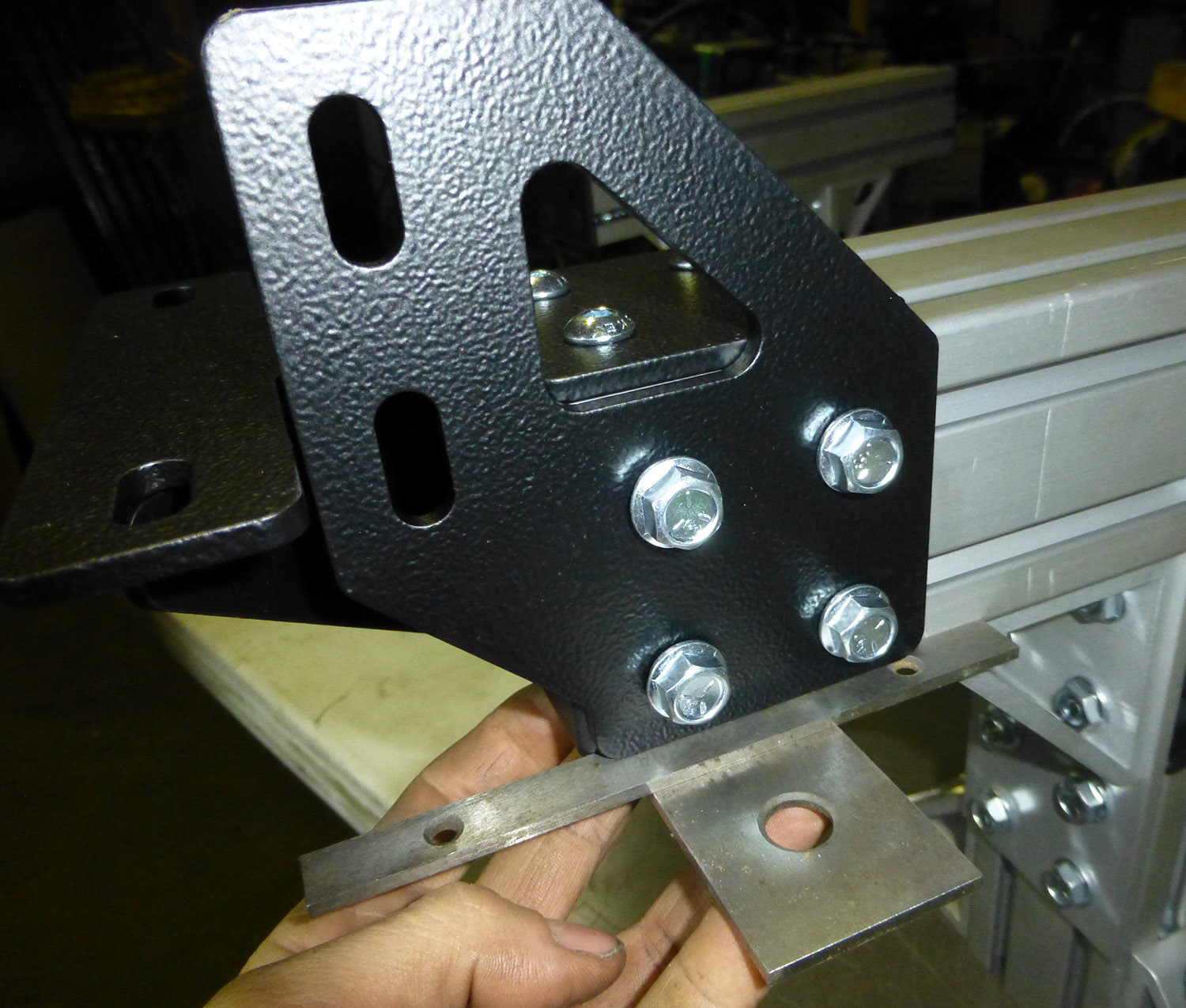
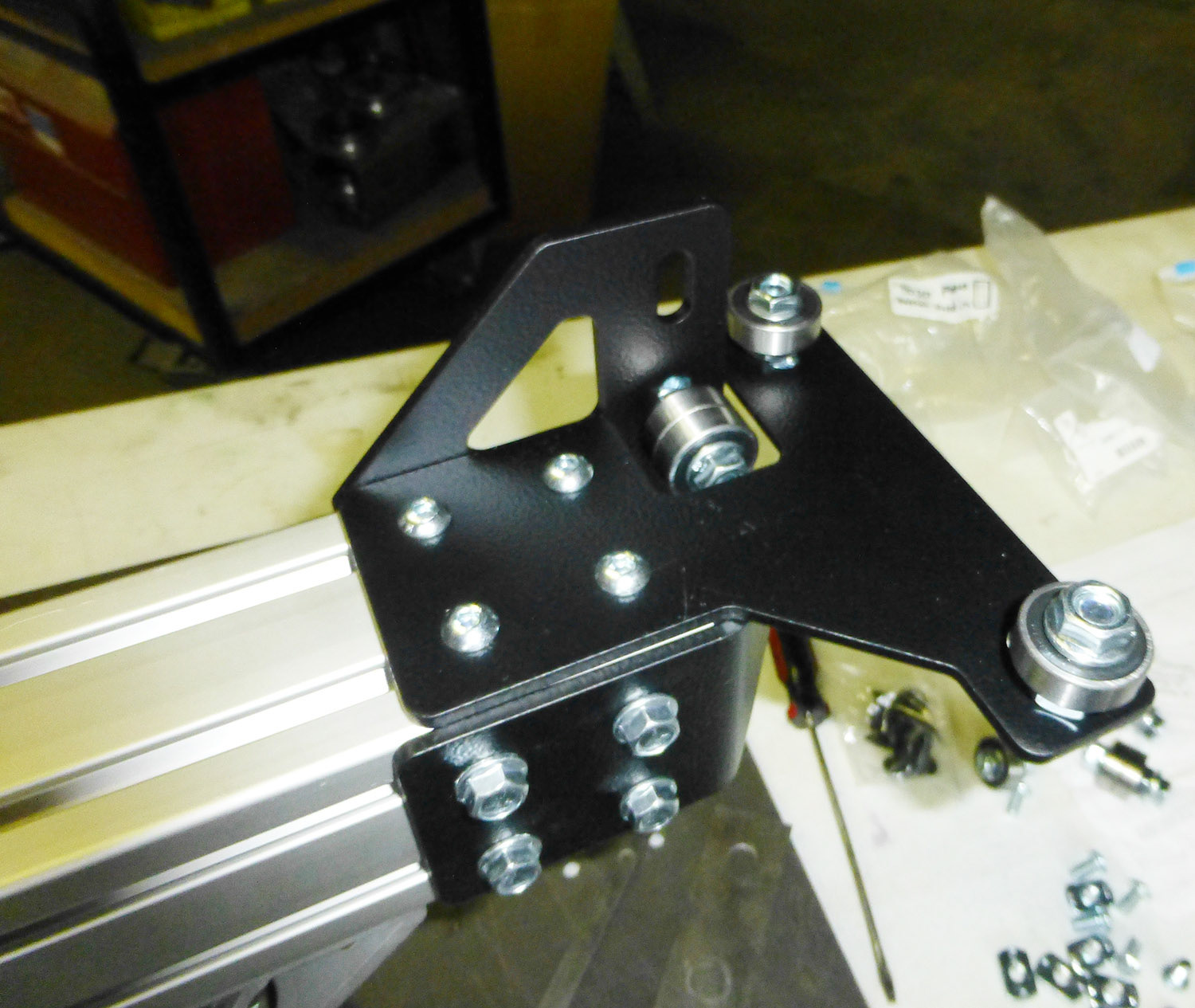
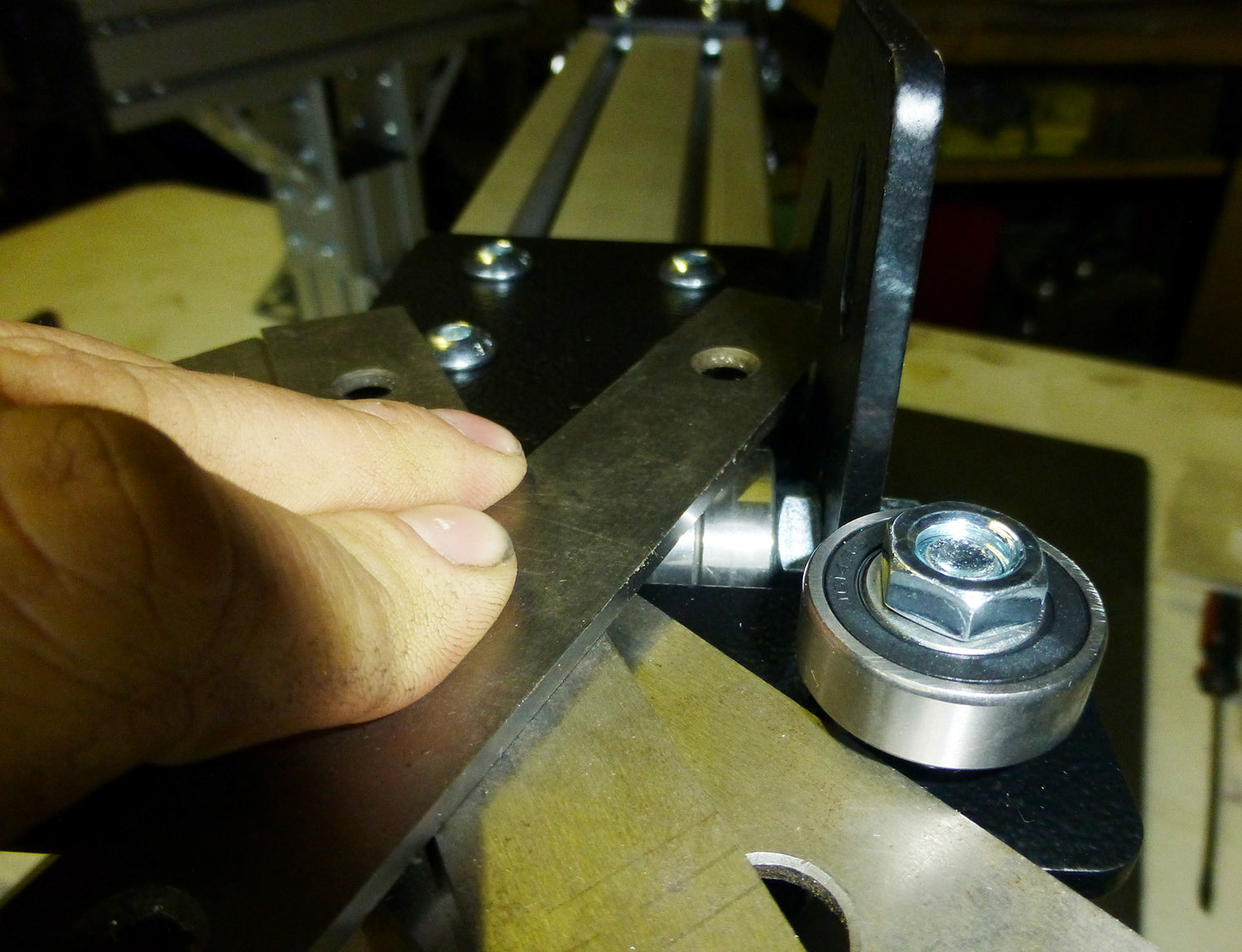
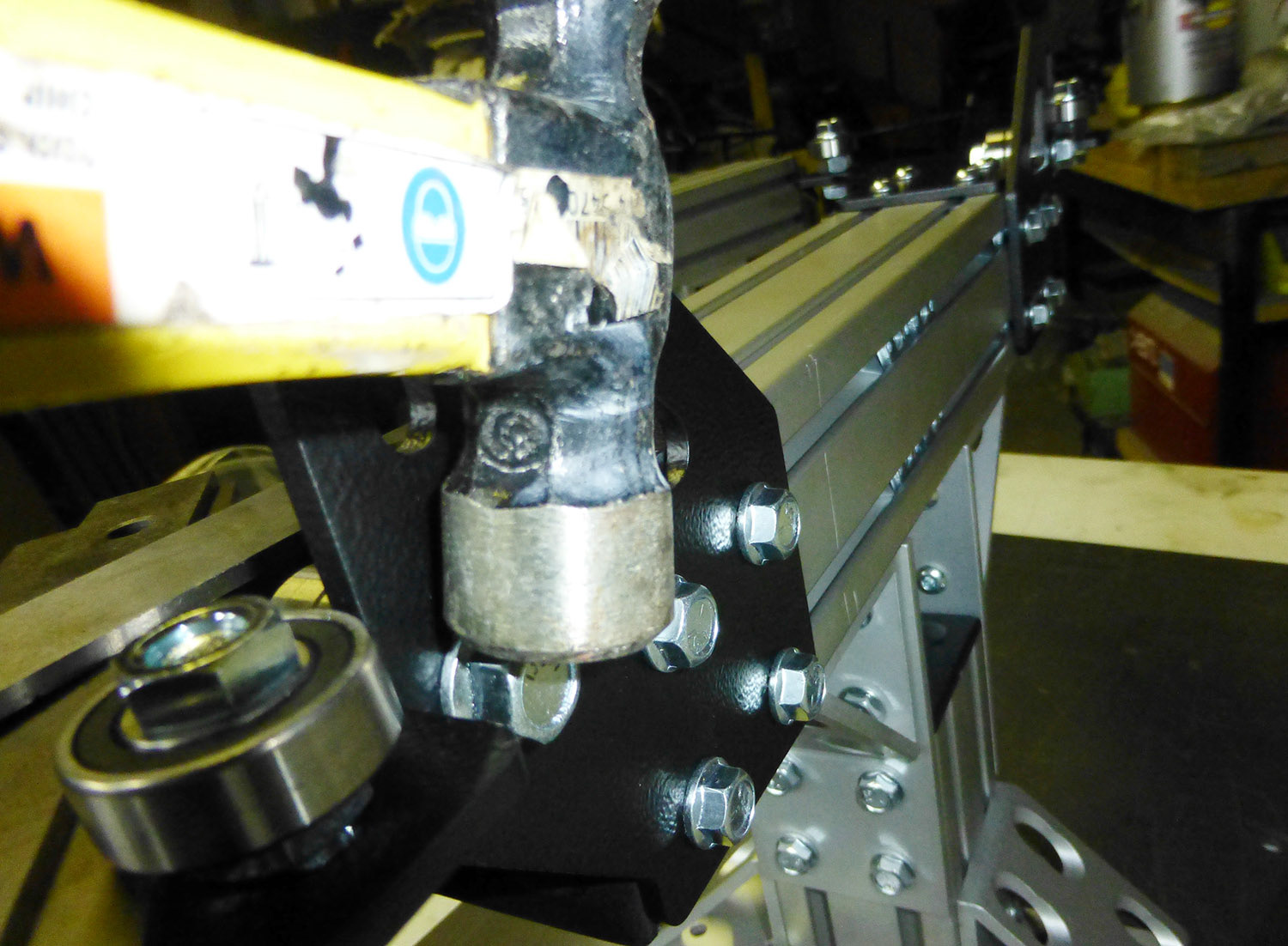
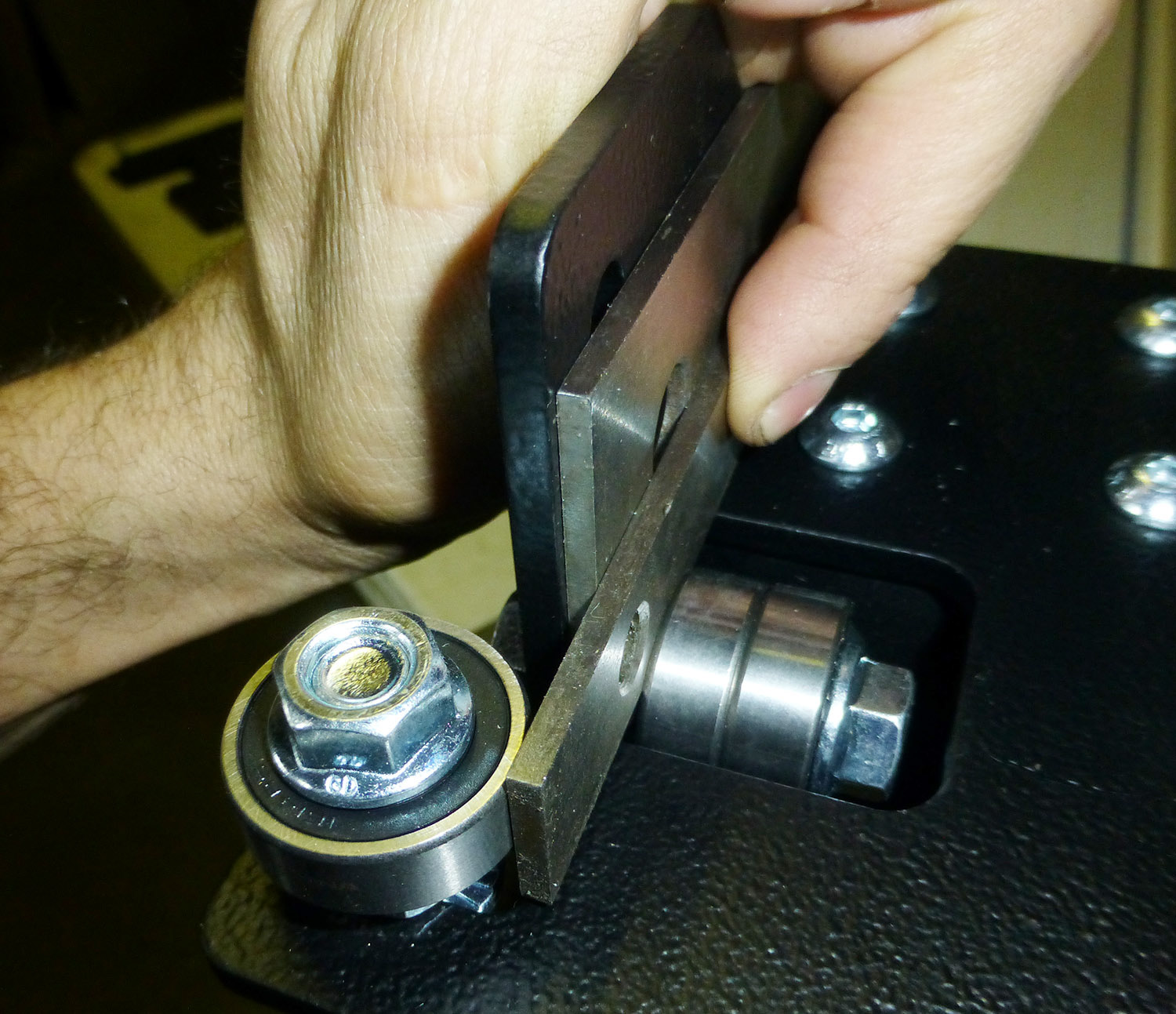
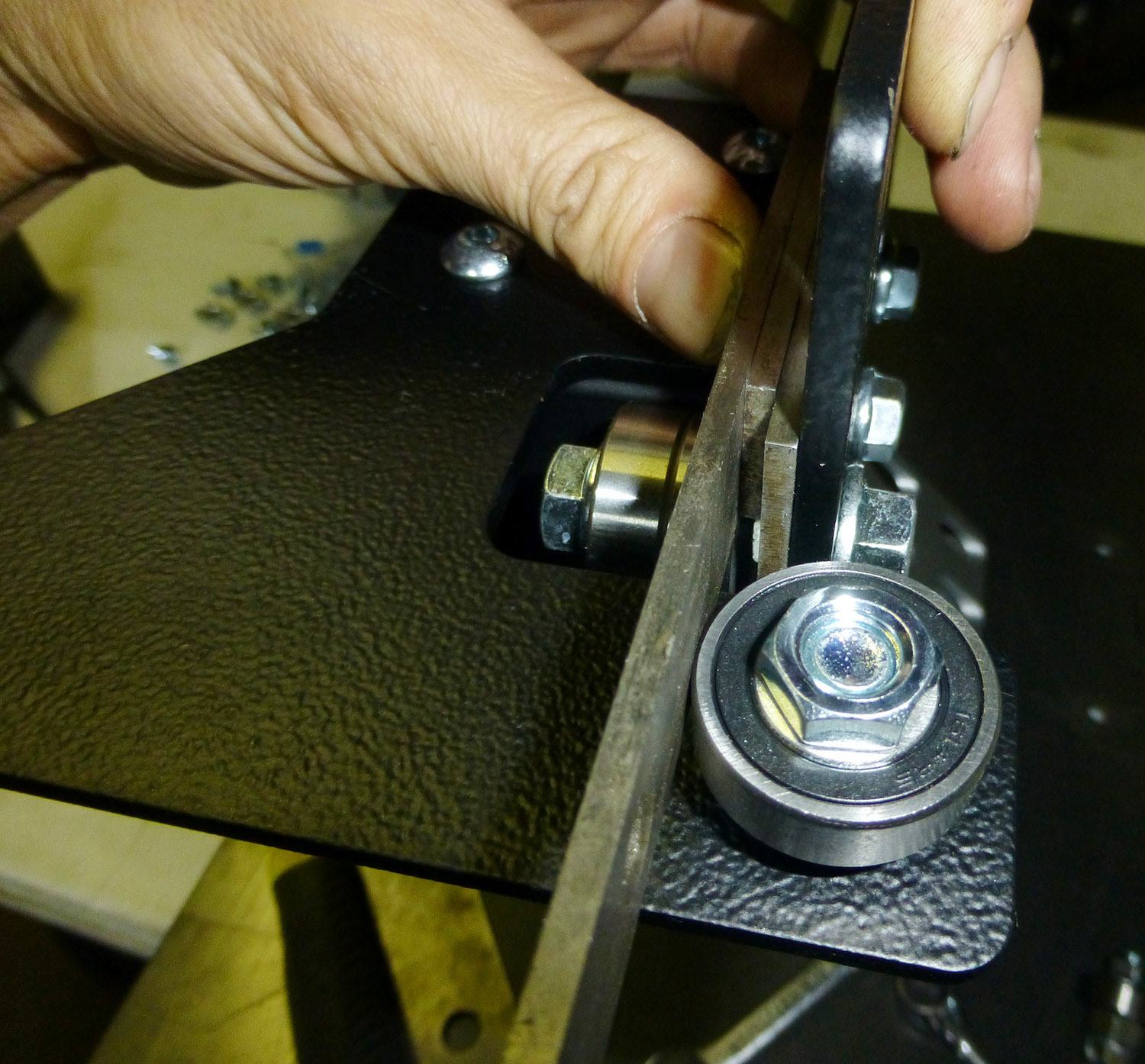
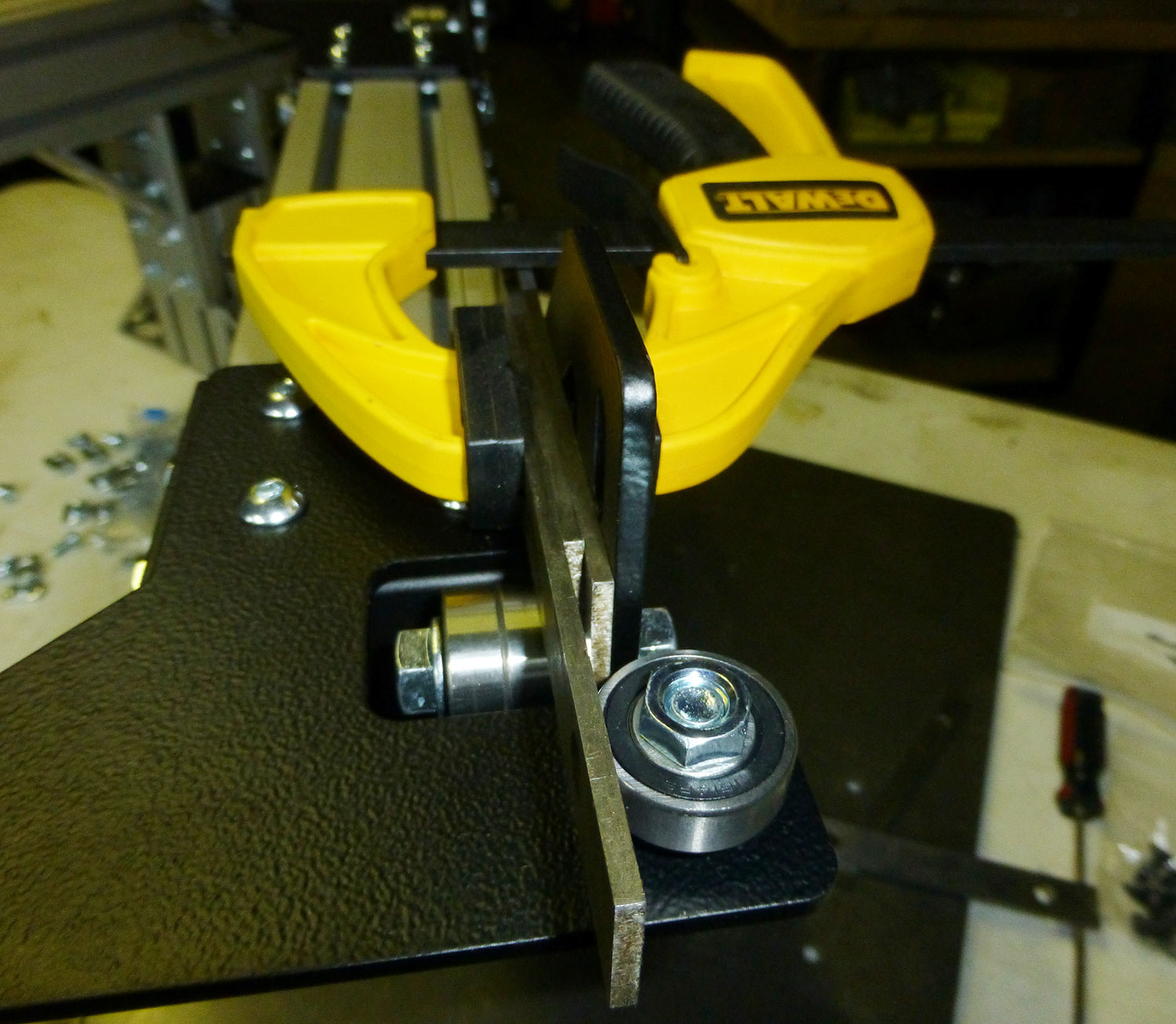
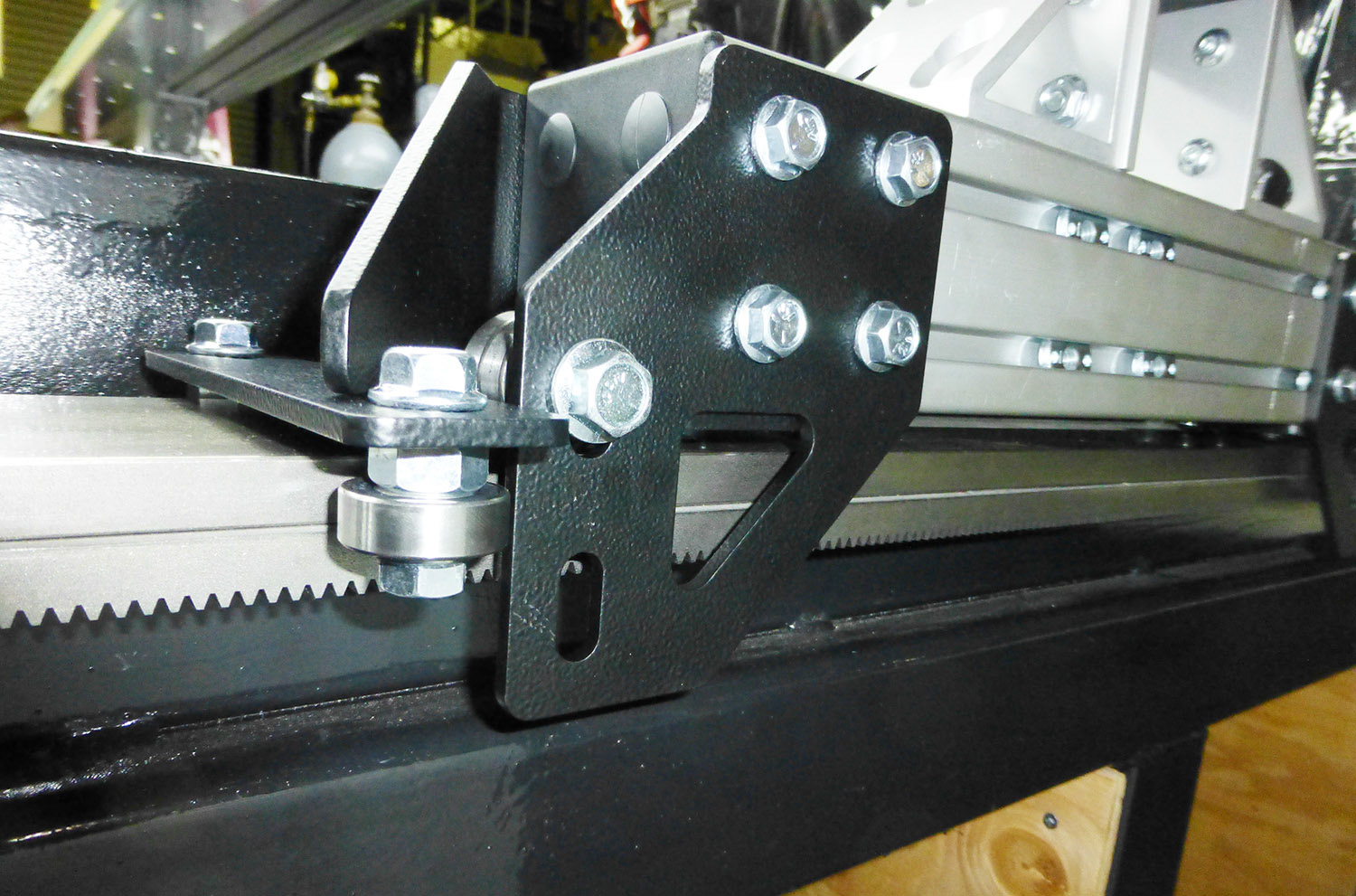
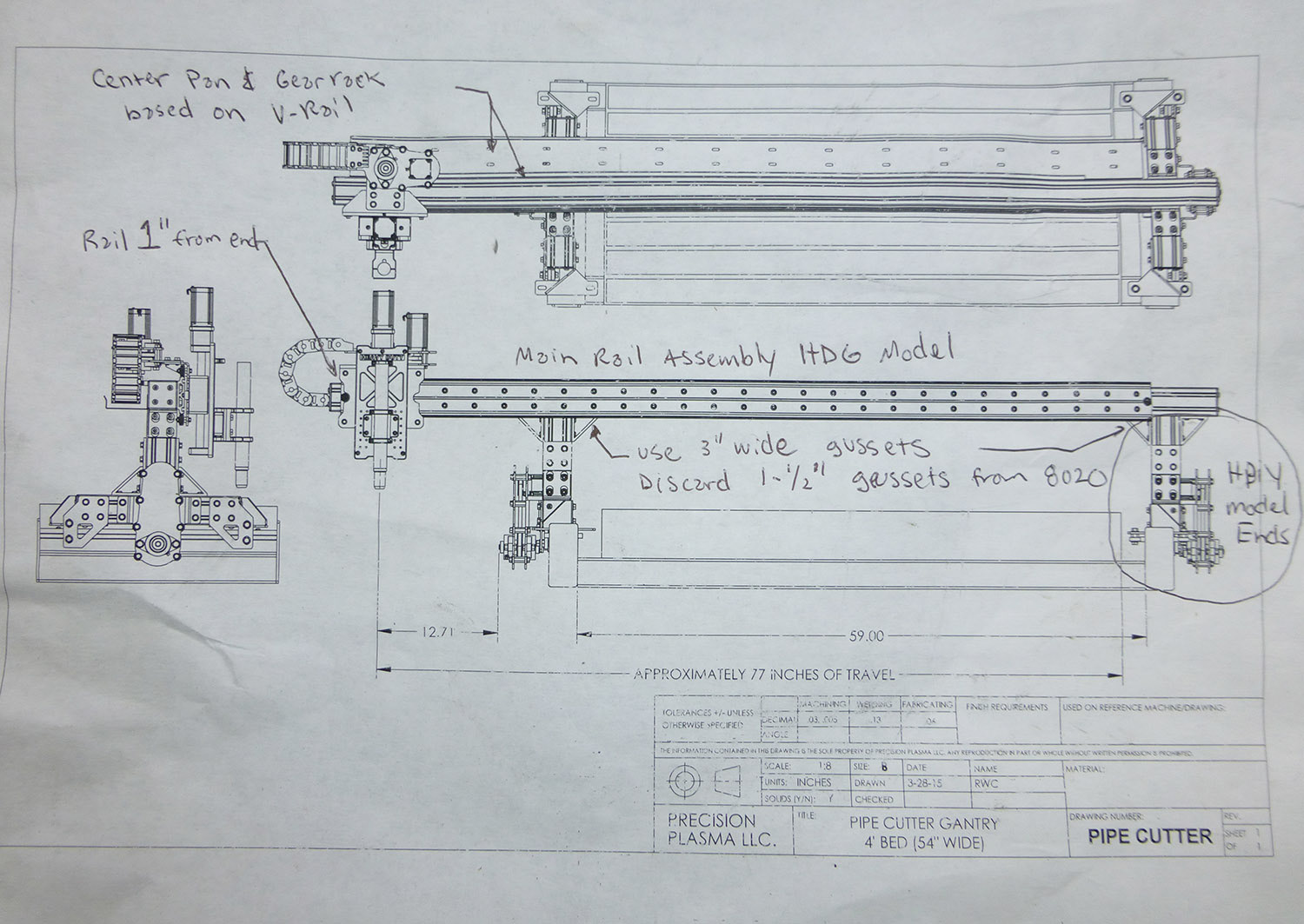
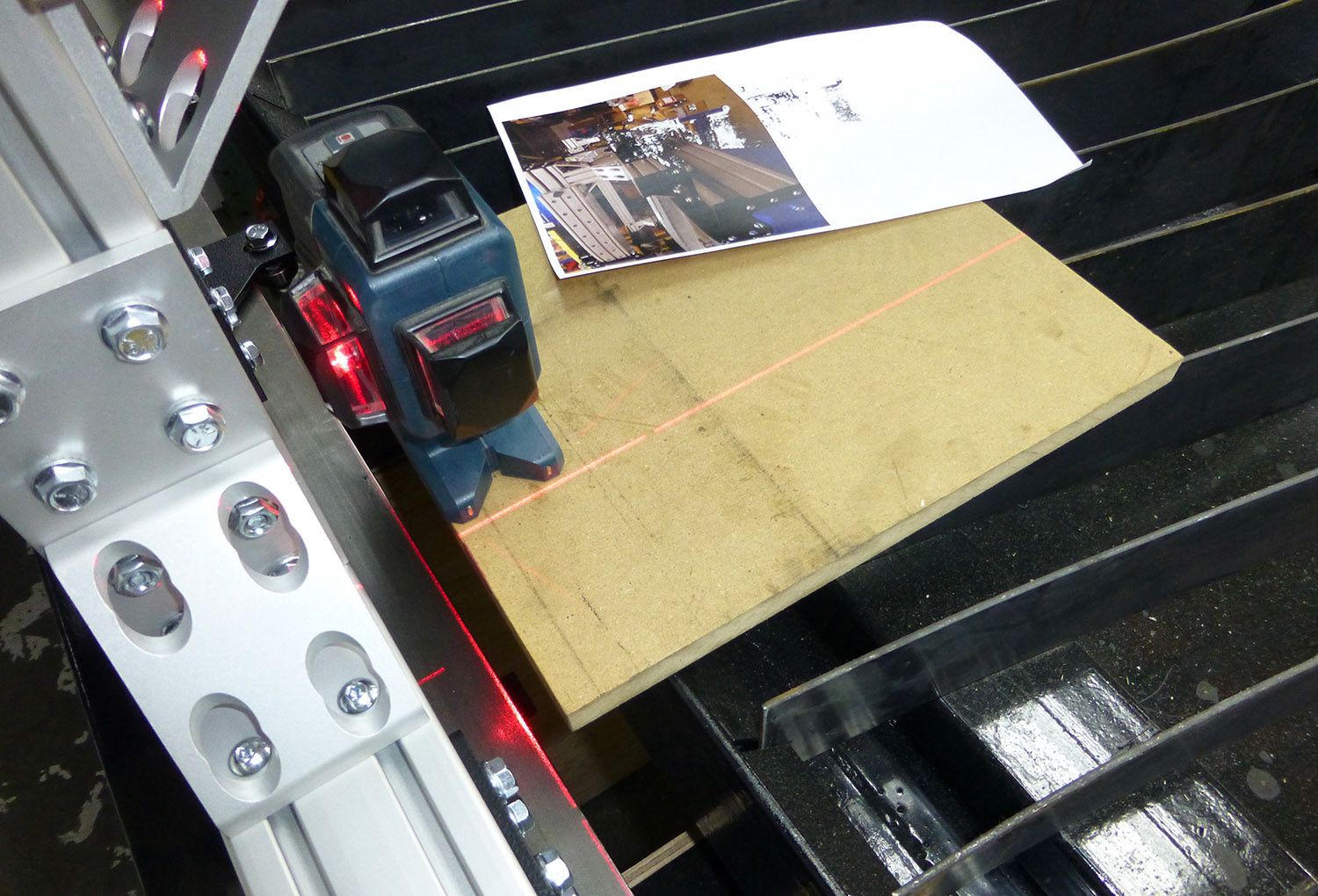
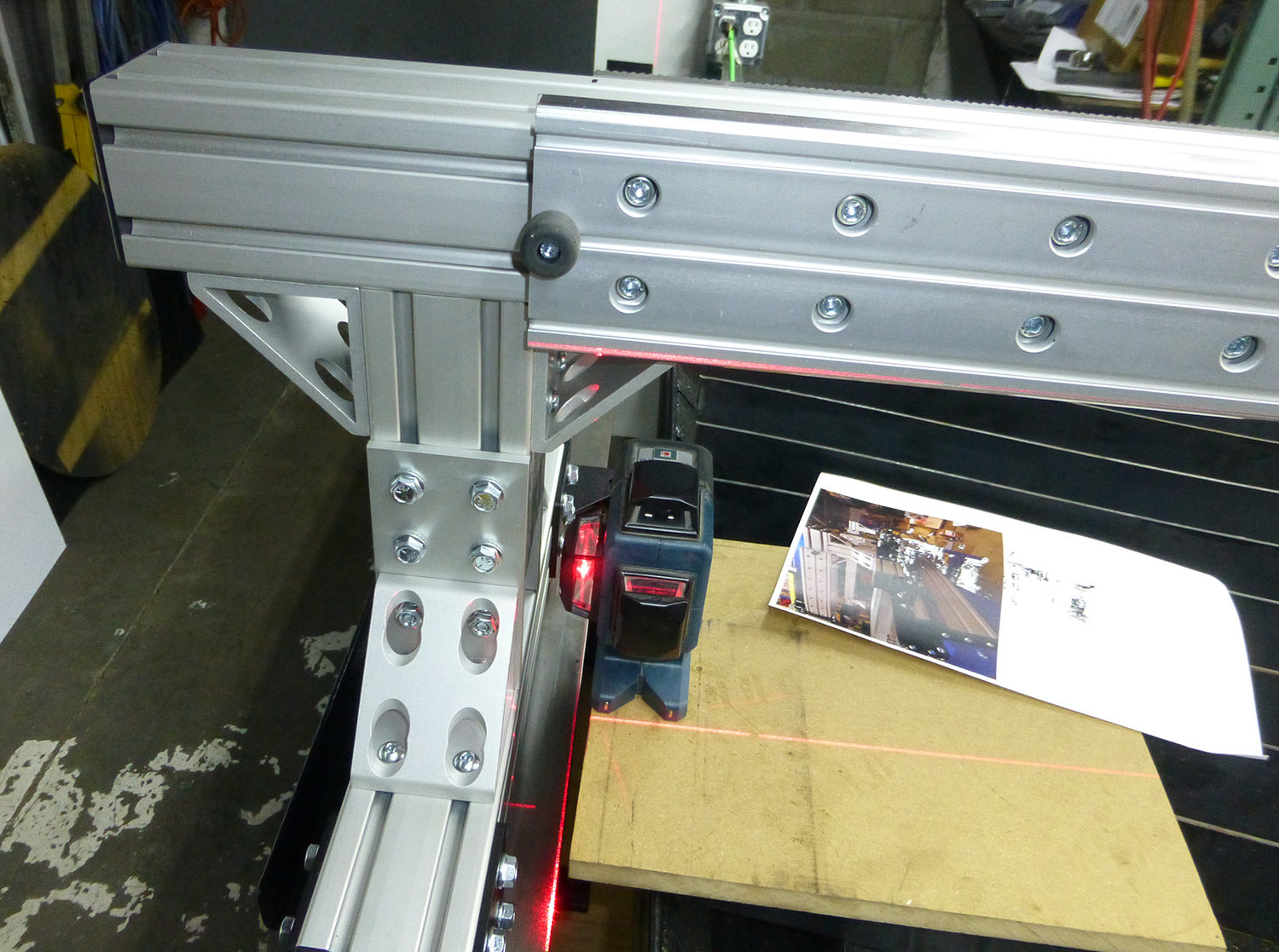
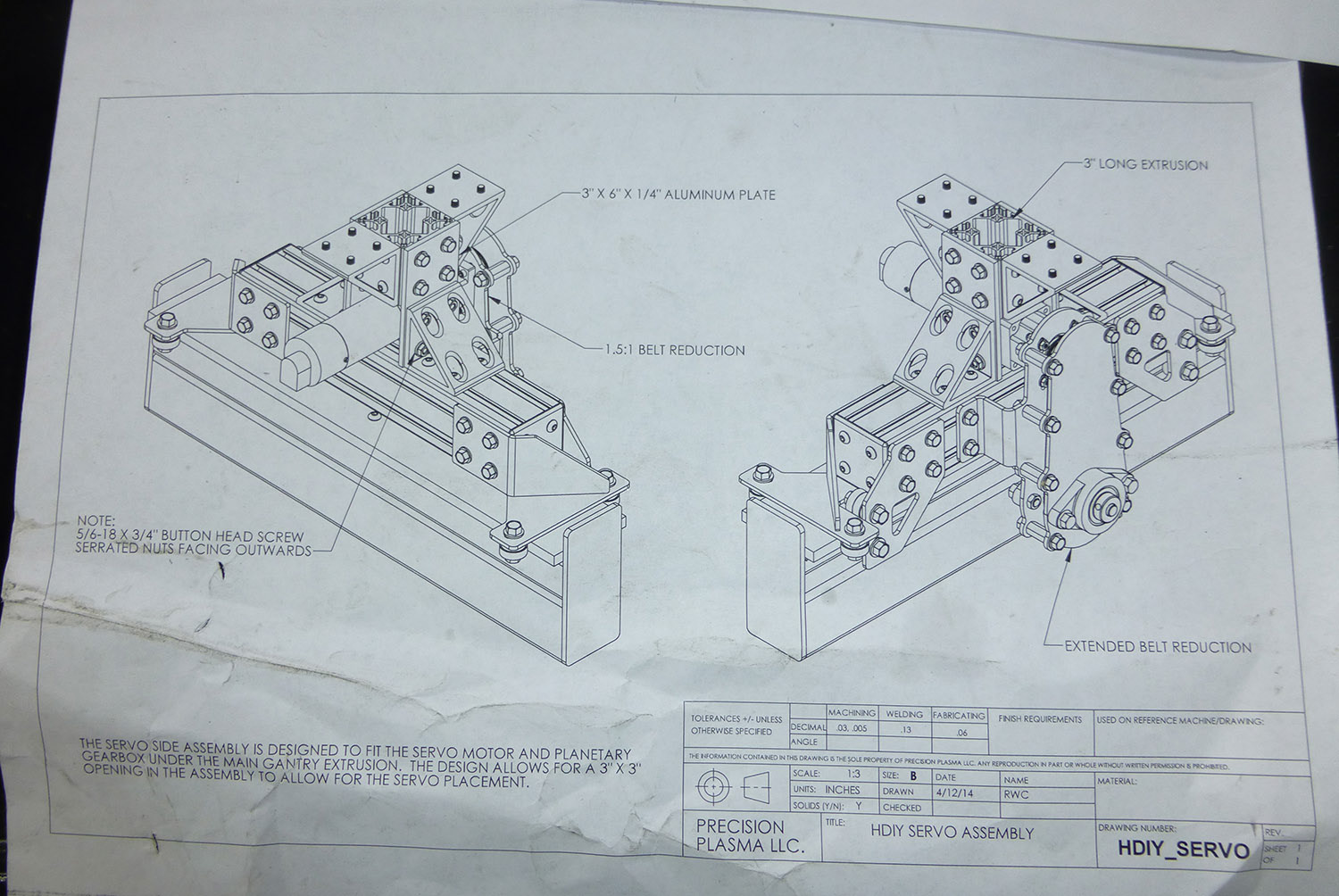

Next, I assembled and installed the gantry, there was a lot of alignment required for this process. To simplify things, I use some machine shop parallels as spacers.
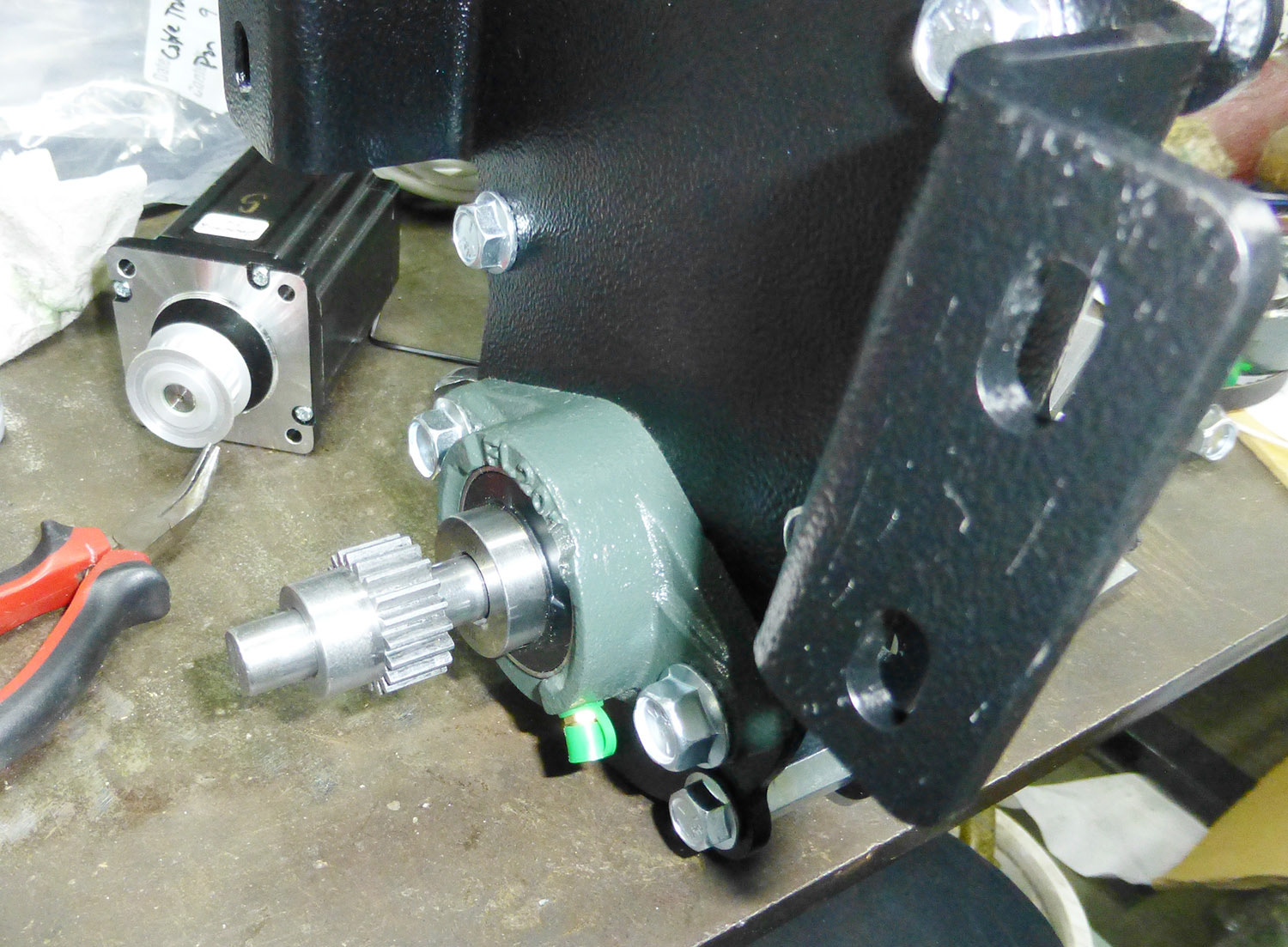
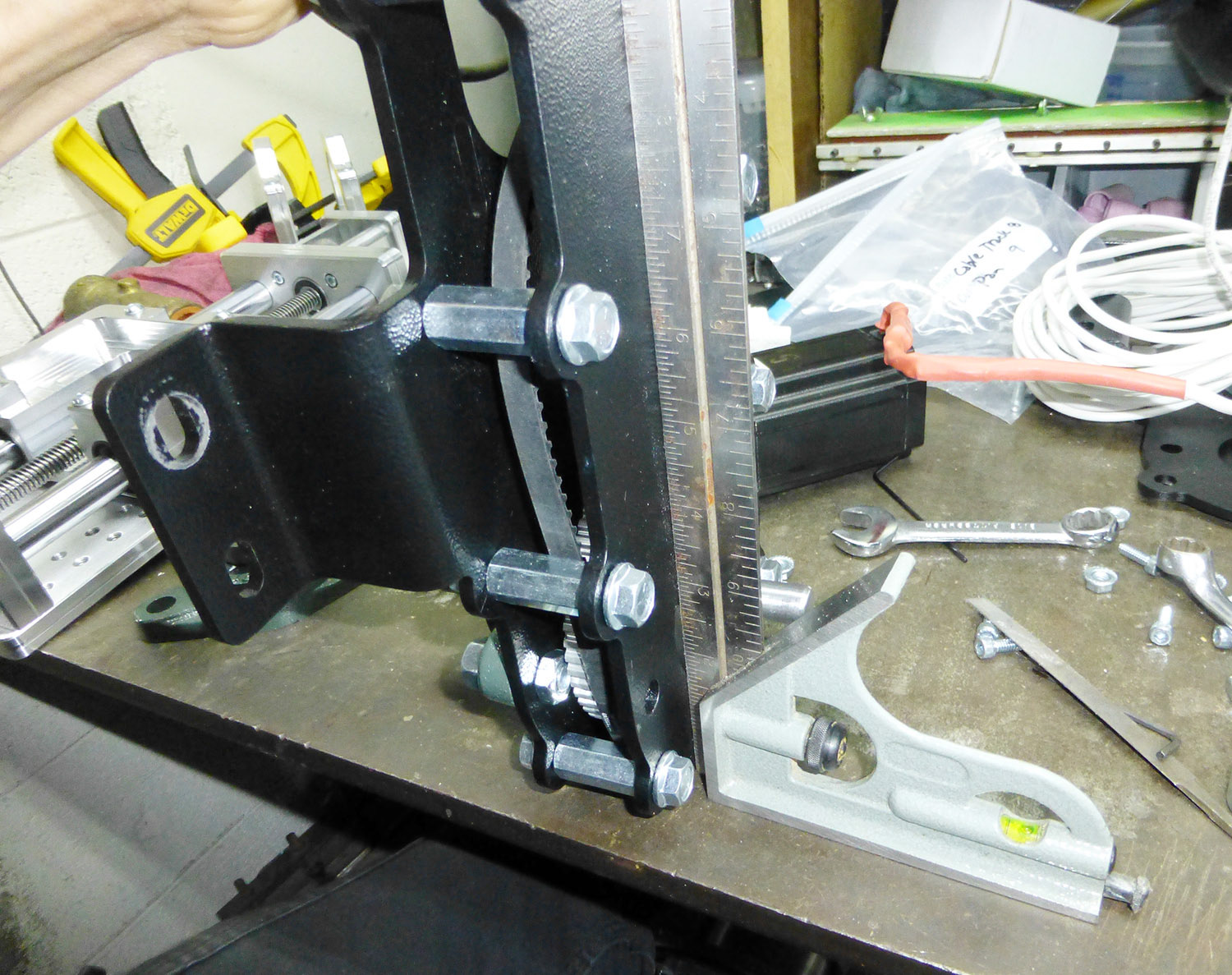
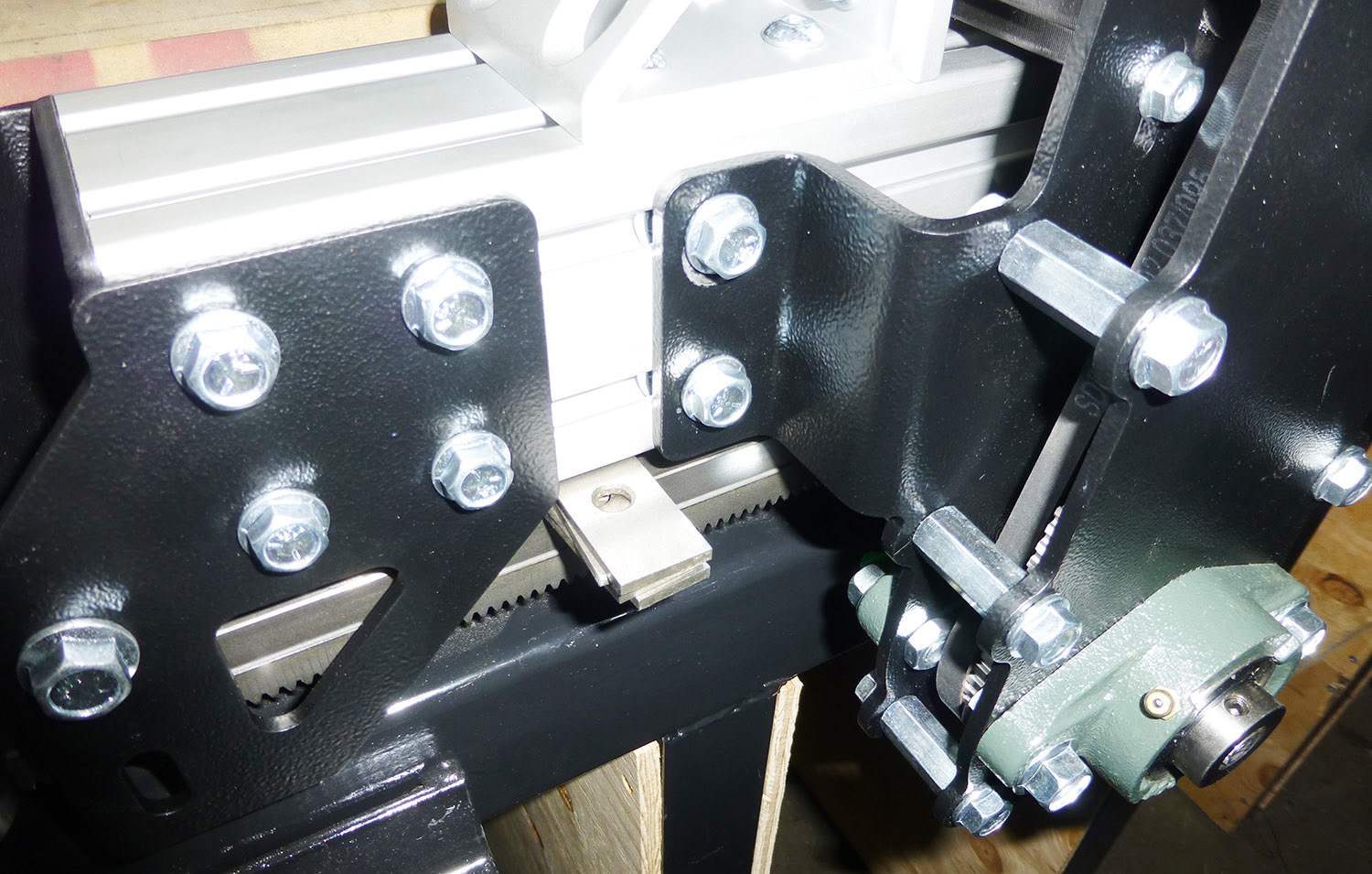
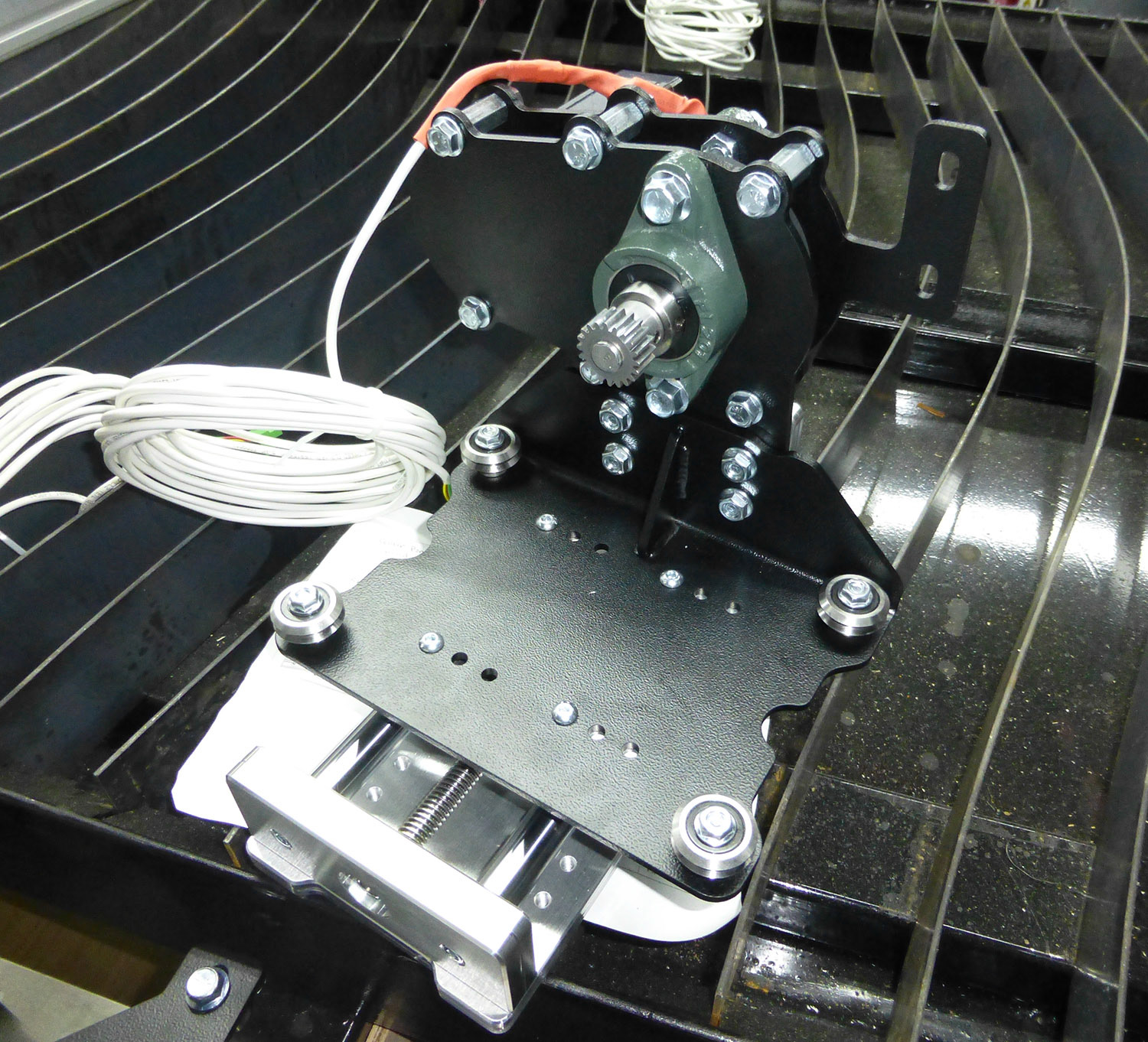
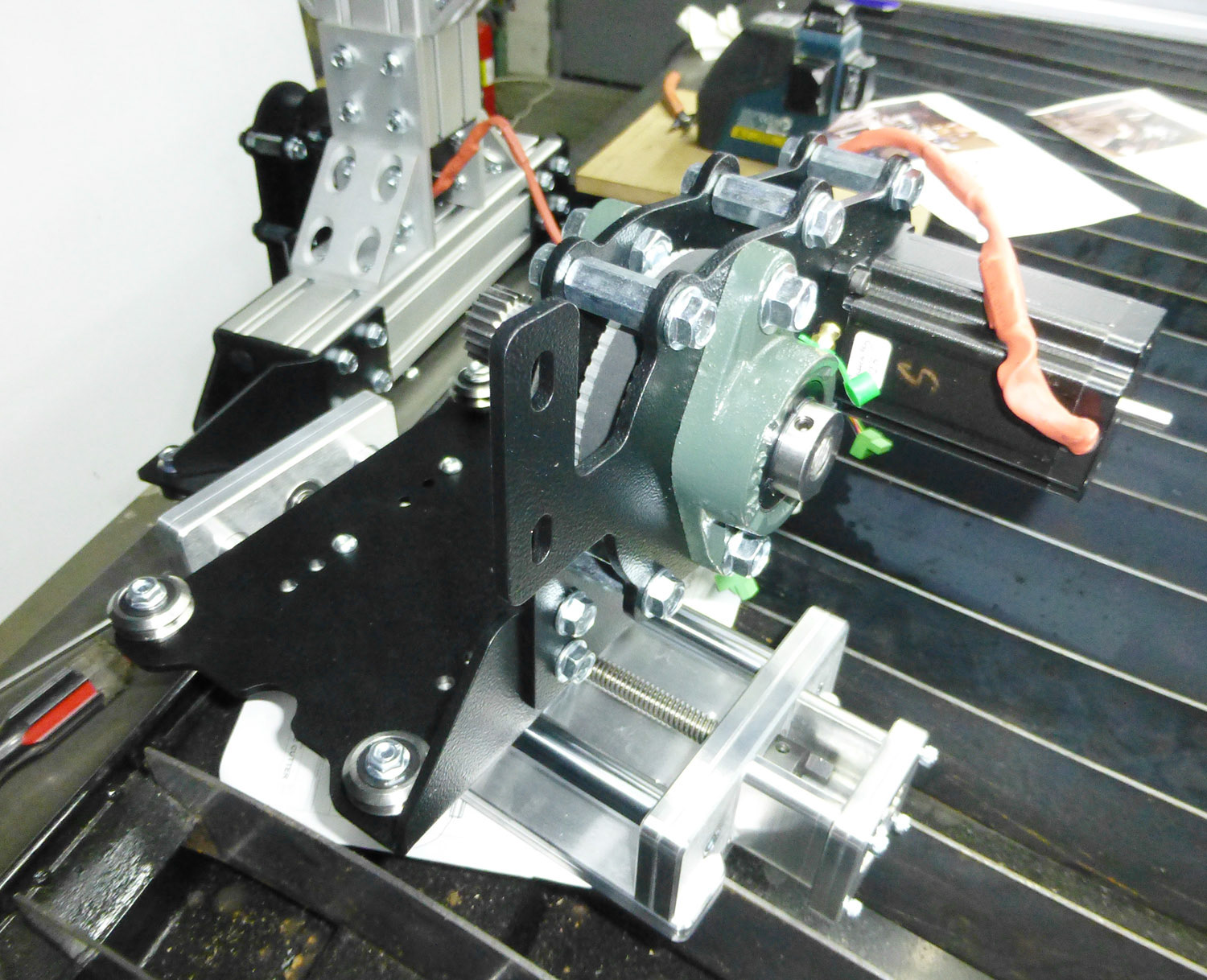
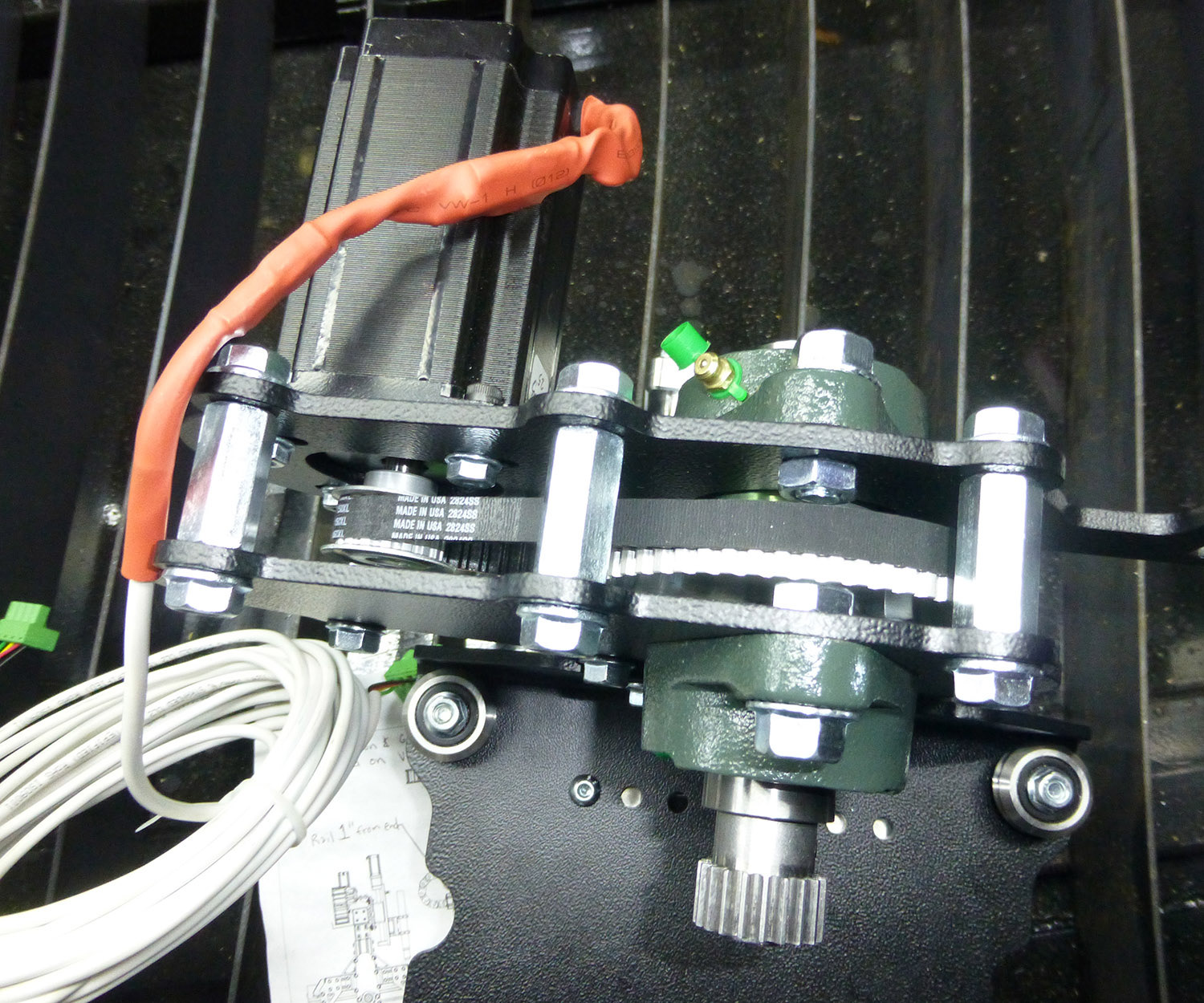
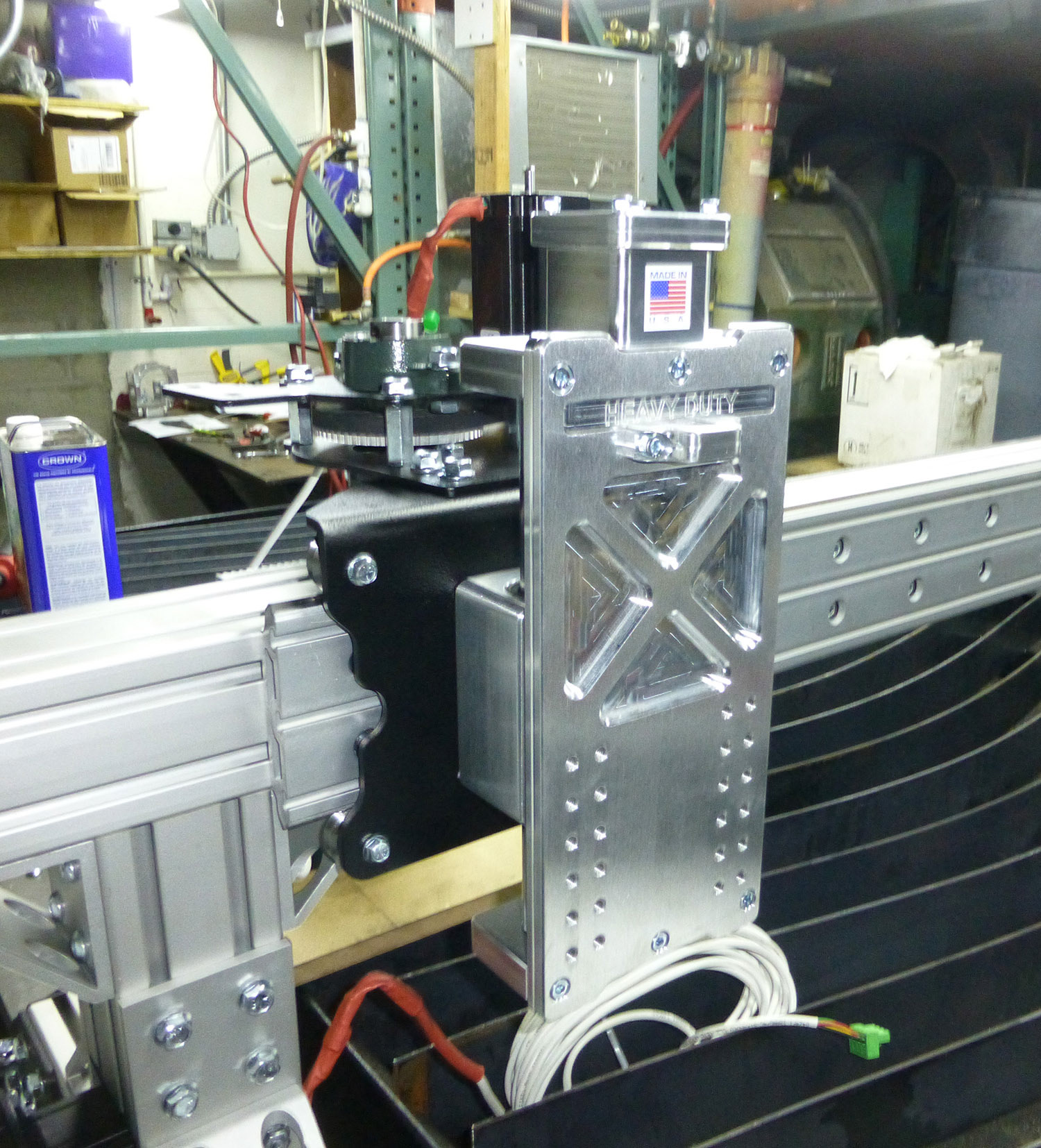
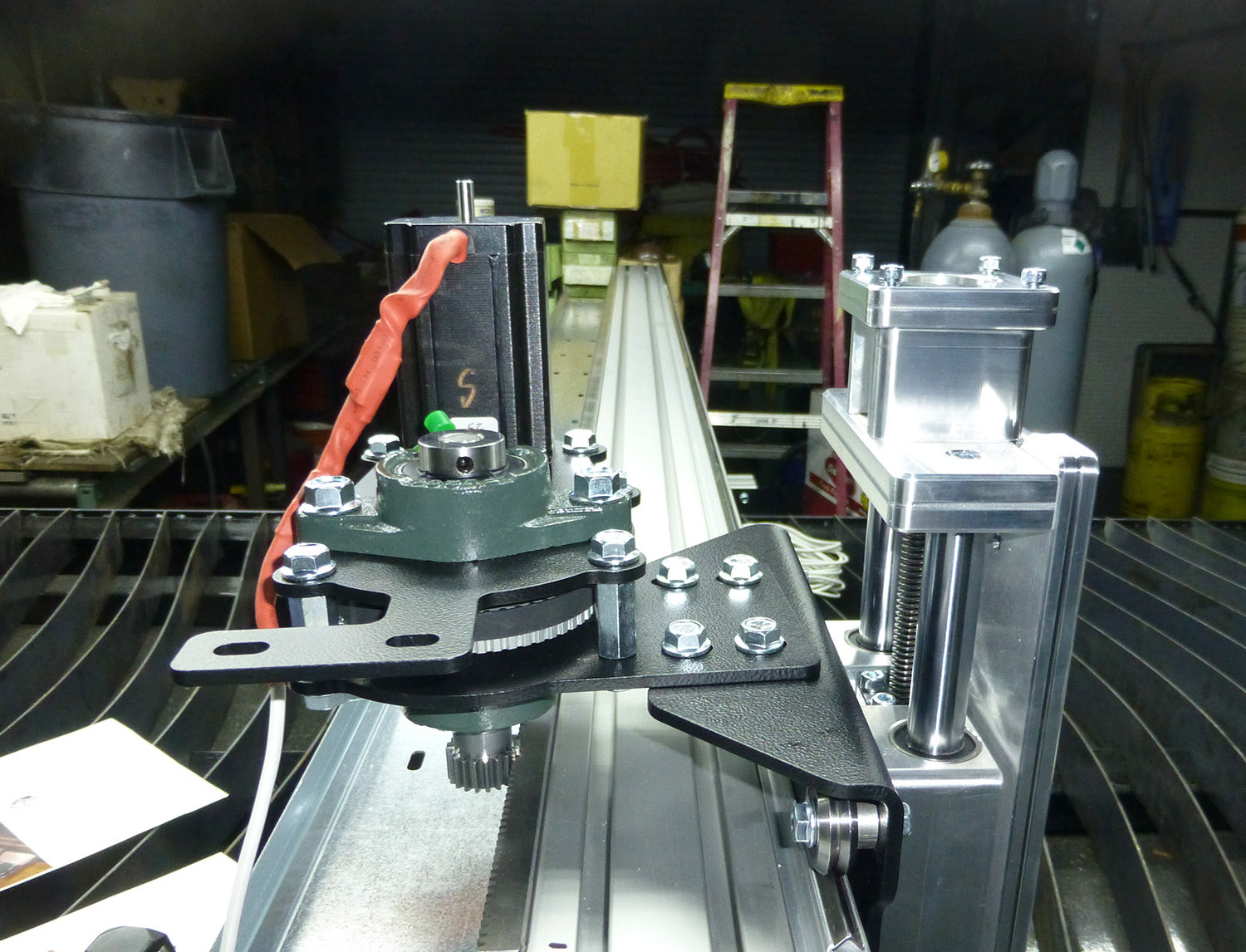
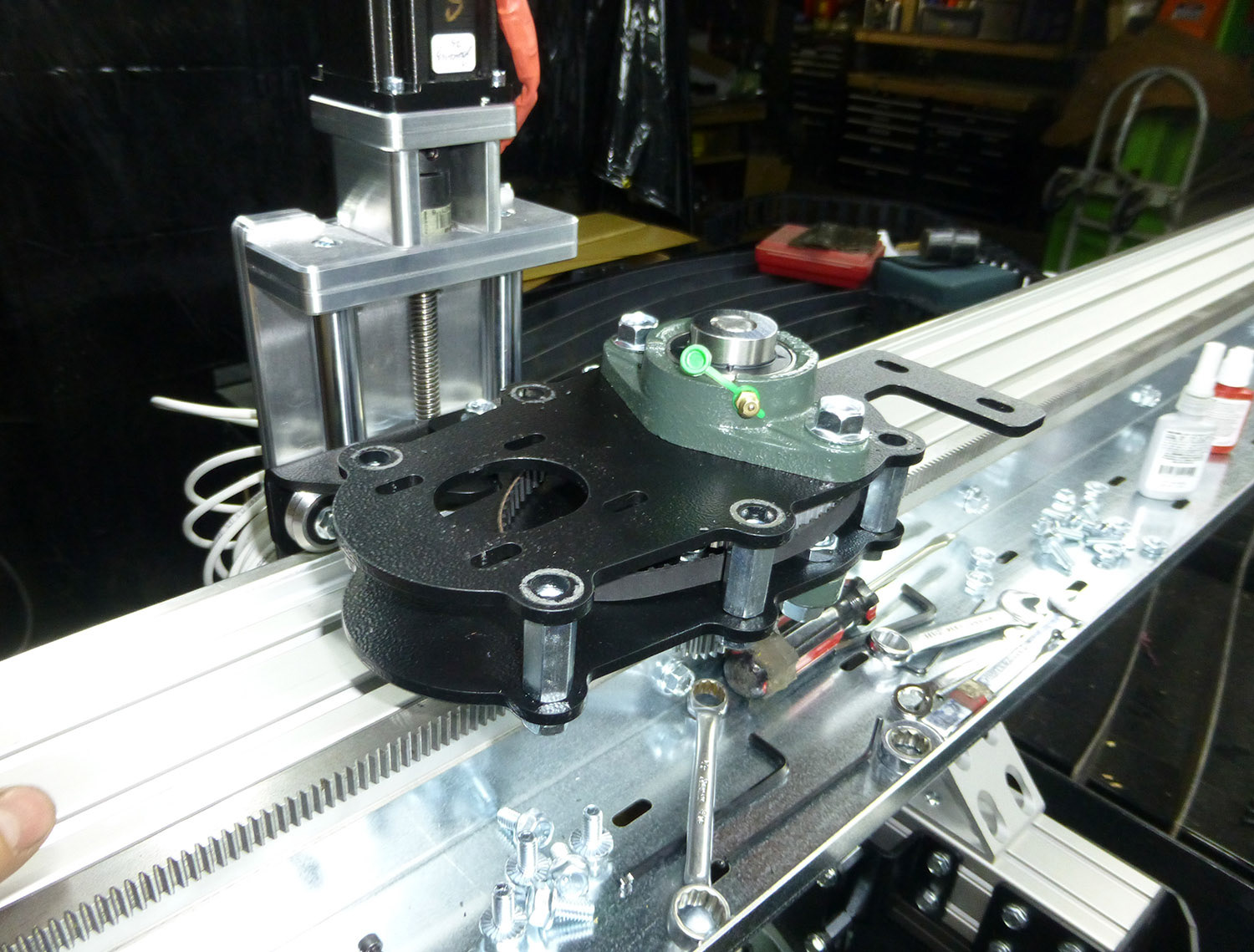
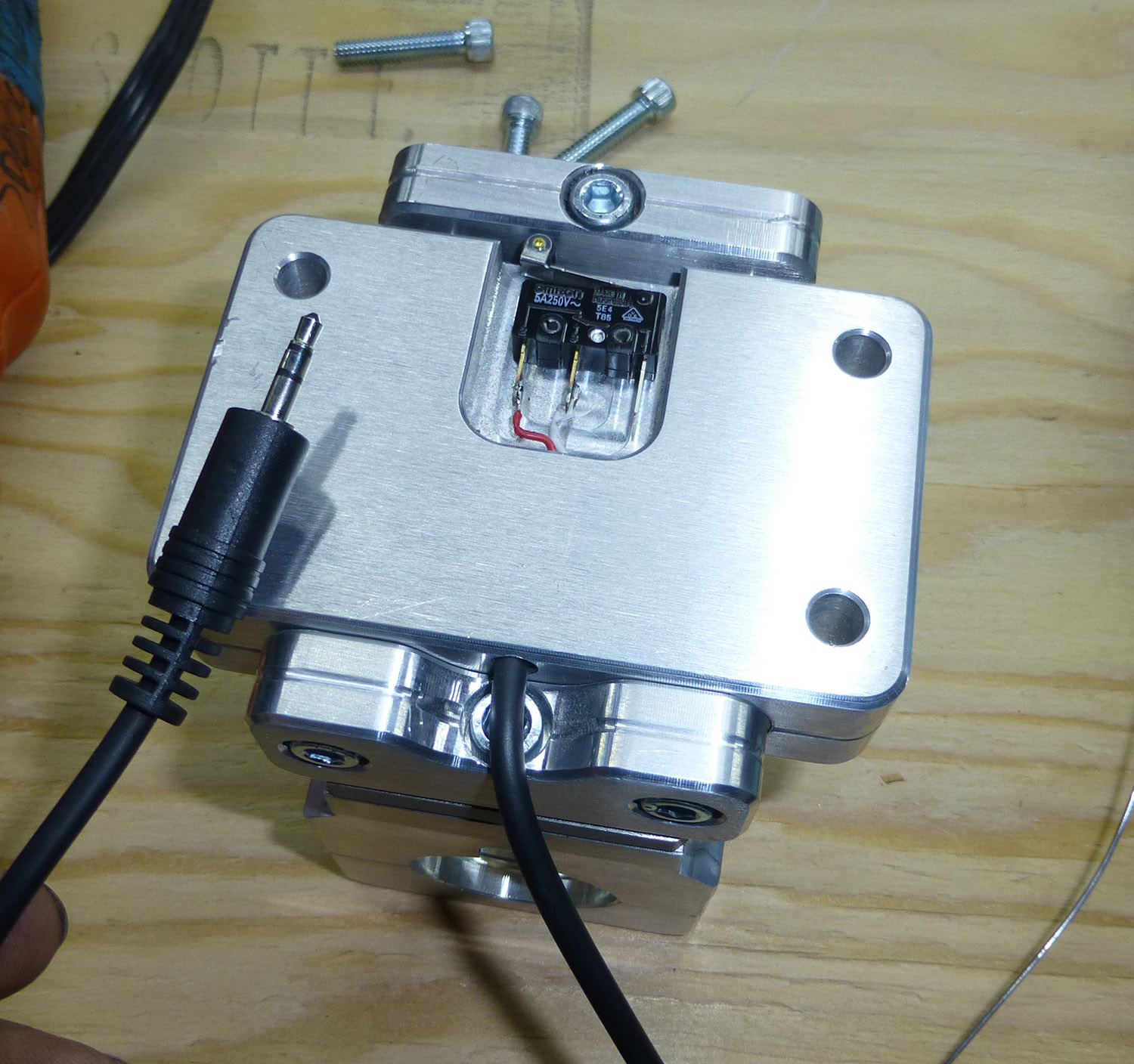
I assembled the plasma cutter carriage and mounted it to the gantry.

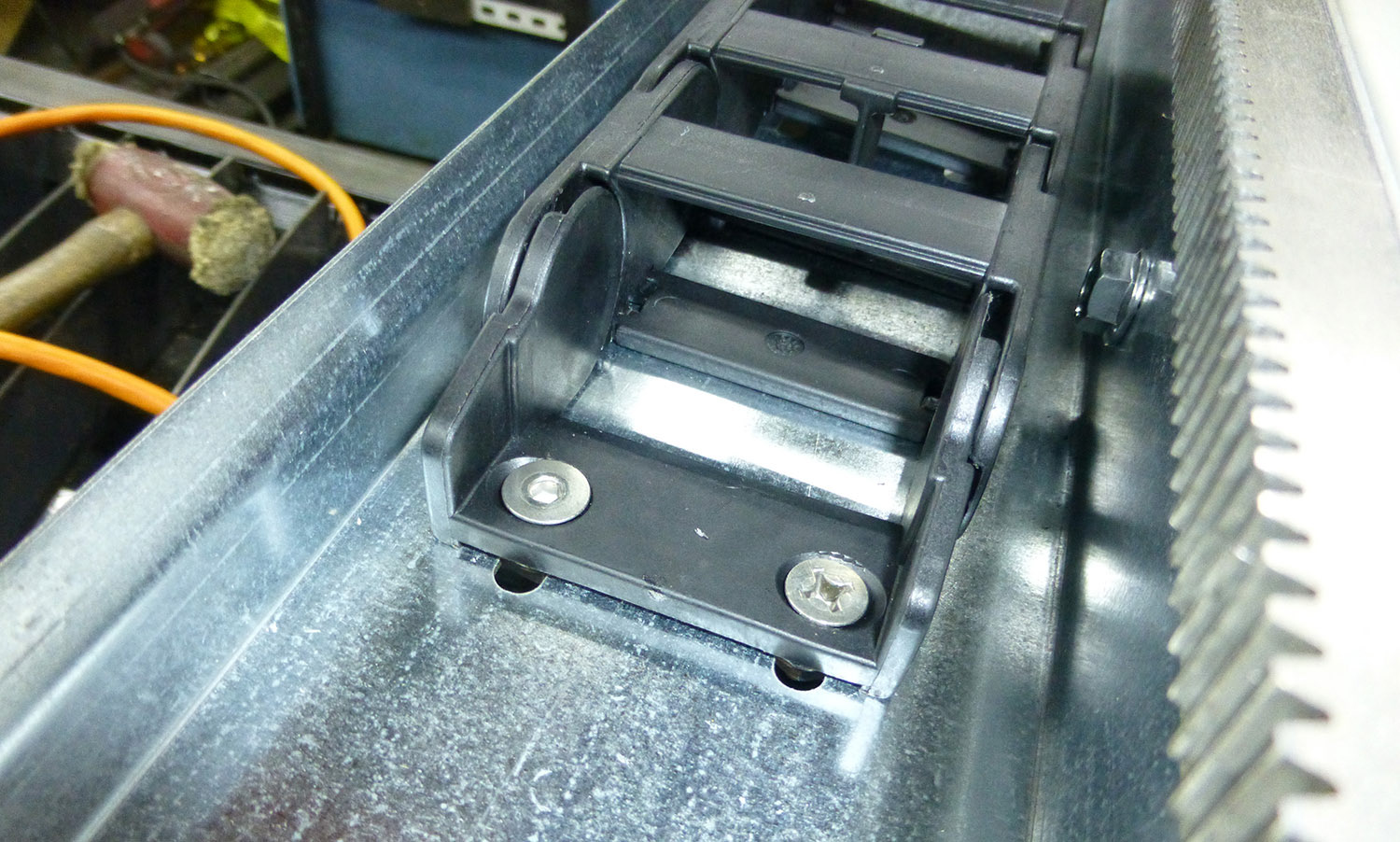
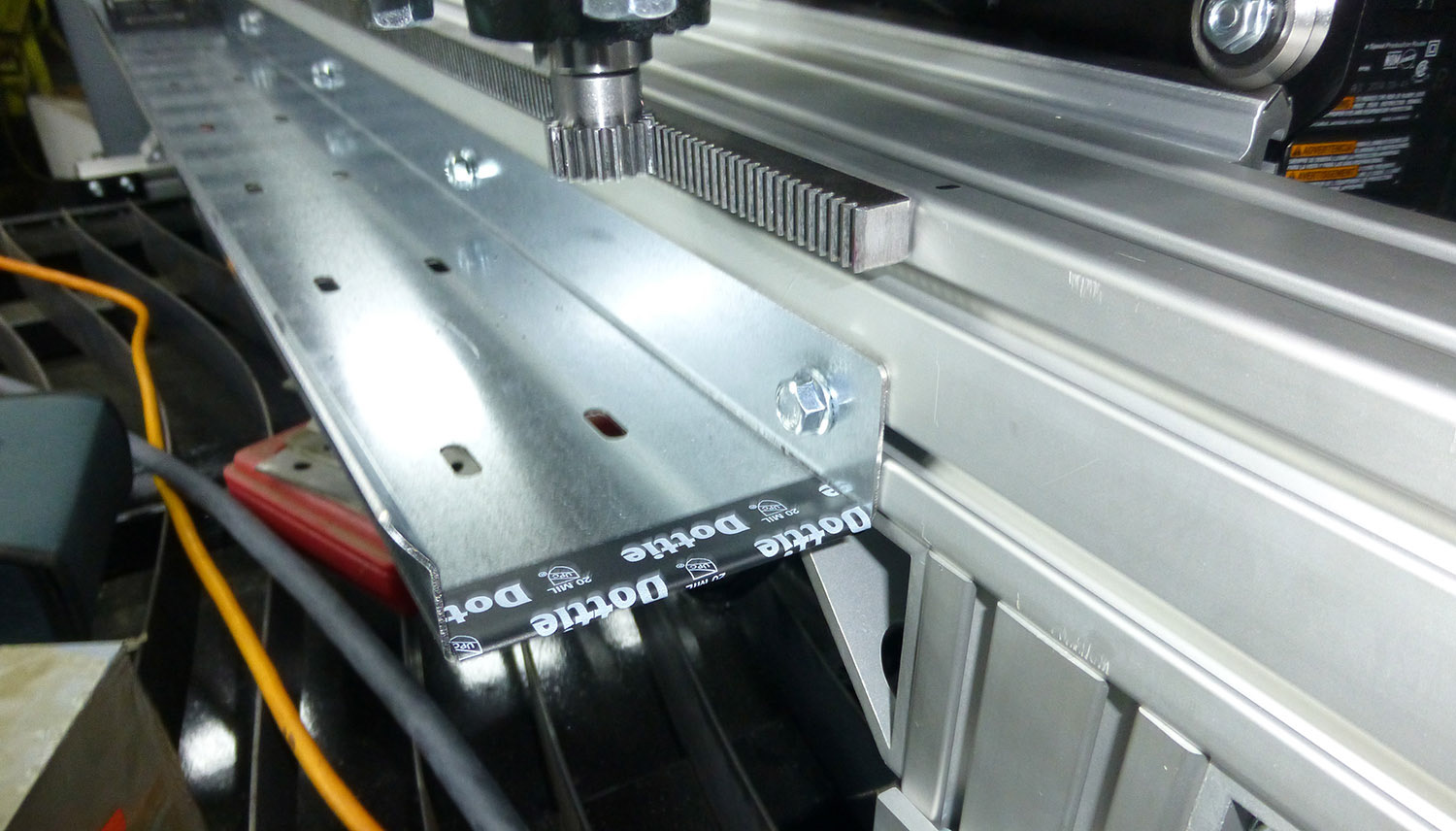
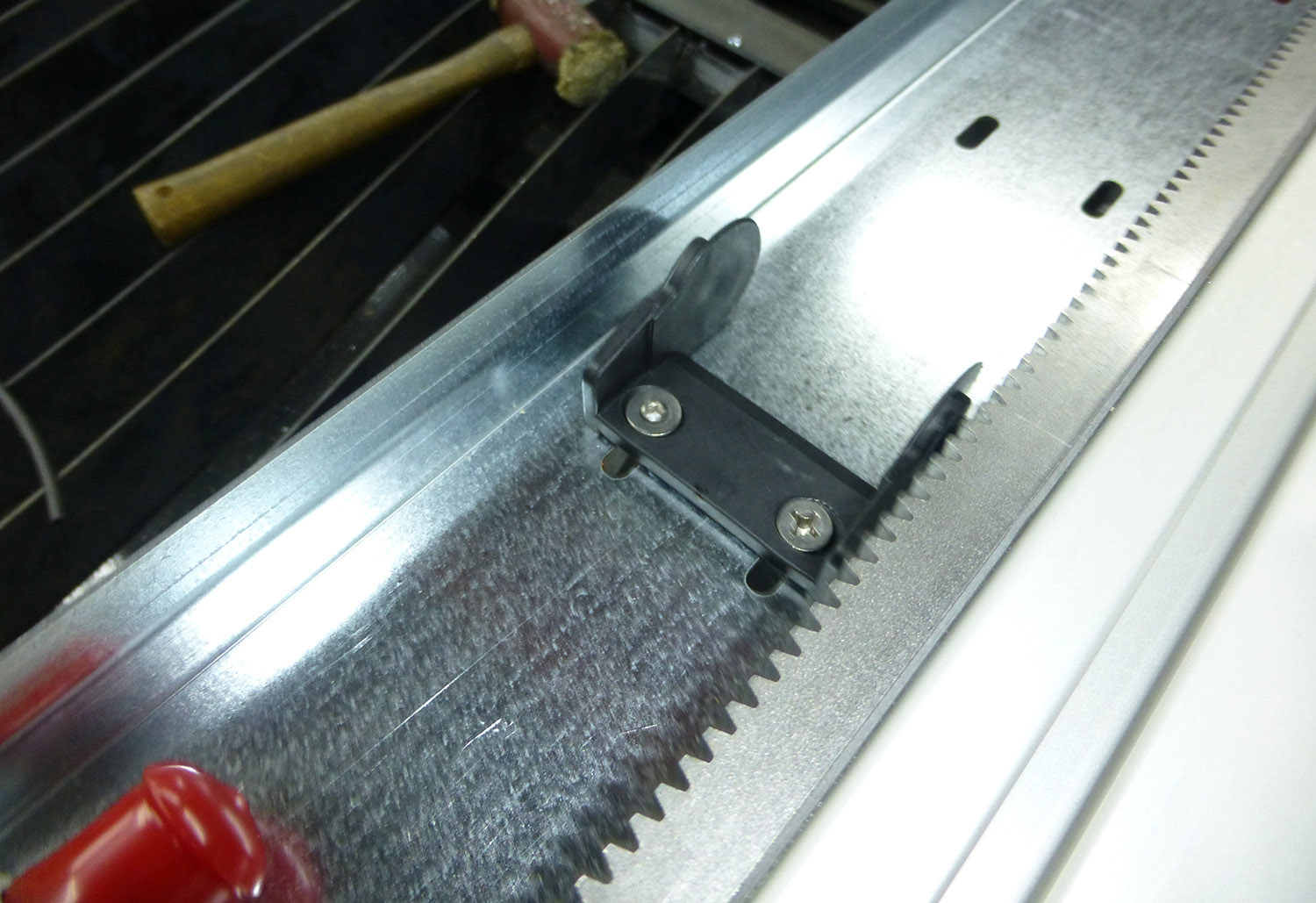
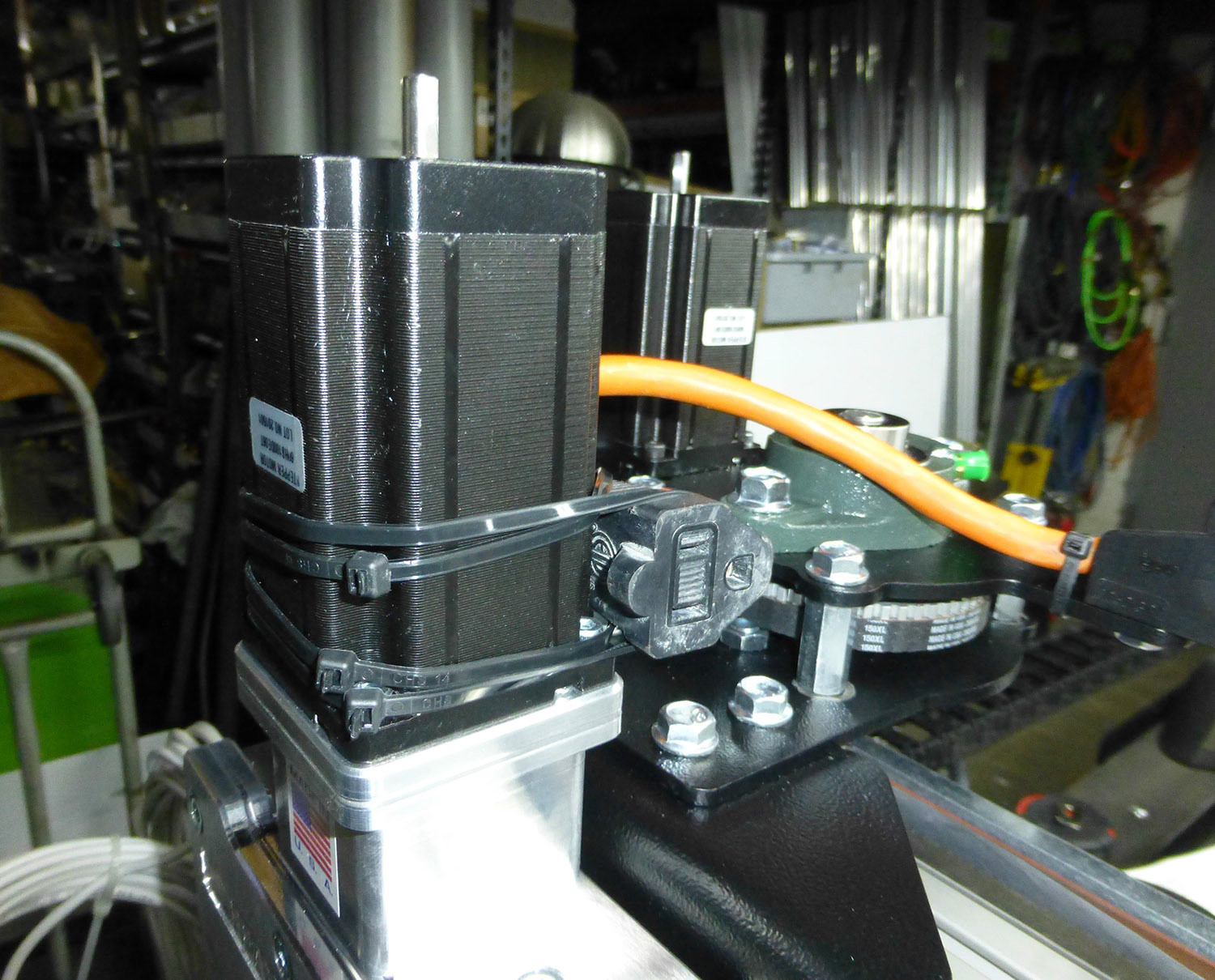
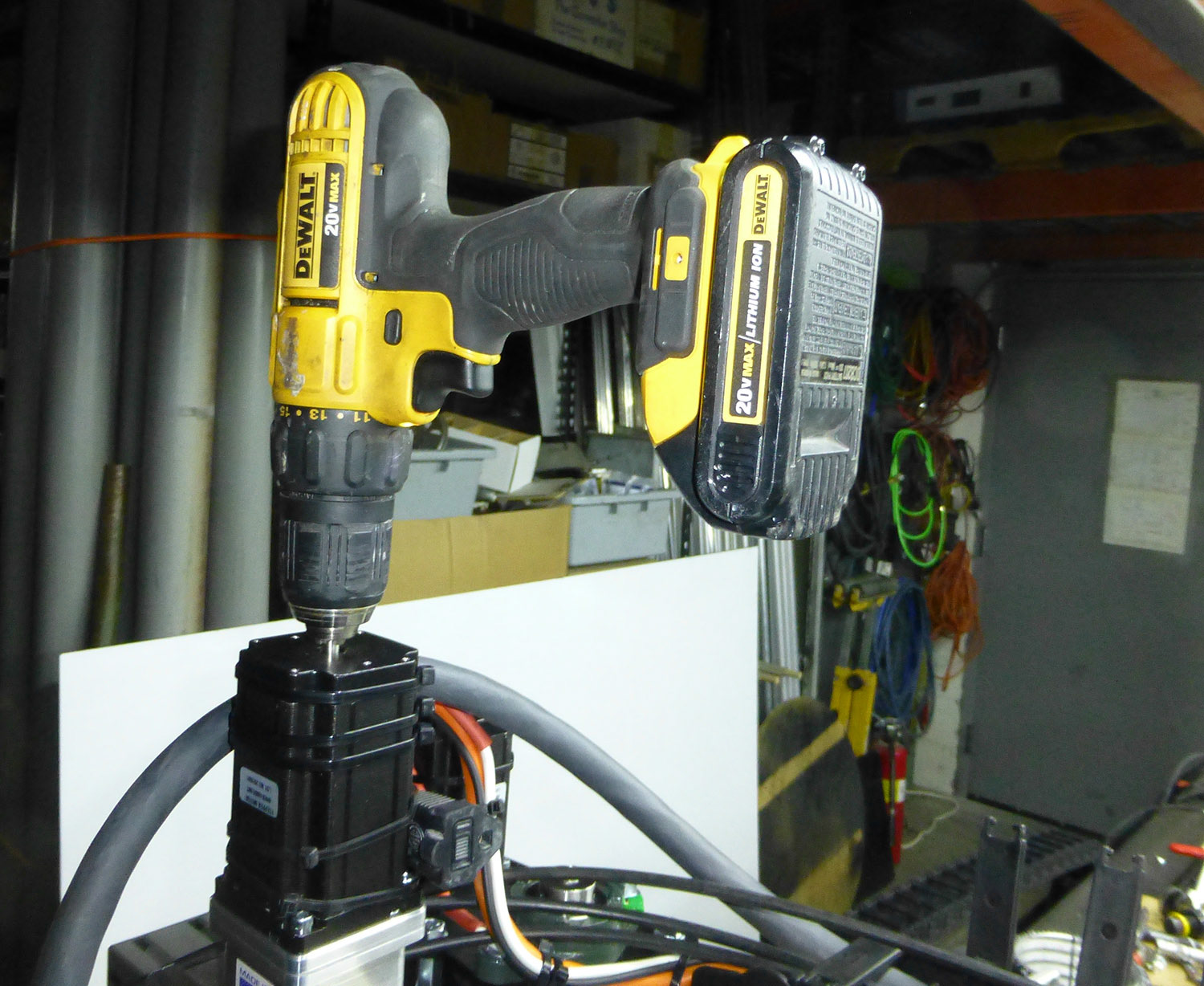
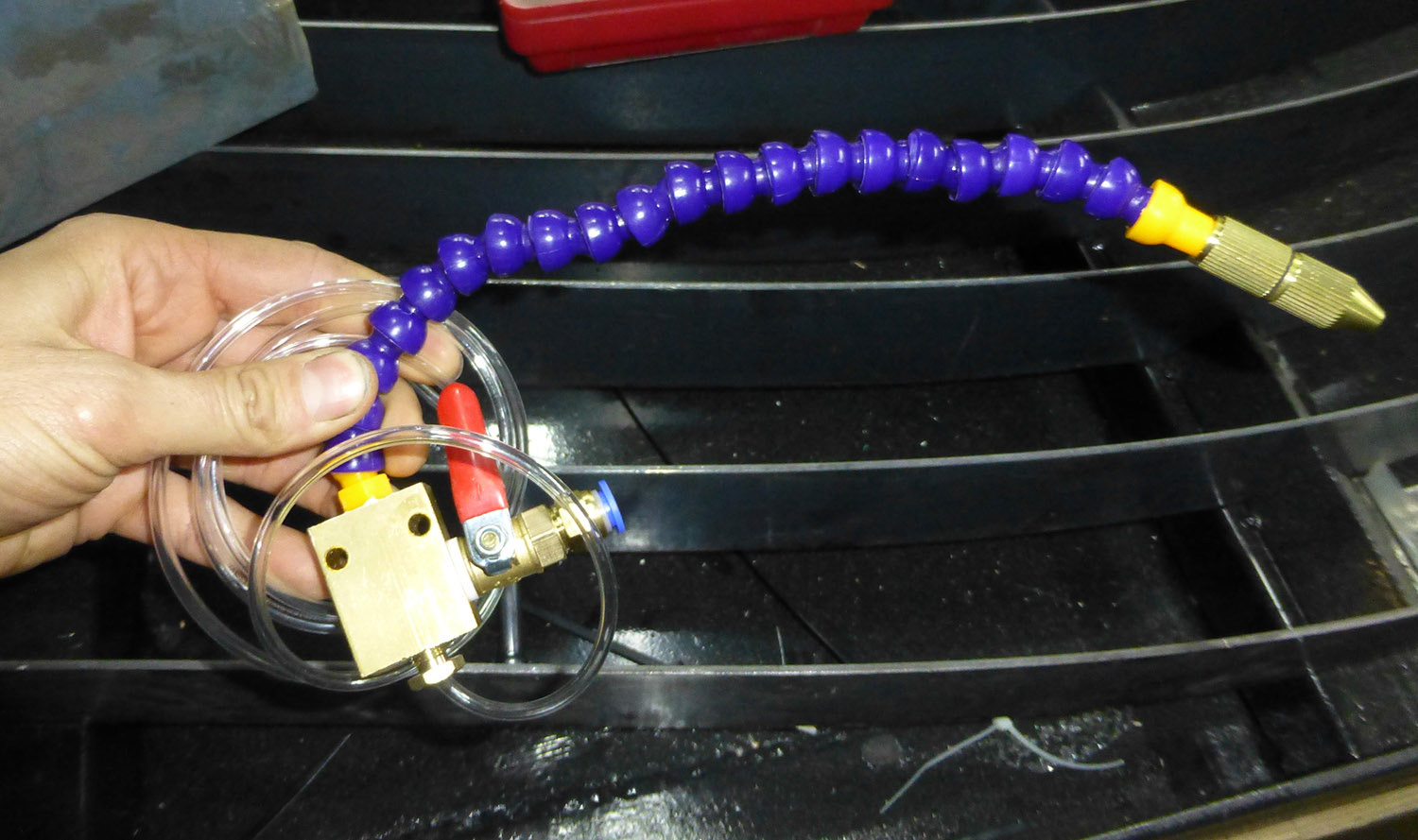
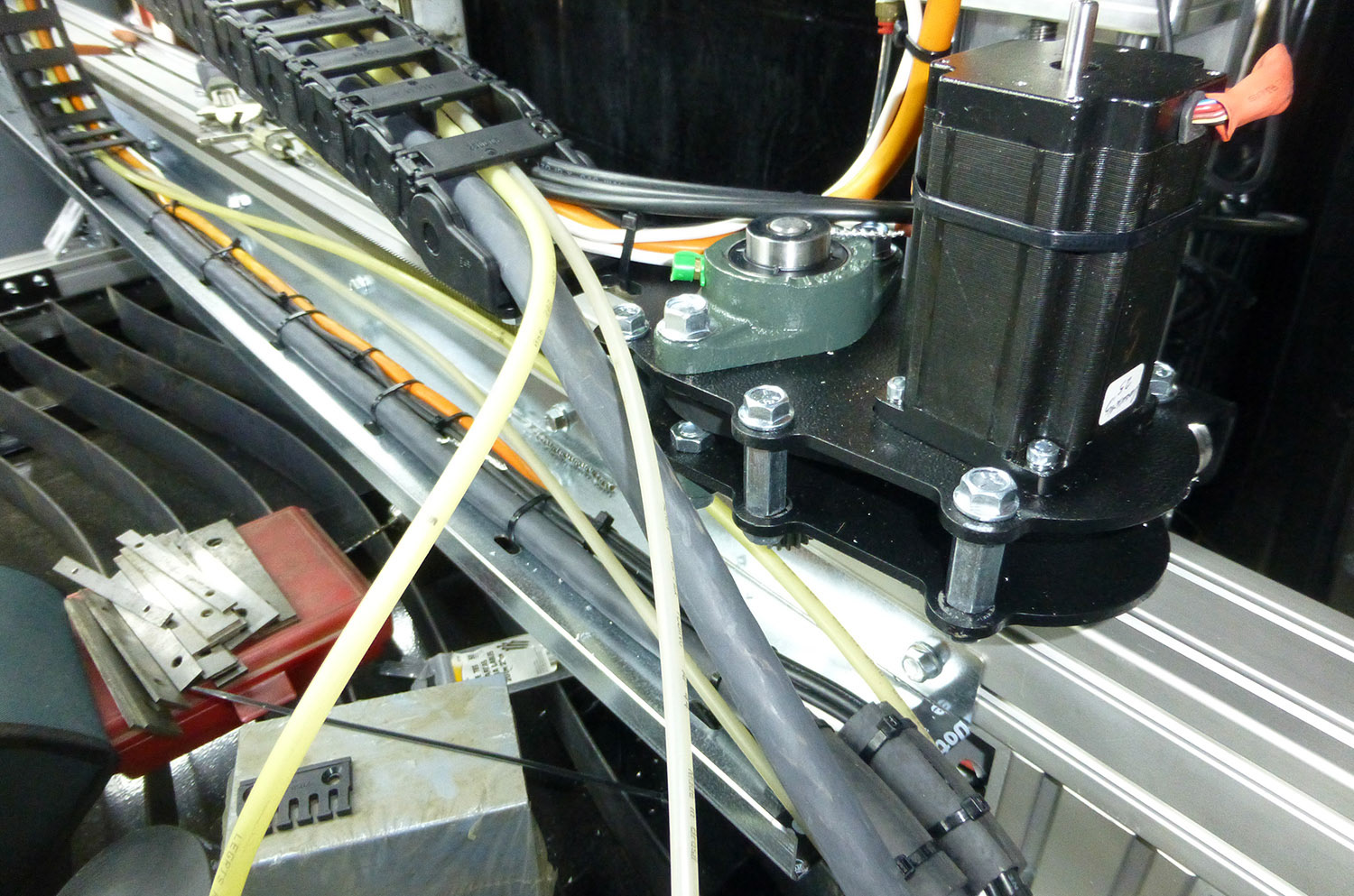
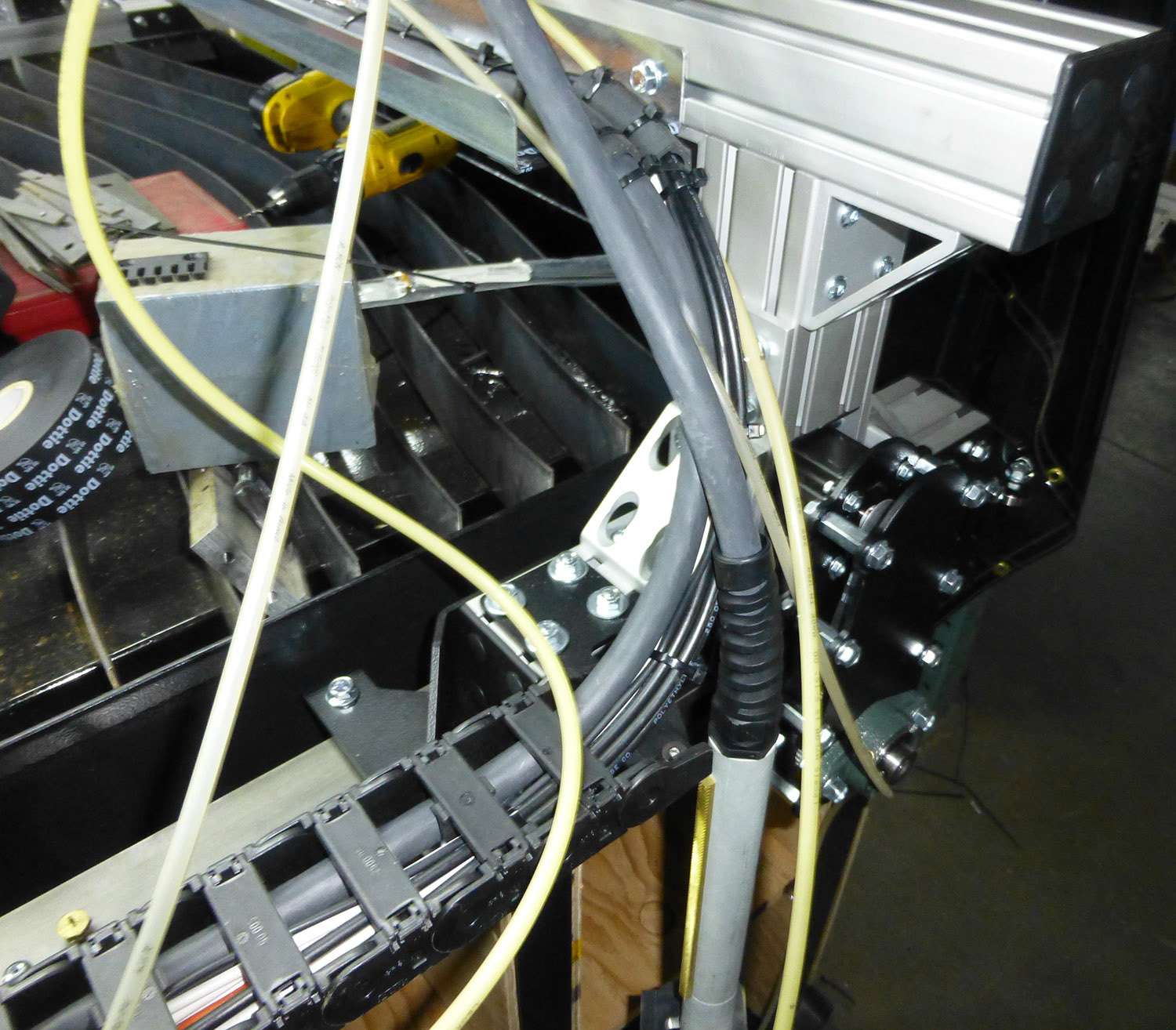
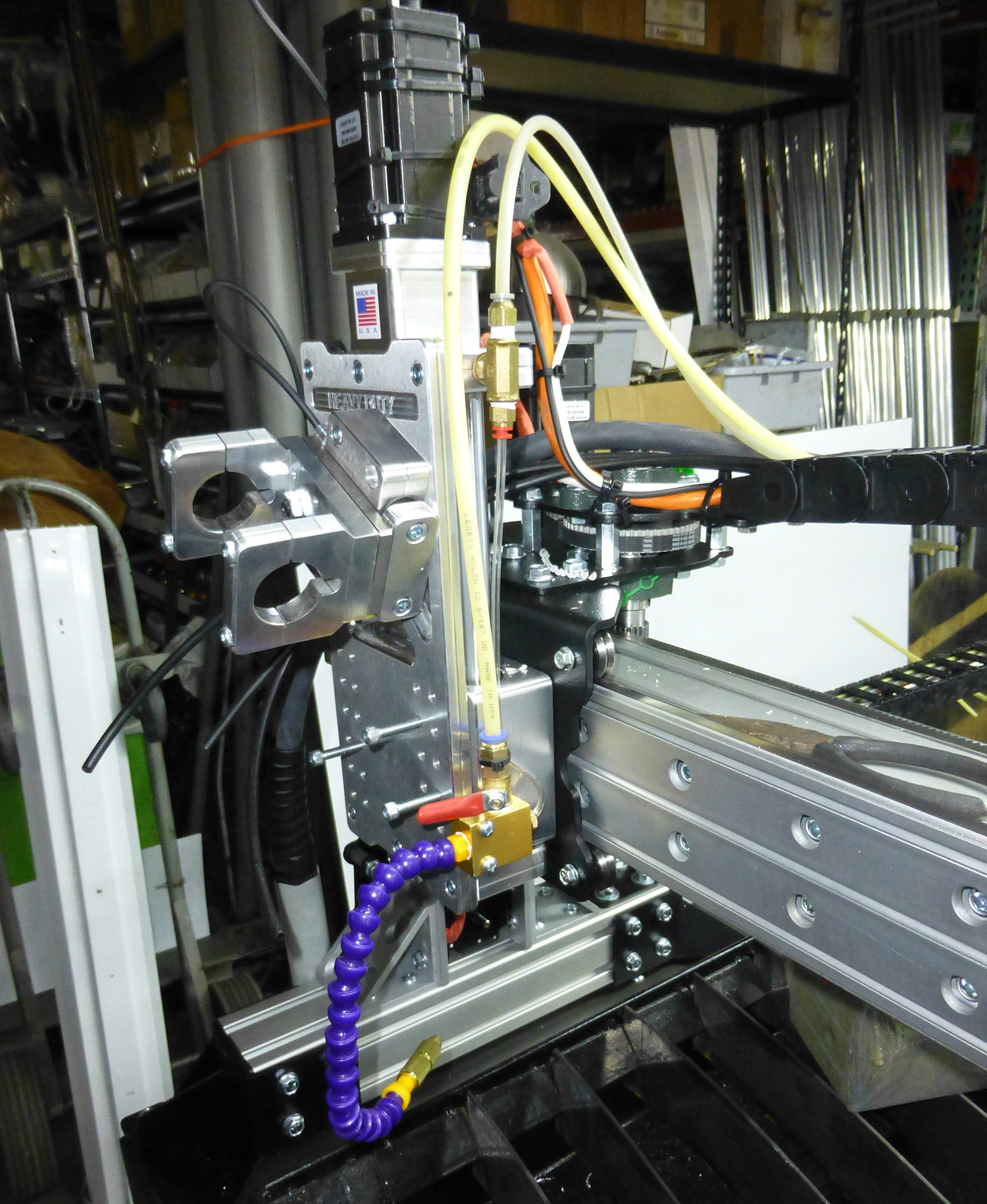
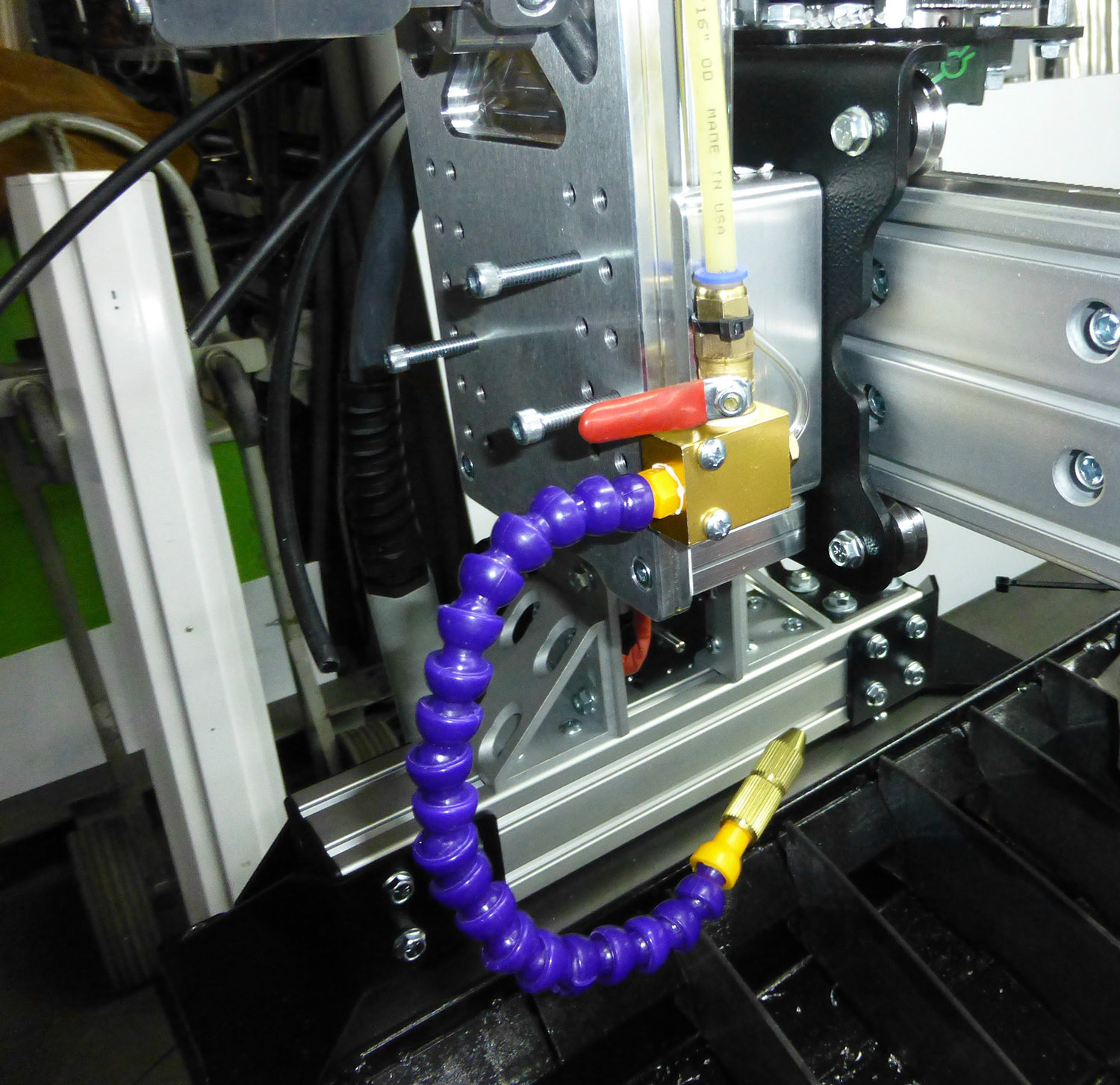
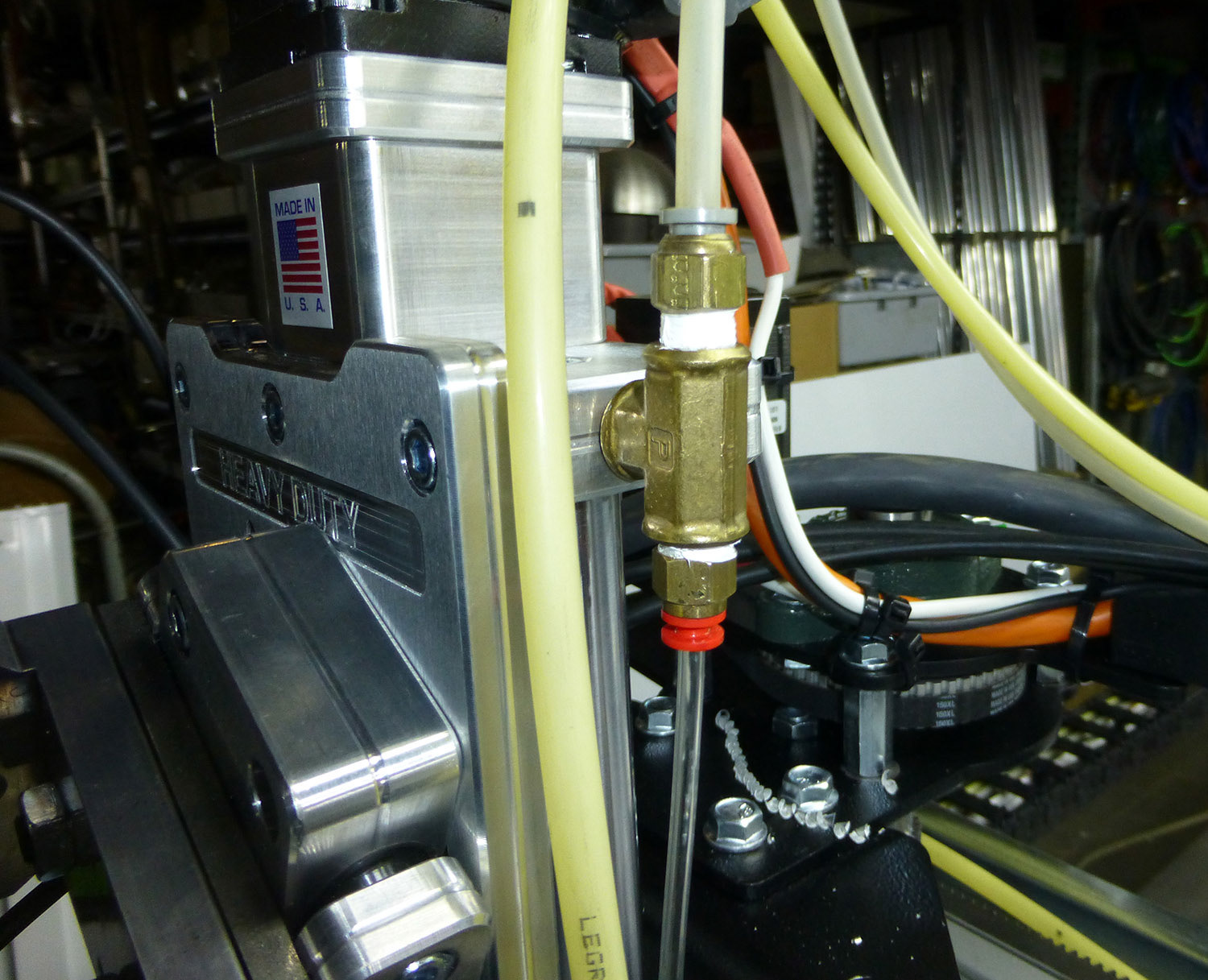
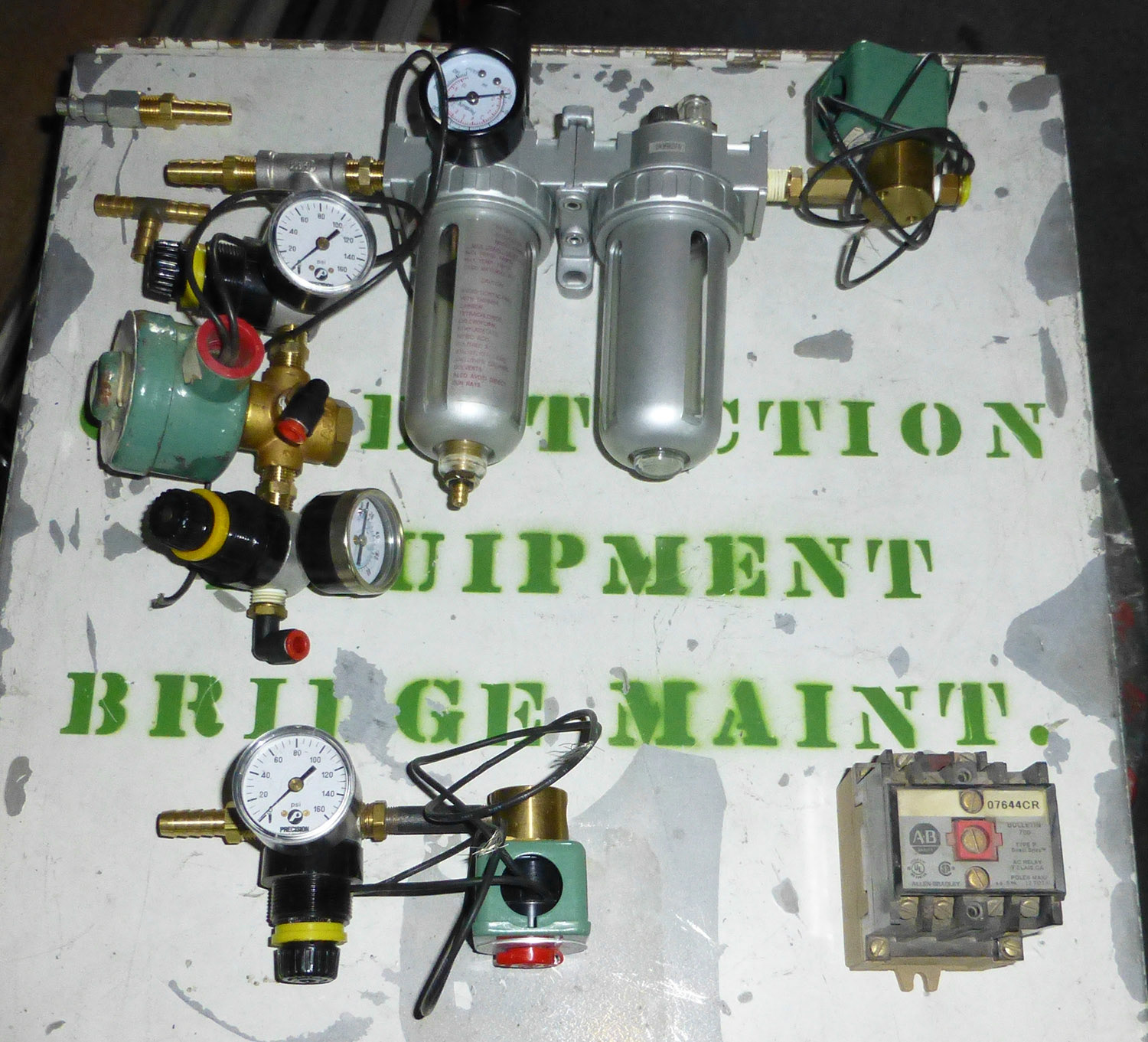
Moving on, I had to install all the wiring and the plasma torch. Because I also planned on using the table as a CNC router, I had run power for it also. Additionally, I installed a coolant system that would provide mist cooling so I can router cut aluminum.
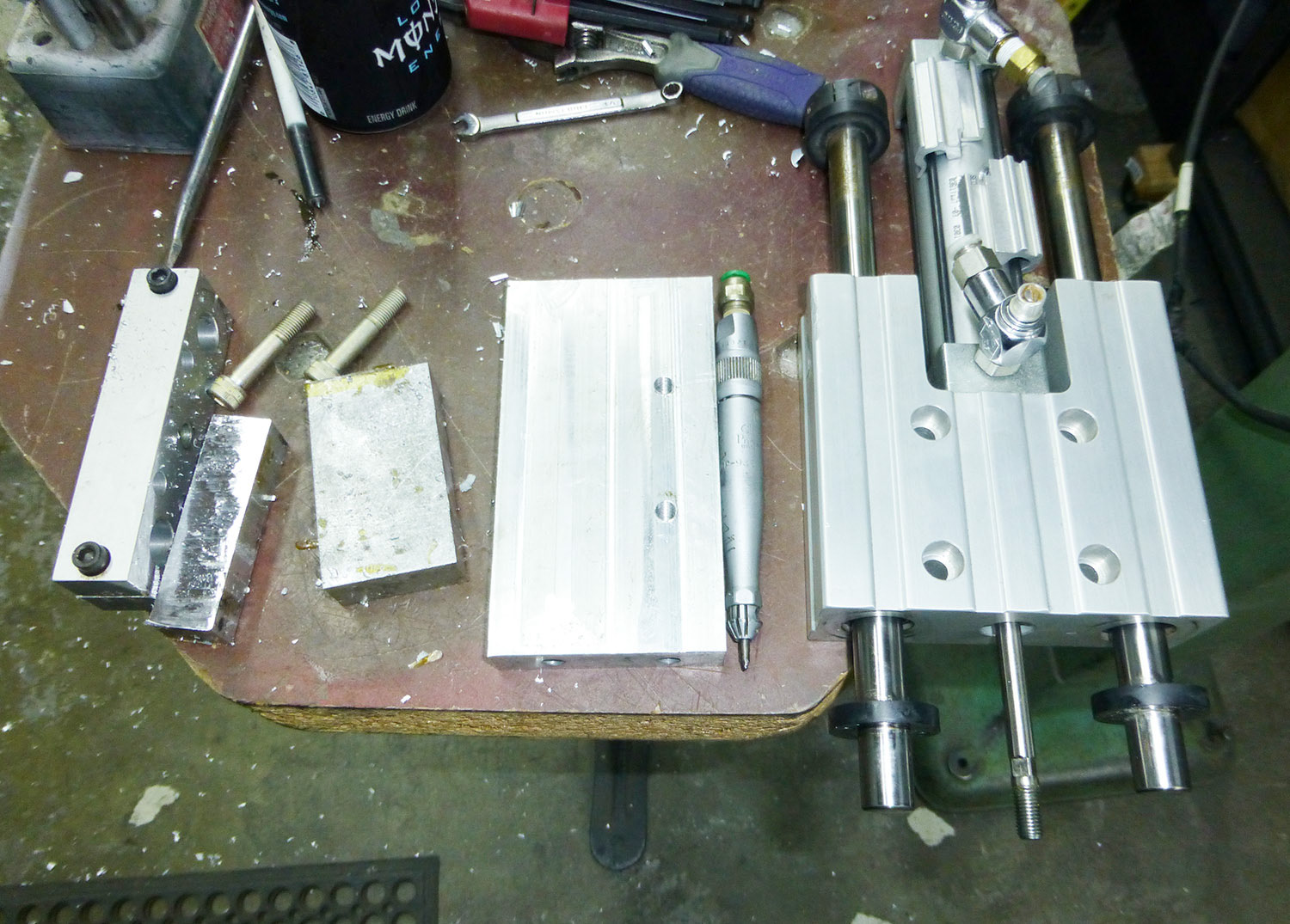
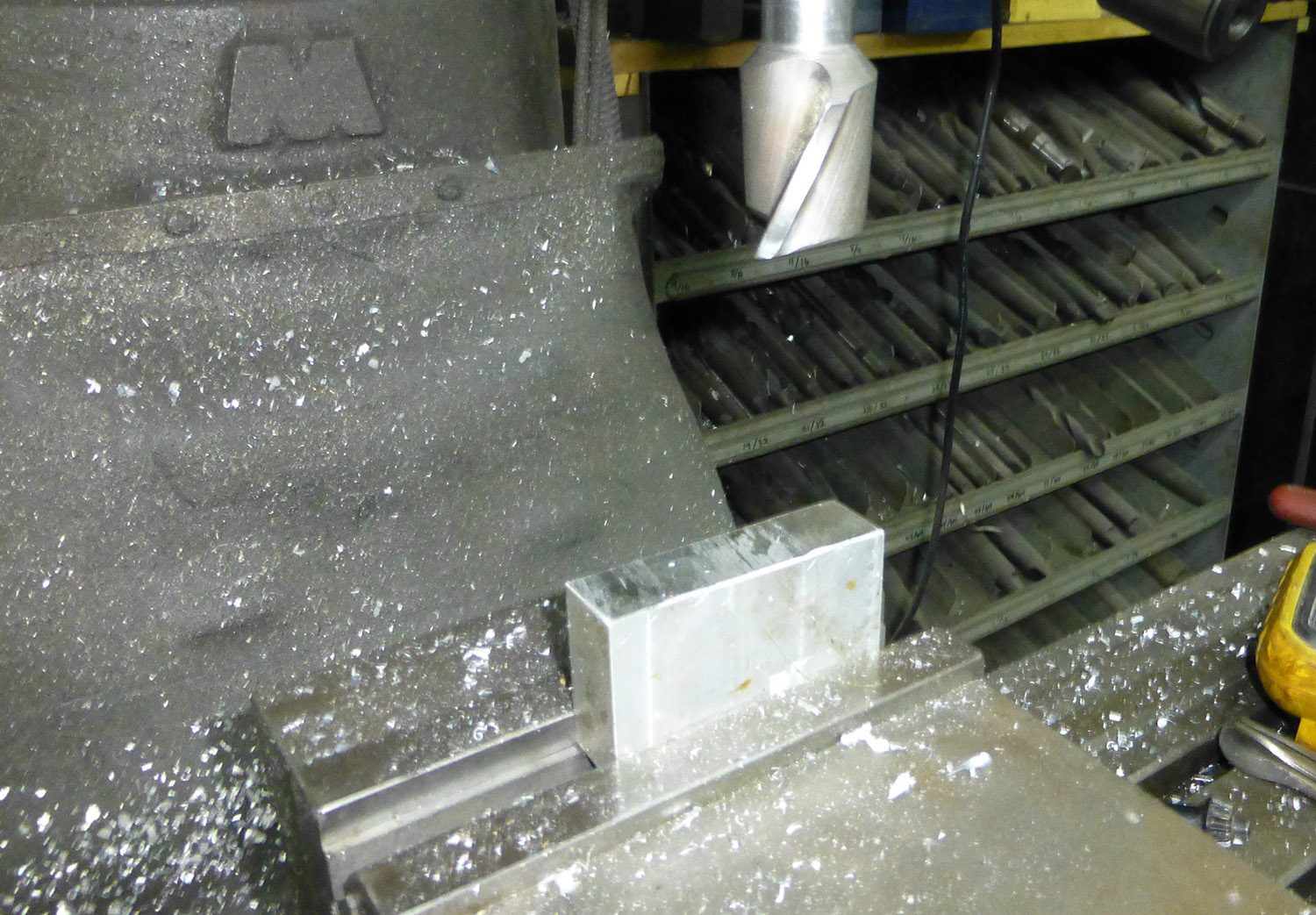
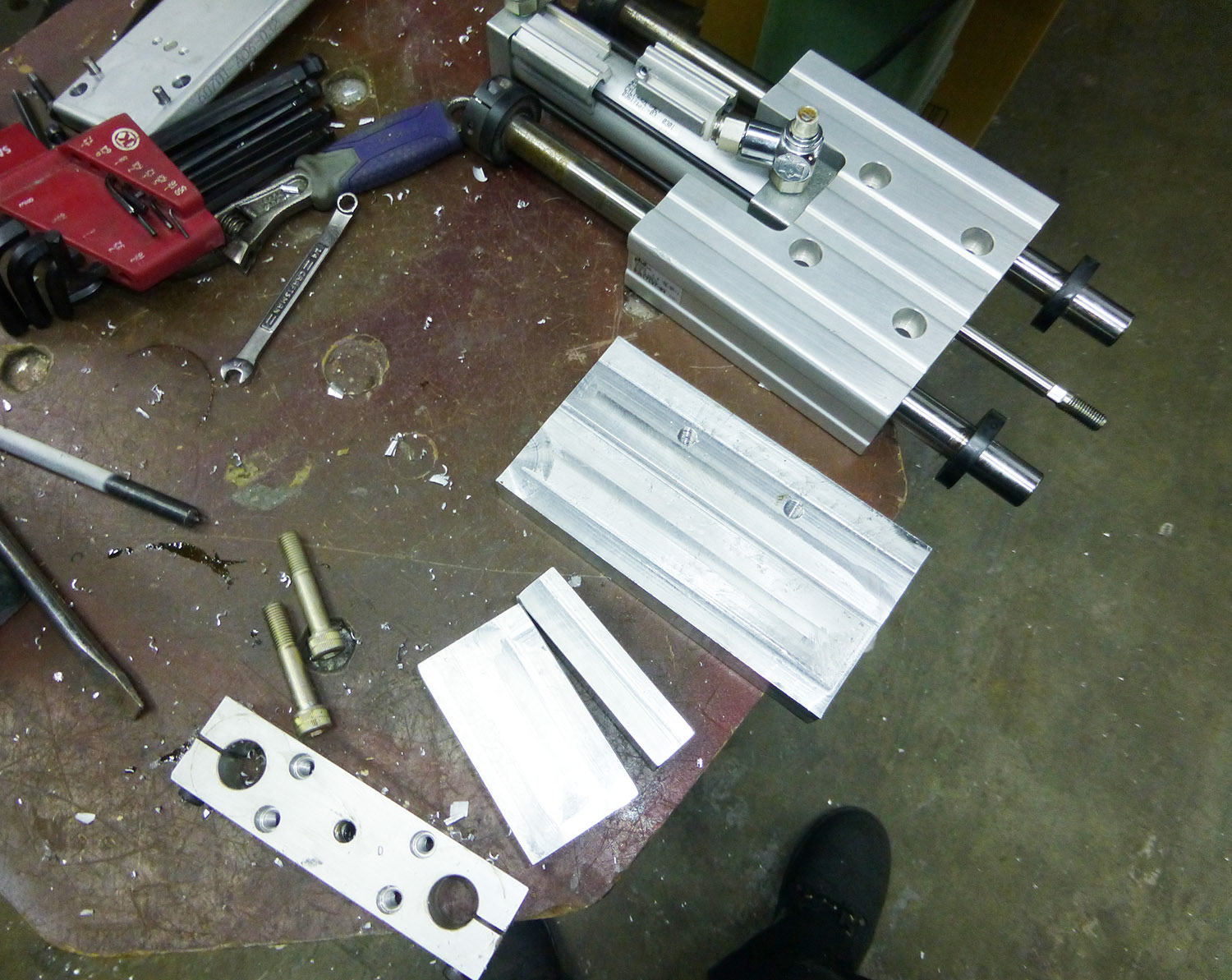
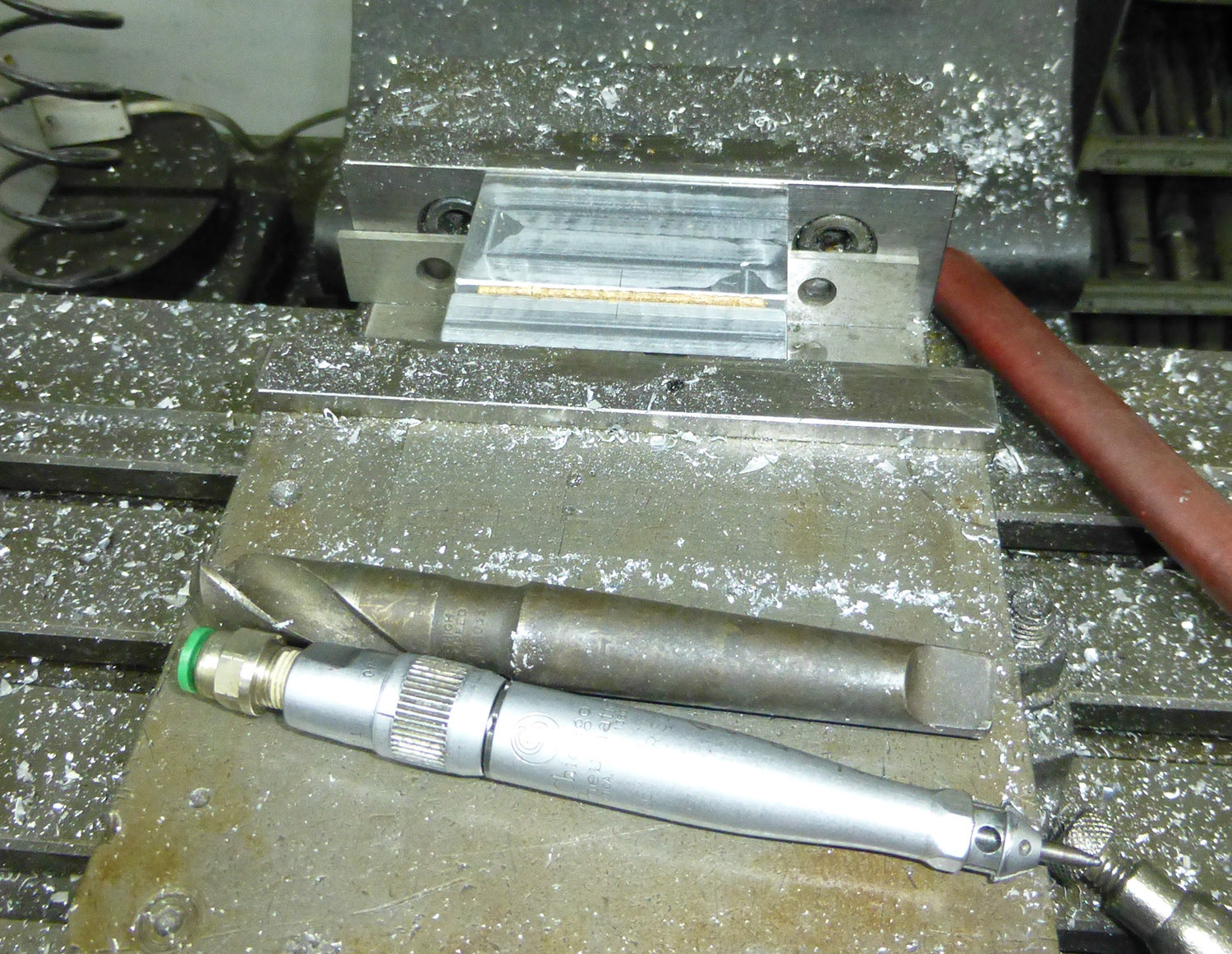
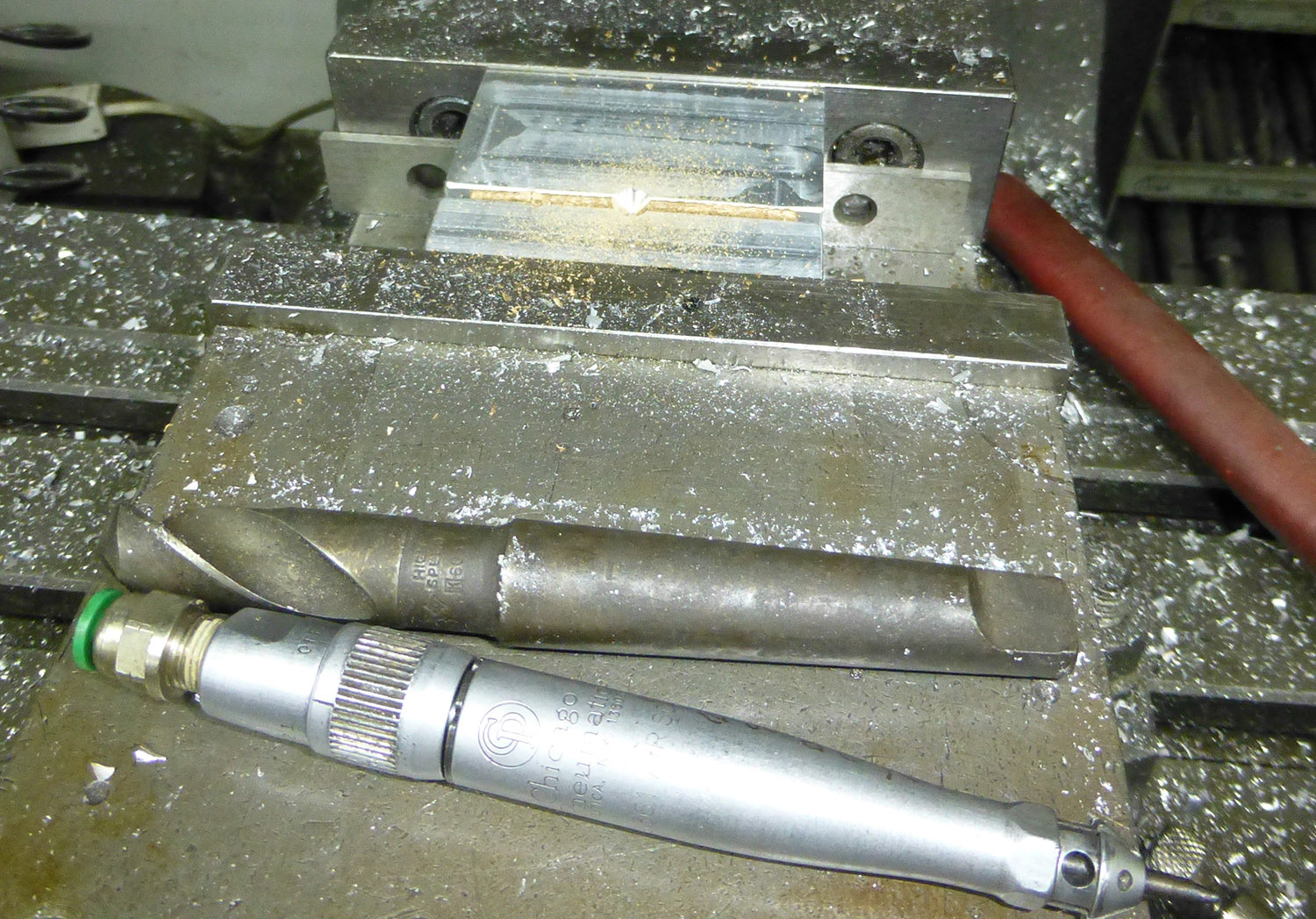
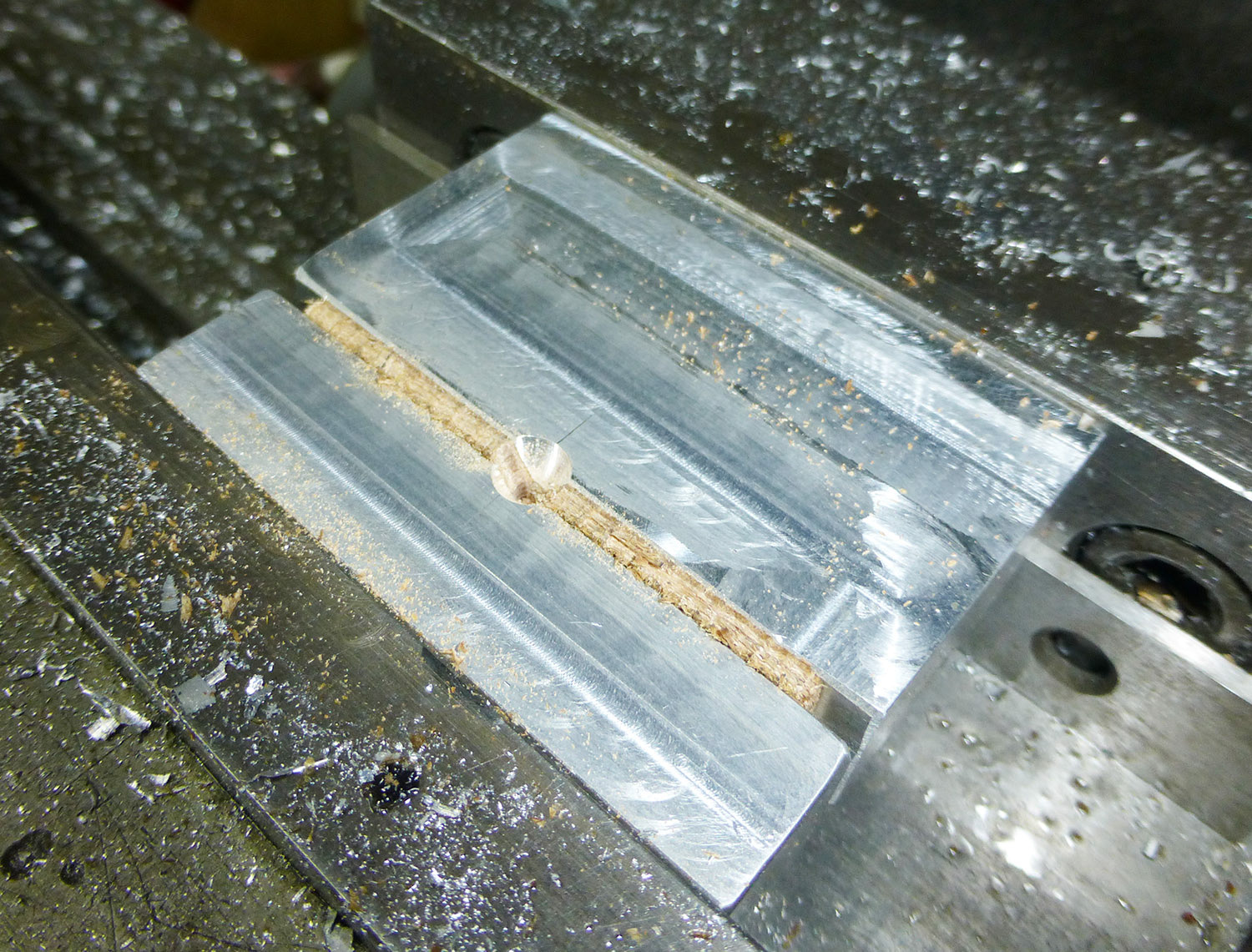
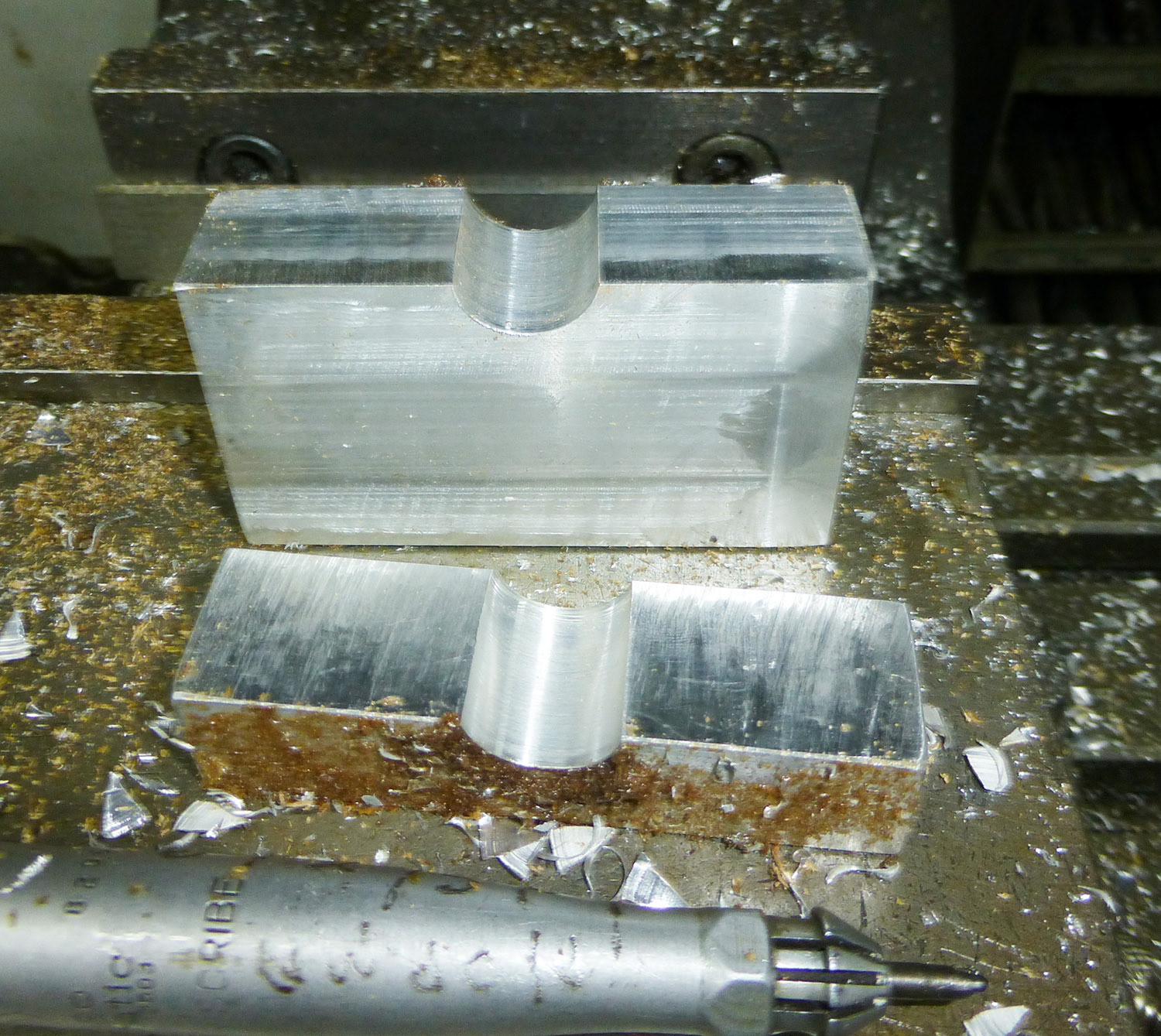
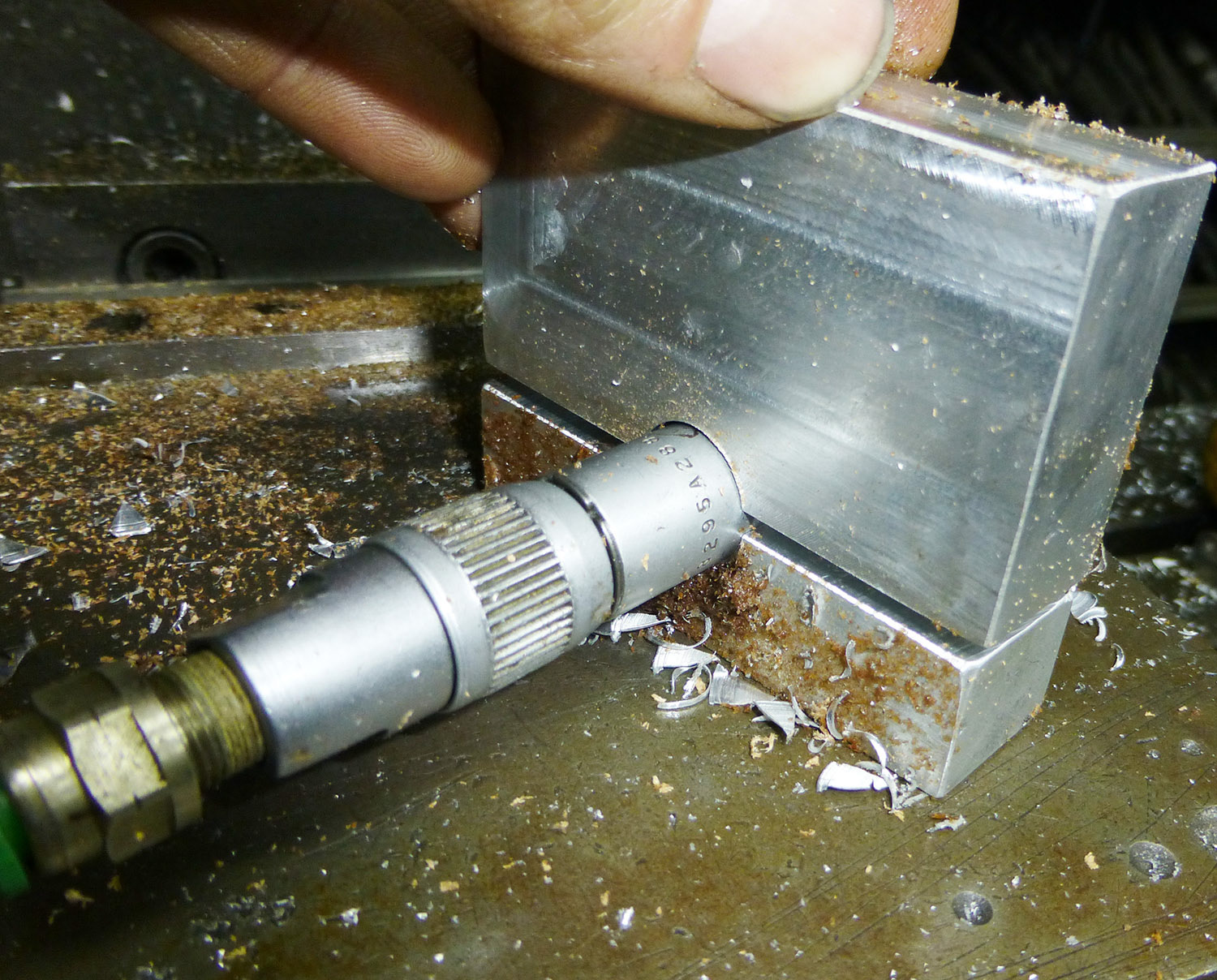
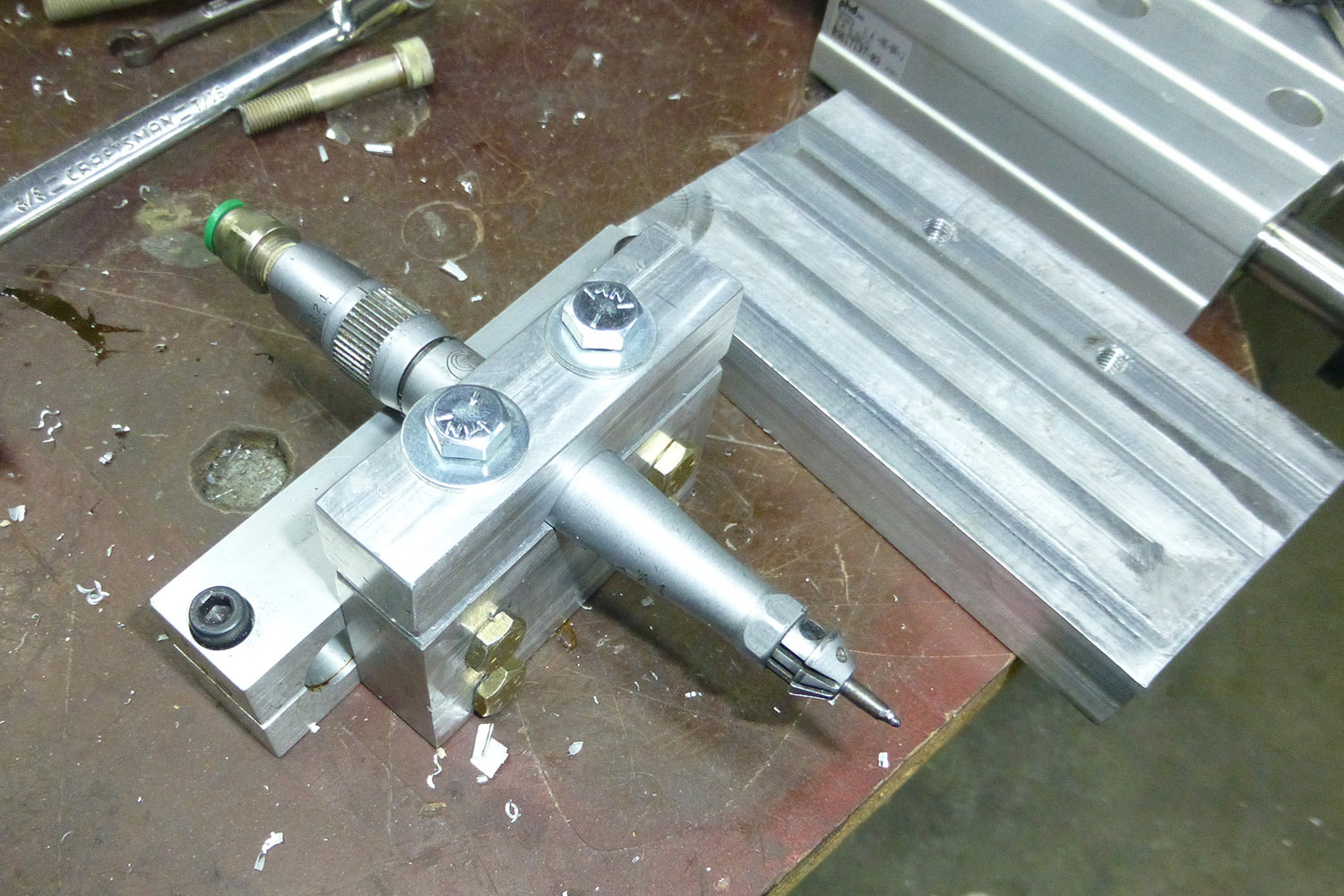
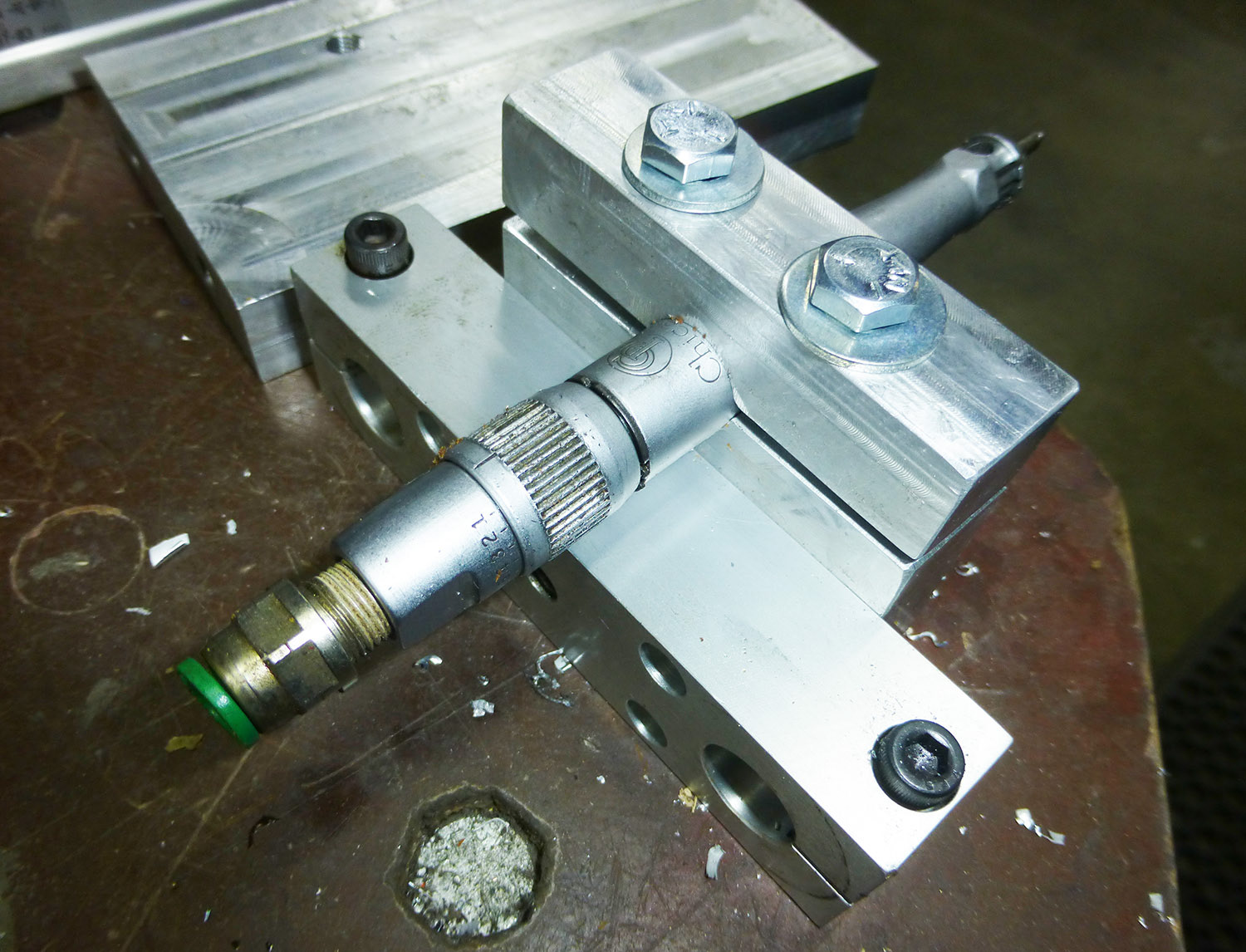

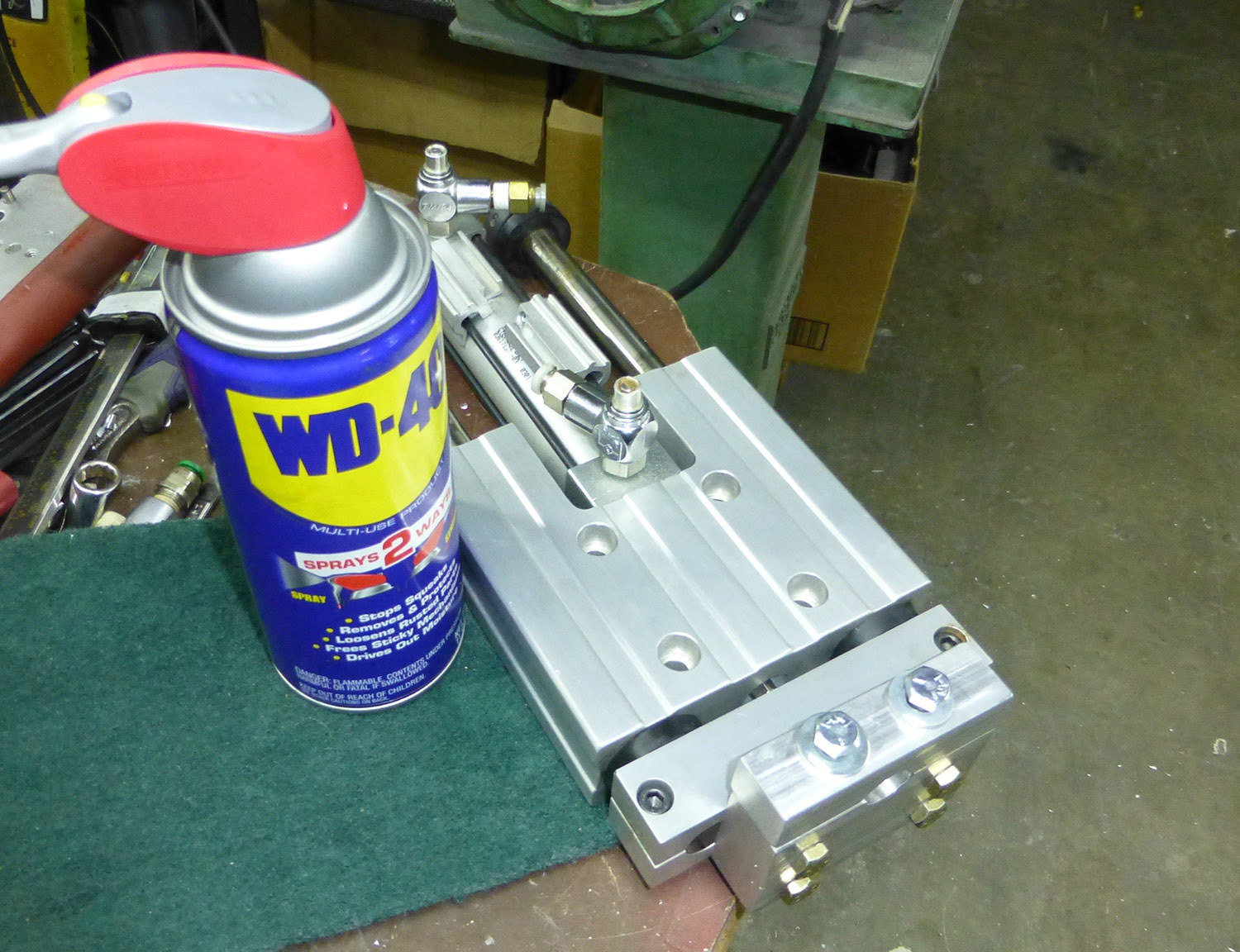
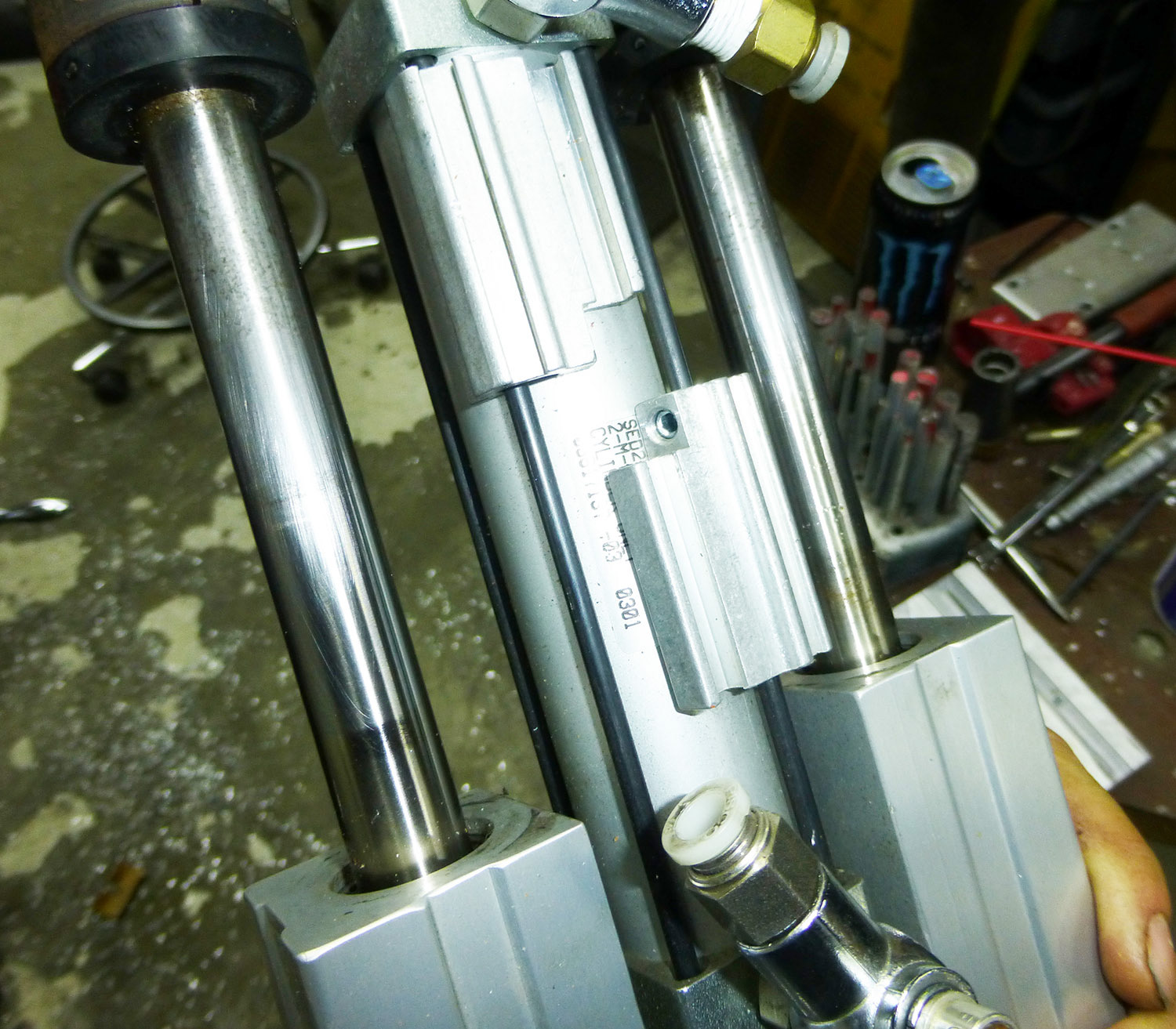
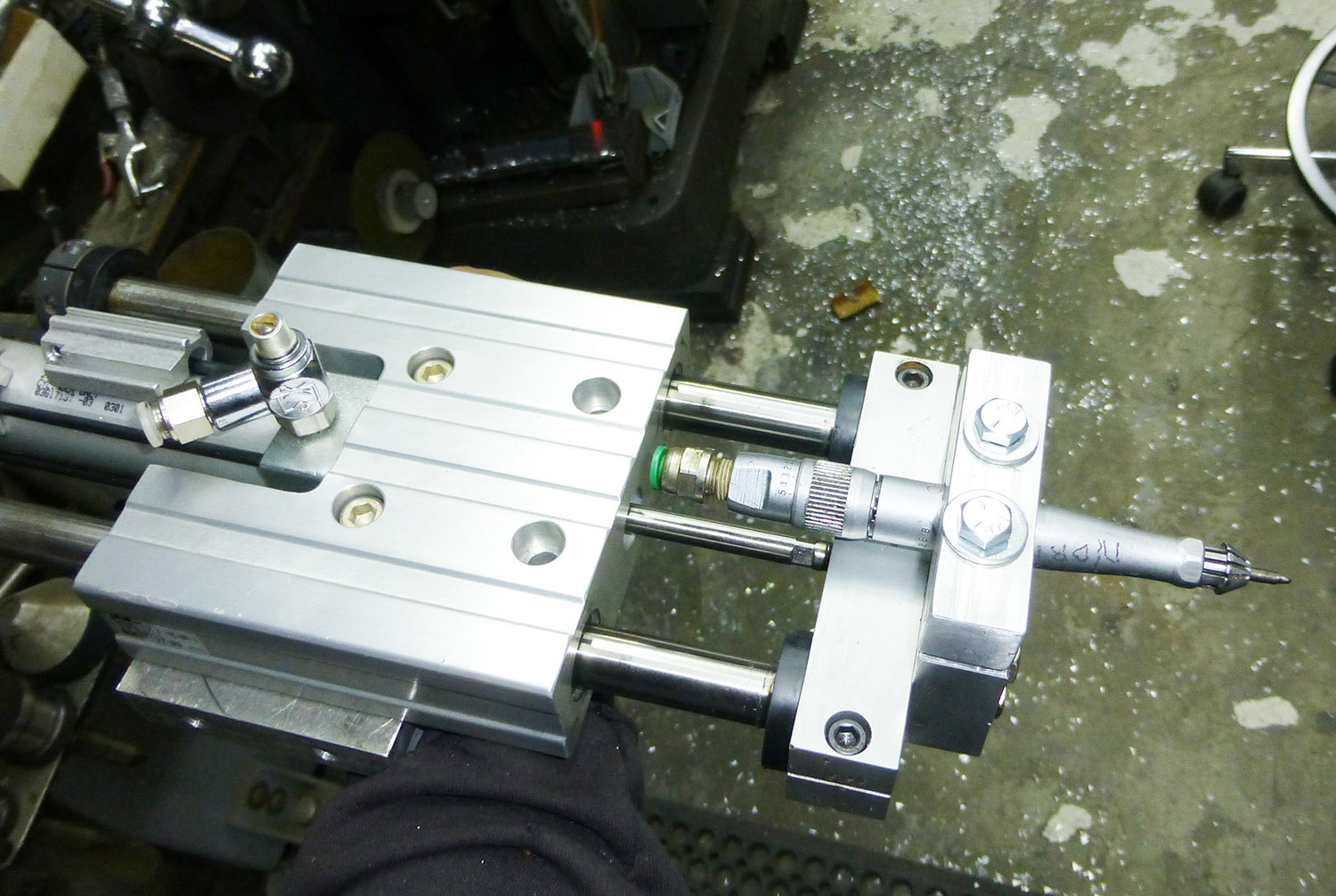
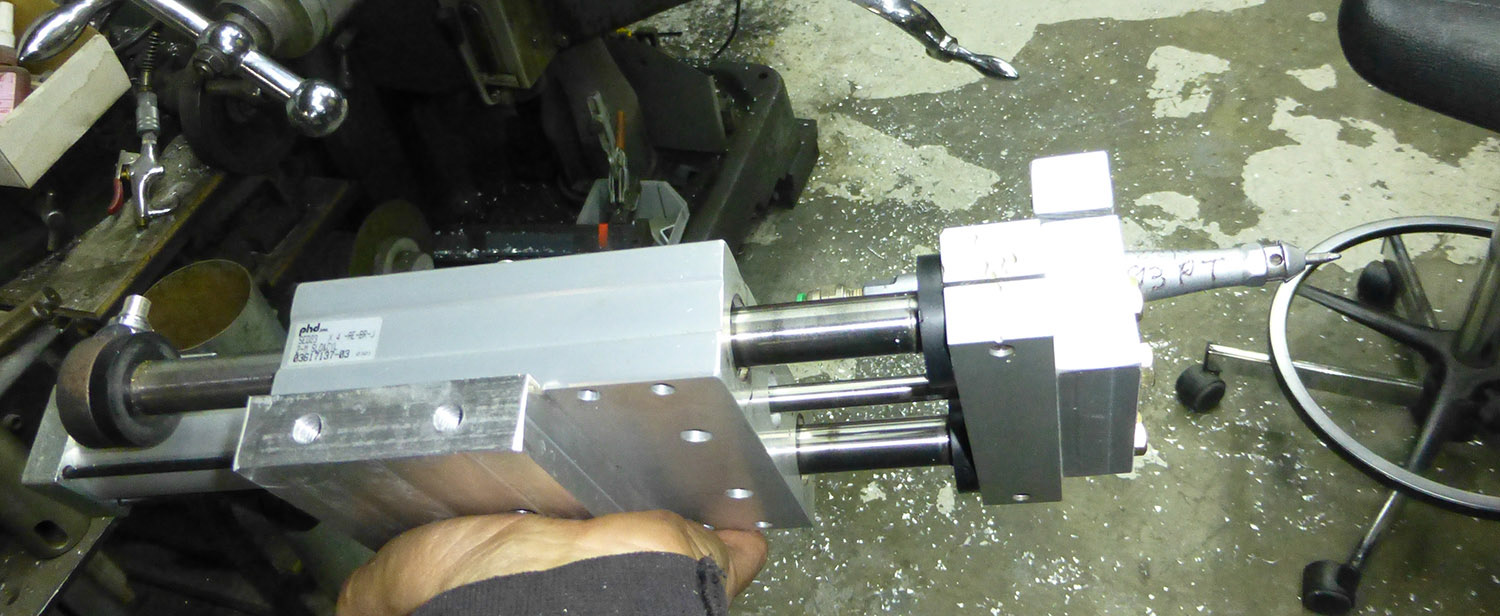
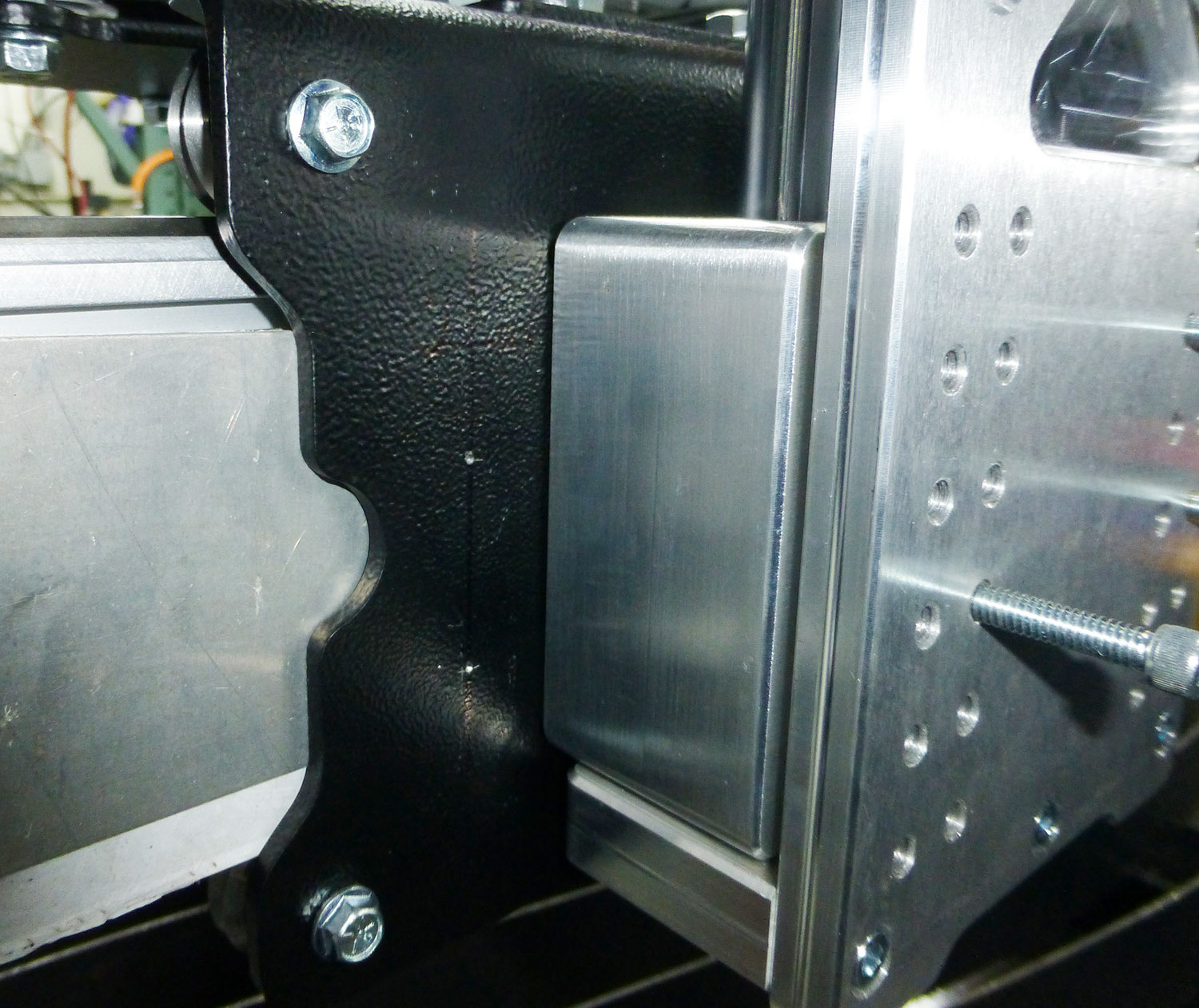
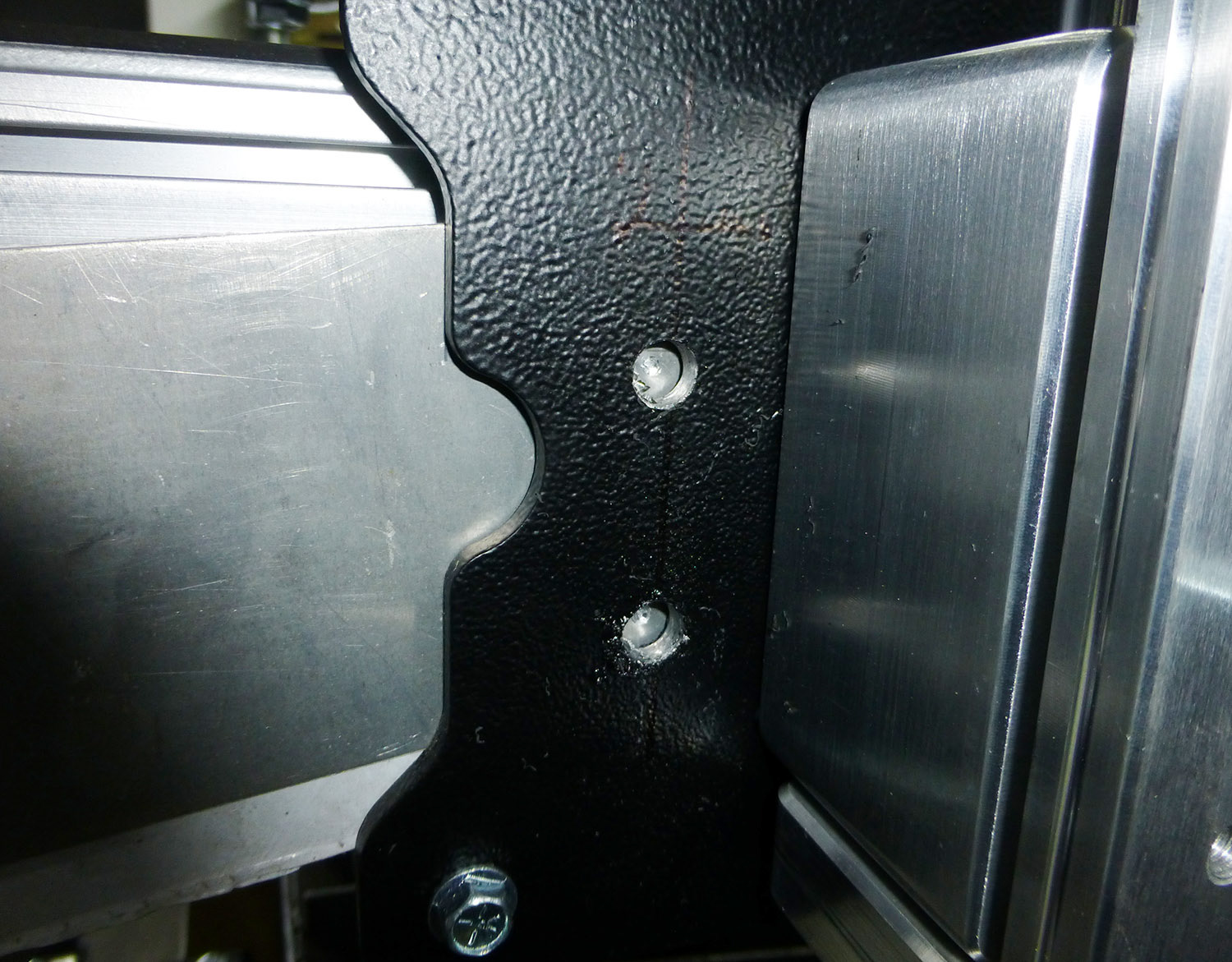
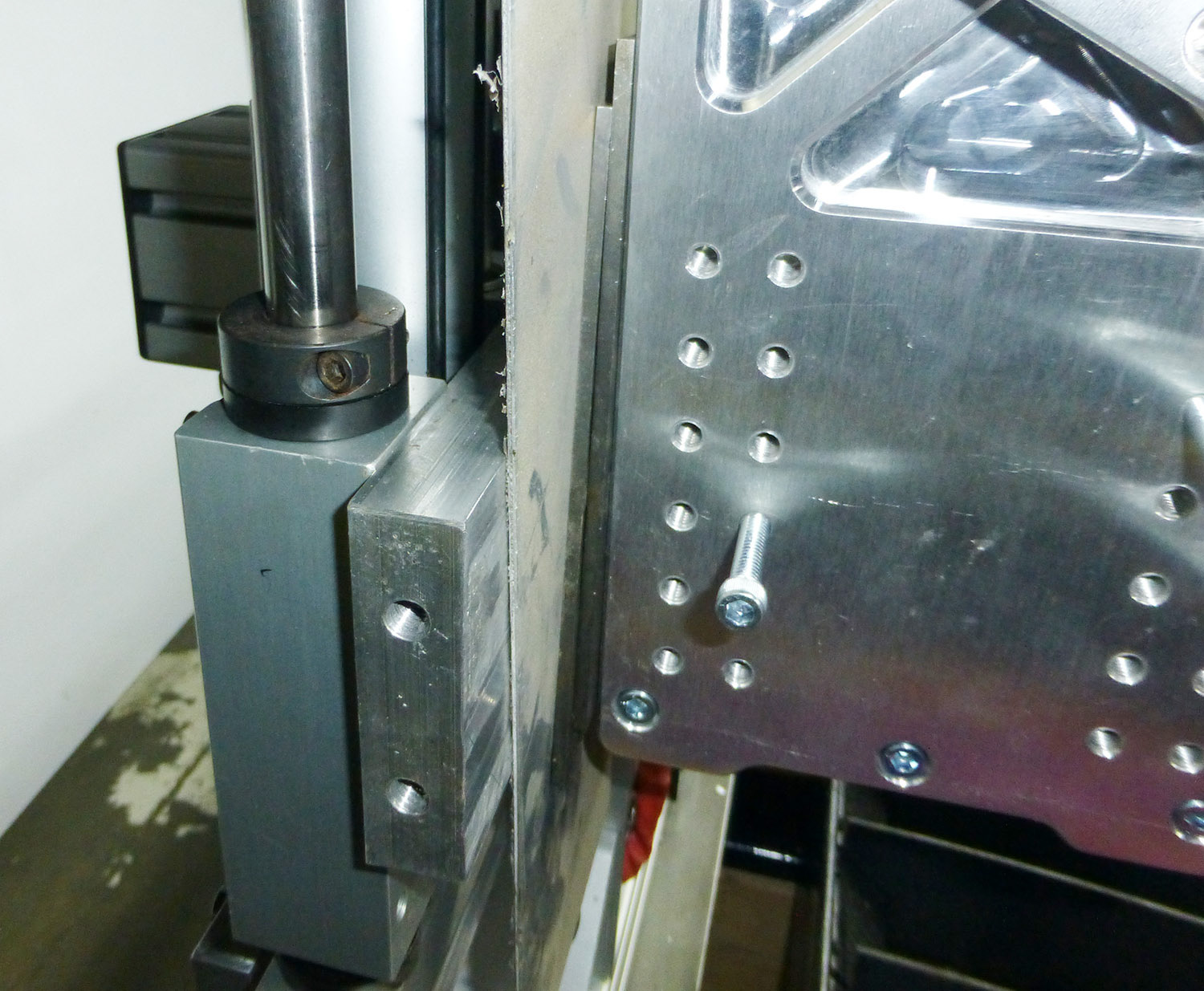
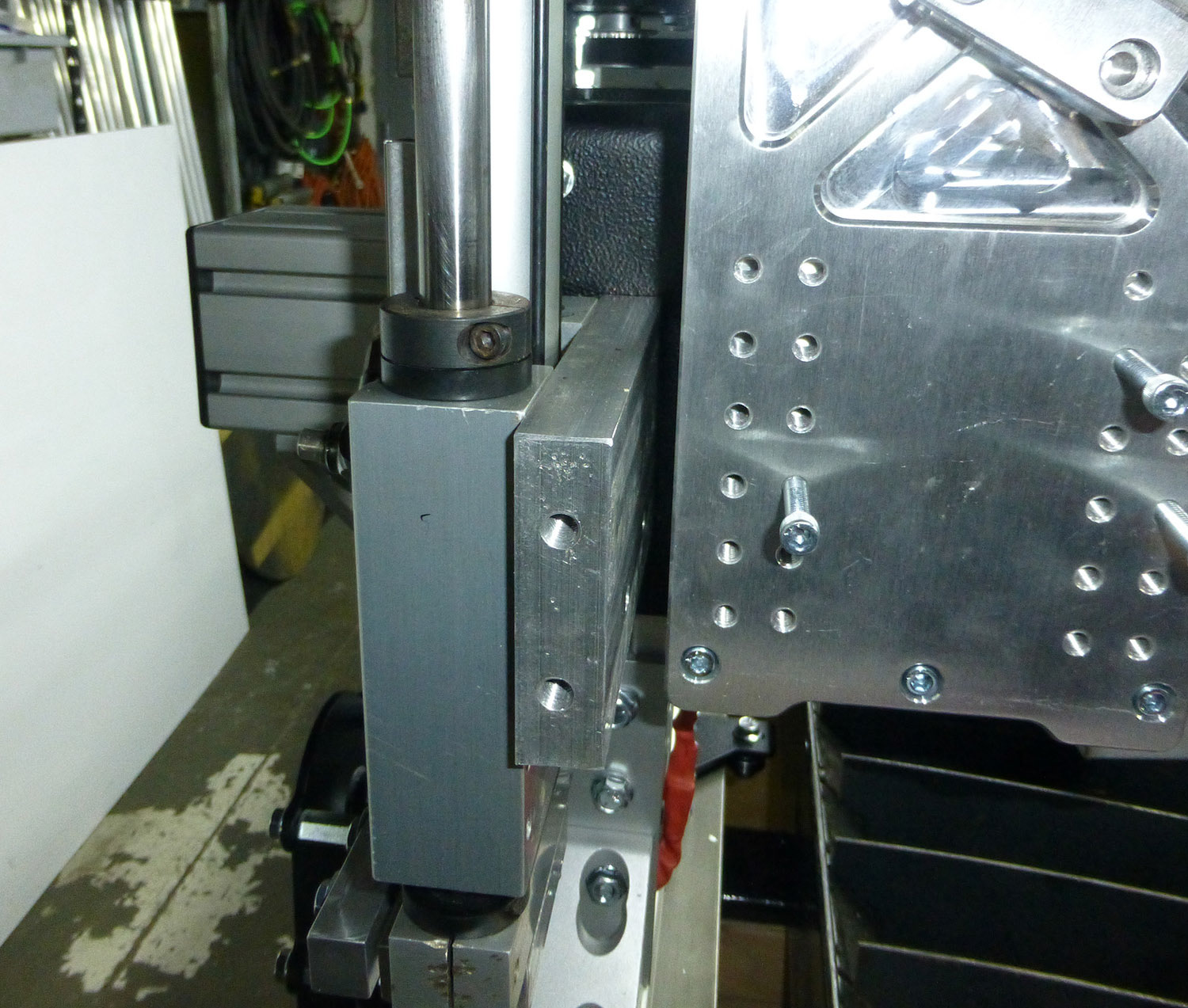
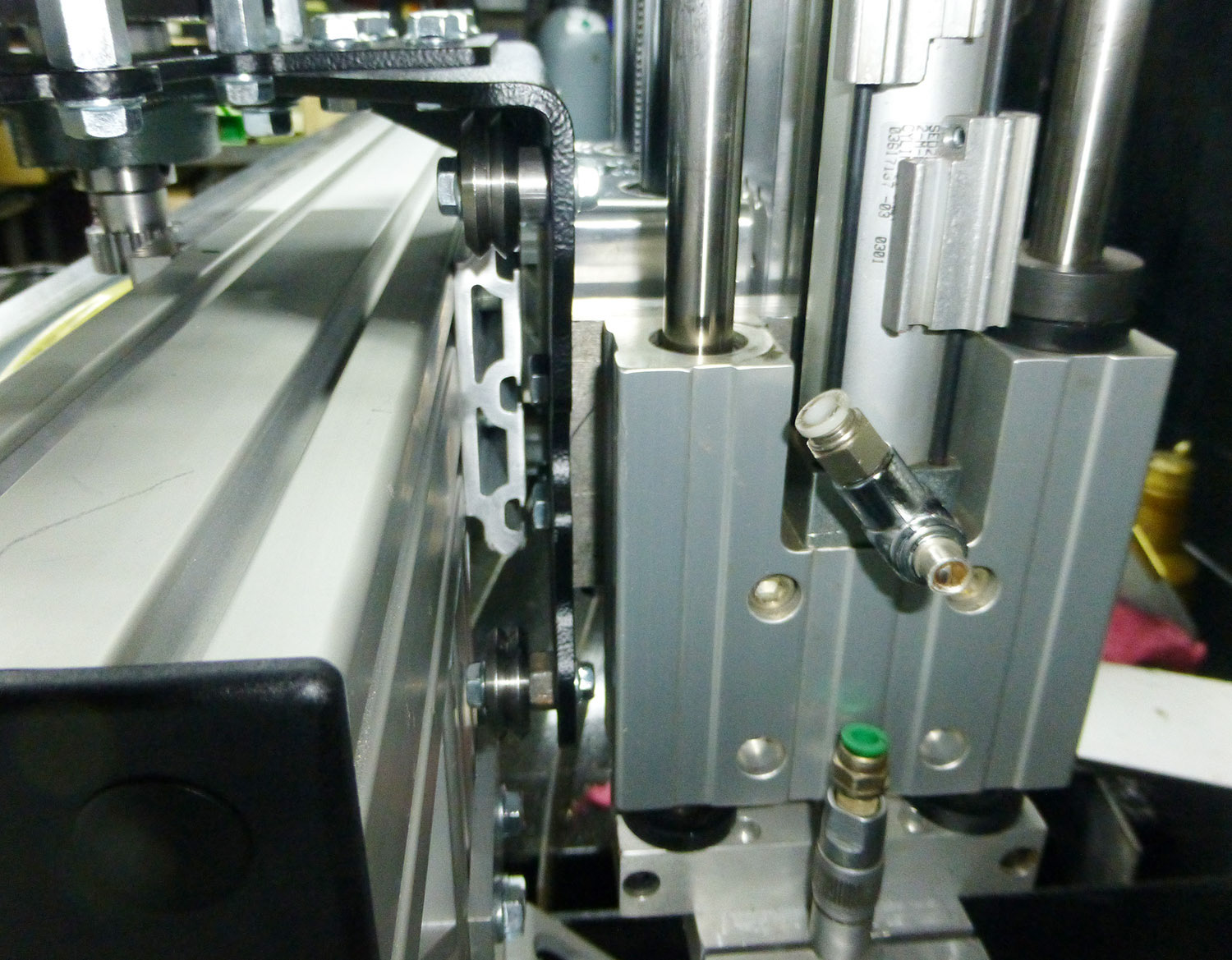
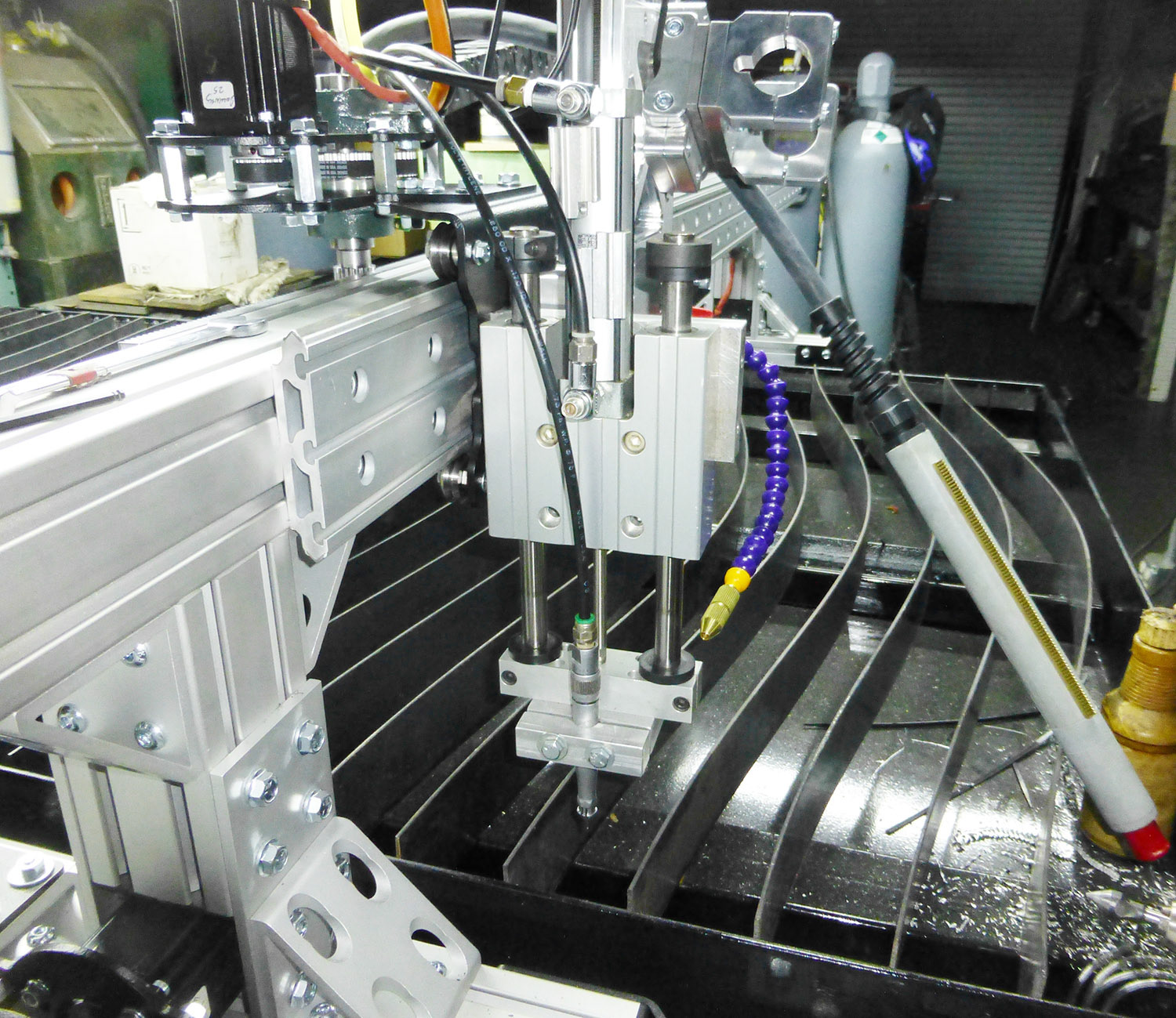
I also wanted to have the functionality of a pneumatic scribe so that I could mark metal. To do so, I had to add an additional linear actuator that would move the scribe up and down. There was just enough room on the carriage for me to mount this sideways.
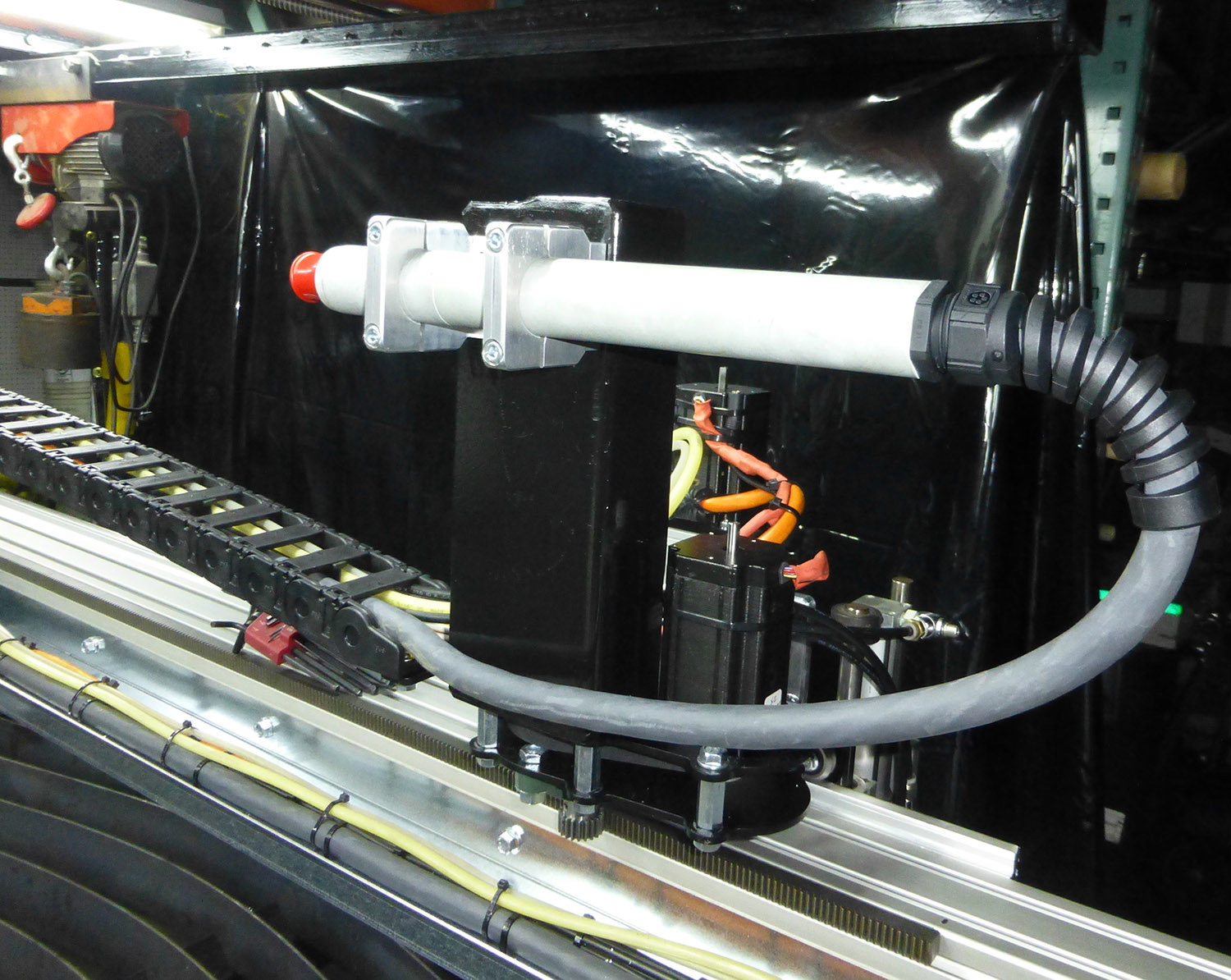
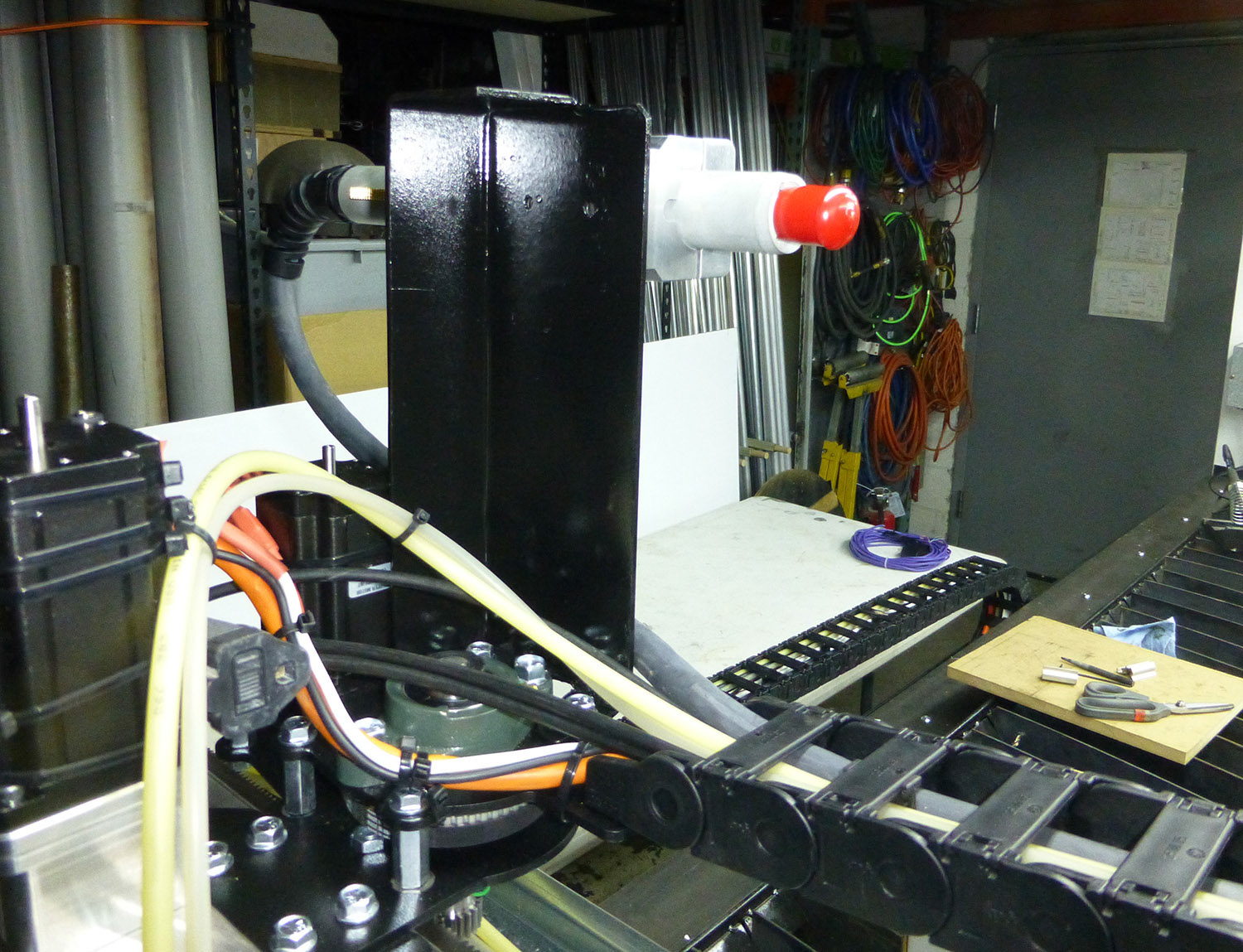
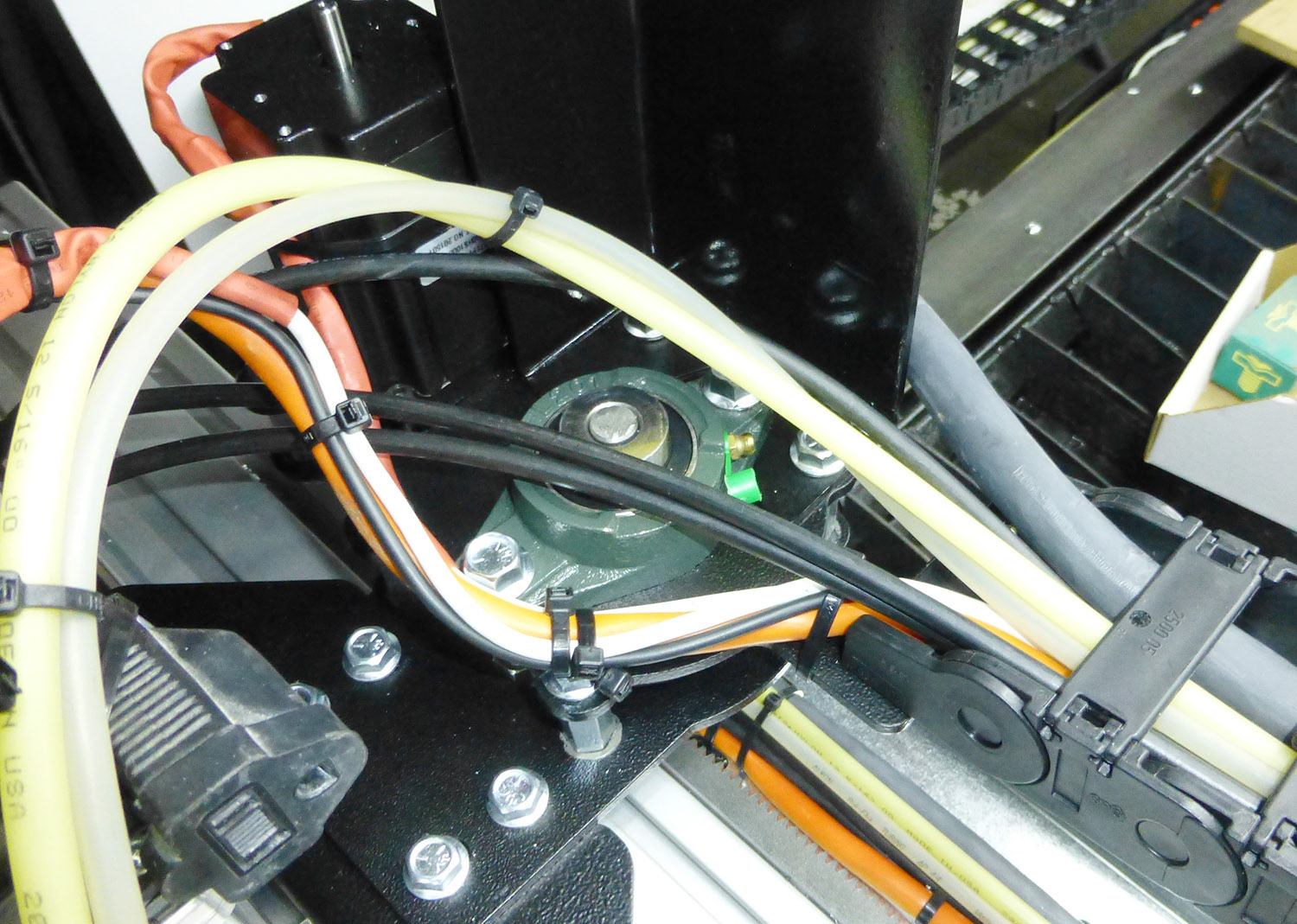
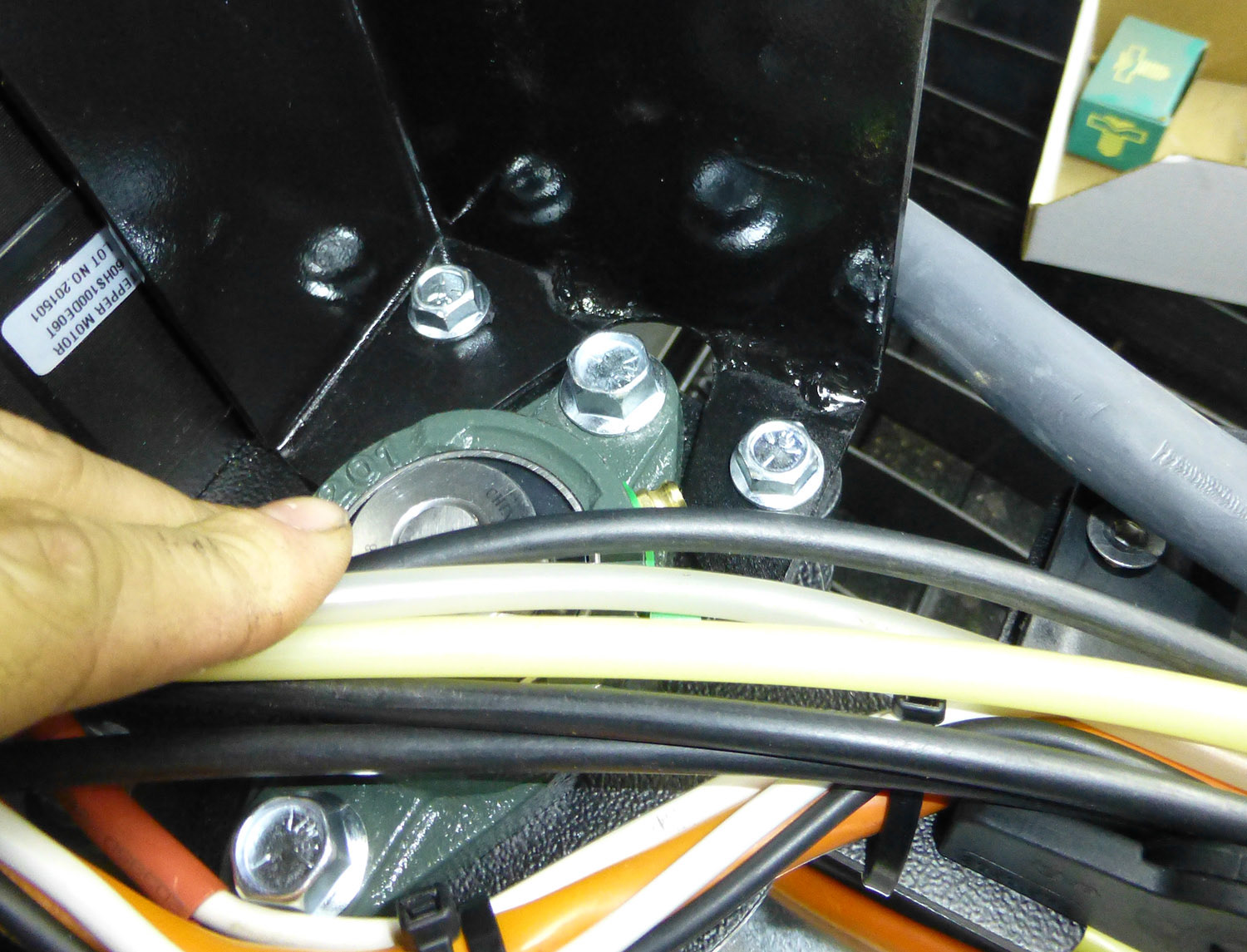
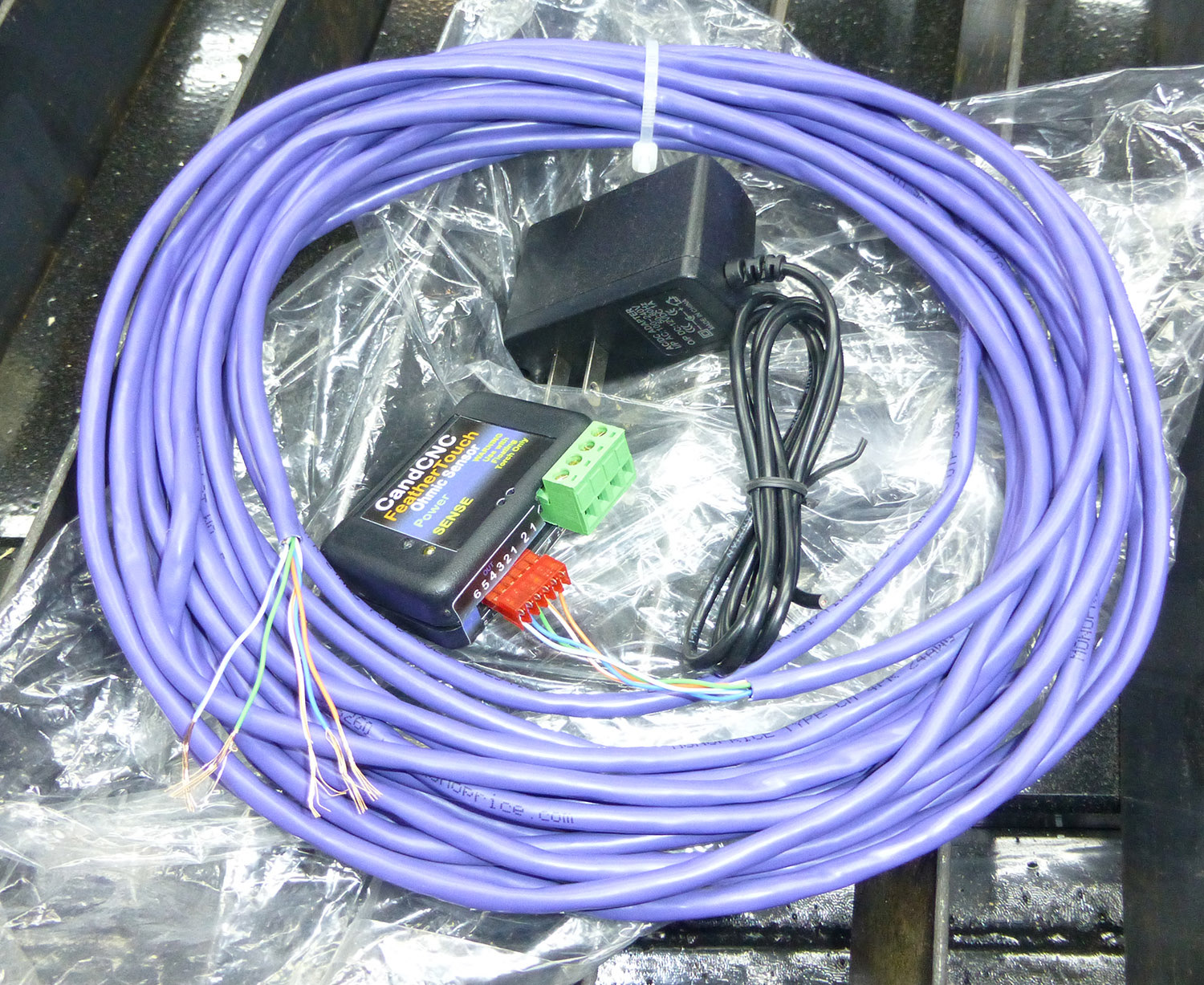
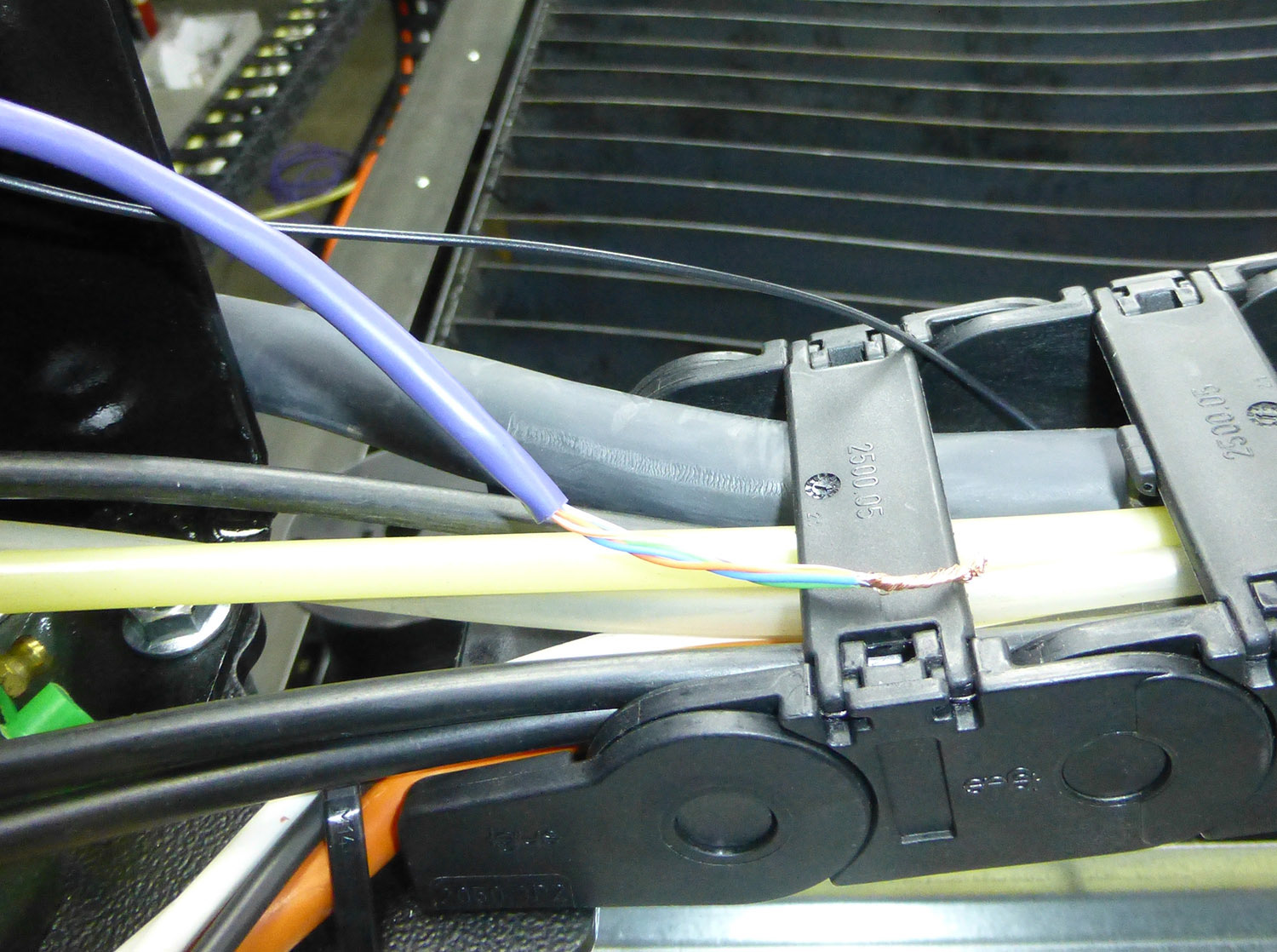
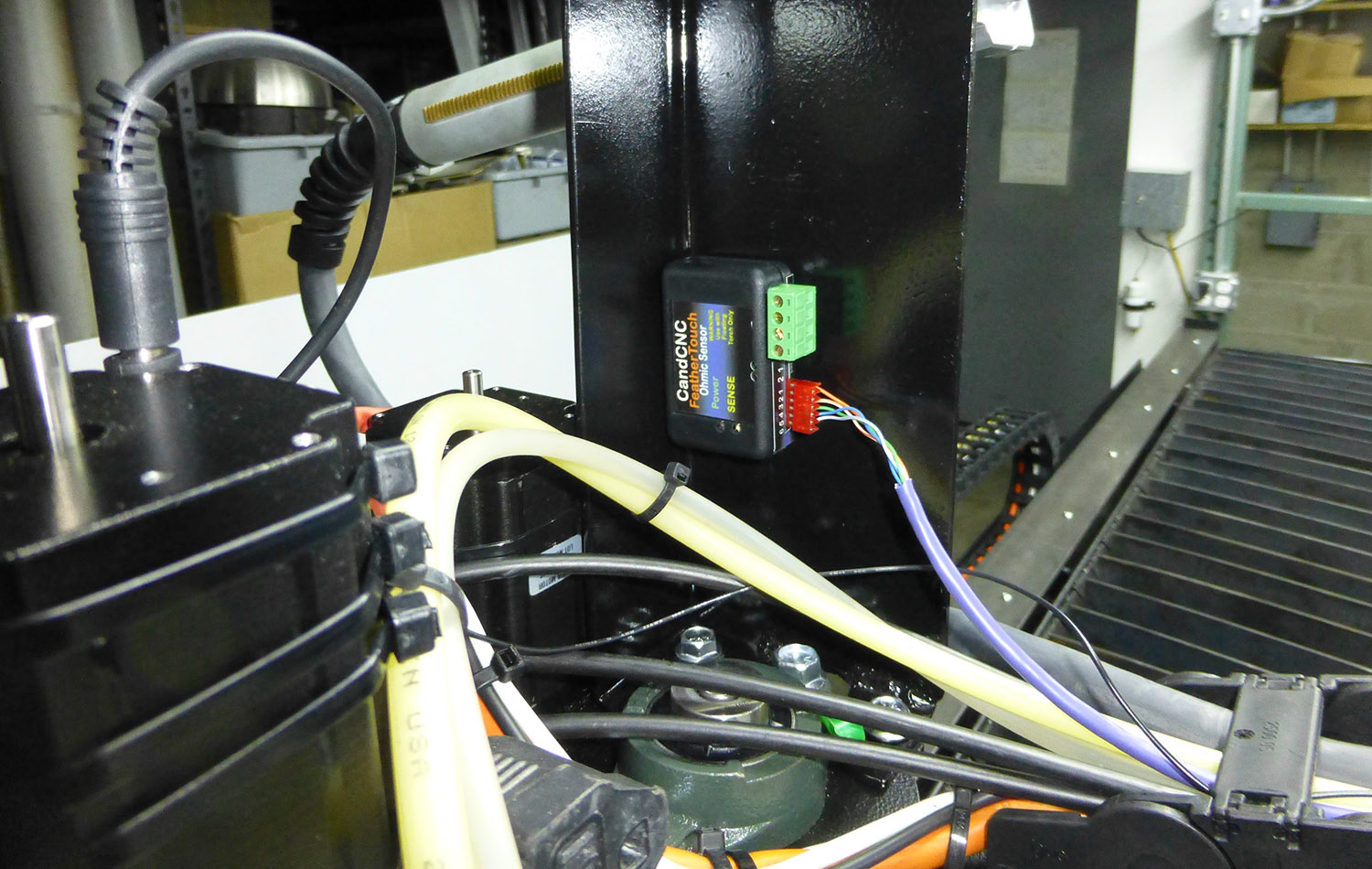
With their scribe installed, I finish the rest of the wiring and plumbing to the carriage.
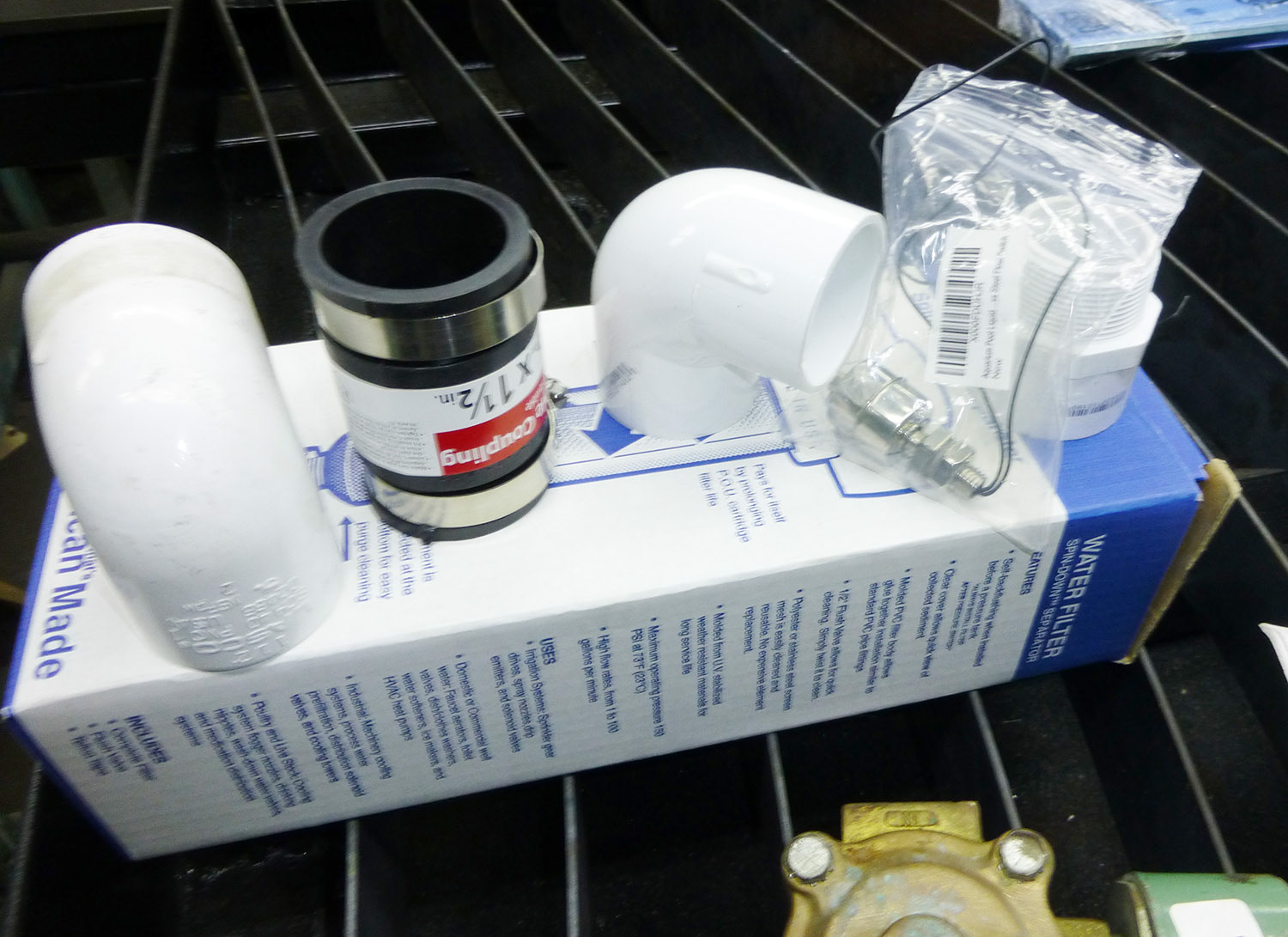
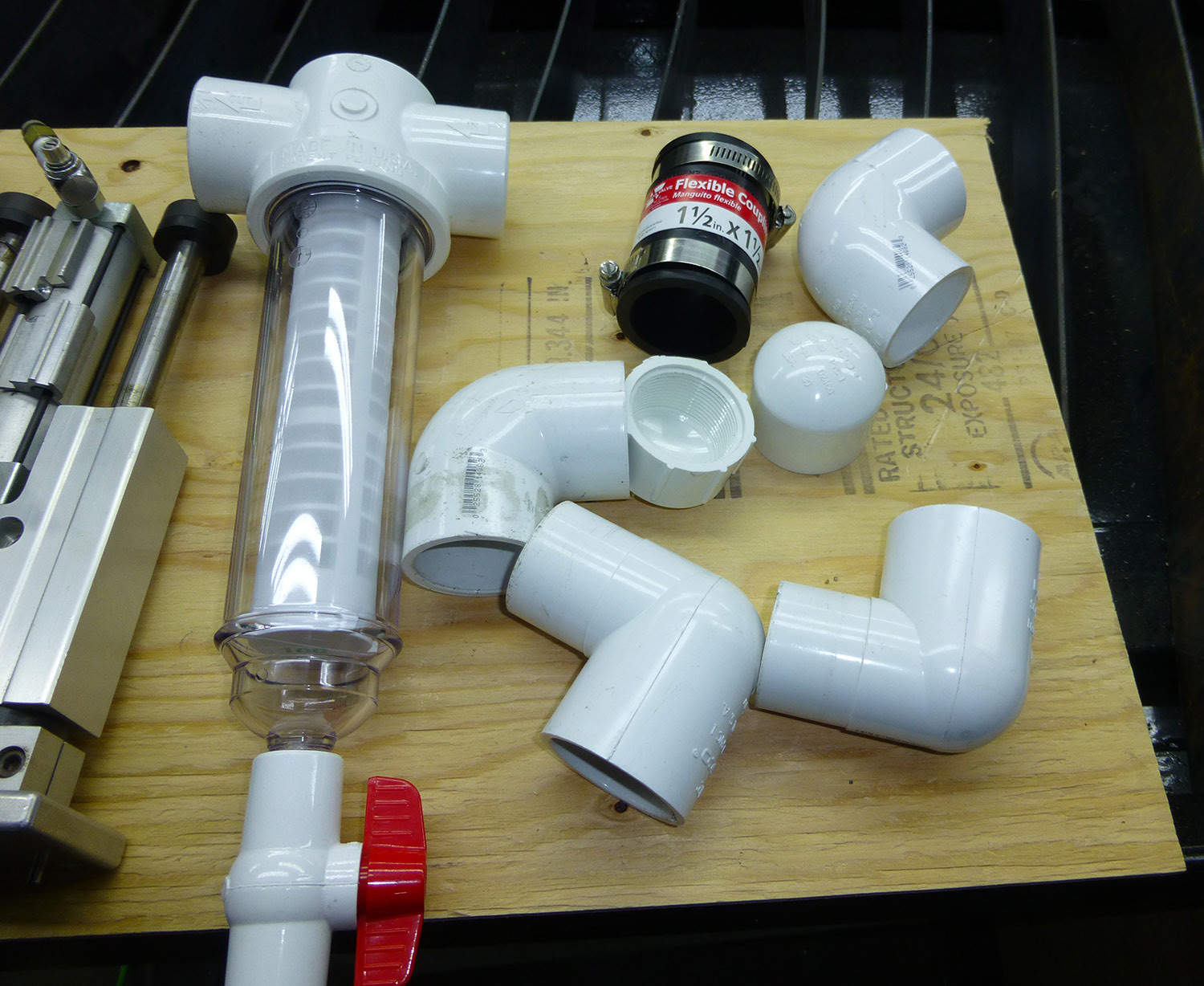
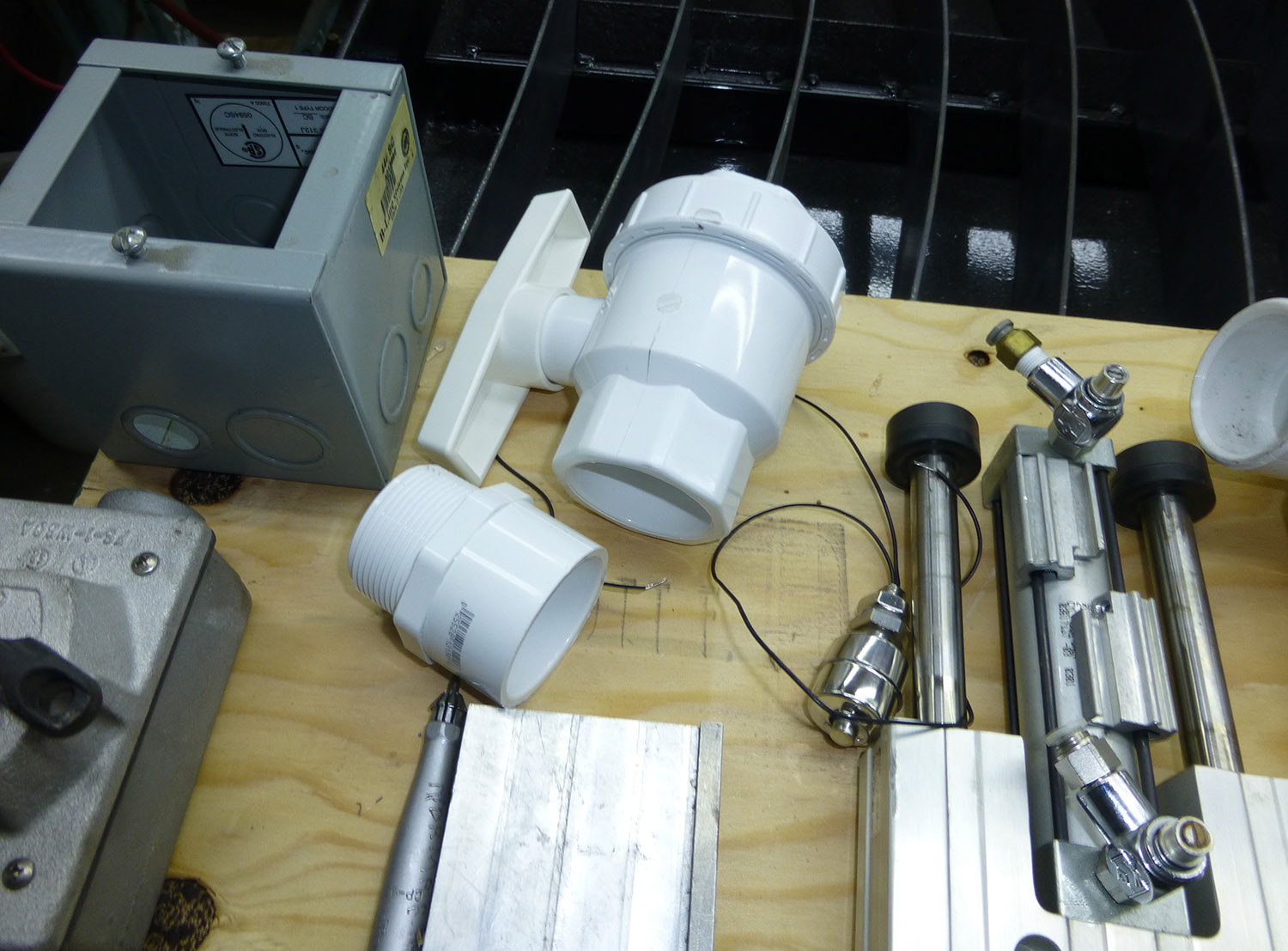
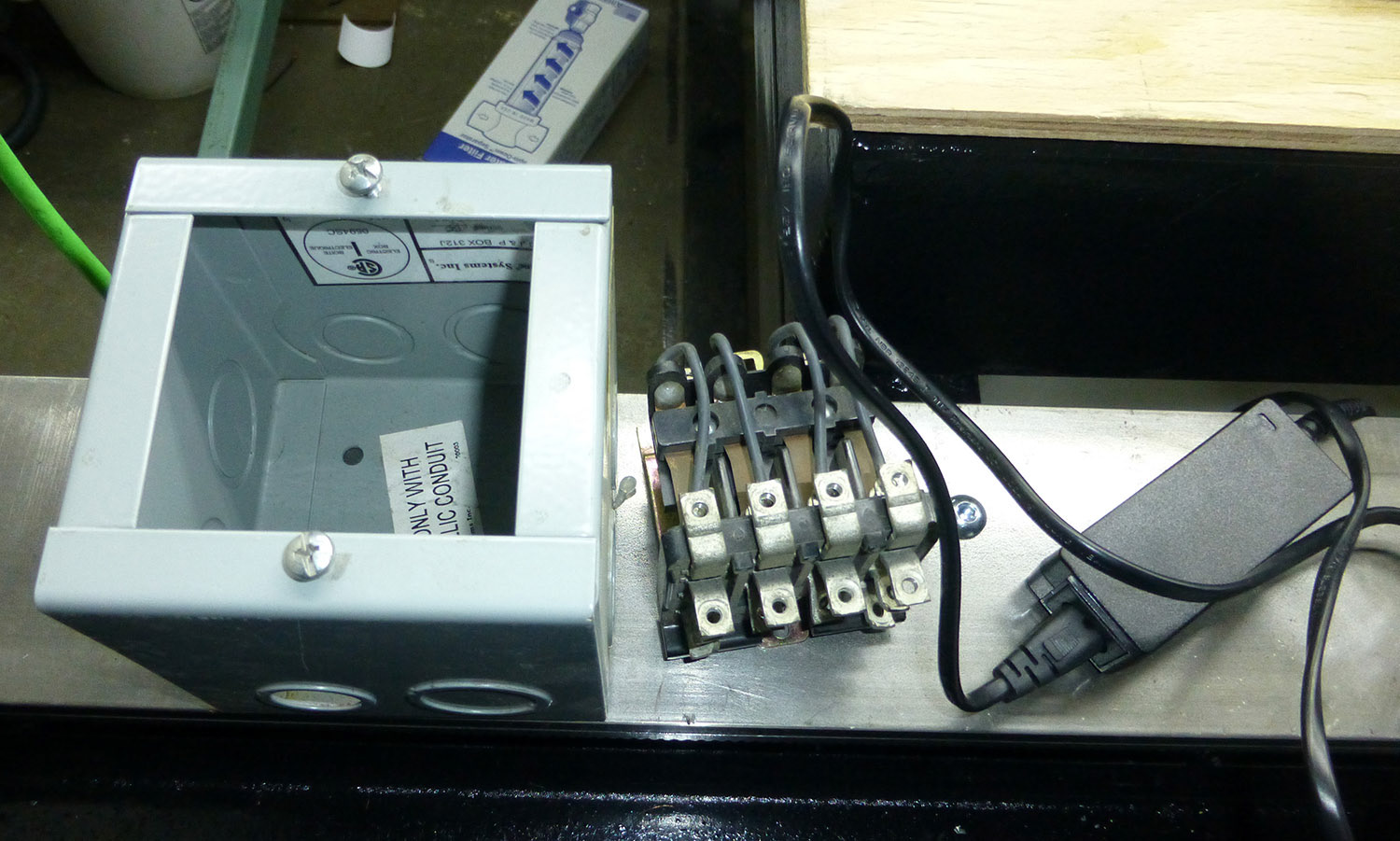
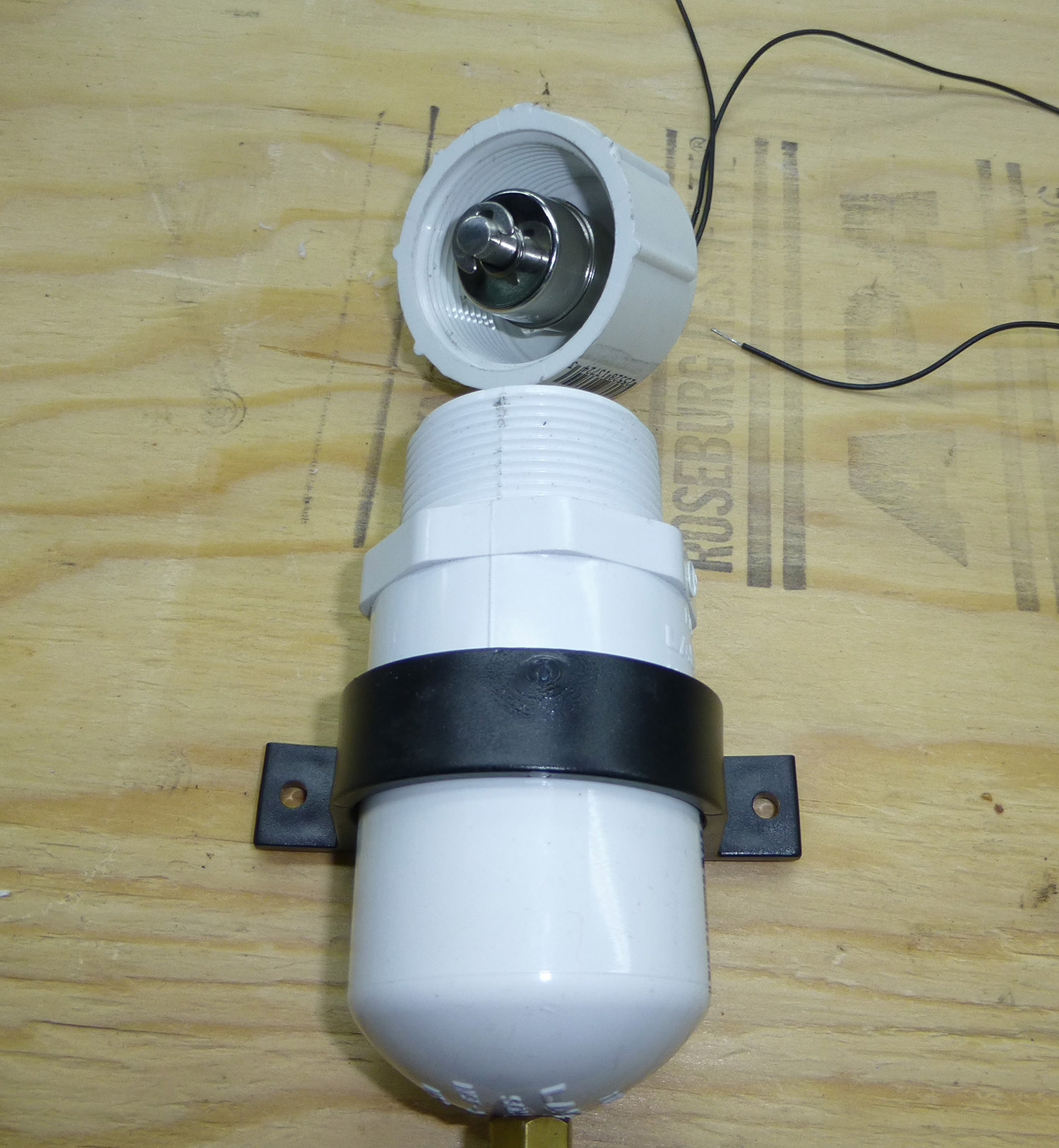
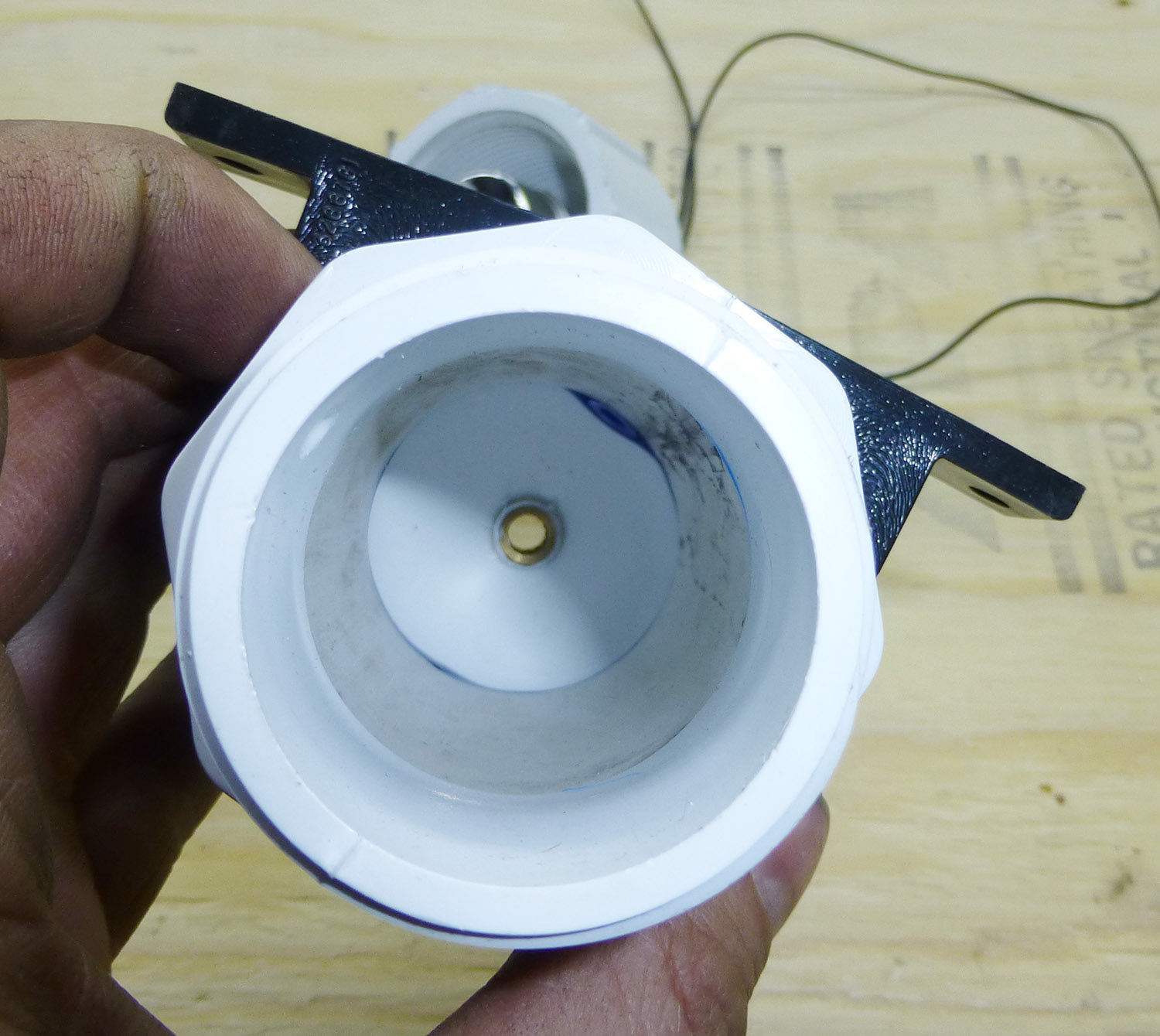
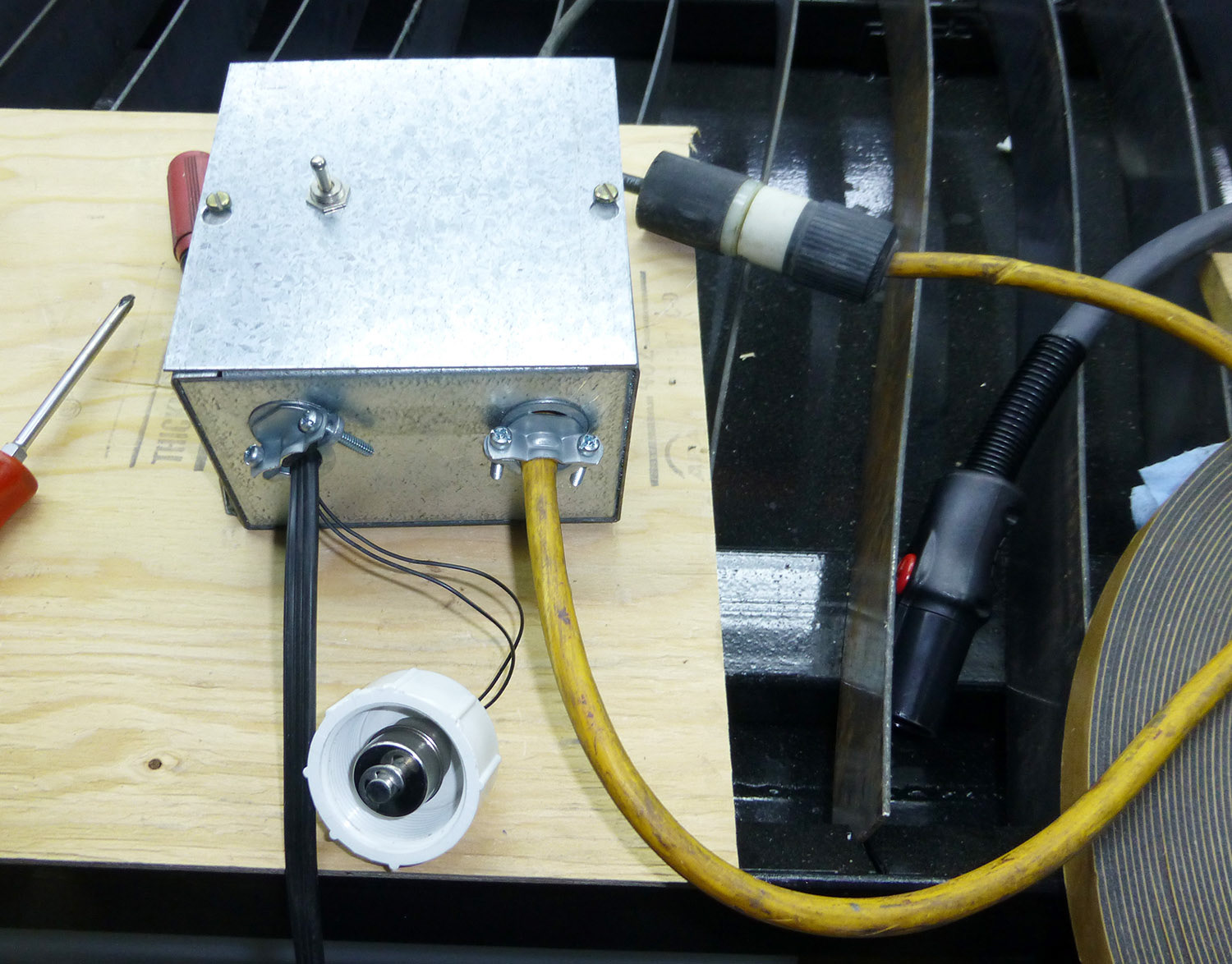
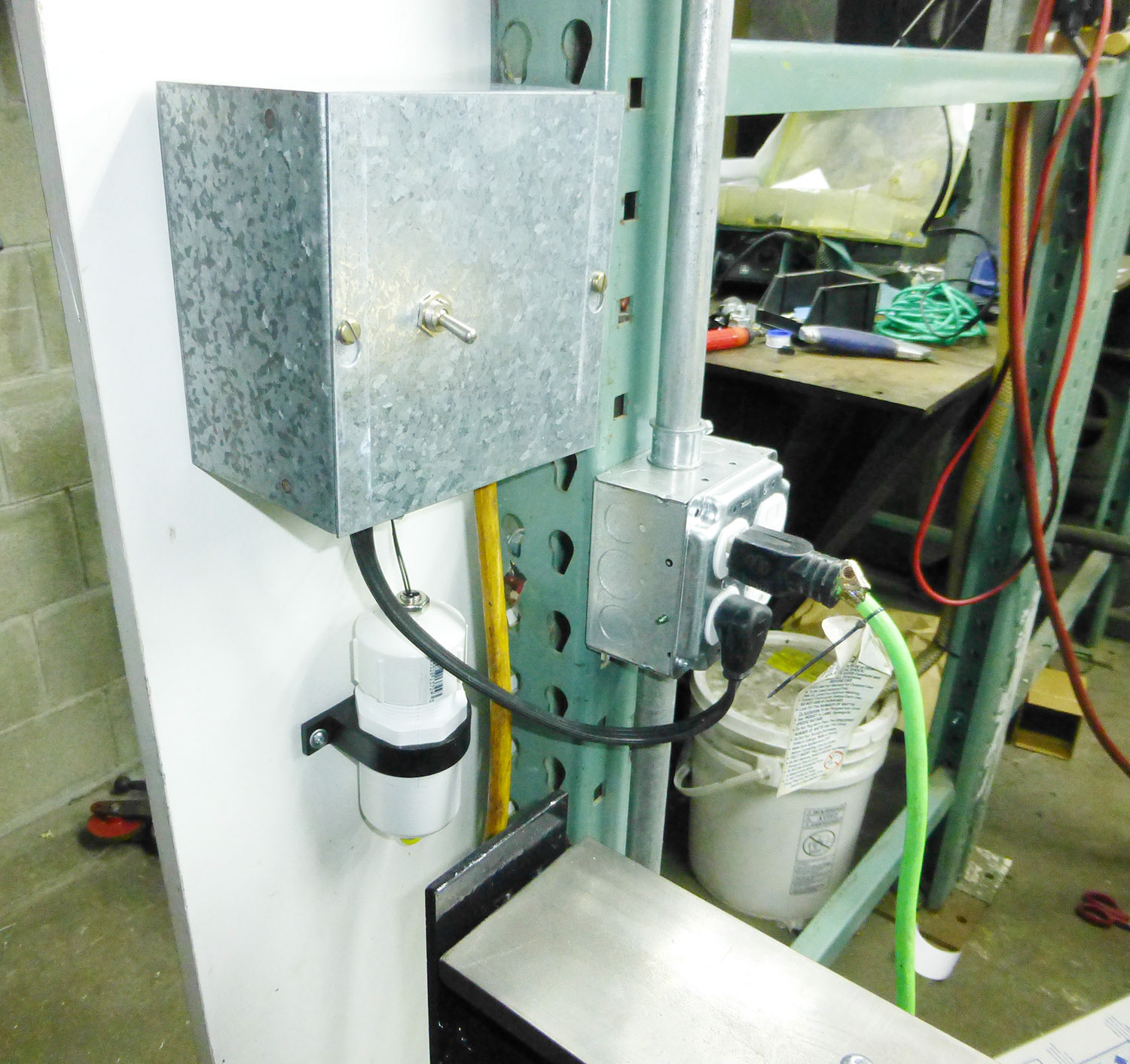
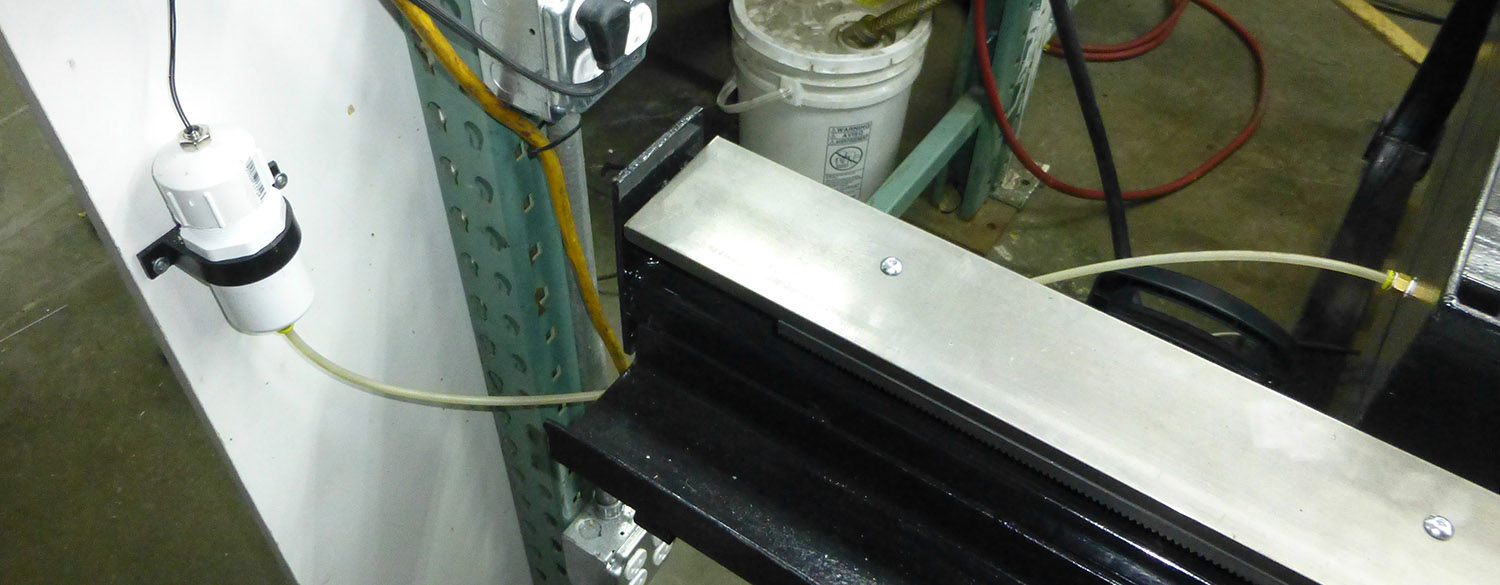
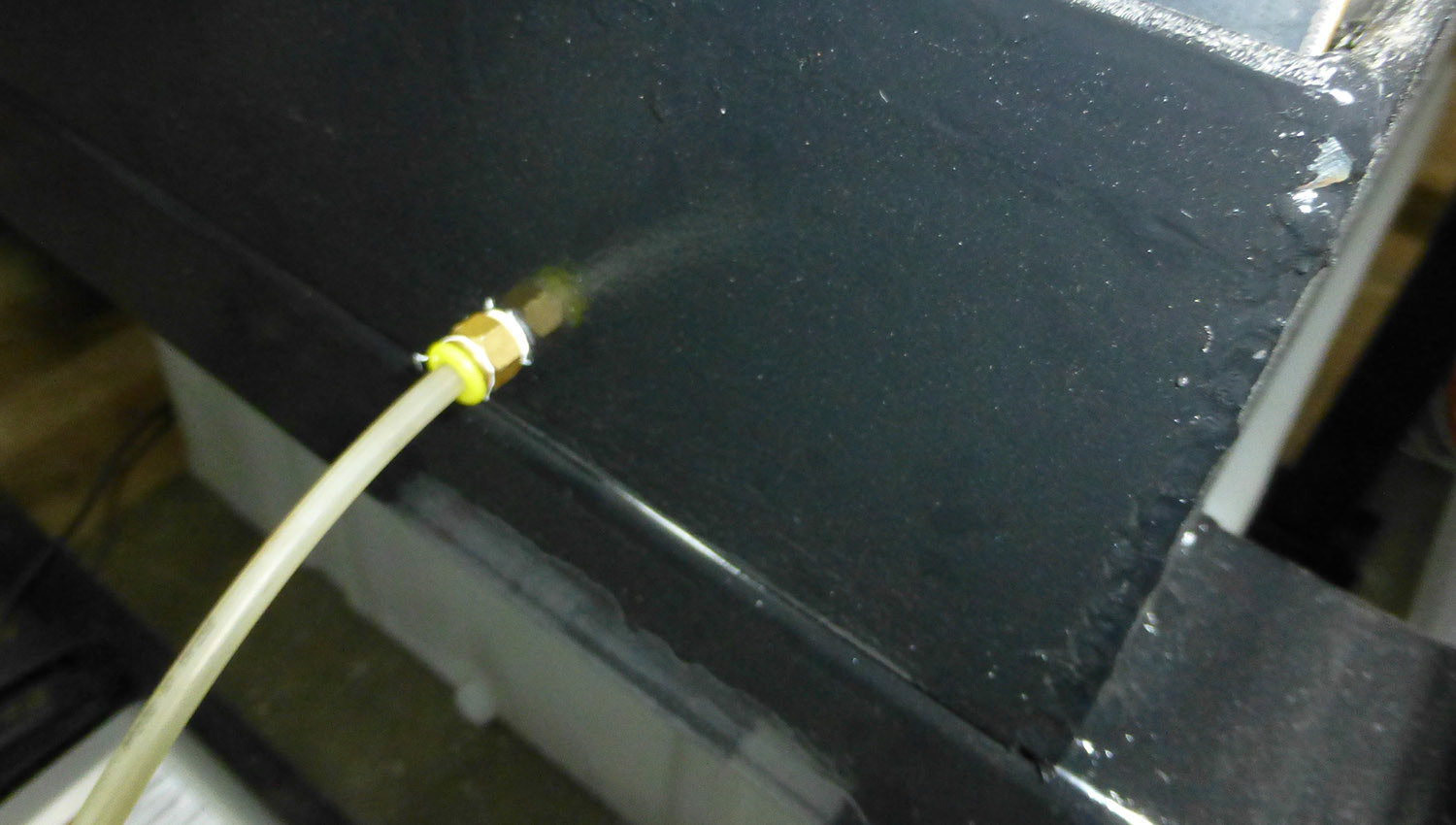
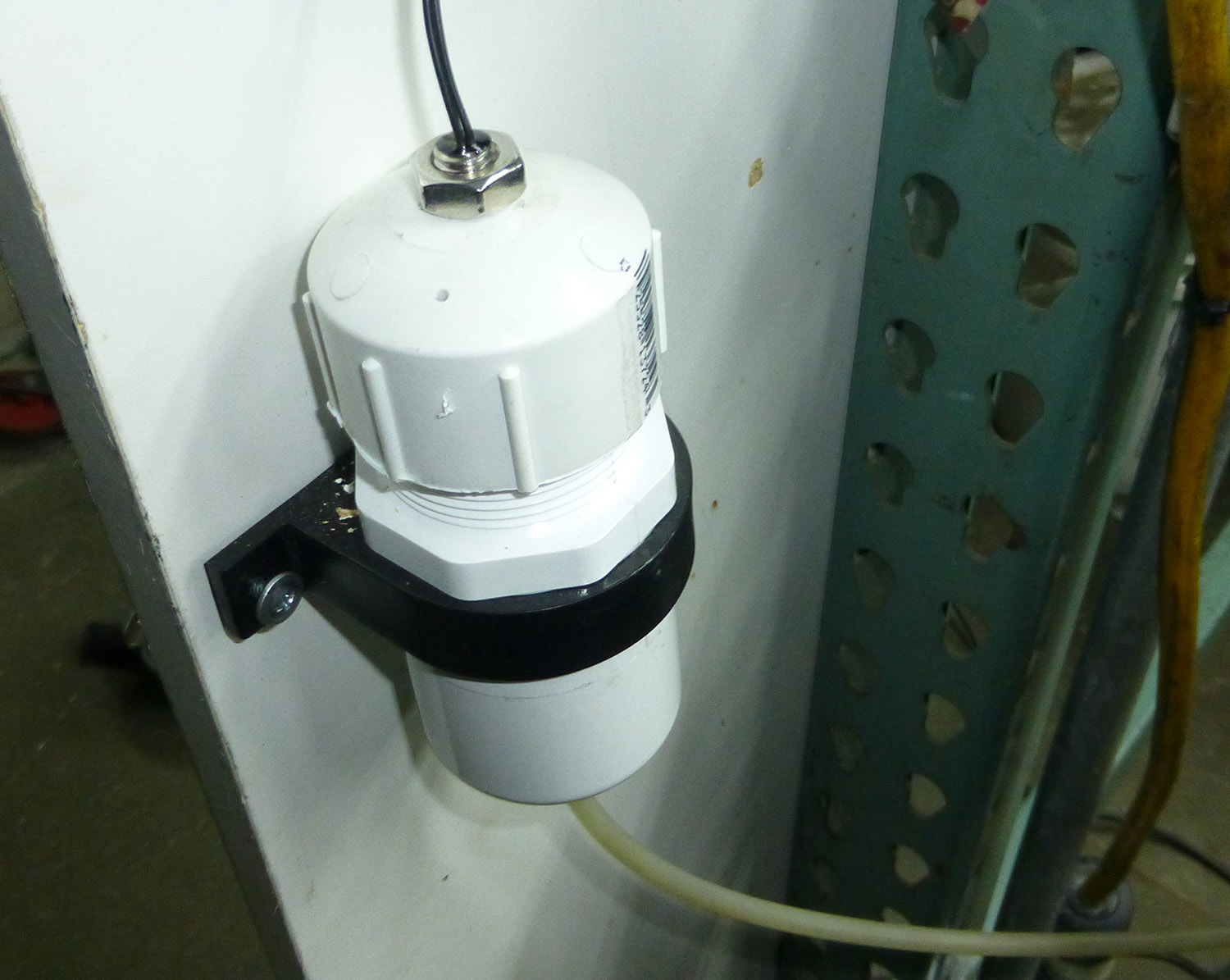
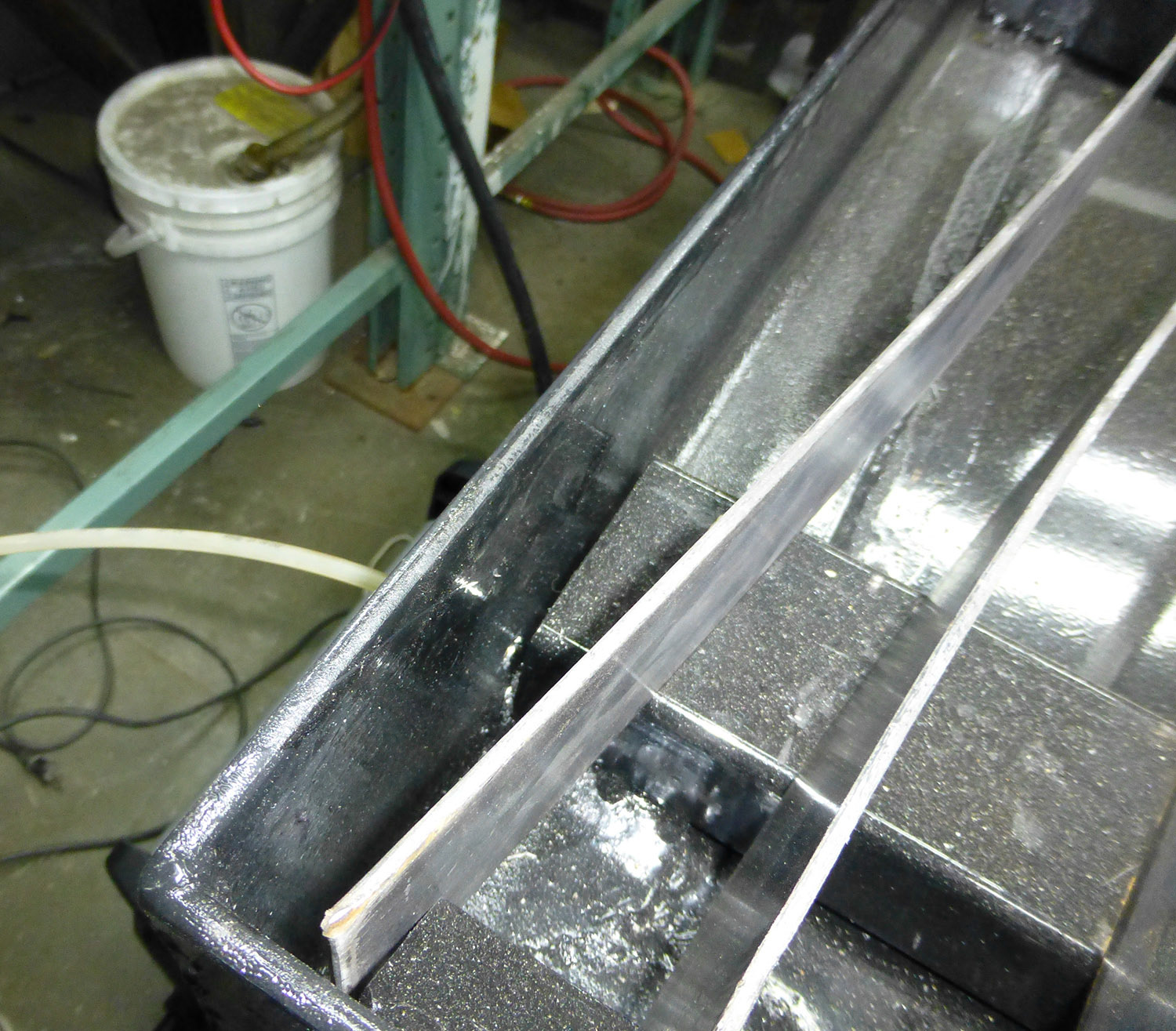
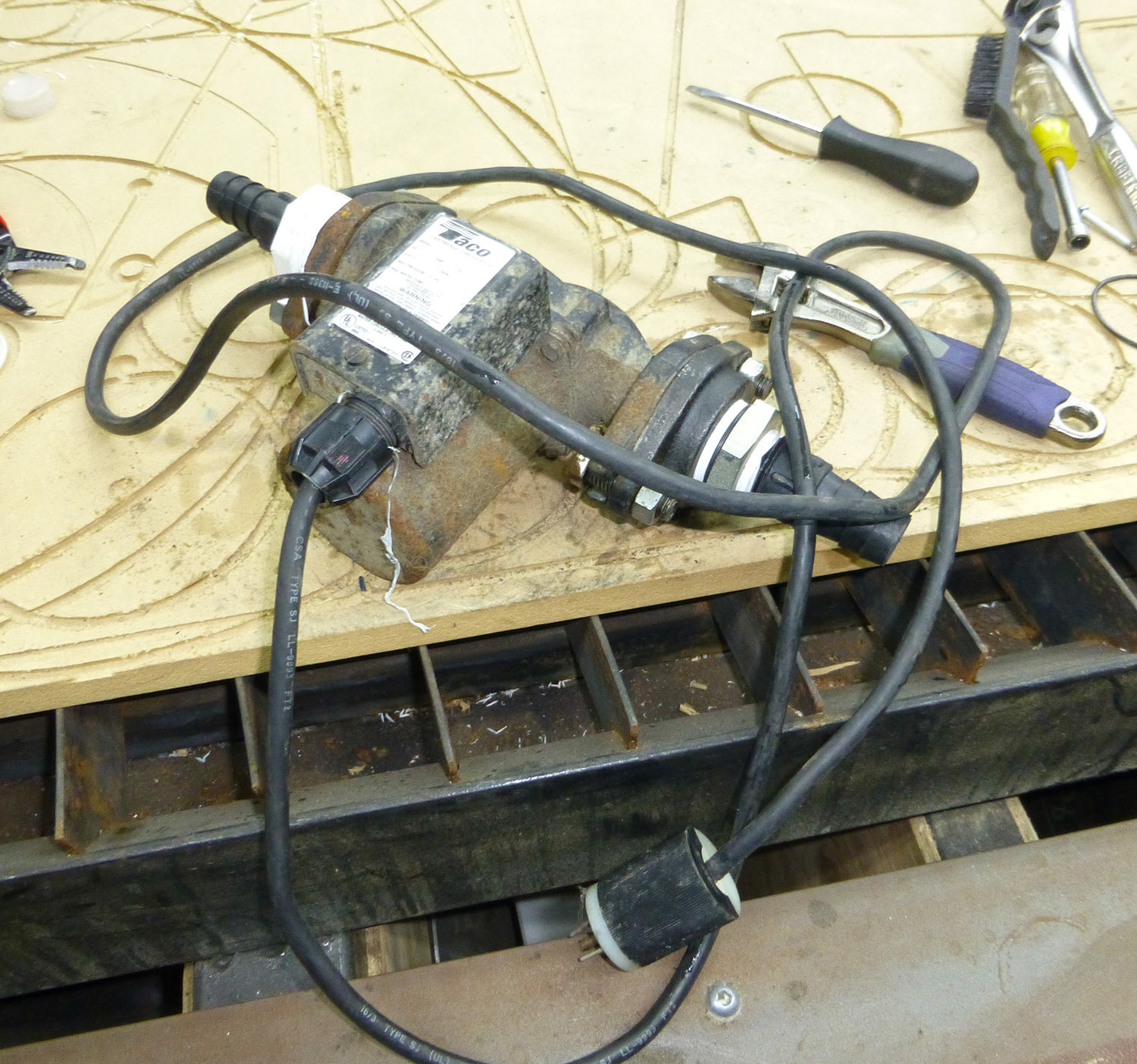
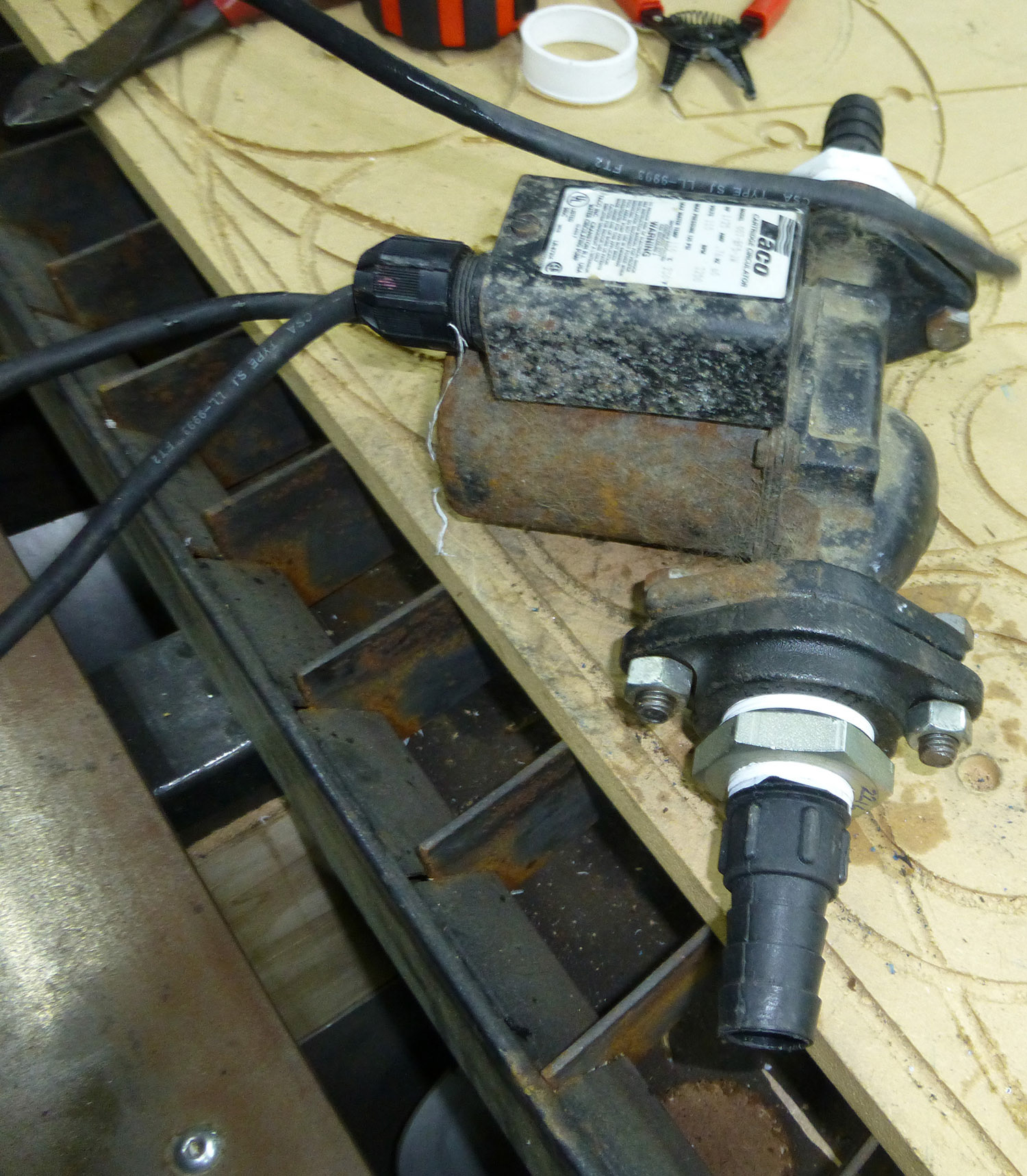
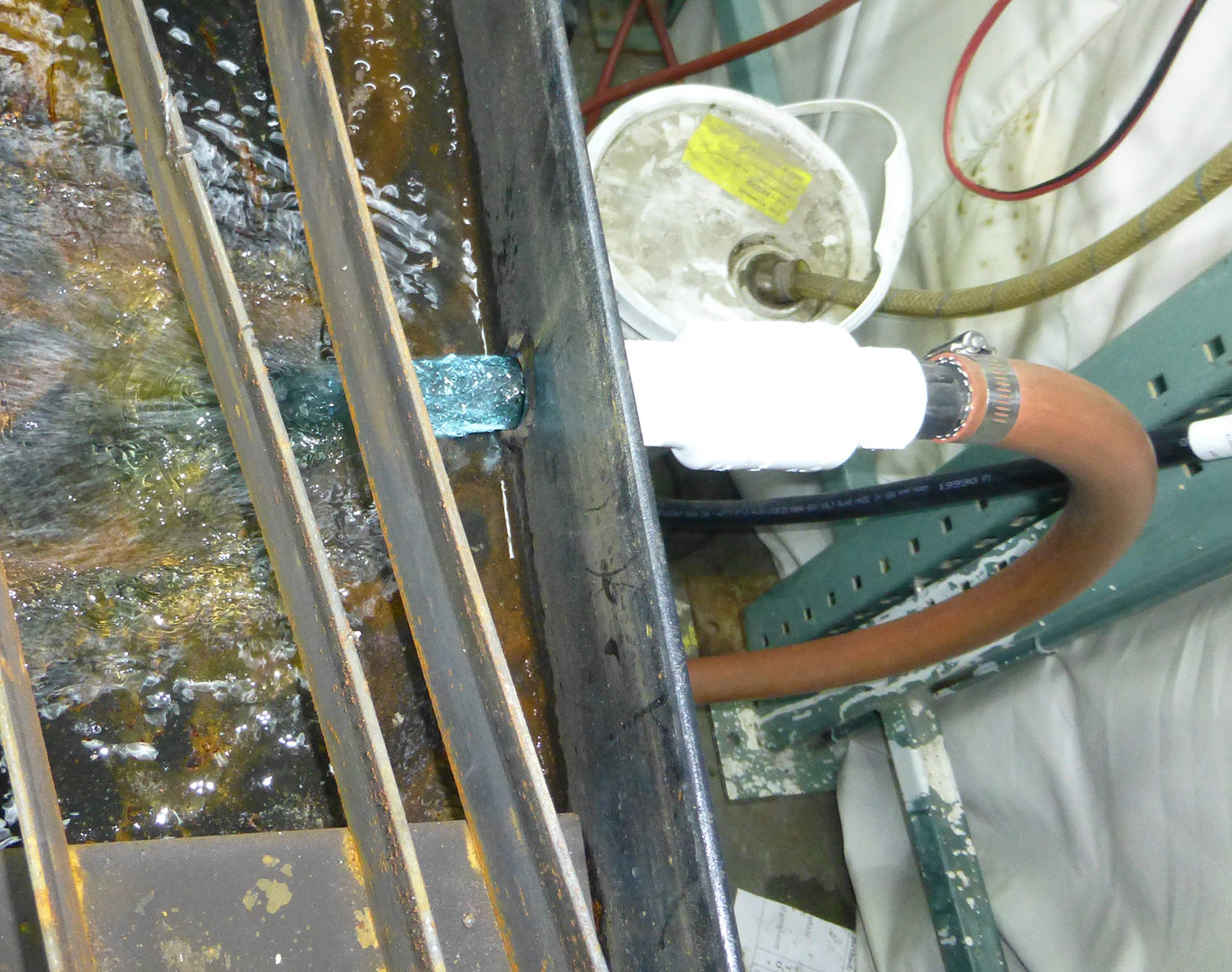
I positioned a 100-gallon water tank under the table and added a filling system. I made a float switch that attached to the wall next to the table that would turn the pump off when the water reached the predetermined height. I added a check valve to the inlet so the water would not back flow through the pump. Under the table drain, I added a quarter turn ball valve and a spin down filter to catch any metal particulates before they got into the tank.
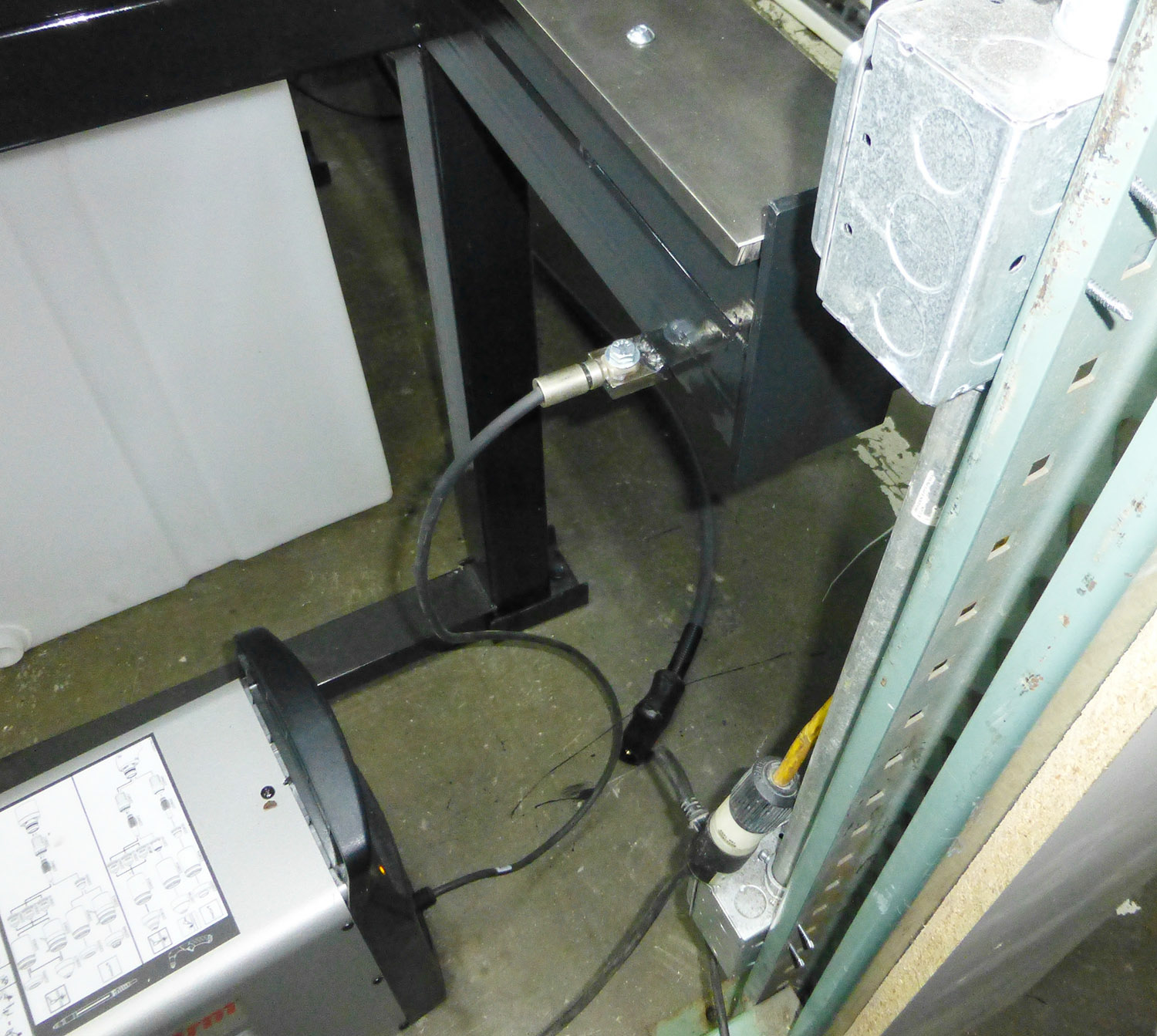
Once everything was working, I leveled the table and anchored it to the floor. I ran an 8-foot ground rod through the concrete and attach the plasma cutter.
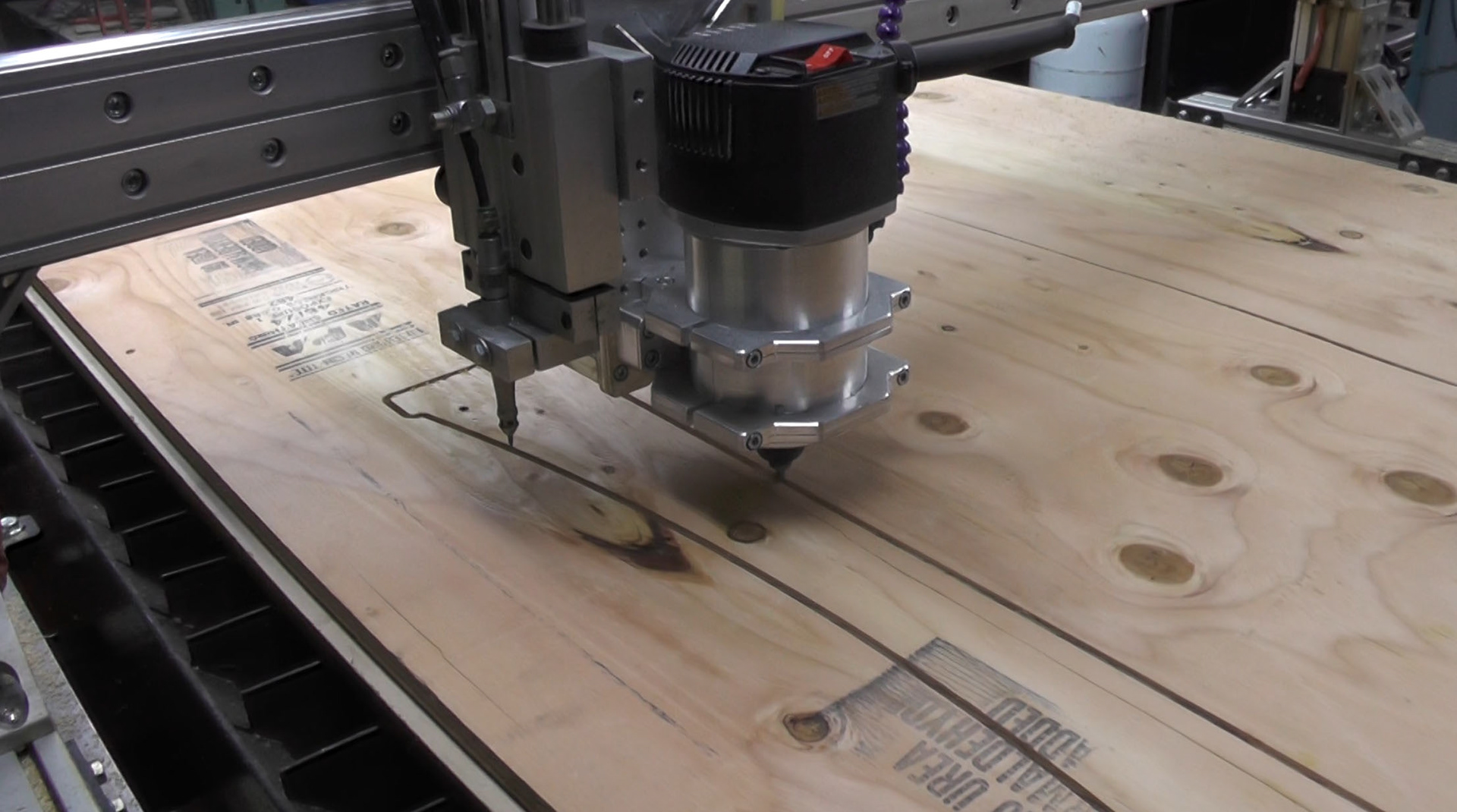
Up and running.